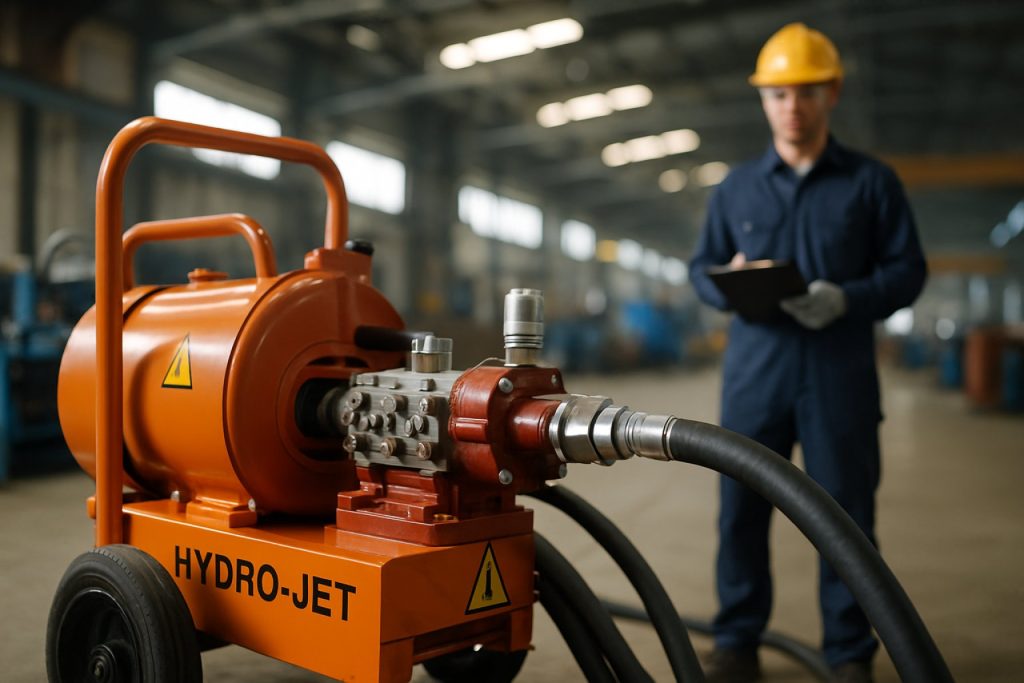
Table of Contents
- Executive Summary: Hydro-Jet Hardware Fabrication in 2025
- Market Sizing and Growth Forecast Through 2030
- Key Industry Drivers and Restraints
- Cutting-Edge Technologies Transforming Hydro-Jet Repairs
- Leading Players and Strategic Partnerships (Official Manufacturer Insights)
- Supply Chain, Materials, and Fabrication Process Trends
- Regulatory Standards and Compliance (ASME & Industry Bodies)
- Case Studies: Breakthrough Projects and Client Successes
- Investment Opportunities and M&A Activity
- Future Outlook: Game-Changing Innovations and Market Disruptors
- Sources & References
Executive Summary: Hydro-Jet Hardware Fabrication in 2025
The hydro-jet repair hardware fabrication sector in 2025 is experiencing significant transformation, shaped by advancements in manufacturing technology, evolving industry standards, and increased adoption across key industries such as oil & gas, shipbuilding, and heavy infrastructure. Hydro-jetting, which relies on high-pressure water jets for cleaning, cutting, and surface preparation, depends on the reliability and precision of its core hardware components—nozzles, pumps, hoses, and control assemblies.
In the current year, leading manufacturers have accelerated integration of automated CNC machining and precision additive manufacturing to enhance fabrication accuracy and reduce lead times for custom hydro-jet components. Notably, OEMs such as Kärcher and Jetstream of Houston have expanded their U.S. and European facilities to accommodate growing demand for high-durability hardware, incorporating advanced alloys and proprietary wear-resistant coatings. These developments are driven by end-user requirements for extended service life and reduced maintenance in harsh operational environments.
The sector is also seeing a shift toward modular hardware designs, enabling more efficient repairs and upgrades. Manufacturers are increasingly offering standardized, interchangeable parts that simplify on-site maintenance and minimize system downtime. This trend is exemplified by companies like StoneAge, Inc., which has introduced modular nozzle and lance systems tailored for rapid deployment and field servicing.
