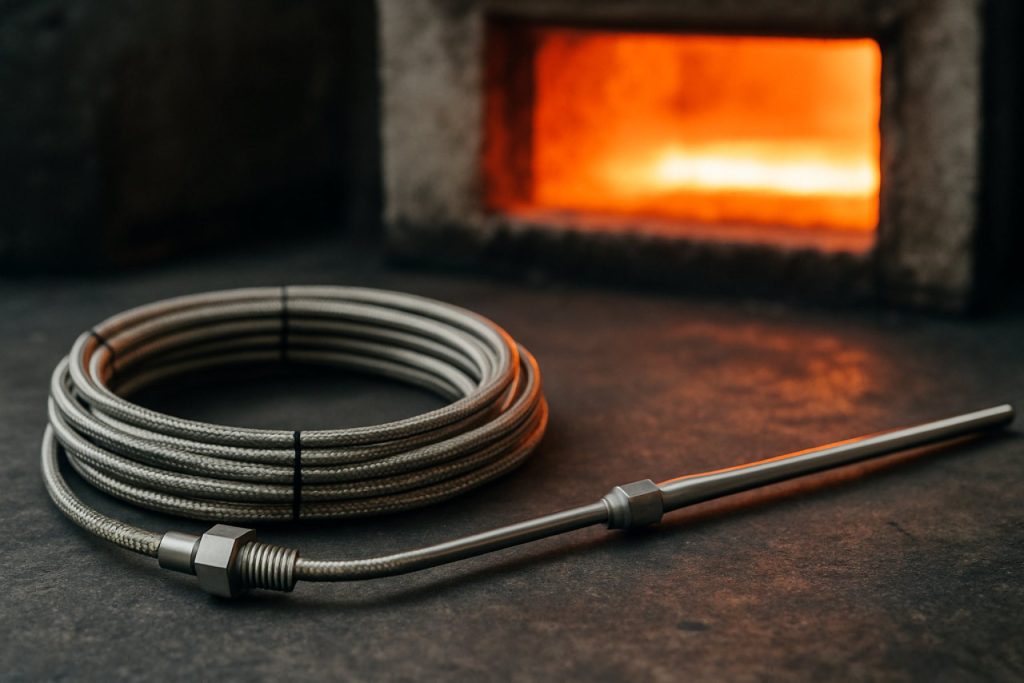
Why 2025 Is a Game-Changer for Jacketed Kiln Thermocouple Manufacturing: Innovations, Global Demand Surges, and the Future of Precision Temperature Control Revealed
- Executive Summary: Key 2025-2030 Market Insights
- Current State of Jacketed Kiln Thermocouple Manufacturing
- Emerging Technologies and Materials: 2025 Breakthroughs
- Major Manufacturers and Industry Leaders (e.g., omega.com, watlow.com, thermocouple.com)
- Regulatory and Standards Landscape: Compliance & Certifications
- Market Forecast: Global Demand & Revenue Projections Through 2030
- Competitive Analysis: New Entrants and Disruptive Players
- Supply Chain Dynamics and Sourcing Strategies
- Industry Applications: From Ceramics to Advanced Metallurgy
- Future Outlook: Innovation Trends and Next-Gen Thermocouple Solutions
- Sources & References
Executive Summary: Key 2025-2030 Market Insights
Jacketed kiln thermocouples, essential for precise temperature measurement in high-temperature industrial processes such as ceramics, glass, and metal manufacturing, are witnessing steady technological and market evolution as of 2025. These specialized thermocouples, characterized by protective metallic or ceramic sheaths (jackets) that enhance durability in harsh kiln environments, are increasingly integral to operational efficiency and product quality control across the global process industries.
The manufacturing landscape in 2025 is dominated by a blend of established multinational instrumentation companies and agile regional specialists. Key players such as Omega Engineering, Thermo Fisher Scientific, and Watlow Electric Manufacturing Company offer broad thermocouple portfolios, including jacketed variants tailored for kiln operations. These companies invest heavily in research and development to improve sensor accuracy, extend operational lifespans, and integrate digital monitoring technologies—trends that are expected to intensify through 2030.
