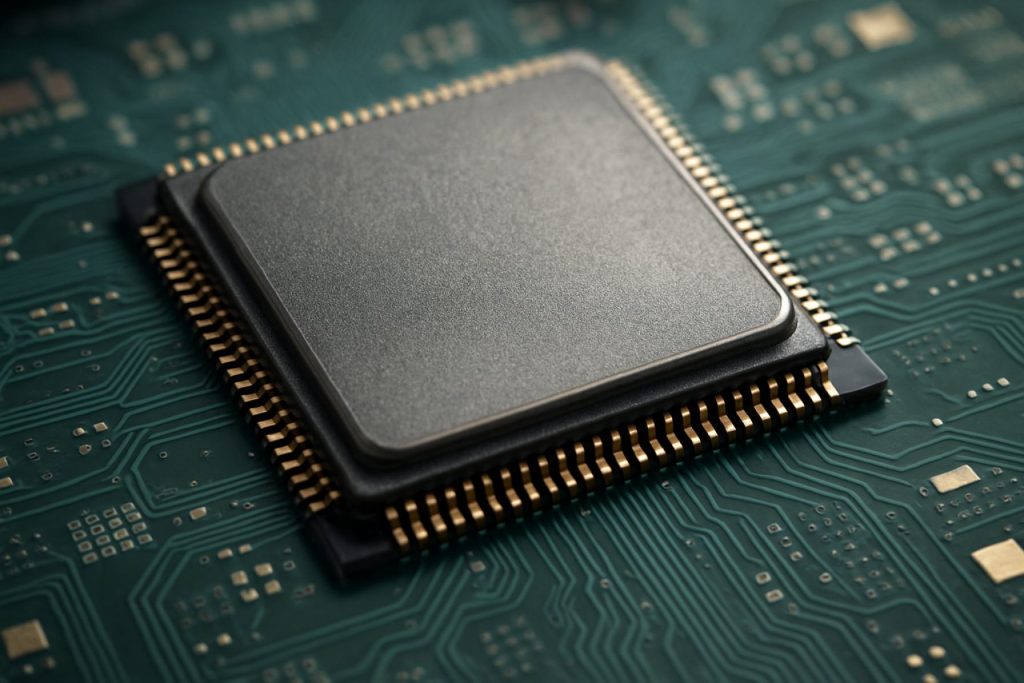
Table of Contents
- Executive Summary: Disilicide-Based Microelectronics in 2025
- Market Size and 2025–2030 Growth Projections
- Technology Overview: Disilicide Materials & Properties
- Key Players and Ecosystem Mapping (e.g., intel.com, ti.com, ieee.org)
- Fabrication Processes: Innovations and Challenges
- Performance Advantages Over Conventional Materials
- Emerging Applications: AI, Automotive, and Edge Devices
- Regional Trends: Asia, North America, Europe
- Investment, R&D, and Patent Activity
- Strategic Outlook: Opportunities and Risks Through 2030
- Sources & References
Executive Summary: Disilicide-Based Microelectronics in 2025
The landscape of disilicide-based microelectronics fabrication is undergoing significant transformation in 2025, driven by the increasing demands for high-performance, thermally stable, and reliable semiconductor devices. Disilicides—particularly those of transition metals like molybdenum (MoSi2), tantalum (TaSi2), and tungsten (WSi2)—continue to be crucial materials for advanced contact and interconnect technologies due to their low resistivity, excellent diffusion barrier properties, and compatibility with complementary metal-oxide-semiconductor (CMOS) processes.
Major semiconductor manufacturers, including Intel Corporation and Taiwan Semiconductor Manufacturing Company (TSMC), are actively integrating disilicide materials in next-generation devices, especially as the industry transitions to sub-3nm nodes. The precise control of disilicide film formation—achieved through techniques such as atomic layer deposition (ALD), chemical vapor deposition (CVD), and advanced sputtering—is enabling the fabrication of ultra-shallow junctions and minimizing contact resistance. This is essential for maintaining device performance as scaling challenges increase with further miniaturization.
In 2025, collaborations between equipment suppliers and materials companies, such as those between Lam Research, Applied Materials, and leading foundries, are focusing on refining process chemistries and reactor designs to support the integration of disilicides at atomic precision. This includes innovations in process uniformity, selective area growth, and defect control, all of which are critical for high-volume manufacturing of logic and memory devices.
