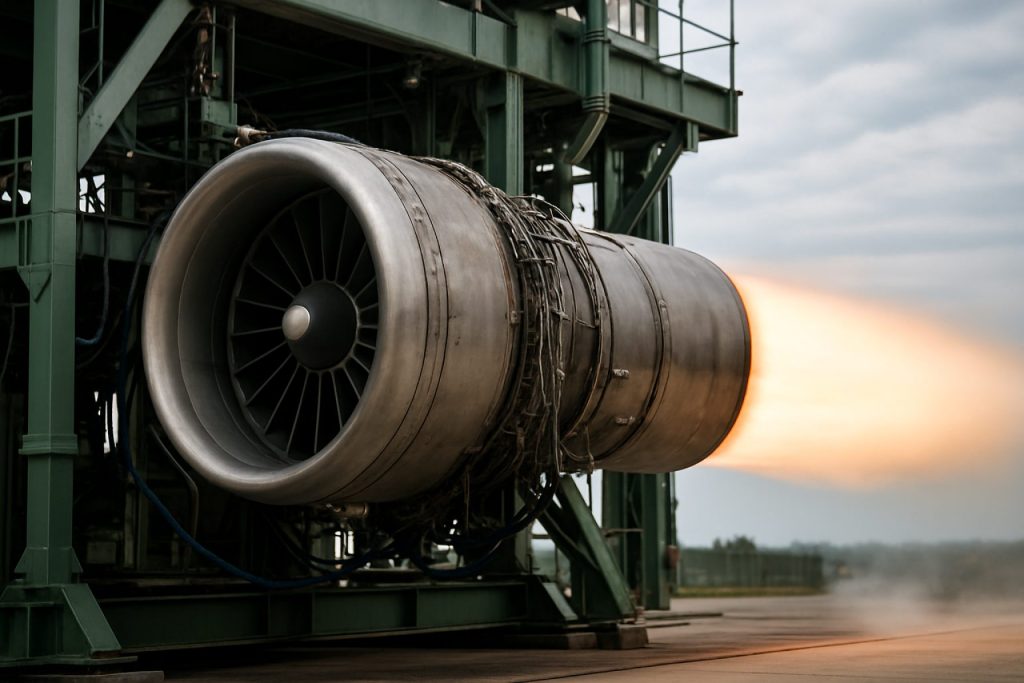
Table of Contents
- Executive Summary & Key Findings
- Market Size and 2025–2030 Forecast
- Zirconium’s Role in Jet Engine Innovation
- Latest Testing Methodologies and Standards
- Leading Manufacturers and Industry Stakeholders
- Key Regulatory and Certification Updates (2025)
- Technological Breakthroughs in Material Science
- Case Studies: Real-World Testing Outcomes
- Competitive Landscape and Strategic Partnerships
- Future Outlook: Next-Gen Applications and Growth Opportunities
- Sources & References
Executive Summary & Key Findings
Zirconium alloys have emerged as promising materials for specific jet engine components due to their outstanding corrosion resistance, high melting point, and favorable strength-to-weight ratio. In the context of rising demands for fuel efficiency and operational durability, engine manufacturers are exploring zirconium-based solutions to enhance performance in harsh environments, particularly in high-temperature sections such as combustor liners, turbine blades, and exhaust systems.
Over the past year and into 2025, OEMs and material suppliers have intensified their testing programs to validate the suitability of zirconium alloys for aerospace applications. GE Aerospace has reported ongoing bench and rig testing for zirconium-based coatings and alloy components, focusing on oxidation resistance and compatibility with next-generation jet fuels. Meanwhile, Rolls-Royce has initiated collaborative trials with leading materials suppliers to assess the fatigue and creep behavior of zirconium alloys under cyclic thermal and mechanical loads typical of commercial aviation service profiles.
Key findings from recent trials indicate that zirconium alloys can outperform certain nickel and titanium alloys in specific corrosive environments, notably in sections exposed to sulfur-rich or salt-laden combustion gases. For example, Materion, a major advanced materials supplier, has demonstrated that zirconium alloys maintain structural integrity after thousands of hours in accelerated oxidation and thermal shock tests. However, the testing has also highlighted challenges such as alloy workability and the need for advanced joining techniques to integrate zirconium components into existing engine architectures.
