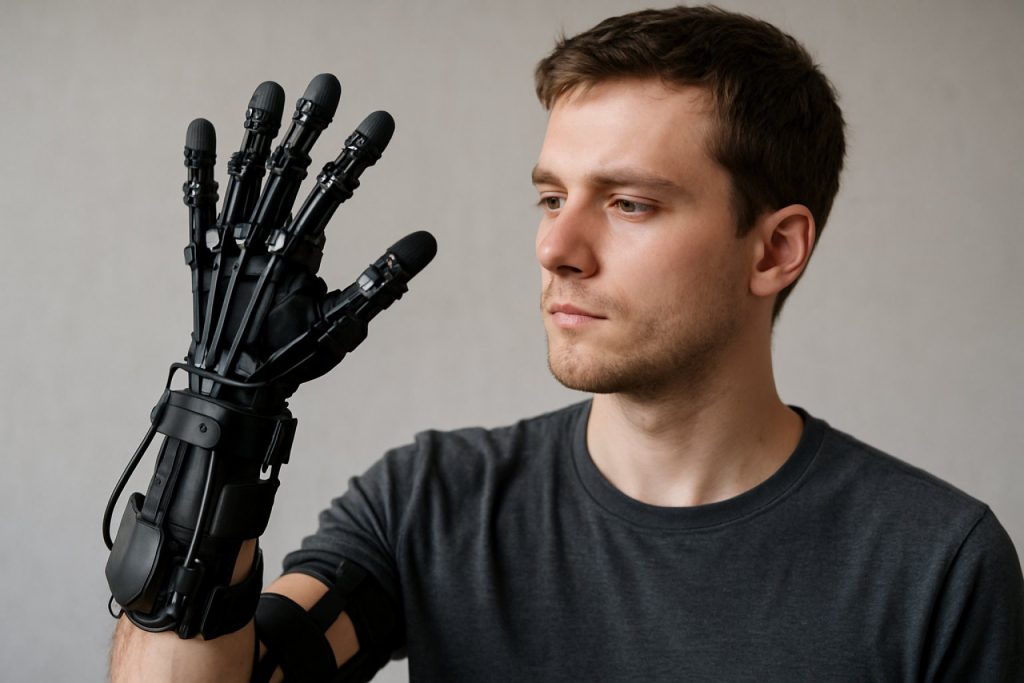
The Next Wave of Immersive Interaction: How Wearable Haptic Robotics Will Transform Industries and Daily Life by 2025. Explore the Breakthroughs, Market Growth, and Future Potential of Tactile Technology.
- Executive Summary: Key Trends and Market Drivers
- Market Size and Forecast (2025–2030)
- Core Technologies: Actuators, Sensors, and Materials
- Leading Players and Innovators (e.g., haptx.com, teslasuit.io, bioniklabs.com)
- Applications Across Healthcare, Gaming, and Industry
- Integration with AI, IoT, and XR Ecosystems
- Regulatory Landscape and Industry Standards (ieee.org, asme.org)
- Challenges: Scalability, Comfort, and Power Management
- Investment, M&A, and Startup Ecosystem
- Future Outlook: Emerging Use Cases and Long-Term Impact
- Sources & References
Executive Summary: Key Trends and Market Drivers
Wearable haptic robotics is rapidly emerging as a transformative sector within the broader field of human-machine interaction, driven by advances in miniaturized actuators, sensor technologies, and artificial intelligence. In 2025, the sector is characterized by a convergence of technological innovation, expanding application domains, and increased investment from both established technology leaders and specialized startups. Key trends include the integration of haptic feedback into consumer wearables, the proliferation of exoskeletons for industrial and medical use, and the growing adoption of haptic devices in immersive virtual and augmented reality environments.
Major technology companies are accelerating the commercialization of wearable haptic solutions. Samsung Electronics continues to develop advanced haptic feedback systems for its wearable devices, focusing on enhancing user experience in smartwatches and fitness trackers. Sony Group Corporation is leveraging its expertise in gaming and entertainment to push the boundaries of haptic gloves and suits, aiming to deliver more immersive experiences for PlayStation VR and other platforms. Meanwhile, HaptX Inc. is recognized for its microfluidic haptic gloves, which provide realistic touch sensations for enterprise training, design, and teleoperation applications.
