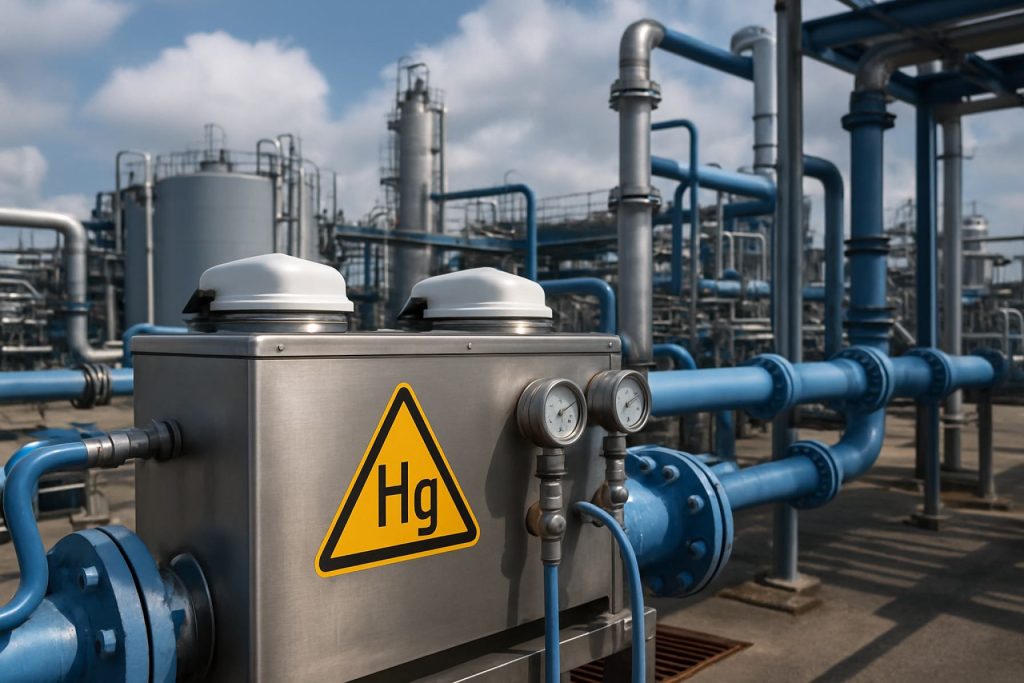
Table of Contents
- Executive Summary: 2025 Outlook for Mercury Vapor Recovery Systems
- Key Market Drivers and Regulatory Pressures Shaping Demand
- Technological Innovations: Next-Gen System Designs and Automation
- Major Players and Strategic Partnerships (Official Company Insights)
- Global Market Forecasts: Growth Projections to 2030
- Regional Analysis: Hotspots and Emerging Markets
- Application Sectors: Power, Mining, Waste, and More
- Environmental Impact and Compliance Strategies
- Challenges, Barriers, and Risk Mitigation Approaches
- Future Trends: Digitalization, IoT Integration, and Sustainability Roadmaps
- Sources & References
Executive Summary: 2025 Outlook for Mercury Vapor Recovery Systems
Mercury vapor recovery systems are experiencing renewed focus in 2025 as global regulatory pressures, corporate sustainability initiatives, and technological advancements align to drive adoption and innovation. Mercury, a potent neurotoxin, remains a critical concern in industries such as chlor-alkali production, fluorescent lighting, waste incineration, and oil and gas processing. Recent years have seen enhanced regulatory frameworks, particularly the Minamata Convention on Mercury, influencing national policies and catalyzing the modernization of vapor recovery infrastructure.
In 2025, leading mercury recovery system manufacturers and engineering firms are prioritizing high-efficiency capture technologies, improved automation, and digital monitoring capabilities. Companies such as Thermo Fisher Scientific and Applied Process Solutions, Inc. have expanded their portfolios to include both turnkey mercury vapor recovery units (MVRUs) and modular solutions tailored for retrofits and small-scale applications. These systems use advanced sorbent beds, catalytic oxidation, and continuous emissions monitoring systems (CEMS) to ensure compliance with evolving emission limits.
Industrial adoption is further propelled by stricter emissions limits in major markets. For instance, the United States Environmental Protection Agency and the European Union have updated standards targeting mercury emissions from industrial sources, reinforcing the need for robust vapor recovery engineering. In response, technology providers such as Pall Corporation and Metso are collaborating with plant operators to integrate mercury-specific filtration and recovery modules into existing gas treatment trains.
