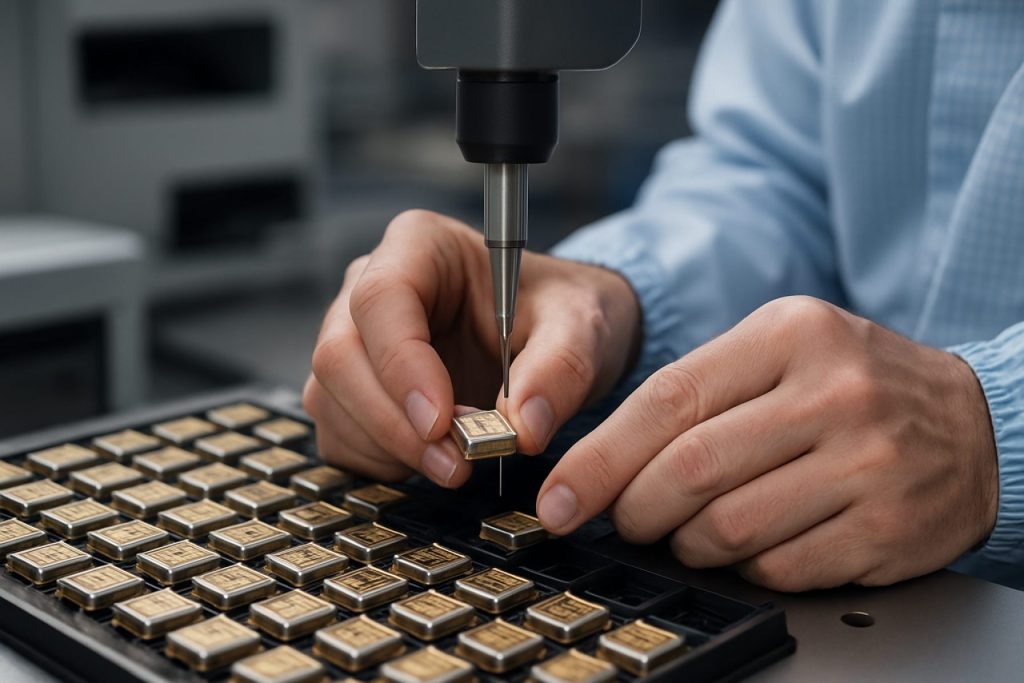
Ferroelectric RF Filter Manufacturing in 2025: Unleashing Next-Gen Wireless Performance and Market Expansion. Explore How Advanced Materials and 5G/6G Demands Are Shaping the Industry’s Future.
- Executive Summary: Key Trends and 2025 Outlook
- Market Size, Growth Rate, and 2025–2030 Forecasts
- Ferroelectric Materials: Innovations and Supply Chain Dynamics
- RF Filter Technology Evolution: From 4G to 6G
- Competitive Landscape: Leading Manufacturers and New Entrants
- Application Sectors: Mobile, IoT, Automotive, and Defense
- Manufacturing Processes and Cost Optimization Strategies
- Regulatory Standards and Industry Collaboration (e.g., ieee.org)
- Challenges: Scalability, Reliability, and Integration
- Future Outlook: Disruptive Opportunities and Strategic Recommendations
- Sources & References
Executive Summary: Key Trends and 2025 Outlook
Ferroelectric RF filter manufacturing is undergoing significant transformation as the demand for high-performance, tunable, and miniaturized radio frequency (RF) components accelerates in the context of 5G, Wi-Fi 6/7, and emerging 6G wireless technologies. In 2025, the sector is characterized by rapid advancements in material science, process integration, and commercial deployment, with leading manufacturers and technology developers intensifying efforts to scale production and improve device reliability.
A key trend is the increasing adoption of barium strontium titanate (BST) and related ferroelectric thin films, which enable voltage-tunable RF filters with superior linearity and low insertion loss. Companies such as Murata Manufacturing Co., Ltd. and TDK Corporation are at the forefront, leveraging their expertise in advanced ceramics and thin-film processing to develop next-generation tunable filters for smartphones, base stations, and IoT devices. These firms are investing in proprietary deposition techniques and wafer-level integration to meet the stringent performance and miniaturization requirements of modern wireless systems.
Another notable development is the collaboration between device manufacturers and foundries to accelerate the commercialization of ferroelectric RF filters. Qorvo, Inc. has announced partnerships with leading foundries to integrate ferroelectric materials into their RF front-end modules, targeting both sub-6 GHz and mmWave applications. This approach is expected to streamline the supply chain and enable higher-volume production, addressing the growing needs of telecom infrastructure and consumer electronics markets.
