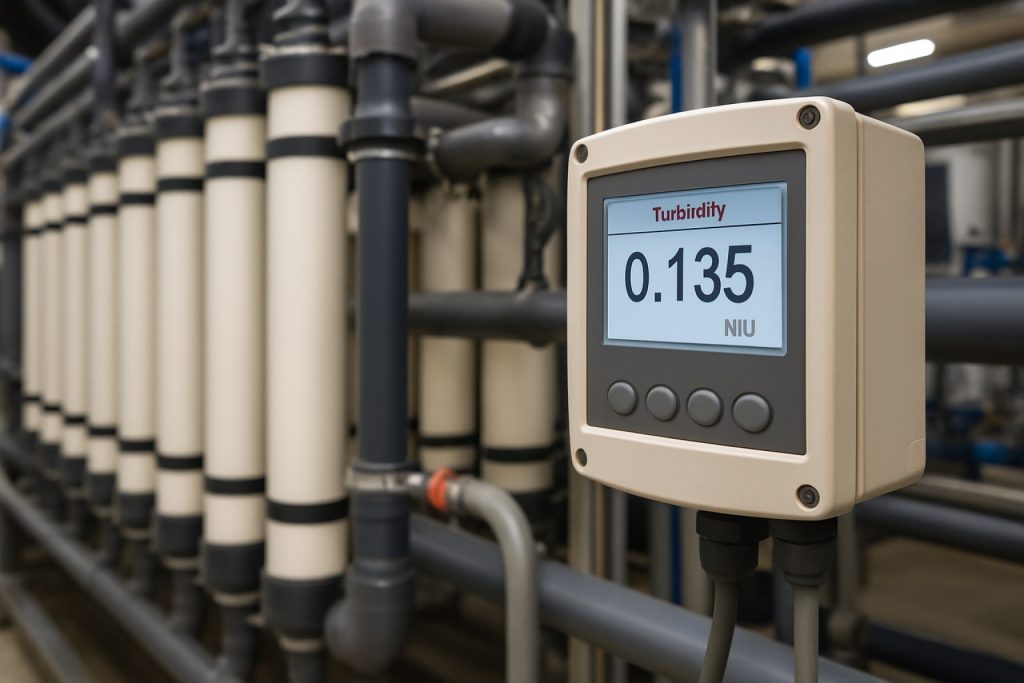
Table of Contents
- Executive Summary: 2025 Outlook and Key Takeaways
- Market Size & Growth Forecasts Through 2030
- Technological Advances in Turbidity Sensors for Ultrafiltration
- Leading Players and New Entrants (e.g. s::can.com, endress.com, hach.com)
- Regulatory Trends and Industry Standards for Water Quality
- Integration with Digital Monitoring and Process Automation
- Application Deep Dive: Municipal, Industrial, and Emerging Sectors
- Competitive Landscape and Strategic Partnerships
- Challenges: Fouling, Calibration, and Maintenance Innovations
- Future Outlook: Disruptive Trends and Investment Hotspots
- Sources & References
Executive Summary: 2025 Outlook and Key Takeaways
Turbidity instrumentation continues to play an indispensable role in the performance and compliance of ultrafiltration (UF) systems, particularly as global standards tighten and water reuse becomes a critical priority. In 2025, the sector is experiencing sustained growth, driven by both regulatory requirements and the rapid adoption of digitalization and automation within water treatment facilities. As ultrafiltration becomes more prevalent for municipal water, industrial reuse, and wastewater polishing, the demand for precise and reliable turbidity measurement is intensifying.
Recent developments in 2025 include the proliferation of compact, low-maintenance turbidity sensors tailored for integration with UF skids, membrane modules, and distributed treatment units. Leading manufacturers such as Hach, Endress+Hauser, and Xylem have introduced advanced optical and nephelometric turbidity meters that offer enhanced sensitivity at very low NTU (Nephelometric Turbidity Unit) ranges, aligning with the stringent post-filtration limits set by regulators in North America, Europe, and parts of Asia. For example, in the United States, the Environmental Protection Agency’s Surface Water Treatment Rule commonly requires post-filtration turbidity below 0.3 NTU in 95% of samples, further underscoring the necessity of high-precision instrumentation.