Data from 2024 and early 2025 indicate a shift towards predictive maintenance and remote diagnostics, leveraging Industrial Internet of Things (IIoT) platforms. This trend reflects a broader industry movement towards operational resilience and cost efficiency. Companies like Siemens are enabling real-time monitoring and system optimization, reducing unplanned downtime and enhancing regulatory reporting.
Looking ahead to the next few years, the mercury vapor recovery sector is expected to witness moderate but steady growth. This is driven by ongoing phase-outs of mercury use in legacy applications, the decommissioning and remediation of contaminated facilities, and the increasing need for safe handling of mercury in resource recovery and recycling. Engineering innovation will likely focus on compact, energy-efficient systems and integration with broader air quality management frameworks. Stakeholders can anticipate further collaboration between equipment manufacturers, end-users, and regulators to develop standardized performance benchmarks, ensuring effective mercury abatement across diverse industrial settings.
Key Market Drivers and Regulatory Pressures Shaping Demand
In 2025, the demand for mercury vapor recovery systems engineering is being shaped by a convergence of strict regulatory frameworks, heightened environmental awareness, and the ongoing modernization of industrial infrastructure. The Minamata Convention on Mercury, a global treaty ratified by over 140 countries, continues to be a central driver, mandating significant reductions in mercury emissions and the adoption of best available techniques in industries such as chlor-alkali manufacturing, waste incineration, and artisanal gold mining. The operational deadlines and compliance milestones set for the mid-2020s are compelling facilities worldwide to upgrade or retrofit their mercury control technologies, thus spurring demand for advanced recovery systems.
In the United States, the Environmental Protection Agency (EPA) maintains stringent limits on mercury emissions from coal-fired power plants and hazardous waste combustors, as outlined in the Mercury and Air Toxics Standards (MATS). These regulations, periodically updated to reflect evolving scientific understanding, are leading utilities and industrial operators to invest in engineered mercury vapor capture and recovery solutions. Similar regulatory pressures are present in the European Union, where the Industrial Emissions Directive and the Mercury Regulation (EU 2017/852) enforce strict controls and reporting requirements, driving adoption of engineered abatement systems and continuous emissions monitoring technologies (Euro Chlor).
On a sectoral level, the chlor-alkali industry remains a major focus due to its historical reliance on mercury cell technology. With many legacy mercury-cell facilities undergoing decommissioning or modernization, there is a strong need for effective mercury vapor recovery during both operational and demolition phases. Companies specializing in process engineering and decontamination, such as Veolia and Golder Associates, report increased project activity related to mercury vapor management, including the deployment of mobile recovery units and engineered sorbent systems.
Waste-to-energy plants, cement manufacturing, and oil and gas refining are also under scrutiny for mercury emissions, prompting investment in recovery systems engineered for high-throughput and variable process conditions. Equipment manufacturers like Metso and Nederman are expanding their product portfolios to include modular mercury removal solutions tailored to these sectors.
Looking ahead to the next few years, the market outlook for mercury vapor recovery systems engineering is robust. Growth is expected in regions with emerging regulatory enforcement, such as Southeast Asia and Latin America, as well as in mature markets responding to tighter emission limits and sustainability commitments. The integration of digital monitoring, automation, and predictive maintenance is anticipated to further enhance the efficiency and compliance of mercury vapor recovery operations, positioning the sector for continued innovation and expansion.
Technological Innovations: Next-Gen System Designs and Automation
The engineering landscape of mercury vapor recovery systems is rapidly evolving, driven by the dual pressures of stricter environmental regulations and the need for operational efficiency. As we enter 2025, manufacturers and system integrators are focusing on next-generation system designs and automation to address these challenges.
One major area of innovation is the integration of advanced sensor technologies and real-time monitoring. Companies such as Thermo Fisher Scientific have developed highly sensitive mercury analyzers capable of continuous emissions monitoring, allowing for immediate detection of mercury vapor concentrations and enabling prompt system responses. These analyzers are increasingly being embedded within recovery system controls, providing operators with actionable data and supporting compliance with evolving regulatory thresholds, such as those set by the Minamata Convention.
System automation is another frontier. Leading engineering firms like Antero Resources are deploying programmable logic controllers (PLCs) and distributed control systems (DCS) to automate the operation of mercury recovery units. Such automation enables precise control of process parameters—temperature, pressure, and flow rates—to optimize the adsorption and desorption cycles in activated carbon or sulfur-impregnated media systems. The result is higher mercury capture efficiency and reduced operational risk.