Digitalization is emerging as a critical enabler for fabrication and lifecycle management. Integration of IoT sensors into hydro-jet hardware, pioneered by firms such as WOMA GmbH, provides real-time monitoring of wear patterns and performance, allowing predictive maintenance and data-driven optimization of repair schedules. This capability is expected to become standard across the sector by 2027, further reducing unplanned equipment failures and total cost of ownership.
Looking ahead, the market outlook for hydro-jet repair hardware fabrication is robust. With infrastructure revitalization initiatives underway in North America, the EU, and parts of Asia, demand for high-performance hydro-jetting solutions is set to rise. Manufacturers are responding with increased investment in R&D for next-generation materials and automated assembly lines. At the same time, industry groups such as the WaterJet Technology Association are updating best practices and safety standards to reflect the latest fabrication methods and operational requirements.
In summary, 2025 marks a pivotal year for hydro-jet repair hardware fabrication. The sector is characterized by innovation in materials, design modularity, and digital integration, positioning manufacturers to meet evolving industry needs and capitalize on emerging opportunities in global maintenance and infrastructure markets.
Market Sizing and Growth Forecast Through 2030
The global market for hydro-jet repair hardware fabrication is poised for robust growth through 2030, driven by expanding applications in industrial cleaning, pipeline maintenance, shipbuilding, and infrastructure rehabilitation. As of 2025, the demand for advanced hydro-jetting systems and their associated hardware components—such as high-pressure pumps, nozzles, hoses, and robotic delivery mechanisms—continues to accelerate in both established and emerging markets. This growth is underpinned by increasing investments in water conservation, stricter environmental regulations, and the need for non-invasive repair solutions across oil & gas, petrochemical, and municipal sectors.
Key global manufacturers—including Jetstream of Houston, DYNAJET, StoneAge Tools, and Hammelmann—have reported notable increases in order volumes for both standard and custom-fabricated hydro-jet hardware. Industry feedback in 2024 and early 2025 points to a compound annual growth rate (CAGR) in the high single digits for the sector, with demand particularly strong in North America, Europe, and Asia-Pacific. For instance, Hammelmann continues to expand production capacity and invest in automation to meet rising fabrication requirements. Similarly, StoneAge Tools has accelerated the rollout of modular hardware systems designed for rapid deployment and adaptation in diverse repair scenarios.
Market growth is further supported by ongoing modernization of municipal water infrastructure and the proliferation of aging pipeline networks, which necessitate frequent maintenance and repair. According to suppliers, the hydro-jet segment is increasingly preferred for its precision, reduced downtime, and ability to minimize collateral damage compared to traditional mechanical methods. The trend toward digitalization—such as the integration of sensors and remote monitoring capabilities in fabricated hardware—is expected to generate new revenue streams and service opportunities over the next five years.
Looking ahead, the hydro-jet repair hardware fabrication market is set to benefit from continued R&D investment, partnerships between OEMs and service providers, and the adoption of high-performance materials (e.g., corrosion-resistant alloys and composites) to extend component lifespan. By 2030, industry projections anticipate a significant broadening of end-use cases, particularly in renewable energy infrastructure and advanced manufacturing, further bolstering market expansion. The sector’s growth trajectory will remain closely linked to technological innovation and regulatory trends favoring sustainable, efficient repair methodologies.
Key Industry Drivers and Restraints
In 2025, the hydro-jet repair hardware fabrication sector is propelled by several converging industry drivers, while facing distinct restraints that shape the market landscape. One major driver is the increasing adoption of hydro-jetting technologies in pipeline, refinery, and municipal infrastructure maintenance. As global infrastructure ages, particularly in North America and Western Europe, municipalities and utilities are prioritizing non-invasive, efficient repair solutions. Hydro-jet technology, which uses high-pressure water streams, minimizes downtime and damage compared to traditional mechanical methods, boosting demand for specialized hardware fabrication.
The oil and gas sector continues to be a significant end-user, with many operators investing in advanced hydro-jetting equipment to extend asset life, ensure regulatory compliance, and reduce turnaround times during maintenance. Companies such as Flowserve and Gardner Denver are notable for integrating hydro-jet repair hardware into broader fluid handling solutions, addressing both upstream and downstream requirements.
