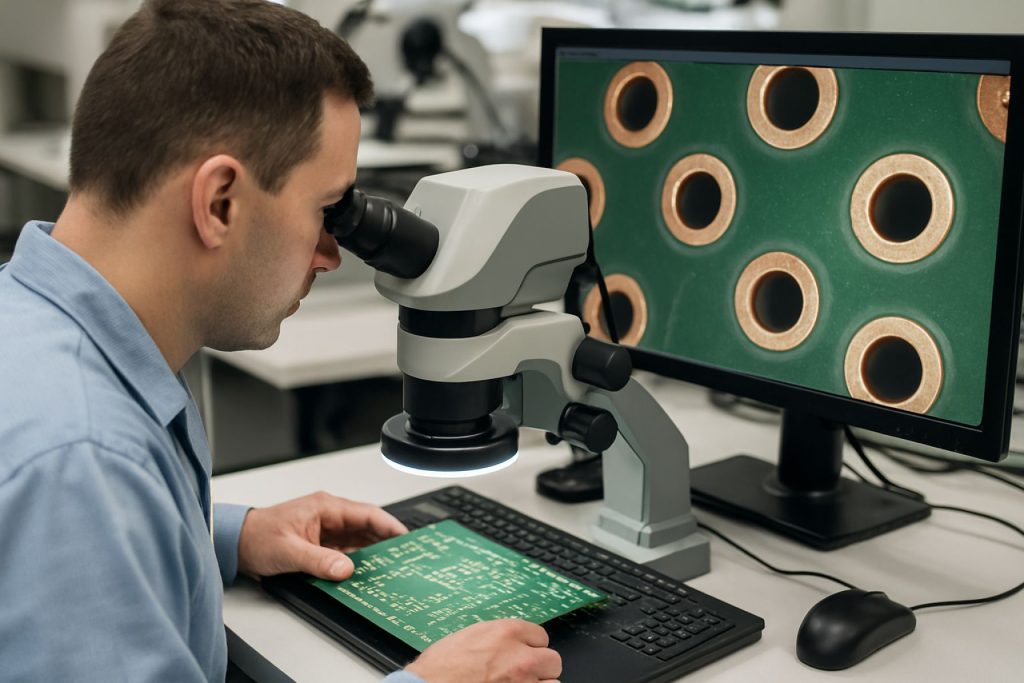
Revolutionizing PCB Microvia Inspection: 2025 Market Dynamics, Technology Breakthroughs, and Strategic Forecasts. Discover how advanced inspection systems are shaping the future of printed wiring board manufacturing.
- Executive Summary: Key Trends and Market Drivers in 2025
- Industry Overview: The Role of Microvia Inspection in PCB Manufacturing
- Technology Landscape: Innovations in Optical and X-ray Inspection Systems
- Leading Players and Strategic Initiatives (e.g., camtek.com, kohyoung.com, omron.com)
- Market Size and Growth Forecasts: 2025–2029
- Regional Analysis: Asia-Pacific, North America, and Europe Market Dynamics
- Emerging Applications: 5G, Automotive, and Advanced Electronics
- Challenges and Barriers: Technical, Regulatory, and Supply Chain Factors
- Sustainability and Quality Assurance in Microvia Inspection
- Future Outlook: Disruptive Technologies and Investment Opportunities
- Sources & References
Executive Summary: Key Trends and Market Drivers in 2025
The market for Printed Wiring Board (PWB) Microvia Inspection Systems is experiencing significant transformation in 2025, driven by the rapid evolution of electronics miniaturization, the proliferation of high-density interconnect (HDI) boards, and the increasing complexity of microvia structures. As the demand for advanced consumer electronics, automotive electronics, and 5G infrastructure accelerates, manufacturers are compelled to adopt more sophisticated inspection solutions to ensure reliability and yield in microvia fabrication.
A key trend in 2025 is the integration of artificial intelligence (AI) and machine learning algorithms into automated optical inspection (AOI) and X-ray inspection systems. Leading equipment manufacturers such as OMRON Corporation and Hitachi High-Tech Corporation are enhancing their inspection platforms with AI-driven defect recognition, enabling faster and more accurate detection of microvia defects such as voids, cracks, and incomplete fills. These advancements are critical as microvia diameters shrink below 100 microns, making traditional inspection methods less effective.
