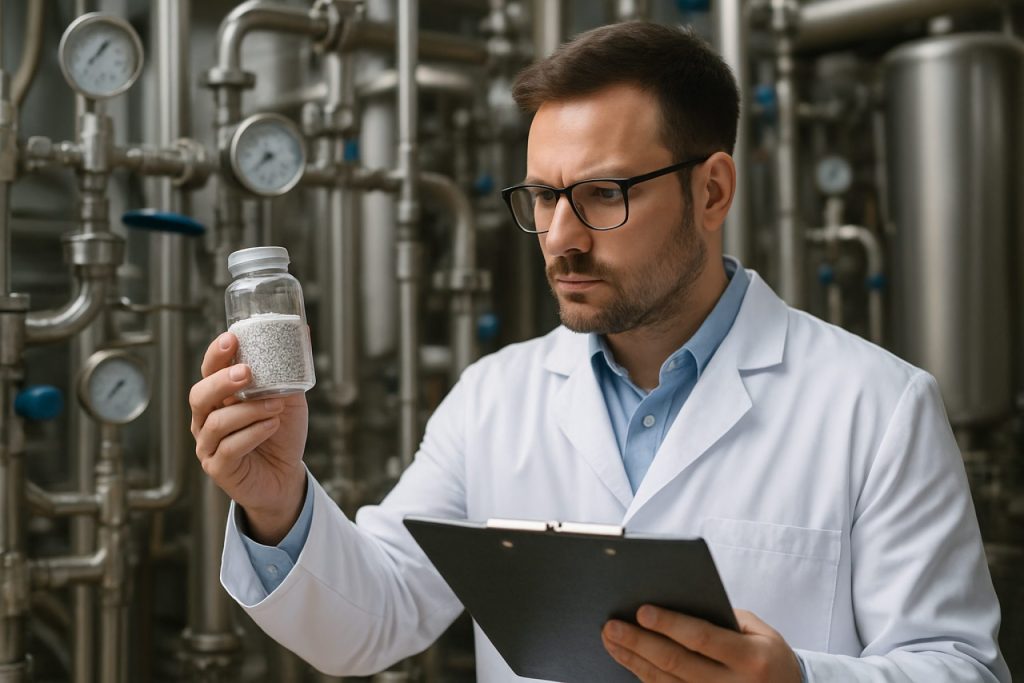
Zeolite Catalysis in Industrial Gas Purification: 2025’s Game-Changer and the Road Ahead. Explore How Advanced Zeolite Technologies Are Redefining Clean Gas Solutions and Driving Double-Digit Growth.
- Executive Summary: Zeolite Catalysis Market in 2025
- Industry Overview: Zeolite Catalysts in Gas Purification
- Key Players and Strategic Initiatives (e.g., basf.com, honeywell.com, zeochem.com)
- Market Size, Segmentation, and 2025–2030 Growth Forecasts (Estimated CAGR: 11–13%)
- Technological Innovations: Next-Gen Zeolite Structures and Performance
- Application Deep Dive: Hydrogen, Natural Gas, and Air Purification
- Sustainability and Regulatory Drivers (Referencing epa.gov, iea.org)
- Competitive Landscape and Patent Trends
- Challenges, Risks, and Barriers to Adoption
- Future Outlook: Disruptive Opportunities and Strategic Recommendations
- Sources & References
Executive Summary: Zeolite Catalysis Market in 2025
The global market for zeolite catalysis in industrial gas purification is poised for robust growth in 2025, driven by tightening environmental regulations, the need for efficient emission control, and the ongoing transition to cleaner industrial processes. Zeolites—crystalline aluminosilicate materials with high surface area and tunable pore structures—are increasingly favored for their ability to selectively adsorb and catalytically convert a range of gaseous pollutants, including nitrogen oxides (NOx), sulfur oxides (SOx), volatile organic compounds (VOCs), and carbon dioxide (CO2).