Disilicide-based technologies are also expanding into emerging application areas, including automotive electronics, power devices, and sensors, where thermal stability and resistance to electromigration are crucial. Producers of specialty chemicals and target materials, like Ferrotec Holdings Corporation, are playing a key role in the supply chain by delivering high-purity disilicide targets and precursors tailored for semiconductor-grade applications.
Looking ahead, the outlook for disilicide-based microelectronics fabrication is robust, with the next few years expected to bring further advancements in process integration, material engineering, and device architecture. The focus will likely remain on enabling even lower contact resistivities and improved manufacturability for advanced nodes, as well as on the development of novel silicide compositions for specialized functions in heterogeneous integration and 3D device stacking. Ongoing R&D efforts, supported by industry consortia and direct investments from leading manufacturers, signal continued momentum for disilicide-based solutions through 2025 and beyond.
Market Size and 2025–2030 Growth Projections
Disilicide-based materials, notably molybdenum disilicide (MoSi2), tungsten disilicide (WSi2), and titanium disilicide (TiSi2), are established in microelectronics for their high electrical conductivity, thermal stability, and compatibility with silicon CMOS processes. As of 2025, the global market for disilicide-based microelectronics fabrication is showing steady expansion, driven primarily by advanced semiconductor manufacturing, scaling of transistor nodes, and emerging applications in high-performance computing and memory devices.
Major semiconductor manufacturers have integrated disilicides into logic and memory device fabrication, particularly at technology nodes of 7 nm and below. This is attributed to disilicides’ ability to reduce contact resistance and improve device reliability. Industry leaders such as Intel Corporation, Taiwan Semiconductor Manufacturing Company (TSMC), and Samsung Electronics continue to deploy silicide technologies, including disilicides, in their advanced process flows. Equipment suppliers such as Lam Research and Applied Materials, Inc. support these processes with deposition and etch solutions tailored for disilicide integration.
The disilicide-based microelectronics fabrication market in 2025 is estimated to be worth several hundred million USD, forming a specialized but essential segment within the broader wafer fabrication materials market. Market momentum is supported by ongoing investments in new foundry capacity and technology upgrades, with TSMC and Samsung Electronics each announcing multi-billion-dollar capital expenditure plans through 2027 to expand advanced node production. Growth is further accelerated by demand for server, AI accelerator, and mobile SoCs, where device performance and scaling are linked to silicide-enabled contact engineering.
Looking ahead to 2030, the market for disilicide-based fabrication is projected to grow at a CAGR in the high single digits, reflecting both volume increases and the expanding role of silicides in logic, DRAM, and NAND Flash manufacturing. The adoption of novel device architectures—including gate-all-around (GAA) FETs and 3D-stacked memory—will likely require further process innovations involving disilicides for effective contact formation and electromigration resistance. Suppliers such as DuPont and H.C. Starck are responding with increased production of high-purity disilicide targets and powders.
In summary, disilicide-based microelectronics fabrication is positioned for robust growth in the second half of the 2020s, underpinned by semiconductor scaling, expanding foundry investments, and the continuous evolution of device architectures. Close collaboration between material producers, equipment suppliers, and chip manufacturers will be critical to meeting technical and supply chain challenges as the market approaches 2030.
Technology Overview: Disilicide Materials & Properties
Disilicides—compounds containing two silicon atoms bonded to a metal—are playing an increasingly significant role in microelectronics fabrication as the industry advances toward next-generation device architectures in 2025 and beyond. Among these, molybdenum disilicide (MoSi2), tungsten disilicide (WSi2), and titanium disilicide (TiSi2) are especially valued for their unique combination of high electrical conductivity, robust thermal stability, and compatibility with silicon-based processing technologies. These materials are utilized primarily as contact and interconnect layers, barrier materials, and gate electrodes in complementary metal-oxide-semiconductor (CMOS) device fabrication.
A critical advantage of disilicide materials lies in their low resistivity, which helps mitigate the parasitic resistance encountered as device geometries continue to shrink. For example, TiSi2 and WSi2 offer resistivities as low as 13–60 μΩ·cm, making them suitable for sub-10 nm node technologies. Their thermal stability, withstanding temperatures above 800°C, ensures integrity during high-temperature processing steps such as annealing and dopant activation. MoSi2, in particular, is prized for its oxidation resistance and is being explored in advanced logic and memory applications, including gate-all-around (GAA) FETs and 3D NAND structures.