In the industrial and healthcare sectors, wearable haptic robotics is being adopted to enhance worker safety, rehabilitation, and assistive mobility. SuitX, a subsidiary of Ottobock, is advancing exoskeletons that reduce fatigue and injury risk for workers in manufacturing and logistics. CYBERDYNE Inc. is expanding the deployment of its HAL (Hybrid Assistive Limb) exoskeletons in rehabilitation centers, supporting patients with neurological and musculoskeletal conditions.
The outlook for the next few years is marked by several drivers: the increasing demand for remote and virtual experiences, the need for ergonomic solutions in physically demanding jobs, and the push for more effective rehabilitation technologies. The integration of AI-driven adaptive feedback and wireless connectivity is expected to further enhance the functionality and user acceptance of wearable haptic devices. Regulatory support and standardization efforts, particularly in medical and industrial applications, are anticipated to facilitate broader adoption.
As the ecosystem matures, collaborations between hardware manufacturers, software developers, and end-user industries are likely to accelerate innovation and market penetration. The sector is poised for robust growth, with wearable haptic robotics set to play a pivotal role in shaping the future of human-machine interaction across multiple domains.
Market Size and Forecast (2025–2030)
The wearable haptic robotics market is poised for significant growth between 2025 and 2030, driven by rapid advancements in sensor technology, miniaturization, and the expanding adoption of immersive applications across industries. As of 2025, the sector encompasses a range of products, including haptic gloves, vests, exoskeletons, and full-body suits, which deliver tactile feedback and force sensations to users in real time. These devices are increasingly integrated into virtual and augmented reality (VR/AR) systems, rehabilitation, remote operation, and training environments.
Key industry players are actively scaling up production and expanding their product portfolios. HaptX is recognized for its advanced haptic gloves, which use microfluidic technology to simulate realistic touch and force feedback, targeting enterprise VR training and design. bHaptics offers a suite of consumer and professional haptic wearables, including vests and arm/hand devices, compatible with leading VR platforms. Teslasuit develops full-body haptic suits that combine motion capture, biometric data collection, and electrical stimulation, serving both entertainment and industrial training markets. SuitX, now part of Ottobock, focuses on wearable exoskeletons for industrial and medical applications, enhancing worker safety and rehabilitation outcomes.
The market outlook for 2025–2030 is shaped by several converging trends. The proliferation of VR/AR in gaming, simulation, and remote collaboration is expected to drive demand for more immersive and realistic haptic experiences. In healthcare, wearable haptic robotics are being adopted for physical therapy, post-stroke rehabilitation, and assistive devices for individuals with mobility impairments. Industrial sectors are leveraging exoskeletons to reduce workplace injuries and improve productivity, with companies like Ottobock and SuitX leading deployments in logistics and manufacturing.
Geographically, North America and Europe are anticipated to remain the largest markets due to strong R&D ecosystems and early adoption in enterprise and healthcare. However, Asia-Pacific is projected to see the fastest growth, fueled by investments in advanced manufacturing and a burgeoning gaming industry.
Looking ahead, the wearable haptic robotics market is expected to experience double-digit annual growth rates through 2030, as device costs decrease, interoperability improves, and new applications emerge. Strategic partnerships between hardware manufacturers, software developers, and end-user industries will be critical in accelerating adoption and expanding the market’s reach.
Core Technologies: Actuators, Sensors, and Materials
Wearable haptic robotics is rapidly advancing, driven by innovations in core technologies such as actuators, sensors, and materials. As of 2025, the sector is witnessing a convergence of miniaturization, energy efficiency, and enhanced realism in tactile feedback, enabling new applications in healthcare, virtual reality (VR), industrial training, and assistive devices.
Actuators are central to wearable haptic systems, converting electrical signals into mechanical motion to simulate touch sensations. Recent years have seen a shift from traditional vibration motors to more sophisticated technologies such as electroactive polymers (EAPs), shape memory alloys (SMAs), and pneumatic actuators. Companies like Tactile Systems Technology are developing wearable devices that use pneumatic actuation for medical rehabilitation, while HaptX employs microfluidic actuators in their haptic gloves to deliver highly localized and realistic force feedback for VR and teleoperation. These actuators are becoming thinner, lighter, and more power-efficient, making them suitable for all-day wear.