Another driver is the shift toward inline, high-throughput inspection systems that can keep pace with the increasing speed of PWB production lines. Companies like Koh Young Technology are deploying 3D AOI systems capable of real-time analysis, supporting zero-defect manufacturing initiatives and reducing costly rework. The adoption of 3D X-ray inspection, as offered by Carl Zeiss AG, is also expanding, providing non-destructive, volumetric analysis of microvias and enabling manufacturers to identify hidden defects that are undetectable by surface inspection alone.
Regulatory and industry standards are also shaping the market. The ongoing updates to IPC standards for microvia reliability and inspection are prompting manufacturers to invest in systems that can document and trace inspection results, supporting both quality assurance and compliance. This is particularly relevant for sectors such as automotive and aerospace, where reliability is paramount.
Looking ahead, the outlook for the next few years points to continued growth in demand for advanced microvia inspection systems, particularly in Asia-Pacific, where the majority of HDI PWB manufacturing is concentrated. The convergence of AI, high-resolution imaging, and data analytics is expected to further enhance inspection accuracy and throughput, supporting the next generation of ultra-fine pitch electronics. As a result, equipment suppliers with strong R&D capabilities and a focus on automation are well-positioned to capture market share in this dynamic landscape.
Industry Overview: The Role of Microvia Inspection in PCB Manufacturing
The increasing complexity and miniaturization of printed wiring boards (PWBs) in 2025 have made microvia inspection systems a critical component in the electronics manufacturing industry. Microvias—tiny holes typically less than 150 microns in diameter—are essential for high-density interconnect (HDI) PCBs, enabling advanced applications in 5G, automotive electronics, and consumer devices. As the demand for finer lines and smaller features grows, ensuring the structural integrity and electrical reliability of microvias has become a top priority for manufacturers.
Microvia failures, such as voids, cracks, or incomplete fills, can lead to catastrophic device malfunctions. To address these challenges, the industry has seen a rapid evolution in inspection technologies. Automated optical inspection (AOI) and X-ray inspection systems are now standard in high-volume production lines, offering non-destructive, high-resolution analysis of microvia quality. Leading equipment manufacturers such as Omron Corporation and Hitachi High-Tech Corporation have developed advanced AOI and X-ray solutions tailored for microvia inspection, integrating artificial intelligence and machine learning algorithms to improve defect detection rates and reduce false positives.
In 2025, the industry is witnessing a shift toward inline, real-time inspection systems that can keep pace with the high throughput of modern PCB fabrication. Companies like Koh Young Technology are pioneering 3D inspection platforms capable of measuring microvia depth, diameter, and fill quality with micron-level accuracy. These systems not only detect defects but also provide valuable process feedback, enabling manufacturers to optimize drilling, plating, and filling processes in real time.
Industry standards and guidelines, such as those from the IPC, continue to evolve, reflecting the need for more stringent inspection criteria as microvia dimensions shrink. The IPC-6012 and IPC-2226 standards, for example, specify requirements for microvia integrity and reliability, driving the adoption of more sophisticated inspection systems across the supply chain.
Looking ahead, the outlook for microvia inspection systems is robust. The proliferation of advanced packaging, the rollout of next-generation wireless infrastructure, and the electrification of vehicles are all fueling demand for HDI PCBs and, by extension, high-performance inspection solutions. As manufacturers strive for zero-defect production and greater traceability, investment in automated, data-driven inspection technologies is expected to accelerate, cementing their role as a cornerstone of quality assurance in PCB manufacturing.
Technology Landscape: Innovations in Optical and X-ray Inspection Systems
The technology landscape for printed wiring board (PWB) microvia inspection systems is undergoing rapid transformation as the electronics industry demands ever-smaller, higher-density interconnects. Microvias—tiny holes typically less than 150 microns in diameter—are critical for high-density interconnect (HDI) PCBs, but their small size and complex structures present significant inspection challenges. In 2025, the focus is on advanced optical and X-ray inspection systems that can ensure reliability and yield in mass production.
Optical inspection systems have evolved with the integration of high-resolution cameras, multi-angle lighting, and sophisticated image processing algorithms. Leading manufacturers such as OMRON Corporation and Koh Young Technology are at the forefront, offering automated optical inspection (AOI) platforms capable of detecting microvia defects such as incomplete drilling, copper voids, and misregistration. These systems now leverage artificial intelligence (AI) and machine learning to improve defect recognition rates and reduce false positives, a trend expected to accelerate through 2025 as more manufacturers adopt smart factory principles.
