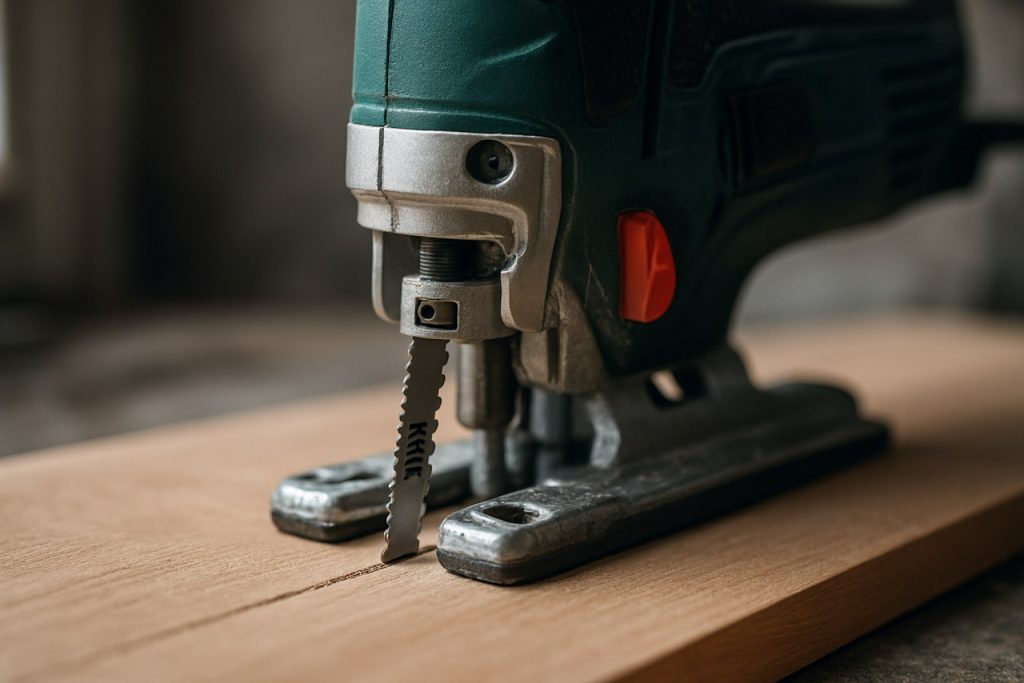
Table of Contents
- Executive Summary: Key Insights and Forecasts (2025–2030)
- Market Size and Growth Projections: High-Precision Jigsaw Blades
- Innovations in Blade Materials: From Carbide Composites to Advanced Coatings
- Precision Manufacturing: Automation, Robotics, and Digital Quality Control
- Application Trends: Automotive, Aerospace, Construction, and Electronics
- Competitive Landscape: Major Manufacturers and Strategic Moves
- Global Supply Chain and Sourcing Dynamics
- Sustainability and Eco-Friendly Blade Engineering Initiatives
- Emerging Challenges: Raw Materials, Regulation, and Intellectual Property
- Future Outlook: Disruptive Technologies and Strategic Opportunities
- Sources & References
Executive Summary: Key Insights and Forecasts (2025–2030)
The high-precision jigsaw blade engineering sector is poised for dynamic advancements from 2025 through 2030, driven by escalating demand for superior cutting accuracy, material versatility, and operational longevity. As industries such as automotive, aerospace, and advanced manufacturing intensify their requirements for intricate component fabrication, manufacturers are responding with innovations focused on micro-geometry optimization, advanced alloys, and surface treatments.
Market leaders are deploying proprietary technologies in metallurgy and edge design. For instance, Bosch is investing in carbide-tipped and bi-metal blade innovations, aiming to deliver enhanced wear resistance and sharper cuts in composite and exotic materials. Similarly, Stanley Black & Decker continues to refine its DEWALT-branded offerings with precision-ground teeth and vibration-dampening architectures, targeting professional-grade applications where cut quality and blade life are paramount.
Recent years have seen the integration of digital manufacturing methods—such as laser-assisted sharpening and computer numerical control (CNC) profiling—enabling tighter tolerances and improved batch consistency. These advancements are expected to accelerate, with Lenox and other leading producers deploying automated inspection systems to ensure each blade meets stringent dimensional and performance criteria.