In parallel, the industry is witnessing increased investment in process automation and quality control, with manufacturers deploying advanced metrology and in-line testing to ensure device consistency and yield. Skyworks Solutions, Inc. and KYOCERA AVX Components Corporation are expanding their manufacturing capabilities, focusing on scalable processes that support both discrete and integrated RF filter solutions.
Looking ahead to the next few years, the outlook for ferroelectric RF filter manufacturing remains robust. The proliferation of connected devices, spectrum crowding, and the push for reconfigurable RF architectures are expected to drive further innovation and capacity expansion. Industry leaders are likely to deepen collaborations with semiconductor foundries and equipment suppliers, while ongoing R&D in ferroelectric materials promises continued improvements in filter performance, reliability, and cost-effectiveness.
Market Size, Growth Rate, and 2025–2030 Forecasts
The ferroelectric RF (radio frequency) filter manufacturing sector is positioned for significant growth from 2025 through 2030, driven by the accelerating adoption of 5G and the anticipated rollout of 6G wireless technologies. Ferroelectric materials, such as barium strontium titanate (BST), enable tunable RF filters with high linearity and low insertion loss, making them increasingly attractive for next-generation wireless infrastructure and mobile devices.
As of 2025, the market for ferroelectric RF filters is still emerging but is gaining momentum due to the need for more agile and compact filtering solutions in crowded spectrum environments. Key industry players include Murata Manufacturing Co., Ltd., which has invested in tunable RF components leveraging ferroelectric materials, and Qorvo, Inc., which is actively developing tunable filter solutions for 5G and beyond. Samsung Electronics and LG Electronics are also exploring ferroelectric-based RF front-end modules for integration into their mobile devices and network equipment.
The global demand for RF filters is projected to rise sharply, with ferroelectric variants expected to capture a growing share due to their reconfigurability and miniaturization advantages. Industry estimates suggest that the overall RF filter market could surpass $20 billion by 2030, with ferroelectric filters representing a rapidly expanding segment within this total. The growth rate for ferroelectric RF filter manufacturing is anticipated to exceed 15% CAGR between 2025 and 2030, outpacing traditional SAW (surface acoustic wave) and BAW (bulk acoustic wave) filter technologies as network requirements become more complex and dynamic.
Manufacturing advancements are also expected to drive down costs and improve yields. Companies such as TDK Corporation and Kyocera Corporation are investing in process optimization and material innovation to scale up production and meet the anticipated surge in demand. Additionally, collaborations between device manufacturers and network operators are fostering the development of application-specific ferroelectric RF filters tailored for automotive, IoT, and industrial wireless applications.
Looking ahead, the outlook for ferroelectric RF filter manufacturing is robust, with the sector poised to benefit from ongoing wireless infrastructure upgrades, the proliferation of connected devices, and the push for more energy-efficient and flexible RF front-end solutions. As the technology matures and manufacturing ecosystems expand, ferroelectric RF filters are expected to become a mainstream component in the global wireless landscape by the end of the decade.
Ferroelectric Materials: Innovations and Supply Chain Dynamics
Ferroelectric RF filter manufacturing is undergoing significant transformation in 2025, driven by the demand for high-performance, tunable components in 5G, Wi-Fi 6/7, and emerging wireless standards. Ferroelectric materials, particularly barium strontium titanate (BST), are at the core of these innovations, enabling voltage-tunable capacitors and filters with low insertion loss and high linearity. The manufacturing landscape is shaped by both established players and new entrants, with a focus on scaling production, improving material quality, and securing robust supply chains.
Key industry participants such as Murata Manufacturing Co., Ltd. and TDK Corporation are leveraging their expertise in ceramic and thin-film technologies to advance ferroelectric RF filter production. Murata, for example, has expanded its portfolio of tunable RF components, integrating BST-based varactors into modules for smartphones and infrastructure equipment. TDK, with its deep roots in electronic materials, continues to invest in research and development of ferroelectric thin films, targeting both discrete and integrated filter solutions for next-generation wireless devices.