Major industrial sectors—such as petrochemicals, power generation, and manufacturing—are accelerating the adoption of zeolite-based catalysts to comply with stricter emission standards. In 2025, the demand for advanced zeolite catalysts is particularly strong in regions with aggressive air quality mandates, including the European Union, North America, and parts of Asia-Pacific. The European Union’s Industrial Emissions Directive and the United States Environmental Protection Agency’s Clean Air Act continue to be significant regulatory drivers.
Key industry players are expanding their production capacities and innovating new zeolite formulations to address evolving purification challenges. BASF, a global leader in chemical manufacturing, has invested in the development of zeolite-based catalysts for selective catalytic reduction (SCR) systems, which are widely used for NOx removal in power plants and heavy-duty vehicles. Honeywell is another major supplier, offering zeolite catalysts for gas purification in refining and petrochemical applications, with a focus on energy efficiency and operational reliability. Zeochem, a specialist in high-purity zeolites, is expanding its portfolio to meet the growing demand for gas drying and purification in industrial and medical sectors.
Recent advancements in zeolite synthesis—such as hierarchical pore structures and metal-exchanged zeolites—are enhancing catalytic performance and selectivity. These innovations are enabling more efficient removal of trace contaminants and greenhouse gases, supporting both regulatory compliance and sustainability goals. The integration of zeolite catalysts into modular and retrofit purification systems is also gaining traction, allowing industries to upgrade existing facilities with minimal disruption.
Looking ahead, the outlook for zeolite catalysis in industrial gas purification remains highly positive. Ongoing R&D efforts, coupled with increasing investments from established manufacturers, are expected to yield next-generation zeolite materials with improved durability, regeneration capability, and lower operational costs. As industries worldwide prioritize decarbonization and cleaner air, zeolite catalysis is set to play a pivotal role in shaping the future of industrial gas purification through 2025 and beyond.
Industry Overview: Zeolite Catalysts in Gas Purification
Zeolite catalysis has become a cornerstone technology in industrial gas purification, driven by the increasing demand for cleaner air, stricter emission regulations, and the need for efficient separation processes. As of 2025, the global industrial sector continues to adopt zeolite-based catalysts for applications such as removal of nitrogen oxides (NOx), sulfur compounds, volatile organic compounds (VOCs), and ammonia from process and exhaust gases. Zeolites, with their unique microporous structures and tunable acidity, offer high selectivity and stability, making them ideal for these challenging environments.
Major chemical and engineering companies are at the forefront of zeolite catalyst production and deployment. BASF, a global leader in chemical manufacturing, supplies a wide range of zeolite catalysts for gas purification, including those used in selective catalytic reduction (SCR) systems for NOx abatement in power plants and industrial boilers. Honeywell (through its UOP division) is another key player, providing zeolite-based adsorbents and catalysts for air separation, natural gas processing, and petrochemical applications. Zeochem, a specialized zeolite manufacturer, focuses on high-purity zeolites for gas drying and purification, serving industries such as medical oxygen production and industrial gas supply.
Recent years have seen significant advancements in zeolite catalyst formulations, with a focus on improving resistance to poisoning, thermal stability, and regeneration capability. For example, the adoption of copper- and iron-exchanged zeolites in SCR systems has enabled more efficient NOx removal at lower temperatures, a critical requirement for compliance with evolving emission standards in Europe, North America, and Asia. Companies like Clariant and ChemChina are actively developing next-generation zeolite catalysts tailored for specific industrial gas streams, including those with high moisture or sulfur content.
The outlook for zeolite catalysis in gas purification remains robust for the next several years. The ongoing transition to cleaner energy sources, electrification of industry, and tightening of air quality regulations are expected to drive further investment and innovation. Emerging applications, such as carbon capture and hydrogen purification, are also creating new opportunities for zeolite-based technologies. Industry collaborations and partnerships with research institutions are accelerating the commercialization of advanced zeolite materials with enhanced selectivity and durability.