The outlook for high-precision jigsaw blade engineering is further strengthened by the growing adoption of Industry 4.0 principles. Real-time process monitoring, data-driven quality assurance, and predictive maintenance are becoming standard in production lines, contributing to reduced downtime and increased throughput. Sustainability also emerges as a focal point, with companies like Bosch and Stanley Black & Decker implementing recycling programs for spent blades and investing in greener manufacturing processes.
- Key insights for 2025–2030:
- Rapid material innovation will support the cutting of next-generation composites and alloys.
- Precision automation and digitalization will underpin consistent blade quality and customizability.
- End-user industries will demand blades with longer service lives and reduced vibration for faster, cleaner cuts.
- Sustainability-driven product lifecycles and recycling initiatives will become more prominent.
Overall, the sector is expected to experience sustained growth, with leading manufacturers leveraging R&D and digitalization to meet evolving industrial requirements and environmental standards.
Market Size and Growth Projections: High-Precision Jigsaw Blades
The market for high-precision jigsaw blade engineering is poised for steady expansion in 2025 and the following years, driven by evolving demands from woodworking, metal fabrication, and advanced manufacturing sectors. Precise growth figures are closely guarded by direct industry participants, but multiple indicators suggest robust momentum. The adoption of automated and CNC-driven cutting systems, which rely on superior blade accuracy, is a prominent growth driver. Leading manufacturers such as Robert Bosch GmbH and Milwaukee Electric Tool Corporation report increasing R&D investment and product portfolio expansion aimed specifically at high-tolerance industrial applications.
The construction and furniture industries—key end-users—continue to demand finer cuts and improved edge quality, pushing OEMs to develop blades with advanced tooth geometries, optimized alloys, and precision-ground finishes. For instance, Robert Bosch GmbH continues to introduce advanced bi-metal and carbide-tipped blades for both domestic and export markets, responding to rising demand for materials like engineered wood and composite panels, which require superior blade performance.
In 2025, the North American and European markets are expected to maintain their dominance due to sustained investment in infrastructure and high-value manufacturing. However, Asia-Pacific is anticipated to show above-average growth rates, spurred by rapid industrialization and technological upgrades in China, India, and Southeast Asia. Companies such as Makita Corporation and HiKOKI Power Tools are expanding their offerings of industrial-grade jigsaw blades in these regions, frequently highlighting precision and longevity as core differentiators.
Digitalization across the supply chain is further catalyzing market growth. Enhanced feedback loops between end-users and blade manufacturers are shortening product development cycles, allowing faster adaptation to shifting material trends and tolerance requirements. As sustainability remains a key concern, there is a notable uptick in the engineering of recyclable and longer-lasting blade materials, with major producers like Stanley Black & Decker investing in eco-friendly product lines.
While price competition remains intense, the market outlook for high-precision jigsaw blade engineering in 2025 and beyond is positive, with innovation, material science, and digital connectivity acting as primary growth levers. Industry leaders are expected to accelerate launches of specialized blade designs, further broadening the application landscape and reinforcing the sector’s upward trajectory.
Innovations in Blade Materials: From Carbide Composites to Advanced Coatings
The evolution of high-precision jigsaw blade engineering in 2025 is characterized by significant advancements in blade materials, notably the integration of carbide composites and state-of-the-art surface coatings. These developments are fundamentally driven by the demand for increased cutting accuracy, extended tool life, and adaptability across a wide range of materials, from hardwoods to advanced composites.
Carbide-tipped blades have become an industry standard for high-precision applications due to their exceptional hardness, wear resistance, and ability to maintain sharp edges over prolonged use. Leading manufacturers such as Bosch and Milwaukee Tool have expanded their offerings of tungsten carbide jigsaw blades, specifically engineered for demanding tasks like cutting through stainless steel, fiber cement, and abrasive laminates. In 2025, these blades are seeing further enhancements through the optimization of carbide grain size and binder composition, resulting in improved toughness and reduced edge micro-chipping.