However, optical methods are limited in their ability to inspect hidden or internal features of microvias, especially in stacked or filled via structures. This limitation has driven significant investment in X-ray inspection technologies. Companies like Viscom AG and Thermo Fisher Scientific (through its Phenom desktop SEM/X-ray solutions) are advancing 2D and 3D X-ray inspection systems. These platforms provide non-destructive analysis of internal microvia quality, including detection of voids, cracks, and plating thickness variations. The latest systems offer higher throughput and resolution, with some models capable of inline integration for real-time process control.
Hybrid inspection systems that combine optical and X-ray modalities are also emerging, aiming to provide comprehensive coverage of both surface and subsurface defects. This approach is particularly relevant for next-generation HDI and substrate-like PCBs used in 5G, automotive, and advanced computing applications. Industry leaders such as Hitachi High-Tech Corporation are investing in multi-sensor platforms that can adapt to diverse inspection requirements.
Looking ahead, the outlook for microvia inspection systems is shaped by ongoing miniaturization, increasing PCB complexity, and the push for zero-defect manufacturing. The integration of AI-driven analytics, cloud connectivity, and real-time feedback loops is expected to further enhance defect detection and process optimization. As the industry moves toward Industry 4.0, inspection systems will play a pivotal role in ensuring the reliability of advanced electronic assemblies.
Leading Players and Strategic Initiatives (e.g., camtek.com, kohyoung.com, omron.com)
The landscape of printed wiring board (PWB) microvia inspection systems in 2025 is shaped by a handful of technologically advanced companies, each leveraging automation, artificial intelligence, and high-resolution imaging to address the increasing complexity of microvias in high-density interconnect (HDI) PCBs. As the demand for miniaturized electronics and 5G infrastructure accelerates, the need for reliable, high-throughput inspection solutions has never been greater.
Among the leading players, Camtek Ltd. stands out for its advanced optical inspection systems tailored for microvia and HDI PCB applications. Camtek’s latest Eagle product line integrates 2D and 3D inspection capabilities, enabling detection of sub-20 micron defects and precise measurement of microvia dimensions. In 2024 and 2025, Camtek has focused on expanding its AI-driven defect classification, reducing false calls and improving yield for major PCB manufacturers in Asia and Europe.
Another key innovator is Koh Young Technology Inc., renowned for its 3D automated optical inspection (AOI) and measurement systems. Koh Young’s Zenith series, widely adopted in the industry, utilizes multi-projection Moiré technology to deliver accurate microvia depth and diameter analysis. In 2025, Koh Young is investing in machine learning algorithms to further automate root cause analysis and predictive maintenance, supporting the zero-defect initiatives of leading electronics OEMs.
Japanese automation giant Omron Corporation continues to play a pivotal role with its VT-S730 and VT-X750 series, which combine X-ray and optical inspection for comprehensive microvia analysis. Omron’s strategic partnerships with global PCB fabricators have led to the deployment of inline inspection systems capable of real-time data feedback, supporting smart factory and Industry 4.0 initiatives. In 2025, Omron is expected to enhance its cloud-based analytics platform, enabling remote diagnostics and process optimization.
Other notable contributors include Ushio Inc., which supplies high-precision UV imaging and inspection solutions, and ATS Corporation, which integrates inspection modules into automated PCB assembly lines. These companies are increasingly collaborating with semiconductor and telecom customers to address the stringent reliability requirements of next-generation devices.
Looking ahead, the sector is poised for further consolidation and technological convergence, with leading players investing in AI, big data analytics, and hybrid inspection modalities. Strategic initiatives in 2025 and beyond will likely focus on enhancing inspection speed, accuracy, and connectivity, ensuring that microvia quality keeps pace with the rapid evolution of advanced electronics manufacturing.
Market Size and Growth Forecasts: 2025–2029
The market for Printed Wiring Board (PWB) Microvia Inspection Systems is poised for significant growth from 2025 through 2029, driven by the increasing complexity and miniaturization of electronic devices. Microvias—tiny holes used to connect layers in high-density interconnect (HDI) PCBs—require precise inspection to ensure reliability, especially as device manufacturers push for higher performance and smaller form factors. The demand for advanced inspection systems is being fueled by sectors such as consumer electronics, automotive electronics, telecommunications, and medical devices, all of which are adopting HDI and complex multilayer PCBs at an accelerated pace.
Key industry players are investing in next-generation inspection technologies, including automated optical inspection (AOI), X-ray inspection, and hybrid systems that combine multiple modalities for enhanced defect detection. Companies such as OMRON Corporation, a global leader in industrial automation, and Koh Young Technology, renowned for its 3D inspection solutions, are expanding their product portfolios to address the stringent requirements of microvia inspection. OMRON Corporation continues to innovate in high-speed, high-precision AOI systems, while Koh Young Technology is advancing 3D measurement capabilities to detect microvia defects such as voids, incomplete fills, and misalignments.
