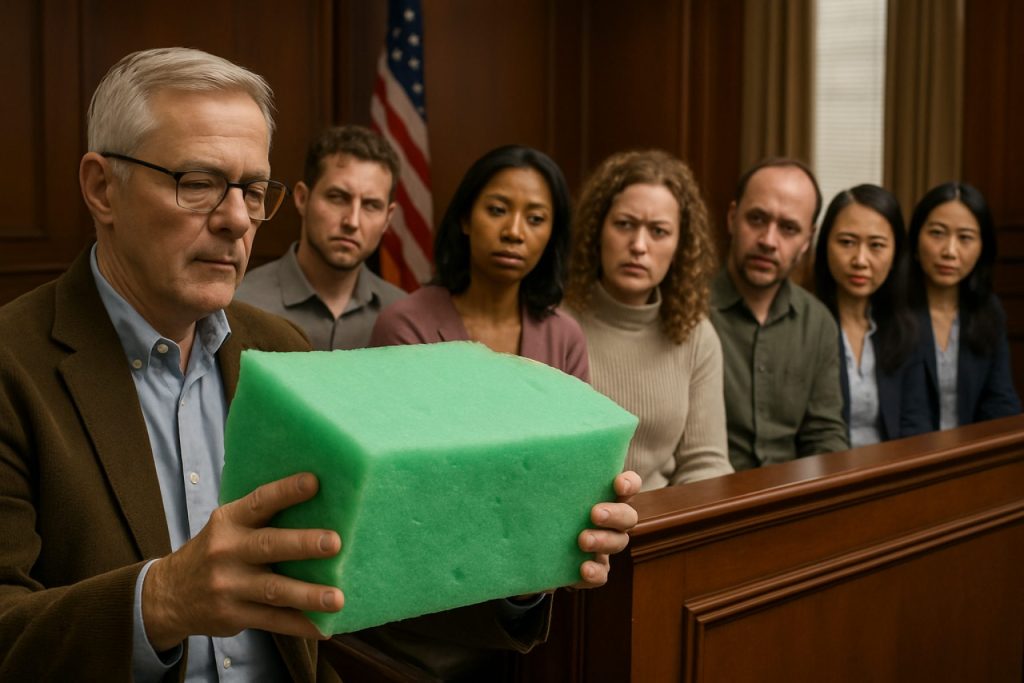
Table of Contents
- Executive Summary & Key Findings
- Jury-Based Polyurethane Recycling: Technology Overview
- 2025 Market Landscape: Regional & Global Trends
- Major Industry Players and Strategic Initiatives
- Current Commercial Deployments and Case Studies
- Cost Analysis and Economic Viability
- Regulatory Drivers and Sustainability Initiatives
- Market Forecasts: 2025–2030 Projections
- Innovation Pipeline: R&D, Patents, and Emerging Startups
- Future Outlook: Challenges, Opportunities, and Strategic Recommendations
- Sources & References
Executive Summary & Key Findings
Polyurethane (PU) recycling technologies are under significant scrutiny and development as global industries seek sustainable solutions to manage rising plastic waste. Jury-based recycling, which entails collaborative evaluation and selection of recycling methods by panels of experts or stakeholders, has emerged as an approach to align technological innovation with practical, scalable implementation. As of 2025, the polyurethane recycling sector is witnessing a convergence of chemical, mechanical, and thermochemical processes, with jury-based methodologies increasingly informing technology adoption, policy formulation, and investment decisions.
Recent initiatives have demonstrated the practical value of jury-based decision-making. For instance, several leading polyurethane producers and recyclers—including Covestro and BASF—have participated in consortia where stakeholder panels assess new recycling technologies for environmental impact, cost-effectiveness, and scalability. In 2024, such approaches helped prioritize chemical recycling routes, notably hydrolysis and glycolysis, as key pathways for flexible and rigid PU foam recovery. These methods are now being piloted at commercial scales across Europe and North America.
In terms of data, the adoption of jury-based frameworks has accelerated the translation of research-stage processes into industrial pilots. According to public statements from Covestro, jury-guided projects have reduced the time from laboratory validation to pilot plant deployment by up to 30%. Moreover, industry collaborations facilitated by organizations like European Diisocyanate & Polyol Producers Association are enabling the standardization of evaluation criteria, ensuring that selected recycling technologies meet both regulatory requirements and market realities.