In the United States, Qorvo, Inc. and Skyworks Solutions, Inc. are actively developing tunable RF front-end modules incorporating ferroelectric elements. Qorvo’s focus includes the integration of BST-based tunable filters to address the growing complexity of carrier aggregation and dynamic spectrum allocation in 5G and beyond. Skyworks is similarly exploring ferroelectric materials to enhance the performance and miniaturization of its filter products, aiming to meet the stringent requirements of mobile and IoT applications.
On the supply chain front, the sourcing and processing of high-purity ferroelectric materials remain critical. Companies such as TDK Corporation and Murata Manufacturing Co., Ltd. maintain vertically integrated operations, controlling material synthesis, wafer fabrication, and device assembly. This integration is increasingly important as demand for RF filters surges and geopolitical factors influence the availability of raw materials, particularly rare earth elements and high-purity oxides.
Looking ahead, the outlook for ferroelectric RF filter manufacturing is robust. The transition to 6G and the proliferation of connected devices are expected to drive further investment in material innovation, process automation, and supply chain resilience. Industry leaders are also exploring new ferroelectric compounds and scalable deposition techniques, such as atomic layer deposition (ALD), to enhance device performance and yield. As a result, the next few years will likely see continued collaboration between material suppliers, device manufacturers, and end-users to ensure the reliable delivery of advanced ferroelectric RF filters for global wireless infrastructure.
RF Filter Technology Evolution: From 4G to 6G
The evolution of RF filter technology from 4G to 6G is driving significant innovation in ferroelectric RF filter manufacturing. Ferroelectric materials, such as barium strontium titanate (BST), are increasingly being adopted for their tunable dielectric properties, enabling dynamic frequency selection and miniaturization critical for next-generation wireless systems. As 5G networks mature and 6G research accelerates, the demand for agile, high-performance RF filters is intensifying, with ferroelectric-based solutions positioned at the forefront of this transition.
In 2025, leading manufacturers are scaling up production of ferroelectric RF filters to meet the requirements of advanced mobile devices, infrastructure, and emerging applications like IoT and automotive connectivity. Murata Manufacturing Co., Ltd., a global leader in electronic components, has invested heavily in the development of tunable RF components using ferroelectric materials, focusing on miniaturization and integration for 5G and anticipated 6G platforms. Similarly, TDK Corporation is leveraging its expertise in material science to produce high-frequency, low-loss ferroelectric filters, targeting both sub-6 GHz and millimeter-wave bands.
The manufacturing process for ferroelectric RF filters involves precise thin-film deposition techniques, such as sputtering and chemical vapor deposition, to achieve uniformity and high yield at scale. Companies like Qorvo, Inc. are advancing proprietary processes to integrate ferroelectric materials with standard semiconductor platforms, enabling monolithic integration and improved performance. These efforts are supported by ongoing collaborations with equipment suppliers and material innovators to enhance process control and reliability.
Recent data from industry consortia and manufacturers indicate that ferroelectric RF filters are achieving insertion losses below 1 dB and tuning ranges exceeding 20%, metrics that are critical for dynamic spectrum allocation in dense wireless environments. The ability to fabricate these filters on 200 mm and 300 mm wafers is also improving cost efficiency and throughput, making them increasingly viable for mass-market adoption.
Looking ahead, the outlook for ferroelectric RF filter manufacturing is robust. As 6G research targets frequencies above 100 GHz and demands even greater reconfigurability, manufacturers are investing in new material compositions and scalable fabrication methods. Strategic partnerships between device makers, foundries, and material suppliers are expected to accelerate commercialization, with companies like Murata Manufacturing Co., Ltd. and TDK Corporation poised to play pivotal roles in shaping the RF landscape for the next decade.
Competitive Landscape: Leading Manufacturers and New Entrants
The competitive landscape for ferroelectric RF filter manufacturing in 2025 is characterized by a dynamic mix of established industry leaders and innovative new entrants, each leveraging advances in materials science and semiconductor processing to address the growing demand for high-performance, tunable RF components in 5G, Wi-Fi 6/7, and emerging wireless applications.
Among the most prominent players, Murata Manufacturing Co., Ltd. continues to be a global leader in RF filter technology, with a strong focus on miniaturized, high-frequency components. Murata’s ongoing investments in ferroelectric materials and thin-film processing have enabled the company to deliver filters with improved selectivity and lower insertion loss, critical for next-generation mobile devices and infrastructure.
Another key manufacturer, TDK Corporation, has expanded its portfolio of RF components to include ferroelectric-based solutions, capitalizing on its expertise in multilayer ceramic and thin-film technologies. TDK’s strategic collaborations with wireless chipset vendors and device OEMs position it well to address the evolving requirements of the telecommunications sector.