The Asia-Pacific region, particularly China, Taiwan, South Korea, and Japan, is expected to remain the largest and fastest-growing market for microvia inspection systems through 2029. This is due to the concentration of PCB manufacturing and the rapid adoption of advanced packaging technologies in these countries. Leading PCB manufacturers such as IBIDEN Co., Ltd. and Meiko Electronics Co., Ltd. are increasingly integrating sophisticated inspection solutions to maintain quality and meet international standards.
From a technology perspective, the period from 2025 to 2029 will likely see further integration of artificial intelligence (AI) and machine learning algorithms into inspection systems, enabling real-time defect classification and predictive maintenance. This trend is supported by ongoing R&D investments from major equipment suppliers and the push for higher throughput and lower false call rates in high-volume manufacturing environments.
Overall, the outlook for the PWB microvia inspection systems market is robust, with double-digit annual growth rates anticipated in the near term. The convergence of miniaturization trends, stringent quality requirements, and technological advancements in inspection equipment will continue to drive market expansion and innovation through 2029.
Regional Analysis: Asia-Pacific, North America, and Europe Market Dynamics
The global market for printed wiring board (PWB) microvia inspection systems is experiencing dynamic regional shifts, with Asia-Pacific, North America, and Europe each exhibiting distinct trends and growth drivers as of 2025 and looking ahead. These systems, essential for ensuring the reliability and performance of high-density interconnect (HDI) PCBs, are increasingly critical as electronics miniaturization accelerates.
Asia-Pacific remains the dominant region, propelled by its robust electronics manufacturing ecosystem. Countries such as China, Japan, South Korea, and Taiwan are home to leading PCB fabricators and original equipment manufacturers (OEMs), driving demand for advanced inspection solutions. The region’s leadership is underpinned by the presence of major industry players like Hitachi High-Tech Corporation and OMRON Corporation, both of which offer state-of-the-art automated optical inspection (AOI) and X-ray inspection systems tailored for microvia analysis. The ongoing expansion of 5G infrastructure, automotive electronics, and consumer devices in Asia-Pacific is expected to sustain double-digit growth rates for microvia inspection systems through the next several years.
North America is characterized by its focus on high-reliability applications, particularly in aerospace, defense, and medical electronics. The region’s stringent quality standards and regulatory requirements are driving adoption of advanced inspection technologies, including 3D X-ray and computed tomography (CT) systems. Companies such as Nordson Corporation (through its Nordson DAGE and YESTECH brands) and Thermo Fisher Scientific (Phenom desktop SEMs) are prominent suppliers, supporting the region’s emphasis on defect detection and process traceability. While North America’s overall PCB production volume is smaller than Asia-Pacific’s, its value-added focus and investment in R&D are expected to foster steady demand for high-end inspection systems through 2025 and beyond.
Europe is witnessing moderate but stable growth, driven by its automotive, industrial, and telecommunications sectors. The region’s emphasis on quality assurance and environmental compliance is reflected in the adoption of sophisticated inspection platforms. Notable European suppliers include Viscom AG and Ortec Group, both of which provide AOI and X-ray solutions for microvia inspection. European manufacturers are also increasingly integrating artificial intelligence (AI) and machine learning into inspection workflows to enhance defect recognition and reduce false calls. The outlook for Europe suggests incremental growth, supported by ongoing digitalization and the region’s push for advanced manufacturing capabilities.
Across all regions, the next few years will see continued investment in automation, data analytics, and AI-driven inspection, as manufacturers seek to address the challenges of shrinking feature sizes and increasing board complexity. Regional dynamics will remain shaped by end-market demand, regulatory environments, and the pace of technological innovation among leading equipment suppliers.
Emerging Applications: 5G, Automotive, and Advanced Electronics
The rapid evolution of 5G telecommunications, automotive electronics, and advanced consumer devices is driving significant advancements in printed wiring board (PWB) microvia inspection systems in 2025. As microvias—tiny, laser-drilled holes connecting layers in high-density interconnect (HDI) boards—become smaller and more numerous, the need for precise, high-throughput inspection has intensified across these emerging applications.