Looking ahead to the next few years, jury-based polyurethane recycling technologies are expected to play a central role in shaping circular economy practices within the plastics sector. With the European Union’s tightening recycling targets for plastics by 2025, and increasing consumer and regulatory pressure worldwide, the use of expert panels to vet recycling innovations will likely expand. This approach is anticipated to further de-risk investments, streamline industrial partnerships, and accelerate the scaling of advanced recycling solutions.
In summary, as of 2025, jury-based evaluation is becoming integral to the technical and commercial advancement of polyurethane recycling. Its continued application promises to expedite the deployment of sustainable recycling technologies, aligning industry efforts with global environmental objectives and regulatory frameworks.
Jury-Based Polyurethane Recycling: Technology Overview
Jury-based polyurethane (PU) recycling technologies have gained notable traction as the demand for sustainable materials management intensifies globally in 2025. Polyurethanes, widely used in insulation, automotive, furniture, and footwear, pose significant end-of-life challenges due to their thermoset nature. Traditional mechanical recycling methods are limited, prompting innovation in chemical recycling and novel jury-based approaches that break down PU into reusable raw materials.
A leading example in this sector is the jury-based chemical recycling process, which involves selective depolymerization of PU using tailored catalysts and solvents. Companies such as BASF and Covestro have reported advancements in developing pilot-scale facilities that convert post-consumer PU foam waste into polyols, key building blocks for new PU products. In 2024, Covestro opened a dedicated pilot plant in Leverkusen, Germany, aiming to demonstrate the scalability of jury-based recycling for flexible foam mattresses and insulation panels. The company’s process utilizes a proprietary glycolysis technique, which is expected to enter commercial scale by 2026.
Similarly, BASF has focused on optimizing its chemical recycling protocols to improve yield and purity of recovered materials. The firm collaborates with European mattress manufacturers to close the loop on PU foam, with ongoing trials indicating that up to 80% of collected material can be effectively converted into high-quality polyols for new applications. This not only reduces landfill dependency but also aligns with circular economy targets set by the European Union.
From a technical perspective, jury-based recycling technologies are evolving to address contamination and mixed-waste streams. Advanced separation methods, including solvent-based purification and automated material identification, are being implemented to ensure input consistency. Industry bodies such as PU Europe have launched knowledge-sharing platforms to standardize best practices, while also advocating for supportive regulatory frameworks that incentivize recycling infrastructure investments.
Looking ahead to the next few years, commercial deployment of jury-based PU recycling is expected to accelerate, driven by tightening waste directives and consumer demand for sustainable products. Key challenges remain around cost competitiveness and processing mixed or contaminated PU waste; however, continued advancements by companies like BASF and Covestro are likely to solidify jury-based recycling as a viable solution within the broader plastics recycling landscape by 2027.
2025 Market Landscape: Regional & Global Trends
The market for polyurethane (PU) recycling is set to undergo significant transformation in 2025, shaped by both regional innovations and global regulatory momentum. Jury-based polyurethane recycling technologies—a term encompassing collaborative, multi-stakeholder solutions including mechanical, chemical, and novel enzymatic recycling—are gaining traction as the industry seeks sustainable end-of-life strategies for PU products.
In Europe, ambitious targets under the EU Green Deal and Circular Economy Action Plan are driving rapid adoption of advanced PU recycling. Major industry coalitions such as Covestro and BASF are piloting chemical recycling plants that break down PU foams into polyols, which can be reused in new products. BASF’s ChemCycling™ initiative is expected to scale in 2025, focusing on both rigid and flexible foams, and integrating with regional waste collection networks to create closed-loop systems.
In North America, strong automotive and construction sectors are fueling demand for recycled PU, with manufacturers like Huntsman Corporation investing in depolymerization processes and collaborating with downstream users. Partnerships with local authorities and industry associations are enabling the expansion of post-consumer PU foam collection and recycling infrastructure. Meanwhile, the European Diisocyanate & Polyol Producers Association (ISOPA) is working to harmonize standards for recycled content, which is expected to influence North American practices in the coming years.
