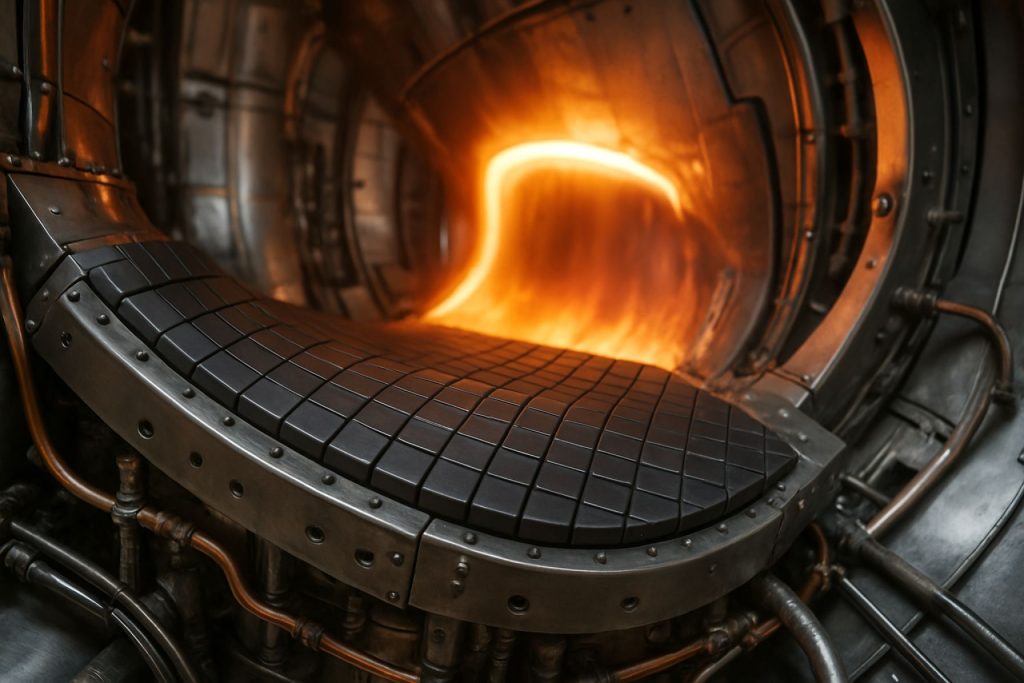
Engineering the Future: How Divertor Materials Are Powering Fusion Reactor Innovation in 2025 and Beyond. Explore the Technologies, Market Growth, and Strategic Shifts Shaping the Next Era of Clean Energy.
- Executive Summary: The State of Divertor Materials in 2025
- Market Size, Growth Forecasts, and Key Drivers (2025–2030)
- Core Technologies: Tungsten, Alloys, and Advanced Composites
- Emerging Materials: High-Entropy Alloys and Liquid Metal Solutions
- Performance Demands: Heat Flux, Erosion, and Neutron Resistance
- Leading Players and R&D Initiatives (e.g., iter.org, f4e.europa.eu, ornl.gov)
- Supply Chain Dynamics and Raw Material Sourcing
- Regulatory Landscape and Industry Standards (e.g., iaea.org, asme.org)
- Investment Trends, Funding, and Strategic Partnerships
- Future Outlook: Commercialization Pathways and Market Opportunities
- Sources & References
Executive Summary: The State of Divertor Materials in 2025
As of 2025, divertor materials engineering stands at the forefront of fusion reactor development, driven by the urgent need to manage extreme heat and particle fluxes in next-generation devices. The divertor, a critical component in magnetic confinement fusion reactors such as tokamaks, is tasked with extracting heat and impurities from the plasma edge, making material selection and engineering a decisive factor for reactor longevity and performance.
Tungsten remains the leading candidate for divertor armor due to its high melting point, low sputtering yield, and favorable thermal conductivity. Major fusion projects, including the international ITER Organization, have committed to tungsten-based divertor designs for their first operational phases. ITER’s full-tungsten divertor, scheduled for installation in the late 2020s, is currently undergoing final qualification and manufacturing, with industrial partners such as Plansee SE and France Métallurgie supplying advanced tungsten components. These companies are recognized for their expertise in refractory metals and have scaled up production to meet the stringent demands of fusion applications.
