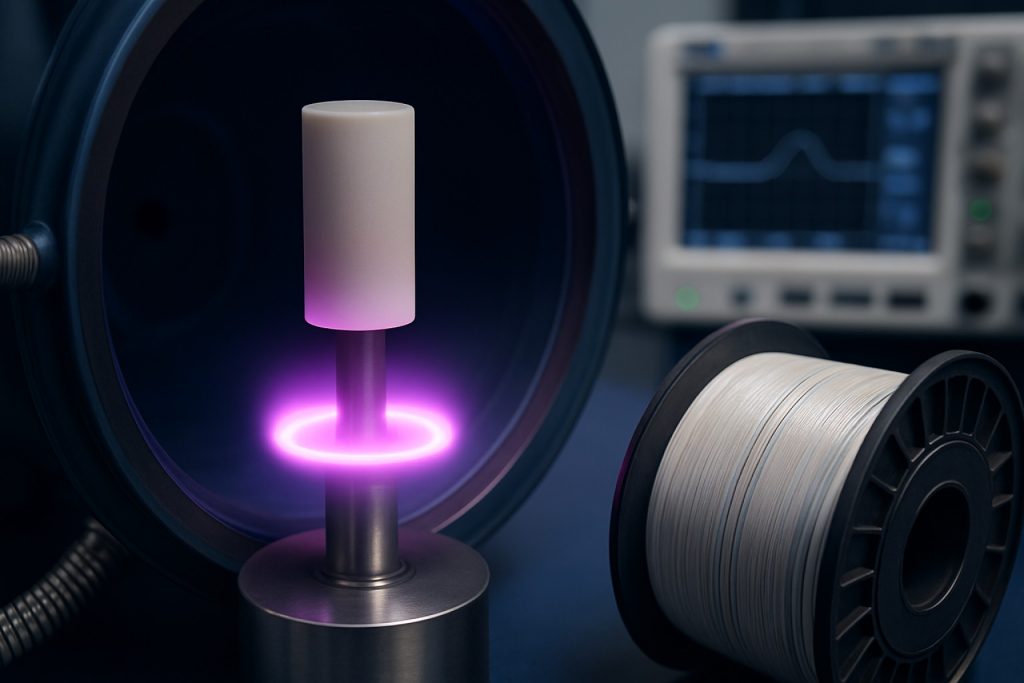
Table of Contents
- Executive Summary: 2025 Outlook and Beyond
- Technology Primer: Plasma Deposition Methods and Ceramic Dielectric Innovations
- Key Manufacturers and Industry Stakeholders (e.g., appliedmaterials.com, lamresearch.com, ieee.org)
- Current and Emerging Applications in Electronics, Energy, and Optoelectronics
- 2025–2028 Global Market Forecast: Volume, Value, and Regional Trends
- Competitive Landscape: Strategies, Partnerships, and Patent Activity
- Technical Challenges and Solutions: Reliability, Scalability, and Integration
- Regulatory, Environmental, and Supply Chain Considerations
- Future Innovations: R&D Pipelines and Next-Generation Material Platforms
- Strategic Recommendations: Investment, Collaboration, and Market Entry
- Sources & References
Executive Summary: 2025 Outlook and Beyond
Plasma-deposited ceramic dielectrics are poised for robust growth and technological advancement in 2025 and the following years, driven largely by their critical role in microelectronics, energy storage, and high-frequency device applications. These thin film dielectrics, produced via plasma-enhanced chemical vapor deposition (PECVD) and related plasma processes, offer superior electrical insulation, high breakdown strength, and excellent thermal stability—attributes essential for next-generation semiconductor devices and advanced capacitors.
Major industry players are intensifying R&D into new ceramic formulations and plasma processing techniques to meet escalating performance demands. Applied Materials and Lam Research are actively developing advanced PECVD platforms capable of depositing high-quality silicon nitride (SiNx), silicon oxide (SiO2), and aluminum oxide (Al2O3) films with precise thickness control and low defect densities. These efforts are directly aligned with the miniaturization and integration trends in logic, memory, and power electronics.