Asia-Pacific is emerging as a dynamic region, with China and Japan investing in scalable mechanical recycling and upcycling solutions. Companies such as Tosoh Corporation in Japan are exploring enzymatic recycling technologies, with pilot programs targeting automotive seat foams and appliance insulation. China’s regulatory push toward “zero-waste cities” is anticipated to create new markets for recycled PU, though infrastructure gaps remain a challenge.
On a global scale, jury-based approaches—where producers, recyclers, and end-users collaboratively define quality criteria and recycling protocols—are becoming essential to meet evolving regulations and customer demands. The next few years will likely see increased investment in digital tracking of PU waste streams and certification schemes, as industry leaders like Covestro and BASF seek to guarantee recycled content and traceability.
Looking ahead, the 2025 market landscape will be characterized by the convergence of policy, technology, and multi-stakeholder collaboration. As jury-based recycling models mature, they are poised to set new standards for circularity in the polyurethane sector, paving the way for broader adoption and cross-regional harmonization.
Major Industry Players and Strategic Initiatives
As polyurethane (PU) waste continues to mount globally, industry stakeholders are ramping up efforts to implement advanced recycling technologies—particularly jury-based (chemical) recycling methods that break down PU into its constituent monomers for reuse. In 2025, several leading manufacturers, chemical companies, and consortia are actively scaling up pilot projects and forming strategic alliances to commercialize these recycling systems.
One of the foremost players in the field is Covestro, which has accelerated its work on chemical recycling of flexible and rigid polyurethane foams. Covestro’s “Evocycle CQ” process, designed for mattress foam recycling, saw a significant uptick in 2024, with plans for further industrialization and cross-sector partnerships in 2025. The company is collaborating with furniture and mattress manufacturers to close the loop on PU waste streams, focusing on efficient depolymerization and purification of recycled polyols.
Another major contributor, BASF, is expanding its chemolysis-based recycling technology. BASF’s “Chemical Recycling” division is expected to commission new demonstration plants in Europe and Asia in 2025, with the aim of converting post-consumer PU foams into high-quality feedstocks for new materials. BASF’s strategy involves not only proprietary recycling processes but also partnerships across the value chain, including logistics firms and end-product manufacturers.
Meanwhile, Huntsman is piloting novel glycolysis-based technologies to recover polyols from PU insulation and automotive components. The company has announced joint ventures with regional waste management operators to secure consistent input streams and optimize process economics. These moves position Huntsman to supply recycled content for its own polyurethane systems as well as external customers.
In addition to these chemical majors, industry organizations such as PU Europe are fostering multi-stakeholder collaborations. PU Europe’s 2025 roadmap emphasizes investment in recycling infrastructure, harmonization of quality standards for recycled polyols, and the creation of digital platforms to trace PU waste and secondary raw materials throughout the supply chain.
Looking ahead to the next few years, the outlook for jury-based polyurethane recycling is robust. Key drivers include mounting regulatory pressures on landfill diversion, rising demand for circular materials, and advances in process economics. Strategic initiatives by leading manufacturers are expected to move these recycling technologies from demonstration scale to commercial reality, with broader adoption in construction, automotive, and consumer goods sectors anticipated by 2027.
Current Commercial Deployments and Case Studies
The deployment of jury-based polyurethane recycling technologies—those utilizing chemical and physical jury methodologies to reclaim and repurpose polyurethane (PU) materials—has accelerated significantly as of 2025. These advancements are largely a response to mounting regulatory pressure and sustainability goals within the automotive, furniture, and construction sectors, which are major consumers of PU foams and elastomers.
One of the most prominent players, Covestro, has scaled up its proprietary chemical recycling process for flexible polyurethane foams at multiple sites globally. Their pilot plants, operational since 2022, are now transitioning to semi-commercial scale, with the company reporting successful real-world demonstrations with mattress manufacturers and automotive suppliers. Covestro’s “smart chemolysis” method has achieved recovery rates exceeding 70% for polyol fractions, and the company projects full commercial operation for select product lines by 2026.