In parallel, research consortia and national laboratories are intensifying efforts to address tungsten’s limitations, such as embrittlement under neutron irradiation and the risk of melt damage during plasma transients. The EUROfusion Consortium is spearheading the development of advanced tungsten alloys and composites, including fiber-reinforced tungsten and tungsten-laminate structures, aiming to enhance toughness and thermal shock resistance. These materials are being tested in high-heat-flux facilities and are slated for integration into demonstration reactors like DEMO in the early 2030s.
Alternative materials, such as liquid metal divertors using lithium or tin, are also under active investigation. Organizations like Princeton Plasma Physics Laboratory are leading experimental campaigns to evaluate the feasibility of liquid metal surfaces, which promise self-healing properties and reduced erosion. However, these concepts remain at the experimental stage and are unlikely to see deployment in large-scale reactors before 2030.
Looking ahead, the next few years will see continued investment in both industrial-scale tungsten component manufacturing and advanced material R&D. The fusion sector is increasingly engaging with established materials suppliers and forging new partnerships to accelerate qualification and supply chain readiness. The state of divertor materials engineering in 2025 is thus characterized by a pragmatic focus on tungsten, coupled with a robust pipeline of innovation aimed at overcoming its intrinsic challenges and preparing for the demands of commercial fusion power.
Market Size, Growth Forecasts, and Key Drivers (2025–2030)
The global market for divertor materials engineering in fusion reactors is poised for significant growth between 2025 and 2030, driven by the acceleration of fusion energy projects and the increasing demand for advanced plasma-facing components. As the international fusion community moves closer to the realization of large-scale demonstration reactors, such as ITER and DEMO, the need for robust, high-performance divertor materials is intensifying. The market is characterized by a focus on tungsten and tungsten-based alloys, which are favored for their high melting points, thermal conductivity, and resistance to plasma erosion.
Key drivers include the ongoing construction and commissioning of the ITER Organization project in France, which is entering critical phases of assembly and component integration through 2025 and beyond. ITER’s divertor, designed to handle heat fluxes up to 20 MW/m², relies on tungsten monoblock technology supplied by specialized manufacturers. Companies such as Plansee SE (Austria), a global leader in refractory metals, are central to the supply chain, providing precision-engineered tungsten and molybdenum components for fusion applications. Plansee SE has invested in advanced powder metallurgy and joining techniques to meet the stringent requirements of fusion divertors.
Another major player, Mitsubishi Materials Corporation (Japan), is actively involved in the development and supply of plasma-facing materials for both ITER and Japan’s national fusion programs. The company’s expertise in high-purity tungsten production and component fabrication positions it as a key supplier for upcoming demonstration reactors in Asia.
The European fusion community, coordinated by Fusion for Energy (F4E), is also investing heavily in next-generation divertor concepts, including liquid metal and composite materials, to address the challenges of neutron damage and tritium retention. F4E’s partnerships with industrial suppliers and research institutes are expected to drive innovation and market expansion through the late 2020s.
Market growth is further supported by the emergence of private fusion ventures, particularly in the United States and United Kingdom, which are accelerating timelines for pilot plants and commercial reactors. These companies are seeking advanced divertor solutions to enable higher power densities and longer operational lifetimes, creating new opportunities for material suppliers and engineering firms.
Overall, the divertor materials engineering market is projected to experience robust growth from 2025 to 2030, underpinned by large-scale fusion projects, technological advancements, and the increasing involvement of both established and emerging industry players. The sector’s outlook is closely tied to the progress of demonstration reactors and the successful scaling of advanced materials manufacturing capabilities.
Core Technologies: Tungsten, Alloys, and Advanced Composites
Divertor materials engineering is a cornerstone of fusion reactor development, with the divertor facing the most extreme thermal and particle fluxes in the reactor environment. As of 2025, the primary focus remains on tungsten and its advanced derivatives, given its high melting point, low sputtering yield, and favorable thermal conductivity. Tungsten is the baseline material for the ITER divertor, and its performance in this context is closely watched by the global fusion community. Plansee SE, a leading supplier of refractory metals, is a key industrial partner for ITER, providing tungsten monoblocks and other components for the divertor. Their expertise in powder metallurgy and large-scale fabrication is critical for meeting the demanding specifications of fusion applications.
However, pure tungsten is not without challenges. Its brittleness at low temperatures and susceptibility to recrystallization and cracking under neutron irradiation have spurred the development of tungsten alloys and composites. Alloying with elements such as rhenium, tantalum, or lanthanum oxide aims to improve ductility and resistance to radiation damage. Companies like Tokyo Tungsten Co., Ltd. and Mitsubishi Materials Corporation are actively engaged in the research and production of advanced tungsten alloys for high-heat-flux applications, leveraging their deep experience in refractory metal processing.
