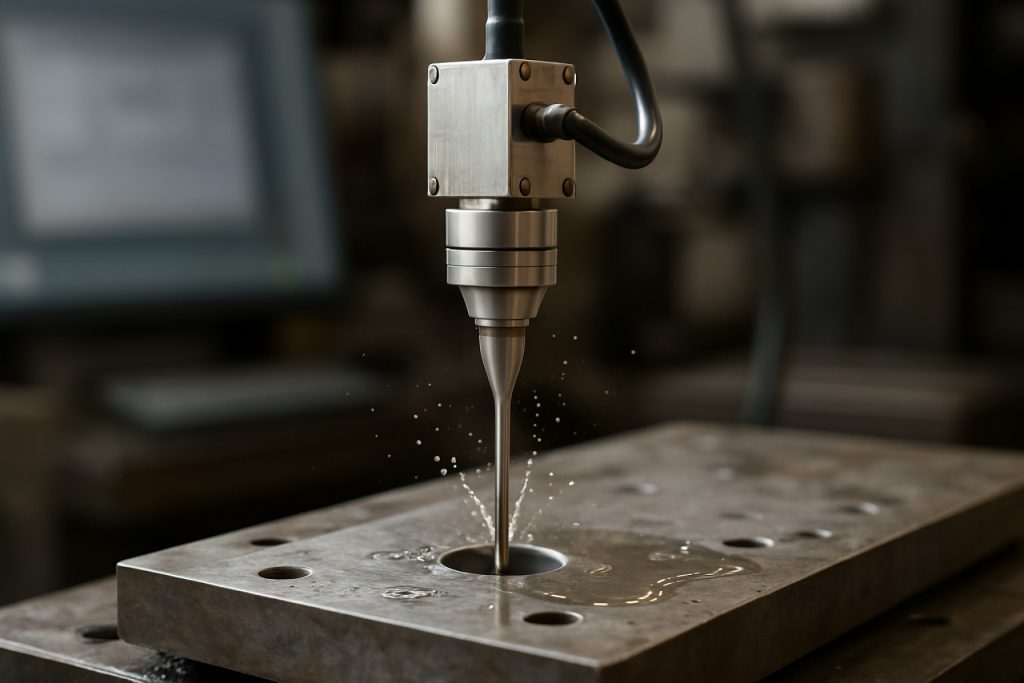
Spis Treści
- Podsumowanie wykonawcze: Wiercenie ultradźwiękowe w 2025 roku
- Przegląd technologii: Jak działają ultradźwięki prowadzone
- Kluczowi gracze i konsorcja przemysłowe
- Ostatnie innowacje i trendy patentowe
- Aktualny rozmiar rynku i prognozy na lata 2025–2030
- Aplikacje użytkowników końcowych: Energia, produkcja i inne
- Krajobraz konkurencyjny i partnerstwa strategiczne
- Normy regulacyjne i wytyczne branżowe
- Wyzwania, ryzyka i ograniczenia
- Perspektywy na przyszłość: Technologie wiercenia ultradźwiękowego nowej generacji
- Źródła i odniesienia
Podsumowanie wykonawcze: Wiercenie ultradźwiękowe w 2025 roku
Technologie wiercenia ultradźwiękowego z prowadzeniem mają potencjał, aby znacząco wpłynąć na zaawansowaną produkcję i przetwarzanie materiałów w 2025 roku oraz w najbliższej przyszłości. Wiercenie ultradźwiękowe, które wykorzystuje wysokoczęstotliwościowe wibracje do ułatwienia usuwania materiału, jest coraz częściej dostosowywane z systemami prowadzenia — od precyzyjnego sterowania ścieżką narzędzia po integrację informacji zwrotnej w czasie rzeczywistym. Te usprawnienia bezpośrednio odpowiadają na wymagania dotyczące wyższej dokładności, zmniejszonego zużycia narzędzi oraz możliwości przetwarzania trudnych materiałów, takich jak nowoczesna ceramika, kompozyty i podłoża półprzewodnikowe.
W ciągu 2024 roku i w 2025 roku wiodący producenci sprzętu zintegrowali ultradźwiękowe systemy prowadzenia, wykorzystując czujniki, wizję maszynową oraz adaptacyjne algorytmy sterujące. Na przykład, Sonimat i Ultrasonic Systems rozwijają swoje platformy, włączając kontrolę ruchu i monitorowanie w czasie rzeczywistym, aby zapewnić optymalne dostarczenie energii i stałą głębokość wiercenia. Te rozwiązania mają szczególne znaczenie w zastosowaniach lotniczych, elektronicznych oraz przy produkcji urządzeń medycznych, gdzie tolerancje są ścisłe, a konwencjonalne wiercenie mechaniczne może prowadzić do mikropęknięć lub delaminacji.
Ostatnie demonstracje firm takich jak Sonimat wykazały, że prowadzone wiercenie ultradźwiękowe może skrócić czas obróbki o nawet 30% w porównaniu do tradycyjnych metod ultradźwiękowych lub mechanicznych, jednocześnie poprawiając jakość otworów i powtarzalność wymiarową. W produkcji półprzewodników wdrożenie systemów prowadzenia ultradźwiękowego pozwoliło na stworzenie bardziej skomplikowanych przejść przez wafle i mikrocech, spełniając wymagania dotyczące miniaturyzacji i precyzji (Ultrasonic Systems).