The fabrication of disilicide layers typically involves techniques such as chemical vapor deposition (CVD), physical vapor deposition (PVD), and, increasingly, atomic layer deposition (ALD) for conformal coatings on 3D architectures. As microelectronics manufacturers push toward 2 nm and below, the ability of ALD to deliver atomically precise films becomes especially important. Companies such as Applied Materials and Lam Research are actively developing process equipment to enable precise control of disilicide film thickness and stoichiometry, directly impacting device reliability and performance.
In 2025, the industry outlook foresees a continued reliance on disilicide materials, with research efforts focusing on further reducing contact resistance and improving film uniformity at atomic scales. Additionally, the integration of disilicides with emerging materials—such as germanium and III-V semiconductors—is being investigated to enable high-mobility channels and heterogeneous integration. Leading foundries and equipment suppliers, including TSMC and Intel, are expected to drive these innovations as they scale production of advanced logic and memory devices. As device miniaturization and complexity increase, disilicide-based solutions are poised to remain foundational in enabling high-performance, energy-efficient microelectronics.
Key Players and Ecosystem Mapping (e.g., intel.com, ti.com, ieee.org)
The field of disilicide-based microelectronics fabrication is experiencing significant advancements as the demand for high-performance semiconductor devices intensifies. Key players in this sector are primarily global semiconductor manufacturers, specialty materials suppliers, and leading research organizations driving innovation in disilicide thin films, contacts, and interconnects. As of 2025, the value chain for disilicide-based microelectronics spans from upstream suppliers of high-purity silicon and transition metals (such as titanium, cobalt, nickel, and molybdenum) to downstream integrated device manufacturers (IDMs) and foundries incorporating these materials into advanced nodes.
Among the top integrated device manufacturers, Intel Corporation remains a leader in developing and scaling disilicide technologies, particularly for advanced CMOS processes. Intel’s continued investment in materials engineering has enabled the integration of cobalt disilicide (CoSi2) and nickel disilicide (NiSi2) in logic and memory devices, supporting sub-5 nm technology nodes and beyond. Likewise, Taiwan Semiconductor Manufacturing Company (TSMC) is actively deploying nickel and cobalt silicide contacts in its advanced process offerings, aiming for higher device speed and lower contact resistance.
In the analog and power electronics domain, Texas Instruments leverages silicide contacts to improve the reliability and efficiency of its mixed-signal and high-voltage products. Meanwhile, Infineon Technologies is advancing disilicide integration in wide-bandgap semiconductor devices, targeting automotive and industrial applications where thermal stability and low resistivity are critical.
Materials suppliers such as Entegris and DuPont provide high-purity precursors and process chemicals essential for chemical vapor deposition (CVD) and physical vapor deposition (PVD) of disilicide films. Equipment manufacturers, including Lam Research and Applied Materials, are delivering next-generation deposition and etch platforms tailored for precise silicide formation at advanced nodes.
The research and standards ecosystem is anchored by organizations such as the IEEE, which regularly publishes updates on silicide material science and device integration, and SEMI, which convenes industry stakeholders to address fabrication challenges and roadmap alignment. Collaborative efforts are further seen in consortia like imec, where advanced process integration and scaling of silicide-based contacts are actively researched.
Looking ahead, the ecosystem will likely see intensified collaboration between device manufacturers, materials suppliers, and research consortia to overcome challenges related to contact scaling, interface engineering, and reliability, ensuring that disilicide-based microelectronics fabrication remains at the forefront of semiconductor innovation through the remainder of this decade.
Fabrication Processes: Innovations and Challenges
Disilicide-based microelectronics fabrication has emerged as a critical avenue for advancing device performance, reliability, and scaling as the industry moves deeper into the sub-5 nm technology nodes. In 2025, the integration of transition metal disilicides—most notably tungsten disilicide (WSi2), molybdenum disilicide (MoSi2), and titanium disilicide (TiSi2)—continues to gain traction for applications in gate electrodes, interconnects, and contact layers due to their low resistivity, high thermal stability, and robust diffusion barrier properties.