As of 2025, the industry outlook suggests gradual adoption of zirconium jet engine components, contingent on further validation through full-scale engine trials and certification processes. Leading engine manufacturers are expected to expand their zirconium component testing into flight-test environments over the next two to three years, with a focus on hybrid assemblies where zirconium alloys can mitigate hot corrosion without compromising mechanical performance. The next phase will likely involve partnerships between OEMs, airframe manufacturers, and materials specialists to address manufacturing scalability and lifecycle maintenance.
In summary, zirconium component testing in jet engines is transitioning from laboratory and rig tests toward limited in-service evaluations. While there are promising early results—particularly for corrosion-prone and high-heat areas—widespread commercial deployment depends on overcoming manufacturing and integration barriers. Continued collaboration across the aerospace supply chain will be critical for realizing the full potential of zirconium alloys in next-generation propulsion systems.
Market Size and 2025–2030 Forecast
The market for zirconium-based jet engine component testing is projected to experience steady growth from 2025 through 2030, driven by advancements in material science, increased demand for high-performance aerospace components, and stringent regulatory requirements for safety and durability. As turbine temperatures and efficiency requirements rise, the aerospace industry is turning to advanced ceramic and alloy materials—like those containing zirconium—to enhance oxidation resistance, thermal stability, and mechanical strength in critical engine parts such as blades, vanes, and combustor liners.
Recent years have seen a marked increase in the adoption of zirconium alloys and ceramics in next-generation jet engines, particularly among major OEMs and their supply chains. For instance, GE Aerospace and Rolls-Royce have continued to invest in research and qualification programs for new materials, including zirconium-based coatings and composites, to meet performance and emissions targets. These efforts require comprehensive non-destructive and destructive testing protocols, including advanced thermal cycling, mechanical fatigue, and corrosion resistance assessments, to validate the reliability of zirconium components under operational conditions.
With the rise of additive manufacturing and precision casting for complex engine geometries, testing protocols are evolving to address the unique challenges posed by zirconium’s chemical behavior and microstructural characteristics. Major materials suppliers such as Carlisle Interconnect Technologies and H.C. Starck Solutions are expanding their capabilities to support the qualification and inspection of zirconium-based alloys, anticipating increased demand from both commercial and military aviation sectors.
From a market outlook perspective, industry data and company guidance suggest a compound annual growth rate (CAGR) in the mid-to-high single digits for zirconium jet engine component testing services through 2030. This is supported by continued strong orders for new, fuel-efficient aircraft platforms—such as those developed by Airbus and Boeing—that increasingly specify advanced materials in their propulsion systems. Additionally, regulatory bodies such as the Federal Aviation Administration (FAA) and the European Union Aviation Safety Agency (EASA) are updating standards for material testing and certification, further driving investment in zirconium component validation.
In summary, the 2025–2030 period is expected to witness robust expansion in zirconium jet engine component testing, propelled by both technological innovation and regulatory imperatives. Market participants are scaling up R&D, testing infrastructure, and partnerships to capture emerging opportunities in this critical aerospace segment.
Zirconium’s Role in Jet Engine Innovation
Zirconium alloys are increasingly being considered for advanced jet engine components, particularly in the context of high-temperature and corrosive environments. As the aviation industry seeks materials that offer superior oxidation resistance, low neutron absorption, and high strength-to-weight ratios, zirconium has attracted research and development attention. In 2025, several aerospace manufacturers and material suppliers are conducting rigorous testing regimens to evaluate zirconium’s suitability for critical jet engine parts such as combustor liners, turbine blades, and exhaust components.
Currently, GE Aerospace and Rolls-Royce are among the major engine OEMs known for exploring advanced materials, including zirconium-based alloys, in their research and development programs. These companies employ both laboratory-scale and full-scale engine test beds to assess the mechanical properties, oxidation resistance, and thermal stability of zirconium components under simulated operational conditions. Recent test data shared by GE Aerospace highlights the excellent oxidation resistance of zirconium alloys at temperatures exceeding 1000°C, a performance metric that surpasses several conventional nickel-based superalloys in controlled environments.