In 2025, plasma-deposited dielectrics are expected to play a pivotal role in supporting advanced nodes (3nm and beyond) and heterogeneous integration strategies. The transition to high aspect ratio structures in 3D NAND, DRAM, and logic devices demands dielectrics with enhanced conformality and step coverage. Tokyo Ohka Kogyo Co., Ltd. (TOK) and ULVAC, Inc. are scaling up their plasma deposition solutions to meet these requirements, with a focus on uniformity and low-k or high-k film properties as dictated by device architecture.
In the energy storage sector, plasma-deposited ceramic dielectrics are gaining traction for their use in high-energy density capacitors and solid-state batteries. Companies such as TDK Corporation are exploring plasma-assisted deposition to enhance dielectric layer performance in multilayer ceramic capacitors (MLCCs), improving reliability and capacitance retention at smaller scales.
Looking forward, the outlook for plasma-deposited ceramic dielectrics is highly promising. The convergence of semiconductor scaling, demands for higher energy storage, and the proliferation of 5G/6G wireless and automotive electronics will continue to expand market opportunities. Industry leaders are expected to invest further in process control, defect reduction, and new material chemistries, ensuring that plasma-deposited ceramics will remain foundational in advanced electronic manufacturing through 2025 and beyond.
Technology Primer: Plasma Deposition Methods and Ceramic Dielectric Innovations
Plasma-deposited ceramic dielectrics are rapidly advancing as critical materials for next-generation electronics, energy storage devices, and advanced sensors. The plasma-enhanced chemical vapor deposition (PECVD) and atomic layer deposition (ALD) techniques remain at the forefront, offering unparalleled control over film thickness, uniformity, and composition. These methods enable the fabrication of ultra-thin dielectric layers with tailored electrical and mechanical properties, essential for miniaturized and high-performance applications.
As of 2025, leading manufacturers have demonstrated significant progress in scaling up plasma deposition processes for ceramics such as silicon dioxide (SiO2), aluminum oxide (Al2O3), hafnium oxide (HfO2), and tantalum oxide (Ta2O5). These materials are utilized in capacitors, gate dielectrics for transistors, and barrier coatings for flexible electronics. For example, Applied Materials, Inc. continues to optimize its plasma deposition platforms, focusing on high-k dielectric films for advanced logic and memory devices. Their recent innovations allow for improved step coverage and reduced defect density even at sub-10 nm nodes.
Another notable trend is the integration of plasma-deposited ceramics into multilayer ceramic capacitors (MLCCs) and microelectromechanical systems (MEMS). TDK Corporation and Murata Manufacturing Co., Ltd. have reported enhancements in dielectric strength and reliability by utilizing plasma-assisted methods to deposit ultra-thin ceramic layers, resulting in higher capacitance per volume and better thermal stability. These advances are particularly important for automotive and 5G communications, where component miniaturization and reliability are paramount.
In the field of energy storage, Samsung Electronics is exploring plasma-deposited ceramic electrolytes for solid-state batteries, aiming for improved ionic conductivity and dendrite suppression. The company’s research points toward scalable plasma-assisted processes for uniform ceramic layer deposition, which is critical for manufacturing safe and high-performance batteries.
Looking ahead to the next few years, the outlook for plasma-deposited ceramic dielectrics is robust. Industry collaborations are underway to refine plasma parameters for defect-free films and to expand the material palette to include novel ceramics such as barium titanate (BaTiO3) and yttrium oxide (Y2O3). Standardization efforts by bodies like the SEMI are expected to accelerate commercialization and ensure process compatibility across different toolsets and fabs. With ongoing investments and customer demand for higher performing, lower footprint components, plasma-deposited ceramic dielectrics are set to underpin key innovations in microelectronics, energy, and connectivity through 2026 and beyond.