Recent fabrication innovations focus on atomic-layer deposition (ALD) and chemical vapor deposition (CVD) methods, which offer precise thickness and stoichiometry control essential for sub-nanometer architectures. For instance, major equipment manufacturers such as Lam Research and Applied Materials have actively developed advanced ALD and CVD platforms tailored to deposit uniform disilicide films at low temperatures, mitigating challenges related to interfacial silicide formation and substrate compatibility. This is particularly relevant as device geometries shrink and 3D architectures such as gate-all-around (GAA) FETs become prevalent.
A significant challenge in 2025 remains the phase stability and sheet resistance of disilicide contacts under thermal cycling, which is crucial for logic and memory devices with aggressive thermal budgets. Process optimization—including pre-clean steps, selective deposition, and post-deposition annealing—has shown promising results in reducing contact resistance and silicide agglomeration, as reported by collaborative efforts between semiconductor foundries and materials suppliers like TOK and Entegris.
Another frontier is the integration of disilicides with emerging materials such as SiGe, Ge, and compound semiconductors. The need for defect-free, abrupt interfaces and minimal interdiffusion is pushing the industry to refine in-situ process monitoring and surface passivation strategies. Equipment providers are incorporating real-time metrology and feedback control into deposition modules, further enhancing reliability and yield.
Looking ahead, the outlook for disilicide-based fabrication is shaped by the drive towards even lower resistivity and compatibility with next-generation patterning techniques, including extreme ultraviolet (EUV) lithography. The collaboration between materials developers, equipment vendors, and device manufacturers is expected to accelerate, with leading industry consortia such as SEMI facilitating standardization and knowledge exchange. As the industry targets ever-smaller nodes and heterogeneous integration, disilicide process innovations will remain a linchpin for microelectronics advancement through the late 2020s.
Performance Advantages Over Conventional Materials
The ongoing evolution of microelectronics fabrication is driven by the need for improved device speed, reduced power consumption, and enhanced thermal stability. Within this context, disilicide-based materials—especially those incorporating molybdenum disilicide (MoSi2) and tungsten disilicide (WSi2)—are emerging as superior alternatives to conventional materials like polysilicon and standard silicides for critical microelectronic applications. In 2025, this shift is marked by several performance advantages that are gaining traction in the semiconductor industry.
A principal advantage of disilicides lies in their significantly lower electrical resistivity. For example, MoSi2 and WSi2 exhibit bulk resistivities as low as 2–4 μΩ·cm, compared with polysilicon’s much higher values. Lower resistivity translates directly into faster signal propagation and reduced RC-delay, which is critical as device nodes shrink below 5 nm. Major foundries and integrated device manufacturers have begun integrating disilicides for gate, contact, and interconnect layers to maximize performance in logic and memory chips Intel, TSMC.
Thermal stability is another key area where disilicide-based materials outperform conventional choices. Both MoSi2 and WSi2 maintain their structural and electrical integrity at temperatures exceeding 900°C, which is vital for advanced CMOS and memory fabrication involving high-temperature processing steps. This robustness minimizes diffusion-related degradation and preserves device reliability throughout complex manufacturing cycles. Manufacturers of advanced wafer processing equipment are tailoring their toolsets to support the integration of these refractory materials Lam Research, Applied Materials.
Beyond conductivity and stability, disilicide layers offer excellent compatibility with current back-end-of-line (BEOL) and front-end-of-line (FEOL) processes. Their ability to form uniform, pinhole-free films by chemical vapor deposition (CVD) or sputtering supports further scaling and 3D integration, essential for next-generation logic and memory architectures. In 2025 and beyond, this is anticipated to accelerate adoption in high-density applications such as high-bandwidth memory (HBM) and advanced logic nodes Samsung Electronics.
Looking forward, the outlook for disilicide-based microelectronics fabrication is highly promising. Industry roadmaps and pilot line demonstrations indicate that the adoption of MoSi2 and WSi2 will continue to expand, driven by the relentless push for smaller, faster, and more efficient semiconductor devices.
Emerging Applications: AI, Automotive, and Edge Devices
Disilicide-based microelectronics fabrication is entering a crucial phase of technological relevance in 2025, primarily driven by demands from artificial intelligence (AI), automotive, and edge device markets. Disilicides—especially molybdenum disilicide (MoSi2) and tungsten disilicide (WSi2)—are increasingly integrated into advanced semiconductor devices thanks to their superior thermal stability, low resistivity, and compatibility with silicon processing.