Kluczowym rozwojem technologii w 2025 roku jest przejście na kontrolę prowadzenia w zamkniętej pętli, gdzie parametry wiercenia są automatycznie dostosowywane w odpowiedzi na dane z czujników dotyczące amplitudy wibracji, zużycia narzędzi i integralności obrabianego elementu. Tego typu podejście adaptacyjne jest promowane przez europejskich i azjatyckich producentów, którzy wdrażają inteligentne linie ultradźwiękowe zarówno w projektach pilotażowych, jak i produkcyjnych. Dodatkowo, współpraca z integratorami automatyki przyspiesza adopcję prowadzonego wiercenia ultradźwiękowego w środowiskach o dużej wydajności.
Patrząc w przyszłość, prognozy dotyczące technologii wiercenia ultradźwiękowego z prowadzeniem są optymistyczne. Kontynuowane postępy w cyfrowych czujnikach, uczeniu maszynowym do optymalizacji procesów oraz integracja z platformami Przemysłu 4.0 mają nadal zwiększać niezawodność i opłacalność. Oczekuje się, że rynek będzie widział szerszą adopcję w sektorach wymagających precyzyjnego, bezuszkodowego wiercenia w zaawansowanych materiałach, przy czym firmy takie jak Sonimat i Ultrasonic Systems są dobrze ulokowane jako kluczowi dostawcy technologii do 2025 roku i dalej.
Przegląd technologii: Jak działają ultradźwięki prowadzone
Technologie wiercenia ultradźwiękowego z prowadzeniem stanowią znaczną ewolucję w dziedzinie zaawansowanej produkcji i inżynierii precyzyjnej. W przeciwieństwie do konwencjonalnego wiercenia mechanicznego, wiercenie ultradźwiękowe wykorzystuje wysokoczęstotliwościowe wibracje ultradźwiękowe — zazwyczaj w zakresie 20–40 kHz — nałożone na wiertło lub narzędzie. Ta energia wibracyjna, gdy jest precyzyjnie kierowana i kontrolowana, zmniejsza wymagany siłę wiercenia, zwiększa prędkość penetracji i minimalizuje generację ciepła, co czyni ją szczególnie korzystną dla twardych i kruchych materiałów, takich jak ceramika, kompozyty i zaawansowane stopy.
Podstawowa technologia obejmuje przetwornik ultradźwiękowy, często piezoelektryczny, który przekształca energię elektryczną w wibracje mechaniczne. Te są przekazywane przez zespół wzmacniacza i rogu do narzędzia wiercącego, które jest wprowadzane w kontakt z obrabianym elementem. Dodanie mechanizmu prowadzenia — często realizowanego poprzez zintegrowane czujniki i pętle informacji zwrotnej w czasie rzeczywistym — umożliwia precyzyjne sterowanie ścieżką narzędzia, optymalną amplitudę wibracji oraz dynamiczną reakcję na zmiany w twardości materiału lub geometrii. To podejście prowadzące zapewnia doskonałą dokładność i powtarzalność, co jest istotne w zastosowaniach w przemyśle lotniczym, produkcji urządzeń medycznych i mikroelektronice.
Ostatnie osiągnięcia, obserwowane w latach 2024–2025, koncentrują się na poprawie integracji systemów ultradźwiękowych z narzędziami CNC oraz platformami robota, co pozwala na wieloosiowe prowadzenie i skoordynowaną kontrolę procesów. Na przykład, SONOTRONIC Nagel GmbH i TELSONIC AG opracowały modułowe głowice wiercące ultradźwiękowo, które mogą być zamontowane na istniejącym sprzęcie produkcyjnym, oferując producentom elastyczność i skalowalność. Te systemy zazwyczaj charakteryzują się kontrolą w zamkniętej pętli, diagnostyką procesów w czasie rzeczywistym oraz przyjaznymi interfejsami użytkownika, umożliwiając operatorom dostosowywanie parametrów w oparciu o informacje zwrotne z procesu.
W 2025 roku kluczowym trendem jest zastosowanie wiercenia ultradźwiękowego z prowadzeniem w sektorze lotniczym, gdzie firmy takie jak Safran badają jego zastosowanie do wiercenia kompozytów wzmocnionych włóknem i stopów wysokotemperaturowych. Zdolność technologii do produkcji czystszych otworów z mniejszą delaminacją i zużyciem narzędzi napędza jej szerszą adopcję. Podobnie, firmy technologii medycznej dostosowują wiercenie ultradźwiękowe z prowadzeniem do minimalnie inwazyjnych operacji na kościach, korzystając z precyzji i zmniejszonego uszkodzenia termicznego.
Patrząc w przyszłość, w nadchodzących latach oczekuje się dalszej miniaturyzacji komponentów ultradźwiękowych, poprawy integracji czujników oraz inteligentniejszej automatyzacji procesów. Zbieżność wiercenia ultradźwiękowego z zasadami Przemysłu 4.0 — w tym monitorowaniem i prognozowaniem w czasie rzeczywistym — prawdopodobnie przyspieszy wdrażanie w zaawansowanych sektorach produkcyjnych, wspierając wyższe standardy wydajności i jakości.
