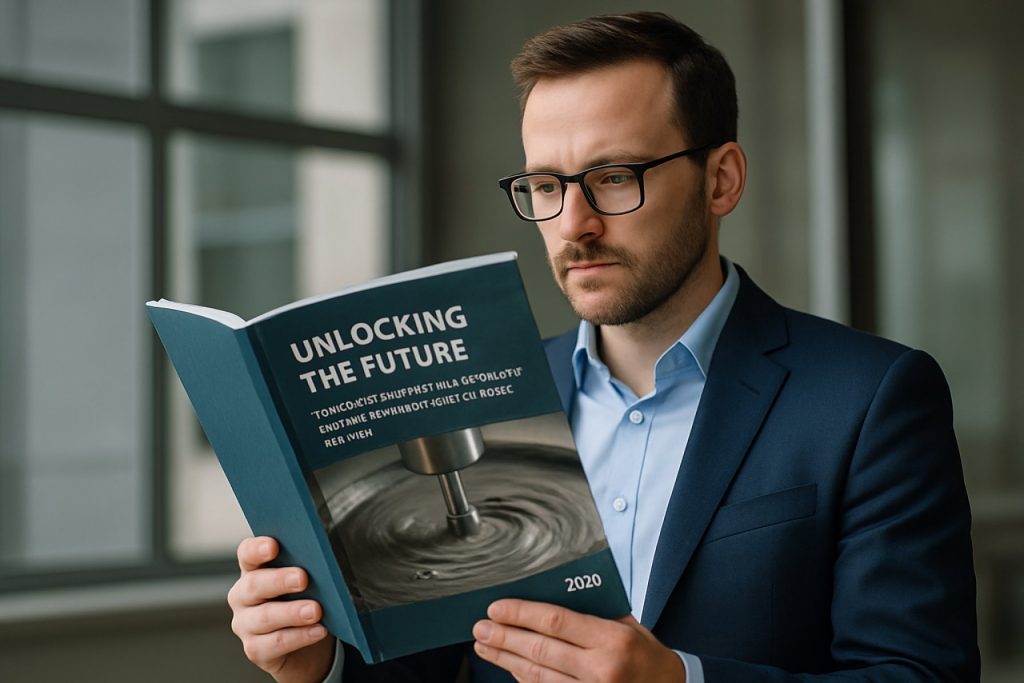
Table of Contents
- Executive Summary: 2025 Outlook & Key Takeaways
- Market Size, Growth Forecasts, and Global Demand Trends (2025–2028)
- Core Technology Innovations in Clay Dispersion Rheology
- Comparative Analysis of Leading Clay Types and Additives
- Major Industry Players and Strategic Partnerships (Citing Imerys.com, basf.com, lkabminerals.com)
- Regulatory Environment and Industry Standards (Referencing imerys.com and theclaymineralsociety.org)
- Emerging Application Sectors: Construction, Ceramics, Drilling, and Beyond
- Sustainability Challenges and Green Rheology Solutions
- Investment Hotspots and R&D Funding Trends
- Future Outlook: Disruptive Technologies and Market Opportunities to 2028
- Sources & References
Executive Summary: 2025 Outlook & Key Takeaways
The optimization of clay dispersion rheology is entering a pivotal phase in 2025, driven by advancements in additive chemistry, process automation, and precision measurement technologies. Industries reliant on clay dispersions—such as construction, ceramics, paper, and oilfield services—are prioritizing enhanced process efficiency, material performance, and environmental compliance. This executive summary distills the key trends and expectations shaping the clay dispersion rheology landscape for 2025 and the immediate years ahead.
- Advanced Additives and Formulation: 2025 will see accelerated adoption of next-generation rheology modifiers and dispersants tailored for various clay types and end-use requirements. Major suppliers such as BASF and Imerys are expanding portfolios with bio-based and multifunctional additives, targeting improved flow characteristics and reduction of agglomeration while supporting sustainability mandates.
- Real-Time Rheology Monitoring: Automated sensors and digital twin platforms are increasingly being deployed for real-time viscosity and yield stress monitoring. Companies like Metrohm are empowering manufacturers to optimize dispersions inline, reducing batch variability and enabling on-the-fly adjustments.
