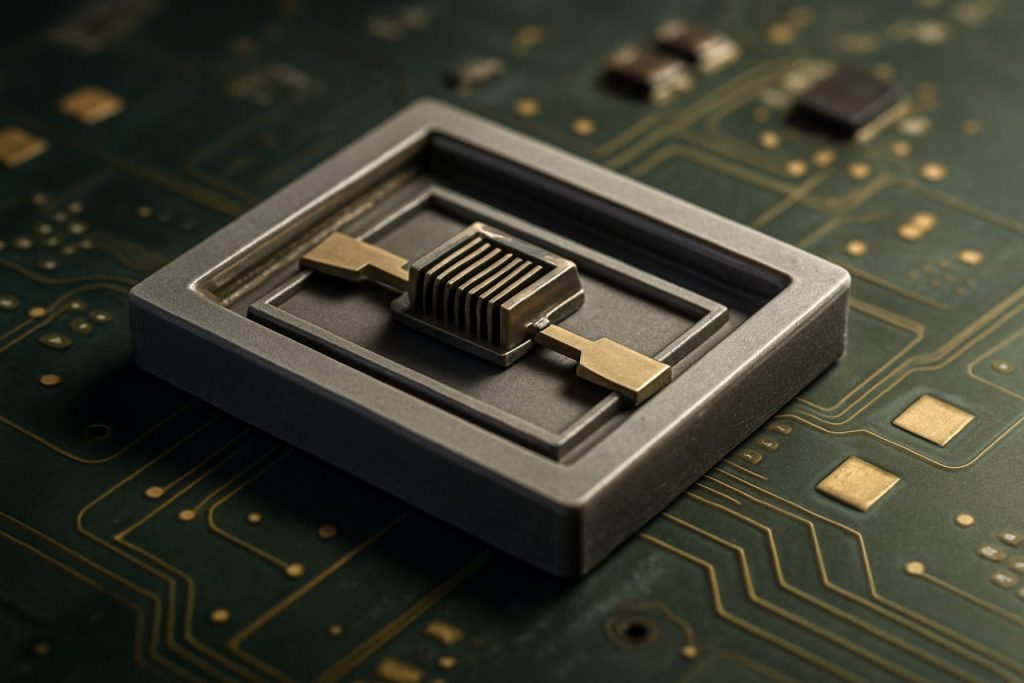
Spis treści
- Podsumowanie: Stan niezawodności przekaźników MEMS w 2025 roku
- Perspektywy rynkowe: Prognozy i czynniki wzrostu do 2030 roku
- Kluczowe zastosowania: Innowacje przemysłowe, motoryzacyjne i IoT
- Nowe metody testowania termo-mechanicznego
- Postępy w naukach materiałowych wpływające na trwałość przekaźników MEMS
- Wiodące firmy i współprace w branży
- Wyzwania: Mechanizmy awarii i wąskie gardła niezawodności
- Standardy regulacyjne i protokoły testowe
- Studia przypadków: Przełomy od wiodących producentów MEMS
- Mapa przyszłości: Rozwiązania z zakresu niezawodności nowej generacji i wpływ na rynek
- Źródła i odniesienia
Podsumowanie: Stan niezawodności przekaźników MEMS w 2025 roku
Niezawodność termo-mechaniczna pozostaje kluczowym zagadnieniem w wdrażaniu urządzeń przekaźników MEMS (mikroelektromechanicznych systemów), zwłaszcza w miarę jak ich integracja w rynku o wysokiej niezawodności nabiera tempa w 2025 roku. Przekaźniki MEMS, które wykorzystują mikroobrobione struktury do realizacji przełączania elektrycznego, są coraz częściej używane w przemyśle lotniczym, telekomunikacyjnym, motoryzacyjnym oraz w instrumentacji testowej ze względu na niskie zużycie energii i precyzyjność działania. Jednak stresy mechaniczne i termiczne, z jakimi się spotykają podczas pracy i cykli środowiskowych, wciąż stanowią wyzwanie zarówno dla trwałości urządzeń, jak i spójności ich wydajności.
W 2025 roku wiodący producenci tacy jak Teledyne oraz Omron Corporation rozwijają kompleksowe protokoły testowania niezawodności termo-mechanicznej. Testy te, obejmujące cykle temperaturowe, cykle mocy oraz oceny wstrząsów mechanicznych, mają na celu symulację trudnych warunków, z którymi przekaźniki MEMS stykają się w rzeczywistych zastosowaniach. Na przykład, Teledyne wykorzystuje przyspieszone testy żywotności do oceny trwałości swoich przekaźników MEMS w Warunkach powtarzalnych obciążeń termicznych i mechanicznych, raportując żywotności operacyjne przekraczające miliard cykli w kontrolowanych warunkach testowych.