From a production standpoint, advances in metallurgy and ceramic science are enabling manufacturers to develop sheaths with improved resistance to chemical corrosion, mechanical wear, and thermal shock. For example, the adoption of high-purity alumina, Inconel alloys, and silicon carbide jackets is becoming standard in new product lines, especially for kilns operating at temperatures exceeding 1200°C. Companies like Pyrosales and Honeywell are notable for supplying custom-engineered jacketed thermocouples optimized for specific kiln atmospheres and process requirements.
Demand is particularly robust from regions undergoing industrial expansion, such as Asia-Pacific and the Middle East, where investments in ceramics, glass, and advanced materials production are fueling new kiln installations. Simultaneously, stricter regulatory standards regarding process safety and energy efficiency are prompting end users in Europe and North America to upgrade legacy thermocouple systems with higher-specification jacketed models.
Looking ahead to 2030, the market outlook for jacketed kiln thermocouple manufacturing is shaped by three primary trends: further integration of smart sensing (including wireless data transmission and predictive maintenance), ongoing material innovation for extreme environments, and a gradual shift toward custom, application-specific solutions. As digitalization accelerates within process industries, manufacturers like Endress+Hauser and Emerson Electric Co. are expected to play leading roles in shaping the next generation of intelligent kiln thermocouples—cementing their importance in global temperature sensing technology markets.
Current State of Jacketed Kiln Thermocouple Manufacturing
Jacketed kiln thermocouple manufacturing in 2025 is characterized by a steady demand from industries requiring precise temperature measurement in high-temperature, corrosive, or abrasive environments—such as ceramics, glass, cement, and metallurgy. The “jacketed” design typically involves a protective sheath (often Inconel, stainless steel, or ceramics) encapsulating the sensing element, thereby extending service life and reliability in demanding kiln atmospheres.
Global production is led by established instrumentation manufacturers with a strong presence in regions where heavy industry and advanced materials processing are concentrated. Companies such as Omega Engineering, Thermocouple Technology, Inc. (TTEC), and Pyromation are recognized for their wide array of thermocouple assemblies, including custom jacketed designs tailored for kiln environments. European firms like Heraeus and ABB also play significant roles, leveraging advanced metallurgy and sensor integration capabilities.
Recent years have seen incremental innovation, with manufacturers focusing on materials science to improve thermocouple longevity and accuracy. There has been a pronounced shift toward mineral-insulated (MI) cable constructions, which provide superior flexibility and mechanical protection. Additionally, proprietary ceramic and high-nickel alloy sheaths are being deployed to withstand ever-harsher kiln atmospheres. Digital integration—such as embedded signal conditioning and smart diagnostics—has started to appear in premium offerings, aligning with the broader trend towards Industry 4.0 and predictive maintenance.
Production processes remain largely semi-automated due to the precision required in assembling and sealing the junctions within the protective jackets. Quality assurance is paramount, often involving multiple stages of high-temperature calibration and leak testing. Customization is a key differentiator, as kiln geometries and process temperatures vary widely across end users. Major kiln operators increasingly specify unique sheath alloys or calibration protocols, pushing manufacturers to maintain flexible production lines.
Looking ahead to the next few years, the outlook is one of moderate growth, driven by ongoing expansion in cement and glass manufacturing, particularly in Asia-Pacific and the Middle East. Environmental regulations are prompting upgrades of older kiln systems, often with a requirement for more robust and accurate temperature monitoring. Manufacturers are expected to respond with further improvements in sheath material performance—especially for ultra-high-temperature and chemically aggressive settings—and with enhanced digital features for process optimization. With sustainability and operational efficiency high on industrial agendas, demand for premium, long-life jacketed thermocouples is likely to rise, consolidating the position of technically advanced suppliers in the market.