Key Manufacturers and Industry Stakeholders (e.g., appliedmaterials.com, lamresearch.com, ieee.org)
As of 2025, the landscape of plasma-deposited ceramic dielectrics is shaped by a dynamic interplay of established equipment manufacturers, materials suppliers, and leading industry organizations. Key players are driving innovation in both process technology and end-use applications, particularly in advanced semiconductor manufacturing, energy storage, and high-frequency electronics.
Leading the charge in plasma deposition equipment for ceramic dielectrics are firms such as Applied Materials, Inc. and Lam Research Corporation. Both companies are renowned for their development of plasma-enhanced chemical vapor deposition (PECVD) and atomic layer deposition (ALD) systems, which are widely adopted for depositing thin, conformal ceramic dielectric films such as silicon nitride, silicon dioxide, and aluminum oxide. In 2024 and 2025, these companies continue to refine process uniformity, throughput, and film quality to meet the stringent requirements of next-generation microelectronics, including sub-5nm logic and advanced memory devices.
Material suppliers such as Entegris, Inc. and Versum Materials (now part of Merck KGaA) provide high-purity precursors essential for plasma-deposited ceramic dielectrics. These companies invest heavily in precursor chemistry innovation and supply chain resilience to support the scaling of deposition technologies into high-volume manufacturing.
On the stakeholder front, industry organizations like the Institute of Electrical and Electronics Engineers (IEEE) and SEMI play a critical role in standardizing deposition processes and promoting collaboration across the value chain. Through technical conferences, standards development, and working groups, these bodies ensure that best practices are disseminated and that industry requirements—such as reliability, dielectric constant optimization, and environmental compliance—are addressed in plasma-deposited ceramic dielectric research and production.
Looking ahead over the next several years, increasing demand for high-performance dielectrics in applications such as 5G/6G RF devices, power electronics, and next-generation displays is expected to spur further investment and collaboration among these manufacturers and stakeholders. Notably, equipment vendors and material suppliers are forming strategic partnerships to accelerate the introduction of new dielectric formulations and deposition processes—an approach that will likely define the competitive landscape through 2026 and beyond.
Current and Emerging Applications in Electronics, Energy, and Optoelectronics
Plasma-deposited ceramic dielectrics are poised to play an increasingly pivotal role in electronics, energy, and optoelectronics through 2025 and beyond. The unique ability of plasma-enhanced processes—such as Plasma-Enhanced Chemical Vapor Deposition (PECVD) and Atomic Layer Deposition (ALD)—to precisely engineer thin, conformal ceramic films is enabling new device architectures and improved performance across several sectors.
In the semiconductor industry, plasma-deposited silicon nitride (SiNx) and silicon dioxide (SiO2) layers are fundamental for advanced logic and memory device isolation, passivation, and as gate dielectrics. With ongoing device scaling in 3D NAND and logic nodes below 3nm, demand for ultra-thin, pinhole-free dielectrics is intensifying. Leading equipment providers, such as Lam Research Corporation and Applied Materials, Inc., are actively advancing PECVD and ALD systems to deposit high-quality ceramic films with precise thickness control and low defectivity, critical for next-generation integrated circuits.
In energy storage and conversion, plasma-deposited ceramic dielectrics are gaining traction in high-energy-density capacitors and solid-state batteries. Advanced dielectric ceramics like Al2O3 and HfO2 are being explored to enhance energy storage density and thermal stability in multilayer ceramic capacitors (MLCCs) and as solid electrolytes. TDK Corporation has reported progress in developing thin-film ceramic capacitors using plasma processes, targeting automotive and industrial applications that require miniaturization and reliability.
For optoelectronics, conformal ceramic coatings deposited via plasma methods are increasingly used as encapsulation layers in OLED displays, photonic integrated circuits, and image sensors, providing both insulation and environmental protection. Companies such as ams OSRAM are integrating plasma-deposited ceramic films to extend the operational lifespans and performance of optoelectronic devices. In photovoltaics, plasma-deposited silicon nitride serves as an anti-reflective coating and surface passivation layer, contributing to record-high solar cell efficiencies, as highlighted by Trina Solar in their latest module releases.