Obecne dane wskazują, że udoskonalenia materiałów — takie jak przyjęcie zaawansowanych podłoży krzemowych na izolatorach (SOI) oraz hermetycznego pakowania na poziomie wafla — przynoszą wymierne korzyści w zakresie odporności na zmęczenie mechaniczne i stabilność termiczną. Omron Corporation opublikowało wyniki dotyczące swojego portfela przekaźników MEMS, które wykazują stabilny opór stykowy oraz znikome przyleganie nawet po długotrwałych cyklach temperaturowych pomiędzy -40°C a 125°C, co jest kluczowym kryterium dla zastosowań motoryzacyjnych i przemysłowych.
Standardy branżowe z organizacji takich jak JEDEC Solid State Technology Association oraz IEEE wciąż kształtują metodologie oraz wymagania dotyczące kwalifikacji przekaźników MEMS. W 2025 roku nowe protokoły testowe podkreślają nie tylko liczbę cykli przełączania, ale także wpływ szybkich przejść temperatury i wibracji — odpowiedź na rosnące zapotrzebowanie na bardziej wytrzymałe przekaźniki w infrastrukturze 5G oraz systemach pojazdów autonomicznych.
Patrząc w przyszłość, perspektywy wskazują na kontynuację doskonalenia metod testowych oraz dalszą współpracę między producentami urządzeń, użytkownikami końcowymi i organami normalizacyjnymi. Celem jest zapewnienie, że przekaźniki MEMS mogą niezawodnie spełniać rygorystyczne wymagania systemów elektronicznych nowej generacji. Oczekuje się, że postępy w projektowaniu MEMS, encapsulacji i monitorowaniu stanu w czasie rzeczywistym jeszcze bardziej zwiększą zaufanie do niezawodności termo-mechanicznej tych kluczowych komponentów w nadchodzących latach.
Perspektywy rynkowe: Prognozy i czynniki wzrostu do 2030 roku
Rynek testowania niezawodności termo-mechanicznej w mikroelektromechanicznych urządzeniach przekaźników (przekaźniki MEMS) jest gotowy na znaczny rozwój do 2030 roku, napędzany przez zwiększoną integrację przełączników MEMS i przekaźników w elektronice motoryzacyjnej, przemysłowej i komunikacyjnej. W miarę jak przekaźniki MEMS są wdrażane w krytycznych środowiskach — takich jak systemy bezpieczeństwa w pojazdach, infrastruktura 5G oraz automatyzacja przemysłowa — ich niezawodność operacyjna w zróżnicowanych stresach termicznych i mechanicznych stała się decydującym czynnikiem przyjęcia. To intensyfikuje zapotrzebowanie na zaawansowane usługi i rozwiązania testowania niezawodności.
Od 2023 roku liderzy branżowi raportują szybki wzrost zastosowań przekaźników MEMS wymagających dużej odporności na cykle termiczne, wibracje i wstrząsy, co napędza przyjęcie kompleksowych protokołów kwalifikacji niezawodności zgodnych z takimi standardami jak AEC-Q100 i MIL-STD-883. Na przykład, TE Connectivity oraz Coto Technology rozszerzyły swoje portfolio przekaźników MEMS i koncentrują się na rygorystycznych procesach weryfikacji termo-mechanicznej, aby spełnić normy niezawodności w motoryzacji i telekomunikacji.
Producenci samochodów i dostawcy Tier 1 coraz bardziej podkreślają strategie zerowych wad, wymagając większej przejrzystości w danych dotyczących niezawodności oraz ścisłej identyfikowalności w całym łańcuchu dostaw przekaźników MEMS. Doprowadziło to do partnerstw z dostawcami rozwiązań testujących oraz przyjęcia zautomatyzowanych systemów testowych zdolnych do monitorowania wydajności przekaźników MEMS na dużą skalę w warunkach symulowanych. Na przykład, Rohde & Schwarz wprowadziła platformy testowe dostosowane do niezawodności urządzeń MEMS, wspierające testy cykli temperaturowych, wilgotności i wibracji.
Do 2030 roku prognozuje się, że proliferacja pojazdów elektrycznych, IoT przemysłowego i infrastruktury bezprzewodowej o wysokiej częstotliwości będzie podtrzymywać wzrost roczny na poziomie dwucyfrowym w sektorze przekaźników MEMS. Ekspansja ta z kolei zwiększy potrzebę zaawansowanych technologii testowania niezawodności termo-mechanicznej, takich jak monitorowanie in-situ, analiza awarii specyficznych dla MEMS i platformy przyspieszonego testowania żywotności. Organizacje branżowe takie jak SEMI są oczekiwane do dalszego udoskonalania najlepszych praktyk i ustalania nowych wytycznych dla kwalifikacji przekaźników MEMS.
Patrząc w przyszłość, integracja analiz danych opartych na AI i cyfrowych bliźniaków w testowaniu niezawodności ma szansę stać się kluczowym czynnikiem wyróżniającym. To umożliwi przewidywalne utrzymanie, szybsze cykle kwalifikacji oraz skrócone czasy rozwoju produktów. W miarę jak złożoność i wymagania dotyczące wydajności przekaźników MEMS rosną, inwestycje w zautomatyzowane, wydajne testy niezawodności termo-mechanicznej będą kluczowe dla dostawców dążących do uchwycenia pojawiających się możliwości rynkowych w sektorach motoryzacyjnym, przemysłowym i nowej generacji komunikacji.