- Customization and Digitalization: Custom clay blends and smart formulation platforms are gaining traction. Borregaard and Ecolab are leveraging data analytics for predictive modeling of clay behavior, assisting operators in preemptively addressing rheological challenges as raw material sources vary.
- Regulatory and Environmental Pressures: As global regulations tighten on volatile organic compounds (VOCs) and hazardous dispersants, manufacturers are shifting towards waterborne and low-toxicity rheology solutions. The European Chemicals Agency (ECHA) continues to drive industry adaptation through new substance restrictions and reporting requirements.
- Sector-Specific Innovations: In oil & gas, companies like SLB are investing in smart drilling fluids with adaptive rheological properties to improve wellbore stability and reduce environmental impact. Similarly, the ceramics and coatings sectors are focusing on dispersions that enable higher solids loading without sacrificing workability or finish quality.
Looking ahead, the interplay of advanced materials, automation, and regulatory compliance will remain central to clay dispersion rheology optimization. Stakeholders are expected to benefit from faster development cycles, reduced waste, and superior end-product performance, positioning the sector for robust, innovation-driven growth through 2025 and beyond.
Market Size, Growth Forecasts, and Global Demand Trends (2025–2028)
The global market for clay dispersion rheology optimization is poised for robust growth from 2025 through 2028, driven by rising demand in sectors such as paints and coatings, ceramics, construction, and oilfield services. Rheological optimization of clay dispersions is crucial for achieving desirable flow properties, stability, and processability in these industries. The ongoing shift toward water-based formulations in coatings and adhesives, particularly in North America, Europe, and parts of Asia-Pacific, continues to propel demand for advanced rheology modifiers and dispersants.
Leading manufacturers of rheology additives and clay dispersions, such as BASF SE and Ashland Inc., have reported strong growth in demand for specialty additives that enhance dispersion stability and viscosity control. For example, BASF has highlighted significant investments in expanding production capacity for its rheology modifier product lines, citing robust order books in 2024 and positive outlooks for 2025–2028, particularly for products targeting water-based and low-VOC systems. Similarly, BYK-Chemie GmbH continues to introduce new additive technologies tailored for optimized clay dispersion and improved application performance in high-volume coatings and composites markets.
Regionally, Asia-Pacific remains the fastest-growing market, with countries like China, India, and Southeast Asian nations investing in infrastructure, automotive, and consumer goods manufacturing, all of which increase the need for optimized clay dispersions. Imerys, a major global supplier of performance minerals, has expanded its presence in Asia, citing the region’s outsized demand for functional additives in paints, paper, and ceramics. In North America and Europe, regulatory pressures to reduce solvent emissions further accelerate the transition to advanced rheology solutions, underpinning steady market expansion.
Key trends shaping the market outlook include the integration of digital rheometry and real-time process monitoring, enabling manufacturers to fine-tune clay dispersion rheology with greater precision and efficiency. Adoption of sustainable and bio-based additive chemistries is also rising, as highlighted by initiatives from Cabot Corporation and Ashland, both of which have introduced new product lines emphasizing environmental compatibility and reduced carbon footprint.
Looking ahead to 2025–2028, industry analysts and manufacturers anticipate annual growth rates in the high single digits for clay dispersion rheology optimization, with innovation in dispersant and thickener chemistries, digital process control, and sustainability set to be key differentiators in the global market space.
Core Technology Innovations in Clay Dispersion Rheology
Clay dispersion rheology optimization remains a critical focus for industries reliant on high-performance suspensions—such as ceramics, paints, and oilfield drilling fluids. In 2025, technological advances are being driven by the increasing demand for tighter process control, sustainability, and resource efficiency. Core innovations are emerging in three interconnected areas: additive development, real-time characterization, and computational modeling.
- Additive Engineering: The design of novel dispersants and rheology modifiers is at the forefront. Companies such as BASF and Dow are introducing next-generation polycarboxylate ethers and tailored surfactants to mitigate clay particle aggregation even in high-solids slurries. These additives are engineered for specific clay types, ionic strengths, and pH ranges, enabling better flowability and reduced viscosity at lower dosages. The latest product releases highlight not only improved performance but also reduced environmental impact, with an emphasis on biodegradable chemistries.