Kluczowi gracze i konsorcja przemysłowe
Krajobraz technologii wiercenia ultradźwiękowego z prowadzeniem w 2025 roku kształtowany jest przez mieszankę ustabilizowanych liderów branżowych, innowacyjnych startupów oraz współpracujących konsorcjów, które koncentrują się na postępie w precyzji, wydajności i automatyzacji procesów wiercenia. Ta technologia, wykorzystująca wysokoczęstotliwościowe wibracje ultradźwiękowe do wspomagania penetracji materiałów, ma szczególne znaczenie w sektorach lotniczych, energetycznych i zaawansowanej produkcji.
Wśród znaczących graczy, SonX pozostaje na czołowej pozycji, wykorzystując swoje zastrzeżone systemy wiercenia ultradźwiękowego do zastosowań w kompozytach i materiałach twardych. Firma kontynuuje rozszerzanie swojej oferty produktowej, aby sprostać rosnącemu zapotrzebowaniu na precyzyjne wiercenie w komponentach lotniczych, napędzanym potrzebą lżejszych i mocniejszych materiałów. Inną prominentną firmą, DeWalt, poczynił postępy w integracji modułów ultradźwiękowych z ich platformami wiercenia przemysłowego, koncentrując się na automatycznych i półautomatycznych rozwiązaniach dla dużych środowisk produkcyjnych.
W sektorze high-tech, Bosch zainwestował znaczne środki w badania i rozwój technologii wiercenia ultradźwiękowego z prowadzeniem, kładąc nacisk na integrację robotów wieloosiowych. Ich systemy mają na celu zmniejszenie zużycia narzędzi i poprawę jakości otworów w trudno obrabialnych stopach, które są coraz częściej stosowane w projektach infrastruktury elektrycznych pojazdów i energii odnawialnej. Podobnie, Sandvik przekracza granice, opracowując wiertła ultradźwiękowe z wbudowanymi czujnikami, które oferują informację zwrotną w czasie rzeczywistym, ułatwiając adaptacyjne procesy wiercenia i prognozowanie konserwacji.
Konsorcja branżowe odgrywają kluczową rolę w standaryzacji i przyspieszaniu adopcji wiercenia ultradźwiękowego z prowadzeniem. ASM International i SAE International aktywnie koordynują grupy robocze i komitety techniczne, koncentrując się na ustalaniu najlepszych praktyk, protokołów bezpieczeństwa i norm interoperacyjności. Te wspólne wysiłki są dodatkowo wspierane przez badania finansowane przez rządy, szczególnie w Europie i Ameryce Północnej, gdzie publiczno-prywatne partnerstwa mają na celu zwiększenie konkurencyjności i zrównoważenia produkcji.
Patrząc w przyszłość, sektor spodziewa się głębszej integracji systemów prowadzenia zasilanych sztuczną inteligencją, rozszerzonego użycia zaawansowanych materiałów oraz szerszej adopcji w sektorze lotniczym, produkcji urządzeń medycznych i energetyce. W miarę jak kluczowi gracze i organizacje branżowe kontynuują współpracę i innowacje, wiercenie ultradźwiękowe z prowadzeniem jest przygotowane do stania się rozwiązaniem powszechnym w wysokoprecyzyjnych, niskouszkodowych procesach wiercenia do późnych lat 2020.
Ostatnie innowacje i trendy patentowe
Technologie wiercenia ultradźwiękowego z prowadzeniem doświadczyły znaczących postępów w ostatnich latach, napędzanych zapotrzebowaniem na zwiększoną precyzję, wydajność i automatyzację we wzorcach przemysłowych i medycznych. W 2025 roku integracja systemów prowadzenia w czasie rzeczywistym z narzędziami do wiercenia ultradźwiękowego przekształca zarówno sektor produkcji, jak i medycyny, prowadząc do wyższej dokładności i mniejszych ryzyk proceduralnych.
Jedną z głównych innowacji jest połączenie technologii wizji komputerowej i fuzji czujników z platformami wiercenia ultradźwiękowego. Wiodący producenci wbudowują zaawansowane mechanizmy informacji zwrotnej, które umożliwiają wiertłu wykrywanie i dostosowywanie do heterogeniczności materiałów w czasie rzeczywistym. Na przykład, firmy specjalizujące się w produkcji urządzeń medycznych wykorzystują systemy dedykowane ultradźwiękowe do minimalnie inwazyjnej chirurgii kości, wykorzystując energię ultradźwiękową do zmniejszenia generacji ciepła i uszkodzeń tkanek pobocznych, jednocześnie utrzymując precyzyjną kontrolę nad trajektoriami wiercenia. Jest to szczególnie widoczne w procedurach ortopedycznych i neurochirurgicznych, gdzie bezpieczeństwo pacjenta i dokładność są kluczowe (Stryker).