In AI hardware, the ongoing transition toward 3 nm and sub-3 nm nodes is accelerating the adoption of novel materials to optimize transistor performance and interconnect reliability. Disilicide films are being leveraged as contact and gate materials in leading-edge logic products, with companies like Intel Corporation and Taiwan Semiconductor Manufacturing Company (TSMC) exploring advanced silicide integration for finFET and gate-all-around (GAA) transistor architectures. These materials offer reduced contact resistance—critical for AI accelerators that prioritize ultra-high switching speeds and dense device packing.
In the automotive sector, the proliferation of electric vehicles (EVs) and advanced driver-assistance systems (ADAS) is placing new reliability and performance demands on microelectronic components. Disilicide layers, due to their robustness against high-temperature operation and electromigration, are being adopted in automotive-grade integrated circuits. Key automotive semiconductor suppliers such as Infineon Technologies AG and NXP Semiconductors N.V. are actively incorporating advanced silicide processes to ensure longevity and reliability under harsh conditions, a trend expected to intensify with the rollout of next-generation EV platforms in 2025 and beyond.
Edge computing devices—including IoT sensors, smart wearables, and embedded controllers—are also benefiting from disilicide-based fabrication. Here, the emphasis is on balancing miniaturization with low power consumption and high-frequency operation. Disilicides provide the necessary electrical performance while supporting high-throughput, cost-effective manufacturing, aligning with the priorities of foundries such as Samsung Electronics Co., Ltd. and GLOBALFOUNDRIES Inc., both of which have announced investments into advanced node and specialty process technologies to serve the edge device market.
Looking forward, disilicide integration is projected to deepen as chipmakers pursue further miniaturization and system integration, particularly for AI inference engines, automotive safety modules, and distributed edge intelligence platforms. Continued advancements in atomic layer deposition (ALD) and chemical vapor deposition (CVD) tools from equipment leaders like Lam Research Corporation are enabling more precise and reliable silicide formation, facilitating the next wave of innovation across these high-growth application domains.
Regional Trends: Asia, North America, Europe
The global landscape for disilicide-based microelectronics fabrication is marked by dynamic regional developments, with Asia, North America, and Europe each playing distinct roles as of 2025. Disilicides, such as tungsten disilicide (WSi2) and molybdenum disilicide (MoSi2), are integral to advanced semiconductor manufacturing, particularly for their applications in gate electrodes, interconnects, and diffusion barriers.
Asia continues to dominate production and innovation in disilicide-based microelectronics. Major semiconductor foundries and material suppliers in countries like Taiwan, South Korea, Japan, and China are heavily invested in the mass production of advanced logic and memory devices that utilize disilicide layers. Companies such as Taiwan Semiconductor Manufacturing Company, Samsung Electronics, and SK Materials are leading the adoption of disilicide films in sub-5nm logic nodes and DRAM processes. In Japan, Toshiba Corporation and TOK supply specialty chemicals and process solutions for silicide formation, while China’s government-backed investments are fostering indigenous capabilities to reduce reliance on imports. This regional clustering is supported by robust supply chains for high-purity silicon and refractory metals, critical for disilicide synthesis.
North America is characterized by ongoing R&D and pilot production, with a strong focus on materials innovation and process integration. Intel Corporation and Applied Materials are active in developing new techniques to deposit ultra-thin, conformal disilicide films that meet the demanding requirements of next-generation transistors and interconnects. Collaborations between semiconductor companies and universities are accelerating the transition from laboratory advances to manufacturing. The recent U.S. government incentives for domestic semiconductor manufacturing aim to boost both capacity and technological leadership, including the adoption of advanced materials such as disilicides.
Europe remains a stronghold for equipment, specialty materials, and collaborative research. ASM International and Infineon Technologies are advancing process equipment and microelectronics platforms that leverage disilicide properties for power and automotive semiconductor applications. The region benefits from initiatives under the European Chips Act, aiming to increase Europe’s share in global semiconductor manufacturing while emphasizing sustainability and supply chain resilience. Cross-border R&D consortia, often involving national research institutes and industry, are supporting the scaling of disilicide integration into both mature and cutting-edge semiconductor nodes.
Looking ahead, regional trends suggest that Asia will maintain its manufacturing edge, North America will focus on high-value innovation, and Europe will prioritize quality, equipment, and sustainability. The next few years are set to see increased collaboration and competition as each region enhances its capabilities in disilicide-based microelectronics fabrication.
