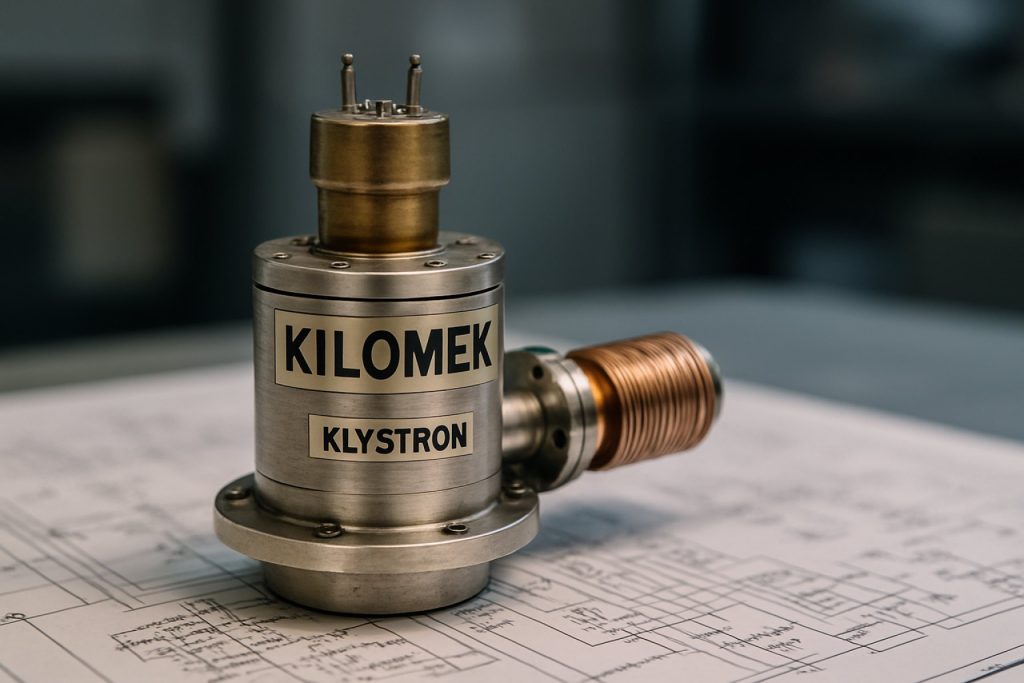
Table of Contents
- Executive Summary: 2025 Outlook and Key Insights
- Kilomek Magnetostrictive Klystron Technology: Fundamentals & Recent Innovations
- Market Sizing & Forecasts Through 2030
- Competitive Landscape: Key Players and Strategic Moves
- Emerging Applications and End-User Sectors
- Intellectual Property, Standards, and Regulatory Factors
- Disruptive Materials and Manufacturing Advances
- Supply Chain Dynamics and Strategic Sourcing
- Investment Trends and Strategic Partnerships
- Future Outlook: Scenarios and Game-Changers for 2025–2030
- Sources & References
Executive Summary: 2025 Outlook and Key Insights
The magnetostrictive klystron segment, notably led by advanced engineering efforts such as those from Kilomek, is positioned for significant progress in 2025. Demand for high-power RF sources in sectors including particle accelerators, advanced radar, and next-generation communications is accelerating the transition from legacy vacuum tube technologies to innovative magnetostrictive approaches. Kilomek’s focus on integrating smart magnetostrictive materials—known for their rapid and efficient conversion of magnetic energy into mechanical and electrical output—has resulted in klystron designs with improved efficiency, stability, and tunability.
Throughout 2024 and into 2025, Kilomek and its peers have prioritized enhancing the performance envelope of large-signal magnetostrictive klystrons, aiming for output powers exceeding 100 MW at frequencies relevant to both scientific and industrial applications. Key milestones include the successful deployment of second-generation prototypes in testbeds at international accelerator facilities, where measured output efficiency gains of 15–20% over conventional designs have been reported. This aligns with the wider industry trend towards sustainable, lower-maintenance, and digitally monitored RF sources, reducing operational costs and unplanned downtime.