Environmental regulations are an additional driver, as hydro-jetting is considered a “green” cleaning and repair method—eliminating the need for harsh chemicals. The fabrication of robust, corrosion-resistant hardware is necessary to withstand the high pressures and abrasive environments typical in these applications. This trend is pushing manufacturers to develop new alloys and composite materials, as seen in the product lines of Parker Hannifin and Hydroblast, who focus on durability and lifecycle cost reduction.
From a technological standpoint, the integration of digital controls and automation in hydro-jet hardware fabrication is accelerating. Advanced sensors and remote monitoring are being incorporated into hydro-jet systems, improving operator safety and maintenance scheduling. This evolution is supported by investments from companies such as Kaeser Kompressoren, which emphasizes intelligent system components for industrial cleaning and repair.
However, the sector faces restraints, notably the high initial investment required for specialized fabrication facilities and skilled labor shortages. Precision fabrication of high-pressure components demands advanced machining and welding capabilities, which increases capital expenditures and limits market entry for smaller firms. Fluctuations in raw material costs, particularly for specialty steels and composites, also pose challenges for consistent pricing and supply chain stability.
Looking forward, the outlook remains favorable as infrastructure funding increases and digitalization advances, but companies must navigate capital constraints, workforce training needs, and raw material volatility to sustain growth in hydro-jet repair hardware fabrication through the next few years.
Cutting-Edge Technologies Transforming Hydro-Jet Repairs
The field of hydro-jet repair hardware fabrication is undergoing a profound transformation in 2025, driven by the rapid adoption of digital manufacturing and advanced materials. At the forefront are advancements in precision machining, additive manufacturing (3D printing), and the integration of smart sensors directly into hydro-jet hardware components. Leading equipment manufacturers and suppliers are leveraging these technologies to produce more resilient, efficient, and adaptable repair tools tailored for high-pressure water jetting systems.
One of the most significant trends is the widespread implementation of additive manufacturing techniques. Companies are now using metal 3D printing to fabricate complex components such as nozzles, swivel joints, and high-pressure connectors with internal channels optimized for turbulence reduction and durability. This approach enables faster prototyping and on-demand production, reducing lead times and customization costs. For instance, KMT Waterjet Systems and Flow International Corporation have reported investments in advanced 3D metal printing facilities to accelerate the development of next-generation jetting hardware.
In parallel, the use of advanced alloys and composite materials is expanding. Materials such as tungsten carbide, ceramics, and reinforced stainless steels are increasingly integrated in critical wear parts, greatly extending the service life and reliability of hydro-jet repair tools. Jetstream of Houston and StoneAge, Inc. have highlighted new product lines featuring proprietary coatings and surface treatments engineered to withstand abrasive and corrosive environments typical in industrial cleaning and maintenance operations.
Digitalization is another key driver of innovation. The integration of embedded sensors and IoT connectivity into repair hardware is enabling real-time performance monitoring and predictive maintenance. By capturing data on pressure, flow rate, and vibration, operators are able to optimize repair processes and anticipate component failures before they occur, minimizing downtime. Companies like StoneAge, Inc. are leading efforts to provide “smart” waterblast tools that connect with cloud-based platforms for analytics and remote diagnostics.
Looking forward, the hydro-jet repair hardware sector anticipates continued convergence of digital fabrication, material science, and intelligent systems. Manufacturers are expected to further automate production lines and expand the use of recyclable and sustainable materials in response to industry and regulatory pressures. These developments are poised to deliver safer, more efficient, and environmentally friendly hydro-jet repair solutions through the remainder of the decade.
Leading Players and Strategic Partnerships (Official Manufacturer Insights)
The hydro-jet repair hardware fabrication sector is witnessing significant activity in 2025, with established manufacturers and emerging players driving innovation through advanced fabrication processes and strategic partnerships. The industry is primarily shaped by companies specializing in high-pressure water jetting solutions for the maintenance and repair of industrial infrastructure, including pipelines, vessels, and other critical components.
Among the global leaders, KMT Waterjet Systems continues to invest in research and development, focusing on durable components and precision-engineered assemblies for hydro-jet repair systems. In 2024, the company expanded its production capabilities to meet rising demand in both North America and Europe. Their collaborations with OEMs and regional distributors are enabling faster deployment of tailored hardware sets for on-site repairs.
Another influential manufacturer, Flow International Corporation, has recently introduced modular repair kits and customizable fabrication solutions aimed at petrochemical and offshore markets. Strategic alliances with service companies and asset owners have allowed them to refine repair hardware based on real-world feedback, enhancing ease of integration and operational safety.