Sensor technology is equally critical, providing the feedback loop necessary for responsive and adaptive haptic experiences. Modern wearable haptic devices integrate a range of sensors, including force, pressure, stretch, and inertial measurement units (IMUs). Sensoryx and Bioservo Technologies are notable for embedding high-precision force and motion sensors in their wearable exoskeletons and gloves, enabling real-time monitoring of user intent and environmental interaction. The trend is toward flexible, skin-conformal sensors that can be seamlessly integrated into textiles, enhancing comfort and accuracy.
Materials science is a foundational pillar for wearable haptic robotics. The adoption of soft, stretchable, and biocompatible materials is enabling devices that conform closely to the human body, reducing fatigue and improving user experience. Companies such as Xsens are leveraging advanced polymers and smart textiles to create sensor-embedded wearables for motion capture and haptic feedback. Additionally, the use of conductive fabrics and silicone-based elastomers is facilitating the integration of both actuation and sensing elements into a single, flexible substrate.
Looking ahead, the next few years are expected to bring further integration of these core technologies, with a focus on wireless operation, longer battery life, and scalable manufacturing. The collaboration between robotics firms, material suppliers, and electronics manufacturers is likely to accelerate the commercialization of lightweight, affordable, and highly functional wearable haptic devices, expanding their reach into consumer, medical, and industrial markets.
Leading Players and Innovators (e.g., haptx.com, teslasuit.io, bioniklabs.com)
The wearable haptic robotics sector is rapidly evolving, with several pioneering companies driving innovation and commercialization as of 2025. These organizations are developing advanced exoskeletons, haptic gloves, and full-body suits that deliver realistic tactile feedback for applications in virtual reality (VR), healthcare, industrial training, and remote operation.
One of the most prominent players is HaptX, renowned for its microfluidic haptic gloves. HaptX’s technology enables users to feel virtual objects with high fidelity, using hundreds of microfluidic actuators to simulate touch, texture, and force feedback. In 2024, HaptX announced partnerships with leading VR and robotics companies to integrate its gloves into enterprise training and telerobotics systems, and in 2025, the company is expanding its reach into medical simulation and remote manipulation for hazardous environments.
Another key innovator is Teslasuit, which offers a full-body haptic suit capable of delivering precise electrical muscle stimulation (EMS) and motion capture. The Teslasuit is used in professional training, rehabilitation, and immersive entertainment, providing users with a comprehensive sense of touch, temperature, and resistance. In 2025, Teslasuit is focusing on expanding its presence in the defense and aerospace sectors, where realistic simulation and remote operation are critical.
In the field of assistive robotics, BIONIK Laboratories stands out for its development of wearable robotic exoskeletons designed to aid rehabilitation and mobility for individuals with neurological and mobility impairments. BIONIK’s InMotion devices are being adopted by hospitals and rehabilitation centers worldwide, and the company is investing in next-generation wearable systems that integrate haptic feedback to enhance patient engagement and outcomes.
Other notable contributors include SuitX, which specializes in modular exoskeletons for industrial and medical use, and BIONIK, which is advancing wearable robotics for both clinical and home settings. Meanwhile, BIONIK Laboratories continues to expand its product line with a focus on user-friendly, data-driven rehabilitation solutions.
Looking ahead, the wearable haptic robotics market is expected to see increased collaboration between hardware manufacturers and software developers, as well as growing adoption in sectors such as remote surgery, hazardous environment operations, and immersive training. As these leading players continue to refine their technologies and expand their applications, wearable haptic robotics is poised to become a cornerstone of human-machine interaction in the coming years.
Applications Across Healthcare, Gaming, and Industry
Wearable haptic robotics are rapidly advancing, with 2025 marking a pivotal year for their integration across healthcare, gaming, and industrial sectors. These systems, which provide tactile feedback and force sensations to users, are enabling new forms of human-machine interaction and immersive experiences.
In healthcare, wearable haptic robotics are being deployed for rehabilitation, surgical training, and assistive devices. Exoskeletons and haptic gloves are now used in physical therapy to help patients regain motor function after strokes or injuries. Companies such as Hocoma are leading with robotic rehabilitation devices that incorporate haptic feedback, allowing therapists to monitor and adjust therapy in real time. Similarly, Bionik Laboratories is developing wearable robotic systems for upper and lower limb rehabilitation, focusing on patient engagement and measurable outcomes. In surgical training, haptic wearables are enhancing simulation realism, enabling trainees to feel tissue resistance and instrument feedback, which is critical for skill acquisition.