Kluczowe zastosowania: Innowacje przemysłowe, motoryzacyjne i IoT
Przyjęcie mikroelektromechanicznych urządzeń przekaźników (przekaźniki MEMS) wciąż rośnie w kluczowych sektorach, takich jak automatyzacja przemysłowa, systemy motoryzacyjne oraz Internet Rzeczy (IoT). W miarę jak te aplikacje wymagają wysokiej niezawodności w zróżnicowanych warunkach środowiskowych i operacyjnych, testowanie niezawodności termo-mechanicznej stało się podstawą w kwalifikacji urządzeń i prognozowaniu cyklu życia na rok 2025 oraz w najbliższej przyszłości.
W dziedzinie przemysłowej przekaźniki MEMS są coraz częściej wykorzystywane do precyzyjnego przełączania w trudnych warunkach, w tym w robotyce przemysłowej, kontroli procesów i ochronie obwodów wysokiego napięcia. Testy termo-mechaniczne — takie jak cykle temperaturowe, cykle mocy i wstrząsy mechaniczne — są niezbędne do zapewnienia, że urządzenia utrzymują niski opór stykowy i stabilną aktywację przez miliony cykli. Na przykład, TE Connectivity raportuje bieżącą kwalifikację przekaźników MEMS przy użyciu protokołów przyspieszonego testowania żywotności dostosowanych do niezawodności klasy przemysłowej, symulując dziesięciolecia zużycia operacyjnego w kilka miesięcy.
Zastosowania motoryzacyjne stawiają jeszcze surowsze wymagania, przekaźniki MEMS stykają się z szerokimi wahaniami temperatury, wibracjami i wilgotnością w zaawansowanych systemach pomocniczych dla kierowców (ADAS), napędach oraz systemach zarządzania akumulatorami. Liderzy branżowi, tacy jak NXP Semiconductors i STMicroelectronics, rozwijają swoje portfele MEMS w motoryzacji, poddając urządzenia testom standardów motoryzacyjnych, takim jak AEC-Q100, wstrząsy termiczne i wysoka temperatura pracy (HTOL). Ostatnie dane od tych producentów podkreślają, że przekaźniki MEMS teraz niezawodnie znoszą ponad 1000 cykli temperaturowych między -40°C a 125°C, spełniając wymagania dla pojazdów elektrycznych nowej generacji.
Innowacje IoT przesuwają granice miniaturyzacji i efektywności energetycznej przekaźników MEMS, z miliardami podłączonych sensorów i aktuatorów wdrożonych w zmiennych warunkach wewnętrznych i zewnętrznych. Firmy takie jak CANTIME Microelectronics łączą zaawansowane pakowanie i solidne testy termo-mechaniczne, aby zapewnić integralność przekaźników w urządzeniach brzegowych, noszonych oraz infrastrukturze inteligentnej. Celem jest zapewnienie spójnej wydajności mimo częstych cykli termicznych wynikających z szybkiego przełączania włącz/wyłącz i zmiennych warunków otoczenia.
Patrząc w przyszłość, trajektoria na 2025 rok i dalej wskazuje na integrację monitorowania niezawodności opartego na AI, testowania stresu w czasie rzeczywistym oraz dalszą harmonizację standardów przemysłowych dla kwalifikacji przekaźników MEMS. W miarę jak geometria urządzeń maleje, a warunki aplikacji stają się coraz trudniejsze, współpraca między producentami półprzewodników a użytkownikami końcowymi będzie kluczowa dla postępu w niezawodności termo-mechanicznej. Ciągłe doskonalenie metod przyspieszonych testów, wraz z solidnym feedbackiem z danych z terenu, powinno prowadzić do dalszych ulepszeń w trwałości przekaźników MEMS i umożliwiać ich szersze wdrożenie w krytycznych, zależnych od misji zastosowaniach.
Nowe metody testowania termo-mechanicznego
Testowanie niezawodności termo-mechanicznej stało się kluczowym celem rozwoju mikroelektromechanicznych urządzeń przekaźników (MEM relay), zwłaszcza gdy te komponenty są coraz częściej wykorzystywane w trudnych warunkach i zminiaturyzowanej elektronice. W 2025 roku branża dostrzega trend w kierunku bardziej kompleksowych i przyspieszonych protokołów testowych, które odpowiadają na unikalne tryby awarii związane z interakcją stresów termicznych i mechanicznych na mikroskalę. Kluczowi gracze branżowi wprowadzają kombinację tradycyjnych testów cykli i nowoczesnych technik monitorowania w czasie rzeczywistym, aby zapewnić trwałość na dłuższą metę.