A defining trend in 2025 is the growing integration of turbidity instruments with digital platforms and supervisory control and data acquisition (SCADA) systems. This connectivity enables real-time monitoring and predictive maintenance, supporting operators in rapid response to membrane fouling events and process upsets. Sensor manufacturers are enhancing data analytics capabilities, providing actionable insights through cloud-based dashboards and mobile interfaces. Notably, Swan Analytical Instruments and Yokogawa Electric Corporation have expanded their offerings to include remote diagnostics and automated calibration functions, reducing operational costs and downtime.
Looking ahead, the outlook for turbidity instrumentation in UF systems remains robust into the next several years. Market drivers include the expansion of decentralized water treatment solutions, stricter effluent discharge norms, and the ongoing replacement of legacy sensors to meet digital transformation goals. Continued innovation is anticipated in sensor miniaturization, reagent-free operation, and self-cleaning mechanisms, further supporting the reliability of UF processes in both developed and emerging markets.
- The adoption of advanced, connected turbidity measurement is now a baseline expectation for UF installations.
- Digital integration and predictive analytics are reshaping operational best practices.
- Manufacturers are focusing on ultra-low NTU detection and maintenance-free designs to support high regulatory and operational demands.
Market Size & Growth Forecasts Through 2030
The market for turbidity instrumentation integrated into ultrafiltration (UF) systems is experiencing robust growth, with demand driven by stricter water quality regulations, the expansion of municipal and industrial water treatment infrastructure, and an increased focus on real-time process optimization. As of 2025, global adoption rates of online turbidity monitoring devices—critical for both regulatory compliance and operational efficiency within UF processes—are accelerating across key sectors, including drinking water, wastewater, food & beverage, and pharmaceutical manufacturing.
Leading instrumentation companies such as Hach, SUEZ Water Technologies & Solutions, and Endress+Hauser report double-digit annual growth in sales of advanced optical and laser-based turbidity sensors specifically designed for integration with membrane filtration skids. According to Hach, the uptake of their TU5 series turbidimeters in UF applications has risen sharply over the past two years, attributed to both regulatory pressures and the need for early fouling detection and membrane integrity assurance. Endress+Hauser similarly highlights increased demand for their Turbimax CUS52D and CUS51D sensors, which are widely deployed in continuous monitoring setups for both municipal and industrial UF installations.
Geographically, Asia-Pacific is projected to exhibit the fastest growth rate through 2030, propelled by large-scale water infrastructure upgrades in China and India, as well as government-backed initiatives targeting reduction in non-revenue water and improvement in potable water quality. North America and Europe remain substantial markets, driven by ongoing regulatory tightening and aging water treatment assets requiring modernization, including the integration of digital analytics and IoT-enabled turbidity sensing platforms.
Outlook through 2030 anticipates a compound annual growth rate (CAGR) for the global turbidity instrumentation segment (specific to UF systems) in the range of 7–9%, with market value estimates expected to approach USD 600 million by the end of the decade. Growth will be further fueled by advances in sensor accuracy, miniaturization, and integration with cloud-based data management systems—enabling predictive maintenance and remote diagnostics, as seen in recent product launches by SUEZ Water Technologies & Solutions and Hach. The continued trend toward digital water technologies and smart treatment plants is set to solidify turbidity monitoring as an essential component of next-generation ultrafiltration operations worldwide.
Technological Advances in Turbidity Sensors for Ultrafiltration
Recent years have witnessed significant technological advancements in turbidity instrumentation specifically designed for ultrafiltration (UF) systems. As ultrafiltration becomes a mainstay for water treatment, particularly in municipal and industrial applications, the demand for precise, reliable, and low-maintenance turbidity sensors has accelerated. In 2025 and looking ahead, manufacturers are focusing on improving sensor sensitivity, automation, and data integration to meet increasingly stringent regulatory and operational demands.
One notable trend is the shift from traditional nephelometric methods to advanced optical and laser-based technologies. These new-generation sensors offer improved detection at extremely low turbidity levels—often below 0.01 NTU—critical for monitoring UF system integrity. For instance, Hach has launched digital turbidity sensors using 360° x 90° detection geometry, enhancing sensitivity and reducing interference from air bubbles or color. Similarly, Evoqua Water Technologies has integrated real-time turbidity monitoring with its UF skids, enabling operators to detect membrane breaches or fouling events rapidly.