In terms of physical system design, there is an ongoing shift toward modular and skid-mounted recovery units. Manufacturers such as Desorption Solutions are offering compact, pre-assembled systems that can be rapidly deployed in a variety of industrial settings, from oil and gas processing plants to waste incineration facilities. This modular approach not only simplifies installation and maintenance but also facilitates scaling of operations as regulatory limits tighten or production volumes change.
Additionally, next-generation systems are incorporating improved sorbent materials, such as enhanced activated carbons and proprietary sulfur-based compounds, which exhibit higher mercury adsorption capacities and longer operational lifetimes. Calgon Carbon Corporation has reported ongoing R&D into these advanced materials, aiming to reduce the frequency of media replacement and lower total lifecycle costs.
Looking ahead, the outlook for mercury vapor recovery systems engineering is shaped by the continued drive toward digitalization and the adoption of artificial intelligence for predictive maintenance and process optimization. As the sector responds to global environmental imperatives, expect further convergence of chemical engineering, automation, and digital analytics within mercury recovery system designs over the next several years.
Major Players and Strategic Partnerships (Official Company Insights)
The mercury vapor recovery systems engineering sector has seen substantial activity from leading industrial equipment manufacturers and environmental technology firms, reflecting heightened regulatory pressure and the global need for safer handling of mercury emissions. As of 2025, several major players are reinforcing their market positions through technological innovation, geographic expansion, and strategic alliances.
Among the leaders, Thermo Fisher Scientific continues to develop advanced mercury monitoring and recovery solutions for industrial and laboratory applications. Their systems are widely deployed in the power generation, waste incineration, and chemical processing sectors, helping facilities comply with stringent international mercury control standards. In 2024, Thermo Fisher enhanced its product portfolio with modular recovery units designed for easier integration and real-time data analytics, addressing the demand for smarter emissions management.
Another key player, Ansell, has focused on engineering containment and filtration systems critical to mercury vapor recovery in manufacturing environments. Their collaborations with industrial automation firms have led to the development of closed-loop recovery systems that minimize human exposure and optimize mercury reclamation efficiency.
Globally, Veolia has taken a prominent role in mercury recovery, especially in hazardous waste treatment and remediation projects. By leveraging proprietary distillation and adsorption technologies, Veolia offers turnkey services for mercury removal and recycling, partnering with utility companies and governments to address legacy contamination and ongoing emissions. Recent years have seen Veolia expand its footprint in Asia and Latin America through joint ventures with local environmental services providers.
Additionally, Merck KGaA (also known as MilliporeSigma in North America) is a significant supplier of specialty chemicals and analytical systems that support mercury vapor recovery and monitoring. Their partnerships with instrumentation manufacturers have resulted in integrated solutions tailored to pharmaceutical, mining, and energy sector requirements.
Strategic partnerships remain a central growth driver in this field. For instance, in early 2025, Veolia and Thermo Fisher announced a collaborative effort to co-develop automated mercury vapor capture modules for large-scale industrial plants, aiming to reduce operational costs and improve regulatory compliance. Such alliances not only accelerate product innovation but also facilitate the transfer of best practices across regions and industries.
Looking ahead, the mercury vapor recovery systems engineering market is expected to witness further consolidation and collaboration, as regulatory scrutiny intensifies and industrial clients seek comprehensive, technologically advanced solutions to mercury control.
Global Market Forecasts: Growth Projections to 2030
The global market for mercury vapor recovery systems is poised for significant growth through 2030, driven by increasingly stringent environmental regulations and heightened awareness of mercury’s environmental and health impacts. As of 2025, demand continues to rise across sectors such as energy, waste management, chemical production, and mining, all of which grapple with mercury emissions compliance mandates.
Key regulatory drivers include the Minamata Convention on Mercury, which compels signatory nations to implement tighter controls on mercury emissions and waste. This framework is directly influencing investment in advanced recovery technologies and system upgrades, particularly in Asia-Pacific and North America. For instance, Veolia and Thermo Fisher Scientific have recently expanded their mercury monitoring and abatement portfolios, targeting industrial clients seeking compliance with evolving standards.
Market data suggests that the mercury vapor recovery systems sector is expected to achieve a compound annual growth rate (CAGR) of approximately 6% to 8% through 2030. This expansion is fueled by increased adoption of engineered recovery solutions in coal-fired power plants, cement manufacturing, and oil and gas processing facilities. Companies like Anguil Environmental Systems and WEG are delivering modular systems designed for rapid deployment and integration with legacy infrastructure, a key requirement among operators facing compressed compliance timelines.