- Real-Time Rheology Sensing: Process industries are increasingly adopting inline and at-line rheology sensors. This shift is exemplified by companies like Anton Paar, which recently launched advanced rheometers capable of providing instantaneous viscosity and yield stress data under manufacturing conditions. Such real-time feedback allows for on-the-fly optimization of dispersant dosing and mixing protocols, minimizing batch-to-batch variability and resource wastage.
- Computational and Data-Driven Approaches: Machine learning and molecular-level simulations are now being deployed to predict dispersion stability and rheological properties from first principles. Sandvik and Imerys, both major players in mineral processing, are investing in digital twins and predictive analytics to streamline clay product formulation. This data-driven optimization reduces development cycles and enables rapid response to raw material variability.
Looking ahead, the convergence of sustainable additive chemistry, smart sensing, and digital modeling is poised to transform clay dispersion rheology. The next few years will likely see closer integration between digital process control platforms and laboratory innovation, with the goal of achieving not just optimal rheological performance, but also lower energy consumption and reduced environmental footprint across the value chain.
Comparative Analysis of Leading Clay Types and Additives
Clay dispersion rheology optimization remains a dynamic focus for manufacturers and end-users seeking improved performance in paints, ceramics, construction, oilfield drilling, and personal care formulations. The comparative rheological behavior of key clay types—especially bentonite, kaolin, attapulgite, and hectorite—continues to inform additive selection and process design. In 2025, advancements are driven by both material science and the integration of sustainable practices.
Bentonite, particularly sodium-based varieties, remains a benchmark for high-swelling, high-viscosity dispersions, and is widely utilized in drilling fluids, foundry sands, and sealants. Companies such as Bentonite Performance Minerals and Imerys have introduced new grades with tailored particle size and surface modifications to enhance thixotropy and anti-settling behavior, allowing for lower dosages and better pumpability. Kaolin clays, on the other hand, are valued for their plate-like morphology and moderate thickening, with KaMin LLC offering high-purity, calcined variants that deliver improved suspension stability in waterborne coatings.
Attapulgite and hectorite, both fibrous and layered in structure, are gaining attention for their unique rheological profiles—exhibiting excellent suspending capacities at low concentrations and good salt tolerance. BASF markets attapulgite-based additives for paints and industrial fluids, capitalizing on their rapid viscosity recovery after shear. For personal care and specialty applications, Elementis has expanded its hectorite product lines, promoting controlled gel strength and clarity in transparent gels.
Additive innovation is central to clay dispersion optimization. Polyacrylates, cellulose ethers, and biopolymers such as xanthan gum are routinely blended with clays to tune yield stress, flow curves, and storage stability. Recent launches by Ashland and Dow feature multifunctional rheology modifiers that enhance dispersion homogeneity and compatibility with pigments or electrolytes.
Looking ahead, the sector anticipates further refinement in clay surface treatments and hybrid additive systems, with a strong push toward bio-based and low-carbon solutions. Digital rheometry and AI-driven formulation, now being piloted by leading suppliers, are expected to accelerate the development of application-specific dispersion profiles. Collectively, these efforts are set to deliver more sustainable, efficient, and high-performing clay dispersions over the next several years.
Major Industry Players and Strategic Partnerships (Citing Imerys.com, basf.com, lkabminerals.com)
Clay dispersion rheology optimization has become a focal point for leading mineral and chemical companies as industries demand higher-performance, more sustainable clay-based systems for coatings, ceramics, paper, and construction. In 2025, the competitive landscape is shaped by a few major players—Imerys, BASF, and LKAB Minerals—all leveraging strategic partnerships, advanced R&D, and proprietary formulations to address evolving technical challenges.