Data connectivity and remote monitoring have become essential features. Leading manufacturers now offer smart sensors compatible with SCADA and IIoT platforms, allowing continuous turbidity data streaming and predictive analytics. SUEZ Water Technologies & Solutions (now part of Veolia) provides advanced digital sensors that support remote configuration, calibration alerts, and historical data trending, streamlining maintenance and compliance reporting. Similarly, Yokogawa Electric Corporation has developed turbidity transmitters with Modbus and HART protocols, facilitating integration into plant-wide automation systems.
Maintenance and calibration are also seeing improvements through self-diagnostic capabilities and auto-cleaning features. For example, Endress+Hauser has introduced sensors with ultrasonic cleaning and drift compensation, reducing manual intervention and ensuring long-term measurement stability—key for UF processes operating around the clock.
Looking forward, the outlook for turbidity instrumentation in UF applications includes further miniaturization, enhanced sensor durability, and expanded analytics powered by AI. Industry players are investing in advanced materials for sensor optics, and machine learning is being piloted to correlate turbidity spikes with specific membrane events for early warning. As regulatory oversight tightens and water reuse initiatives expand, these advances will be central to ensuring UF system reliability and water quality compliance through 2025 and beyond.
Leading Players and New Entrants (e.g. s::can.com, endress.com, hach.com)
The market for turbidity instrumentation tailored to ultrafiltration (UF) systems is marked by a blend of established leaders and technologically innovative new entrants. As regulatory scrutiny and operational demands intensify in 2025, leading companies are focusing on advanced sensor technologies, digital connectivity, and enhanced durability to meet the evolving requirements of water and wastewater treatment facilities, as well as industrial and municipal users.
Among the sector’s frontrunners, Hach maintains a prominent position, with a portfolio of turbidity analyzers widely used in UF installations. Their recent instruments emphasize low detection limits and automatic cleaning mechanisms, crucial for minimizing maintenance in high-solids environments typical of UF processes. Hach’s integration of digital communication protocols (e.g., Modbus, Ethernet/IP) aligns with the broader trend towards Industry 4.0-enabled water treatment plants, facilitating real-time data acquisition for process optimization.
Endress+Hauser continues to expand its base in the UF sector by offering turbidity sensors with robust hygienic designs and compliance with international standards (such as ISO 7027). Their recent focus has been on sensor longevity and process integration, with models like the Turbimax series designed for continuous monitoring and easy calibration. In 2025, Endress+Hauser’s instruments are increasingly found in pilot and full-scale membrane filtration plants, supporting both regulatory compliance and cost-effective operation.
Innovative firms such as s::can are gaining traction through modular, multi-parameter probes that combine turbidity with additional water quality metrics (e.g., UV254, color, organics). s::can’s fully digital platforms enable remote diagnostics and predictive maintenance, vital for decentralized or unmanned UF installations. The company’s focus on easy integration with Supervisory Control and Data Acquisition (SCADA) systems responds to utilities’ growing demand for unified, cloud-connected monitoring solutions.
New entrants are leveraging advances in optics, miniaturization, and artificial intelligence. For instance, Xylem (via its brands such as YSI and WTW) is introducing compact, low-drift turbidity sensors that can be embedded directly into membrane modules, reducing footprint and installation complexity. Their recent models emphasize wireless connectivity and advanced self-cleaning features to address fouling challenges in UF applications.
Looking ahead, the competitive landscape is expected to see further collaboration between sensor manufacturers and automation providers, with a clear emphasis on plug-and-play solutions, data-driven maintenance, and adaptive process control. With the tightening of water quality standards worldwide and the growing adoption of membrane-based treatment, both established leaders and agile newcomers are poised to capture opportunities through continuous innovation and customer-centric design.
Regulatory Trends and Industry Standards for Water Quality
Turbidity monitoring remains a critical parameter in the operation and validation of ultrafiltration (UF) systems, especially as regulatory standards around potable water, wastewater reuse, and industrial process water continue to tighten into 2025 and beyond. Regulators such as the U.S. Environmental Protection Agency (EPA) and the World Health Organization (WHO) have established maximum allowable turbidity thresholds for treated water—often set at or below 0.3 NTU for drinking water—prompting water utilities and industrial operators to upgrade instrumentation to meet compliance requirements.
