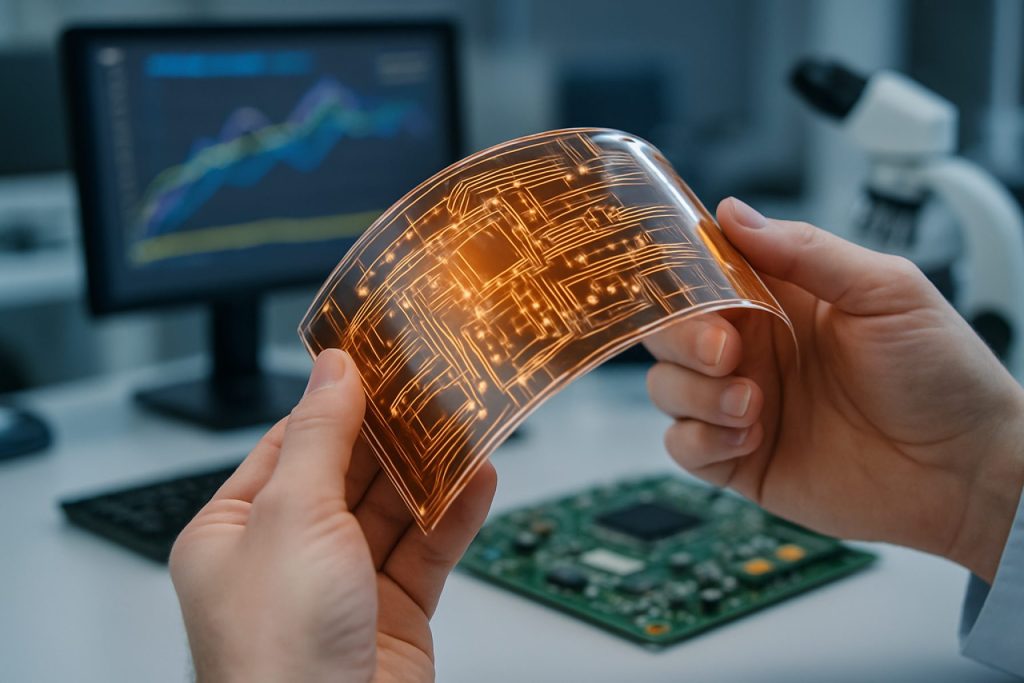
Defect Engineering for Flexible Electronics in 2025: How Precision Control is Shaping the Next Generation of Wearables, Displays, and IoT Devices. Explore the Market Forces and Innovations Driving Unprecedented Growth.
- Executive Summary: 2025 Outlook and Key Takeaways
- Market Size, Growth Forecasts, and Investment Trends (2025–2030)
- Core Technologies in Defect Engineering for Flexible Electronics
- Material Innovations: Polymers, Substrates, and Nanomaterials
- Process Control and Quality Assurance: Advanced Inspection and Metrology
- Key Applications: Wearables, Flexible Displays, Sensors, and Medical Devices
- Competitive Landscape: Leading Companies and Strategic Partnerships
- Regulatory Standards and Industry Initiatives (e.g., ieee.org, sema.org)
- Challenges: Yield, Scalability, and Reliability in Mass Production
- Future Outlook: Emerging Opportunities and R&D Directions Through 2030
- Sources & References
Executive Summary: 2025 Outlook and Key Takeaways
Defect engineering has emerged as a pivotal strategy in advancing the performance and reliability of flexible electronics, a sector poised for significant growth in 2025 and beyond. As the demand for bendable displays, wearable sensors, and conformable medical devices accelerates, manufacturers are increasingly focused on controlling and exploiting material defects to enhance device efficiency, mechanical resilience, and longevity.
In 2025, leading industry players are intensifying efforts to optimize defect densities in critical materials such as organic semiconductors, metal oxides, and two-dimensional (2D) materials. Companies like Samsung Electronics and LG Electronics—both global leaders in flexible OLED displays—are investing in advanced in-line inspection and atomic-level defect passivation techniques to minimize yield losses and improve display lifetimes. These efforts are complemented by collaborations with material suppliers and equipment manufacturers to develop new encapsulation and self-healing technologies that address defect-induced degradation.
