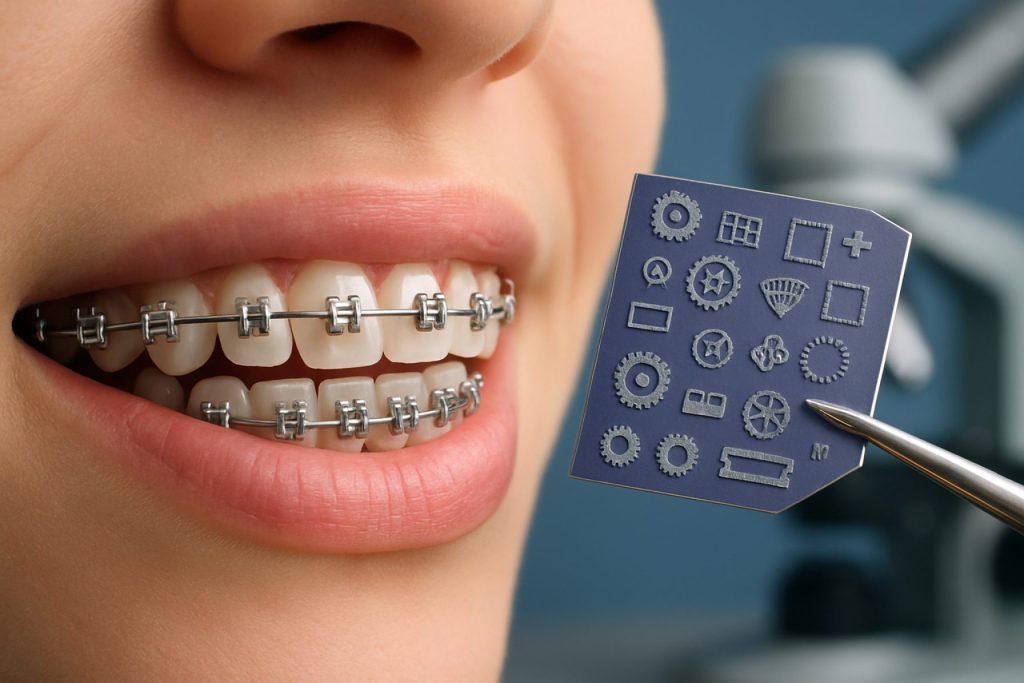
Table of Contents
- Executive Summary: Key Findings and Forecasts to 2029
- Market Size and Growth Projections for Orthodontic Microfabrication
- Breakthrough Microfabrication Technologies Reshaping Orthodontics
- Key Players and Strategic Partnerships (2025 Landscape)
- Material Science Innovations: Biocompatibility and Durability Advances
- Digital Workflow Integration: CAD/CAM and AI in Device Design
- Regulatory & Standards Update: Navigating Compliance in 2025
- Supply Chain and Manufacturing Trends: From Prototyping to Mass Customization
- Competitive Analysis: Startups vs. Established Manufacturers
- Future Outlook: Emerging Opportunities and Challenges (2025–2029)
- Sources & References
Executive Summary: Key Findings and Forecasts to 2029
Orthodontic device microfabrication is undergoing significant transformation, driven by advances in digital design, additive manufacturing, and precision engineering. As of 2025, the sector is characterized by rapid adoption of high-resolution 3D printing and computer-aided design (CAD) for the production of customized orthodontic appliances, including brackets, archwires, and clear aligners. Key players are leveraging these technologies to enhance device accuracy, patient comfort, and treatment efficacy.
A prominent trend is the integration of micro-scale manufacturing with digital workflows. Companies like 3D Systems and Stratasys are leading the field with medical-grade 3D printers capable of producing intricate orthodontic components in biocompatible materials. These devices allow for mass customization, enabling orthodontists to tailor devices precisely to individual patients’ anatomies. In 2024 and early 2025, 3D Systems reported expanded adoption of its NextDent 5100 printer in dental laboratories globally, citing reductions in production time from days to hours and improved fit of orthodontic devices.
Direct-to-consumer aligner providers, including Align Technology, continue to invest in microfabrication to scale up production while maintaining quality control. The company’s proprietary SmartTrack material and automated digital manufacturing platform have set industry benchmarks, processing millions of unique aligners annually as of 2025. Align Technology projects continued double-digit growth in aligner shipments through 2029, underpinned by further advances in microfabrication and AI-driven design optimization.