In response, manufacturers are focusing on the development of next-generation online turbidity analyzers with enhanced accuracy, reduced maintenance, and digital connectivity. For example, Hach and SUEZ Water Technologies & Solutions have released instruments leveraging LED-based optics and advanced signal processing to reliably detect sub-0.1 NTU levels, supporting the stringent validation needs of modern UF membranes. Meanwhile, Evoqua Water Technologies and YSI, a Xylem brand, are emphasizing real-time data integration and remote calibration capabilities, which streamline regulatory reporting and maintenance workflows.
On the industry standards front, the International Organization for Standardization (ISO) and ASTM International continue to update methods such as ISO 7027 and ASTM D7315, respectively, which define measurement protocols for turbidity instrumentation, including requirements for calibration, detection limits, and interferences. These standards are being increasingly referenced in public tenders and utility specifications, ensuring that only compliant devices are accepted for UF system monitoring. Furthermore, organizations like the American Water Works Association (AWWA) regularly publish guidance and operational best practices for the deployment and maintenance of turbidity sensors in UF plants.
Looking forward, the integration of turbidity instruments with digital plant control systems is expected to accelerate, driven by the adoption of Industrial Internet of Things (IIoT) architectures. Vendors such as Endress+Hauser are introducing smart turbidity sensors equipped with protocols like HART and Modbus, enabling seamless data sharing with SCADA and plant asset management platforms. This digitalization not only supports proactive compliance but also enables predictive maintenance and continuous process optimization—key trends as regulatory scrutiny intensifies and performance benchmarks evolve through 2025 and the coming years.
Integration with Digital Monitoring and Process Automation
The integration of turbidity instrumentation with digital monitoring and process automation is rapidly shaping the operational landscape of ultrafiltration (UF) systems in 2025. Turbidity sensors—critical for ensuring water quality and regulatory compliance—are increasingly being networked into digital control architectures, enabling real-time data acquisition, advanced analytics, and remote system management.
Leading manufacturers are deploying next-generation turbidity probes with digital interfaces, such as Modbus, Profibus, and Ethernet/IP, facilitating seamless integration with supervisory control and data acquisition (SCADA) and distributed control systems (DCS). For example, Endress+Hauser offers turbidity sensors with digital Memosens technology, allowing for robust data transmission and predictive maintenance features. Similarly, Hach delivers online turbidity analyzers designed for continuous monitoring within UF skids, supporting connectivity with plant-wide automation systems.
The trend towards digitalization is also evident in the deployment of cloud-based monitoring platforms and Industrial Internet of Things (IIoT) solutions. These enable centralized oversight of multiple UF installations, historical trend analysis, and AI-driven process optimization. For instance, Veolia Water Technologies & Solutions integrates turbidity sensors into its digital asset performance management suites, offering operators proactive alerts and remote diagnostics.
Data interoperability and cybersecurity are emerging focal points as utilities and industrial operators scale their digital transformation efforts. Industry bodies such as the American Water Works Association are publishing guidelines that emphasize secure data integration and validation for online instrumentation. Meanwhile, solution providers are embedding secure communication protocols and encrypted data channels into their instrumentation to mitigate cyber risks.
Looking ahead, the next few years are poised to bring broader adoption of smart turbidity sensors with self-calibration, edge analytics, and machine learning capabilities. These advancements will further automate filtration process adjustments, minimize operator intervention, and improve membrane lifecycle management. As regulatory requirements for water quality monitoring continue to tighten and digital infrastructure matures, the integration of turbidity instrumentation with digital monitoring and automation will become standard practice across municipal and industrial ultrafiltration facilities.
Application Deep Dive: Municipal, Industrial, and Emerging Sectors
Turbidity instrumentation is a cornerstone of process control and regulatory compliance in ultrafiltration (UF) systems across municipal, industrial, and emerging sectors. In 2025, the adoption and sophistication of these instruments are accelerating to meet stricter water quality standards, enhance operational efficiency, and support data-driven management.