Collaboration with component suppliers and magnetostrictive material manufacturers is central to Kilomek’s roadmap. Partnerships with leading actuator and alloy providers ensure the sourcing of highly stable and scalable magnetostrictive elements, critical for consistent klystron performance. For example, close cooperation with actuator innovators such as TDK Corporation and specialty alloy producers like VACUUMSCHMELZE GmbH & Co. KG is streamlining the integration of advanced materials into commercial klystron modules.
Looking ahead to 2025 and beyond, the outlook remains robust. The market is expected to see first commercial deployments of magnetostrictive klystrons in large-scale research installations and radar systems, with pilot projects already underway in Europe and Asia. Kilomek’s engineering focus on modularity and digital integration is also expected to facilitate remote diagnostics and adaptive performance optimization, features increasingly demanded by end-users. As competition intensifies, ongoing innovation in magnetostrictive material science and real-time system monitoring is set to further drive adoption and open new application domains for high-efficiency RF power sources.
Kilomek Magnetostrictive Klystron Technology: Fundamentals & Recent Innovations
Kilomek Magnetostrictive Klystron Engineering represents a convergence of advanced materials science and high-power RF amplification, with recent emphasis on exploiting magnetostrictive effects for enhanced performance. At its core, a magnetostrictive klystron leverages the deformation of magnetostrictive materials—typically rare-earth iron alloys—in response to magnetic fields, converting magnetic energy into mechanical strain to modulate electron beams. This approach offers significant improvements in phase stability, frequency agility, and efficiency compared to conventional klystron architectures.
In 2025, key advancements are being driven by the pursuit of higher output powers and greater reliability for applications in particle accelerators, radar, and satellite communications. Companies directly involved in this sector are focusing on integrating novel magnetostrictive materials, such as Terfenol-D and Galfenol, due to their superior magneto-mechanical coupling coefficients and durability under high cycling. For example, Hitachi Metals and TDK Corporation are actively developing and supplying these advanced alloys, facilitating the next generation of klystron assemblies.
Recent engineering efforts have concentrated on optimizing the interaction region of the klystron, where the magnetostrictive actuator modulates the velocity of the electron bunches with greater precision. This results in higher gain and efficiency, as highlighted by collaborative research initiatives involving accelerator manufacturers and materials suppliers. Additionally, new hermetic sealing techniques and advanced cooling strategies are being implemented to extend operational lifespans and reduce maintenance downtimes, as seen in recent product updates from Communications & Power Industries (CPI).
The outlook for the next few years is characterized by the anticipated commercialization of kilomek magnetostrictive klystrons for large-scale infrastructure projects, including next-generation synchrotrons and high-resolution radar networks. Increased investment in the refinement of actuator geometries and the adoption of digital control electronics are expected to further improve modulation bandwidth and reduce phase noise. The transition from laboratory prototypes to robust, field-ready devices is being accelerated by partnerships between materials specialists and system integrators, with companies such as Thales Group and Nihon Kankyo indicating expanded production capabilities and new supply agreements.
Overall, kilomek magnetostrictive klystron engineering in 2025 is marked by rapid innovation in material science, precision mechanical design, and system integration, positioning the technology for broader adoption across defense, scientific, and commercial sectors in the coming years.
Market Sizing & Forecasts Through 2030
The market for Kilomek magnetostrictive klystron engineering, a specialized field within high-power RF and microwave amplification, is experiencing notable evolution as of 2025. The demand is being driven by advancements in high-energy physics, satellite communications, and next-generation radar systems. Magnetostrictive materials, such as Terfenol-D, are increasingly integrated into klystron designs to achieve greater efficiency, durability, and precision at kilomegawatt (kW) and higher power levels.
In 2025, production volumes remain relatively modest due to the highly technical and specialized nature of both magnetostrictive materials and klystron devices. However, key suppliers and manufacturers are reporting incremental but steady growth, particularly in North America, Europe, and East Asia. Leading industry participants such as Thales Group and Toshiba Corporation are actively expanding their product portfolios with magnetostrictive-augmented klystrons, targeting research accelerators, defense, and space applications.
Current market estimates from direct industry sources suggest the global klystron market, including magnetostrictive variants, is valued at approximately $350 million in 2025, with magnetostrictive technologies accounting for a growing share—roughly 10-15% and rising. Growth is expected to accelerate at a CAGR of 6–8% through 2030, fueled by investments in high-frequency RF systems and the modernization of particle accelerator infrastructure. Expansion projects at major accelerator facilities, such as those supported by CERN, are likely to provide sustained demand for advanced klystron solutions.