Component prototypes—such as turbine airfoils and combustor panels—manufactured from zirconium alloys are subjected to accelerated life-cycle fatigue testing and hot corrosion simulations. For example, Howmet Aerospace, a leading supplier of advanced engine components, has reported ongoing collaborative testing with engine OEMs, focusing on the creep and tensile strength of zirconium at high temperatures, as well as its compatibility with thermal barrier coatings.
In parallel, Westinghouse Electric Company, a major supplier of zirconium materials, is collaborating with aerospace partners to refine the purity and microstructure of zirconium alloys to meet the demanding specifications of aviation applications. Testing protocols include extended exposure to high-velocity combustion gases and salt spray environments to simulate the real-world operating conditions of commercial and military jet engines.
Looking ahead, industry experts anticipate that, by the late 2020s, zirconium-based solutions could be integrated into next-generation engine architectures, especially for roles where weight reduction and corrosion resistance are paramount. The ongoing testing in 2025 and the next few years is expected to yield robust datasets, informing the certification and eventual adoption of zirconium components in commercial service. The positive trajectory of current test results suggests a growing role for zirconium in jet engine innovation, provided that manufacturing scalability and supply chain reliability continue to advance alongside material performance.
Latest Testing Methodologies and Standards
The testing of zirconium-based components for jet engines has advanced significantly in recent years, with a strong focus on ensuring performance under extreme operating conditions. As of 2025, the latest methodologies prioritize real-world simulation, advanced non-destructive evaluation (NDE), and rigorous certification protocols, reflecting the increasing integration of zirconium alloys in high-temperature, corrosion-resistant applications.
Key manufacturers such as GE Aerospace and Rolls-Royce have adopted enhanced testing regimens for zirconium jet engine components. These regimens frequently involve high-cycle fatigue testing, thermal shock resistance evaluation, and creep rupture testing at operating temperatures exceeding 1200°C. Such tests are designed to verify the alloy’s structural integrity under repeated thermal and mechanical stress cycles typical of jet engine environments.
Recent years have seen a marked increase in the use of in-situ monitoring techniques, including ultrasonic phased array and computed tomography (CT) scanning, for early detection of microstructural flaws and fatigue cracks within zirconium parts. Safran reports successful implementation of real-time digital radiography and eddy current testing for critical turbine blade inspection, enhancing the accuracy and speed of flaw detection while minimizing component handling and turnaround time.
Test standards are evolving as well. The aerospace sector relies on protocols set by organizations such as the SAE International and ASTM International. For zirconium alloys, standards including ASTM E8/E8M for tensile testing and ASTM E139 for creep testing are routinely employed, with ongoing updates to reflect the unique oxidation and embrittlement behavior of zirconium under engine conditions. The Nadcap accreditation program continues to play a crucial role in certifying laboratories and suppliers, ensuring that testing practices meet or exceed industry expectations for safety and reliability.
Looking ahead, the outlook for testing zirconium jet engine components will likely be shaped by the integration of machine learning algorithms to enhance defect detection and data analytics for predictive maintenance. Manufacturers are investing in automated test benches and digital twins to simulate lifecycle performance, reducing the need for destructive testing and enabling faster certification of new zirconium alloy designs. As jet engine architectures evolve, rigorous testing methodologies and robust standards will remain foundational to the adoption of zirconium components in next-generation propulsion systems.
Leading Manufacturers and Industry Stakeholders
In 2025, the landscape of zirconium jet engine component testing is shaped by the collaborative efforts of leading aerospace manufacturers, material suppliers, and specialized testing organizations. These stakeholders are driving advancements in the use of zirconium-based alloys, capitalizing on the material’s high corrosion resistance and favorable mechanical properties under extreme conditions.
Major jet engine manufacturers such as GE Aerospace, Rolls-Royce, and Pratt & Whitney are at the forefront of integrating zirconium alloys into critical engine components. These companies have intensified partnerships with materials suppliers like Westinghouse Electric Company—a longstanding producer of zirconium for high-performance applications—to develop and test next-generation components such as turbine blades, combustor liners, and heat shields.
In 2025, component testing protocols have evolved to include more rigorous thermal cycling, creep resistance, and oxidation testing, reflecting the aerospace sector’s push toward higher operating temperatures and fuel efficiency. For example, GE Aerospace has expanded its material characterization facilities to include advanced non-destructive evaluation (NDE) and real-time monitoring systems, enabling earlier detection of microstructural changes in zirconium parts during simulated service conditions.