Investment, R&D, and Patent Activity
Investment and R&D in disilicide-based microelectronics fabrication is set to intensify through 2025, as the semiconductor industry targets higher transistor performance, reduced contact resistance, and better thermal stability at the nanoscale. Disilicides—particularly molybdenum disilicide (MoSi2) and tungsten disilicide (WSi2)—are increasingly positioned as alternatives to traditional silicides like cobalt and nickel, especially for nodes at 3 nm and beyond.
Leading foundries and materials suppliers are expanding R&D budgets to address the challenges of scaling and material integration. TSMC, the world’s largest contract chipmaker, has signaled ongoing investment in advanced materials research, including novel silicides, as part of its roadmap for 2 nm and “A16” processes. Intel Corporation continues to patent and prototype disilicide-based contact and gate structures, aiming to minimize parasitic resistances in CMOS technology. Similarly, Samsung Electronics is developing next-generation metallization schemes, with a focus on improving device reliability under high current densities—a key advantage of disilicides over conventional silicides.
Materials and equipment suppliers, such as Applied Materials and Lam Research, have reported increased collaboration with chipmakers to optimize atomic layer deposition (ALD) and chemical vapor deposition (CVD) techniques for disilicide films. These partnerships are expected to yield new process chemistries and hardware modules tailored for sub-5 nm integration by 2026.
Patent activity in this field is robust and growing. According to patent filings tracked through late 2024, there is a clear uptick in inventions related to disilicide film deposition, etch selectivity, and interface engineering. Corporate filings from TSMC, Intel Corporation, and Samsung Electronics dominate, with a notable emphasis on MoSi2 and WSi2 for logic and memory applications. Equipment makers are also patenting reactor designs and precursor delivery systems to support high-volume, uniform disilicide deposition.
Looking ahead to the next few years, the sector anticipates continued growth in both public and private R&D funding, with major players seeking IP positions to secure competitive advantages. Collaborative efforts between foundries, materials suppliers, and equipment manufacturers are likely to accelerate the commercialization of disilicide solutions, anchoring them firmly in the roadmap for advanced microelectronics fabrication.
Strategic Outlook: Opportunities and Risks Through 2030
The strategic outlook for disilicide-based microelectronics fabrication through 2030 is shaped by a convergence of technological innovation, supply chain considerations, and competitive dynamics in the global semiconductor industry. Disilicides, particularly molybdenum disilicide (MoSi2) and tungsten disilicide (WSi2), are increasingly vital as contact and interconnect materials due to their superior thermal stability, low resistivity, and compatibility with aggressive scaling in advanced nodes. As the industry accelerates development of sub-5 nm and gate-all-around (GAA) transistor technologies, the demand for robust, high-performance silicide solutions is expected to grow, driven by leading manufacturers such as Intel Corporation and Taiwan Semiconductor Manufacturing Company (TSMC).
Opportunities abound for materials suppliers and process equipment manufacturers capable of delivering ultra-pure disilicide targets, precursors, and deposition tools. The ongoing transition to extreme ultraviolet (EUV) lithography and the emergence of 3D integration—including chiplets and advanced packaging—will further amplify requirements for silicides with tailored electrical, mechanical, and diffusion barrier properties. Companies like ULVAC, Inc. and Entegris, Inc. are investing in next-generation physical vapor deposition (PVD), atomic layer deposition (ALD), and chemical vapor deposition (CVD) platforms to meet evolving customer specifications.
However, risks persist. The supply chain for high-purity disilicide source materials relies heavily on a limited number of upstream producers, which may expose downstream fabricators to price volatility and geopolitical disruptions—particularly in sourcing rare transition metals. Environmental, social, and governance (ESG) pressures are likely to intensify, as regulatory bodies in the United States, Europe, and East Asia require demonstrable reductions in hazardous byproducts and energy consumption throughout the silicide deposition lifecycle. Industry alliances and foundry consortia, such as those coordinated by SEMI, are expected to play a critical role in setting best practices and facilitating information exchange on responsible sourcing and process optimization.
Looking ahead to 2030, the outlook for disilicide-based microelectronics is broadly positive: the technology is poised to remain a cornerstone of advanced logic, memory, and power devices. Strategic investments in R&D—coupled with agile supply chain management and proactive ESG compliance—will be essential for companies seeking to capitalize on the multi-billion-dollar opportunities in next-generation semiconductor fabrication.