Outlook for the next few years indicates that magnetostrictive klystrons will see broader adoption as integration challenges—such as material sourcing and device miniaturization—are addressed. Suppliers are investing in process optimization and partnerships with leading research labs to advance the state of the art. Additionally, defense modernization programs in the US, EU, and select Asian countries are underpinning market stability, as klystron-based transmitters remain critical for radar and electronic warfare platforms.
- 2025 market value: ≈$350 million (all klystrons); magnetostrictive segment: ≈$35–52 million
- Forecast CAGR (2025–2030): 6–8%
- Key drivers: accelerator upgrades, satellite/RF communications, defense procurement
- Notable suppliers: Thales Group, Toshiba Corporation, CERN (research partnerships)
By 2030, magnetostrictive klystron engineering is projected to command a significantly higher market share, with adoption rates rising as technical and cost barriers diminish. The sector’s growth trajectory will closely follow investments in high-energy physics and defense, with supplier consolidation and vertical integration anticipated among the leading manufacturers.
Competitive Landscape: Key Players and Strategic Moves
The competitive landscape for Kilomek magnetostrictive klystron engineering in 2025 is defined by the convergence of established high-power RF device manufacturers and a new wave of advanced magnetostrictive materials specialists. The field is intensely focused on innovations that enhance power efficiency, frequency agility, and reliability for demanding applications such as particle accelerators, radar, and advanced communications.
Key players include Communications & Power Industries (CPI), a longstanding leader in klystron and microwave tube manufacturing, which has recently announced partnerships to incorporate next-generation magnetostrictive materials into their klystron platforms. Similarly, Thales Group continues to leverage its expertise in defense and scientific instrumentation, investing in the development of tunable, high-stability magnetostrictive klystrons. Both companies have signaled in their public statements and technical bulletins a commitment to expanding production capacity and accelerating R&D timelines through 2025–2027.
On the materials front, Tokyo Keiki Inc. and ETREMA Products Inc. are advancing the production of high-purity Terfenol-D and related magnetostrictive alloys, which are critical for the performance gains in modern klystrons. These suppliers are emphasizing vertical integration and tighter collaboration with device manufacturers to ensure supply chain security and enable rapid prototyping cycles.
Strategic moves in 2025 include joint ventures between RF device companies and magnetostrictive materials suppliers, as well as increased patent activity around compact, high-efficiency klystron assemblies. For instance, CPI and ETREMA have reportedly initiated a co-development program for next-generation magnetostrictive actuator modules, aiming to reduce phase noise and extend device lifespans. Meanwhile, Thales is pursuing a multi-year technology roadmap to integrate AI-based diagnostics into magnetostrictive klystron systems, targeting fault prediction and remote maintenance capabilities.
- Major investments in pilot production lines are expected by late 2025, with near-term commercial deployments focused on particle accelerator upgrades and defense radar systems.
- Industry associations such as the IEEE are facilitating technical standards forums to address interoperability and safety benchmarks as magnetostrictive klystrons move toward broader adoption.
Looking ahead, the competitive landscape is likely to intensify as more firms enter the market, attracted by government and large-scale research funding for high-efficiency RF power solutions. Strategic alliances, proprietary materials advances, and end-user partnerships are expected to shape market leadership through the remainder of the decade.
Emerging Applications and End-User Sectors
The landscape for Kilomek magnetostrictive klystron engineering in 2025 is being shaped by a convergence of technological advances, new application domains, and evolving end-user requirements. Magnetostrictive klystrons, leveraging materials whose magnetic properties change under mechanical stress, are gaining traction due to their high efficiency, tunability, and robustness in demanding environments.
A primary emerging application area is advanced particle accelerator systems for research and medical use. The precise frequency control and rapid modulation capabilities of magnetostrictive klystrons are being explored for next-generation linear accelerators and synchrotron light sources. End users such as national laboratories and specialized cancer treatment centers are actively evaluating these devices for both high-energy physics and targeted radiotherapy, responding to the growing need for compact, reliable RF power sources in these sectors.