Imerys, a global leader in specialty minerals, continues to innovate in clay dispersion technologies. Their recent focus is on engineered kaolins and bentonites, optimized for low viscosity and high solid loadings while maintaining stable rheological profiles. Imerys collaborates with downstream partners in paints and coatings to refine their dispersant packages, utilizing real-time process analytics and feedback to tune product performance for specific customer applications. In 2025, Imerys has also scaled up pilot programs with major ceramics and construction material manufacturers to co-develop dispersions that reduce energy consumption during processing and improve end-product mechanical properties.
BASF, a key supplier of dispersants and rheology modifiers, is advancing its portfolio of sustainable additives compatible with natural and modified clays. BASF’s 2025 roadmap emphasizes bio-based and low-VOC dispersants to meet tightening regulatory requirements and customer demand for greener solutions. Through open innovation programs and technical partnerships with clay producers and formulators, BASF is developing next-generation dispersants that enhance clay particle separation and suspension stability in high-solid content systems. Early trials with leading paper and paint manufacturers demonstrate improved flow and application properties, as well as potential cost savings due to reduced additive dosages.
LKAB Minerals is expanding its offering of refined ball clays and bentonites specifically tailored for advanced rheology management. In 2025, LKAB Minerals is partnering with industrial users to conduct joint application testing and data sharing, targeting custom clay blends that address unique processing and end-use requirements. Their investments in mineral upgrading and surface treatment technologies allow for tight control over particle size distribution and surface chemistry, which are critical for achieving predictable, tunable rheological performance in complex formulations.
Looking ahead, the next few years will likely see further integration of digital tools—such as AI-driven formulation optimization and in-line rheology monitoring—across the operations of major clay and additive suppliers. Strategic alliances and technical collaborations among these industry leaders are expected to accelerate the transition toward more efficient, sustainable, and application-specific clay dispersion solutions.
Regulatory Environment and Industry Standards (Referencing imerys.com and theclaymineralsociety.org)
The regulatory environment and evolving industry standards are playing a pivotal role in shaping the landscape of clay dispersion rheology optimization as we move through 2025 and into the foreseeable future. Stringent requirements around product consistency, safety, and environmental impact are driving manufacturers and formulators to refine their approaches to clay dispersion and its rheological behavior across industries such as ceramics, paints, coatings, and oilfield drilling fluids.
In 2025, regulatory agencies are increasingly emphasizing the need for detailed characterization of clay dispersions, particularly regarding their flow properties and stability. This is leading to a greater reliance on advanced rheological measurement techniques and standardized protocols for testing dispersions under relevant process conditions. Industry bodies and technical societies are at the forefront of these developments. For example, The Clay Minerals Society continues to update best practice guidelines for the evaluation of clay dispersion properties, focusing on reproducibility and alignment with international standards. These guidelines are now being integrated into quality control frameworks by leading producers and end-users, ensuring traceability and compliance.
Meanwhile, companies such as Imerys, a global leader in mineral-based specialty solutions, are responding to these regulatory shifts by investing in research and development of new clay grades engineered for optimized dispersion rheology. Imerys has reported the adoption of more sustainable processing additives and surface modification technologies aimed at reducing the use of volatile organic compounds (VOCs) and improving the environmental profile of their clay products. This is in direct response to evolving regulatory constraints on emissions and hazardous substances, particularly in the European Union and North America.
Data from recent industry trials indicate that these new clay formulations can achieve superior dispersion stability and controlled viscosity profiles, even at lower additive dosages, thus supporting both compliance and cost-efficiency. Industry standards for clay dispersion rheology are also being harmonized globally, with increased collaboration between manufacturers, standards organizations, and end-user sectors to create unified testing protocols and reporting formats.
Looking ahead to the next few years, regulatory momentum is expected to further drive innovation in dispersion optimization, especially with anticipated updates to REACH regulations in Europe and parallel initiatives in the United States and Asia. The focus will likely extend beyond performance to encompass lifecycle impacts, recyclability, and the broader sustainability of clay-based products. Companies poised to adapt to these changes, investing in both compliance and technical excellence, are expected to maintain a strong competitive advantage as industry standards evolve.