Metal component microfabrication is also evolving. Dentsply Sirona has expanded its use of laser sintering and milling to produce miniaturized brackets and tubes with enhanced strength and aesthetics. In parallel, American Orthodontics and other manufacturers are deploying automated inspection technologies within microfabrication lines to meet stringent international quality standards.
Looking ahead to 2029, the orthodontic microfabrication market is forecast to experience robust growth, propelled by continued innovation in materials (such as shape-memory polymers and advanced ceramics), smarter manufacturing automation, and integration of AI for predictive device design. The convergence of these technologies is expected to further reduce turnaround time, lower costs, and expand access to high-precision orthodontic care globally.
Market Size and Growth Projections for Orthodontic Microfabrication
The orthodontic device microfabrication market, driven by the demand for highly customized and minimally invasive orthodontic solutions, is poised for significant growth in 2025 and the immediate years beyond. This expansion is underpinned by rapid advancements in digital dentistry, specifically the integration of microelectromechanical systems (MEMS), additive manufacturing (3D printing), and precision laser micromachining for producing brackets, wires, aligners, and auxiliary components.
The adoption of microfabrication technologies has notably accelerated in the orthodontic sector, with leading manufacturers scaling up production capacities to meet surging demand for personalized appliances. For instance, 3D Systems and Stratasys—key providers of 3D printing systems—have actively partnered with orthodontic labs to deliver high-throughput, precision aligner production. Align Technology, the maker of Invisalign, continues to invest in microfabrication infrastructure, leveraging its proprietary SmartTrack material and advanced digital workflows to produce over 14 million aligners annually as of 2024. With expanding international operations and the integration of AI-driven design, the company anticipates continued volume growth into 2025 and beyond.
Additionally, Dentsply Sirona and Envista Holdings Corporation have enhanced their digital orthodontics portfolios, incorporating microfabrication for clear aligners and fixed appliance components. These firms are investing in new fabrication facilities and automated workflows, projecting double-digit growth in the orthodontic segment. The expansion is supported by rising global orthodontic treatment uptake, particularly among adult populations in North America, Europe, and Asia-Pacific.
On the supply side, providers of micromachining and MEMS-based solutions, such as TESCAN and MicroFab Technologies, are witnessing increased collaboration with dental device OEMs for the development of ultra-fine orthodontic components. This is further buoyed by regulatory approvals and the growing acceptance of digitally fabricated orthodontic devices by professional bodies.
Looking ahead to the next few years, the orthodontic device microfabrication market is expected to maintain robust growth, with new entrants and established players expanding digital production capabilities. The convergence of AI, additive manufacturing, and micromachining will continue to lower costs, increase customization, and boost market penetration worldwide, with industry leaders forecasting sustained double-digit annual growth through 2027.
Breakthrough Microfabrication Technologies Reshaping Orthodontics
Microfabrication technologies are fundamentally transforming the design and manufacture of orthodontic devices, ushering in a new era of highly customized, efficient, and aesthetically pleasing solutions. Heading into 2025, the orthodontic sector has witnessed accelerated adoption of digital workflows and micro-scale manufacturing methods, particularly in the production of clear aligners, brackets, and ancillary components.
A primary driver of recent progress has been the integration of high-resolution 3D printing, such as stereolithography (SLA) and digital light processing (DLP), into orthodontic device production. Leading companies like Align Technology (maker of Invisalign) continue to refine their proprietary digital manufacturing platforms, enabling the fabrication of aligners that are tailored to individual patient anatomies with sub-millimeter precision. The company’s recent launches highlight the use of advanced photopolymer resins and precision micro-molding techniques, resulting in aligners with improved fit and clarity.
Similarly, 3D Systems and Stratasys have expanded their dental and orthodontic portfolios with new microfabrication printers capable of producing detailed dental models, indirect bonding trays, and even custom brackets. These devices leverage layer thicknesses as low as 30 microns—enabling the creation of intricate features for improved patient comfort and treatment efficacy. In 2024, Formlabs announced new dental resins and validated workflows specifically targeting orthodontic applications, underscoring the industry’s pivot toward end-to-end digital manufacturing.