In the United States, Qorvo, Inc. and Skyworks Solutions, Inc. are actively developing tunable RF filters utilizing ferroelectric materials, aiming to provide agile frequency management for 5G and beyond. Qorvo, in particular, has highlighted the potential of ferroelectric barium strontium titanate (BST) in enabling adaptive filtering, which is increasingly important as spectrum allocations become more fragmented and dynamic.
Emerging entrants are also shaping the competitive landscape. Akoustis Technologies, Inc. is commercializing single-crystal ferroelectric materials for high-frequency RF filters, targeting both mobile and infrastructure markets. Akoustis’ patented XBAW® technology leverages the unique properties of ferroelectric films to achieve high Q-factors and steep filter skirts, attributes sought after in Wi-Fi 6E/7 and 5G front-end modules.
Looking ahead, the sector is expected to see further consolidation and collaboration, as established players seek to integrate ferroelectric filter capabilities into broader RF front-end solutions. At the same time, new entrants with proprietary material processes or device architectures may attract strategic investments or partnerships. The ongoing evolution of wireless standards and the push for spectrum efficiency will continue to drive innovation and competition among manufacturers, with a particular emphasis on scalable, cost-effective ferroelectric filter production.
Application Sectors: Mobile, IoT, Automotive, and Defense
Ferroelectric RF filter manufacturing is poised for significant growth and diversification across multiple application sectors in 2025 and the coming years, driven by the increasing demand for high-performance, miniaturized, and tunable RF components. The unique properties of ferroelectric materials—such as high dielectric tunability, low insertion loss, and compatibility with advanced semiconductor processes—are enabling their adoption in mobile communications, IoT, automotive, and defense applications.
In the mobile sector, the proliferation of 5G and the anticipated rollout of 6G networks are intensifying the need for agile and compact RF filters capable of handling complex spectrum environments. Leading manufacturers such as Murata Manufacturing Co., Ltd. and TDK Corporation are actively developing and scaling production of ferroelectric-based RF filters, leveraging their expertise in multilayer ceramic and thin-film technologies. These filters are being integrated into smartphones and wireless infrastructure to support dynamic frequency allocation and improved signal integrity.
The IoT sector is witnessing rapid expansion, with billions of connected devices requiring efficient spectrum management and low-power operation. Ferroelectric RF filters, with their tunability and small form factor, are increasingly favored for IoT modules and gateways. Companies like Qorvo, Inc. are investing in the development of tunable filter solutions that can be embedded in a wide range of IoT devices, from smart meters to industrial sensors, to enable reliable connectivity in crowded RF environments.
In the automotive industry, the shift toward connected and autonomous vehicles is driving demand for robust RF filtering solutions that can operate reliably under harsh conditions and across multiple frequency bands. Ferroelectric filters are being adopted for vehicle-to-everything (V2X) communications, radar, and infotainment systems. TAIYO YUDEN CO., LTD. and Murata Manufacturing Co., Ltd. are among the suppliers advancing automotive-grade ferroelectric RF components, focusing on high reliability and integration with automotive electronics platforms.
The defense sector continues to be a critical market for ferroelectric RF filters, where requirements for frequency agility, miniaturization, and resistance to electronic countermeasures are paramount. Organizations such as Northrop Grumman Corporation are exploring ferroelectric filter technologies for use in advanced radar, electronic warfare, and secure communications systems. The ability to rapidly tune filter characteristics in response to evolving threats is a key advantage driving adoption in military applications.
Looking ahead, the convergence of these sectors and the ongoing advancements in ferroelectric material science and manufacturing processes are expected to further accelerate the deployment of ferroelectric RF filters. Industry leaders are investing in R&D and capacity expansion to meet the growing demand, positioning ferroelectric RF filter technology as a cornerstone of next-generation wireless and electronic systems.
Manufacturing Processes and Cost Optimization Strategies
Ferroelectric RF filter manufacturing is undergoing significant transformation in 2025, driven by the demand for high-performance, tunable components in 5G, Wi-Fi 6/7, and emerging wireless applications. The core of these filters lies in the integration of ferroelectric materials—such as barium strontium titanate (BST)—onto semiconductor substrates, enabling voltage-controlled frequency agility and miniaturization. The manufacturing process typically involves thin-film deposition (often via sputtering or chemical vapor deposition), photolithography, etching, and advanced packaging to ensure compatibility with RF front-end modules.