Looking ahead, the industry is expected to see expanded adoption of plasma-deposited ceramics in emerging applications such as flexible electronics, quantum devices, and advanced power modules. Continued collaboration between material suppliers, equipment manufacturers, and device makers will be critical to address challenges like process scalability, interface engineering, and novel material integration, ensuring plasma-deposited ceramic dielectrics remain at the forefront of electronics, energy, and optoelectronics innovation.
2025–2028 Global Market Forecast: Volume, Value, and Regional Trends
The global market for plasma-deposited ceramic dielectrics is poised for significant growth between 2025 and 2028, driven by expanding applications in microelectronics, energy storage, and advanced sensor technologies. Plasma-enhanced chemical vapor deposition (PECVD) and related plasma-based techniques are increasingly favored for creating high-purity, conformal dielectric films such as silicon dioxide (SiO2), silicon nitride (SiNx), and aluminum oxide (Al2O3). These materials are critical for miniaturized devices, high-frequency circuits, and next-generation semiconductor manufacturing.
In 2025, leading equipment suppliers such as Applied Materials and Lam Research are reporting strong demand for plasma deposition tools, particularly from memory and logic chip manufacturers scaling towards sub-5nm nodes. The rapid adoption of advanced dielectric films in 3D NAND and DRAM production is a core market driver, with Asia-Pacific—especially Taiwan, South Korea, and China—accounting for the majority of new installations (TSMC, Samsung Electronics).
Volume-wise, the deployment of plasma-deposited ceramic dielectrics is projected to grow at a compound annual growth rate (CAGR) exceeding 7% from 2025 through 2028. This increase is underpinned by the expansion of semiconductor fabs and the integration of ceramic dielectrics into advanced packaging, power electronics, and RF devices. Value growth is anticipated to outpace volume, reflecting both higher material performance requirements and the adoption of complex multi-layer stacks in logic and memory devices. Major wafer fabrication companies, including Intel and GlobalFoundries, are investing in new lines and material innovations to meet these stringent demands.
- Asia-Pacific: Expected to maintain dominance due to aggressive fab expansions and heavy investment in local supply chains. Chinese foundries such as SMIC are accelerating domestic sourcing of both equipment and precursor chemicals.
- North America: Growth is fueled by strategic investments in semiconductor manufacturing under initiatives like the CHIPS Act. U.S.-based fabs are ramping up adoption of plasma-deposited ceramics for both logic and power electronics (TSMC Arizona).
- Europe: The region is leveraging investments from companies like Infineon Technologies to push advances in automotive and industrial power semiconductors, both of which increasingly rely on robust ceramic dielectric layers for insulation and reliability.
Looking ahead to 2028, market participants anticipate sustained innovation in precursor chemistry and reactor design, aiming to enhance throughput, step coverage, and film properties. Collaboration between equipment OEMs and semiconductor manufacturers will be critical to meeting tighter device specifications and environmental targets, positioning plasma-deposited ceramic dielectrics as a foundational technology in the ongoing evolution of advanced electronics.
Competitive Landscape: Strategies, Partnerships, and Patent Activity
The competitive landscape for plasma-deposited ceramic dielectrics is rapidly evolving as demand for advanced electronic components and energy storage solutions accelerates into 2025. Market participants are deploying multifaceted strategies, emphasizing proprietary process development, strategic partnerships, and aggressive patenting to secure technological leadership.
Major materials providers such as DuPont and Honeywell continue to invest in plasma-enhanced chemical vapor deposition (PECVD) technologies, aiming to achieve higher dielectric constants, lower leakage currents, and improved reliability for next-generation capacitors and microelectronic devices. These firms are focusing on process integration with semiconductor foundries and device manufacturers, often through joint development agreements or technology licensing.