Emerging Technologies and Materials: 2025 Breakthroughs
The manufacturing of jacketed kiln thermocouples is undergoing notable advances as the industry enters 2025, propelled by the demand for higher precision, durability, and reliability in extreme-temperature process environments. Jacketed thermocouples, which feature protective metal or ceramic sheaths, are critical in kiln applications for industries such as cement, ceramics, and advanced materials. Several emerging technologies and materials are influencing this sector.
One major innovation is the integration of advanced sheath materials. Manufacturers like Omega Engineering and Thermocouple USA are increasingly offering thermocouples with sheaths made from high-purity alumina, silicon carbide, and even new grades of molybdenum and Inconel. These materials offer enhanced resistance to chemical attack, oxidation, and thermal shock, which are critical for extending sensor life and reducing maintenance downtime in aggressive kiln atmospheres.
Additionally, 2025 is seeing the adoption of additive manufacturing (AM) and precision forming techniques to produce complex sheath geometries and custom sensor tip designs. This enables more uniform response times and better thermal coupling, as reported by leading process sensor manufacturers like AMETEK, whose subsidiaries specialize in temperature measurement solutions. AM is also facilitating reduced material waste and faster prototyping of bespoke sensor configurations tailored to specific kiln profiles.
On the sensor element front, the use of high-stability thermoelectric alloys—such as new, tightly controlled Type S, R, and B wires—remains a focus. Companies such as Pyrosales emphasize the importance of precise material pairing and purity to minimize drift at temperatures exceeding 1500°C. Emerging alternatives, including the integration of thin-film and microfabricated thermocouple junctions, are under pilot testing, promising faster response and improved long-term calibration stability.
Digitization is another key trend. Intelligent jacketed kiln thermocouples equipped with on-board diagnostics, digital calibration storage, and real-time connectivity are entering the market. Firms like Endress+Hauser are promoting smart temperature sensors that can communicate predictive maintenance needs, thereby reducing unplanned kiln shutdowns and ensuring process quality.
Looking ahead, the sector anticipates increased adoption of hybrid protective sheaths (combining ceramics with refractory metals), broader use of AI-driven quality control in thermocouple production, and continued miniaturization of robust sensor assemblies. As manufacturers respond to increasingly demanding kiln environments, these breakthroughs are expected to set new benchmarks for performance and reliability through 2025 and beyond.
Major Manufacturers and Industry Leaders (e.g., omega.com, watlow.com, thermocouple.com)
The global market for jacketed kiln thermocouple manufacturing is characterized by a concentrated cluster of established industry leaders, primarily headquartered in North America, Europe, and East Asia. These manufacturers provide advanced thermocouple assemblies engineered to withstand the harsh, high-temperature, and corrosive environments typical of kiln operations in ceramics, glass, cement, and metallurgy industries.
Omega Engineering is widely recognized as a frontrunner in thermocouple technology, offering a broad range of high-precision, mineral-insulated, and metal-sheathed thermocouples. Their product lines include customizable jacketed assemblies suitable for kiln use, with a focus on robust sheath materials and precise temperature measurement up to 1700°C. Omega’s commitment to R&D and vertical integration enables rapid adaptation to evolving industrial requirements and standards (Omega Engineering).
Watlow is another major player, renowned for its innovation in thermal solutions. The company manufactures thermocouples specifically designed for high-temperature and corrosive kiln atmospheres, leveraging advanced sheath materials like Inconel® and platinum alloys. Watlow’s global manufacturing footprint and digital integration initiatives position it as a preferred supplier for multinational kiln operators seeking reliability and traceability (Watlow).
Specialty providers such as Thermocouple Technology, Inc. (TCI) focus exclusively on thermocouple and temperature sensor solutions. TCI’s offerings include jacketed kiln thermocouples with tailored sheath diameters and insulation to meet stringent industrial safety and accuracy requirements. Their commitment to rapid prototyping and custom engineering appeals to clients in research, specialty ceramics, and advanced material processing (Thermocouple Technology, Inc.).