The gaming industry is witnessing a surge in wearable haptic robotics, driven by the demand for deeper immersion in virtual and augmented reality environments. Companies like bHaptics and HaptX are commercializing haptic vests, gloves, and full-body suits that deliver precise tactile sensations synchronized with in-game events. These devices are compatible with leading VR platforms and are being adopted by both consumers and developers to create more engaging and realistic experiences. The trend is expected to accelerate as content creators leverage haptic feedback to differentiate their offerings and as hardware becomes more affordable and ergonomic.
In industrial settings, wearable haptic robotics are improving safety, training, and productivity. For example, TACTILE and Sarcos Technology and Robotics Corporation are developing wearable exoskeletons and haptic interfaces that assist workers in handling heavy loads, reducing fatigue and injury risk. These systems also enable remote operation of machinery in hazardous environments, with haptic feedback providing operators with a sense of touch and resistance, thus enhancing precision and situational awareness. As industries continue to automate and digitize, the adoption of wearable haptic robotics is projected to grow, particularly in manufacturing, logistics, and maintenance.
Looking ahead, the convergence of advances in materials science, miniaturization, and wireless connectivity is expected to drive further innovation in wearable haptic robotics. By 2025 and beyond, these technologies are poised to become integral to healthcare delivery, entertainment, and industrial operations, with ongoing research and commercialization efforts from leading companies shaping the future landscape.
Integration with AI, IoT, and XR Ecosystems
The integration of wearable haptic robotics with artificial intelligence (AI), the Internet of Things (IoT), and extended reality (XR) ecosystems is accelerating in 2025, driven by advances in sensor miniaturization, wireless connectivity, and real-time data processing. This convergence is enabling more immersive, responsive, and context-aware experiences across sectors such as healthcare, industrial training, gaming, and remote collaboration.
Leading companies are embedding AI algorithms directly into wearable haptic devices to enable adaptive feedback and personalized user experiences. For example, HaptX has developed haptic gloves that leverage AI to interpret user intent and environmental context, dynamically adjusting force feedback for realistic touch sensations in virtual and augmented reality applications. Similarly, Teslasuit integrates biometric sensors and machine learning to monitor physiological signals and tailor haptic responses, supporting applications in rehabilitation, sports training, and immersive entertainment.
IoT connectivity is further enhancing the capabilities of wearable haptic robotics by enabling seamless communication between devices and cloud-based platforms. Companies like Ultraleap are pioneering mid-air haptics and gesture tracking systems that can be networked with other smart devices, allowing for synchronized multisensory feedback in collaborative XR environments. This is particularly relevant for remote operations and telepresence, where real-time haptic feedback can bridge the gap between physical and digital interactions.
The XR ecosystem—encompassing virtual, augmented, and mixed reality—is a primary driver for the adoption of wearable haptic robotics. Major XR hardware manufacturers, including Meta and HTC, are actively exploring partnerships and integrations with haptic technology providers to deliver more immersive and interactive experiences. For instance, Meta’s research into next-generation haptic gloves aims to enable users to “feel” virtual objects, enhancing realism and presence in the metaverse.
Looking ahead, the next few years are expected to see deeper integration of wearable haptic robotics with AI-driven analytics, IoT-enabled device orchestration, and XR content platforms. This will likely result in more intuitive user interfaces, improved accessibility, and expanded use cases in fields such as remote surgery, industrial maintenance, and education. As interoperability standards mature and 5G/6G connectivity becomes ubiquitous, the ecosystem for wearable haptic robotics is poised for significant growth and innovation.
Regulatory Landscape and Industry Standards (ieee.org, asme.org)
The regulatory landscape and industry standards for wearable haptic robotics are rapidly evolving as the sector matures and adoption accelerates across healthcare, industrial, and consumer applications. In 2025, the focus is on ensuring safety, interoperability, and performance, with leading standards organizations and industry consortia playing pivotal roles.
The IEEE has been at the forefront of standardization efforts for haptic devices, including wearable robotics. The IEEE 1918.1 standard, which addresses tactile internet and haptic communications, is increasingly referenced in the development of wearable haptic systems, particularly those intended for remote operation and telepresence. Ongoing work within IEEE working groups is expected to yield further guidelines on latency, reliability, and user safety, which are critical for medical and industrial-grade wearables.