In summary, zeolite catalysis is poised to play an increasingly vital role in industrial gas purification through 2025 and beyond, supported by strong industry engagement from leading manufacturers and a dynamic regulatory landscape that prioritizes environmental performance.
Key Players and Strategic Initiatives (e.g., basf.com, honeywell.com, zeochem.com)
The industrial gas purification sector is witnessing significant advancements in zeolite catalysis, driven by the strategic initiatives of leading chemical and materials companies. As of 2025, several key players are shaping the landscape through innovation, capacity expansion, and targeted partnerships.
BASF SE remains a global leader in zeolite-based catalysts, leveraging its extensive R&D infrastructure to develop advanced materials for gas purification. The company’s zeolite catalysts are integral to processes such as air separation, natural gas sweetening, and removal of volatile organic compounds (VOCs). BASF’s ongoing investments in digitalization and process optimization are aimed at enhancing catalyst performance and sustainability, with a focus on reducing energy consumption and emissions in industrial gas streams. The company’s strategic collaborations with industrial gas producers and technology licensors further reinforce its market position (BASF SE).
Honeywell International Inc. is another major player, particularly through its UOP division, which supplies zeolite-based adsorbents and catalysts for gas purification and separation. Honeywell’s molecular sieve technologies are widely adopted in hydrogen purification, air drying, and carbon capture applications. In 2025, Honeywell is expanding its portfolio to address the growing demand for low-carbon and energy-efficient solutions, aligning with global decarbonization trends. The company’s focus on modular, scalable purification systems is expected to accelerate adoption in emerging markets and distributed industrial settings (Honeywell International Inc.).
Zeochem AG, a specialist in high-purity zeolites and molecular sieves, continues to invest in production capacity and product innovation. Zeochem’s materials are used extensively in the purification of industrial gases such as oxygen, nitrogen, and hydrogen. The company’s recent initiatives include the development of tailored zeolite formulations for specific contaminants and the expansion of its global distribution network to better serve customers in Asia and North America. Zeochem’s commitment to quality and regulatory compliance positions it as a preferred supplier for critical gas purification applications (Zeochem AG).
Other notable contributors include Evonik Industries AG, which is advancing zeolite-based adsorbents for environmental and industrial gas treatment, and Arkema S.A., which is exploring new zeolite chemistries for selective gas separations. These companies are increasingly focusing on circular economy principles, aiming to improve catalyst recyclability and reduce lifecycle emissions.
Looking ahead, the competitive landscape is expected to intensify as demand for cleaner industrial processes grows. Strategic investments in R&D, supply chain resilience, and digital process control will be critical for companies seeking to maintain leadership in zeolite catalysis for gas purification through 2025 and beyond.
Market Size, Segmentation, and 2025–2030 Growth Forecasts (Estimated CAGR: 11–13%)
The global market for zeolite catalysis in industrial gas purification is poised for robust expansion between 2025 and 2030, with an estimated compound annual growth rate (CAGR) of 11–13%. This growth is driven by tightening environmental regulations, the need for cleaner industrial processes, and the increasing adoption of advanced gas purification technologies across sectors such as petrochemicals, natural gas processing, and air separation.
In 2025, the market size for zeolite-based gas purification catalysts is projected to exceed USD 2.5 billion, with Asia-Pacific leading demand due to rapid industrialization and stringent emission standards in China, India, and Southeast Asia. North America and Europe follow closely, propelled by ongoing investments in sustainable manufacturing and the retrofitting of existing plants to meet stricter air quality norms.
Market segmentation reveals that synthetic zeolites—particularly types 13X, ZSM-5, and 4A—dominate due to their high selectivity and thermal stability. These zeolites are widely used in applications such as the removal of nitrogen oxides (NOx), sulfur compounds, volatile organic compounds (VOCs), and carbon dioxide (CO2) from industrial gas streams. The petrochemical and oil & gas sectors account for the largest share, followed by power generation, chemical manufacturing, and air separation units.