W kontekście przemysłowym wiercenie ultradźwiękowe z prowadzeniem jest stosowane do obróbki kompozytów i materiałów zaawansowanych, zwłaszcza w sektorach lotniczym i motoryzacyjnym. Producenci zgłaszają poprawę jakości otworów i wydłużoną trwałość narzędzi dzięki bezkontaktowemu, opartemu na wibracjach mechanizmowi cięcia wiertłem ultradźwiękowym. Integracja z ramionami robotów i cyfrowymi kontrolerami pozwala na w pełni zautomatyzowane prowadzenie wiercenia, co zmniejsza interwencję manualną i zwiększa wydajność (Sandvik). Kontynuowana miniaturyzacja przetworników ultradźwiękowych oraz opracowywanie bardziej robustnych algorytmów prowadzenia mają na celu dalsze rozszerzenie zastosowań w ciągu najbliższych kilku lat.
Aktywność patentowa w tej dziedzinie odzwierciedla rosnącą innowacyjność. Ostatnie zgłoszenia podkreślają przełomy, takie jak AI zasilane korekcje ścieżek, detekcja wad in-situ oraz dynamiczna regulacja parametrów ultradźwiękowych na podstawie danych z materiałów w czasie rzeczywistym. Kluczowi gracze w branży przyspieszają swoje strategie własności intelektualnej, aby zabezpieczyć przewagi konkurencyjne, przy czym wzrasta liczba zgłoszeń związanych z systemami hybrydowymi, które łączą aktywację ultradźwiękową z laserowym lub mechanicznym prowadzeniem dla środowisk wielomateriałowych (GE).
Patrząc w przyszłość, perspektywy dla technologii wiercenia ultradźwiękowego z prowadzeniem pozostają silne. Kontynuowane ulepszenia w integracji czujników, prowadzeniu zasilanym AI oraz adaptacyjną kontrolą mają przynieść systemy zdolne do samoprofesjonalizowania się w różnych ustawieniach operacyjnych. W miarę jak zatwierdzenia regulacyjne dla aplikacji medycznych i lotniczych postępują, oczekuje się szerszej adopcji. W ciągu najbliższych kilku lat wiercenie ultradźwiękowe z prowadzeniem prawdopodobnie ewoluuje od przypadków specjalistycznych do szerszego standardu przemysłowego i klinicznego.
Aktualny rozmiar rynku i prognozy na lata 2025–2030
Technologie wiercenia ultradźwiękowego z prowadzeniem, wykorzystujące wysokoczęstotliwościowe wibracje mechaniczne do zwiększenia prędkości penetracji i precyzji, zyskują na znaczeniu w sektorach przemysłowych i energetycznych. W 2025 roku rynek nadal wschodzi, ale wykazuje szybki potencjał wzrostu, napędzany rosnącym zapotrzebowaniem na zaawansowane rozwiązania wiercenia w sektorach takich jak nafta i gaz, geotermalne, lotnicze oraz produkcja urządzeń medycznych. Zdolność technik ultradźwiękowych do wiercenia twardszych materiałów przy zmniejszonym zużyciu narzędzie i większej dokładności stawia je jako alternatywę przełomową dla konwencjonalnych metod wiercenia obrotowego.
Główne firmy, takie jak Baker Hughes i Schlumberger, aktywnie inwestują w badania i wdrażanie pilotażowe systemów wiercenia ultradźwiękowego z prowadzeniem, skierowanych szczególnie do aplikacji w dół otworów, gdzie precyzja kierowania i minimalne uszkodzenia formacji są krytyczne. Firmy te zgłaszały udane próby terenowe dla wierteł wspomaganych ultradźwiękowo, które wykazały do 30% poprawy w prędkości penetracji (ROP) oraz znaczne wydłużenie życia wierteł w twardych formacjach skał w porównaniu ze standardowymi systemami obrotowymi.
Aktualny rozmiar rynku globalnego dla technologii wiercenia ultradźwiękowego z prowadzeniem szacuje się na niskie setki milionów USD, głównie skoncentrowanym w Ameryce Północnej oraz wybranych regionach europejskich i bliskowschodnich, gdzie operacje wiercenia o wysokiej wartości uzasadniają wdrożenie zaawansowanych rozwiązań. Oczekuje się, że adopcja rynku przyspieszy w latach 2025–2030, a prognozy wzrostu CAGR wynoszą od 18% do 25%, napędzane rozwijającymi się zastosowaniami technologii w budownictwie odwiertów geotermalnych, odwiertach do wychwytywania i składowania dwutlenku węgla (CCS) oraz precyzyjnym tworzeniem otworów dla komponentów strukturalnych w sektorze lotniczym.
W następnych pięciu latach przewiduje się dalszą komercjalizację, ponieważ firmy takie jak Halliburton kontynuują rozwój zintegrowanego prowadzenia, informacji zwrotnej w czasie rzeczywistym i automatyzacji dla zespołów wiercenia ultradźwiękowego. Zbieżność energii ultradźwiękowej z cyfrowymi czujnikami umieszczonymi w otworach oraz algorytmami kierowania zasilanymi AI ma na celu odblokowanie nowych poziomów wydajności wiercenia i oceny formacji w czasie rzeczywistym. Kilka projektów pilotażowych planowanych na koniec 2025 roku i 2026 roku ma na celu zweryfikowanie tych zintegrowanych systemów w złożonych środowiskach, co może katalizować szerszą adopcję w branży do 2030 roku.