The ASME (American Society of Mechanical Engineers) is also contributing to the regulatory framework, particularly through its standards for robotics and exoskeletons. ASME’s efforts include the development of performance and safety benchmarks for wearable robotic devices, with a focus on human-robot interaction, mechanical integrity, and risk mitigation. These standards are increasingly referenced by manufacturers seeking to certify their products for clinical and workplace use.
In parallel, regulatory agencies in major markets are updating their frameworks to address the unique challenges posed by wearable haptic robotics. The U.S. Food and Drug Administration (FDA) has issued guidance for medical exoskeletons and is expected to expand its oversight to include a broader range of wearable haptic devices, especially those used in rehabilitation and assistive contexts. The European Union’s Medical Device Regulation (MDR) similarly covers wearable robotics, requiring rigorous clinical evaluation and post-market surveillance.
Industry consortia and alliances are also emerging to promote interoperability and best practices. For example, the IEEE Haptics Technical Committee and the ASME Robotics Division are facilitating collaboration between academia, industry, and regulators to harmonize standards globally.
Looking ahead, the next few years will likely see the introduction of more granular standards addressing cybersecurity, data privacy, and AI integration in wearable haptic robotics. As the technology becomes more embedded in critical applications, compliance with these evolving standards will be essential for market access and user trust. The ongoing collaboration between standards bodies, regulatory agencies, and industry stakeholders is expected to accelerate the safe and effective deployment of wearable haptic robotics worldwide.
Challenges: Scalability, Comfort, and Power Management
Wearable haptic robotics, which enable users to experience tactile feedback in virtual and remote environments, are rapidly advancing but face significant challenges in scalability, comfort, and power management as the sector moves through 2025 and beyond. These challenges are central to the widespread adoption of haptic wearables in fields such as healthcare, gaming, industrial training, and teleoperation.
Scalability remains a primary hurdle. While prototype devices and limited production runs have demonstrated the potential of haptic wearables, mass production is constrained by the complexity of integrating multiple actuators, sensors, and flexible electronics into compact, lightweight form factors. Companies like HaptX and Teslasuit have developed advanced haptic gloves and full-body suits, respectively, but scaling these technologies for broader consumer or enterprise markets requires overcoming manufacturing bottlenecks and reducing costs. For example, HaptX utilizes microfluidic actuators to deliver realistic force feedback, but the intricate design and assembly processes currently limit production volumes and affordability.
Comfort is another critical factor influencing user acceptance. Wearable haptic devices must balance the need for robust feedback with ergonomic design, minimizing weight, bulk, and heat generation. Teslasuit integrates haptic feedback, motion capture, and biometric sensors into a single garment, but ensuring long-term comfort for users—especially during extended sessions—remains a challenge. Similarly, bHaptics offers modular haptic vests and accessories designed for gaming and VR, focusing on adjustable fits and breathable materials. However, as the industry pushes toward more immersive and full-body solutions, maintaining comfort without sacrificing performance will be a key area of innovation.
Power management is a persistent technical challenge, particularly as devices become more sophisticated and wireless. High-fidelity haptic feedback requires significant energy, and current battery technologies often limit operational time and increase device weight. Companies such as bHaptics and Teslasuit are exploring energy-efficient actuators and optimized firmware to extend battery life, but breakthroughs in lightweight, high-capacity batteries or energy harvesting will be necessary for all-day use scenarios.
Looking ahead, addressing these challenges will be crucial for the mainstream adoption of wearable haptic robotics. Industry leaders are expected to invest in advanced materials, modular designs, and smarter power solutions, with incremental improvements anticipated over the next few years. Collaboration between hardware manufacturers, component suppliers, and research institutions will likely accelerate progress toward scalable, comfortable, and energy-efficient haptic wearables.
Investment, M&A, and Startup Ecosystem
The wearable haptic robotics sector is experiencing a surge in investment and startup activity as the technology matures and finds applications across healthcare, gaming, industrial training, and assistive devices. In 2025, venture capital and corporate investment are increasingly targeting companies that can demonstrate scalable solutions and clear paths to commercialization. The sector is characterized by a mix of established players and agile startups, with notable activity in North America, Europe, and Asia.