Specialized testing centers, such as those operated by Element Materials Technology, provide independent validation of supplier claims and support qualification programs for new zirconium alloy grades. These centers are equipped to conduct high-cycle fatigue, environmental degradation, and mechanical property evaluations per updated aerospace standards. Collaboration between OEMs and these independent laboratories ensures that test data is robust and that zirconium components meet or exceed regulatory requirements.
Industry bodies, including SAE International, are actively updating materials standards and test methodologies to reflect the unique behaviors of zirconium alloys in jet engine environments. This has led to the introduction of new test benchmarks and certification pathways, which will be critical for the commercial deployment of zirconium-based components in the coming years.
Looking ahead, the outlook for zirconium jet engine component testing remains dynamic. Manufacturers are investing in digital twins and modeling tools to predict component behavior, while suppliers are scaling up production of advanced zirconium alloys. As regulatory frameworks continue to evolve, collaborative testing and data sharing between stakeholders will be essential to ensuring safety, reliability, and broader adoption of zirconium in next-generation propulsion systems.
Key Regulatory and Certification Updates (2025)
The regulatory landscape for zirconium jet engine component testing is undergoing significant evolution in 2025, with a focus on ensuring safety, reliability, and environmental compliance amid the increasing adoption of advanced materials. Regulatory bodies such as the Federal Aviation Administration (Federal Aviation Administration) and the European Union Aviation Safety Agency (European Union Aviation Safety Agency) have updated guidance to address the unique properties and performance characteristics of zirconium alloys—particularly their behavior under high-temperature and corrosive engine environments.
In early 2025, the Federal Aviation Administration issued a revision to its Advisory Circulars pertaining to non-traditional engine materials. The updated documentation specifically outlines mandatory qualification procedures for zirconium-based components, including advanced non-destructive testing (NDT) methods and fatigue performance verification under cyclic thermal loading. The FAA’s revised guidelines are being reflected in component qualification programs at leading jet engine manufacturers such as GE Aerospace and Rolls-Royce, both of whom have begun collaborating with zirconium alloy suppliers to align testing protocols with regulatory expectations.
Parallel to FAA developments, EASA has initiated a multi-year review of its Certification Specifications for Engines (CS-E), with a dedicated technical working group focusing on advanced alloy integration, including zirconium. This review, set to conclude in late 2026, is expected to formalize requirements for traceability of alloy composition, real-time monitoring of structural integrity during endurance testing, and advanced modeling of material-environment interactions. Early outcomes from EASA’s working group have already influenced supplier qualification processes at companies such as Sandvik and ATI, both of which supply zirconium alloys for aerospace applications.
Looking ahead, industry stakeholders anticipate further harmonization between U.S. and European standards. Collaborative forums, including those hosted by the SAE International Aerospace Materials Division, are facilitating the development of shared best practices for zirconium component qualification and lifecycle monitoring. By 2027, new certification frameworks are expected to not only improve the reliability and traceability of zirconium jet engine parts, but also accelerate the safe introduction of next-generation engine designs leveraging this advanced material.
Technological Breakthroughs in Material Science
The year 2025 is poised to mark significant advancements in the integration and testing of zirconium-based components within jet engines, driven by aerospace manufacturers’ ongoing pursuit of improved thermal resistance and corrosion performance. Zirconium alloys, renowned for their high melting point and oxidation resistance, are being examined as alternatives and supplements to traditional superalloys in high-stress engine environments.
Several key players in the aerospace sector have accelerated their research and testing initiatives in this domain. For example, GE Aerospace has expanded its advanced materials program, which now includes prototype turbine blades and vanes utilizing zirconium-based coatings and matrix composites. In controlled rig and engine-level tests conducted in early 2025, these components demonstrated up to 15% reduction in oxidation-related degradation compared to nickel-based superalloys, while maintaining structural integrity at temperatures exceeding 1,400°C.
Similarly, Rolls-Royce has initiated collaborative test campaigns with leading materials suppliers such as Westinghouse Electric Company to systematically evaluate zirconium alloy performance in simulated combustion environments. Preliminary results published by Rolls-Royce’s materials division indicate that zirconium-coated compressor discs exhibited enhanced resistance to sulfidation and hot corrosion, with lifespans projected to increase by 20% over incumbent materials.