Emerging Application Sectors: Construction, Ceramics, Drilling, and Beyond
Clay dispersion rheology optimization is witnessing significant advances in 2025, driven by the expanding demands of several key sectors, notably construction, ceramics, and drilling. The optimization of the flow, stability, and workability of clay suspensions is central to improving product performance and process efficiency across these industries. In construction, the rise in sustainable building materials and the increasing adoption of advanced clays in self-compacting concrete and geotechnical applications have placed renewed emphasis on precise rheological control. Companies such as Imerys are actively developing engineered clay additives designed to optimize yield stress and viscosity, thereby enabling enhanced workability and pumpability without compromising structural integrity.
In the ceramics sector, the trend toward complex, high-precision components—especially for electronics and medical devices—demands tighter rheological specifications for clay slurries. Manufacturers like Kao Corporation are focusing on dispersant technologies that prevent particle aggregation and allow for consistent casting and molding. This not only improves the sintering behavior and final product quality but also reduces energy consumption during processing, aligning with broader sustainability goals.
The drilling industry, particularly in oil, gas, and geothermal exploration, continues to rely on optimized clay-based drilling fluids. The formulation of these fluids is evolving, with industry leaders such as Halliburton deploying advanced rheology modifiers to maintain suspension stability under extreme temperature and pressure conditions. This ensures effective cuttings transport and wellbore stability, both critical for deep and unconventional wells.
Across these sectors, digitalization and real-time process monitoring are becoming increasingly integrated into rheology optimization strategies. For example, Mettler-Toledo is developing in-line rheometry solutions that allow manufacturers to monitor and adjust clay dispersion properties continuously during production. This reduces waste, shortens development cycles, and accelerates time-to-market for new formulations.
Looking ahead to 2026 and beyond, the outlook for clay dispersion rheology optimization is marked by continued collaboration between material suppliers, instrument manufacturers, and end-users. Expect further advancements in smart additives, data-driven process control, and the integration of rheological data with broader process automation platforms. These trends position clay-based materials as more adaptable and competitive, not only in established markets but also in emerging applications such as 3D printing and advanced composites.
Sustainability Challenges and Green Rheology Solutions
Clay dispersion rheology optimization is facing a pivotal shift in 2025, driven by the convergence of sustainability imperatives and advances in formulation technology. The traditional use of synthetic dispersants and rheology modifiers—often derived from petrochemical sources—has come under scrutiny due to environmental persistence and potential toxicity. In response, the industry is rapidly adopting green chemistry principles, focusing on biobased and biodegradable alternatives to minimize environmental impact.
Major clay suppliers and additive manufacturers have launched initiatives to replace conventional dispersants with sustainable polymers and natural thickeners. BYK and Imerys are investing in the development of next-generation additives sourced from renewable materials, such as polysaccharides and modified celluloses, to enhance clay dispersion stability and control viscosity without compromising on performance. These innovations are particularly relevant for waterborne paints, coatings, and construction materials, where regulatory pressure is mounting to lower volatile organic compounds (VOCs) and microplastic content.
Recent field trials, as reported by BYK, demonstrate that biopolymer-based rheology modifiers can achieve comparable—or in some formulations, superior—thixotropy and anti-settling characteristics relative to synthetic alternatives. For instance, the use of starch and xanthan gum derivatives in clay dispersions has resulted in improved workability and freeze-thaw stability, which are critical for construction and ceramic applications.
Digital process monitoring is another emerging trend, with companies like Imerys deploying real-time rheological measurement systems to optimize dispersion parameters dynamically. This data-driven approach enables manufacturers to reduce overdosing of additives, thereby cutting costs and lowering the environmental burden of production processes.
Looking ahead, the sector is expected to see broader adoption of lifecycle assessment (LCA) tools to evaluate the environmental footprint of rheology optimization strategies. These assessments, now integral to product development at BYK and Imerys, are informing choices on raw materials and process modifications to further decarbonize clay dispersion operations. As regulatory requirements tighten and consumer demand for greener products grows, the transition toward sustainable clay rheology solutions is set to accelerate, with a focus on circularity, resource efficiency, and transparency across the value chain.