In Europe, companies like Tempsens Instruments have expanded their global reach, delivering kiln thermocouples to both established and emerging markets. Their expertise in high-purity ceramic insulators and exotic sheath materials enables them to support demanding applications in glass and refractory sectors (Tempsens Instruments).
Looking ahead to 2025 and beyond, the sector is expected to see increased automation in manufacturing, the adoption of digital quality controls, and a growing emphasis on sustainability—particularly in material sourcing and recycling. Industry leaders are investing in IoT-enabled sensor technologies, predictive maintenance, and lifecycle analytics, driven by end users’ demand for operational efficiency and regulatory compliance. Collaborations between kiln OEMs and thermocouple manufacturers are likely to intensify, resulting in more integrated, smart temperature monitoring systems tailored for Industry 4.0 environments.
Regulatory and Standards Landscape: Compliance & Certifications
The regulatory and standards landscape for jacketed kiln thermocouple manufacturing is experiencing heightened scrutiny and harmonization in 2025, reflecting the growing demands for both process safety and product reliability in high-temperature industrial environments. As kiln thermocouples are essential for precise temperature monitoring in sectors like ceramics, cement, glass, and refractory manufacturing, compliance with established standards remains fundamental to global market participation.
The key international standard for thermocouples, including jacketed variants, continues to be IEC 60584, which specifies requirements for thermocouple types, tolerances, and reference tables. Manufacturers are also expected to comply with the ASTM E230/E230M standards for temperature–electromotive force (EMF) relationships, which are broadly referenced in the Americas and increasingly recognized in other regions. In 2025, these standards form the backbone of quality assurance for leading producers such as OMEGA Engineering, Endress+Hauser, and Thermocouple Technology, Inc..
A notable trend is the stricter enforcement of regional certifications. The European Union maintains the Pressure Equipment Directive (PED) and ATEX Directive for equipment in potentially explosive atmospheres, both of which can apply to kiln thermocouple assemblies used in hazardous zones. Manufacturers such as Endress+Hauser and Siemens provide documentation and certifications that demonstrate conformity with these directives, facilitating market access for their products across Europe.
In North America, National Electrical Manufacturers Association (NEMA) standards and Underwriters Laboratories (UL) certifications play a crucial role in ensuring safe installation and operation, particularly for assemblies interfacing with electrical systems. Leading U.S. manufacturers, including OMEGA Engineering and Thermocouple Technology, Inc., continue to highlight UL and NEMA compliance in their product literature to meet customer and regulatory expectations.
The outlook for the next several years suggests increased alignment between international and regional requirements, driven by digitalization and demands for traceable, verifiable quality. Digital calibration certificates and traceability to national metrology institutes, such as NIST or PTB, are becoming standard offerings from major manufacturers. Additionally, sustainability considerations, such as RoHS and REACH compliance, are gaining importance—especially for European customers—prompting manufacturers to invest in cleaner, more transparent supply chains.
In summary, jacketed kiln thermocouple manufacturers in 2025 face a complex but increasingly harmonized regulatory environment that prioritizes performance, traceability, and safety. The ability to demonstrate multi-standard compliance and provide robust certification packages is now a key differentiator in both established and emerging industrial markets.
Market Forecast: Global Demand & Revenue Projections Through 2030
The global market for jacketed kiln thermocouples is poised for steady expansion through 2030, driven by growing demand in sectors such as cement, ceramics, glass, and metallurgy, where precise high-temperature measurement is critical. As of 2025, manufacturers are reporting increased inquiries and orders, reflecting robust activity in industrial automation and process control. Factors such as stricter energy efficiency regulations, the modernization of aging industrial infrastructure, and the expanding adoption of Industry 4.0 technologies continue to fuel demand for durable, high-accuracy thermocouple solutions capable of withstanding corrosive and high-temperature kiln environments.