Jedną z głównych metodologii zyskujących na znaczeniu jest wysoko przyspieszone testowanie żywotności (HALT) dostosowane do przekaźników MEM, które poddaje urządzenia szybkim cyklom temperatury i mechaniki, aby wywołać wczesne awarie i ocenić solidność. Na przykład, STMicroelectronics szczegółowo opisała inicjatywy w zakresie wdrażania protokołów wieloosiowych wstrząsów mechanicznych i rampy termicznej w ich R&D MEMS, mając na celu lepsze symulowanie rzeczywistych stresów, jakim podlegają urządzenia przekaźników w środowiskach motoryzacyjnych i przemysłowych.
Równolegle, mikro-skalowana korelacja obrazu cyfrowego (DIC) i laserowa wibrometria Dopplera są coraz częściej wykorzystywane do monitorowania deformacji oraz dynamicznej reakcji pod obciążeniem termicznym, zapewniając wysokiej rozdzielczości wgląd w mechanizmy awarii, takie jak przyleganie, zmęczenie i degradacja kontaktów. Texas Instruments raportuje integrację in-situ systemów pomiarowych w ich laboratoriach niezawodności przekaźników MEM, co pozwala na śledzenie w czasie rzeczywistym reakcji mikrostruktury na cykle termiczne i aktywację mechaniczną.
Kolejną nową metodologią jest zastosowanie testowania niezawodności na poziomie wafla, co pozwala na jednoczesną ocenę dużej liczby przekaźników w kontrolowanych warunkach obciążenia termicznego i mechanicznego. To podejście, jak podkreśla Bosch Sensortec, zwiększa pewność statystyczną i skraca czas weryfikacji produktów przekaźników MEMS przeznaczonych do zastosowań krytycznych dla bezpieczeństwa.
Patrząc w przyszłość, w ciągu najbliższych kilku lat możemy spodziewać się przyjęcia hybrydowych platform testowych, które łączą elektryczne, termiczne i mechaniczne czynniki obciążenia w jednolitym zautomatyzowanym środowisku. Wspólne wysiłki producentów półprzewodników oraz dostawców sprzętu są w toku, aby opracować znormalizowane protokoły, a organizacje takie jak MEMS & Sensors Industry Group promują wytyczne dotyczące powszechnej akceptacji standardów niezawodności termo-mechanicznej.
Ogólnie rzecz biorąc, trajektoria testowania niezawodności termo-mechanicznej w urządzeniach przekaźników MEM dąży w kierunku bardziej przewidywalnych, bogatych w dane metodologii, które przyspieszają wykrywanie awarii i kwalifikację — co jest niezbędne do spełnienia rygorystycznych wymagań nowej generacji elektroniki w sektorach motoryzacyjnym, przemysłowym i lotniczym.
Postępy w naukach materiałowych wpływające na trwałość przekaźników MEMS
Niezawodność termo-mechaniczna urządzeń przekaźników (MEMS) jest ściśle związana z postępami w naukach materiałowych, szczególnie w miarę jak te urządzenia stają wobec coraz surowszych wymagań operacyjnych i środowiskowych w 2025 roku i w nadchodzących latach. Przekaźniki MEMS, które polegają na deformacji i ruchu struktur na mikroskalę do przełączania, są podatne na mechanizmy awarii, takie jak przyleganie, zmęczenie, pełzanie i zużycie, z których wszystkie są pogarszane przez termiczne i mechaniczne cykle. W związku z tym rygorystyczne testowanie niezawodności termo-mechanicznej stało się punktem centralnym zarówno w środowisku akademickim, jak i przemysłowym.
Ostatnie osiągnięcia w zakresie osadzania cienkowarstwowego i inżynierii powierzchni doprowadziły do użycia wytrzymałych materiałów, takich jak tungsten, ruthenium i węglik krzemu, w stykach przekaźników i elementach strukturalnych. Materiały te charakteryzują się wysokimi temperaturami topnienia, niskim przyleganiem oraz doskonałą odpornością na elektromigrację i utlenianie, co jest krytycznym czynnikiem podczas wysokotemperaturowych cykli i przedłużonej aktywacji. Na przykład, Coventor (firma z grupy Lam Research) podkreśla integrację zaawansowanych materiałów z predykcyjnym modelowaniem metodą elementów skończonych w celu symulacji i testowania trwałości urządzeń MEMS pod wpływem skojarzonych stresów termicznych i mechanicznych.
Aby sprostać wyzwaniu powtarzalnych cykli, producenci coraz częściej stosują zautomatyzowane protokoły przyspieszonego testowania żywotności. Protokoły te narażają przekaźniki MEMS na miliony, a nawet miliardy cykli aktywacji w podwyższonych temperaturach, często w zakresie od -40°C do 150°C, aby symulować dziesięciolecia życia operacyjnego w skondensowanych ramach czasowych. Dane z Teledyne — uznanego dostawcy przekaźników MEMS — pokazują znaczenie takich testów, ukazując, że zoptymalizowane układy materiałowe mogą prowadzić do przekaźników o wartościach średniego czasu do awarii (MTTF) przekraczających 1010 cykli w trudnych warunkach termicznych.