Key industry players include Honeywell International Inc., which manufactures zeolite catalysts for gas purification and emission control, and BASF SE, a major supplier of zeolite-based adsorbents and catalysts for industrial gas treatment. Arkema S.A. and Zeochem AG are also prominent, offering a range of synthetic zeolites tailored for specific purification processes. Clariant AG is another significant player, focusing on zeolite catalysts for environmental and process gas purification.
Looking ahead to 2030, the market is expected to benefit from ongoing R&D in zeolite material science, including the development of hierarchical and nano-structured zeolites with enhanced adsorption and catalytic properties. The integration of zeolite catalysis in emerging applications—such as hydrogen production, carbon capture and storage (CCS), and renewable gas purification—will further expand market opportunities. Strategic collaborations between catalyst manufacturers and end-users are anticipated to accelerate technology adoption and customization for specific industrial needs.
Overall, the outlook for zeolite catalysis in industrial gas purification remains highly positive, underpinned by regulatory momentum, technological innovation, and the global push toward cleaner industrial operations.
Technological Innovations: Next-Gen Zeolite Structures and Performance
The landscape of zeolite catalysis for industrial gas purification is undergoing significant transformation in 2025, driven by the demand for higher efficiency, selectivity, and sustainability. Zeolites, crystalline aluminosilicates with well-defined microporous structures, have long been integral to gas purification processes, particularly in removing contaminants such as CO2, H2S, and volatile organic compounds (VOCs) from industrial streams. Recent technological innovations are now pushing the boundaries of what these materials can achieve.
A major trend in 2025 is the development of next-generation zeolite structures with tailored pore sizes and surface functionalities. Companies like BASF and Honeywell are at the forefront, leveraging advanced synthesis techniques to create zeolites with enhanced adsorption and catalytic properties. For example, BASF’s portfolio includes zeolites engineered for selective removal of trace impurities, which are critical in natural gas upgrading and air purification. Honeywell, through its UOP division, continues to innovate in the design of zeolite-based adsorbents and catalysts for sulfur removal and dehydration applications, focusing on improved cycle stability and regeneration efficiency.
Another significant innovation is the integration of hierarchical pore structures—combining micro-, meso-, and macropores within a single zeolite crystal. This approach, adopted by manufacturers such as Zeochem and Tosoh Corporation, enhances mass transfer rates and increases the accessibility of active sites, resulting in faster and more efficient gas purification. Zeochem, a global supplier of specialty zeolites, has introduced products with optimized pore architectures for pressure swing adsorption (PSA) and temperature swing adsorption (TSA) systems, which are widely used in hydrogen and oxygen production.
The push for sustainability is also shaping zeolite innovation. Companies are increasingly focusing on reducing the environmental footprint of zeolite production and regeneration. Arkema and Evonik Industries are investing in greener synthesis routes, such as solvent-free processes and the use of renewable raw materials, to align with global decarbonization goals. These efforts are expected to yield commercial-scale, eco-friendly zeolites within the next few years.
Looking ahead, the outlook for zeolite catalysis in industrial gas purification is robust. The convergence of advanced materials engineering, digital process optimization, and sustainability imperatives is set to deliver zeolite catalysts with unprecedented performance. As regulatory pressures on emissions intensify and industries seek cost-effective purification solutions, the adoption of next-gen zeolite technologies is poised to accelerate, with leading manufacturers playing a pivotal role in shaping the future of clean industrial gas streams.
Application Deep Dive: Hydrogen, Natural Gas, and Air Purification
Zeolite catalysis has become a cornerstone technology in industrial gas purification, particularly for hydrogen, natural gas, and air streams. As of 2025, the demand for high-purity gases is intensifying, driven by the growth of hydrogen energy, stricter emission regulations, and the expansion of natural gas infrastructure. Zeolites—crystalline aluminosilicates with uniform micropores—are prized for their selective adsorption, ion-exchange, and catalytic properties, making them indispensable in removing contaminants such as water, CO2, sulfur compounds, and volatile organics.