Patrząc w przyszłość, prognozy dla technologii wiercenia ultradźwiękowego z prowadzeniem pozostają wyjątkowo pozytywne, pod warunkiem kontynuacji walidacji w terenie i obniżenia kosztów. W miarę skalowania wdrożeń, zarówno wydatki kapitałowe, jak i operacyjne mają się zmniejszyć, dalej poszerzając rynek. Oczekuje się także, że regulacyjne ukierunkowanie na efektywne wiercenie o niskim wpływie na środowisko wzmocni adopcję, pozycjonując prowadzenie ultradźwiękowe jako technologię transformacyjną w globalnym krajobrazie wiercenia.
Aplikacje użytkowników końcowych: Energia, produkcja i inne
Technologie wiercenia ultradźwiękowego z prowadzeniem doświadczają znacznych postępów i adopcji w różnych sektorach końcowych, szczególnie w energetyce i zaawansowanej produkcji. Te systemy wykorzystują wysokoczęstotliwościowe wibracje mechaniczne do zwiększenia efektywności wiercenia, precyzji i przystosowalności materiałów. W 2025 roku przemysł energetyczny — zwłaszcza nafta i gaz oraz geotermalne — nadal napędza większość komercyjnych wdrożeń i testów terenowych rozwiązań wiercenia ultradźwiękowego.
W sektorze nafty i gazu czołowe firmy integrują moduły wiercenia ultradźwiękowego z tradycyjnymi zespołami wiercenia obrotowego, aby poprawić prędkość penetracji (ROP), zmniejszyć zużycie wierteł i umożliwić dostęp do twardszych lub nietypowych formacji. Schlumberger publicznie zademonstrował projekty pilotażowe, w których wykorzystano narzędzia ultradźwiękowe do wspomagania budowy odwiertów, zgłaszając poprawioną jakość otworów i mniej czasu nieproduktywnego. Podobnie, Baker Hughes badał systemy hybrydowe, które synchronizują aktywację ultradźwiękową z rzeczywistym prowadzeniem w dół otworów, zwiększając precyzję podczas długiego wiercenia i operacji bocznych.
Sektor geotermalny to kolejny obszar, w którym wiercenie ultradźwiękowe z prowadzeniem zyskuje na znaczeniu, ponieważ technologia oferuje drogę do ekonomicznego dostępu do złożysk wysokotemperaturowych i twardych skał. Firmy takie jak Halliburton współpracowały z publicznymi instytutami badawczymi nad pilotażowymi głowicami wiercącymi ultradźwiękowo, zauważając obiecujące wyniki dotyczące zmniejszonego odpadania narzędzi i przyspieszonego wiercenia przez krystaliczną skałę. W miarę wzrastającego popytu na energię odnawialną i globalnego dążenia do dekarbonizacji, przestrzeń zastosowań geotermalnych przewiduje dalsze inwestycje i walidację terenową tych zaawansowanych narzędzi do 2025 roku i później.
W zaawansowanej produkcji wiercenie ultradźwiękowe z prowadzeniem jest coraz częściej stosowane do precyzyjnej obróbki komponentów lotniczych, urządzeń medycznych i półprzewodników. Producenci tacy jak SONXTECH i Ultrasonic Systems oferują kompletne rozwiązania do automatyzacji obróbki ultradźwiękowej z prowadzeniem, umożliwiając przetwarzanie kruchych lub kompozytowych materiałów z minimalnymi mikropęknięciami i doskonałą kontrolą wymiarową. Wraz ze wzrostem popytu na lekkie, wysokowydajne materiały w branży motoryzacyjnej i lotniczej, te technologie mają uzyskać dalszy impet.
Patrząc w przyszłość, przewiduje się, że kontynuowane badania i rozwój oraz współpraca międzysektorowa przyniosą dalsze zyski w zakresie solidności narzędzi, oprogramowania kontrolnego oraz optymalizacji procesów opartych na danych. W miarę jak cyfryzacja i automatyzacja będą kontynuowały swoje tempo w sektorach energetycznym i produkcyjnym, wiercenie ultradźwiękowe z prowadzeniem ma szansę stać się kluczową technologią enableującą dostęp podpowierzchniowy nowej generacji oraz precyzyjną produkcję.
Krajobraz konkurencyjny i partnerstwa strategiczne
Krajobraz konkurencyjny dla technologii wiercenia ultradźwiękowego z prowadzeniem szybko ewoluuje w 2025 roku, gdy ustabilizowani producenci sprzętu do wiercenia i innowacyjne firmy technologiczne zdobywają na znaczeniu, aby skomercjalizować zaawansowane systemy ultradźwiękowe z prowadzeniem. Te technologie, które wykorzystują wysokoczęstotliwościowe wibracje ultradźwiękowe do zwiększenia penetracji skał i kontroli kierunkowej, są integrowane zarówno w konwencjonalnych, jak i zautomatyzowanych platformach wiercenia w sektorach energetycznych, górniczych i budowlanych.