Key industry players are refining these processes to improve yield, reduce costs, and scale production. Murata Manufacturing Co., Ltd., a global leader in RF components, has invested in proprietary thin-film technologies and automated production lines to enhance throughput and consistency in ferroelectric device fabrication. Their focus on in-line process monitoring and defect reduction has contributed to lower per-unit costs and higher device reliability. Similarly, TDK Corporation is leveraging its expertise in materials science and multilayer ceramic integration to optimize the deposition and patterning of ferroelectric films, aiming for higher capacitance tunability and lower insertion loss in mass-produced filters.
Cost optimization strategies in 2025 center on both materials and process innovations. Manufacturers are increasingly adopting larger wafer sizes (200mm and above) to benefit from economies of scale, while also exploring alternative ferroelectric compositions that offer improved performance at lower processing temperatures. Automation and AI-driven process control are being implemented to minimize human error and maximize yield, with companies like Qorvo, Inc. integrating real-time analytics into their filter production lines to rapidly identify and correct process deviations.
Another trend is the co-packaging of ferroelectric RF filters with other front-end components, reducing assembly steps and overall system cost. Skyworks Solutions, Inc. and KYOCERA AVX Components Corporation are both pursuing advanced packaging solutions, such as system-in-package (SiP) and wafer-level chip-scale packaging (WLCSP), to streamline integration and further drive down costs.
Looking ahead, the outlook for ferroelectric RF filter manufacturing is positive, with continued investment in process automation, material innovation, and supply chain optimization expected to further reduce costs and enable broader adoption in next-generation wireless devices. As 5G and beyond-5G networks proliferate, the ability to manufacture high-performance, tunable RF filters at scale will remain a critical differentiator for leading component suppliers.
Regulatory Standards and Industry Collaboration (e.g., ieee.org)
The regulatory landscape and industry collaboration for ferroelectric RF filter manufacturing are evolving rapidly as the technology matures and adoption accelerates in 2025. Ferroelectric RF filters, leveraging tunable dielectric materials such as barium strontium titanate (BST), are increasingly critical for next-generation wireless infrastructure, including 5G and emerging 6G systems. Regulatory standards are being shaped by both international and national bodies to ensure device interoperability, safety, and performance.
The IEEE continues to play a central role in developing standards relevant to RF components, including those utilizing ferroelectric materials. The IEEE Standards Association (IEEE-SA) is actively engaged in updating protocols for RF filter performance, electromagnetic compatibility, and environmental compliance. These standards are essential for manufacturers to ensure their products meet global requirements and can be integrated into multi-vendor networks. In parallel, the International Electrotechnical Commission (IEC) and the International Telecommunication Union (ITU) are contributing to harmonized testing and certification frameworks, particularly as spectrum allocations and device requirements evolve for 5G and beyond.
Industry collaboration is also intensifying, with leading manufacturers and material suppliers forming consortia and joint ventures to accelerate innovation and standardization. Companies such as Murata Manufacturing Co., Ltd. and TDK Corporation are at the forefront, both participating in global standardization efforts and collaborating with network operators and equipment vendors to validate ferroelectric RF filter performance in real-world deployments. These collaborations often extend to academic institutions and government research labs, fostering pre-competitive research and the development of open standards.
In the United States, the Federal Communications Commission (FCC) is monitoring the integration of advanced RF components, including ferroelectric filters, to ensure compliance with spectrum management and device authorization rules. Meanwhile, the European Telecommunications Standards Institute (ETSI) is updating its technical specifications to reflect the unique properties and benefits of tunable ferroelectric devices, particularly their potential to enhance spectrum efficiency and reduce interference.
Looking ahead, regulatory bodies are expected to further refine standards for reliability, environmental impact (such as RoHS and REACH compliance), and cybersecurity as ferroelectric RF filters become more prevalent in critical communications infrastructure. Industry alliances and standards organizations will remain pivotal in aligning technical requirements, accelerating certification processes, and supporting the global scale-up of ferroelectric RF filter manufacturing.
Challenges: Scalability, Reliability, and Integration
Ferroelectric RF filter manufacturing is at a pivotal stage in 2025, as the industry seeks to address critical challenges related to scalability, reliability, and integration. These challenges are particularly pressing as demand for high-performance, miniaturized RF components accelerates in 5G, Wi-Fi 6/7, and emerging 6G applications.