Technological advances are also propelling market growth. Innovations in sorbent materials, real-time mercury vapor analytics, and automated recovery processes are enhancing system efficiency and reducing operational costs. Metso and Alfa Laval have both introduced next-generation mercury removal units with improved capture rates and lower maintenance requirements, appealing to heavy industries facing cost and emissions pressures.
Looking to the next few years, the outlook remains robust, with developing economies increasingly investing in mercury management infrastructure. Continued policy tightening—especially in China and India—alongside international funding for mercury reduction projects, is expected to sustain demand for engineered recovery systems worldwide. The sector’s growth trajectory will likely be reinforced by ongoing industrial modernization and the global push for cleaner, safer industrial processes.
Regional Analysis: Hotspots and Emerging Markets
The global landscape for mercury vapor recovery systems engineering is shaped by both regulatory pressures and the presence of legacy industries handling mercury or mercury-containing products. In 2025, regional hotspots for deployment and innovation are most pronounced in North America, Western Europe, and parts of East Asia, while emerging markets in Latin America, Southeast Asia, and the Middle East are rapidly ramping up adoption due to increasing environmental compliance and industrial modernization.
North America remains a leading market, driven by stringent mercury emission regulations enforced by the U.S. Environmental Protection Agency (EPA) and the Canadian government. The region’s mature industrial base—spanning coal-fired power generation, oil and gas refining, and hazardous waste management—fuels ongoing demand for advanced mercury vapor recovery solutions. Companies such as Mercury Removal Systems, LLC and Dover Corporation continue to supply engineered recovery systems tailored for both new installations and retrofit projects, responding to evolving technology standards like continuous monitoring and automated recovery.
Western Europe, particularly Germany, the UK, and the Netherlands, is characterized by a proactive stance on mercury management, in part due to the EU Mercury Regulation and the Minamata Convention. Regional suppliers like Günther GmbH and EnviroChemie GmbH have focused on integrating mercury vapor recovery into broader industrial wastewater and flue gas treatment systems. The trend here is towards modular, energy-efficient recovery units, often with digital controls and data reporting to meet EU transparency requirements.
East Asia stands out for its scale and speed of adoption, with China, South Korea, and Japan investing heavily in environmental remediation and industrial upgrades. Chinese manufacturers such as Haier Group (for appliances recycling) and China Energy Conservation and Environmental Protection Group are pushing both domestic and export markets for mercury vapor recovery technologies, particularly in the lamp recycling and mining sectors.
Emerging markets—including Brazil, India, Vietnam, and Saudi Arabia—are on a fast trajectory for mercury vapor recovery systems. This is spurred by international treaties, foreign investment, and local public health initiatives. Companies like Thermax Limited in India are introducing locally-adapted vapor recovery solutions. These regions often focus on cost-effective, scalable systems for use in small- to mid-sized industrial facilities, as well as e-waste and healthcare sectors.
Looking ahead to the next few years, regulatory harmonization and technology transfer are expected to further accelerate mercury vapor recovery systems deployment globally. The outlook is especially robust in regions tightening environmental standards and those seeking to leverage circular economy opportunities through mercury recovery and recycling.
Application Sectors: Power, Mining, Waste, and More
Mercury vapor recovery systems engineering is rapidly evolving to address the persistent environmental and regulatory challenges posed by mercury emissions across key industrial sectors. In 2025 and the immediate future, the application of advanced mercury vapor recovery solutions is particularly prominent in the power generation, mining, and waste management industries, as well as in sectors such as cement and chemical manufacturing.
In the power sector, coal-fired power plants remain significant sources of anthropogenic mercury emissions. Mercury-specific control technologies—such as activated carbon injection (ACI), sorbent-enhanced filtration, and integrated multi-pollutant capture systems—are being actively deployed and upgraded. For example, GE Steam Power and Babcock & Wilcox both offer engineered mercury vapor recovery solutions, integrating sorbent injection and particulate control to achieve compliance with stringent regulatory limits such as those imposed by the US Mercury and Air Toxics Standards (MATS), which continue to influence global best practices.
The mining industry, especially gold and non-ferrous metal extraction operations, is another focal area. Mercury is often released during ore processing, particularly in artisanal and small-scale gold mining, as well as larger-scale smelting and refining. Technologies such as vacuum retorts, condensers, and carbon-based adsorption systems are being advanced to capture and recycle mercury vapors. Companies like Thermo Fisher Scientific supply monitoring and recovery solutions tailored for mining applications, supporting both environmental protection and worker safety.