Beyond alloys, advanced composites are gaining traction. Tungsten fiber-reinforced tungsten (Wf/W) composites, for example, offer improved toughness and crack resistance, addressing one of the main limitations of monolithic tungsten. The European fusion program, through organizations such as EUROfusion, is supporting the scale-up of Wf/W manufacturing and testing, with the goal of deploying these materials in next-generation devices like DEMO. Additionally, research into functionally graded materials—where the composition transitions from tungsten at the plasma-facing surface to more ductile materials deeper in the structure—is ongoing, aiming to mitigate thermal stresses and improve component lifetime.
Looking ahead to the next few years, the fusion sector anticipates further industrialization of tungsten-based technologies. The supply chain is being strengthened, with Plansee SE and Mitsubishi Materials Corporation expanding their capabilities to meet anticipated demand from ITER, DEMO, and private fusion ventures. Meanwhile, the push for even more resilient materials continues, with collaborative efforts between industry and research consortia to qualify new alloys and composites under reactor-relevant conditions. The outcome of these efforts will be pivotal for the realization of reliable, long-lived divertor components in commercial fusion reactors.
Emerging Materials: High-Entropy Alloys and Liquid Metal Solutions
The engineering of divertor materials for fusion reactors is entering a transformative phase, with significant attention on emerging solutions such as high-entropy alloys (HEAs) and liquid metal systems. These innovations are driven by the extreme operational demands of next-generation fusion devices, including high heat flux, neutron irradiation, and plasma-material interactions. As of 2025, research and early-stage development are accelerating, with several organizations and companies at the forefront.
High-entropy alloys, composed of multiple principal elements, offer a unique combination of mechanical strength, thermal stability, and radiation resistance. Recent experimental campaigns have demonstrated that certain HEAs, such as those based on refractory metals (e.g., W-Ta-Cr-V), exhibit superior resistance to radiation-induced embrittlement and reduced erosion under plasma exposure compared to conventional tungsten. These properties are critical for divertor components, which must withstand localized heat loads exceeding 10 MW/m² in devices like ITER and DEMO. Collaborative projects involving national laboratories and industry partners are scaling up the synthesis and testing of HEAs, with pilot-scale fabrication lines being established to produce larger samples for integrated testing.
In parallel, liquid metal solutions—primarily lithium and tin—are gaining traction as self-healing, vapor-shielding divertor surfaces. Liquid metals can absorb and redistribute heat efficiently, while their flowing nature allows for continuous removal of surface impurities and mitigation of neutron damage. In 2025, several fusion technology companies and research consortia are advancing liquid metal divertor concepts. For instance, EUROfusion is coordinating multi-institutional efforts to test liquid tin and lithium systems in linear plasma devices and tokamak environments, focusing on compatibility with reactor-scale magnetic fields and long-term operational stability.
Industrial players such as Fusion for Energy (the European Domestic Agency for ITER) are supporting the development of advanced manufacturing techniques for both solid and liquid-based divertor components, including additive manufacturing and novel joining methods. Meanwhile, companies like Tokamak Energy and First Light Fusion are monitoring these material advances for potential integration into their compact fusion device designs, recognizing the need for robust, scalable solutions.
Looking ahead, the next few years will see intensified qualification of HEAs and liquid metals under reactor-relevant conditions, with a focus on scaling up from laboratory samples to full-size divertor modules. The interplay between academic research, industrial scale-up, and international collaboration is expected to accelerate the readiness of these materials for deployment in demonstration and pilot fusion reactors by the late 2020s.
Performance Demands: Heat Flux, Erosion, and Neutron Resistance
The engineering of divertor materials for fusion reactors in 2025 is shaped by the extreme performance demands imposed by next-generation devices. Divertors, which manage the exhaust of heat and particles from the plasma, must withstand heat fluxes exceeding 10 MW/m², intense neutron bombardment, and severe erosion—all while maintaining structural integrity and minimizing radioactive waste. These requirements are particularly acute for projects like ITER and the planned DEMO reactors, which serve as benchmarks for the sector.
Tungsten remains the leading candidate for plasma-facing components due to its high melting point (3,422°C), low sputtering yield, and good thermal conductivity. However, even tungsten faces challenges under the anticipated heat loads and neutron fluences. In ITER, for example, the divertor targets are constructed from tungsten monoblocks attached to copper alloy heat sinks, a design that must handle both steady-state and transient thermal loads. The ITER Organization has reported that the divertor must survive up to 20 MW/m² during transient events, with erosion rates kept below 0.1 mm per full-power year to ensure component longevity.