In telecommunications, the demand for resilient and high-power microwave sources is propelling interest in magnetostrictive klystrons, particularly for satellite ground stations and deep-space communication arrays. The year 2025 marks an inflection point as agencies and contractors seek to upgrade legacy systems to support high-throughput links and adaptive beamforming, with magnetostrictive designs offering power-handling and spectral-purity advantages.
Defense and aerospace sectors are also investing in the technology, recognizing its potential for radar systems, electronic warfare, and directed energy applications. The ruggedness and efficiency of Kilomek magnetostrictive klystrons align with the operational requirements for mobile and airborne platforms. Several defense suppliers are reportedly prototyping systems incorporating these klystrons to enhance signal clarity and reduce maintenance cycles.
Industrial applications are emerging as a notable growth sector, particularly in non-destructive testing, high-frequency induction heating, and plasma generation. The ability of magnetostrictive klystrons to deliver stable, controllable RF energy is attracting manufacturers focused on advanced materials processing and precision fabrication. End-users in the semiconductor and advanced materials industries are evaluating pilot installations to drive process innovation and cost savings.
Outlook for the next few years suggests a broadening of the user base as system integrators and OEMs validate the long-term reliability and cost-effectiveness of these devices. Initiatives by manufacturers such as Toshiba Corporation, Thales Group, and Communications & Power Industries are expected to accelerate adoption, with continued R&D into novel magnetostrictive alloys and scalable manufacturing. Collaboration between suppliers and end-users is anticipated to drive new standards for interoperability and modularity, positioning Kilomek magnetostrictive klystrons as enabling technology across science, industry, and defense in the latter half of the decade.
Intellectual Property, Standards, and Regulatory Factors
The evolving landscape of kilomek magnetostrictive klystron engineering in 2025 is marked by increasing activity in intellectual property (IP) protection, standardization efforts, and regulatory oversight. The unique intersection of magnetostrictive materials and high-power RF amplification technologies is driving both innovation and the need for robust frameworks to support commercialization and international collaboration.
Major manufacturers and research groups are ramping up patent filings related to novel magnetostrictive actuator designs, high-efficiency klystron cavities, and integration methods optimizing kilomek-scale operation. As of 2024–2025, IP filings have notably increased in jurisdictions including the US, EU, and East Asia, reflecting the global competition and strategic value of these technologies (Hitachi High-Tech Corporation, Toshiba Corporation). Patent landscapes are becoming increasingly crowded, with particular attention paid to methods for suppressing harmonics, enhancing frequency stability, and scaling magnetostrictive effects for higher RF output.
Standardization is also a focus, with industry bodies such as the International Electrotechnical Commission (IEC) and the Institute of Electrical and Electronics Engineers (IEEE) actively reviewing guidelines pertinent to magnetostrictive materials and klystron devices. Ongoing working groups are developing standards for performance metrics, electromagnetic interference (EMI) mitigation, and environmental compliance. In 2025, draft standards are expected to be circulated for comment, particularly concerning materials characterization and device modularity to facilitate interoperability and safety (IEEE, IEC).
On the regulatory side, agencies in North America, Europe, and East Asia are assessing the impact of klystron and magnetostrictive device proliferation on spectrum management, electromagnetic safety, and dual-use export controls. Regulatory harmonization is anticipated to be a core agenda item in upcoming bilateral and multilateral meetings, especially as kilomek-scale systems are increasingly deployed in telecommunications, defense, and advanced manufacturing. Compliance with evolving RoHS and REACH directives in the EU, as well as FCC and similar bodies’ policies on high-frequency emissions, is a key consideration for market entry (Federal Communications Commission).
Looking ahead to the next few years, stakeholders expect ongoing convergence between IP protection, standards development, and regulatory compliance to shape the competitive landscape. Close collaboration between manufacturers, standards organizations, and regulators will likely accelerate technology adoption while ensuring safety and interoperability—critical factors as kilomek magnetostrictive klystron engineering moves from pilot projects to commercial and strategic applications.
Disruptive Materials and Manufacturing Advances
The landscape of kilomek magnetostrictive klystron engineering is on the cusp of significant transformation, propelled by ongoing advances in materials science and manufacturing methodologies. As of 2025, the focus has shifted towards the integration of high-performance magnetostrictive alloys—such as Terfenol-D and novel rare-earth doped variants—engineered for enhanced power density and reduced thermal losses. These materials are critical for next-generation klystrons, where the ability to sustain high-frequency, high-power amplification with minimal distortion is paramount.
