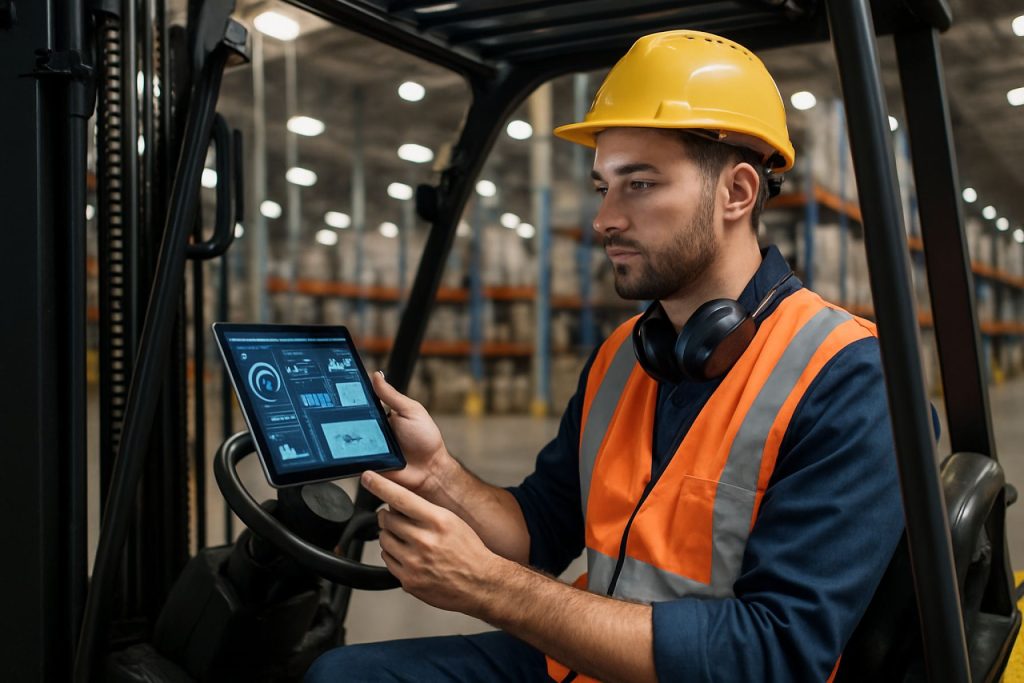
Unlocking the Future of Forklift Telematics Systems Integration in 2025: How Smart Connectivity and Predictive Analytics Are Transforming Material Handling. Discover the Key Trends, Market Growth, and Technology Innovations Shaping the Next Five Years.
- Executive Summary: 2025 Market Landscape and Key Drivers
- Market Size, Growth Forecasts, and CAGR (2025–2030)
- Core Technologies: IoT, Cloud, and Edge Computing in Forklift Telematics
- Integration Challenges: Legacy Systems, Interoperability, and Cybersecurity
- Leading Vendors and Industry Initiatives (e.g., Toyota, Hyster-Yale, Crown Equipment)
- Case Studies: Real-World Deployments and Measured ROI
- Regulatory Standards and Industry Guidelines (e.g., OSHA, ISO)
- Emerging Trends: AI, Predictive Maintenance, and Fleet Optimization
- Regional Analysis: North America, Europe, Asia-Pacific, and Rest of World
- Future Outlook: Strategic Recommendations and Innovation Roadmap
- Sources & References
Executive Summary: 2025 Market Landscape and Key Drivers
The integration of telematics systems into forklift fleets is rapidly transforming the material handling landscape in 2025, driven by the convergence of digitalization, safety mandates, and operational efficiency imperatives. Telematics—encompassing real-time data collection, wireless connectivity, and analytics—enables fleet operators to monitor forklift usage, operator behavior, maintenance needs, and asset location with unprecedented precision. This evolution is being propelled by both regulatory pressures and the pursuit of cost savings, as companies seek to minimize downtime, reduce accidents, and optimize asset utilization.
Key industry players such as Toyota Industries Corporation, Crown Equipment Corporation, and Hyster-Yale Materials Handling have expanded their telematics offerings, integrating advanced IoT modules and cloud-based platforms into their forklift product lines. These systems provide actionable insights through dashboards and mobile applications, supporting predictive maintenance, automated compliance reporting, and real-time safety alerts. For example, Toyota Industries Corporation has continued to enhance its T-Matics platform, while Crown Equipment Corporation offers the InfoLink system, both of which are designed to seamlessly integrate with warehouse management systems (WMS) and enterprise resource planning (ERP) solutions.