Leading industry participants such as Omega Engineering, Thermocouple Technology, Inc. (TTEC), Tempsens Instruments, and Pyrosales have all expanded their product portfolios in recent years to address the evolving needs of kiln operators. These companies are investing in advanced sheath materials (including high-purity ceramics, Inconel, and Hastelloy alloys) and improved sensor calibration protocols, aiming to enhance operational lifespan and measurement fidelity in aggressive kiln conditions. For example, Omega Engineering has focused on mineral-insulated, metal-sheathed (MIMS) thermocouples, which are particularly suited for high-temperature, high-vibration kiln applications, and has reported increased demand from Asia-Pacific and Middle Eastern markets.
Revenue growth is expected to average a CAGR of 4–6% through 2030, with Asia-Pacific leading the expansion due to continued investments in heavy industry and infrastructure. China and India, in particular, are set to remain key markets for kiln thermocouple suppliers as they upgrade cement and glass manufacturing facilities to meet both domestic and export demand. Meanwhile, North America and Europe will see moderate but stable demand, driven by retrofitting projects and stricter compliance with emissions and energy management standards.
On the supply side, manufacturing capacity expansion and digitalization initiatives have led to shorter lead times and more customized solutions. Companies like Tempsens Instruments are leveraging digital platforms to streamline order processing, while others, such as Pyrosales, are investing in R&D partnerships with kiln OEMs to develop next-generation thermocouple assemblies with integrated diagnostics.
Looking ahead, the outlook for jacketed kiln thermocouple manufacturing remains positive through 2030. Innovations in sensor materials, predictive maintenance, and data integration are expected to further differentiate market leaders. As global decarbonization efforts intensify, demand for precise, resilient, and compliant kiln temperature measurement solutions will remain strong, underpinning long-term sectoral growth.
Competitive Analysis: New Entrants and Disruptive Players
The jacketed kiln thermocouple manufacturing landscape in 2025 is characterized by both established multinational instrumentation firms and a new wave of technology-driven entrants. Traditionally dominated by long-standing companies with vertically integrated production and deep process experience, the sector is now witnessing the emergence of agile players leveraging advances in materials science, digital integration, and modular manufacturing techniques.
Major incumbents include Yokogawa Electric Corporation, Honeywell International, and Emerson Electric, all of which maintain comprehensive portfolios of industrial temperature sensors, including specialist thermocouples for high-temperature kiln applications. These companies benefit from broad global distribution networks, rigorous quality control, and close relationships with kiln OEMs and end-users in cement, ceramics, and metallurgy. Their competitive strength stems from proprietary mineral-insulated cable technology, automated assembly lines, and the ability to offer integrated monitoring and control solutions.
However, since 2023, the sector has seen notable disruption from new entrants, particularly start-ups and regional manufacturers in Asia and Europe. These companies are introducing differentiated value propositions: for instance, some have developed flexible or miniaturized jacketed thermocouples utilizing advanced sheath materials such as alloys with enhanced oxidation or corrosion resistance, broadening their use in aggressive kiln atmospheres. Others focus on rapid customization, providing quick-turn manufacturing and delivery services tailored to small-batch needs, which is attractive to specialty kiln operators and research institutions.
Companies such as OMEGA Engineering and Tempsens Instruments have expanded their R&D efforts, with particular emphasis on digital connectivity—embedding smart diagnostics into thermocouple assemblies to enable real-time health monitoring and predictive maintenance. This digitalization trend is lowering the barrier to entry for software-oriented firms that can partner with component manufacturers to provide ‘smart’ kiln thermocouples.
Regional players—especially in India and China—are rapidly scaling, leveraging lower manufacturing costs and government support for domestic instrumentation industries. Firms like Pyro Industrial Systems have expanded exports of jacketed thermocouples, competing aggressively on price and customization. Meanwhile, European SMEs are focusing on innovation, such as additive-manufactured protective sheaths, to carve out premium market segments.