A transformative trend in 2025 is the adoption of advanced coatings, including titanium nitride (TiN), titanium aluminum nitride (TiAlN), and diamond-like carbon (DLC). These coatings significantly reduce friction and thermal buildup, enabling cleaner cuts and allowing higher cutting speeds without compromising blade integrity. DeWalt has introduced coated high-speed steel (HSS) and bi-metal blades targeting the professional woodworking and metal fabrication sectors, citing enhanced blade longevity and smoother, burr-free finishes. Similarly, Lenox is employing multi-layer coating technologies on their fine-tooth jigsaw blades, aimed at minimizing blade deformation and tooth wear during extended, high-precision operations.
Another noteworthy innovation is the emergence of composite blade cores, which combine the rigidity of high-strength steel with the vibrational dampening properties of engineered polymers. This hybrid construction, being piloted by select European manufacturers, addresses the persistent challenge of blade wander and vibration in intricate cuts, promising a step-change in jigsaw accuracy and operator comfort.
Looking ahead to the next few years, the high-precision jigsaw blade sector is set to benefit from further material science breakthroughs. Ongoing research into nano-structured carbide matrices and self-lubricating coatings could yield blades with substantially longer service intervals and the ability to tackle next-generation engineered materials. As end-user expectations for accuracy and efficiency rise, manufacturers are expected to focus on sustainable material sourcing and recyclable blade designs, aligning innovation with environmental stewardship—a trend anticipated by industry leaders like Bosch.
Precision Manufacturing: Automation, Robotics, and Digital Quality Control
High-precision jigsaw blade engineering has entered a new era in 2025, driven by advancements in precision manufacturing, automation, robotics, and digital quality control. The integration of these technologies is enabling manufacturers to meet the stringent demands of industries such as aerospace, automotive, and advanced woodworking, where tolerance margins often fall below 0.05 mm. The ongoing digital transformation is reshaping the entire production lifecycle of jigsaw blades, from material selection to final inspection.
Automated production lines, utilizing collaborative robots (cobots) and advanced CNC systems, now perform critical tasks such as laser cutting, edge grinding, and tooth setting with unprecedented accuracy and repeatability. Leading manufacturers, including Robert Bosch GmbH and Makita Corporation, have implemented fully automated cells capable of producing high volumes of blades while maintaining consistent quality at every stage. These systems leverage real-time data analytics to adjust machining parameters, optimize tool wear, and minimize material wastage.
Digital quality control has become a cornerstone of precision blade manufacturing. In-line optical metrology and non-contact measurement systems—such as laser triangulation and high-resolution machine vision—are now standard. These technologies allow for 100% inspection of each blade, ensuring dimensional accuracy and tooth geometry within micron-level tolerances. Companies like Stanley Black & Decker and DeWalt are investing in AI-driven quality analytics to identify patterns in defect occurrence and implement predictive maintenance for machinery, thereby reducing downtime and increasing throughput.
Looking forward, the next few years are expected to see further convergence of robotics and digital twins in blade engineering. Digital twins—virtual representations of manufacturing processes—allow for simulation and optimization before physical production, reducing prototyping costs and accelerating time-to-market. Real-time feedback from robotic cells is being used to update these digital twins, creating closed-loop systems that continually self-optimize for yield and precision. Moreover, the adoption of Industry 4.0 standards among major blade producers is fostering greater interoperability and data transparency across the supply chain.
With these technological advancements, high-precision jigsaw blade engineering is poised for significant gains in productivity, quality assurance, and customization. This evolution is expected to support the increasing demands of industries requiring specialized cutting solutions, while also enabling manufacturers to respond rapidly to changing market requirements and sustainability pressures.
Application Trends: Automotive, Aerospace, Construction, and Electronics
In 2025, high-precision jigsaw blade engineering continues to gain traction across diverse industries, particularly automotive, aerospace, construction, and electronics. The demand for tighter tolerances, advanced materials, and superior cutting performance is shaping both the development and application of these specialized blades.
In the automotive sector, manufacturers are increasingly utilizing high-precision jigsaw blades to achieve intricate cuts in lightweight metals and composites, supporting the trend toward vehicle weight reduction and structural optimization. Leading toolmakers such as Bosch and Stanley Black & Decker are focusing on carbide-tipped and bi-metal blades that maintain edge sharpness even when cutting high-strength steels and aluminum alloys now prevalent in electric vehicle chassis and battery housings. The shift to electric vehicles is expected to further drive demand for blades capable of handling new, engineered materials with precision and repeatability.