Patrząc w przyszłość, rosnące przyjęcie przekaźników MEMS w sektorach motoryzacyjnym, lotniczym i telekomunikacyjnym — gdzie urządzenia są narażone na agresywne warunki — z pewnością napędzi dalszą innowacyjność w materiałach i testach niezawodności. Organizacje branżowe takie jak MEMS & Sensors Industry Group aktywnie wspierają współpracę między dostawcami materiałów, producentami urządzeń a dostawcami sprzętu testowego w celu ustandaryzowania punktów odniesienia dla niezawodności termo-mechanicznej dla przekaźników MEMS nowej generacji.
Podsumowując, w miarę jak zakres operacyjny przekaźników MEMS się rozszerza, oczekuje się, że postępy w materiałach i bardziej zaawansowane metodologie testowania niezawodności termo-mechanicznej odegrają kluczową rolę w zapewnieniu trwałości urządzeń, a solidne, ustandaryzowane testy staną się coraz bardziej krytyczne do 2025 roku i później.
Wiodące firmy i współprace w branży
Rosnące przyjęcie mikroelektromechanicznych systemów (MEMS) w motoryzacji, lotnictwie i zastosowaniach przemysłowych przyspieszyło zapotrzebowanie na solidne testy niezawodności termo-mechanicznej. W 2025 roku wiodący producenci przekaźników MEMS oraz organizacje badawcze wciąż priorytetowo traktują wysiłki na rzecz współpracy, aby zapewnić długowieczność urządzeń w warunkach łączonych obciążeń termicznych i mechanicznych.
Jednym z czołowych graczy w branży, CANTIMEMS, zainwestowało w kompleksowe protokoły niezawodności, które symulują rzeczywiste scenariusze cyklów termicznych i wibracyjnych dla swoich produktów przekaźników MEMS. Ich opublikowana dokumentacja techniczna szczegółowo opisuje analizy wewnętrznych naprężeń i przyspieszone testy żywotności, zapewniając przejrzystość dla klientów z branży motoryzacyjnej i przemysłowej, którzy szukają rozwiązań do niezawodnego przełączania.
Innym znaczącym uczestnikiem, OMRON Corporation, stworzyła wewnętrzne obiekty testowe, w których przekaźniki MEMS poddawane są testom żywotności w wysokich temperaturach (HTOL) oraz wstrząsom mechanicznym. Dane dotyczące niezawodności OMRON, przedstawione w ich najnowszych specyfikacjach produktów, demonstrują ciągłe poprawy w stabilności oporu styku i wytrzymałości przełączania, nawet po wyczerpujących cyklach obciążeń termo-mechanicznych.
Wspólne wysiłki są również wyraźne. STMicroelectronics aktywnie współpracuje z producentami samochodów i dostawcami Tier 1, aby opracować ustandaryzowane protokoły niezawodności dostosowane do trudnych warunków pracy pojazdów elektrycznych. Te partnerstwa doprowadziły do wdrożenia wspólnych programów kwalifikacyjnych, gwarantujących, że komponenty przekaźników MEMS spełniają lub przewyższają wymagania klasy motoryzacyjnej.
Organizacje branżowe, takie jak SEMI, odgrywają kluczową rolę, ułatwiając grupy robocze skupione na standardach niezawodności urządzeń MEMS. W 2025 roku Grupa Branżowa MEMS oraz Czujników SEMI przewodzi inicjatywom mającym na celu harmonizację metod testowych termo-mechanicznych, zachęcając do wymiany danych wśród członków, aby przyspieszyć kwalifikację urządzeń i skrócić czas wprowadzenia na rynek.
Patrząc w przyszłość, dalsze współprace oczekiwane są w zakresie monitorowania w czasie rzeczywistym wydajności przekaźników MEMS podczas testów niezawodności, wykorzystując zaawansowane czujniki zwrotne i analizy danych oparte na AI. Oczekuje się, że te postępy będą pilotowane przez konsorcja z udziałem wiodących graczy, takich jak Bosch oraz TE Connectivity, mając na celu umożliwienie przewidywalnego utrzymania i przedłużenia czasów życia przekaźników w krytycznych zastosowaniach.
Ogólnie rzecz biorąc, rok 2025 oznacza okres intensyfikacji wspólnych działań wśród producentów, OEM i organizacji normalizacyjnych. Ta ekosystem współpracy ma za zadanie napędzać dalszą innowacyjność w niezawodności termo-mechanicznej, budując zaufanie klientów i torując drogę do szerszego wdrożenia przekaźników MEMS w rozwijających się sektorach.
Wyzwania: Mechanizmy awarii i wąskie gardła niezawodności
Testowanie niezawodności termo-mechanicznej jest kluczowym aspektem rozwoju i kwalifikacji urządzeń przekaźników mikroelektromechanicznych (MEM Relays), ponieważ te komponenty są coraz częściej wdrażane w wymagających środowiskach, takich jak motoryzacja, lotnictwo i zastosowania przemysłowe. Główne wyzwania wynikają ze złożonej interakcji cykli termicznych, stresu mechanicznego i zmęczenia materiału, które łącznie wpływają na trwałość urządzenia oraz integralność operacyjną.