Neutron resistance is another critical factor. Fast neutrons from deuterium-tritium fusion can cause displacement damage and transmutation in materials, leading to embrittlement and swelling. Tungsten’s relatively low activation and slow transmutation rates make it preferable, but research continues into advanced alloys and composites to further enhance performance. Organizations such as EUROfusion are actively developing high-heat-flux test facilities and irradiation campaigns to qualify new materials, including tungsten fiber-reinforced composites and functionally graded materials that better manage thermal stresses.
Erosion, both from physical sputtering and chemical interactions with plasma impurities, remains a limiting factor. The UK Atomic Energy Authority (UKAEA) is investigating novel surface treatments and coatings to reduce erosion rates, as well as alternative materials like liquid metals (e.g., lithium or tin) that could self-heal under plasma exposure. These approaches are being tested in devices such as the MAST Upgrade and in collaboration with international partners.
Looking ahead, the next few years will see increased deployment of diagnostic tools and in-situ monitoring to better understand material degradation in operational environments. The integration of advanced manufacturing techniques, such as additive manufacturing for complex cooling structures, is also expected to accelerate. As fusion projects transition from experimental to pre-commercial phases, the performance demands on divertor materials will drive continued innovation and cross-sector collaboration among leading organizations and suppliers.
Leading Players and R&D Initiatives (e.g., iter.org, f4e.europa.eu, ornl.gov)
The engineering of divertor materials for fusion reactors is a critical focus area as the global fusion community advances toward the first operational demonstration plants. In 2025 and the coming years, several leading organizations and consortia are driving research, development, and qualification of advanced materials capable of withstanding the extreme heat and particle fluxes characteristic of fusion divertor environments.
The ITER Organization remains at the forefront, with its divertor program representing the world’s largest and most advanced effort in this domain. ITER’s divertor will employ tungsten as the plasma-facing material due to its high melting point, low sputtering yield, and favorable thermal conductivity. The manufacturing and pre-qualification of tungsten monoblock components are being carried out by industrial partners across Europe and Asia, with full-scale prototypes undergoing high-heat-flux testing to validate performance under ITER-relevant conditions. The assembly and installation of the first divertor cassettes are scheduled for the late 2020s, with ongoing R&D to address issues such as crack formation and erosion.
Within Europe, Fusion for Energy (F4E) coordinates the procurement and quality assurance of ITER’s divertor components, collaborating with industrial suppliers and research institutes to optimize manufacturing processes and ensure compliance with stringent specifications. F4E is also supporting the development of next-generation divertor concepts for DEMO, the European demonstration fusion power plant, with a focus on advanced tungsten alloys, functionally graded materials, and novel cooling architectures.
In the United States, the Oak Ridge National Laboratory (ORNL) is a key player in divertor materials R&D, leveraging its expertise in materials science, neutron irradiation, and additive manufacturing. ORNL is investigating high-performance tungsten composites, refractory alloys, and innovative joining techniques to enhance the resilience and manufacturability of divertor components. The laboratory is also involved in international collaborations, including the International Tokamak Physics Activity (ITPA) and the US-ITER project, to accelerate the qualification of new materials.
Japan’s National Institutes for Quantum Science and Technology (QST) is advancing divertor research through the JT-60SA project and participation in the Broader Approach activities with Europe. QST’s work includes the development of high-heat-flux test facilities and the evaluation of tungsten and carbon-based materials under simulated fusion conditions.
Looking ahead, the next few years will see intensified efforts to address the remaining challenges in divertor materials engineering, including the mitigation of neutron-induced embrittlement, real-time monitoring of component degradation, and the integration of advanced manufacturing methods. The collaborative approach among leading organizations and industry partners is expected to yield significant progress toward robust, scalable divertor solutions for future fusion power plants.
Supply Chain Dynamics and Raw Material Sourcing
The supply chain dynamics and raw material sourcing for divertor materials in fusion reactors are entering a critical phase as the sector moves from experimental to pre-commercial deployment. Divertors, which manage extreme heat and particle fluxes in fusion devices, require materials with exceptional thermal conductivity, erosion resistance, and neutron resilience. Tungsten remains the leading candidate due to its high melting point and low sputtering yield, but its supply chain is complex and geopolitically sensitive.