Waste management is also a major application sector, with municipal solid waste incinerators, hazardous waste treatment plants, and fluorescent lamp recyclers investing in mercury vapor recovery. Veolia offers closed-loop recovery and stabilization services, utilizing engineered systems to capture, recover, and safely store or recycle mercury from diverse waste streams. In 2025, the integration of real-time monitoring and automation is enhancing the efficiency and reliability of these recovery systems.
Looking ahead, regulatory tightening and sustainability goals are expected to drive further adoption of mercury vapor recovery systems in cement manufacturing, chemical processing (notably chlor-alkali plants transitioning from mercury cell technology), and the oil and gas sector. Industry leaders such as DuPont are expanding their mercury capture technologies portfolio, focusing on modular solutions and digital integration to optimize performance and lifecycle management. The sector outlook for 2025 and beyond anticipates continued innovation, with data-driven engineering, IoT-enabled diagnostics, and stricter cross-sectorial regulations accelerating the deployment of advanced mercury vapor recovery systems across a broadening array of applications.
Environmental Impact and Compliance Strategies
The engineering of mercury vapor recovery systems is increasingly shaped by stringent environmental regulations and evolving compliance strategies, particularly as global and regional authorities intensify efforts to minimize hazardous emissions. As of 2025, the deployment of advanced mercury vapor recovery technologies is a cornerstone for industries such as coal-fired power generation, waste incineration, chlor-alkali production, and fluorescent lamp recycling, where unmitigated mercury emissions pose significant ecological and public health risks.
Key drivers for innovation and adoption include the Minamata Convention on Mercury, which mandates participating nations to implement best available techniques (BAT) for controlling and ultimately phasing out mercury emissions. In response, engineering firms and system manufacturers are advancing solutions that combine high-efficiency sorbent injection, activated carbon filtration, and multi-stage condensation to capture and recover mercury from exhaust streams with removal efficiencies often exceeding 95% in controlled environments (Chemical Equipment & Specialties, Inc.).
In the United States and Europe, compliance is shaped by regulations such as the Mercury and Air Toxics Standards (MATS) and the Industrial Emissions Directive (IED), respectively. These frameworks require continuous emissions monitoring systems (CEMS) and robust capture technologies, prompting facilities to retrofit or upgrade existing equipment. Recent system designs emphasize modularity, allowing scalable integration with legacy infrastructure while minimizing operational downtime (Thermo Fisher Scientific).
Environmental impact assessments conducted in 2024 and into 2025 indicate that facilities adopting next-generation mercury vapor recovery systems have achieved substantial reductions in atmospheric mercury release, with several reporting compliance levels well below regulatory thresholds. For instance, power plants equipped with advanced sorbent-based systems have documented up to a 90% year-on-year decrease in mercury emissions (Alstom). In the lamp recycling sector, closed-loop recovery systems now enable the reclamation and reuse of mercury, further reducing environmental burden and supporting circular economy objectives (Bulbtronics, Inc.).
- Ongoing R&D is focused on optimizing capture media, reducing maintenance requirements, and integrating digital monitoring for real-time compliance verification (Nalco Water, an Ecolab Company).
- Emerging strategies include hybrid recovery systems that combine thermal desorption with wet scrubbing, enhancing overall mercury capture rates.
- Outlook for 2025–2027 anticipates further tightening of global emission limits, driving broader adoption of advanced engineering solutions and cross-industry collaboration to standardize best practices.
Challenges, Barriers, and Risk Mitigation Approaches
Mercury vapor recovery systems are critical for mitigating environmental and occupational health risks associated with mercury emissions in industries such as chlor-alkali, fluorescent lamp recycling, and gold mining. However, engineering and deploying these systems in 2025 and the near future presents a range of challenges and barriers, accompanied by evolving strategies for risk mitigation.
- Technical Complexities and Process Integration: Efficient mercury vapor capture requires sophisticated adsorption and filtration technologies, such as activated carbon beds and proprietary sorbents. Integration into legacy industrial processes, where operational parameters (temperature, pressure, flow rates) vary significantly, continues to be a challenge. Manufacturers must tailor recovery system designs to site-specific conditions, complicating standardization and increasing engineering costs. For example, Calgon Carbon Corporation and W. L. Gore & Associates, Inc. both stress the importance of adaptable system engineering for effective mercury control.