Na rok 2025 główne mechanizmy awarii obserwowane w urządzeniach przekaźników MEM obejmują przyleganie (przyczepność powierzchni styku), zużycie mechaniczne, pękanie wywołane stresem termicznym oraz degradację kontaktów spowodowaną mikro-spawaniem lub korozją trących. Na przykład, przyleganie pozostaje trwałym wyzwaniem, szczególnie w podwyższonych temperaturach i w warunkach wilgotności, które mogą degradują wydajność aktywacji przekaźnika w czasie. Liderzy branżowi tacy jak Coventor i STMicroelectronics raportowali, że nawet drobne zanieczyszczenia powierzchni czy różnice w geometrii styku mogą znacznie przyspieszyć przyleganie i zwiększyć współczynniki awarii przełączania.
Zużycie mechaniczne jest zaostrzane przez powtarzające się cykle, zwłaszcza w zastosowaniach z wysoką częstotliwością przełączania. Ciągła aktywacja ramion przekaźnika MEM może prowadzić do zmęczenia mikrostrukturalnego, co ostatecznie prowadzi do pęknięć lub trwałej deformacji. Cykle termiczne, powszechnie symulowane w testach niezawodności w zakresie od -40°C do +125°C, mogą wywołać niezgodności rozprężania i kurczenia się materiałów między różnymi warstwami lub interfejsami, prowadząc do delaminacji lub pękania. Texas Instruments podkreśla znaczenie solidnych rozwiązań pakujących oraz struktur łagodzących stres w celu ograniczenia pękania i delaminacji w ramach przyspieszonych protokołów testów termicznych.
Degradacja kontaktów, szczególnie na styku metalowym, stanowi kolejne krytyczne wąskie gardło. Mikro-spawanie może wystąpić z powodu wysokich gęstości prądowych podczas przełączania, podczas gdy korozja trąca jest przyspieszana przez narażenie na środowisko i wibracje mechaniczne. Problemy te mogą powodować zwiększenie oporu styku, interwały przerw w obwodzie, czy nawet katastrofalne awarie. Zgodnie z badaniami Analog Devices, trwające badania koncentrują się na zaawansowanych materiałach stykowych, takich jak stopy metali szlachetnych oraz inżynierowane powłoki powierzchniowe, aby przedłużyć trwałość urządzeń i przeciwdziałać degradacji środowiskowej.
Patrząc w przyszłość, perspektywy dotyczące testowania niezawodności przekaźników MEM obejmują przyjęcie bardziej złożonych systemów monitorowania w czasie rzeczywistym oraz algorytmów uczenia maszynowego mających na celu przewidywanie wystąpienia awarii na podstawie danych dotyczących wydajności w czasie rzeczywistym. Wysiłki standaryzacyjne prowadzone przez organizacje takie jak konsorcjum SEMI są w toku, aby zharmonizować protokoły testowania żywotności przyspieszonej, odnosząc się do wzrastającej złożoności i różnorodności zastosowań przekaźników MEMS. Przez następne kilka lat możemy spodziewać się integracji analiz predykcyjnych oraz możliwości autodiagnostycznych w modułach przekaźników MEM, co zwiększy zapewnienie niezawodności i zmniejszy awarie w terenie w systemach krytycznych dla misji.
Standardy regulacyjne i protokoły testowe
Testowanie niezawodności termo-mechanicznej dla mikroelektromechanicznych urządzeń przekaźników (MEM relays) staje się coraz bardziej ustandaryzowane, jako że te komponenty są integrowane w krytycznych zastosowaniach w branżach motoryzacyjnych, lotniczych i telekomunikacyjnych. W 2025 roku standardy regulacyjne oraz protokoły napędzane przez branżę ewoluują, aby odpowiadać na unikalne wyzwania, jakie niesie miniaturyzacja i ruchome struktury wewnątrz przekaźników MEMS, które podlegają cyklom temperaturowym, wstrząsom mechanicznym oraz długotrwałym obciążeniom operacyjnym.
Międzynarodowo uznawane standardy, takie jak te z JEDEC Solid State Technology Association oraz Międzynarodowej Komisji Elektrotechnicznej (IEC), stanowią podstawowe ramy dla testowania niezawodności mechanicznej i środowiskowej. Dla urządzeń MEMS, zastosowanie standardów JEDEC JESD22 (w tym wstrząsy mechaniczne, wibracje i cykle temperatury) stało się powszechną praktyką, a dodatkowe protokoły specyficzne dla MEMS są w trakcie opracowywania, aby uchwycić niuanse działania przekaźników. Na przykład seria IEC 60749, która dotyczy niezawodności półprzewodników, jest często dostosowywana przez producentów w celu rozszerzenia jej dotyczących przekaźników MEMS.