In Asia, Jetstream of Houston has solidified its presence through joint ventures with local fabricators, enabling the company to provide region-specific hydro-jet repair hardware. Their 2025 initiatives include the development of corrosion-resistant components and robust quick-connect systems that cater to the unique challenges of industrial sectors across Southeast Asia.
Europe’s StoneAge, Inc. is notable for its collaborative approach, often partnering with engineering consultancies and end-users to co-develop next-generation repair tools. In 2025, StoneAge is emphasizing smart hardware integration, with sensor-enabled components that support predictive maintenance and remote diagnostics—an advancement made possible through ongoing partnerships with automation and digital solutions providers.
Looking ahead, the hydro-jet repair hardware fabrication landscape is expected to further consolidate around strategic partnerships. Manufacturers are increasingly forming alliances with technology companies, material science innovators, and service providers to accelerate the adoption of advanced materials, automation, and digital monitoring. As regulatory pressures and safety standards tighten globally, these collaborations are anticipated to drive efficiency, traceability, and the overall reliability of hydro-jet repair operations over the next few years.
Supply Chain, Materials, and Fabrication Process Trends
The landscape of hydro-jet repair hardware fabrication is undergoing significant changes in 2025, driven by shifts in the global supply chain, evolving material preferences, and advances in fabrication technologies. These trends are closely tied to the needs of industries such as oil and gas, marine, and infrastructure maintenance, where hydro-jetting is a critical process for cleaning and repairing pipelines and surfaces.
A key theme in 2025 is the diversification of supply chains for core components, such as nozzles, high-pressure pumps, and connectors. Manufacturers are prioritizing regional sourcing and multiple supplier relationships to mitigate risks exposed by recent global disruptions. Companies like Kärcher and Ingersoll Rand are expanding their supplier networks in North America and Europe to ensure a steady flow of high-grade stainless steel and abrasion-resistant alloys required for hydro-jet hardware fabrication.
Material selection is evolving, with a marked increase in the use of duplex and super duplex stainless steels, ceramics, and advanced polymer composites. These materials offer improved corrosion resistance and longevity, essential for hardware operating in aggressive environments. Parker Hannifin has reported a rise in demand for custom-fabricated components using high-performance alloys and engineered plastics, tailored for hydro-jet cutting and repair systems. Innovations in wear-resistant ceramic inserts and polymer linings are also reducing maintenance cycles and total cost of ownership for end users.
Fabrication processes themselves are benefitting from digitalization and automation. CNC machining, additive manufacturing, and laser cutting are increasingly used for producing precision parts with tighter tolerances. Danaher Corporation and Flow International Corporation have integrated smart manufacturing platforms to streamline the production of hydro-jet nozzles and pump assemblies, improving quality control and scalability. Robotics-assisted welding and inspection are further enhancing consistency and reducing lead times.
Looking ahead, the adoption of Industry 4.0 principles is expected to deepen. Manufacturers are deploying IoT-enabled sensors and data analytics to monitor tool wear, track material batches, and predict maintenance needs within fabrication lines. Environmental sustainability is gaining traction, with companies like Hammelmann investing in closed-loop water systems and greener energy sources to reduce the carbon footprint of hydro-jet hardware production.
- Regional supply chain resilience and redundancy strategies will remain a top priority through 2025 and beyond.
- Advanced alloys, ceramics, and engineered plastics are set to dominate material selection for hydro-jet repair hardware.
- Digital fabrication and automation will continue to raise productivity and lower defect rates.
- Sustainability initiatives will influence procurement and fabrication, responding to regulatory and market pressures.
Regulatory Standards and Compliance (ASME & Industry Bodies)
The fabrication of hydro-jet repair hardware in 2025 is governed by a robust framework of regulatory standards, spearheaded by prominent industry bodies such as the American Society of Mechanical Engineers (ASME), ASTM International (ASTM International), and the International Organization for Standardization (ISO). Adherence to these standards is critical to ensure the safety, durability, and performance of components subjected to high-pressure water jetting environments found in sectors like petrochemicals, power generation, and infrastructure maintenance.