The 2025 market landscape is characterized by several key drivers:
- Regulatory Compliance: Stricter safety and emissions regulations in North America, Europe, and parts of Asia are compelling fleet operators to adopt telematics for automated record-keeping and incident reporting.
- Operational Efficiency: Real-time data analytics enable proactive maintenance scheduling, reducing unplanned downtime and extending equipment life cycles.
- Labor Optimization: Telematics systems help monitor operator performance, support training initiatives, and ensure adherence to safety protocols, addressing skilled labor shortages and reducing accident rates.
- Integration with Digital Supply Chains: Seamless connectivity with WMS and ERP platforms is becoming standard, allowing for holistic visibility and control across logistics operations.
Looking ahead, the next few years will see further standardization of telematics protocols, increased adoption of AI-driven analytics, and deeper integration with autonomous material handling solutions. Major manufacturers and technology providers are expected to collaborate on open platforms and interoperability standards, accelerating the digital transformation of warehouse and logistics environments. As a result, forklift telematics systems integration will remain a central pillar of smart, data-driven supply chain strategies through 2025 and beyond.
Market Size, Growth Forecasts, and CAGR (2025–2030)
The global market for forklift telematics systems integration is poised for robust growth from 2025 through 2030, driven by accelerating digital transformation in logistics, warehousing, and manufacturing sectors. As companies seek to optimize fleet management, enhance safety, and comply with increasingly stringent regulatory requirements, the adoption of telematics solutions is becoming a strategic imperative. Major forklift manufacturers and telematics providers are investing heavily in R&D and partnerships to deliver integrated, scalable solutions that address these evolving needs.
Key industry players such as Toyota Industries Corporation, KION Group, and Crown Equipment Corporation are embedding advanced telematics hardware and software into their forklift offerings. These systems enable real-time monitoring of vehicle health, operator behavior, location tracking, and predictive maintenance, which collectively drive operational efficiency and cost savings. For example, Toyota Industries Corporation has expanded its I_Site telematics platform, while KION Group integrates its fleet management solutions across its Linde and STILL brands.
The market outlook for 2025–2030 anticipates a compound annual growth rate (CAGR) in the high single digits, with some industry estimates suggesting a CAGR of 8–10%. This growth is underpinned by several factors:
- Increasing automation and digitalization in supply chain operations.
- Rising demand for data-driven decision-making and predictive analytics in fleet management.
- Stricter safety and environmental regulations, particularly in North America, Europe, and parts of Asia-Pacific.
- Expansion of e-commerce and third-party logistics (3PL) providers, which require scalable and integrated telematics solutions.
In addition to OEMs, specialized telematics providers such as Jungheinrich AG and Hyster-Yale Materials Handling, Inc. are collaborating with software developers and IoT platform companies to offer retrofit solutions and cloud-based analytics. These partnerships are expected to further accelerate market penetration, especially among small and medium-sized enterprises seeking cost-effective integration options.
Looking ahead, the forklift telematics systems integration market is expected to see continued innovation in areas such as AI-driven analytics, remote diagnostics, and seamless interoperability with warehouse management systems (WMS) and enterprise resource planning (ERP) platforms. As digital infrastructure matures and the benefits of telematics become more widely recognized, the sector is set for sustained expansion through 2030.
Core Technologies: IoT, Cloud, and Edge Computing in Forklift Telematics
Forklift telematics systems integration is rapidly evolving in 2025, driven by the convergence of Internet of Things (IoT), cloud computing, and edge computing technologies. These core technologies are enabling seamless data collection, real-time analytics, and actionable insights for fleet operators, warehouse managers, and logistics providers. The integration of telematics systems with broader enterprise platforms is a key trend, as companies seek to optimize operations, enhance safety, and reduce costs.
IoT-enabled sensors and devices are now standard on new forklift models, capturing data on vehicle location, usage patterns, operator behavior, and equipment health. Leading manufacturers such as Toyota Industries Corporation and Crown Equipment Corporation have developed proprietary telematics platforms that integrate with their fleets, providing real-time monitoring and predictive maintenance capabilities. These systems are increasingly interoperable, allowing integration with third-party fleet management software and warehouse management systems (WMS).
Cloud computing plays a central role in telematics integration by enabling centralized data storage, advanced analytics, and remote access to fleet information. Companies like Hyster-Yale Materials Handling and Jungheinrich AG offer cloud-based telematics solutions that aggregate data from multiple sites, supporting enterprise-wide visibility and benchmarking. The cloud also facilitates over-the-air (OTA) software updates, ensuring that telematics systems remain current and secure.