Within the aerospace industry, the adoption of advanced jigsaw blade technologies is crucial for processing composite materials, titanium alloys, and honeycomb structures. Aerospace manufacturers, including suppliers to companies like Airbus and Boeing, require blades that deliver burr-free, accurate cuts to minimize secondary finishing. Blade producers are responding by integrating specialized tooth geometries and coatings—such as titanium nitride—for enhanced wear resistance and reduced heat buildup during extended cutting cycles.
The construction sector is witnessing increased demand for high-precision jigsaw blades in applications ranging from interior fit-outs to façade fabrication. Modern construction materials, including engineered woods, laminates, and composite panels, necessitate blades that can cut cleanly and efficiently. Companies like Makita and Hilti are emphasizing blade versatility and quick-change systems, enabling tradespeople to switch between material types without compromising on cut quality or productivity.
In the electronics industry, the drive for miniaturization and the use of fragile substrates such as PCB laminates and plastics require ultra-fine, precision jigsaw blades. Blade manufacturers are developing micro-toothed and diamond-grit designs to reduce chipping and ensure clean edges, supporting applications in device prototyping and small-batch production. This segment is expected to see continued innovation as the complexity and material diversity of electronic devices increase.
Looking ahead through the next few years, the trajectory for high-precision jigsaw blade engineering points toward further material specialization, digital integration (such as blade wear sensors), and closer collaboration between tool manufacturers and end users. These advances will underpin productivity improvements and higher-quality outputs across automotive, aerospace, construction, and electronics sectors.
Competitive Landscape: Major Manufacturers and Strategic Moves
The competitive landscape of high-precision jigsaw blade engineering in 2025 is marked by strategic investments, technological advancements, and global expansion among leading manufacturers. The market is dominated by established players such as Robert Bosch GmbH, Stanley Black & Decker, Makita Corporation, and Hilti Group, all of whom have intensified efforts to differentiate their offerings through precision engineering and material innovation.
Recent years have seen Robert Bosch GmbH continue to expand its global manufacturing footprint, strengthening its presence in both Europe and Asia. Bosch’s ongoing investment in automated production lines and advanced metallurgy has enabled the company to consistently deliver blades with micron-level tolerances, crucial for industries demanding high precision cuts. In 2025, Bosch’s push towards sustainability is also evident, with increased use of recyclable packaging and eco-friendly blade coatings.
Stanley Black & Decker, through its DEWALT brand, has focused on multi-material blade systems and proprietary tooth geometries, aiming to address evolving industry requirements for versatility and durability. The company’s integration of AI-driven manufacturing analytics in its North American facilities has allowed for tighter quality control and rapid prototyping of new blade designs. Strategic partnerships with tool retailers and professional trade associations have helped Stanley Black & Decker maintain a strong distribution network globally.
Makita Corporation has leveraged its expertise in power tool ecosystems, offering high-precision jigsaw blades that are optimized for cordless platforms. The company is investing in new carbide and bi-metal technologies, aiming to extend blade life and performance, especially for demanding applications in construction and manufacturing. Makita’s regional R&D centers, particularly in Asia-Pacific, are expected to play a pivotal role in product development through 2026.
Meanwhile, Hilti Group is targeting the professional segment with premium blades engineered for specialized tasks such as metal fabrication and architectural woodworking. Hilti’s strategy includes direct customer engagement through digital platforms and on-site demonstrations, emphasizing the precision and reliability of its jigsaw blade portfolio.
Looking ahead, competition is expected to intensify as manufacturers invest in smart manufacturing, sustainable materials, and digital integration. Strategic collaborations with OEMs and end-users, as well as continuous innovation in blade geometry and coatings, are likely to define the sector’s competitive dynamics through the latter half of the decade.
Global Supply Chain and Sourcing Dynamics
The global supply chain and sourcing landscape for high-precision jigsaw blade engineering is in a state of notable transition as 2025 unfolds. Central to this evolution are the increasing demands for tighter tolerances, advanced materials, and sustainable practices, all of which are influencing sourcing strategies and logistics across key markets in North America, Europe, and Asia-Pacific.