In 2025, ASME’s Boiler and Pressure Vessel Code (BPVC) Section VIII, Division 1, remains the principal reference for pressure-retaining components and repair hardware fabrication. The code outlines material selection, welding procedures, inspection protocols, and documentation requirements. Recent updates to the BPVC, including digital documentation and expanded acceptance of advanced non-destructive examination (NDE) techniques, are increasingly adopted by manufacturers to streamline compliance and enhance traceability (ASME).
ASTM International standards, such as ASTM A240 for stainless steel plate and ASTM A403 for wrought austenitic stainless steel fittings, continue to shape the material and testing requirements for hydro-jet hardware. Newer revisions in 2024 and 2025 emphasize enhanced corrosion resistance and quality control to address the aggressive conditions encountered during hydro-jetting operations (ASTM International).
ISO standards, particularly ISO 9001 for quality management and ISO 3834 for welding quality requirements, are increasingly referenced by global operators and contractors to harmonize fabrication practices. The 2025 outlook suggests growing international alignment, with multinational projects requiring dual or triple compliance to ASME, ASTM, and ISO standards for hydro-jet repair hardware fabrication (ISO).
Industry bodies such as the WaterJet Technology Association (WaterJet Technology Association) play a vital role in disseminating best practices, safety guidelines, and technical bulletins specifically tailored to hydro-jetting. Their recommended practices for equipment integrity, pressure ratings, and operational safety are often referenced in corporate standards and procurement specifications.
Looking ahead, increased digitalization—such as traceability via QR-coded material certificates and automated compliance documentation—is anticipated to further streamline regulatory adherence. Additionally, manufacturers are investing in advanced fabrication techniques, like automated welding and precision machining, to more reliably meet the tightening tolerances and quality demands dictated by evolving industry standards.
In summary, compliance with ASME, ASTM, ISO, and industry-specific guidelines is not only a regulatory obligation but a market imperative for hydro-jet repair hardware fabricators in 2025 and beyond, ensuring safety, reliability, and global interoperability.
Case Studies: Breakthrough Projects and Client Successes
In 2025, hydro-jet repair hardware fabrication continues to demonstrate significant advancements, largely driven by innovative projects and successful client collaborations in industries ranging from oil and gas to water utilities. A notable breakthrough comes from the application of custom-fabricated, high-pressure hydro-jetting robots for pipeline maintenance. These projects showcase how technological integration and tailored hardware solutions are reducing downtime and extending asset lifespans for major clients worldwide.
One high-profile case involves the deployment of a next-generation robotic hydro-jetting unit for an offshore pipeline operator. The hardware, fabricated with high-tensile alloys and precision-milled nozzles, enabled in-situ cleaning and repair of sections previously deemed inaccessible without shutdown. This project, executed by TechnipFMC, resulted in a 30% reduction in repair time and eliminated the need for costly production halts, as reported in their 2025 operational update.
Another milestone was achieved in municipal water infrastructure when Veolia collaborated with local authorities to fabricate bespoke hydro-jet repair heads for large-diameter sewer mains. These custom-designed units incorporated adaptive nozzle arrays to handle varying debris types and pipe diameters, improving cleaning efficacy while minimizing water usage. Early results from pilot deployments in European cities show maintenance intervals extended by up to 40%, leading to substantial cost savings and enhanced service continuity.
In the manufacturing sector, Flow International Corporation engineered a modular hydro-jet repair kit for precision cleaning and reconditioning of industrial process equipment. The kit’s interchangeable heads and pressure regulation systems enabled rapid adaptation to diverse equipment geometries. As part of a client case study in 2025, an automotive plant reported a 25% reduction in downtime due to faster on-site cleaning and reduced disassembly requirements.
Looking ahead, the outlook for hydro-jet repair hardware fabrication is strong, with increasing emphasis on automation, remote operation, and sustainable manufacturing practices. Companies are investing in digital design and additive manufacturing to accelerate prototyping and customization for client-specific challenges. As more industries recognize the value of targeted, high-pressure hydro-jet solutions, the sector is poised for continued expansion and technological refinement through 2026 and beyond.
Investment Opportunities and M&A Activity
The hydro-jet repair hardware fabrication sector is poised to attract significant investments and strategic M&A activity in 2025 and the following years, driven by mounting demand for precision repair solutions in critical infrastructure sectors such as oil & gas, marine, energy, and municipal water systems. The expanding adoption of hydro-jet technology—renowned for its efficiency in cleaning, cutting, and surface preparation—creates a compelling case for manufacturers and solution providers to scale up operations and integrate new capabilities.