In the realm of flexible sensors and circuits, DuPont and Kuraray are notable for their work on polymer substrates and conductive inks, where defect control at the nanoscale is critical for maintaining electrical performance under repeated flexing. The integration of defect-tolerant materials and novel device architectures is enabling the production of flexible electronics with higher yields and improved mechanical durability, a trend expected to continue as manufacturing scales up.
Recent data from industry consortia and manufacturing alliances indicate that defect-related yield losses in flexible electronics production lines have decreased by up to 30% over the past two years, thanks to the adoption of real-time monitoring and machine learning-based defect classification. Organizations such as SEMI are facilitating knowledge exchange and standardization efforts, which are accelerating the deployment of best practices across the supply chain.
Looking ahead, the outlook for defect engineering in flexible electronics is robust. The next few years will likely see the commercialization of devices with unprecedented form factors and reliability, driven by continued innovation in defect detection, mitigation, and exploitation. As flexible electronics penetrate new markets—including automotive interiors, smart packaging, and biomedical implants—defect engineering will remain a cornerstone of competitive differentiation and technological progress.
Market Size, Growth Forecasts, and Investment Trends (2025–2030)
The market for defect engineering in flexible electronics is poised for significant expansion between 2025 and 2030, driven by the rapid adoption of flexible displays, wearable devices, and advanced sensor technologies. As manufacturers strive to improve device reliability and performance, defect engineering—encompassing the identification, control, and mitigation of material and process-induced defects—has become a critical enabler for commercial viability.
In 2025, the flexible electronics sector is expected to surpass $40 billion in global market value, with defect engineering solutions representing a growing share of this figure. Major display manufacturers such as Samsung Electronics and LG Electronics are investing heavily in advanced inspection and repair technologies to address yield losses associated with microcracks, delamination, and particle contamination in OLED and flexible TFT production lines. These companies have reported yield improvements of up to 10% in new-generation flexible panels through the integration of in-line defect detection and self-healing material systems.
The next five years will see increased capital expenditure from leading semiconductor and display equipment suppliers, including Applied Materials and Lam Research, who are developing specialized tools for nanoscale defect analysis and atomic-level repair. These investments are expected to accelerate the commercialization of flexible electronics in automotive, healthcare, and consumer applications, where reliability standards are stringent.
On the materials front, companies such as DuPont and Kuraray are expanding their portfolios of engineered substrates and encapsulants designed to minimize defect propagation during device bending and stretching. Collaborative efforts between material suppliers and device manufacturers are anticipated to yield new defect-tolerant architectures, further reducing failure rates and enabling mass production.
Investment trends indicate a surge in venture capital and strategic partnerships targeting startups specializing in AI-driven defect inspection and predictive maintenance for roll-to-roll manufacturing. Industry consortia, including the SEMI and FlexTech Alliance, are facilitating joint R&D programs to standardize defect classification and accelerate technology transfer from lab to fab.
Looking ahead to 2030, the market for defect engineering solutions in flexible electronics is projected to grow at a compound annual rate exceeding 12%, underpinned by the proliferation of foldable devices, smart textiles, and flexible medical sensors. As the ecosystem matures, the integration of real-time defect monitoring and adaptive process control will become standard practice, ensuring both high yields and robust device lifetimes.
Core Technologies in Defect Engineering for Flexible Electronics
Defect engineering has emerged as a pivotal discipline in the advancement of flexible electronics, enabling the fine-tuning of material properties to achieve high performance, reliability, and manufacturability. As of 2025, the field is witnessing rapid progress, driven by the integration of novel materials, advanced characterization techniques, and scalable manufacturing processes. The core technologies in defect engineering for flexible electronics are centered around the manipulation and control of structural, electronic, and interfacial defects in thin films, nanomaterials, and organic semiconductors.
One of the most significant developments is the use of two-dimensional (2D) materials, such as graphene and transition metal dichalcogenides (TMDs), where defect engineering is employed to modulate electrical conductivity, mechanical flexibility, and chemical stability. Companies like Samsung Electronics and LG Electronics are actively developing flexible displays and sensors that leverage defect-controlled 2D materials to enhance device performance and longevity. For instance, controlled introduction of vacancies and grain boundaries in TMDs has been shown to improve charge carrier mobility and stretchability, which are critical for foldable and rollable devices.