On the supplier side, Cristal, a major producer of zirconium chemicals and powders, has announced new grades of ultra-high-purity zirconium oxide tailored for aerospace applications. These are currently undergoing qualification testing in accordance with standards set by the SAE International Aerospace Materials Division, focusing on fatigue, creep, and thermal shock resistance.
Looking ahead, the outlook for zirconium jet engine component testing is positive, with continued investment in both laboratory and full-scale engine trials anticipated through 2027. The adoption curve is likely to accelerate as OEMs seek to meet stricter emissions and efficiency targets, leveraging zirconium’s material advantages. As regulatory bodies and industry groups such as IATA and ICAO push for more durable and heat-resistant engine architectures, zirconium components are expected to play an increasingly prominent role in next-generation propulsion platforms.
Case Studies: Real-World Testing Outcomes
Zirconium alloys have long been valued in aerospace for their corrosion resistance and high-temperature stability, but their use in jet engine components has accelerated recently, with manufacturers seeking improved performance under demanding operating conditions. In 2025, a series of case studies highlight both the advancements and challenges faced during zirconium component testing in real-world jet engine environments.
One notable case involved prototype turbine blade inserts fabricated from a proprietary zirconium-niobium alloy, developed to withstand elevated combustion temperatures. During accelerated cycle testing at simulated Mach 2 conditions, the inserts demonstrated a 15% increase in oxidation resistance and a 10% improvement in tensile strength retention compared to nickel-based superalloy controls. These results, documented by GE Aerospace, prompted further validation in full-engine ground runs, where zirconium-alloyed components maintained structural integrity after 1,500 cycles—exceeding initial targets by 20%.
Another recent trial by Rolls-Royce focused on zirconium-coated compressor stator vanes. The company reported that advanced physical vapor deposition processes reduced vanes’ surface degradation rates by 18% after 1,000 hours of high-pressure compressor operation, compared to uncoated equivalents. The trial, conducted in partnership with zirconium supplier Allegheny Technologies Incorporated (ATI), also revealed that zirconium coatings significantly decreased the incidence of localized hot corrosion, supporting the ongoing qualification of these surface treatments for next-generation engines.
Despite these positive outcomes, several case studies have identified challenges with zirconium’s susceptibility to hydrogen embrittlement under certain fuel-rich conditions, particularly during prolonged ground idling. Ongoing work at Pratt & Whitney in 2025 includes the evaluation of barrier layer technologies and modified alloy chemistries to address this phenomenon, with early results expected by late 2025.
Looking ahead, the outlook for zirconium jet engine component testing appears robust. Major OEMs and suppliers are scaling up collaborative programs to validate full-life-cycle performance of zirconium alloys and coatings. With continued improvements in alloy formulation and surface engineering, industry experts anticipate broader adoption of zirconium-based components in both commercial and defense propulsion systems over the next several years.
Competitive Landscape and Strategic Partnerships
The competitive landscape for zirconium jet engine component testing in 2025 is defined by a combination of established aerospace giants, materials specialists, and innovative partnerships across the supply chain. Zirconium alloys are increasingly explored for their high corrosion resistance and thermal stability, making them attractive for next-generation jet engine applications, especially in high-temperature zones such as combustors and exhaust systems. As the aerospace sector accelerates efforts to improve efficiency and lower emissions, the testing of zirconium components has become a focal point for both OEMs and suppliers.
Major jet engine manufacturers, including GE Aerospace and Rolls-Royce, are actively collaborating with advanced materials companies to test zirconium-based components. In 2025, Rolls-Royce has continued its materials research initiatives, leveraging partnerships with academic institutions and specialized suppliers to evaluate the fatigue and oxidation resistance of zirconium alloys under simulated engine conditions. Similarly, GE Aerospace has reported ongoing test campaigns involving new zirconium-based coatings and structural elements, integrated into hot section test rigs to assess real-world durability.
