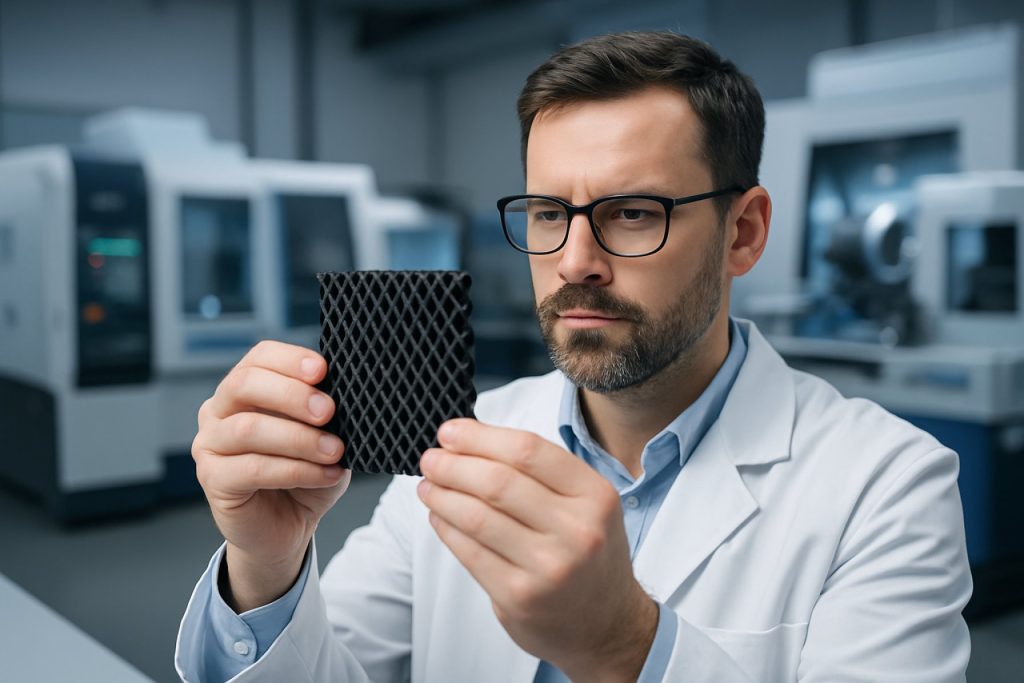
Auxetic Polymer Manufacturing in 2025: Why This Game-Changing Material Is Set To Disrupt High-Tech Industries. Discover Market Forecasts, Breakthroughs, and Investment Opportunities.
- Executive Summary: Auxetic Polymers and Their 2025 Market Trajectory
- Defining Auxetic Polymers: Unique Properties and Industrial Significance
- Key Manufacturers & Industry Stakeholders (e.g., auxetics.co.uk, teijin.com, evonik.com)
- Current State of Auxetic Polymer Manufacturing Technologies
- Emerging Production Methods and Scalability Challenges
- Industry Applications: Aerospace, Medical Devices, Sports, and Beyond
- Global Market Size, 2025 Forecasts, and Growth Drivers
- Competitive Landscape and Strategic Partnerships
- Regulatory and Environmental Considerations
- Future Outlook: Innovation Pipelines and Market Opportunities to 2029
- Sources & References
Executive Summary: Auxetic Polymers and Their 2025 Market Trajectory
Auxetic polymer manufacturing is emerging as a transformative segment within advanced materials, characterized by polymers that exhibit a negative Poisson’s ratio—expanding perpendicular to applied force. As of 2025, the manufacturing landscape is shaped by rapid advancements in process optimization and scalability, driven by demand from high-performance sectors such as aerospace, automotive, medical devices, and sports equipment.
Key events in 2024-2025 include increased investment in scalable additive manufacturing and extrusion techniques, allowing for the reliable production of auxetic polymer foams, films, and fibers. Notably, Arkema, a global specialty chemicals leader, has intensified its research and collaboration efforts around advanced polyamide and polyurethane systems, targeting auxetic structures for flexible electronics and impact-resistant components. SABIC has also begun exploring thermoplastic composites with tunable auxetic properties, focusing on lightweighting and energy absorption for transportation and safety applications.
A major manufacturing milestone has been the refinement of 3D printing methods—specifically selective laser sintering (SLS) and fused deposition modeling (FDM)—to produce custom-designed auxetic lattices with precise control over geometry and mechanical response. Companies such as Evonik Industries have expanded their portfolio of high-performance polymers suitable for these advanced fabrication methods, aiming to meet growing customer requirements in prototyping and small-batch production.
Recent collaborations between material suppliers and end-users are accelerating the transition from laboratory-scale demonstration to commercial-scale implementation. For example, Covestro has partnered with leading sports brands to develop auxetic polyurethane foams for next-generation protective gear, leveraging their expertise in scalable foam manufacturing and polymer chemistry.
Looking ahead through 2025 and into the next few years, the outlook for auxetic polymer manufacturing is robust. Industry leaders are expected to invest further in digital design tools and automation to streamline production, reduce costs, and enable mass customization. Standardization efforts are also underway, with industry bodies working to codify best practices and performance benchmarks for auxetic polymers, which will further facilitate adoption in regulated sectors such as medical devices and aerospace.