Recent years have also seen growing exploration of micro-electromechanical systems (MEMS) for smart orthodontic devices. Companies such as GC Corporation have begun investigating sensor-integrated appliances that can monitor oral conditions or compliance in real time, enabled by miniaturized circuitry produced via microfabrication. While broader clinical deployment is expected post-2025, initial prototypes are under development in collaboration with academic and industrial partners.
Looking ahead, industry leaders anticipate further convergence of microfabrication, AI-driven design, and biocompatible materials. The ongoing expansion of digital design libraries and direct-to-print workflows—championed by Dentsply Sirona and Envista Holdings—is expected to accelerate chairside customization and reduce turnaround times. As regulatory pathways for digitally fabricated orthodontic devices become more established, the next few years are likely to see even more rapid clinical translation of these breakthroughs.
Key Players and Strategic Partnerships (2025 Landscape)
The orthodontic device microfabrication sector in 2025 is witnessing substantial momentum, driven by rapid technological innovation and a surge in strategic collaborations among established players, emerging startups, and material science leaders. This dynamic landscape is characterized by concerted efforts to miniaturize orthodontic components, improve patient comfort, and accelerate treatment efficacy through precise, digitally controlled manufacturing processes.
One of the most prominent industry leaders, 3M, continues to advance microfabrication for orthodontics, leveraging its expertise in advanced ceramics, polymers, and digital production. 3M’s ongoing collaborations with dental software firms and material suppliers aim to integrate artificial intelligence (AI) with micro-engineered brackets and wires, facilitating highly customized treatment solutions.
Another key player, Align Technology, the maker of Invisalign, has expanded its digital manufacturing footprint in 2025 through new partnerships with precision manufacturing companies specializing in micro-scale 3D printing. This enables the production of aligners with enhanced fit and function. Align Technology’s investments in multi-material printing and micro-molding reflect a commitment to continuous improvement in patient-specific orthodontic devices.
On the supplier side, Dentsply Sirona has intensified its collaborations with engineering firms to refine microfabricated orthodontic components, particularly self-ligating brackets and archwires. In 2025, Dentsply Sirona’s partnerships have focused on integrating smart sensor technology into orthodontic appliances, paving the way for “smart braces” capable of real-time treatment monitoring.
Emerging disruptors have also entered the scene. Desktop Metal is partnering with dental labs and device manufacturers to scale up the use of advanced metal additive manufacturing for orthodontic appliances, targeting both the customization and mass production of micro-scale components. Similarly, Stratasys is collaborating with orthodontic specialists to develop next-generation biocompatible resins and micro-precision printing platforms, enabling more intricate geometries for brackets and retainers.
Looking forward, these strategic partnerships are expected to redefine the orthodontic device microfabrication landscape. Industry alliances are increasingly oriented toward integrating AI-driven design, smart materials, and IoT-enabled monitoring, which should result in more efficient workflows, better patient outcomes, and scalable mass customization. This cross-industry collaboration is likely to accelerate innovation and set new standards for orthodontic treatment in the years ahead.
Material Science Innovations: Biocompatibility and Durability Advances
Orthodontic device microfabrication is undergoing significant advancements in material science, particularly in the realms of biocompatibility and durability. As the market for clear aligners and customized orthodontic appliances continues to expand in 2025, manufacturers are investing in novel materials and fabrication techniques that promise improved patient comfort and performance.
A major trend in 2025 is the integration of high-performance polymers and hybrid composite materials in microfabricated orthodontic devices. For instance, companies like 3M have introduced advanced polyurethane and polyetheretherketone (PEEK) blends that offer enhanced flexibility, wear-resistance, and minimal cytotoxicity, addressing long-standing concerns about allergies and tissue response. These materials are specifically engineered to withstand the oral environment, characterized by fluctuating pH, temperature changes, and constant mechanical stress.
Digital workflows and additive manufacturing are also reshaping microfabrication. Straumann Group and Align Technology have expanded their use of biocompatible photopolymers and resin-based materials suitable for high-resolution 3D printing of aligners and brackets. These resins are validated for intraoral use, showing low water absorption and high fracture toughness, which contribute to the devices’ longevity and patient safety.