Edge computing is gaining traction as a complementary technology, particularly for latency-sensitive applications such as collision avoidance, real-time safety alerts, and local decision-making. By processing data at or near the forklift, edge devices reduce the need for constant cloud connectivity and enable faster response times. This is especially valuable in environments with limited network infrastructure or strict data privacy requirements.
Looking ahead, the next few years are expected to see deeper integration between forklift telematics and other industrial IoT systems, such as automated guided vehicles (AGVs), robotics, and smart warehouse infrastructure. Open APIs and standardized data protocols are being adopted to facilitate interoperability across diverse equipment and software platforms. Industry leaders are also exploring the use of artificial intelligence and machine learning to derive predictive insights from telematics data, further enhancing operational efficiency and safety.
- Widespread adoption of IoT sensors and cloud-based telematics platforms by major forklift manufacturers.
- Growing use of edge computing for real-time safety and operational applications.
- Movement toward open standards and API-driven integration for cross-platform compatibility.
- Increasing focus on predictive analytics and AI-driven insights for fleet optimization.
As forklift telematics systems become more integrated and intelligent, companies across the supply chain are poised to benefit from improved asset utilization, reduced downtime, and enhanced workplace safety.
Integration Challenges: Legacy Systems, Interoperability, and Cybersecurity
The integration of forklift telematics systems is accelerating in 2025, driven by the need for real-time data, safety compliance, and operational efficiency. However, this integration faces significant challenges, particularly regarding legacy systems, interoperability, and cybersecurity.
Many warehouses and logistics operations still rely on older forklift fleets equipped with minimal or proprietary onboard electronics. Integrating modern telematics—such as fleet management, operator monitoring, and predictive maintenance—into these legacy systems is complex. Retrofitting older forklifts with telematics hardware often requires custom solutions or adapters, and compatibility issues can arise when connecting to existing warehouse management systems (WMS) or enterprise resource planning (ERP) platforms. Leading manufacturers like Toyota Industries Corporation and KION Group have responded by offering modular telematics kits and open APIs, but seamless integration across mixed-brand fleets remains a technical hurdle.
Interoperability is another major concern. The forklift telematics ecosystem is fragmented, with different vendors using proprietary data formats and communication protocols. This fragmentation complicates data aggregation and analysis, especially for operators managing multi-brand fleets or integrating telematics data with broader supply chain systems. Industry bodies such as the MHI and Industrial Truck Association are advocating for standardization, but as of 2025, universal standards for telematics data exchange are still evolving. Some progress is being made through collaborative initiatives and partnerships between OEMs and technology providers, aiming to develop interoperable platforms and middleware solutions.
Cybersecurity has emerged as a critical challenge as forklift telematics systems become more connected. The increased use of cloud-based analytics, remote diagnostics, and wireless communications exposes fleets to potential cyber threats, including unauthorized access, data breaches, and operational disruptions. Manufacturers such as Crown Equipment Corporation and Hyster-Yale Materials Handling are investing in secure communication protocols, encrypted data storage, and regular software updates to mitigate these risks. Additionally, regulatory scrutiny is increasing, with new guidelines expected from industry bodies and government agencies to ensure data privacy and system integrity.
Looking ahead, the outlook for forklift telematics integration is cautiously optimistic. Continued investment in open standards, cybersecurity frameworks, and retrofit-friendly solutions is expected to reduce integration barriers. However, the pace of progress will depend on industry collaboration and the willingness of operators to modernize legacy assets. As digital transformation accelerates across logistics and warehousing, overcoming these integration challenges will be essential for realizing the full benefits of telematics-driven fleet management.
Leading Vendors and Industry Initiatives (e.g., Toyota, Hyster-Yale, Crown Equipment)
The integration of telematics systems into forklift fleets has become a central focus for leading material handling equipment manufacturers, as the industry moves toward greater connectivity, safety, and operational efficiency. In 2025, major vendors such as Toyota Material Handling, Hyster-Yale Materials Handling, and Crown Equipment Corporation are at the forefront of this transformation, each advancing proprietary telematics platforms and forging strategic partnerships to expand their digital offerings.