In the 5G sector, the demand for higher frequency operation and miniaturized components has led to the widespread adoption of HDI PCBs with complex microvia structures. Leading telecom equipment manufacturers are requiring inspection systems capable of detecting sub-20 micron defects, such as voids, cracks, and incomplete fills, to ensure signal integrity and reliability. Companies like Carl Zeiss AG and Hitachi High-Tech Corporation are at the forefront, offering advanced 3D X-ray and automated optical inspection (AOI) solutions tailored for these stringent requirements.
Automotive electronics, particularly in electric vehicles (EVs) and advanced driver-assistance systems (ADAS), are also fueling the adoption of sophisticated microvia inspection. The automotive industry’s zero-defect tolerance and the need for robust, high-reliability interconnects have prompted major suppliers to integrate inline inspection systems with machine learning algorithms for real-time defect classification and process feedback. OMRON Corporation and Koh Young Technology Inc. are notable for their deployment of AI-driven AOI and 3D inspection platforms in automotive PCB manufacturing lines.
In advanced electronics, including smartphones, wearables, and medical devices, the trend toward ultra-thin, multi-layered PCBs with stacked microvias is accelerating. Inspection systems must now address challenges such as high aspect ratio via inspection and the detection of microcracks or delamination at the sub-micron level. Camtek Ltd. and CyberOptics Corporation are recognized for their high-resolution, non-destructive inspection technologies that support these demanding applications.
Looking ahead, the outlook for microvia inspection systems is marked by continued innovation in imaging resolution, data analytics, and automation. Industry leaders are investing in AI-powered defect recognition, cloud-based data integration, and closed-loop process control to meet the evolving needs of 5G, automotive, and advanced electronics sectors. As device complexity and reliability requirements grow, the role of advanced microvia inspection will become even more critical in ensuring product quality and manufacturing yield.
Challenges and Barriers: Technical, Regulatory, and Supply Chain Factors
The landscape of printed wiring board (PWB) microvia inspection systems in 2025 is shaped by a complex interplay of technical, regulatory, and supply chain challenges. As microvias become increasingly critical for high-density interconnect (HDI) PCBs—driven by 5G, automotive electronics, and miniaturized consumer devices—the demand for reliable, high-throughput inspection systems has never been higher. However, several barriers persist that could impact the pace of innovation and adoption in the coming years.
Technical Challenges remain at the forefront. Microvias, often less than 100 microns in diameter, require inspection systems with extremely high resolution and accuracy. Traditional 2D automated optical inspection (AOI) systems are often insufficient for detecting defects such as voids, cracks, or incomplete fills within these tiny structures. Advanced 3D AOI and X-ray inspection technologies are being adopted, but these come with increased complexity, cost, and integration challenges. Leading equipment manufacturers such as Omron Corporation and Koh Young Technology are investing in AI-driven algorithms and hybrid inspection platforms to address these issues, but the rapid pace of PCB miniaturization continues to push the limits of current inspection capabilities.
Regulatory Barriers are also evolving. As microvia reliability is critical for safety in sectors like automotive and aerospace, regulatory bodies are tightening standards for defect detection and traceability. The IPC—the global electronics industry standards organization—has updated its IPC-6012 and IPC-2226 standards to include more stringent requirements for microvia integrity and inspection. Compliance with these standards necessitates not only advanced inspection hardware but also robust data management and reporting systems, increasing the burden on manufacturers and system suppliers.
Supply Chain Factors have become more pronounced in the wake of global disruptions. The semiconductor and electronics manufacturing industries continue to face shortages in critical components such as high-resolution sensors, precision actuators, and specialized imaging chips—key elements in advanced inspection systems. Companies like Hitachi High-Tech Corporation and Camtek Ltd., both major suppliers of inspection equipment, have reported extended lead times and increased costs for certain system components. Additionally, the geographic concentration of key suppliers in East Asia exposes the industry to risks from geopolitical tensions and logistics bottlenecks.
Looking ahead, the outlook for PWB microvia inspection systems will depend on the industry’s ability to overcome these barriers. Continued investment in R&D, closer collaboration between equipment suppliers and PCB manufacturers, and proactive engagement with regulatory bodies will be essential to ensure inspection technologies keep pace with the evolving demands of next-generation electronics.
Sustainability and Quality Assurance in Microvia Inspection
Sustainability and quality assurance are increasingly central to the evolution of printed wiring board (PWB) microvia inspection systems in 2025 and the coming years. As the electronics industry faces mounting pressure to deliver higher-density interconnects with minimal environmental impact, manufacturers are investing in advanced inspection technologies that not only ensure product reliability but also support greener manufacturing practices.