- Regulatory Uncertainty and Compliance Risks: Evolving regulations, such as the Minamata Convention on Mercury and local emission standards, create uncertainty for system designers and plant operators. Regulatory updates may require retrofitting or re-engineering of existing systems to meet stricter emission limits, particularly in regions tightening enforcement in 2025 and beyond. Companies like Evonik Industries AG highlight ongoing investments in R&D to anticipate and adapt to stricter standards.
- Operational Barriers and Maintenance: Mercury recovery systems often require regular maintenance and careful monitoring to ensure performance and prevent sorbent saturation or system leaks. Remote and resource-limited sites, such as artisanal gold mining operations, face added logistical and training barriers to proper system operation. 3M and other suppliers emphasize the need for robust, low-maintenance designs and comprehensive training modules for operators as part of their risk mitigation strategies.
- Material Handling and Waste Management: Captured mercury must be securely handled and transported for recycling or disposal, introducing risks of secondary exposure or environmental release. Companies are increasingly partnering with certified hazardous waste handlers and investing in sealed containment solutions. Veolia Environnement S.A. exemplifies this approach, offering integrated recovery and disposal services.
Looking ahead, risk mitigation in mercury vapor recovery engineering is expected to focus on modular, automated systems, real-time monitoring, and circular economy approaches to mercury reuse. Collaborations between technology providers, industry end-users, and regulatory bodies will be essential for addressing these ongoing challenges and ensuring effective, sustainable mercury management.
Future Trends: Digitalization, IoT Integration, and Sustainability Roadmaps
The future trajectory of mercury vapor recovery systems engineering is being decisively shaped by advancements in digitalization, the integration of Internet of Things (IoT) technologies, and rigorous sustainability roadmaps. As regulatory requirements tighten worldwide and industries pursue more responsible environmental stewardship, the sector is witnessing an accelerated adoption of intelligent monitoring, control, and data-driven optimization solutions.
By 2025, leading manufacturers and system integrators are rolling out IoT-enabled mercury vapor recovery modules that provide real-time analytics for emissions detection, system health, and predictive maintenance. For example, Thermo Fisher Scientific has developed advanced continuous mercury monitoring solutions that leverage cloud connectivity and remote diagnostics, enabling operators to anticipate equipment failures and optimize processes for minimal emissions. Similarly, A-Gas has incorporated digital tracking and inventory management tools into their mercury recovery services, ensuring full traceability and compliance throughout the handling chain.
Automation is another key trend, with programmable logic controllers (PLCs) and machine learning algorithms being embedded into recovery system architectures. These innovations allow for dynamic adjustment of scrubbing cycles, temperature, and pressure parameters based on real-time mercury concentrations, leading to improved recovery efficiency and reduced energy consumption. Thermo Fisher Scientific and Pall Corporation have both invested in next-generation control systems that seamlessly integrate with facility-wide digital ecosystems, promoting interoperability and streamlined reporting.
Sustainability roadmaps are driving the industry towards closed-loop recovery models, reduced chemical consumption, and circular economy principles. Companies such as A-Gas are piloting mercury reclamation projects that focus on reuse and safe reintegration of recovered mercury, minimizing landfill disposal and hazardous waste generation. Environmental performance certification and transparent lifecycle analysis are increasingly requested by clients, with suppliers responding by publishing verified environmental product declarations (EPDs) and adopting ISO 14001-aligned management systems.
Looking ahead to the next few years, the convergence of digitalization, IoT, and sustainability is expected to result in highly adaptive, low-footprint mercury vapor recovery systems. The sector is likely to see further collaboration with industrial IoT providers, the development of AI-driven emissions mitigation strategies, and broader adoption of blockchain-enabled traceability for mercury handling. Together, these trends will support both compliance with evolving regulations and corporate commitments to environmental responsibility.
Sources & References
- Applied Process Solutions, Inc.
- Pall Corporation
- Metso
- Siemens
- Euro Chlor
- Veolia
- Nederman
- Calgon Carbon Corporation
- Ansell
- Anguil Environmental Systems
- Alfa Laval
- Dover Corporation
- Günther GmbH
- EnviroChemie GmbH
- Haier Group
- China Energy Conservation and Environmental Protection Group
- Thermax Limited
- GE Steam Power
- Babcock & Wilcox
- DuPont
- Alstom
- Nalco Water, an Ecolab Company
- Calgon Carbon Corporation
- W. L. Gore & Associates, Inc.
- Evonik Industries AG
- Thermo Fisher Scientific
- A-Gas