Kluczowi gracze branżowi, tacy jak Baker Hughes i Halliburton, aktywnie rozwijają i patentują moduły wiercenia ultradźwiękowego z prowadzeniem, mając na celu poprawę wydajności wiercenia i zmniejszenie nieproduktywnego czasu (NPT) w trudnych warunkach podpowierzchniowych. W 2024 roku i na początku 2025 roku Schneider Electric ogłosił strategiczne inwestycje w systemy monitorowania i sterowania w czasie rzeczywistym, zaprojektowane specjalnie do integracji z głowicami wiercącymi ultradźwiękowo, co daje operatorom lepszą informację zwrotną do precyzyjnego wiercenia i kierowania otworami.
Nowo pojawiające się firmy technologiczne, takie jak Sonimat i Ultrasonic Systems, nawiązały sojusze z głównymi dostawcami usług wiertniczych, aby wspólnie testować prototypy ultradźwiękowe zarówno w projektach onshore, jak i offshore. Te partnerstwa koncentrują się na weryfikacji niezawodności operacyjnej, wydłużonej żywotności wierteł oraz potencjalnych obniżenia emisji dwutlenku węgla dzięki zmniejszeniu wymagań energetycznych. W szczególności Sandvik zainicjował współpracę z instytucjami akademickimi i firmami eksploracyjnymi dotyczących minerałów akumulatorowych, aby dostosować wiercenie ultradźwiękowe do wydobycia litu i pierwiastków ziem rzadkich, co odzwierciedla wszechstronność technologii poza tradycyjnymi celami węglowodorowymi.
Strategiczne partnerstwa rozciągają się również na cyfryzację i automatyzację. Siemens i Honeywell integrują swoje przemysłowe platformy automatyzacji z kontrolą wiercenia ultradźwiękowego, umożliwiając zdalną obsługę i analizy wydajności w czasie rzeczywistym. Te współprace mają na celu zwiększenie bezpieczeństwa, minimalizowanie interwencji manualnej oraz umożliwienie autonomicznych procesów wiercenia, które są priorytetem zarówno w środowiskach wysokiego ryzyka, jak i w lokalizacjach zdalnych.
Patrząc w przyszłość, przewiduje się, że rywalizacja w sektorze nasili się, gdy projekty pilotażowe przejdą do dużych wdrożeń komercyjnych. Firmy priorytetowo traktują ochronę własności intelektualnej oraz współprace międzysektorowe, aby przyspieszyć adopcję rynkową. W miarę jak agencje regulacyjne i konsorcja branżowe, takie jak American Petroleum Institute, opracowują normy bezpieczeństwa i interoperacyjności dla wiercenia ultradźwiękowego, krajobraz prawdopodobnie będzie sprzyjał tym, którzy mają solidne rury badawczo-rozwojowe i ustanowione partnerstwa w zakresie testów terenowych. Trend w sektorze wskazuje, że do 2027 roku technologie wiercenia ultradźwiękowego z prowadzeniem będą integralną częścią nowoczesnych rozwiązań wiercenia, z zastosowaniami międzysektorowymi i solidną podstawą strategicznych współprac.
Normy regulacyjne i wytyczne branżowe
Technologie wiercenia ultradźwiękowego z prowadzeniem zyskują na znaczeniu w sektorach przemysłowych, takich jak lotnictwo, energia i zaawansowana produkcja. W miarę przyspieszenia adopcji, opracowywanie i egzekwowanie norm regulacyjnych oraz wytycznych branżowych stały się kluczowe dla zapewnienia bezpieczeństwa, interoperacyjności i spójności wydajności. W 2025 roku nadzór i standaryzacja są kształtowane przez połączenie organizacji normalizacyjnych, agencji rządowych i konsorcjów branżowych.
Międzynarodowa Organizacja Normalizacyjna (ISO) odgrywa znaczącą rolę w ustalaniu benchmarków dla testowania ultradźwiękowego i aparatów do wiercenia. Normy takie jak ISO 16810 (nieniszczące badanie — terminologia badania ultradźwiękowego) oraz ISO 13585 (nieniszczące badanie spawów — badania ultradźwiękowe — badania techniczne) są teraz odniesione i w niektórych przypadkach aktualizowane, aby uwzględniać niuanse zastosowań ultradźwiękowych w wierceniu. Ponadto Międzynarodowa Komisja Elektrotechniczna (IEC) jest aktywnie zaangażowana w harmonizację norm dotyczących bezpieczeństwa elektrycznego i kompatybilności elektromagnetycznej dla sprzętu ultradźwiękowego, co jest krytyczne, biorąc pod uwagę integrację czujników i systemów prowadzenia w czasie rzeczywistym w tych platformach.