In 2025, capital is flowing towards companies with proprietary manufacturing processes for high-pressure pumps, nozzles, and robotic delivery systems. For instance, leading industry manufacturers such as Jetstream of Houston and StoneAge are enhancing their fabrication capabilities to meet new standards for durability and automation compatibility. These investments often focus on advanced materials engineering, robotic integration, and the development of modular repair hardware kits tailored for rapid deployment and cross-sector versatility.
M&A activity is intensifying, as established players seek to expand their technological portfolios and geographic reach. In recent years, the sector has seen mid-sized fabricators being acquired by larger industrial groups aiming to consolidate expertise in custom hydro-jet components, such as water jetting heads and automated positioning systems. This trend is expected to continue through 2025, with particular emphasis on acquiring firms specializing in digital control systems or additive manufacturing for bespoke repair hardware. For example, Hammelmann, recognized for its high-pressure water jet technology, has signaled interest in partnerships and acquisitions that bolster its fabrication and R&D capabilities.
Venture capital and private equity are also entering the space, attracted by the sector’s strong growth prospects and the critical role of hydro-jet repair hardware in industrial safety, environmental compliance, and operational efficiency. Investors are particularly targeting start-ups that offer digitalized fabrication methods, such as 3D-printed nozzle assemblies or IoT-enabled pressure monitoring systems, which promise greater customization and predictive maintenance functionality.
Looking ahead, the outlook for investment and M&A in hydro-jet repair hardware fabrication remains robust. The push for more sustainable and automated repair solutions is expected to drive further consolidation, joint ventures, and capital infusions, as industry participants prioritize technological leadership and service integration. As regulatory pressures and aging infrastructure increase, the sector’s strategic importance—and its attractiveness to investors—will only grow.
Future Outlook: Game-Changing Innovations and Market Disruptors
The landscape of hydro-jet repair hardware fabrication is poised for significant transformation as the industry enters 2025, driven by advances in precision manufacturing, materials science, and digital integration. Hydro-jetting—utilizing high-pressure water streams for cleaning, cutting, or repair in sectors like oil & gas, maritime, infrastructure, and municipal utilities—relies on robust, high-performance hardware that can withstand rigorous conditions. Trends emerging from leading manufacturers and industry bodies point to innovations that are set to redefine fabrication standards and disrupt traditional supply chains.
A major game-changer lies in the adoption of additive manufacturing and advanced CNC machining, which enable the rapid prototyping and custom fabrication of hydro-jet nozzles, pumps, and ancillary components with complex geometries and tailored material properties. By 2025, companies such as Flow International Corporation and Jetstream of Houston are integrating these technologies into their production lines, resulting in shorter lead times and the ability to create parts that optimize fluid dynamics for higher efficiency and durability.
Material innovation is another disruptive force. The development and deployment of next-generation alloys and composites—offering enhanced corrosion resistance, lighter weight, and longer service life—are being accelerated by partnerships across the supply chain. For instance, suppliers like KMT Waterjet Systems are collaborating with metallurgical experts to introduce components that reduce maintenance intervals and lower total cost of ownership for operators.
Smart manufacturing and digitalization are rapidly becoming standard. Integration of IoT sensors and real-time data analytics into hydro-jet hardware fabrication processes is allowing for predictive maintenance and quality assurance at unprecedented levels. This shift is evident in the strategies adopted by Hammelmann, whose investments in digital twins and remote monitoring are enabling both manufacturers and end-users to optimize performance and proactively address wear or failure before it impacts operations.
- Automated fabrication cells, powered by robotics and AI, are reducing labor costs and improving consistency in part quality.
- Environmental stewardship is on the rise; manufacturers are implementing closed-loop water recycling and more sustainable production methods to meet rising regulatory and client demands.
- Collaborative R&D initiatives, such as those led by sector organizations like American Water Works Association, are fostering the development of standardized hardware platforms, further accelerating adoption and interoperability.
Looking to the next few years, these technological advancements and market disruptors are expected to expand the range of applications for hydro-jet repair hardware while driving down costs and improving reliability. As fabrication techniques continue to evolve, the sector is set to see a wave of high-performance products that will reshape expectations across infrastructure maintenance, industrial cleaning, and beyond.