Scalability remains a significant hurdle. Ferroelectric materials, such as barium strontium titanate (BST), offer tunability and low loss, but their deposition and patterning at wafer scale are complex. Leading manufacturers like Murata Manufacturing Co., Ltd. and TDK Corporation have invested in advanced thin-film deposition techniques, including metal-organic chemical vapor deposition (MOCVD) and sputtering, to improve uniformity and throughput. However, achieving consistent ferroelectric properties across large wafers and high-volume production lines remains a technical bottleneck. The industry is also exploring 200 mm and 300 mm wafer processing to align with mainstream semiconductor manufacturing, but this transition introduces new yield and equipment compatibility issues.
Reliability is another core concern. Ferroelectric RF filters must maintain stable performance over billions of switching cycles and across wide temperature ranges. Degradation mechanisms, such as fatigue, imprint, and dielectric breakdown, can impact device longevity. Companies like Qorvo, Inc. and Skyworks Solutions, Inc. are actively developing reliability testing protocols and material engineering solutions to mitigate these effects. For instance, optimizing electrode materials and interface engineering are strategies being pursued to enhance endurance and reduce failure rates in commercial products.
Integration with existing RF front-end modules and CMOS platforms is a third major challenge. Ferroelectric filters must be compatible with standard semiconductor processes to enable cost-effective, high-density integration. Murata Manufacturing Co., Ltd. and TDK Corporation are working on monolithic integration approaches, aiming to co-fabricate ferroelectric devices with other passive and active components. However, issues such as thermal budget constraints, cross-contamination, and process complexity must be overcome to achieve seamless integration.
Looking ahead, the next few years will likely see incremental progress as manufacturers refine deposition techniques, develop robust reliability standards, and advance integration schemes. Collaborative efforts between material suppliers, equipment vendors, and device manufacturers will be essential to scale up production and meet the stringent requirements of next-generation wireless systems.
Future Outlook: Disruptive Opportunities and Strategic Recommendations
The future outlook for ferroelectric RF filter manufacturing in 2025 and the coming years is shaped by rapid advancements in wireless communication, the proliferation of 5G and emerging 6G technologies, and the increasing demand for high-performance, miniaturized components. Ferroelectric materials, particularly barium strontium titanate (BST), are at the forefront of this transformation due to their tunable dielectric properties, enabling agile and reconfigurable RF filters that outperform traditional solutions in terms of size, power consumption, and frequency agility.
Key industry players such as Murata Manufacturing Co., Ltd. and TDK Corporation are investing heavily in the development and scaling of ferroelectric-based RF components. Murata has demonstrated leadership in integrating ferroelectric materials into multilayer ceramic devices, while TDK is advancing thin-film technologies to enable high-frequency, low-loss RF filters suitable for next-generation mobile devices and infrastructure. These companies are expected to expand their manufacturing capacities and introduce new product lines tailored for 5G/6G base stations, smartphones, and IoT devices.
In the United States, Qorvo, Inc. and Skyworks Solutions, Inc. are actively exploring ferroelectric and tunable filter technologies to address the growing complexity of RF front-end modules. Their focus is on leveraging ferroelectric materials to achieve dynamic spectrum management and interference mitigation, which are critical for dense urban deployments and the increasing number of connected devices.
Strategically, the next few years will likely see increased collaboration between material suppliers, device manufacturers, and system integrators to accelerate the commercialization of ferroelectric RF filters. Partnerships with foundries and investments in advanced deposition and patterning techniques will be essential to achieve the high yield and reliability required for mass-market adoption. Furthermore, the integration of ferroelectric filters with advanced packaging solutions, such as system-in-package (SiP) and 3D integration, will be a disruptive opportunity, enabling further miniaturization and performance gains.
To capitalize on these opportunities, manufacturers should prioritize R&D in material engineering, process scalability, and reliability testing. Engaging with standardization bodies and participating in industry consortia will also be crucial to ensure interoperability and accelerate time-to-market. As the competitive landscape intensifies, companies that can deliver cost-effective, high-performance ferroelectric RF filters at scale will be well-positioned to capture significant market share in the evolving wireless ecosystem.
Sources & References
- Murata Manufacturing Co., Ltd.
- Skyworks Solutions, Inc.
- KYOCERA AVX Components Corporation
- LG Electronics
- Kyocera Corporation
- Akoustis Technologies, Inc.
- Northrop Grumman Corporation
- IEEE
- International Telecommunication Union