Major manufacturers such as Bosch, Makita, and Stanley Black & Decker continue to invest in vertically integrated production and regional diversification to mitigate risks from geopolitical tensions, shipping disruptions, and fluctuating raw material costs. In the wake of recent global disruptions, these companies are focusing on nearshoring and multi-sourcing strategies—prioritizing suppliers in stable regions and establishing secondary supply lines to ensure resilience and continuity for high-precision blade components such as high-speed steel (HSS), bi-metal alloys, and carbide tips.
Precision in blade engineering relies heavily on the consistent supply of specialty steel and advanced coatings. Producers like Sandvik are expanding their global footprint, leveraging both European and Asian facilities to meet just-in-time manufacturing requirements for jigsaw blade OEMs. This is accompanied by a trend toward procurement partnerships with steel specialists capable of delivering ultra-fine tolerances, especially as custom blade geometries and multi-material cutting capabilities gain traction.
Simultaneously, digital supply chain management is being widely adopted. Real-time inventory monitoring, predictive analytics, and supplier traceability systems are being rolled out by key players such as Bosch and Stanley Black & Decker to increase transparency and responsiveness in the face of demand variability. These digital advancements are critical as demand for high-precision blades surges in sectors like automotive, aerospace, and green construction.
Looking forward, supply chain sustainability is becoming a strategic imperative. Companies are increasingly sourcing recycled steel and implementing closed-loop logistics to reduce emissions and comply with tightening environmental standards, particularly in the EU and North America. The outlook for the next several years suggests further investments in automation, regional supply hubs, and collaborative supplier ecosystems, all designed to support the rapid innovation cycles and quality benchmarks that define the high-precision jigsaw blade sector.
Sustainability and Eco-Friendly Blade Engineering Initiatives
The drive toward sustainability is reshaping high-precision jigsaw blade engineering in 2025, as manufacturers and suppliers respond to environmental regulations and evolving market preferences. Key players are integrating eco-friendly practices throughout their production cycles, with a focus on material sourcing, energy usage, waste reduction, and end-of-life blade management.
Material innovation is at the forefront of sustainability efforts. Leading companies are increasingly adopting recycled steel and carbide alloys to reduce the carbon footprint of their blades, while maintaining the stringent tolerances required for high-precision performance. For example, Robert Bosch GmbH and Stanley Black & Decker have both implemented programs to incorporate recycled metals and optimize material efficiency, reducing the demand for virgin resources. Simultaneously, manufacturers are investing in advanced surface coatings that extend blade life and reduce the frequency of replacement, minimizing material waste.
Process improvements are equally vital. Modern production lines increasingly use renewable energy sources and high-efficiency machinery. Festool GmbH highlights the use of green electricity at its facilities, aligning with its broader sustainability objectives. These shifts not only help reduce greenhouse gas emissions but also reflect a broader industry trend toward transparent, lifecycle-based environmental accounting.
Packaging and logistics are also undergoing transformations. Companies are reducing single-use plastics and prioritizing recyclable or biodegradable materials in blade packaging. Makita Corporation and Hitachi, Ltd. have both introduced packaging redesigns to lower environmental impacts and streamline transportation, further decreasing their overall carbon footprint.
End-of-life blade management is gaining attention, with take-back and recycling programs under development or expansion. As regulatory frameworks tighten—especially in the European Union—manufacturers anticipate increased responsibility for post-consumer blade recovery and recycling. Collaborative efforts between manufacturers and industry bodies, such as the Verband Deutscher Maschinen- und Anlagenbau (VDMA), are underway to set best practices and support circular economy models.
Looking ahead, sustainability is expected to remain central to high-precision jigsaw blade engineering. Continued investment in green metallurgy, eco-design, and closed-loop supply chains will likely define industry leaders in the next several years, with transparent ESG reporting and compliance with international standards becoming prerequisites for market participation.
Emerging Challenges: Raw Materials, Regulation, and Intellectual Property
The landscape of high-precision jigsaw blade engineering in 2025 is shaped by a dynamic interplay of raw material sourcing, regulatory frameworks, and intellectual property (IP) considerations. As demand for advanced cutting solutions intensifies across automotive, aerospace, and construction sectors, manufacturers are encountering new complexities in ensuring both performance and compliance.