Toyota Material Handling, a global leader in forklift manufacturing, continues to enhance its Toyota T-Matics system, which provides real-time data on fleet utilization, operator performance, and maintenance needs. The company’s telematics solutions are designed for seamless integration with warehouse management systems (WMS) and enterprise resource planning (ERP) platforms, supporting data-driven decision-making and predictive maintenance. Toyota’s ongoing investments in IoT and cloud-based analytics reflect its commitment to supporting customers’ digital transformation initiatives and sustainability goals.
Hyster-Yale Materials Handling, through its Hyster Tracker and Yale Vision telematics suites, is similarly focused on delivering actionable insights to fleet managers. These systems offer features such as access control, impact detection, and automated compliance reporting. In 2025, Hyster-Yale is emphasizing open architecture and API compatibility, enabling customers to integrate telematics data with third-party logistics and safety platforms. This approach is intended to foster interoperability and future-proof investments as digital ecosystems evolve.
Crown Equipment Corporation’s InfoLink system remains a benchmark for forklift telematics, providing cloud-based dashboards that monitor equipment status, operator behavior, and energy consumption. Crown’s telematics initiatives in 2025 are increasingly centered on advanced analytics and machine learning, with the goal of optimizing fleet right-sizing and reducing total cost of ownership. The company is also expanding its telematics integration capabilities to support mixed-brand fleets, addressing a key challenge for large-scale logistics operators.
Across the industry, these leading vendors are collaborating with technology partners and standards organizations to promote interoperability and data security. The outlook for the next few years points to further convergence between telematics, automation, and artificial intelligence, with forklift OEMs expected to introduce more sophisticated, plug-and-play solutions. As regulatory and customer demands for transparency and sustainability intensify, telematics integration will remain a strategic priority for both manufacturers and end-users.
Case Studies: Real-World Deployments and Measured ROI
The integration of forklift telematics systems has moved from pilot projects to large-scale, measurable deployments across global supply chains, with 2025 marking a period of accelerated adoption and clearer ROI metrics. Leading manufacturers and logistics operators are leveraging telematics to optimize fleet utilization, enhance safety, and reduce operational costs, with several high-profile case studies illustrating tangible benefits.
One notable example is the deployment of the Toyota Industries Corporation I_Site telematics platform across multi-site warehouse operations in Europe and North America. By integrating real-time data on forklift usage, operator behavior, and maintenance needs, Toyota’s clients have reported up to 30% reductions in unplanned downtime and significant improvements in operator safety compliance. The system’s ability to generate actionable insights has enabled fleet right-sizing, with some users reducing their forklift fleets by 10–15% without sacrificing productivity.
Similarly, Crown Equipment Corporation has documented the impact of its InfoLink telematics solution in large distribution centers. In a 2024–2025 deployment for a major retail client, Crown’s system provided granular data on equipment utilization, leading to a 20% increase in asset productivity and a measurable decrease in energy consumption. The client also leveraged telematics-driven maintenance scheduling, resulting in a 25% reduction in maintenance costs and fewer critical failures.
Another significant case is the integration of Hyster-Yale Materials Handling’s Hyster Tracker and Yale Vision systems in automotive manufacturing plants. These telematics platforms have enabled real-time monitoring of operator access, impact events, and battery health. Automotive clients have reported improved regulatory compliance and a 40% reduction in damage-related costs, as well as enhanced traceability for incident investigations.
Looking ahead, the outlook for forklift telematics integration is robust. Industry leaders such as Jungheinrich AG and KION Group are expanding their telematics offerings with advanced analytics, AI-driven predictive maintenance, and seamless integration with warehouse management systems (WMS) and enterprise resource planning (ERP) platforms. These developments are expected to further boost ROI by enabling proactive decision-making and tighter alignment between material handling operations and broader supply chain objectives.
In summary, real-world deployments in 2025 demonstrate that forklift telematics systems integration delivers measurable ROI through cost savings, safety improvements, and operational efficiencies. As technology matures and integration deepens, the next few years are poised to see even greater value realization across diverse industrial sectors.
Regulatory Standards and Industry Guidelines (e.g., OSHA, ISO)
The integration of telematics systems into forklift fleets is increasingly shaped by evolving regulatory standards and industry guidelines, particularly as digitalization and safety expectations rise in 2025 and beyond. Regulatory bodies such as the Occupational Safety and Health Administration (OSHA) in the United States and the International Organization for Standardization (ISO) globally are central to this landscape, setting frameworks that influence both the adoption and technical requirements of telematics solutions.