Looking ahead to the next few years, competition is expected to intensify. Incumbents are responding with strategic investments in automation and co-development with kiln manufacturers, while disruptive entrants continue to push boundaries on materials, form factors, and digital integration. The balance between cost, performance, and service flexibility will shape the sector’s competitive dynamics through at least 2027.
Supply Chain Dynamics and Sourcing Strategies
The supply chain dynamics and sourcing strategies for jacketed kiln thermocouple manufacturing in 2025 are shaped by the growing demand in high-temperature process industries, ongoing raw material volatility, and the strategic localization of supply chains. Jacketed thermocouples, essential for accurate temperature measurement in harsh kiln environments, require specialized materials such as high-nickel alloys, stainless steel sheaths, and high-purity insulators. The global supply of these materials continues to be influenced by geopolitical events and capacity constraints, particularly in nickel and specialty alloy markets.
Leading manufacturers, such as Omega Engineering and Minco Products, are actively diversifying their sourcing strategies to hedge against disruptions. For example, multiple vendors for sheath materials and thermocouple wire are being qualified, and strategic inventories are maintained closer to production sites. Companies in the US and Europe are increasingly seeking to source critical metals and components domestically or from allied regions, reducing reliance on single-source suppliers—especially from regions like East Asia, where recent supply chain bottlenecks have had pronounced effects.
There is a notable trend in 2025 toward vertical integration by some key players. Thermocouple Technology, Inc. (TTEC), for instance, continues to invest in in-house alloy processing and sheath manufacturing to secure supply and enhance quality control, reflecting a broader move among specialized manufacturers to bring critical processes under direct control. This strategy helps mitigate risks associated with fluctuating lead times and quality inconsistencies from external suppliers.
Digitalization and traceability have also become central to sourcing strategies. Manufacturers are leveraging real-time supply chain monitoring platforms and blockchain-based traceability systems to ensure transparency from raw material procurement through to finished thermocouple delivery. This is particularly relevant for customers in regulated sectors such as chemical processing and advanced ceramics, who demand full traceability for quality assurance and regulatory compliance.
Looking ahead, as the adoption of advanced kiln systems and higher-temperature processes increases—especially in sectors like battery materials and green hydrogen production—the demand for robust, high-purity jacketed thermocouples is expected to rise. Manufacturers are preparing by forming strategic partnerships with mining and metallurgy firms, and by investing in R&D for next-generation thermocouple materials and automated assembly processes. These moves aim to ensure both security of supply and rapid responsiveness to shifting customer needs in 2025 and beyond.
Industry Applications: From Ceramics to Advanced Metallurgy
Jacketed kiln thermocouples are critical components in a wide range of high-temperature industrial processes. Their durable construction—typically comprising noble or base metal sensor elements encased in protective metallic or ceramic sheaths—enables reliable and precise temperature measurement in the harsh conditions of kilns used across the ceramics, glass, cement, and advanced metallurgy sectors. As of 2025, the manufacturing of jacketed kiln thermocouples is closely aligned with the increasing demand for tighter process control, fuel efficiency, and product quality in these industries.
In the ceramics industry, precise temperature monitoring is essential for sintering, firing, and glazing processes. The trend toward high-performance ceramics and technical ceramics, used in electronics and medical devices, is driving demand for thermocouples capable of withstanding rapid temperature cycling and aggressive chemical environments. Leading manufacturers such as OMEGA Engineering and Thermocouple Technology, Inc. (TTEC) supply custom-designed, mineral-insulated, and noble metal thermocouples specifically for kiln applications, emphasizing robust sheathing materials like Inconel, platinum, and alumina to extend lifespan and accuracy.