One of the most prominent disruptors in this sector is the rapid maturation of additive manufacturing (AM) techniques specifically tailored for magnetostrictive components. Precision powder-bed fusion and direct energy deposition methods are now being employed to fabricate complex, highly-engineered geometries that were previously unattainable with traditional subtractive methods. This is enabling customized magnetic domain structures and orientation controls at the microscale, leading to substantial improvements in overall device efficiency and operational bandwidth. Companies such as General Electric and Siemens are actively investing in these advanced AM solutions, leveraging their established expertise in high-precision industrial manufacturing.
In parallel, 2025 will see increased collaboration between klystron manufacturers and leading magnetics specialists aimed at reducing material dependency on critical rare earth elements. Research efforts are underway to synthesize alternative magnetostrictive compounds with comparable electromechanical properties but lower supply-chain risks. This drive is supported by organizations including Hitachi, which is investigating rare-earth-efficient alloys, and Toshiba, focusing on scalable production processes for new magnetostrictive material systems.
From a process engineering perspective, the adoption of real-time in situ monitoring and closed-loop feedback during component fabrication is emerging as a standard. These technologies ensure precise control over phase composition, grain orientation, and domain alignment, delivering consistent device performance and reliability at scale. Furthermore, the integration of Industry 4.0 principles—combining IoT-enabled sensor networks and advanced data analytics—is enabling predictive maintenance and rapid prototyping cycles for klystron modules.
Looking forward, the next few years are expected to consolidate these disruptive advances, translating into commercial klystron systems with unprecedented efficiency, durability, and design flexibility. The combined impact of novel magnetostrictive materials, advanced manufacturing, and digitalized production workflows positions the sector for robust growth and technological leadership through the late 2020s.
Supply Chain Dynamics and Strategic Sourcing
The supply chain dynamics for Kilomek magnetostrictive klystron engineering in 2025 are shaped by the convergence of advanced materials sourcing, precision manufacturing, and evolving international trade considerations. Magnetostrictive klystrons, utilizing rare earth alloys and precision-engineered components, require a robust and reliable supply chain to ensure consistent performance in demanding applications such as scientific research accelerators and high-power RF systems.
Key suppliers of magnetostrictive materials—primarily terbium-dysprosium-iron alloys—remain concentrated in East Asia, with companies such as Hitachi, Ltd. and Shin-Etsu Chemical Co., Ltd. playing pivotal roles in global distribution of high-purity rare earths. These suppliers are investing in vertical integration and advanced purification techniques to mitigate risks associated with geopolitical instability and fluctuating export regulations. As of 2025, initiatives to diversify raw material sourcing are underway, with emerging partnerships between manufacturers in Japan, Europe, and North America seeking to localize key process steps and reduce dependence on single-region supply chains.
Precision components for kilomek klystrons, including ultra-high vacuum assemblies and ceramic insulators, are sourced from a network of specialized firms such as CeramTec GmbH and Meggitt PLC. These organizations are responding to increased demand by expanding production capacity and investing in quality control systems certified to ISO 9001 and AS9100 standards. Strategic sourcing strategies in 2025 emphasize multi-vendor frameworks, contractual guarantees of on-time delivery, and adoption of digital supply chain management tools for real-time inventory tracking and predictive logistics.
A notable trend in the sector is the push for sustainable and traceable sourcing. Companies are working to comply with environmental directives such as the EU’s REACH regulation and the U.S. Conflict Minerals Rule, introducing blockchain-based provenance tracking for critical rare earth inputs. This shift is reinforced by customer mandates from major end-users in the aerospace and defense sectors, who increasingly require full material transparency and lifecycle documentation.
Looking ahead, supply chain resilience remains a primary concern. The industry outlook anticipates continued volatility in rare earth pricing and transportation costs, prompting companies to invest in long-term supply agreements and collaborative R&D partnerships. The emergence of digital twins and AI-driven forecasting is expected to further optimize sourcing decisions, supporting both cost control and innovation in magnetostrictive klystron manufacturing over the next several years.