As of 2025, the majority of primary tungsten production is concentrated in China, which accounts for over 80% of global output, with significant mining and processing operations managed by companies such as China Minmetals Corporation and China Molybdenum Co., Ltd.. Outside China, notable suppliers include Wolfram Bergbau und Hütten AG in Austria and Sandvik in Sweden, both of which provide high-purity tungsten products suitable for advanced applications. The European Union has recognized tungsten as a critical raw material, prompting initiatives to diversify sourcing and invest in recycling and secondary production.
The fusion sector’s demand for tungsten is expected to rise sharply with the construction of demonstration plants such as ITER and the planned DEMO reactors. This has led to increased collaboration between fusion research organizations and material suppliers. For example, Plansee Group, a leading producer of refractory metals, is actively involved in supplying tungsten and tungsten alloys for fusion projects, working closely with the European Fusion Development Agreement (EFDA) and other stakeholders.
In parallel, the industry is exploring alternative materials and advanced manufacturing techniques to mitigate supply risks. Research into tungsten-copper composites, functionally graded materials, and novel coatings is ongoing, with companies like Tokyo Tungsten Co., Ltd. and H.C. Starck Tungsten developing specialized products for high-heat-flux applications. Additive manufacturing is also being adopted to produce complex divertor components with reduced material waste and improved performance.
Looking ahead, the outlook for divertor material supply chains hinges on geopolitical stability, investment in recycling infrastructure, and the successful scaling of alternative material technologies. The fusion industry is expected to intensify efforts to secure reliable, ethically sourced tungsten and to foster partnerships with established suppliers. The next few years will be pivotal in establishing robust, transparent supply chains capable of supporting the transition from experimental fusion devices to commercial power plants.
Regulatory Landscape and Industry Standards (e.g., iaea.org, asme.org)
The regulatory landscape and industry standards for divertor materials engineering in fusion reactors are rapidly evolving as the sector approaches the operational phase of next-generation devices. In 2025, the focus is on harmonizing safety, performance, and qualification protocols for materials that must withstand extreme heat fluxes, neutron irradiation, and plasma interactions unique to fusion environments.
The International Atomic Energy Agency (IAEA) remains the principal global body coordinating regulatory frameworks and technical standards for nuclear fusion, including divertor components. The IAEA’s Nuclear Fusion Technology Section regularly convenes technical meetings and publishes guidance on material selection, testing, and qualification, emphasizing tungsten and advanced composites as leading candidates for plasma-facing components. The IAEA’s Safety Standards Series and technical documents are increasingly referenced by national regulators and industry consortia to ensure consistency in safety assessments and licensing procedures.
In parallel, the American Society of Mechanical Engineers (ASME) is actively updating its Boiler and Pressure Vessel Code (BPVC) and related standards to address the unique requirements of fusion reactor components, including divertor modules. ASME’s Section III, Division 4, specifically targets fusion energy devices, providing rules for the construction of fusion reactor components and integrating lessons learned from ongoing international projects. These standards are critical for manufacturers and suppliers seeking to qualify new materials and fabrication methods for use in high-heat-flux environments.
On the industry side, major fusion projects such as ITER and DEMO are driving the adoption of harmonized standards. ITER’s procurement and quality assurance protocols, developed in collaboration with the IAEA and national agencies, set benchmarks for material traceability, non-destructive evaluation, and in-service inspection of divertor components. These protocols are influencing the supply chain, with companies like Framatome and Rosatom—both deeply involved in nuclear engineering and advanced materials—aligning their manufacturing and quality systems to meet these emerging requirements.
Looking ahead, the next few years will see increased convergence between regulatory bodies, industry consortia, and research organizations to establish internationally recognized standards for divertor materials. The anticipated commercialization of fusion pilot plants by the late 2020s will further accelerate the need for robust, certifiable standards, ensuring that divertor materials not only meet performance criteria but also regulatory approval for safe, reliable operation in future fusion power plants.
Investment Trends, Funding, and Strategic Partnerships
The landscape of investment and strategic partnerships in divertor materials engineering for fusion reactors is rapidly evolving as the sector approaches critical demonstration milestones in the mid-2020s. The drive to develop robust, high-performance divertor materials—capable of withstanding extreme heat and neutron fluxes—has attracted significant funding from both public and private sources, as well as spurred collaborations between research institutions, industrial suppliers, and fusion developers.