Similarly, BASF announced in late 2024 the commissioning of its first dedicated PU mattress recycling facility in Germany. Using its “chemical recycling jury” approach, BASF claims to regenerate both polyols and isocyanates—key PU precursors—with yield and purity levels suitable for new foam production. The site is expected to process up to 1,000 tons of post-consumer mattresses annually, with plans to expand capacity and geographic reach in the next two years.
On the mechanical side, Huntsman Corporation has partnered with several regional waste handlers in Europe to implement jury-based physical recycling of rigid and flexible PU foams. Their “mechanical jury” process involves size reduction, cleaning, and reconstitution into new composite panels for the construction and packaging sectors. Early data from 2025 suggest a 30–40% reduction in landfill-bound PU waste in participating regions, with the recycled content meeting critical performance and safety standards.
Industry-wide, commercial deployments of jury-based recycling are still in their early stages, but significant growth is anticipated. The European association Polyurethane Europe has projected that by 2027, at least 15% of all new flexible PU products manufactured in Europe will incorporate recycled content sourced from jury-based technologies. Regulatory alignment, especially under the EU Green Deal, is expected to further accelerate adoption and infrastructure deployment.
These case studies underscore a pivotal shift toward circularity in the polyurethane sector, with commercial jury-based recycling technologies moving rapidly from pilot to full-scale application. The outlook for the next few years is marked by continued investment, scale-up, and cross-industry collaboration, setting new benchmarks for sustainable PU material management.
Cost Analysis and Economic Viability
The economic viability of jury-based polyurethane (PU) recycling technologies is a subject of increasing scrutiny as the global push towards circularity accelerates. In 2025, operational costs, capital expenditures, and market dynamics are shaping the adoption and scalability of these processes. Jury-based recycling, which encompasses various physical and chemical methods for converting post-consumer and post-industrial PU waste into usable feedstocks, faces notable cost-related challenges and opportunities.
Key cost drivers for jury-based PU recycling include feedstock collection and sorting, process energy requirements, catalyst or reagent costs, and downstream purification. Physical recycling methods—such as mechanical grinding—tend to have lower capital and operational expenditures but yield products with limited market value due to property degradation. Conversely, chemical processes such as glycolysis, hydrolysis, and aminolysis can generate higher-value outputs (e.g., polyols), but at higher energy and input costs. For instance, companies like Covestro and BASF have reported ongoing investments in pilot and demonstration facilities, signaling that significant economies of scale are still being sought to achieve commercial competitiveness.
In 2025, the jury-based recycling sector is seeing increased price pressure as virgin polyol prices fluctuate and as regulatory incentives—such as extended producer responsibility (EPR) schemes in the EU—begin to impact cost structures. Producers such as Huntsman have highlighted the importance of integrating recycled polyols into existing production lines to reduce overall costs and environmental footprint. However, the market price for recycled polyols often remains higher than for virgin equivalents, primarily due to the complexity of PU waste streams and the technical requirements for product purification.
Economic outlook for the next few years suggests incremental improvements rather than disruptive cost reductions. Process optimization, improved catalysts, and regional consolidation of recycling facilities are expected to drive down costs gradually. Partnerships between material suppliers, recyclers, and end-users are being formed to share risk and investment—trends evidenced by recent collaborations among major polyurethane producers and recyclers. Government funding and mandates, especially in Europe and parts of Asia, will further influence cost structures and the pace of technology adoption.
Overall, while jury-based PU recycling technologies in 2025 still face a cost premium compared to virgin production, industry leaders are optimistic about medium-term gains from technological innovation, policy support, and scaling effects. The trajectory for economic viability is closely tied to regulatory developments and growing demand for sustainable materials across automotive, furniture, insulation, and footwear sectors.
Regulatory Drivers and Sustainability Initiatives
Polyurethane (PU) recycling technologies are experiencing significant regulatory momentum and sustainability-driven innovation in 2025, as governments and industry stakeholders respond to mounting environmental pressures. The European Union remains at the forefront with its Circular Economy Action Plan and updated Waste Framework Directive, which specifically target plastic waste reduction and promote advanced recycling solutions for complex polymers such as polyurethane. Recent EU policies emphasize Extended Producer Responsibility (EPR), mandating manufacturers to ensure the recyclability of PU-based products and to integrate recycled content into new materials. This regulatory landscape directly incentivizes the adoption and scaling of jury-based polyurethane recycling technologies, which encompass both mechanical and chemical (notably glycolysis and hydrolysis) processes.