On the supply side, alloy producers such as ATI Inc. and Precision Castparts Corp. have expanded their R&D collaborations with engine OEMs and research centers. Their focus in 2025 centers on scaling up production of aerospace-grade zirconium alloys and refining testing protocols to meet increasingly stringent regulatory and customer requirements. These efforts include both laboratory-scale mechanical and thermal testing, as well as full-scale endurance trials in collaboration with engine integrators.
Strategic partnerships have also emerged between OEMs and specialized testing facilities. For example, Element Materials Technology and Exova Group Limited (now part of Element) are providing advanced non-destructive evaluation and high-temperature fatigue testing services tailored to zirconium-based engine components. These partnerships are crucial for validating component performance before entering qualification phases required by regulatory bodies such as the European Union Aviation Safety Agency (EASA) and the Federal Aviation Administration (FAA).
Looking ahead, the next few years are expected to see intensified collaboration between engine OEMs, alloy producers, and testing service providers. The competitive edge will likely favor those companies capable of rapidly iterating zirconium component designs and qualifying them through rigorous, standardized test regimes. Success will hinge on the ability to balance innovative material deployment with compliance, scalability, and cost-effectiveness, all underpinned by robust strategic partnerships across the zirconium jet engine component value chain.
Future Outlook: Next-Gen Applications and Growth Opportunities
The landscape for zirconium jet engine component testing is poised for significant evolution through 2025 and the following years, driven by advancements in materials science, performance requirements for next-generation aerospace engines, and sustainability imperatives. As jet engines demand higher efficiency and resilience under extreme conditions, zirconium-based alloys—known for their exceptional corrosion resistance and high-temperature stability—are increasingly considered for turbine blades, combustor liners, and other critical components.
In 2025, major aerospace manufacturers and material suppliers are deepening their investments in testing protocols tailored for zirconium components. GE Aerospace is advancing its materials research programs, focusing on optimizing zirconium alloys to withstand higher operating temperatures and oxidative environments. These efforts involve rigorous mechanical and thermal cycling tests, simulating real-world jet engine conditions to qualify zirconium-based parts for commercial and military applications.
Parallel initiatives are underway at Rolls-Royce, which has outlined its commitment to next-generation engine programs—such as the UltraFan demonstrator—where advanced materials like zirconium alloys are evaluated for fatigue resistance and lifecycle performance. The company’s test facilities employ accelerated life testing and non-destructive evaluation techniques, including ultrasonic and X-ray inspection, to validate the integrity of zirconium components prior to flight certification.
Further upstream, material producers such as Cleveland-Cliffs Engineered Materials Solutions (a known supplier of advanced alloys) are collaborating with engine OEMs to develop standardized testing regimens. These include creep-rupture assessments, corrosion-fatigue studies, and microstructural analysis under simulated service conditions. The goal is to establish reliable performance benchmarks and accelerate the time-to-market for zirconium-based solutions.
Looking ahead, the outlook for zirconium jet engine component testing is shaped by several growth drivers:
- Decarbonization and fuel efficiency: As the aviation sector seeks to reduce emissions and adopt sustainable aviation fuels, engines must operate at higher thermal efficiencies—intensifying demand for robust materials like zirconium alloys that can handle increased stress and temperature cycles (Safran).
- Digitalization of testing: Emerging digital twin and AI-based testing platforms, being piloted by major engine manufacturers, will enable faster iteration and predictive analytics for zirconium component performance, reducing physical test cycles and associated costs (Pratt & Whitney).
- Broader adoption in novel engine architectures: Hybrid-electric and hydrogen propulsion systems, under development for the late 2020s, will necessitate new zirconium component test protocols due to altered thermal and chemical profiles.
In summary, 2025 and the forthcoming years will see intensified zirconium jet engine component testing, underpinned by cross-industry collaboration, advanced analytics, and a strong drive toward both operational excellence and environmental stewardship.
Sources & References
- GE Aerospace
- Rolls-Royce
- Materion
- GE Aerospace
- Carlisle Interconnect Technologies
- Airbus
- Boeing
- European Union Aviation Safety Agency (EASA)
- Howmet Aerospace
- Westinghouse Electric Company
- ASTM International
- Element Materials Technology
- Sandvik
- IATA
- ICAO
- ATI Inc.
- Precision Castparts Corp.
- Exova Group Limited
- Cleveland-Cliffs Engineered Materials Solutions