In the realm of organic electronics, defect passivation techniques—such as the incorporation of self-assembled monolayers and molecular dopants—are being refined to suppress trap states and improve charge transport. Konica Minolta and Merck KGaA are notable for their work in organic light-emitting diodes (OLEDs) and organic photovoltaics, where defect engineering at the molecular level is crucial for achieving high efficiency and operational stability in flexible formats.
Advanced in-situ and operando characterization tools, including transmission electron microscopy (TEM) and scanning probe microscopy, are now being integrated into production lines to monitor and control defect populations in real time. Equipment manufacturers such as JEOL Ltd. and Hitachi High-Tech Corporation are supplying the industry with state-of-the-art analytical instruments tailored for flexible substrates and nanomaterials.
Looking ahead, the next few years are expected to see the convergence of artificial intelligence (AI) and machine learning with defect engineering, enabling predictive modeling and automated defect detection during manufacturing. This is anticipated to accelerate the commercialization of flexible electronics in applications ranging from wearable health monitors to foldable smartphones and large-area flexible sensors. As industry leaders and material suppliers continue to invest in defect engineering, the sector is poised for significant breakthroughs in both device performance and production scalability.
Material Innovations: Polymers, Substrates, and Nanomaterials
Defect engineering has emerged as a pivotal strategy in advancing the performance and reliability of flexible electronics, particularly as the industry moves into 2025 and beyond. The manipulation and control of defects—intentional or otherwise—within polymers, substrates, and nanomaterials are enabling new functionalities and improved device lifespans, which are critical for applications ranging from wearable sensors to foldable displays.
In the realm of polymer substrates, companies such as DuPont and Kuraray are at the forefront of developing high-performance films with engineered defect densities. These materials are designed to balance flexibility with mechanical robustness, while minimizing the propagation of microcracks and pinholes that can compromise device integrity. For instance, recent product lines from DuPont incorporate advanced polyimide formulations with controlled cross-linking, reducing defect-related failures in flexible printed circuits.
Nanomaterials, particularly 2D materials like graphene and transition metal dichalcogenides (TMDs), are also benefiting from defect engineering. Companies such as Samsung Electronics and LG Electronics are investing in scalable synthesis methods that allow for the controlled introduction of vacancies, grain boundaries, and dopants. These engineered defects can tune electronic, optical, and mechanical properties, enabling higher mobility in thin-film transistors and improved stretchability in flexible displays. In 2024, Samsung Electronics announced advancements in defect-tolerant oxide semiconductors for their next-generation foldable devices, highlighting the commercial relevance of this approach.
On the substrate side, Toray Industries and Teijin Limited are developing ultra-clean PET and PEN films with minimized particulate and chemical defects, which are essential for high-yield manufacturing of flexible OLED and sensor arrays. These companies employ in-line defect inspection and real-time feedback systems to ensure substrate quality at scale.
Looking ahead, the outlook for defect engineering in flexible electronics is robust. Industry roadmaps suggest that by 2027, defect-tolerant materials will be standard in commercial flexible devices, with ongoing collaborations between material suppliers and device manufacturers to co-optimize processes. The integration of AI-driven defect detection and self-healing materials is also anticipated, as companies like BASF and Dow explore smart polymers capable of autonomously repairing micro-defects, further extending device lifetimes.
In summary, defect engineering is transitioning from a research focus to a manufacturing imperative, with leading material innovators and electronics manufacturers driving the adoption of defect-optimized polymers, substrates, and nanomaterials for the next generation of flexible electronics.
Process Control and Quality Assurance: Advanced Inspection and Metrology
Defect engineering is a cornerstone of process control and quality assurance in the rapidly evolving field of flexible electronics. As the industry moves into 2025, the demand for high-performance, reliable, and scalable flexible devices—such as foldable displays, wearable sensors, and flexible photovoltaics—has intensified the focus on advanced inspection and metrology techniques. The unique mechanical and material challenges of flexible substrates, including polymers and ultrathin glass, necessitate defect detection and control methods that go beyond those used in traditional rigid electronics.
Recent years have seen significant investments in in-line and real-time inspection systems tailored for roll-to-roll (R2R) and sheet-to-sheet (S2S) manufacturing processes. Companies like KLA Corporation and Hitachi High-Tech Corporation have developed advanced optical and electron-beam inspection tools capable of identifying sub-micron defects such as pinholes, cracks, and delamination in flexible substrates. These systems are increasingly integrated with machine learning algorithms to enable predictive analytics and automated process adjustments, reducing yield loss and improving throughput.