In the municipal sector, utilities are under increasing pressure to ensure safe potable water and to meet evolving regulatory thresholds for turbidity—often below 0.1 NTU for membrane filtration. Modern UF plants rely heavily on real-time, low-range turbidity analyzers with high sensitivity and rapid response times to detect membrane breakthrough and optimize backwashing cycles. For example, Hach and Evoqua Water Technologies offer instruments specifically designed for continuous monitoring at critical control points in municipal UF trains. In 2025, integration with SCADA and IoT platforms is becoming standard, enabling more predictive maintenance and remote diagnostics.
The industrial sector—notably food & beverage, pharmaceuticals, and microelectronics—demands even tighter turbidity control to safeguard sensitive processes and comply with stringent product quality requirements. Instruments tailored for industrial UF applications now feature automated cleaning, advanced signal processing for challenging matrices, and robust construction for aggressive environments. Companies such as SUEZ Water Technologies & Solutions are expanding offerings that include digital connectivity and in-line calibration, minimizing downtime and manual intervention.
In emerging sectors, including water reuse, decentralized treatment, and resource recovery, the versatility and miniaturization of turbidity sensors are becoming key. Compact, low-power devices are enabling real-time monitoring in distributed and mobile UF units, supporting the trend toward modular water treatment solutions. Xylem and Endress+Hauser are actively developing innovative platforms with wireless data transmission and cloud-based analytics, facilitating deployment in remote or rapidly changing environments.
Looking ahead, the next few years are expected to see further convergence of turbidity instrumentation with digital ecosystems—leveraging advances in machine learning for anomaly detection, automated control, and regulatory reporting. As UF systems diversify and regulations tighten, manufacturers are likely to continue investing in sensor miniaturization, energy efficiency, and interoperability, ensuring that turbidity monitoring remains central to water quality management across all sectors.
Competitive Landscape and Strategic Partnerships
The competitive landscape for turbidity instrumentation in ultrafiltration systems is intensifying as water quality standards grow stricter and the demand for advanced process monitoring escalates. In 2025, the market is characterized by a mix of established analytical technology providers and emerging niche players, each focusing on innovation, reliability, and integration capabilities.
Major instrumentation companies such as Hach, SUEZ Water Technologies & Solutions, and Endress+Hauser continue to dominate by offering comprehensive solutions that integrate real-time turbidity monitoring with ultrafiltration system controls. Hach has recently expanded its TU5 series, emphasizing enhanced accuracy and digital connectivity for water treatment operators, while SUEZ leverages its Sievers brand of analytical instruments to provide robust solutions for municipal and industrial ultrafiltration applications.
Strategic partnerships are a key trend, with instrumentation manufacturers collaborating with ultrafiltration system integrators, membrane suppliers, and automation companies. For example, Pentair has initiated technology alliances to seamlessly embed turbidity sensors within their ultrafiltration skids, reducing installation complexity and improving data fidelity. Similarly, Xylem has partnered with digital automation providers to advance cloud-based analytics platforms, which aggregate sensor data for predictive maintenance and regulatory compliance.
Innovation is also being driven by partnerships with research institutions. Veolia Water Technologies is working with European universities to pilot smart turbidity probes that offer self-calibration and adaptive measurement, addressing challenges of sensor fouling and drift in high-solids ultrafiltration processes. These collaborations aim to accelerate commercialization and meet evolving regulatory requirements for effluent quality.
In Asia-Pacific, companies like Yokogawa Electric Corporation are strengthening their market position by integrating advanced optical turbidity sensors into modular ultrafiltration units for municipal water reuse projects. This regional focus is expected to continue, with local partnerships accelerating technology adoption in fast-growing markets.
Looking ahead to the next few years, the competitive landscape will likely see further consolidation as leading players acquire innovative startups specializing in digital water monitoring and IoT-enabled turbidity measurement. Strategic alliances between sensor manufacturers and automation software companies are anticipated to deepen, fostering the next generation of smart ultrafiltration systems that emphasize predictive analytics, regulatory compliance, and operational efficiency.
Challenges: Fouling, Calibration, and Maintenance Innovations
Turbidity instrumentation is integral to the monitoring and control of ultrafiltration (UF) systems, providing real-time data on water clarity and the presence of suspended solids. Despite technological advances, the sector continues to grapple with three core challenges—fouling of sensor optics, the need for frequent calibration, and ongoing maintenance. In 2025 and the coming years, the industry is witnessing both persistent difficulties and notable innovations aimed at overcoming these obstacles.