Wiodący producenci przekaźników MEMS, tacy jak MEMSIC oraz Cantilever Sensors, aktywnie uczestniczą w definiowaniu i doskonaleniu tych protokołów testowych, zapewniając, że metodologie testów odzwierciedlają rzeczywiste scenariusze zastosowań. Ich opublikowane dane dotyczące niezawodności często zawierają wyniki z przyspieszonych testów żywotności — cyklów temperaturowych między -40°C a +125°C, ocen żywotności w wysokiej temperaturze (HTOL) oraz wytrzymałości na aktywację mechaniczną przekraczającą miliard cykli, co zostało potwierdzone w ich dokumentacji technicznej.
Wymagania sektora motoryzacyjnego, określone przez Automotive Industry Action Group (AIAG) i szczegółowo opisane w standardach AEC-Q100, są rozszerzane na urządzenia przekaźników MEMS, co zmusza dostawców do przyjęcia rygorystycznych procesów kwalifikacji. Oprócz testów stresowych mechanicznych i environmentalnych, producenci integrują protokoły analizy awarii, takie jak mikroskopia elektronowa i monitorowanie in-situ, aby zidentyfikować mechanizmy awarii unikalnych dla architektur przekaźników MEMS.
Patrząc w przyszłość przez następne kilka lat, przewiduje się, że organy regulacyjne i konsorcja branżowe będą dążyć do dalszej harmonizacji testowania niezawodności przekaźników MEM z szerszymi standardami urządzeń półprzewodnikowych, wprowadzając przy tym specyficzne poprawki do standardów MEMS. Oczekuje się, że wzrost technik cyfrowego bliźniaka oraz uczenia maszynowego dla predykcyjnego modelowania niezawodności również wpłynie na przyszły rozwój protokołów. Współpraca między organizacjami standardyzacyjnymi a wytwórniami MEMS będzie kluczowa, aby zapewnić, że testowanie niezawodności rozwija się równolegle z złożonością urządzeń i wymaganiami rynkowymi.
Studia przypadków: Przełomy od wiodących producentów MEMS
Testowanie niezawodności termo-mechanicznej jest kluczowym procesem w kwalifikacji i masowym wdrażaniu urządzeń przekaźników mikroelektromechanicznych (MEMS relay), a wiodący producenci MEMS wprowadzają nowe metodologie i raportują znaczące przełomy w 2025 roku. Ta sekcja bada ostatnie osiągnięcia i studia przypadków od czołowych graczy branżowych, koncentrując się na wydajności w rzeczywistych warunkach, protokołach testowania przyspieszonego oraz spostrzeżeniach dotyczących przyszłych kierunków rozwoju.
Jednym z godnych uwagi przykładów jest CANTIME MEMS, które na początku 2025 roku ogłosiło pomyślną kwalifikację swoich przekaźników MEMS nowej generacji dla wysokiej niezawodności w automatyzacji przemysłowej i zastosowaniach motoryzacyjnych. Ich podejście opierało się na zestawie przyspieszonych testów żywotności, obejmujących cykle temperaturowe między -40°C a +125°C oraz wstrząsy mechaniczne o wysokiej G. CANTIME MEMS informuje, że ich przekaźniki konsekwentnie przekraczają standardy branżowe dotyczące stabilności oporu kontaktowego i wytrzymują ponad 109 cykli przełączania bez mierzalnej degradacji, podkreślając solidne pakowanie i metalurgię kontaktów jako kluczowe czynniki.
Podobnie, Teledyne podkreśliło nowe protokoły niezawodności dla swoich produktów przekaźników opartych na MEMS. W 2025 roku Teledyne wdrożyło zaawansowane monitorowanie in-situ podczas testów wstrząsów termicznych i wibracji, co umożliwiło wykrywanie w czasie rzeczywistym zjawisk zmęczenia mechanicznego oraz przylegania. Ich przekaźniki MEMS, zaprojektowane dla lotnictwa i obrony, przeszły rygorystyczne testy cykli temperaturowych zgodnych z JEDEC i testy obciążeń mechanicznych, osiągając wartości MTTF przekraczające 10 lat w ramach standardowych profili misji typowych dla systemów satelitarnych i awioniki.
Tymczasem Uniwersytet Carnegie Mellon we współpracy z Qorvo zrealizował badania dotyczące niezawodności mikroelektromechanicznych przekaźników do przełączania RF. W 2025 roku ich wspólne studium przypadku wykazało, że nowe techniki hermetycznej obudowy oraz podłoża o niskim współczynniku rozszerzalności termicznej mogą zmniejszyć koncentrację stresu mechanicznego podczas cykli temperaturowych, co skutkuje poprawą trwałości urządzeń oraz niższymi współczynnikami awarii w przypadku powtarzających się cykli zasilania i analiz środowiskowych.