In 2024 and 2025, Applied Materials and Lam Research have both highlighted plasma-based ceramic dielectric solutions as part of their advanced thin-film deposition equipment portfolios. Their recent collaborations with leading foundries signal a trend toward vertical integration and co-innovation, especially in the context of 3D NAND, logic, and memory applications where dielectric performance is increasingly critical.
Startups and niche players are also gaining ground through targeted partnerships and specialization. Oxford Instruments has been active in developing customizable plasma deposition systems for high-k ceramic films, securing contracts with both research institutes and commercial device manufacturers. These collaborations facilitate rapid prototyping and materials testing, accelerating commercialization cycles.
The patent landscape remains highly dynamic. According to recent disclosures and filings, companies are prioritizing intellectual property around novel plasma chemistries, precursor formulations, and in-situ process control methods. ULVAC and Tokyo Electron have each announced significant patent grants related to their plasma ceramic dielectric deposition processes, underlining the sector’s focus on defensible differentiation as global competition intensifies.
Looking ahead to the next few years, industry observers anticipate further consolidation as established players seek to acquire or ally with innovators offering unique process IP or integration expertise. Equally, strategic partnerships between equipment manufacturers, materials providers, and end-users are expected to deepen, driven by the need to address increasingly stringent device performance and miniaturization requirements. The race to secure process know-how and application-specific patents will likely define the competitive dynamics of plasma-deposited ceramic dielectrics through at least 2027.
Technical Challenges and Solutions: Reliability, Scalability, and Integration
Plasma-deposited ceramic dielectrics are increasingly central to advanced electronic and energy devices, but technical challenges persist in reliability, scalability, and integration—especially as the industry anticipates rapid deployment in 2025 and beyond.
A primary reliability concern is the defect density in plasma-enhanced chemical vapor deposition (PECVD) and related plasma-based processes. These methods can introduce nano-voids, pinholes, and interface states that compromise dielectric breakdown strength and long-term stability. Recent advances focus on process optimization—such as adjusting plasma power, precursor flow rates, and substrate temperatures—to minimize such defects. For instance, Applied Materials has developed advanced PECVD systems capable of tighter process control, leading to lower impurity incorporation and improved dielectric integrity.
Scalability remains a challenge, especially for high-volume manufacturing of large-area substrates and for achieving ultra-thin, conformal coatings on complex 3D architectures (e.g., in advanced logic and memory). Recent introductions of atomic layer deposition (ALD)-enhanced plasma tools by companies like Lam Research aim to address this, offering precise layer-by-layer control and uniformity even at the sub-10 nm scale. These tools are now being adopted for production lines in 2025, supporting next-gen semiconductors and high-capacitance MLCCs.
Integration with existing device architectures is another major focus. Ceramic dielectrics must maintain compatibility with metal electrodes and other layers, avoiding issues like delamination or unwanted interfacial reactions during subsequent processing. Tokyo Ohka Kogyo (TOK) has recently expanded its plasma process offerings to include tailored surface treatments that enhance adhesion and minimize interfacial defects, supporting robust integration for advanced packaging and system-in-package (SiP) modules.
Looking ahead, the next few years will likely see broader adoption of in-situ diagnostics and machine learning-driven process control to further boost reliability and repeatability. Major equipment providers, including KLA Corporation, are rolling out real-time monitoring tools for plasma-deposited films, enabling early detection of process drift and defect formation. This real-time feedback is expected to be critical as manufacturers push toward even thinner dielectrics and more demanding device geometries.
In summary, while plasma-deposited ceramic dielectrics face ongoing challenges in reliability, scalability, and integration, the industry in 2025 is responding with advanced process equipment, smarter diagnostics, and tailored surface engineering. These developments position the technology for expanded roles in high-performance electronics, energy storage, and emerging applications over the next several years.