In hydrogen production, especially via steam methane reforming (SMR) and water-gas shift processes, zeolite-based adsorbents are widely used in pressure swing adsorption (PSA) units to separate hydrogen from CO, CO2, CH4, and moisture. Leading industrial gas companies such as Linde and Air Liquide have integrated advanced zeolite PSA systems in their large-scale hydrogen plants, enabling product purities exceeding 99.999%. These systems are being further optimized for energy efficiency and cycle speed, with ongoing investments in next-generation zeolite materials to enhance selectivity and capacity.
For natural gas purification, zeolites play a critical role in removing water vapor and acid gases (notably CO2 and H2S) to prevent pipeline corrosion and meet stringent quality standards. Companies like BASF and Arkema manufacture zeolite molecular sieves tailored for dehydration and sweetening units in LNG and pipeline gas processing. Recent developments focus on improving thermal stability and regenerability, as operators seek to reduce operational costs and environmental impact. The adoption of hybrid systems—combining zeolites with other adsorbents or membranes—is also gaining traction for challenging feedstocks.
In air purification, zeolites are extensively used in oxygen and nitrogen generation via PSA and vacuum swing adsorption (VSA) technologies. Zeochem and Chemiewerk Bad Köstritz are prominent suppliers of synthetic zeolites for medical, industrial, and environmental air separation units. The ongoing miniaturization of oxygen concentrators and the push for decentralized air purification solutions are driving demand for high-performance zeolite grades with rapid adsorption/desorption kinetics.
Looking ahead, the outlook for zeolite catalysis in gas purification remains robust. The global shift toward low-carbon hydrogen, expansion of LNG trade, and tightening air quality regulations are expected to sustain double-digit growth in zeolite demand through the late 2020s. Industry leaders are investing in digital process control and advanced material synthesis to further boost efficiency and sustainability, positioning zeolites as a key enabler of cleaner industrial gas value chains.
Sustainability and Regulatory Drivers (Referencing epa.gov, iea.org)
The adoption of zeolite catalysis for industrial gas purification is increasingly shaped by sustainability imperatives and evolving regulatory frameworks. In 2025, global and national policies are intensifying pressure on industries to reduce emissions of greenhouse gases (GHGs) and hazardous air pollutants, with zeolite-based technologies emerging as a preferred solution due to their efficiency, selectivity, and environmental compatibility.
Regulatory agencies such as the United States Environmental Protection Agency (EPA) are enforcing stricter standards on industrial emissions, particularly targeting nitrogen oxides (NOx), sulfur oxides (SOx), volatile organic compounds (VOCs), and particulate matter. The EPA’s National Ambient Air Quality Standards (NAAQS) and the Clean Air Act continue to drive the adoption of advanced purification systems, with zeolite catalysts playing a central role in selective catalytic reduction (SCR) and adsorption processes for NOx and VOC abatement. The EPA also encourages the use of best available control technologies (BACT), where zeolite-based systems are frequently recognized for their high removal efficiencies and operational robustness.
On the international stage, the International Energy Agency (IEA) highlights the critical role of industrial decarbonization in meeting net-zero targets. The IEA’s 2024 and 2025 outlooks emphasize the need for rapid deployment of low-carbon technologies, including advanced catalysis for gas purification, to achieve emissions reductions in hard-to-abate sectors such as chemicals, refining, and power generation. Zeolite catalysts, with their tunable pore structures and high thermal stability, are increasingly integrated into industrial processes to capture and convert pollutants, aligning with the IEA’s recommendations for sustainable industrial transformation.