Metrology solutions are also evolving to address the specific needs of flexible electronics. For example, Carl Zeiss AG offers high-resolution microscopy and surface analysis tools that can characterize nanoscale features and surface roughness without damaging delicate films. Non-contact profilometry and 3D imaging are becoming standard for monitoring layer thickness uniformity and detecting embedded defects in multilayer flexible devices.
In 2025, the industry is witnessing a shift toward hybrid inspection platforms that combine multiple modalities—such as optical, X-ray, and infrared imaging—to capture a comprehensive defect profile. Onto Innovation Inc. and Thermo Fisher Scientific Inc. are among the companies advancing these integrated solutions, which are critical for ensuring the reliability of next-generation flexible electronics in applications ranging from medical devices to automotive interiors.
Looking ahead, the next few years are expected to bring further automation and AI-driven analytics into defect engineering workflows. The integration of digital twins and real-time feedback loops will enable manufacturers to not only detect but also predict and prevent defect formation during production. As flexible electronics continue to scale, robust process control and quality assurance—anchored by advanced inspection and metrology—will remain essential for meeting the stringent reliability and performance standards demanded by end users and regulatory bodies.
Key Applications: Wearables, Flexible Displays, Sensors, and Medical Devices
Defect engineering has emerged as a pivotal strategy in advancing flexible electronics, particularly in key application areas such as wearables, flexible displays, sensors, and medical devices. As the industry moves into 2025, the focus on controlling and manipulating defects at the atomic and molecular levels is enabling significant improvements in device performance, reliability, and manufacturability.
In the wearables sector, companies are leveraging defect engineering to enhance the mechanical flexibility and electrical conductivity of materials like graphene, organic semiconductors, and metal oxides. For instance, Samsung Electronics and LG Electronics are actively developing flexible and stretchable substrates for next-generation smartwatches and fitness bands. By precisely controlling defect densities in thin-film transistors (TFTs) and transparent electrodes, these manufacturers are achieving higher device lifespans and improved signal integrity, which are critical for continuous health monitoring and biometric sensing.
Flexible displays represent another major application, with defect engineering playing a crucial role in yield improvement and display uniformity. BOE Technology Group, a global leader in display manufacturing, has reported advances in defect passivation techniques for organic light-emitting diode (OLED) and quantum dot displays. These methods reduce pixel failure rates and enhance color consistency, supporting the mass production of foldable smartphones and rollable tablets. Similarly, TCL Technology is investing in defect-tolerant architectures to enable ultra-thin, bendable screens for consumer electronics.
In the field of flexible sensors, defect engineering is being used to tailor the sensitivity and selectivity of devices for applications ranging from environmental monitoring to human-machine interfaces. Companies such as DuPont are developing advanced conductive inks and films with engineered defect sites, which facilitate tunable electrical and chemical responses. This approach is particularly valuable for e-skin patches and flexible biosensors, where precise control over defect structures can lead to enhanced detection of physiological signals or environmental analytes.
Medical devices are also benefiting from defect engineering, especially in implantable and wearable diagnostics. Medtronic and Boston Scientific are exploring flexible substrates with engineered defect profiles to improve biocompatibility and device integration with soft tissues. These innovations are expected to accelerate the adoption of flexible electronics in continuous glucose monitors, neural interfaces, and smart bandages over the next few years.
Looking ahead, the integration of defect engineering with scalable manufacturing processes remains a key challenge and opportunity. As leading companies continue to refine defect control at the nanoscale, the next wave of flexible electronic products is poised to deliver unprecedented performance, durability, and new form factors across consumer, industrial, and healthcare markets.
Competitive Landscape: Leading Companies and Strategic Partnerships
The competitive landscape for defect engineering in flexible electronics is rapidly evolving as major industry players and emerging innovators intensify their focus on material quality, device reliability, and scalable manufacturing. As of 2025, the sector is characterized by a blend of established electronics giants, specialized materials companies, and collaborative consortia, all seeking to address the unique challenges posed by defects in flexible substrates and devices.
Among the global leaders, Samsung Electronics continues to set benchmarks in flexible display technology, leveraging advanced defect detection and mitigation strategies in its OLED and foldable device lines. The company’s investments in in-line inspection systems and proprietary defect passivation techniques have enabled mass production of flexible displays with improved yield and durability. Similarly, LG Electronics remains at the forefront, with its OLED division pioneering new encapsulation and self-healing material systems to minimize defect propagation in flexible panels.