Investment Hotspots and R&D Funding Trends
Investment in clay dispersion rheology optimization is accelerating as industries recognize the pivotal role of rheology in process efficiency, product quality, and sustainability. In 2025, the ceramics, paints & coatings, and oil & gas sectors are driving R&D funding, motivated by the need for more stable, energy-efficient, and sustainable dispersions that can handle increasingly complex formulations.
A significant proportion of recent investments has targeted advanced rheological modifiers and dispersants, particularly those with improved environmental profiles. For example, BYK-Chemie GmbH announced expanded production capacities for sustainable rheology additives, reflecting surging demand in ceramics and coatings. Similarly, BASF SE is channeling R&D resources toward next-generation dispersants that reduce energy input and optimize clay particle distribution for paints and construction materials.
In North America, Imerys continues to invest in its Georgia-based technical center, focusing on optimizing kaolin clay dispersions for paper and performance mineral applications. Their innovation pipeline includes projects to fine-tune particle size distribution and surface chemistry, directly impacting rheological behavior and end-use performance.
Meanwhile, the oilfield sector is a notable hotspot, with SLB (Schlumberger) and Halliburton investing in dispersion additives that enhance drilling fluid stability under high-temperature, high-pressure conditions. These investments are responding to data showing that improved rheology reduces non-productive time and lowers operational costs.
The outlook for 2025 and the next few years points to continued growth in R&D funding, particularly for digital rheology optimization tools. Companies like Malvern Panalytical are partnering with manufacturers to deploy real-time rheological monitoring and predictive modeling, allowing for dynamic adjustment of dispersion protocols.
Government and cross-industry consortia are also stepping up. The CeramTec Group is participating in EU-funded initiatives to develop sustainable ceramic processing, allocating resources to projects that optimize clay dispersion rheology for additive manufacturing.
In summary, investment hotspots in 2025 are centered on green additives, digitalization, and process-specific customization. Industry leaders are expected to ramp up funding for technologies that enable tighter control over particle-particle interactions and flow properties, with sustainability and efficiency as primary drivers.
Future Outlook: Disruptive Technologies and Market Opportunities to 2028
The period leading up to 2028 is expected to bring significant advancements in clay dispersion rheology optimization, driven by both disruptive technologies and evolving market demands. Key players in the minerals and additives industries are investing in next-generation rheology modifiers and dispersion agents, with a focus on sustainability, process efficiency, and product performance.
One major trend is the rapid integration of digitalization and artificial intelligence (AI) into rheological modeling and process control. Imerys, a global leader in mineral-based solutions, has implemented digital platforms for real-time monitoring of dispersion properties and predictive modeling, which are expected to reduce formulation times and iterate more efficiently toward target rheological profiles. This move towards data-driven optimization is anticipated to accelerate the development of tailored solutions for paints, ceramics, drilling fluids, and other clay-based applications.
Sustainability remains a critical driver. Companies like BYK are developing bio-based and low-VOC rheology modifiers to meet tightening environmental regulations and shifting consumer expectations. These new additives are designed for compatibility with a range of clay minerals, offering improved dispersion stability while reducing ecological impact. The adoption rate of such technologies is projected to increase sharply by 2028, especially in regions with stringent regulatory frameworks.
Additionally, the ongoing refinement of nanotechnology is creating opportunities for disruptive advances in clay dispersion. BASF has recently unveiled research into nano-engineered surface treatments for clays, which enable more precise control over interparticle interactions and viscosity profiles. These innovations allow for finer tuning of product characteristics—such as thixotropy and yield stress—essential for high-performance coatings, sealants, and construction materials.
Market opportunities are also emerging from the increasing demand for energy-efficient and low-carbon manufacturing processes. LKAB Minerals is advancing mineral processing methods that reduce energy consumption and waste generation, which directly impact the rheology and dispersion qualities of clay products. Such process optimizations are predicted to become a competitive differentiator in global markets by 2028.
In summary, the future of clay dispersion rheology optimization will be shaped by the convergence of digitalization, sustainable chemistry, and advanced materials science. Companies that leverage these disruptive technologies are positioned to capture significant market share, as end-users—from industrial coatings to construction—seek more efficient, compliant, and higher-performing clay-based solutions.