Sustainability drivers extend beyond compliance, as industries seek to minimize operational costs and environmental footprints. Zeolite catalysts offer advantages such as lower energy consumption, longer operational lifetimes, and the potential for regeneration and recycling, supporting circular economy principles. These attributes are particularly valued in sectors facing carbon pricing mechanisms and environmental, social, and governance (ESG) reporting requirements.
Looking ahead, regulatory tightening is expected to continue, with both the EPA and IEA projecting more ambitious emission reduction targets through 2030. This trajectory will likely accelerate investment in zeolite-based purification technologies, spurring innovation in catalyst design and process integration. As industries adapt to these evolving standards, zeolite catalysis is poised to remain at the forefront of sustainable gas purification solutions, underpinning both regulatory compliance and broader decarbonization strategies.
Competitive Landscape and Patent Trends
The competitive landscape for zeolite catalysis in industrial gas purification is characterized by a mix of established chemical giants, specialized catalyst manufacturers, and emerging technology firms. As of 2025, the sector is witnessing intensified activity, driven by tightening global emissions regulations and the push for cleaner industrial processes. Major players such as BASF, Honeywell, and Zeochem continue to dominate the market, leveraging decades of experience in zeolite synthesis, process integration, and large-scale supply capabilities.
BASF, with its extensive portfolio of zeolite-based adsorbents and catalysts, remains a leader in supplying solutions for air purification, natural gas upgrading, and industrial emissions control. The company’s ongoing investments in R&D and production capacity underscore its commitment to innovation in this field. Honeywell (through its UOP division) is another key competitor, offering proprietary zeolite formulations for pressure swing adsorption (PSA) and other gas separation technologies, widely adopted in hydrogen purification and air separation units.
Specialty manufacturers such as Zeochem and Arkema are also prominent, focusing on high-purity zeolites tailored for specific gas purification applications, including removal of volatile organic compounds (VOCs), sulfur compounds, and moisture. These companies are increasingly targeting niche markets, such as biogas upgrading and carbon capture, where customized zeolite properties can deliver performance advantages.
Patent activity in zeolite catalysis for gas purification remains robust. The past two years have seen a surge in filings related to novel zeolite structures, improved regeneration methods, and hybrid materials that combine zeolites with other adsorbents or catalytic phases. Companies like BASF and Honeywell are particularly active, seeking to protect innovations that enhance selectivity, capacity, and operational stability under harsh industrial conditions. Additionally, Asian manufacturers, notably in China and Japan, are increasing their patent output, reflecting the region’s growing investment in advanced materials for environmental applications.
Looking ahead, the competitive landscape is expected to evolve as new entrants—often spin-offs from academic research or startups—bring disruptive technologies to market. Collaborations between industrial firms and research institutions are likely to accelerate, aiming to address emerging challenges such as CO2 capture and purification of complex gas streams. The next few years will likely see further consolidation among established players, alongside a steady stream of patent filings as companies race to secure intellectual property in this rapidly advancing field.
Challenges, Risks, and Barriers to Adoption
The adoption of zeolite catalysis for industrial gas purification faces several challenges, risks, and barriers as of 2025 and looking ahead. While zeolites are recognized for their high selectivity, thermal stability, and tunable pore structures, their widespread implementation in gas purification processes is not without obstacles.
One of the primary challenges is the cost and complexity of synthesis. High-performance zeolites often require precise control over composition and structure, which can involve expensive raw materials and energy-intensive hydrothermal synthesis processes. This can limit their economic viability for large-scale applications, especially in industries with tight margins. Companies such as BASF and Honeywell, both major producers of zeolite catalysts, continue to invest in process optimization, but cost reduction remains a key hurdle.
Deactivation and fouling of zeolite catalysts present another significant risk. Industrial gas streams often contain impurities such as sulfur compounds, heavy metals, or particulates that can poison or block the active sites of zeolites, reducing their effectiveness and operational lifespan. This necessitates frequent regeneration or replacement, increasing operational costs and downtime. Arkema, a global supplier of specialty chemicals and zeolite materials, has highlighted the importance of developing more robust zeolite formulations to address these durability concerns.