On the materials front, DuPont and Kuraray are notable for their development of high-performance polymer substrates and barrier films, which are critical for reducing defect density and enhancing device longevity. Both companies have announced ongoing collaborations with device manufacturers to tailor material properties for next-generation flexible electronics, focusing on defect tolerance and mechanical resilience.
In the semiconductor and inspection equipment domain, Applied Materials and Lam Research are advancing process control solutions specifically adapted for flexible and stretchable electronics manufacturing. Their recent product lines incorporate AI-driven defect classification and real-time monitoring, which are increasingly adopted by fabs aiming to scale up flexible device production while maintaining stringent quality standards.
Strategic partnerships are a defining feature of the current landscape. For example, Samsung Electronics and DuPont have engaged in joint development agreements to co-engineer flexible display materials with enhanced defect resistance. Industry consortia such as the SEMI FlexTech Alliance are also facilitating pre-competitive research, bringing together stakeholders from across the value chain to address common defect engineering challenges through shared roadmaps and pilot projects.
Looking ahead, the next few years are expected to see intensified collaboration between device makers, material suppliers, and equipment vendors, with a focus on integrating defect engineering at every stage of the flexible electronics lifecycle. As flexible devices move into broader applications—wearables, automotive interiors, and medical sensors—the ability to control and mitigate defects will remain a key differentiator for leading companies in this dynamic sector.
Regulatory Standards and Industry Initiatives (e.g., ieee.org, sema.org)
Defect engineering has emerged as a critical focus in the development and commercialization of flexible electronics, with regulatory standards and industry initiatives playing a pivotal role in shaping the landscape as of 2025. The rapid adoption of flexible displays, wearable sensors, and conformable medical devices has intensified the need for robust frameworks to ensure device reliability, safety, and performance, particularly as these products enter mass markets.
Key industry bodies such as the IEEE and the SEMI have been instrumental in establishing guidelines and standards that address defect detection, classification, and mitigation in flexible electronic materials and devices. The IEEE, through its Standards Association, has expanded its portfolio to include working groups focused on flexible and printed electronics, with ongoing efforts to standardize test methods for mechanical durability, electrical performance under strain, and defect tolerance. These standards are increasingly referenced by manufacturers and suppliers to harmonize quality benchmarks across the supply chain.
In parallel, SEMI has updated its suite of standards to encompass flexible substrates and roll-to-roll manufacturing processes, which are particularly susceptible to unique defect modes such as microcracks, delamination, and particulate contamination. SEMI’s collaborative task forces, comprising leading material suppliers, equipment manufacturers, and device integrators, have prioritized the development of protocols for in-line defect inspection and real-time process control, aiming to reduce yield losses and improve device lifetimes.
Industry consortia and alliances, such as the FlexTech Alliance, continue to drive pre-competitive research and pilot programs that address defect engineering challenges. These initiatives often result in best practice documents and roadmaps that inform both regulatory development and commercial strategies. For example, recent FlexTech projects have demonstrated the integration of advanced metrology tools for sub-micron defect detection in organic and hybrid electronic layers, a capability now being adopted by major display and sensor manufacturers.
Looking ahead, the next few years are expected to see further convergence between regulatory standards and industry-driven innovation. The anticipated introduction of new IEEE and SEMI standards specific to emerging materials—such as stretchable conductors and self-healing polymers—will likely accelerate the qualification of next-generation flexible electronics for medical, automotive, and consumer applications. As regulatory frameworks mature, collaboration between industry leaders and standards organizations will remain essential to address evolving defect engineering requirements and to ensure the safe, reliable deployment of flexible electronic technologies worldwide.
Challenges: Yield, Scalability, and Reliability in Mass Production
Defect engineering is central to the advancement of flexible electronics, particularly as the industry moves toward mass production in 2025 and beyond. The unique mechanical demands of flexible substrates—such as bending, stretching, and folding—introduce new defect modes not typically encountered in rigid electronics. These include microcracks, delamination, and interface instabilities, all of which can significantly impact device yield, scalability, and long-term reliability.