W Stanach Zjednoczonych Amerykańskie Towarzystwo Badań Nieniszczących (ASNT) kontynuuje dostarczanie rekomendowanych praktyk i ram certyfikacyjnych dla operatorów i sprzętu w dziedzinie ultradźwięków. Ich normy, w tym ASNT SNT-TC-1A dotyczące kwalifikacji i certyfikacji personelu, są dostosowywane przez producentów systemów wiercenia ultradźwiękowego, aby zapewnić, że personel w terenie może bezpiecznie i skutecznie wdrażać te technologie. Podobnie w Europie Europejska Komisja Normalizacyjna (CEN) pracuje nad dostosowaniem swoich norm serii EN do pojawiających się możliwości wiercenia ultradźwiękowego, aby ułatwić akceptację międzykrajową oraz dostęp do rynku.
Grupy przemysłowe, takie jak Amerykański Instytut Naftowy (API) i Stowarzyszenie Przemysłu Lotniczego (AIA), współpracują z twórcami technologii i użytkownikami końcowymi w celu opracowania wytycznych specyficznych dla zastosowań, szczególnie dla wiercenia w dół otworów i wytwarzania materiałów kompozytowych. Te wytyczne uwzględniają nie tylko wydajność techniczną, ale także czynniki środowiskowe i wymagania dotyczące interoperacyjności danych.
Patrząc w przyszłość, w kolejnych latach oczekuje się wprowadzenia specjalistycznych norm dostosowanych do wiercenia ultradźwiękowego z prowadzeniem, odzwierciedlających postępy w automatyzacji, integrację sztucznej inteligencji i zdalne sterowanie. Interesariusze przewidują, że zgodność regulacyjna uprości proces komercjalizacji i zwiększy zaufanie użytkowników, wspierając jednocześnie bezpieczne skalowanie tej innowacyjnej technologii wiercenia w różnorodnych środowiskach przemysłowych.
Wyzwania, ryzyka i ograniczenia
Technologie wiercenia ultradźwiękowego z prowadzeniem, które wykorzystują wysokoczęstotliwościowe wibracje do poprawy penetracji i precyzji procesów wiercenia, zyskują na znaczeniu w sektorach takich jak lotnictwo, energia i zaawansowana produkcja. Pomimo znaczących postępów i pilotażowych wdrożeń w 2025 roku, kilka wyzwań, ryzyk i wrodzonych ograniczeń nadal ogranicza ich szerszą adopcję i pełną industrializację.
Głównym wyzwaniem technicznym pozostaje kontrola procesów i powtarzalność. Systemy wiercenia ultradźwiękowego, szczególnie te zaprojektowane do zastosowań prowadzących lub kierowanych, wymagają precyzyjnej synchronizacji między wibracjami ultradźwiękowymi a podawaniem mechanicznym. Zróżnicowania w składzie materiałowym, grubości i heterogenicznościach mogą prowadzić do niestabilnych wskaźników cięcia, zużycia narzędzi i wykończenia powierzchni. Producenci, tacy jak Sonimat i Weber Ultrasonics, podkreślają potrzebę zaawansowanej integracji czujników oraz systemów informacji zwrotnej w zamkniętej pętli, aby utrzymać stabilność procesów, jednak takie systemy zwiększają złożoność i koszty.
Innym krytycznym ograniczeniem jest trwałość narzędzi. Przetworniki ultradźwiękowe i wiertła podlegają przyspieszonemu zużyciu z powodu połączenia mechanicznych i wibracyjnych stresów, szczególnie podczas pracy z twardymi lub ściernymi materiałami takimi jak ceramika, kompozyty czy formacje geologiczne. Może to prowadzić do wyższych cykli konserwacyjnych i niespodziewanych przestojów. Niektórzy dostawcy aktywnie opracowują zaawansowane materiały i powłokie narzędzi, jednak w 2025 roku operacyjny czas życia wierteł ultradźwiękowych wciąż pozostaje w tyle za konwencjonalnymi narzędziami superłącznie wypalającymi w wielu wymagających scenariuszach.
Ryzyka ekonomiczne pozostają również znaczące. Początkowa inwestycja kapitałowa w systemy wiercenia ultradźwiękowego z prowadzeniem jest znacznie wyższa niż w przypadku tradycyjnego sprzętu do wiercenia mechanicznego. Integracja z istniejącymi procesami produkcyjnymi lub wierceniem wymaga znacznej zmiany procesu, przeszkolenia operatorów i w niektórych przypadkach modernizacji obiektów. Jak zauważa Sonotronic, potencjalni użytkownicy podnoszą obawy dotyczące zwrotu z inwestycji i długoterminowego wsparcia dla tych stosunkowo nowych systemów.
Operacyjnie, technologia napotyka ograniczenia w zakresie skalowalności i zastosowania. Chociaż wiercenie wspomagane ultradźwiękowo odnosi sukcesy w aplikacjach wymagających wysokiej precyzji lub minimalnego stresu termicznego/mechanicznego — takich jak mikrowiercenie w kruchych materiałach — jest mniej skuteczne w przypadku dużych średnic lub głębokich otworów. Energia potrzebna do utrzymania wysokoczęstotliwościowych wibracji na długich długościach wiercenia wzrasta nieproporcjonalnie, co prowadzi do utraty wydajności i przegrzania systemu.