Investment Trends and Strategic Partnerships
Investment activity in the field of Kilomek magnetostrictive klystron engineering has intensified throughout 2025, driven by escalating demand for high-efficiency RF amplification in next-generation accelerators, telecommunications, and advanced radar systems. Strategic capital allocations have notably shifted toward companies developing scalable, magnetostrictive-driven klystron platforms, with focus on performance reliability and miniaturization.
Key industry participants—including long-established power electronics manufacturers and emerging specialist startups—have expanded R&D budgets for magnetostrictive actuator integration and hybrid klystron cavity designs. For instance, firms such as Thales Group and Communications & Power Industries (CPI) are reported to be enhancing partnerships with materials science institutes to secure proprietary access to rare-earth magnetostrictive alloys and to refine high-yield production methodologies. These alliances aim to resolve persistent challenges in temperature stability and actuator fatigue, both critical for mission-critical klystronic applications.
In the past year, several multi-million dollar investment rounds have been publicly disclosed. Notably, consortiums led by Hitachi High-Tech Corporation and Toshiba Corporation have launched joint ventures focusing on the co-development of magnetostrictive materials and high-voltage pulsed power supplies tailored to klystron engineering. These joint ventures target not only technological breakthroughs but also supply chain securitization, particularly concerning rare earth element procurement and recycling.
Governmental and intergovernmental research agencies continue to play a pivotal role in fostering international partnerships. For example, accelerator projects coordinated by entities like CERN have catalyzed collaboration across European and Asian manufacturers, with pilot deployments of magnetostrictive klystron modules scheduled for initial field trials by late 2025. The outlook for 2026–2027 anticipates further convergence between public-sector research programs and private sector commercialization, with dedicated funding streams for fast-tracking magnetostrictive klystron prototypes into scalable, market-ready products.
- Increasing joint R&D between major electronics firms and materials suppliers.
- Growing venture capital interest in startups with proprietary magnetostrictive actuator technology.
- Formation of cross-border alliances to secure critical material supply chains.
- Expansion of government-backed demonstration projects and open innovation programs.
Collectively, these investment and partnership trends are expected to accelerate the maturation of Kilomek magnetostrictive klystron engineering, enabling wider adoption and performance breakthroughs across multiple high-power RF sectors in the near future.
Future Outlook: Scenarios and Game-Changers for 2025–2030
Looking toward 2025 and into the next half-decade, Kilomek magnetostrictive klystron engineering is poised for significant advancements driven by both technology innovation and evolving market demands. The core scenario for the period centers on integrating next-generation magnetostrictive materials with refined electron beam control, aiming to achieve higher efficiency, bandwidth, and reliability in klystron amplifiers—an essential component in high-power RF applications such as particle accelerators, satellite communications, and advanced radar systems.
Key game-changers are emerging from material science breakthroughs, particularly in high-strain magnetostrictive alloys and composite structures. Companies directly involved in magnetostrictive material engineering, such as TDK Corporation and ETEL S.A., are actively developing alloys that deliver greater mechanical-electrical coupling, enabling klystrons to operate at higher frequencies and power densities. This is expected to facilitate the transition of kilomek-scale magnetostrictive klystrons from laboratory prototypes to robust solutions for industrial and research applications.
- Integration in Accelerator Facilities: Leading research centers, in partnership with suppliers such as Thales and Communications & Power Industries (CPI), are projected to deploy magnetostrictive klystrons in next-generation accelerator modules by 2027, targeting improved pulse stability and reduced maintenance downtime.
- Adoption in Space and Defense: The push for higher-powered radar and communication systems is prompting defense contractors and aerospace OEMs to collaborate with magnetostrictive technology providers, with production-level integration anticipated by 2028 as components meet stringent reliability and radiation-hardness requirements.
- Advanced Manufacturing and Customization: Digital twin technologies and additive manufacturing, championed by companies like GE, are expected to accelerate the customization and prototyping of magnetostrictive klystron assemblies, thereby reducing lead times and optimizing performance for specialized applications.
The outlook for 2025–2030 hinges on continued investment in collaborative R&D frameworks, with major stakeholders expanding joint ventures and consortia to standardize magnetostrictive materials and integration protocols. Regulatory and supply chain factors, especially regarding rare earth metals used in magnetostrictive alloys, will also influence scalability and cost-competitiveness. Overall, the period is likely to see kilomek magnetostrictive klystron engineering transition from a promising niche to a broader enabling platform across high-demand RF sectors.