One of the primary challenges in scaling up production is maintaining high yield rates while minimizing the occurrence of critical defects. For example, roll-to-roll (R2R) manufacturing, a leading technique for large-area flexible electronics, is highly sensitive to particulate contamination and substrate uniformity. Even minor defects can propagate during processing, leading to substantial yield losses. Companies such as Kateeva and Samsung Electronics have invested in advanced in-line inspection and defect mapping systems to identify and mitigate these issues in real time, aiming to push yields closer to those seen in traditional silicon-based manufacturing.
Scalability is further complicated by the diversity of materials used in flexible electronics, including organic semiconductors, metal nanowires, and 2D materials like graphene. Each material system presents unique defect landscapes. For instance, LG Display has reported on the challenges of scaling up OLED-based flexible displays, where pinhole defects and moisture ingress can drastically reduce device lifetimes. To address this, companies are developing multilayer encapsulation techniques and self-healing materials that can localize and repair damage, thereby improving scalability and reliability.
Reliability remains a critical concern, especially for applications in wearables, medical devices, and foldable smartphones. Mechanical cycling and environmental exposure can exacerbate defect formation over time. BOE Technology Group, a major supplier of flexible displays, has focused on developing robust barrier layers and flexible electrodes to enhance device longevity. Additionally, industry consortia such as the SEMI organization are working to standardize reliability testing protocols for flexible electronics, which is expected to accelerate qualification and adoption in high-reliability markets.
Looking ahead, the next few years will likely see increased collaboration between material suppliers, equipment manufacturers, and device integrators to develop defect-tolerant architectures and predictive analytics for process control. The integration of AI-driven inspection systems and real-time feedback loops is anticipated to further improve yield and reliability, paving the way for broader commercialization of flexible electronic products.
Future Outlook: Emerging Opportunities and R&D Directions Through 2030
Defect engineering is poised to play a transformative role in the evolution of flexible electronics through 2030, as the industry seeks to balance mechanical flexibility with high electronic performance. In 2025, the sector is witnessing a surge in R&D investments aimed at controlling and exploiting defects in materials such as organic semiconductors, metal oxides, and two-dimensional (2D) materials. These efforts are driven by the need to enhance device reliability, stretchability, and energy efficiency for applications ranging from wearable health monitors to foldable displays.
Major material suppliers and device manufacturers are intensifying collaborations with academic and government research centers to accelerate defect engineering breakthroughs. For instance, Samsung Electronics and LG Electronics are actively developing flexible OLED and quantum dot displays, where defect passivation and interface engineering are critical to achieving high yields and long-term stability. Similarly, Toray Industries and Kuraray are advancing polymer substrates and encapsulation materials with tailored defect profiles to improve mechanical endurance and barrier properties.
Emerging opportunities are also evident in the field of 2D materials, such as graphene and transition metal dichalcogenides (TMDs). Companies like Versarien and Graphenea are scaling up production of high-quality graphene, with a focus on minimizing grain boundaries and point defects that can degrade electronic mobility. These materials are expected to underpin next-generation flexible transistors and sensors, with defect engineering enabling tunable electronic and optical properties.
Looking ahead, the integration of artificial intelligence (AI) and machine learning in defect detection and process optimization is anticipated to accelerate. Automated inspection systems, being developed by equipment leaders such as Applied Materials, are expected to provide real-time feedback during roll-to-roll manufacturing, reducing defect densities and improving device uniformity. Furthermore, industry consortia and standards bodies, including SEMI, are working to establish guidelines for defect characterization and reliability testing specific to flexible electronics.
By 2030, the convergence of advanced defect engineering, scalable manufacturing, and smart inspection technologies is projected to unlock new markets for flexible electronics, including biomedical implants, conformable photovoltaics, and smart packaging. The sector’s outlook remains robust, with ongoing R&D expected to yield materials and devices that combine unprecedented flexibility, durability, and performance.
Sources & References
- LG Electronics
- DuPont
- Kuraray
- Konica Minolta
- JEOL Ltd.
- Hitachi High-Tech Corporation
- Teijin Limited
- BASF
- KLA Corporation
- Hitachi High-Tech Corporation
- Carl Zeiss AG
- Onto Innovation Inc.
- Thermo Fisher Scientific Inc.
- BOE Technology Group
- Medtronic
- Boston Scientific
- IEEE
- Kateeva
- LG Display
- Versarien