Microvias—tiny, laser-drilled holes connecting layers in high-density interconnect (HDI) PCBs—are critical to the performance of modern electronics. However, their small size and complex geometry make them challenging to inspect. Defects such as voids, cracks, or incomplete fills can compromise board reliability, making robust inspection essential for quality assurance. In 2025, leading equipment manufacturers are deploying automated optical inspection (AOI), X-ray inspection, and hybrid systems that combine multiple modalities to detect sub-micron defects with high throughput and accuracy.
Companies such as OMRON Corporation and Koh Young Technology are at the forefront, offering 3D AOI and X-ray solutions tailored for microvia inspection. These systems leverage artificial intelligence and machine learning to improve defect detection rates while reducing false positives, thus minimizing unnecessary rework and material waste. OMRON Corporation emphasizes the integration of sustainability into its inspection platforms, focusing on energy efficiency and the reduction of hazardous substances in manufacturing environments.
Another key player, Via Mechanics, specializes in laser drilling and inspection systems for microvias, supporting the trend toward finer features and higher board densities. Their equipment is designed to optimize process control, reducing scrap rates and supporting closed-loop manufacturing—an important aspect of sustainable production.
Industry bodies such as the IPC are also driving quality and sustainability standards. The IPC-6012 and IPC-2226 standards, for example, set rigorous requirements for HDI and microvia reliability, pushing manufacturers to adopt advanced inspection and process control systems. Compliance with these standards is increasingly seen as a prerequisite for market access, especially in automotive, aerospace, and medical electronics.
Looking ahead, the outlook for microvia inspection systems is shaped by the dual imperatives of quality and sustainability. The adoption of smart factory principles—real-time data analytics, predictive maintenance, and closed-loop feedback—will further enhance both yield and resource efficiency. As environmental regulations tighten and customer expectations rise, investment in advanced, sustainable inspection solutions is expected to accelerate, reinforcing the industry’s commitment to both product excellence and environmental stewardship.
Future Outlook: Disruptive Technologies and Investment Opportunities
The future of printed wiring board (PWB) microvia inspection systems is poised for significant transformation as the electronics industry continues to demand higher density interconnects and zero-defect manufacturing. In 2025 and the coming years, several disruptive technologies and investment opportunities are emerging, driven by the need for greater accuracy, speed, and automation in microvia inspection.
One of the most notable trends is the integration of artificial intelligence (AI) and machine learning algorithms into automated optical inspection (AOI) and X-ray inspection systems. Leading manufacturers such as OMRON Corporation and Koh Young Technology are actively developing AI-powered solutions that can detect microvia defects—including voids, incomplete fills, and misalignments—with higher precision and reduced false positives. These systems leverage large datasets to continuously improve defect recognition, enabling real-time process adjustments and predictive maintenance.
Another disruptive technology is the adoption of 3D inspection techniques. Companies like ATS Corporation and Viscom AG are advancing 3D X-ray and computed tomography (CT) systems, which provide volumetric analysis of microvias. This allows for the detection of hidden defects that traditional 2D imaging might miss, a critical capability as microvias become smaller and more densely packed in high-end PWBs for applications such as 5G, automotive electronics, and advanced computing.
Investment is also flowing into the development of in-line inspection systems that can be seamlessly integrated into high-speed manufacturing lines. Teradyne, Inc. and Camtek Ltd. are among the companies focusing on scalable, modular inspection platforms that support Industry 4.0 initiatives. These systems enable real-time data collection and analytics, supporting closed-loop process control and traceability, which are increasingly demanded by OEMs and EMS providers.
Looking ahead, the convergence of AI, 3D imaging, and smart factory integration is expected to drive further innovation and investment in microvia inspection. As the industry moves toward sub-50 micron microvias and heterogeneous integration, inspection systems will need to deliver even greater sensitivity and throughput. Companies with strong R&D capabilities and partnerships with semiconductor and electronics manufacturers are well-positioned to capitalize on these trends. The outlook for 2025 and beyond suggests robust growth opportunities for both established players and innovative startups in the PWB microvia inspection ecosystem.
Sources & References
- Hitachi High-Tech Corporation
- Carl Zeiss AG
- IPC
- Koh Young Technology
- Viscom AG
- Thermo Fisher Scientific
- Camtek Ltd.
- Ushio Inc.
- ATS Corporation
- Koh Young Technology
- Meiko Electronics Co., Ltd.
- Nordson Corporation
- Via Mechanics
- IPC