Patrząc w przyszłość, dalszy postęp zależy od solidnych opracowań materiałów, cyfrowej optymalizacji procesów i wykazania oszczędności kosztów cyklu życia. Organizacje branżowe i wiodący producenci współpracują w sprawie inicjatyw standaryzacyjnych i interoperacyjnych, aby rozwiązać te wąskie gardła. Niemniej jednak, dopóki te techniczne i ekonomiczne bariery nie zostaną bardziej w pełni przezwyciężone, wiercenie ultradźwiękowe z prowadzeniem będzie prawdopodobnie pozostawało rozwiązaniem specjalistycznym, a nie wszechobecnym w krajobrazie przemysłowym wiercenia i wytwarzania.
Perspektywy na przyszłość: Technologie wiercenia ultradźwiękowego nowej generacji
Technologie wiercenia ultradźwiękowego z prowadzeniem mają szansę stać się przełomową siłą w precyzyjnej produkcji i przetwarzaniu zaawansowanych materiałów do 2025 roku i w kolejnych latach. Te systemy wykorzystują wysokoczęstotliwościowe wibracje ultradźwiękowe — często w zakresie 20–40 kHz — w połączeniu z zaawansowanymi mechanizmami prowadzenia, takimi jak ramiona robota i wizja komputerowa, aby osiągnąć bezprecedensową dokładność w wierceniu złożonych geometrii, delikatnych podłoży i materiałów kompozytowych. Integracja prowadzenia w czasie rzeczywistym jest szczególnie ważna w sektorach, takich jak lotnictwo, motoryzacja i produkcja urządzeń medycznych, gdzie tolerancje są ścisłe, a integralność materiału ma znaczenie kluczowe.
Ostatnie demonstracje i wdrożenia pilotażowe wykazały wyraźne poprawy w jakości otworów, zmniejszonej delaminacji w kompozytach i znaczących zmniejszenia zużycia narzędzi w porównaniu do konwencjonalnego wiercenia mechanicznego lub ściernego. Firmy takie jak SONOTRONIC Nagel GmbH i Dukane aktywnie rozwijają systemy wiercenia ultradźwiękowego z zintegrowanymi modułami prowadzenia, kierując się automatycznymi liniami produkcyjnymi i robotycznymi komórkami roboczymi. Te systemy mogą dynamicznie dostosowywać trajektorie wiercenia na podstawie informacji zwrotnej z czujników siły i monitorowania optycznego, umożliwiając adaptacyjne obrabianie w odpowiedzi na niespójności materiałów lub niewłaściwe ustawienie części.
Perspektywy dla lat 2025–2027 kształtowane są przez kilka zbieżnych trendów. Po pierwsze, rosnąca adopcja kompozytowych i wielomateriałowych zestawów w zastosowaniach lotniczych i motoryzacyjnych przyspiesza zapotrzebowanie na rozwiązania wiercenia, które mogą obsługiwać kruche lub warstwowe podłoża bez powodowania mikropęknięć lub delaminacji. Po drugie, dążenie do produkcji zgodnej z zasadami Przemysłu 4.0 napędza inwestycje w cyfrowe, oparte na danych kontrolowanie procesów — w obszarze, w którym systemy z prowadzeniem ultradźwiękowym, ze swoimi bogatymi pętlami informacji zwrotnej, oferują przekonywającą przewagę. Po trzecie, postępy w robotyce przemysłowej obniżają bariery do wdrażania głowic ultradźwiękowych na platformach wieloosiowych, co pozwala na bardziej elastyczne i skalowalne komórki obróbcze.
- Sektor lotniczy: Producenci samolotów i dostawcy poziomi coraz częściej definiują wiercenie ultradźwiękowe dla kompozytowych kadłubów. Airbus podkreślił znaczenie nowatorskich technologii wiercenia dla utrzymania integralności strukturalnej w nowej generacji samolotów.
- Urządzenia medyczne: Zapotrzebowanie na precyzyjnie wiercone mikrocechy w implantach i narzędziach chirurgicznych ma wspierać adopcję systemów ultradźwiękowych z prowadzeniem, a takie firmy jak Dukane współpracują z producentami urządzeń medycznych.
- Energie i elektronika: Wiercenie ultradźwiękowe jest rozważane dla krzemu, szafiru i ceramiki w produkcji akumulatorów i półprzewodników, z systemami prowadzenia umożliwiającymi powtarzalność procesów.
Patrząc w przyszłość, kontynuowane badania i rozwój oraz wczesne wdrożenia komercyjne mają poprawić nie tylko dokładność i prędkość procesów, ale także zmniejszyć koszty operacyjne i wpływ na środowisko poprzez minimalizację zużycia narzędzi i odpadów. W miarę jak ekosystemy cyfrowe w produkcji będą się rozwijać, wiercenie ultradźwiękowe z prowadzeniem ma szansę odegrać kluczową rolę w wysoko wartościowych sektorach przemysłowych, napędzających precyzję.
Źródła i odniesienia
- SONOTRONIC Nagel GmbH
- TELSONIC AG
- SonX
- Bosch
- Sandvik
- ASM International
- GE
- Baker Hughes
- Halliburton
- Siemens
- Honeywell
- American Petroleum Institute
- ISO
- ASNT
- CEN
- API
- AIA
- Weber Ultrasonics
- Sonotronic
- Dukane
- Airbus