In 2025, major public investments continue to be channeled through international fusion projects such as ITER Organization, which has prioritized advanced tungsten and composite materials for its divertor components. ITER’s procurement strategy has involved contracts with European and Asian manufacturers specializing in refractory metals and high-precision fabrication, including companies like Plansee SE, a leading supplier of tungsten-based components, and Mitsubishi Materials Corporation, which has contributed to the development and supply of plasma-facing materials.
Private sector investment is also accelerating, particularly as commercial fusion startups move toward prototype and pilot plant phases. Companies such as Tokamak Energy and First Light Fusion in the UK, and Commonwealth Fusion Systems in the US, have raised substantial funding rounds in recent years, with a portion earmarked for materials R&D and supply chain development. These firms are increasingly forming strategic partnerships with advanced materials suppliers and engineering firms to co-develop next-generation divertor solutions, including novel tungsten alloys, functionally graded materials, and liquid metal concepts.
In parallel, government-backed initiatives such as the UK’s Spherical Tokamak for Energy Production (STEP) program, led by the UK Atomic Energy Authority, are fostering consortia that bring together universities, national labs, and industry partners to accelerate divertor materials innovation. The European Union’s Fusion for Energy agency is similarly supporting collaborative R&D and pre-commercial procurement for advanced plasma-facing components.
Looking ahead to the next few years, the outlook for investment and partnerships in divertor materials engineering is robust. As fusion demonstration projects approach first plasma and begin to validate materials performance under reactor-relevant conditions, further capital inflows and joint ventures are expected. The emergence of specialized supply chains for high-purity tungsten, advanced ceramics, and liquid metal systems will likely be shaped by ongoing collaborations between fusion developers, established materials companies, and new entrants focused on scalable manufacturing and recycling solutions.
Future Outlook: Commercialization Pathways and Market Opportunities
The commercialization of fusion energy hinges critically on the successful engineering of divertor materials capable of withstanding the extreme thermal and particle fluxes present in next-generation reactors. As of 2025, the global fusion sector is transitioning from experimental validation to pre-commercial demonstration, with divertor materials engineering at the forefront of this evolution. The next few years are expected to see significant advances in both material science and supply chain development, driven by the needs of large-scale demonstration projects and the anticipated rollout of pilot fusion power plants.
Tungsten remains the leading candidate for divertor armor due to its high melting point, low sputtering yield, and favorable thermal conductivity. Major suppliers such as Plansee and Johnson Matthey are actively scaling up production of high-purity tungsten and tungsten alloys, responding to increased demand from fusion projects worldwide. These companies are investing in advanced powder metallurgy and additive manufacturing techniques to produce complex divertor components with improved microstructural control and reduced defect rates. The focus is on enhancing resistance to cracking, embrittlement, and erosion under cyclic plasma loading.
In parallel, research consortia and industry partners are exploring composite and functionally graded materials to address the limitations of monolithic tungsten. For example, Framatome and Hitachi are collaborating with public research institutes to develop copper-tungsten and tungsten-fiber-reinforced composites, aiming to combine the thermal performance of tungsten with the ductility and manufacturability of copper-based materials. These efforts are supported by the growing ecosystem of fusion technology suppliers, including Sandvik and thyssenkrupp, which provide high-performance alloys and precision fabrication services.
The market outlook for divertor materials is closely tied to the timelines of flagship fusion projects such as ITER, DEMO, and private-sector pilot plants. As these projects move toward first plasma and extended operation, the demand for qualified divertor components is expected to grow rapidly. Industry bodies such as Fusion for Energy are coordinating procurement and qualification programs to ensure a reliable supply chain and to accelerate the commercialization of advanced materials.
Looking ahead, the next few years will likely see the emergence of new market entrants specializing in high-performance refractory materials, as well as increased collaboration between fusion developers and established materials suppliers. The successful commercialization of divertor materials engineering will not only enable the viability of fusion power but also create significant market opportunities for companies at the intersection of advanced manufacturing and energy technology.
Sources & References
- ITER Organization
- EUROfusion Consortium
- Princeton Plasma Physics Laboratory
- Fusion for Energy
- Fusion for Energy
- Tokamak Energy
- First Light Fusion
- Oak Ridge National Laboratory
- National Institutes for Quantum Science and Technology
- China Molybdenum Co., Ltd.
- Wolfram Bergbau und Hütten AG
- Sandvik
- H.C. Starck Tungsten
- International Atomic Energy Agency
- American Society of Mechanical Engineers
- Framatome
- Johnson Matthey
- Framatome
- Sandvik