Patrząc w przyszłość, producenci MEMS aktywnie rozwijają modele cyfrowych bliźniaków oraz predykcyjne analizy oparte na AI, aby jeszcze bardziej zwiększyć oceny niezawodności, dążąc do przyspieszenia cykli kwalifikacji oraz przewidywania mechanizmów awarii przed badaniami fizycznymi. W miarę jak przekaźniki MEMS są coraz szerzej przyjmowane w sektorach motoryzacyjnym, przemysłowym oraz komunikacyjnym, prognozy na 2025 rok i później obejmują rozszerzone wykorzystanie testowania profilu misji w rzeczywistych warunkach, szersze wdrażanie w systemach krytycznych dotyczących bezpieczeństwa oraz kontynuację współpracy między liderami branży a instytucjami badawczymi w celu ustalenia nowych standardów w zakresie niezawodności termo-mechanicznej.
Mapa przyszłości: Rozwiązania z zakresu niezawodności nowej generacji i wpływ na rynek
Testowanie niezawodności termo-mechanicznej dla urządzeń przekaźników mikroelektromechanicznych (MEM relay) wchodzi w kluczową fazę, ponieważ branża wymaga wyższej wytrzymałości, dłuższych czasów pracy i szerszego wdrożenia w krytycznych urządzeniach elektronicznych. W 2025 roku kilku wiodących producentów przekaźników MEMS oraz konsorcjów półprzewodnikowych intensyfikuje wysiłki w celu opracowania zaawansowanych protokołów testowych i predykcyjnych modeli niezawodności, które odpowiadają unikalnym wyzwaniom tych systemów elektromechanicznych.
Centralnym punktem uwagi w 2025 roku jest integracja szybkich i w czasie rzeczywistym testów niezawodności, które uchwycą zarówno efekty cykli termicznych, jak i aktywacji mechanicznej w rzeczywistych warunkach. Na przykład, Teledyne oraz Cantilever Labs, uznawani za pionierów w rozwoju przekaźników MEM, współpracują z producentami OEM, aby ustandaryzować testowanie żywotności przyspieszonej, które symuluje trudne warunki motoryzacyjne i przemysłowe. Protokóły te narażają urządzenia na tysiące cykli temperaturowych i miliony zdarzeń aktywacji, mierząc dryf oporu stykowego, przyleganie i wskaźniki awarii, aby zapewnić defektywność poniżej ppm.
Równolegle organizacje takie jak Semiconductor Industry Association prowadzą międzybranżowe grupy robocze, aby zharmonizować metryki niezawodności i raportowanie dla przekaźników MEM. Obejmuje to ustanowienie uzgodnionych definicji dla mechanizmów awarii, takich jak spawanie, odbicie oraz mikro-zużycie, oraz wdrażanie zaawansowanych narzędzi metrologicznych do kwantyfikacji deformacji poniżej mikrometra podczas testów. Takie inicjatywy są kluczowe, ponieważ przekaźniki MEM są coraz bardziej integrowane w systemy bezpieczeństwa motoryzacyjnego, infrastrukturze 5G oraz nowoczesnych urządzeniach medycznych, gdzie niezawodność na poziomie zerowych wad jest niezbędna.
Na froncie technologicznym pojawiają się nowe rozwiązania, aby zaspokoić ograniczenia tradycyjnych testerów wstrząsów termicznych i zmęczenia mechanicznego. Kistler i Keysight Technologies wprowadzają modułowe, wysoko wrażliwe platformy testowe, które łączą monitorowanie elektryczne w czasie rzeczywistym z czujnikami siły/przesunięcia na poziomie nano. To umożliwia przewidywalne utrzymanie i analizę przyczyn pierwotnych, znacząco skracając cykle rozwojowe dla producentów przekaźników MEM.
Patrząc w przyszłość przez najbliższe lata, mapa przyszłości wskazuje na większe przyjęcie cyfrowych bliźniaków oraz analiz opartych na AI do oceny niezawodności. Firmy takie jak Texas Instruments inwestują w środowiska symulacyjne, które odzwierciedlają skojarzone zachowanie termiczne i mechaniczne przekaźników MEM w różnych scenariuszach zastosowania, co umożliwia kwalifikację wirtualną i szybsze czasy wprowadzania na rynek.
Podsumowując, sektor znajduje się na krawędzi znacznej transformacji w testowaniu niezawodności termo-mechanicznej dla urządzeń przekaźników MEM. Zbieżność zaawansowanego sprzętu, znormalizowanych ram testowych oraz ulepszonych analiz opartych na AI ma dostarczyć bezprecedensowego poziomu zapewnienia jakości, torując drogę do szerszej penetracji rynku w zastosowaniach krytycznych i wysokowydajnych.
Źródła i odniesienia
- Teledyne
- Teledyne
- JEDEC Solid State Technology Association
- IEEE
- Coto Technology
- Rohde & Schwarz
- NXP Semiconductors
- STMicroelectronics
- Texas Instruments
- Bosch Sensortec
- Bosch
- Analog Devices
- MEMSIC
- Automotive Industry Action Group
- Carnegie Mellon University
- Cantilever Labs
- Semiconductor Industry Association