Regulatory, Environmental, and Supply Chain Considerations
The regulatory, environmental, and supply chain landscape for plasma-deposited ceramic dielectrics is evolving rapidly as these materials become increasingly central to advanced electronics, renewable energy systems, and high-performance capacitors. As of 2025, regulatory scrutiny has intensified around the materials and processes used in plasma deposition, particularly concerning hazardous precursor gases and the lifecycle impacts of ceramics.
Key regulatory bodies are updating standards to reflect new plasma deposition chemistries. For example, the U.S. Environmental Protection Agency (EPA) has increased oversight on perfluorinated compounds and volatile organics often used in plasma-enhanced chemical vapor deposition (PECVD) processes. In the European Union, REACH regulations continue to restrict the use of certain metal-organics and halogenated materials, encouraging manufacturers to adopt greener alternatives and closed-loop gas recycling systems. Companies such as Applied Materials are responding by developing plasma tools that emphasize reduced chemical consumption and improved abatement solutions.
Environmental considerations are also driving innovation in the composition of ceramic dielectrics. Leading manufacturers like TDK Corporation and Murata Manufacturing have begun substituting lead-based compounds with barium titanate and other environmentally benign ceramics in their plasma-deposited layers, aligning with global moves to eliminate hazardous substances from electronic products. These companies are also reporting progress in reducing defect rates and energy consumption in plasma-assisted deposition processes, thus lowering their carbon footprint.
On the supply chain front, access to high-purity ceramic precursors and specialized plasma equipment remains a strategic challenge. The market in 2025 is experiencing tightness in the supply of rare earth elements and high-purity gases, partly due to geopolitical factors and increased demand from the electric vehicle and semiconductor sectors. Equipment providers like Kurt J. Lesker Company and Oxford Instruments are investing in global sourcing diversification and vertical integration to ensure continuity for their customers. At the same time, collaborative efforts are underway to establish traceability and sustainability certification for ceramic raw materials.
Looking ahead, regulatory and supply chain pressures are expected to further accelerate the adoption of plasma processes that minimize emissions, waste, and hazardous inputs. The anticipated tightening of environmental standards, particularly in Asia and North America, will likely drive additional investment in advanced abatement, recycling, and digital process monitoring technologies by 2026 and beyond. The industry’s ability to adapt to these evolving expectations will be critical for the broad deployment of plasma-deposited ceramic dielectrics in next-generation electronics and clean energy applications.
Future Innovations: R&D Pipelines and Next-Generation Material Platforms
Plasma-deposited ceramic dielectrics are poised for significant technological advancements in 2025 and the ensuing years, driven by the relentless miniaturization of electronic components and the push for higher device reliability in sectors such as semiconductors, energy storage, and flexible electronics. The plasma-enhanced chemical vapor deposition (PECVD) process remains the principal method, enabling precise control over film thickness, composition, and uniformity at low substrate temperatures—a critical factor for integration with heat-sensitive substrates and next-generation device architectures.
In the semiconductor industry, leading manufacturers are intensifying efforts to improve plasma-deposited silicon nitride (SiNx) and silicon dioxide (SiO2) dielectrics with enhanced barrier properties and reduced defect densities. Applied Materials, Inc. reports ongoing development of advanced PECVD platforms capable of sub-nanometer thickness control, enabling the scaling of logic and memory devices to sub-3 nm nodes. These innovations are vital for supporting the ever-increasing demands of high-performance computing and AI workloads.
In parallel, companies like Lam Research Corporation are exploring new ceramic dielectric chemistries beyond traditional Si-based materials, focusing on aluminum oxide (Al2O3), hafnium oxide (HfO2), and hybrid nanolaminate structures. These materials offer higher dielectric constants (k-values), improved leakage current performance, and greater compatibility with emerging transistor architectures, such as gate-all-around (GAA) FETs and 3D NAND devices. Lam Research’s R&D pipeline includes in-situ plasma treatments and atomic-layer-deposited ceramic stacks, aiming to further reduce interface trap densities and enhance long-term device reliability.