A primary challenge is the volatility in the supply and pricing of high-grade steels, tungsten, and carbide—materials essential for fabricating durable, precise blade teeth. Global disruptions in mining and metallurgy have led to notable price swings and sporadic shortages, compelling leading manufacturers such as Bosch and Stanley Black & Decker to diversify suppliers and invest in recycling initiatives. Recent efforts include increased use of recycled carbide and research into alternative alloys to maintain cutting standards without overreliance on critical raw materials.
From a regulatory perspective, evolving standards around workplace safety, emissions, and sustainable manufacturing are prompting companies to re-engineer not just blades but entire production lines. In the European Union, the tightening of REACH chemical regulations and the implementation of stricter eco-design directives are pushing jigsaw blade manufacturers to minimize use of hazardous substances and increase product traceability. Firms such as Festool are responding by adopting cleaner coating processes and transparent supply chain documentation to assure compliance and market access.
Intellectual property protection remains a pivotal concern as technological innovation accelerates. Advanced tooth geometries, composite layering, and proprietary heat-treating techniques are at the heart of competitive differentiation. However, the rapid proliferation of counterfeit and patent-infringing products, particularly in online marketplaces, threatens margins and brand reputation. In response, established players like Makita are expanding their patent portfolios and collaborating with international customs bodies to monitor and enforce IP rights. Furthermore, the digitization of design files raises concerns about unauthorized reproduction, pushing the sector to explore digital watermarking and blockchain-based tracking for sensitive CAD assets.
Looking ahead, high-precision jigsaw blade manufacturers are expected to intensify investments in sustainable sourcing, regulatory adaptation, and digital IP defense. The interplay of these challenges will not only shape product innovation but also determine the global competitiveness of industry leaders in the coming years.
Future Outlook: Disruptive Technologies and Strategic Opportunities
The field of high-precision jigsaw blade engineering is undergoing rapid transformation, driven by technological advancements and evolving market demands. As of 2025, key players in the industry are accelerating the adoption of next-generation materials and manufacturing processes to address challenges in precision, durability, and application-specific performance.
One of the most significant trends is the integration of advanced metallurgy and coating technologies. Manufacturers are increasingly deploying tungsten carbide, bi-metal composites, and proprietary alloys to enhance cutting accuracy and blade longevity. Innovations in surface treatments—such as titanium nitride coatings—are reducing friction and heat buildup, thereby extending blade life in high-volume industrial applications. For example, Robert Bosch GmbH and Stanley Black & Decker have introduced lines of jigsaw blades specifically engineered for ultra-fine woodworking and composite material cutting, leveraging these material advances.
Precision engineering is also benefiting from digitalization. The adoption of computer-aided design (CAD) and simulation tools is enabling manufacturers to optimize tooth geometry, gullet spacing, and blade thickness for specific substrates. This move towards application-specific customization is expected to intensify through 2025 and beyond, as industrial clients seek tailored solutions for sectors such as aerospace, automotive, and advanced construction. Companies like Lenox (a Stanley Black & Decker brand) are at the forefront, offering customizable blade configurations to meet industry-specific tolerances and cutting requirements.
Another disruptive area is the incorporation of smart manufacturing and Industry 4.0 principles. Real-time quality control, enabled by machine vision and in-line metrology, is improving the consistency and traceability of blade production. This is particularly relevant as global supply chains demand higher levels of certification and documentation for safety-critical applications. Robert Bosch GmbH and Makita Corporation have signaled investments in advanced automation and data-driven manufacturing systems, underpinning their strategies for market leadership.
Looking ahead, the next few years are likely to see disruptive opportunities in the form of additive manufacturing (3D printing) for rapid prototyping and niche blade production. This could further shrink development cycles and enable unprecedented design freedom. Moreover, sustainability considerations—such as recyclable materials and energy-efficient production—are set to become strategic differentiators as regulations tighten and end-users prioritize eco-friendly products. Companies actively investing in R&D and digital capabilities are best positioned to capitalize on these shifts, ensuring high-precision jigsaw blade engineering remains at the cutting edge of industrial tooling technology.