OSHA’s regulations, while not yet mandating telematics, emphasize operator safety, equipment maintenance, and incident reporting—areas where telematics integration provides significant compliance advantages. Telematics systems can automate the collection of data on operator behavior, maintenance schedules, and safety incidents, supporting adherence to OSHA’s Powered Industrial Trucks Standard (29 CFR 1910.178). As OSHA continues to review and update its standards, there is industry anticipation that digital recordkeeping and real-time monitoring could become more explicitly referenced or required in future revisions, especially as telematics adoption becomes widespread.
On the international front, ISO standards such as ISO 3691-1 (Industrial trucks – Safety requirements) and ISO 13849 (Safety of machinery – Safety-related parts of control systems) are increasingly relevant. These standards are being updated to reflect the integration of digital and connected technologies, including telematics. Manufacturers and integrators are aligning their systems to ensure compatibility with these evolving requirements, which address not only safety but also cybersecurity and data integrity—critical as telematics data becomes central to fleet management and regulatory compliance.
Industry organizations, including the Industrial Truck Association (Industrial Truck Association), are also issuing best practice guidelines for telematics integration. These guidelines often address interoperability, data privacy, and the secure handling of operational data, reflecting growing concerns about data breaches and system vulnerabilities as more forklifts become connected.
Major forklift manufacturers such as Toyota Industries Corporation, KION Group, and Crown Equipment Corporation are actively developing telematics-ready equipment and collaborating with standards bodies to ensure their solutions meet or exceed regulatory expectations. These companies are also participating in pilot programs and industry consortia to shape future standards, particularly around data sharing and system interoperability.
Looking ahead, the next few years are expected to bring more explicit regulatory references to telematics in forklift safety and operational standards. This will likely drive further standardization, increased adoption, and a focus on secure, interoperable systems that support both compliance and operational efficiency.
Emerging Trends: AI, Predictive Maintenance, and Fleet Optimization
The integration of telematics systems in forklift fleets is rapidly evolving, driven by advances in artificial intelligence (AI), predictive maintenance, and fleet optimization technologies. As of 2025, leading forklift manufacturers and technology providers are embedding sophisticated telematics modules into their vehicles, enabling real-time data collection, remote diagnostics, and advanced analytics. This integration is transforming traditional fleet management by providing actionable insights that enhance safety, efficiency, and cost-effectiveness.
A key trend is the deployment of AI-powered analytics platforms that process vast streams of telematics data from forklifts. These platforms can identify patterns in operator behavior, equipment usage, and environmental conditions, allowing for proactive interventions. For example, AI algorithms can detect unsafe driving practices or predict when a component is likely to fail, triggering maintenance before a breakdown occurs. Companies such as Toyota Industries Corporation and Crown Equipment Corporation are at the forefront, offering integrated telematics solutions that leverage machine learning to optimize fleet performance and reduce unplanned downtime.
Predictive maintenance is another area experiencing significant growth. By continuously monitoring forklift health indicators—such as battery status, hydraulic pressure, and engine temperature—telematics systems can forecast maintenance needs with high accuracy. This minimizes costly repairs and extends equipment lifespan. Hyster-Yale Materials Handling and Jungheinrich AG have introduced telematics-enabled maintenance programs that automatically schedule service based on real-time data, reducing manual intervention and improving operational reliability.
Fleet optimization is being revolutionized through the integration of telematics with warehouse management systems (WMS) and enterprise resource planning (ERP) platforms. This connectivity enables centralized oversight of mixed-brand fleets, real-time asset tracking, and dynamic task allocation. As a result, logistics operators can maximize equipment utilization, minimize idle time, and ensure compliance with safety protocols. Linde Material Handling and Mitsubishi Logisnext are notable for their open telematics architectures, which facilitate seamless integration with third-party software and IoT ecosystems.
Looking ahead, the next few years are expected to see further convergence of telematics, AI, and automation. The adoption of 5G connectivity and edge computing will enable even faster data processing and more granular control over forklift operations. Industry leaders are investing in scalable, cloud-based telematics platforms that support remote updates, cybersecurity, and interoperability across global fleets. As these technologies mature, forklift telematics systems integration will become a cornerstone of smart, data-driven logistics operations worldwide.
Regional Analysis: North America, Europe, Asia-Pacific, and Rest of World
The integration of telematics systems into forklift fleets is accelerating globally, with distinct regional trends shaping adoption and innovation. In North America, the market is characterized by rapid digitalization of logistics and a strong focus on safety and regulatory compliance. Major manufacturers such as Crown Equipment Corporation and Hyster-Yale Materials Handling are embedding advanced telematics into their fleets, enabling real-time monitoring of equipment health, operator behavior, and location tracking. The U.S. Occupational Safety and Health Administration’s (OSHA) emphasis on workplace safety is driving demand for telematics solutions that provide actionable data for incident prevention and compliance documentation.