Surface engineering is another area of innovation. Dentsply Sirona is developing coatings and surface treatments that reduce bacterial adhesion and staining, enhancing both the functional durability and aesthetic stability of orthodontic components. Recent in-house testing has demonstrated a significant decrease in biofilm formation on nano-textured and hydrophilic surfaces, a breakthrough for long-term oral health during orthodontic treatment.
Looking ahead, the industry is focused on sustainable, recyclable materials and closed-loop manufacturing processes. Companies such as Envista Holdings are piloting biobased polymers and exploring the reuse of medical-grade plastics, anticipating stricter regulatory standards and growing environmental awareness among practitioners and patients.
In summary, 2025 marks a pivotal year for material science in orthodontic microfabrication, with the convergence of biocompatible polymers, advanced composites, and intelligent surface modifications driving the next generation of durable, patient-friendly devices. The outlook for the coming years is one of continued innovation, regulatory adaptation, and a shift towards greener manufacturing practices.
Digital Workflow Integration: CAD/CAM and AI in Device Design
The integration of digital workflows—especially CAD/CAM (Computer-Aided Design/Computer-Aided Manufacturing) and artificial intelligence (AI)—has transformed orthodontic device microfabrication as of 2025, with significant advancements anticipated over the next several years. The convergence of these technologies enables unprecedented levels of precision, customization, and efficiency in the design and production of orthodontic appliances such as clear aligners, brackets, and retainers.
In 2025, leading orthodontic manufacturers have universally adopted CAD/CAM systems to streamline device design and fabrication. These systems translate high-resolution intraoral scans into precise 3D models, which are then used to digitally plan orthodontic treatments and design patient-specific devices. For instance, Align Technology employs proprietary CAD software to generate individualized aligner series, while 3Shape provides comprehensive digital orthodontic workflows, integrating advanced 3D scanning, design, and simulation tools into a single platform.
AI-driven algorithms are now embedded within these digital workflows to automate and optimize the design process. AI assists in tooth movement simulation, appliance staging, and even in predicting patient outcomes based on vast datasets of prior cases. Dentsply Sirona leverages machine learning in its SureSmile system to improve treatment planning accuracy and reduce manual intervention, expediting the transition from digital design to physical device production.
Microfabrication of orthodontic devices increasingly relies on advanced manufacturing techniques, such as high-resolution 3D printing and robotic milling, directly informed by CAD/CAM-generated files. Stratasys and Formlabs supply 3D printing solutions specifically tailored for dental and orthodontic labs, enabling batch production of highly customized appliances with micron-level accuracy. The use of biocompatible photopolymer resins and thermoplastics, compatible with these printing platforms, is expanding rapidly, allowing for new device geometries and improved patient comfort.
Looking ahead, the next few years are expected to bring tighter integration of AI and digital workflows, with cloud-based platforms offering real-time collaboration between orthodontists, labs, and device manufacturers. The growing adoption of open digital ecosystems—championed by companies like 3Shape—is likely to accelerate innovation by enabling interoperability across different hardware and software solutions. Additionally, regulatory bodies and organizations such as the American Dental Association are developing updated standards and best practices to ensure the reliability and safety of digitally fabricated orthodontic devices as these technologies become ubiquitous in clinical practice.
Regulatory & Standards Update: Navigating Compliance in 2025
The regulatory landscape for orthodontic device microfabrication is undergoing notable evolution in 2025, driven by rapid advances in digital manufacturing, novel materials, and the increasing adoption of additive manufacturing techniques. Regulatory bodies such as the U.S. Food and Drug Administration (FDA) and the European Medicines Agency (EMA) are updating guidelines to address the unique challenges posed by microfabricated orthodontic devices, particularly those produced via 3D printing and other advanced fabrication methods.
In the United States, the FDA’s Center for Devices and Radiological Health (CDRH) has intensified its focus on the validation and verification processes for microfabricated orthodontic devices. Updated guidance documents emphasize the need for robust process controls, traceability, and documentation throughout the design and manufacturing chain. Of particular note is the FDA’s ongoing pilot program for premarket submissions of additively manufactured dental devices, which provides a more streamlined pathway for market clearance while maintaining rigorous safety and efficacy standards (U.S. Food and Drug Administration).