In North America, regulatory drivers are also intensifying. The U.S. Environmental Protection Agency (EPA) has launched new guidelines aiming to minimize landfill disposal of end-of-life foams and encourage innovative recycling pilots, particularly for automotive and construction sectors where PU waste is prevalent. Additionally, the Canadian government’s zero plastic waste agenda is pushing local manufacturers to invest in closed-loop recycling models and to partner with technology providers specializing in polyurethane recovery.
On the industry side, sustainability initiatives are rapidly evolving. Major PU producers and suppliers such as Covestro and BASF have set ambitious decarbonization and circularity targets for 2025 and beyond. For example, Covestro is piloting plant-scale chemical recycling facilities in Europe, with the goal of feeding recycled polyols back into its flexible and rigid foam production streams. Similarly, BASF is advancing its ChemCycling™ project, focused on turning post-consumer PU waste into high-quality raw materials through pyrolysis and other chemical routes. These initiatives are typically aligned with voluntary sustainability frameworks such as the Global Commitment by the Ellen MacArthur Foundation, which tracks progress towards plastic circularity and recycled content uptake.
Looking ahead, regulatory frameworks are expected to become more stringent, with the EU poised to introduce mandatory recycled content quotas for polyurethane applications in furniture, automotive, and construction industries by 2027. Concurrently, voluntary industry coalitions—such as the Polyurethane Recycling Industry Group—are standardizing best practices and fostering cross-sectoral collaboration to accelerate technology adoption. As a result, jury-based polyurethane recycling technologies are projected to transition from pilot to commercial scale over the next few years, underpinning the industry’s shift toward circular material flows and reduced carbon footprints.
Market Forecasts: 2025–2030 Projections
Jury-based polyurethane recycling technologies—encompassing chemolysis, enzymatic depolymerization, and advanced mechanical processes—are poised for significant growth in the 2025–2030 period. The global push for a circular plastics economy, combined with tightening regulatory frameworks across the US, EU, and Asia, is compelling manufacturers and recyclers to adopt innovative routes for post-consumer and post-industrial polyurethane (PU) waste.
In 2025, market activity is centered around pilot and early-commercial scale facilities. Companies such as Covestro and BASF are leading with proprietary jury-based chemolysis processes, which break down rigid and flexible PU foams into polyol intermediates suitable for closed-loop recycling. For example, Covestro has announced the expansion of its pilot plant capabilities in Germany, targeting commercial output from recycled PU feedstocks by 2026. Meanwhile, BASF continues to scale its chemical recycling network in Europe, aiming for integration with downstream polyurethane manufacturing.
North America and Europe are expected to remain the primary markets for these technologies, due to robust legislative pressure and the presence of major end-users in automotive, construction, and furniture. Recent industry data indicates that over 1 million metric tons of PU waste is generated annually in Europe alone, with less than 10% currently recycled through advanced methods (European Polyurethane Association). Jury-based recycling is projected to increase this share to 25–30% by 2030, supported by both private investment and EU circular economy targets.
On the technology front, enzymatic and jury-based depolymerization approaches are advancing toward commercialization. Partnerships between material producers and technology startups—such as those fostered by Covestro—are expected to accelerate the deployment of modular recycling units that can be integrated into existing waste management infrastructure.
By 2030, leading industry bodies anticipate that global capacity for jury-based PU recycling could reach 800,000–1,000,000 metric tons per year, up from pilot-scale volumes in 2025 (PU Europe). The sector outlook remains positive, contingent on continued collaboration across the value chain and the scaling of proven technologies to meet both regulatory and market-driven sustainability goals.