In advanced metallurgy, including steel, aluminum, and superalloy production, jacketed thermocouples play a vital role in controlling furnace atmospheres and heat treatment cycles. The push for decarbonization and efficiency continues to stimulate investment in monitoring technology. Companies such as Pyrometry, Inc. and WIKA offer thermocouple assemblies tailored for continuous casting, annealing, and vacuum furnaces, with innovations focusing on resistance to thermal shock, oxidation, and contamination.
Glass and cement kilns present additional challenges due to corrosive vapors and dust. Here, jacketed thermocouples featuring sapphire or high-density ceramic protection tubes are becoming more common, responding to the need for longer service intervals and reduced downtime. Firms like Honeywell and Therm-x are addressing these specific requirements with advanced sheath designs and temperature measurement solutions integrated into digital plant monitoring systems.
Looking ahead to the next few years, the industry is expected to see further growth in demand for specialized thermocouples as sectors pursue digitization (Industry 4.0) and stricter emissions standards. The integration of jacketed kiln thermocouples with wireless data transmission and predictive maintenance platforms is a key area of innovation. Additionally, global expansion of ceramics and specialty metals manufacturing, particularly in Asia and Europe, is likely to drive continued advancements in both materials and manufacturing techniques for these crucial sensors.
Future Outlook: Innovation Trends and Next-Gen Thermocouple Solutions
The future of jacketed kiln thermocouple manufacturing is defined by a convergence of material innovation, digital integration, and growing demands from advanced industrial sectors. As we move through 2025 and beyond, manufacturers are focused on enhancing both the durability and intelligence of kiln thermocouples, particularly for high-temperature and corrosive environments found in ceramics, glass, cement, and specialty metallurgy.
Material advancements remain at the forefront. There is an ongoing shift toward proprietary sheath alloys and new ceramic insulations to combat chemical attack and minimize drift at temperatures well above 1500°C. Companies such as OMEGA Engineering and Thermocouple Technology, Inc. are developing jacketed designs with enhanced outer sheaths—using alloys like Inconel and superalloys—which offer both improved mechanical strength and resistance to aggressive kiln atmospheres. Innovations in mineral-insulated cable construction further enable longer probe life and higher measurement stability.
Digitalization is rapidly transforming thermocouple manufacturing and usage. The trend toward “smart” thermocouples—embedded with diagnostic chips or digital transmitters—is gaining momentum. These next-generation solutions can store calibration data, monitor health in real time, and communicate directly with plant management systems for predictive maintenance. Manufacturers such as Endress+Hauser and WIKA are incorporating digital communication protocols (e.g., HART, IO-Link) into their kiln-rated thermocouple assemblies, supporting Industry 4.0 initiatives throughout process industries.
Automation of manufacturing processes is also a key trend. Automated welding, calibration, and insulation processes are being implemented to reduce variability and enhance quality assurance for jacketed thermocouples. This is especially important for applications where even minor measurement errors can lead to significant production losses or safety issues. Companies like Pyromation are investing in advanced manufacturing technologies to streamline production and offer custom, rapid-turn solutions.
Sustainability concerns are influencing both product design and manufacturing practices. There is increasing focus on extending thermocouple service life, reducing scrap, and selecting recyclable or lower-impact materials for sheaths and insulators. In parallel, energy efficiency in kiln and furnace operations is driving demand for more precise and reliable temperature sensors, spurring further R&D in this area.
Looking forward, the sector is poised for further integration of advanced materials, digital functionality, and sustainable practices. As kiln operating conditions become more extreme and process controls more sophisticated, jacketed thermocouple manufacturers will continue to evolve—delivering solutions that balance performance, longevity, and data-driven intelligence for the industries they serve.
Sources & References
- Omega Engineering
- Thermo Fisher Scientific
- Watlow Electric Manufacturing Company
- Pyrosales
- Honeywell
- Endress+Hauser
- Emerson Electric Co.
- Pyromation
- Heraeus
- AMETEK
- Omega Engineering
- Watlow
- Tempsens Instruments
- Siemens
- Minco Products
- WIKA