On the international front, the adoption of the Medical Device Regulation (MDR 2017/745) in Europe has resulted in stricter requirements for technical documentation, post-market surveillance, and clinical evidence for orthodontic devices that employ microfabrication. Manufacturers are increasingly required to demonstrate the biocompatibility and mechanical reliability of novel materials, such as photopolymer resins and shape-memory alloys, which are commonly used in microfabricated aligners and brackets (Straumann Group).
Industry bodies like the International Organization for Standardization (ISO) have also issued updated standards relevant to microfabricated orthodontic devices. ISO 13485 remains central for quality management, but more targeted standards such as ISO 22674 (for metallic materials) and ISO/TS 19807 (for additive manufacturing in dentistry) are increasingly referenced by both manufacturers and regulators (International Organization for Standardization). Adherence to these standards is becoming a prerequisite for both global market access and insurance reimbursement.
Looking ahead, device manufacturers are investing in digital traceability systems and automated quality control, anticipating further harmonization of global regulatory requirements. The integration of artificial intelligence for device design and validation is also prompting regulators to consider new frameworks for software as a medical device (SaMD) in orthodontics (3D Systems). As compliance becomes more complex, collaboration between manufacturers, software providers, and regulatory bodies will be essential to ensure safe, effective, and innovative orthodontic microfabrication in the coming years.
Supply Chain and Manufacturing Trends: From Prototyping to Mass Customization
The microfabrication of orthodontic devices is undergoing significant transformation in 2025, as the industry leverages advanced manufacturing technologies to address both efficiency and personalization. Traditionally reliant on manual processes and standardized products, the sector is rapidly adopting digital workflows, additive manufacturing, and automated quality control to support both rapid prototyping and scalable mass customization.
A central trend is the integration of digital scanning and computer-aided design (CAD) with microfabrication processes, enabling precise, patient-specific orthodontic devices. Companies like Align Technology continue to expand digital treatment planning and 3D printing platforms, facilitating the production of clear aligners and retainers tailored to individual dental morphologies. In 2025, Align Technology announced upgrades to its proprietary 3D printing systems, increasing throughput and material accuracy to meet growing global demand for customized appliances.
Material innovation is also shaping supply chain dynamics. Dentsply Sirona recently reported advances in biocompatible polymers and resin formulations specifically engineered for microfabrication, supporting the production of thinner, more durable orthodontic devices. These new materials are designed to withstand the mechanical stresses of oral environments while allowing for intricate geometries achievable only through high-resolution additive manufacturing.
Automation is increasingly present across the orthodontic device supply chain. Straumann Group has implemented automated post-processing and inspection systems at its manufacturing sites, reducing human error and ensuring consistent device quality. In parallel, distributed manufacturing models are emerging: dental clinics and labs can now leverage cloud-based ordering and local 3D printing hubs, shortening lead times and reducing transportation costs.
Looking ahead to the next several years, the orthodontic device microfabrication sector is expected to see continued adoption of AI-driven design optimization and in-line quality assurance. Suppliers such as 3D Systems are investing in machine learning algorithms to automate the customization of orthodontic appliances, further reducing design-to-manufacture cycles. Regulatory bodies are also updating standards to accommodate these digital-first workflows, ensuring traceability and safety in mass-customized products.
As these trends mature, the orthodontic device industry is poised for greater scalability, cost-effectiveness, and personalization. The convergence of high-precision microfabrication, advanced materials, and digital supply chain management will define the competitive landscape through 2025 and beyond, supporting both clinical innovation and broader patient access to customized orthodontic care.
Competitive Analysis: Startups vs. Established Manufacturers
The orthodontic device microfabrication sector in 2025 is characterized by a dynamic interplay between innovative startups and established manufacturers, each leveraging distinct strengths to capture market share. The competitive landscape is being shaped by advances in digital manufacturing, materials science, and patient-specific treatment protocols, with both incumbents and newcomers racing to commercialize next-generation solutions.
Established players such as 3M and Dentsply Sirona retain significant market power due to their robust global distribution networks, mature regulatory compliance processes, and extensive R&D infrastructure. These companies have accelerated their investments in microfabrication technologies, particularly additive manufacturing (3D printing) for custom brackets and aligners. For instance, 3M continues to expand its Clarity line of clear aligners, leveraging proprietary manufacturing workflows to enhance precision and turnaround times. Similarly, Dentsply Sirona has integrated advanced CAD/CAM solutions into its SureSmile system, enabling more efficient production of patient-specific orthodontic appliances.