Key industry leaders such as HaptX and Teslasuit continue to attract attention for their advanced haptic feedback systems. HaptX, based in the United States, is known for its microfluidic haptic gloves, which have secured partnerships with major industrial and defense clients. The company has raised significant funding rounds in recent years, with continued investor interest in 2025 as it expands its product line and manufacturing capabilities. Teslasuit, headquartered in the UK, offers a full-body haptic suit and has established collaborations with automotive, medical, and entertainment sectors, positioning itself as a key player in the wearable haptics market.
The startup ecosystem is vibrant, with new entrants focusing on niche applications such as rehabilitation, remote collaboration, and immersive training. Companies like bHaptics from South Korea are gaining traction with modular, consumer-friendly haptic vests and accessories, targeting the rapidly growing VR and gaming markets. Meanwhile, SenseGlove in the Netherlands is making strides in industrial training and robotics teleoperation, leveraging recent funding to scale production and expand its client base.
Mergers and acquisitions are also shaping the landscape. Larger technology and robotics firms are acquiring innovative startups to integrate haptic capabilities into their broader product portfolios. This trend is expected to accelerate through 2025 and beyond, as companies seek to consolidate intellectual property and talent. Strategic investments from industry giants in sectors such as automotive, healthcare, and defense are further fueling growth and cross-sector collaboration.
Looking ahead, the wearable haptic robotics market is poised for continued expansion, driven by advances in materials, miniaturization, and wireless connectivity. The influx of capital and strategic partnerships is expected to accelerate commercialization, with a growing number of startups reaching scale or being acquired by established players. As the technology becomes more affordable and accessible, the sector is likely to see increased adoption across both enterprise and consumer markets.
Future Outlook: Emerging Use Cases and Long-Term Impact
The future outlook for wearable haptic robotics in 2025 and the coming years is marked by rapid technological maturation, expanding use cases, and a growing ecosystem of industry players. As haptic feedback systems become more compact, energy-efficient, and capable of delivering nuanced sensations, their integration into wearable robotics is poised to transform multiple sectors.
In healthcare, wearable haptic robotics are expected to play a pivotal role in rehabilitation and assistive technologies. Companies such as HaptX are advancing haptic gloves that provide realistic touch feedback, enabling more effective physical therapy and remote rehabilitation. These systems allow patients to perform exercises with real-time guidance and feedback, potentially reducing recovery times and improving outcomes. Similarly, exiii is developing lightweight, wearable haptic devices that can be used for both prosthetic control and immersive training scenarios.
In the realm of virtual and augmented reality, wearable haptic robotics are set to redefine user interaction. bHaptics and Teslasuit are leading the charge with full-body haptic suits and vests that deliver precise tactile feedback, enhancing immersion for gaming, simulation, and professional training. These technologies are being adopted by entertainment companies and are also finding applications in military and emergency response training, where realistic simulation is critical for skill development.
Industrial and collaborative robotics are another area of significant growth. Wearable haptic exoskeletons, such as those developed by SuitX (now part of Ottobock), are being deployed to augment human strength and reduce workplace injuries. These systems provide workers with real-time feedback and support, enabling safer and more efficient handling of heavy materials. As manufacturing and logistics sectors continue to automate, the demand for wearable haptic solutions that facilitate human-robot collaboration is expected to rise.
Looking ahead, the convergence of artificial intelligence, advanced materials, and miniaturized actuators will further expand the capabilities and accessibility of wearable haptic robotics. Industry leaders anticipate broader adoption in consumer electronics, sports training, and even remote social interaction, where touch feedback can bridge the gap between digital and physical experiences. As standards and interoperability improve, the ecosystem is likely to see increased collaboration between hardware manufacturers, software developers, and end users, accelerating innovation and market penetration.
Overall, the next few years will likely witness wearable haptic robotics moving from niche applications to mainstream adoption, fundamentally reshaping how humans interact with machines and digital environments.
Sources & References
- HaptX Inc.
- SuitX
- Ottobock
- CYBERDYNE Inc.
- bHaptics
- Teslasuit
- Sensoryx
- Bioservo Technologies
- Xsens
- HaptX
- Teslasuit
- SuitX
- Hocoma
- TACTILE
- Sarcos Technology and Robotics Corporation
- Ultraleap
- Meta
- HTC
- IEEE
- ASME
- SenseGlove