Beyond microelectronics, the energy storage sector is leveraging plasma-deposited ceramics for solid-state battery electrolytes and protective coatings. TDK Corporation is advancing PECVD and related plasma-assisted deposition techniques to create ultrathin, conformal ceramic layers for lithium-ion and solid-state batteries. These innovations are expected to address critical challenges such as dendrite suppression and interfacial stability, enabling safer and higher-capacity energy storage solutions.
Looking ahead, the integration of AI-driven process control and real-time plasma diagnostics is anticipated to accelerate innovation cycles and yield further breakthroughs in film quality and deposition throughput. Collaborative consortia, such as those led by SEMI, are fostering cross-industry R&D efforts to standardize plasma methodologies and speed up the commercialization of next-generation ceramic dielectrics. As a result, the industry outlook for 2025 and the following years suggests robust growth in both the breadth of plasma-deposited ceramic materials and their application scope, from quantum computing components to advanced wearable electronics.
Strategic Recommendations: Investment, Collaboration, and Market Entry
Strategic positioning in the rapidly developing field of plasma-deposited ceramic dielectrics requires a nuanced approach, balancing investment in R&D, targeted collaborations, and agile market entry strategies. As of 2025, the demand for advanced dielectric materials is being driven by the need for higher performance in microelectronics, energy storage, and emerging applications such as flexible electronics and next-generation semiconductors. Market entrants must act decisively to secure technical capabilities and commercial partnerships that align with these trends.
- Investment in R&D and Advanced Manufacturing: Companies should allocate resources to plasma-enhanced chemical vapor deposition (PECVD) and related plasma-based processes, as these techniques enable the deposition of high-purity, conformal ceramic dielectrics with nanometer-scale control. For instance, Oxford Instruments and Plasma-Therm have expanded their PECVD toolsets and process capabilities, directly targeting the fabrication of high-k dielectrics and ultra-thin films for advanced logic and memory devices. Early investment in proprietary process recipes and tool integration will be key to differentiation.
- Collaboration with Equipment and Material Suppliers: Strategic alliances with leading toolmakers and precursor suppliers will accelerate process optimization and reduce development cycles. Partnerships with established players like Entegris (materials) and Advanced Micro-Fabrication Equipment Inc. (AMEC) (equipment) provide access to cutting-edge precursor chemistries and plasma deposition hardware, supporting rapid scale-up and qualification for volume manufacturing.
- Market Entry through Niche Applications: New entrants and innovators should consider targeting high-growth niches—such as dielectric coatings for power electronics, flexible substrates, or thin-film capacitors—where plasma-deposited ceramics offer clear performance or reliability advantages. For example, ULVAC has piloted plasma-deposited dielectric coatings for capacitors and sensors, leveraging their unique process expertise to enter markets with less entrenched competition.
- Engagement in Industry Consortia and Standardization: Participation in industry organizations, such as SEMI, fosters access to evolving standards, roadmaps, and collaborative research efforts. This engagement can help mitigate risks associated with technology adoption and ensure alignment with customer qualification requirements.
Outlook through the next few years suggests that agility in process innovation, close supplier relationships, and selective market targeting will be critical. Companies that secure early wins in plasma-deposited ceramic dielectrics—and build intellectual property portfolios around novel processes—are positioned to capture premium segments in microelectronics and energy storage as adoption accelerates.
Sources & References
- Tokyo Ohka Kogyo Co., Ltd. (TOK)
- ULVAC, Inc.
- Murata Manufacturing Co., Ltd.
- Entegris, Inc.
- Institute of Electrical and Electronics Engineers (IEEE)
- ams OSRAM
- Trina Solar
- SMIC
- Infineon Technologies
- DuPont
- Honeywell
- Oxford Instruments
- ULVAC
- KLA Corporation
- Kurt J. Lesker Company
- Oxford Instruments
- Plasma-Therm
- Advanced Micro-Fabrication Equipment Inc. (AMEC)