In contrast, startups are driving disruptive innovation by focusing on highly specialized microfabrication techniques and digital-first business models. Companies such as LightForce Orthodontics are pioneering fully customized, 3D-printed ceramic brackets that promise improved fit and faster treatment times. LightForce, for example, has reported rapid adoption among orthodontists in North America, citing significant reductions in chair time and labor costs due to their AI-driven design and manufacturing pipeline. Other startups, like ArchForm, are emphasizing direct-to-practitioner workflows with in-office aligner fabrication enabled by compact 3D printers, allowing clinics to offer same-day appliances and improved patient experiences.
The competitive outlook for the next few years will likely see established manufacturers continuing to acquire or partner with emerging technology firms to augment their digital capabilities. Strategic collaborations, such as 3Shape and Ormco’s alliance on digital orthodontics, exemplify this trend, as companies seek to offer end-to-end, digitally integrated treatment ecosystems. Meanwhile, startups are expected to push the envelope on biocompatible materials and scalable, decentralized manufacturing, challenging incumbents to further innovate.
Overall, the competitive landscape in orthodontic device microfabrication is set to intensify through 2025 and beyond, with rapid technology adoption, strategic alliances, and a focus on customization shaping the market’s evolution.
Future Outlook: Emerging Opportunities and Challenges (2025–2029)
The period from 2025 to 2029 is poised to witness rapid advances in orthodontic device microfabrication, with a focus on precision, material innovation, and scalable production. Several driving factors—ranging from digital dentistry integration to patient demand for customized, minimally invasive solutions—are shaping the trajectory of this sector.
One prominent trend is the continued evolution of additive manufacturing, particularly resin-based 3D printing, which allows for the production of highly detailed and patient-specific orthodontic components. Industry leaders such as 3D Systems and Formlabs are investing in new photopolymer resins and hardware that deliver faster print speeds, finer resolution, and biocompatibility improvements. These advances are expected to streamline the production of clear aligners, custom brackets, and indirect bonding trays, reducing delivery times and improving fit and comfort.
Material science breakthroughs are also anticipated to drive the field forward. Companies like Envista Holdings Corporation are exploring advanced polymers and shape-memory alloys for brackets and archwires that can be microfabricated with exceptional accuracy. This enables the development of devices that exert more controlled forces, potentially reducing treatment times and side effects. Furthermore, antimicrobial coatings and smart materials—capable of responding to intraoral conditions—are being integrated into microfabrication pipelines, addressing both hygiene and therapeutic efficacy.
Automation and artificial intelligence (AI) are set to revolutionize the microfabrication workflow. Digital design platforms, such as those developed by Align Technology, are increasingly adopting AI-driven algorithms for treatment planning and device customization. The seamless transfer of these digital plans to microfabrication equipment is improving consistency, accuracy, and scalability. The expected integration of closed-loop feedback systems between intraoral scanners, design software, and fabrication machinery could further minimize errors and reduce manual intervention.
Despite these opportunities, challenges remain. Regulatory pathways for novel materials and manufacturing techniques are evolving, requiring close collaboration with authorities such as the FDA and international standards bodies. Industry participants—like Dentsply Sirona—are investing in robust validation and quality control protocols to ensure compliance and patient safety. Additionally, the need for skilled technicians and interdisciplinary expertise may strain existing educational infrastructure, necessitating new training initiatives.
Looking ahead, the orthodontic device microfabrication sector is expected to experience significant growth, driven by ongoing innovation in digital workflows, materials, and manufacturing automation. Companies that can successfully navigate regulatory, technical, and workforce challenges will be well-positioned to capture emerging opportunities in the global orthodontics market.
Sources & References
- 3D Systems
- Stratasys
- Align Technology
- Dentsply Sirona
- American Orthodontics
- Envista Holdings Corporation
- MicroFab Technologies
- Formlabs
- GC Corporation
- Desktop Metal
- Straumann Group
- Envista Holdings
- Align Technology
- 3Shape
- Formlabs
- American Dental Association
- International Organization for Standardization
- LightForce Orthodontics
- ArchForm