Innovation Pipeline: R&D, Patents, and Emerging Startups
Innovation in jury-based polyurethane (PU) recycling technologies is accelerating in 2025, spurred by mounting regulatory pressures and sustainability commitments across the materials sector. Jury-based approaches—named for their modular, multi-step processes that “judge” and separate PU waste streams for tailored recycling—are gaining traction as a bridge between mechanical and chemical recycling. These pipelines are characterized by advancements in sorting, depolymerization, and upcycling, often integrating machine learning for real-time decision-making.
Several major players and startups have announced significant R&D milestones and patent filings in this space. In early 2025, Bayer and BASF confirmed collaboration on a modular jury-based platform that combines AI-driven waste sorting with catalytic depolymerization. Their pilot projects in Germany and the U.S. are designed to process complex post-consumer and post-industrial PU streams, aiming for commercial demonstration by late 2026.
Emerging startups are also entering the field, focusing on scalable, decentralized jury-based recycling units. For example, Covestro launched a startup incubator in 2024, with at least two spin-offs filing patents for jury-based systems that can be installed at waste aggregation sites. These systems utilize sensor arrays and digital twins to optimize the sorting and processing of PU foams, elastomers, and thermosets in real time.
On the intellectual property front, a notable uptick in international patent applications related to jury-based recycling technologies has been registered since late 2023, with filings covering modular reactor designs, selective depolymerization catalysts, and adaptive sorting algorithms. Dow has publicly disclosed several pending patents targeting hybrid jury-based recycling that integrates solvent-based purification with enzymatic degradation, aiming to maximize material recovery from mixed PU waste.
Looking ahead, the innovation pipeline is expected to yield several commercial-scale jury-based recycling facilities between 2026 and 2028, particularly in Europe and Asia, as governments ramp up extended producer responsibility schemes. Industry observers anticipate a wave of licensing deals and joint ventures, as large chemical manufacturers look to secure access to emerging intellectual property and startup innovations. The next few years could see jury-based platforms become a central pillar of the circular polyurethane economy, with pilot-to-commercial upscaling driving down process costs and unlocking new recycled feedstock streams.
Future Outlook: Challenges, Opportunities, and Strategic Recommendations
Jury-based polyurethane (PU) recycling technologies, which refer to processes evaluated and selected by panels of technical experts, are poised to undergo significant advancements in 2025 and the subsequent years. The increasing regulatory pressure to reduce PU waste, particularly from automotive, construction, and furniture sectors, continues to drive the urgency for scalable and economically viable recycling solutions. Recent initiatives in Europe and North America, underpinned by ambitious sustainability goals, are further shaping the trajectory of this technology.
One of the key challenges for jury-based PU recycling technologies lies in the heterogeneity of polyurethane waste streams. The presence of various additives, composite materials, and flame retardants complicates mechanical recycling routes, necessitating robust chemical recycling methods. Companies such as Covestro and BASF have intensified research into depolymerization and solvolysis, aiming to convert PU waste into its monomers or other valuable intermediates. However, the scalability and economic feasibility of these technologies remain under scrutiny, with pilot projects expected to yield critical data in 2025.
Opportunities are emerging as industry consortia and cross-sector collaborations accelerate. The European Union’s push for a circular economy, exemplified by alliances between manufacturers and recyclers, is fostering a supportive environment for innovation. For instance, Covestro is advancing its Evocycle® CQ technology for soft and rigid PU foams, targeting commercial rollout within the next few years. Similarly, BASF is piloting chemical recycling processes that promise higher yields and lower energy consumption compared to traditional methods.
Strategic recommendations for stakeholders in 2025 and beyond include investing in advanced sorting and pretreatment infrastructure, which is crucial for maximizing feedstock quality and minimizing process disruptions. Engaging in pre-competitive collaboration, such as joint ventures or shared pilot plants, will help distribute risk and accelerate technology validation. Policymakers are encouraged to refine waste classification frameworks to better incentivize high-quality recycling and support traceability systems.
In summary, the outlook for jury-based PU recycling technologies in 2025 is cautiously optimistic. While technical and economic barriers persist, momentum is building through targeted R&D, policy support, and collaborative industry efforts. The next few years will be pivotal in determining which jury-selected technologies can transition from pilot to commercial scale, directly impacting the sustainability of the broader polyurethane value chain.