In Europe, sustainability and efficiency are key drivers. The region’s stringent environmental regulations and push for electrification are prompting manufacturers like Jungheinrich AG and Linde Material Handling to integrate telematics with energy management systems. European fleets are leveraging telematics for predictive maintenance, route optimization, and battery management, aligning with the EU’s Green Deal objectives. The adoption of cloud-based platforms and interoperability standards is also more advanced, facilitating cross-border fleet management and data sharing.
The Asia-Pacific region is witnessing robust growth, fueled by rapid industrialization and e-commerce expansion, particularly in China, Japan, and Southeast Asia. Local and global players such as Toyota Industries Corporation and Mitsubishi Logisnext are investing in telematics to support large-scale warehouse automation and supply chain visibility. In China, government initiatives to modernize logistics infrastructure are accelerating the deployment of telematics-enabled forklifts, with a focus on cost efficiency and scalability. The region is also seeing increased collaboration between OEMs and technology providers to develop localized telematics solutions tailored to diverse regulatory and operational environments.
In the Rest of World (RoW), including Latin America, the Middle East, and Africa, telematics integration is at an earlier stage but gaining momentum. Adoption is driven by multinational logistics operators and large industrial projects seeking to improve asset utilization and reduce operational risks. Companies such as KION Group AG are expanding their telematics offerings in these markets, often through partnerships with local distributors and service providers. Challenges such as connectivity infrastructure and cost sensitivity persist, but the outlook is positive as digital transformation initiatives and regulatory frameworks evolve.
Looking ahead to 2025 and beyond, regional disparities in forklift telematics integration are expected to narrow as technology costs decline and global standards mature. The convergence of telematics with IoT, AI, and cloud analytics will further enhance fleet intelligence, safety, and sustainability across all regions.
Future Outlook: Strategic Recommendations and Innovation Roadmap
The integration of telematics systems into forklift fleets is rapidly evolving, with 2025 marking a pivotal year for both technological advancement and strategic adoption. As warehouse automation and digital transformation accelerate, telematics is becoming central to operational efficiency, safety, and data-driven decision-making. The future outlook for forklift telematics systems integration is shaped by several key trends and strategic imperatives.
First, interoperability and open-platform architectures are emerging as critical requirements. Leading manufacturers such as Toyota Industries Corporation and KION Group are increasingly offering telematics solutions that can integrate with a wide range of warehouse management systems (WMS), enterprise resource planning (ERP) platforms, and even third-party telematics devices. This shift is driven by customer demand for unified data streams and seamless analytics across mixed-brand fleets, enabling more holistic fleet optimization and predictive maintenance strategies.
Second, the proliferation of IoT sensors and edge computing is enabling real-time data collection and analysis at the forklift level. Companies like Crown Equipment Corporation and Hyster-Yale Materials Handling are embedding advanced telematics modules that monitor operator behavior, equipment health, and environmental conditions. This granular data is increasingly being leveraged for AI-driven insights, such as automated safety alerts, dynamic route optimization, and energy management, supporting both sustainability and productivity goals.
Third, cybersecurity and data privacy are becoming top priorities as telematics systems handle sensitive operational data. Industry leaders are investing in robust encryption, secure cloud infrastructure, and compliance with international data standards to address growing concerns around data breaches and regulatory requirements.
Looking ahead, strategic recommendations for organizations include prioritizing telematics solutions that offer modularity and scalability, ensuring future-proof integration as technology standards evolve. Collaboration with OEMs and technology partners is essential to co-develop custom analytics and automation features tailored to specific operational needs. Additionally, investing in workforce training and change management will be crucial to maximize the value of telematics data and foster a culture of continuous improvement.
Innovation roadmaps for 2025 and beyond point toward deeper integration with autonomous material handling systems, enhanced AI-driven analytics, and the convergence of telematics with broader supply chain visibility platforms. As forklift telematics systems become more intelligent and interconnected, they will play a foundational role in the next generation of smart, resilient, and sustainable warehouse operations.
Sources & References
- Toyota Industries Corporation
- Crown Equipment Corporation
- Hyster-Yale Materials Handling
- KION Group
- MHI
- Toyota Material Handling
- ISO
- Industrial Truck Association
- Hyster-Yale Materials Handling
- Linde Material Handling