Integration with existing infrastructure is also a barrier. Many industrial gas purification systems are designed around traditional adsorbents or catalytic materials. Retrofitting or replacing these systems to accommodate zeolite-based technologies can require significant capital investment and process redesign. This is particularly relevant in sectors such as petrochemicals and natural gas processing, where downtime and process changes can have substantial financial implications.
Regulatory and supply chain risks are emerging as well. As environmental regulations tighten, the demand for advanced purification technologies is rising, but so is scrutiny over the sourcing and lifecycle impacts of catalyst materials. Ensuring a stable supply of high-purity aluminosilicates and other zeolite precursors is critical, especially as global supply chains remain vulnerable to geopolitical and logistical disruptions. Companies like Zeochem, a specialized zeolite manufacturer, are working to diversify sourcing and improve supply chain resilience.
Looking forward, overcoming these challenges will require continued innovation in zeolite synthesis, improved catalyst durability, and closer collaboration between catalyst suppliers and end-users. The outlook for zeolite catalysis in industrial gas purification remains promising, but addressing these barriers is essential for broader adoption and long-term sustainability.
Future Outlook: Disruptive Opportunities and Strategic Recommendations
The future of zeolite catalysis in industrial gas purification is poised for significant transformation, driven by tightening environmental regulations, the global push for decarbonization, and advances in material science. As of 2025, zeolites remain at the forefront of gas purification technologies, particularly for applications such as removal of nitrogen oxides (NOx), sulfur compounds, volatile organic compounds (VOCs), and carbon dioxide (CO2) from industrial emissions. The next few years are expected to witness both disruptive opportunities and strategic shifts in the sector.
One of the most promising disruptive opportunities lies in the development of next-generation zeolite catalysts with enhanced selectivity, stability, and regeneration capabilities. Major chemical and catalyst manufacturers such as BASF and Honeywell are investing in research to engineer zeolites with tailored pore structures and active sites, enabling more efficient capture and conversion of target gases. For example, the adoption of copper-exchanged zeolites for selective catalytic reduction (SCR) of NOx is expanding, with ongoing improvements in hydrothermal stability and resistance to poisoning by industrial contaminants.
The integration of zeolite-based systems into modular, decentralized gas purification units is another emerging trend. Companies like Arkema and Zeochem are developing compact, scalable solutions suitable for both large-scale plants and smaller, distributed emission sources. This modularity is expected to lower capital expenditure and facilitate compliance with evolving emission standards, especially in regions with stringent air quality mandates.
Digitalization and process optimization are also set to play a pivotal role. The use of real-time monitoring and AI-driven process control can maximize zeolite catalyst lifespans and minimize operational costs. Industry leaders such as Evonik Industries are exploring digital twins and advanced analytics to optimize catalyst performance and predict maintenance needs, further enhancing the economic viability of zeolite-based purification.
Strategically, companies are advised to invest in R&D partnerships with academic institutions and technology providers to accelerate the commercialization of novel zeolite formulations. Collaboration with end-users in sectors such as petrochemicals, power generation, and waste management will be crucial for tailoring solutions to specific process requirements. Additionally, securing supply chains for high-purity raw materials and rare elements used in advanced zeolite synthesis will be a key competitive differentiator.
In summary, the outlook for zeolite catalysis in industrial gas purification is robust, with disruptive innovation expected in catalyst design, system integration, and digital process management. Companies that proactively invest in these areas and align with global sustainability trends are likely to capture significant market share and drive the next wave of industrial emission control technologies.
Sources & References
- BASF
- Honeywell
- Zeochem
- Clariant
- ChemChina
- Evonik Industries AG
- Arkema S.A.
- Linde
- Air Liquide
- International Energy Agency