- Fouling of Sensor Optics: Biofouling and scaling on sensor surfaces remain among the foremost challenges in UF applications, especially in municipal and industrial settings where feedwater quality varies. Accumulation of organic matter, minerals, or microbial films can compromise measurement accuracy and necessitate frequent manual cleaning. Companies such as Endress+Hauser and Hach are addressing this challenge by developing sensors with self-cleaning mechanisms—such as ultrasonic cleaning or wiper systems—minimizing downtime and reducing operator intervention.
- Calibration Complexity: Maintaining measurement reliability requires regular calibration, often using formazin or other calibration standards. This process can be labor-intensive and subject to human error. In 2025, a move towards automated, on-site calibration routines is underway. For example, SWAN Analytical Instruments offers turbidity analyzers with built-in calibration routines and diagnostics, allowing plant operators to schedule calibrations and receive alerts if calibration drifts are detected.
- Maintenance Innovations: The integration of remote monitoring and predictive maintenance tools is a key trend. Instrumentation providers such as Siemens are embedding digital connectivity into their turbidity meters, enabling real-time health monitoring and analytics. These systems can predict when maintenance is required, helping utilities and industries transition from reactive to proactive asset management.
Looking forward, the growing adoption of digitalization, Industrial Internet of Things (IIoT), and AI-driven diagnostics is expected to further reduce manual intervention and enhance the reliability of turbidity measurement in UF systems. As water quality regulations tighten and operational efficiency becomes paramount, solutions that automate cleaning, calibration, and maintenance will likely become standard across new installations and retrofit projects.
Future Outlook: Disruptive Trends and Investment Hotspots
The future landscape for turbidity instrumentation within ultrafiltration (UF) systems is set for significant transformation as new technologies, regulatory requirements, and market drivers converge. As we enter 2025 and look ahead, several disruptive trends and focal points for investment are becoming apparent, shaping the sector’s competitive dynamics and technological evolution.
A key trend is the rapid advancement in sensor technology. Next-generation online turbidity sensors are now offering higher accuracy, real-time data transmission, and automated calibration—capabilities that are increasingly critical as UF systems are deployed in diverse settings from municipal water plants to industrial reuse facilities. Companies such as Hach and Evoqua Water Technologies have recently introduced smart turbidity meters with digital connectivity, enabling integration with SCADA and IoT platforms for predictive maintenance and process optimization. These innovations are attracting investment as utilities and plant operators seek to reduce manual intervention and operational costs while ensuring compliance with tightening water quality standards.
Simultaneously, there’s a strong push towards miniaturization and portability. Compact, low-maintenance probes are facilitating real-time monitoring even in decentralized and remote UF installations. Xylem YSI and Swan Analytical Instruments have invested in robust, field-ready devices that can operate in harsh environments, targeting not only traditional water treatment but also rapidly expanding markets such as point-of-use and mobile water purification systems. This trend is anticipated to accelerate as global water scarcity drives adoption of flexible UF solutions in regions with limited infrastructure.
- Artificial Intelligence and Data Analytics: The integration of AI-driven analytics is poised to disrupt turbidity monitoring. By leveraging machine learning algorithms, future instruments will not only detect anomalies in water quality but also predict membrane fouling and optimize cleaning cycles. Several major OEMs, including Veolia Water Technologies & Solutions, have announced pilot projects to embed advanced data analytics within their UF instrumentation suites, signaling a shift towards condition-based asset management.
- Regulatory and Sustainability Drivers: Stricter global regulations, especially in Europe and North America, are pushing for lower turbidity thresholds in potable and reuse applications. This is spurring investment in high-sensitivity instrumentation capable of continuous, low-level detection. Industry bodies such as the American Water Works Association are updating guidelines to reflect these technological advances, further catalyzing market uptake.
Looking ahead, investment hotspots are likely to center on digital water solutions, AI-enabled monitoring, and ruggedized instrumentation for decentralized systems. Stakeholders who prioritize R&D in these areas are poised to capitalize on both regulatory momentum and the growing demand for resilient, automated UF operations worldwide.