Overall, the momentum within auxetic polymer manufacturing is set to accelerate, underpinned by technological innovation, strategic partnerships, and growing end-user demand for materials with superior toughness, flexibility, and multifunctionality.
Defining Auxetic Polymers: Unique Properties and Industrial Significance
Auxetic polymers are a class of materials distinguished by their negative Poisson’s ratio, meaning they become thicker perpendicular to an applied stretch rather than thinner. This counterintuitive mechanical behavior is typically achieved through engineered molecular structures or by carefully designing the polymer’s microstructure. Historically, auxetic effects were observed in foams and some crystalline materials, but recent advances in polymer chemistry and processing have enabled the fabrication of auxetic polymers with tunable and reliable properties.
The unique properties of auxetic polymers include enhanced energy absorption, improved fracture resistance, and superior indentation resilience. These attributes make them particularly attractive for a range of industrial sectors. For instance, in protective equipment, auxetic polymers can dissipate impact forces more efficiently than conventional materials. In filtration and biomedical devices, their ability to expand laterally under tension can be harnessed for adaptive porosity and enhanced functionality.
Industrial significance is further underlined by increasing efforts from material suppliers and manufacturers to commercialize auxetic polymer solutions. Recognized polymer producers such as Dow and BASF have active research initiatives focusing on functional polymers and advanced composites, which include auxetic architectures. In Asia, SABIC is exploring advanced polymer processing routes, including those relevant to auxetic materials for automotive and electronics applications. These companies emphasize the integration of auxetic properties into thermoplastics, thermosets, and elastomeric matrices to enhance performance in demanding environments.
In 2025, the industrial landscape for auxetic polymer manufacturing is marked by a transition from laboratory-scale demonstrations to scalable production. Techniques such as melt extrusion, 3D printing, and additive manufacturing are being refined to produce consistent auxetic structures at commercial volumes. For example, Evonik Industries is actively developing specialized polymer powders and filaments suitable for additive manufacturing of auxetic components, targeting sectors such as sports gear and medical devices.
Looking ahead, the next several years are expected to witness increased adoption of auxetic polymers in safety equipment, flexible electronics, and smart textiles. As companies expand their manufacturing capabilities, the unique mechanical and functional advantages of auxetic polymers are poised to drive innovation and differentiation across multiple industries. Collaboration between material suppliers, end-use manufacturers, and research institutions is likely to accelerate the commercialization and mainstream use of auxetic polymers in the near future.
Key Manufacturers & Industry Stakeholders (e.g., auxetics.co.uk, teijin.com, evonik.com)
The landscape of auxetic polymer manufacturing is witnessing significant activity as of 2025, with a select group of companies and stakeholders driving innovation and scale-up. Auxetic materials, characterized by their negative Poisson’s ratio—expanding perpendicular to applied force—are increasingly targeted for advanced applications in defense, medical, sports, and automotive sectors, fueling industry interest and investment.
Among the most prominent early movers is Auxetix Ltd, a UK-based specialist focusing exclusively on the development and manufacturing of auxetic materials and fibers. Auxetix Ltd’s patented spinning processes for auxetic yarns and films have positioned it as a key supplier for specialized applications, including protective gear and medical textiles. The company maintains collaborations with industrial partners and is scaling up production in response to growing demand from European and Asian customers.
In the broader polymer and chemical sector, Teijin Limited—a global conglomerate with expertise in high-performance fibers and polymers—is actively exploring auxetic formulations as part of its advanced materials portfolio. Teijin’s ongoing R&D leverages its deep experience with aramid and polyethylene fibers to optimize the mechanical properties of auxetic polymers, aiming for enhanced impact resistance and energy absorption. Though commercial-scale auxetic products are still emerging, Teijin’s commitment to this segment is underscored by participation in cross-industry consortiums and dedicated innovation programs.
Similarly, Evonik Industries AG, a major German specialty chemicals group, has incorporated auxetic polymer research into its broader strategy for next-generation materials. Evonik’s expertise in polyamide and polyurethane chemistry, alongside its global production capabilities, positions the company to potentially scale up auxetic polymer manufacturing as market-ready applications multiply. Their collaborations with academic and industrial partners aim to accelerate the translation of laboratory-scale auxetic effects into commercially viable products.
Other important stakeholders include polymer processing equipment suppliers and advanced materials research institutes, which provide technological infrastructure and validation. In China and South Korea, several high-tech materials companies (often operating under larger chemical or textile conglomerates) are reportedly investing in pilot-scale auxetic fiber lines, though few have publicized their brands or production capacities.
Looking to the next few years, the auxetic polymer manufacturing sector is expected to transition from pilot-scale to pre-commercial and early commercial production, especially as end-user industries validate new use-cases. Key challenges remain in process scalability, cost reduction, and integration into existing manufacturing lines. However, with ongoing investment from established players like Teijin and Evonik, as well as specialized firms such as Auxetix Ltd, the industry outlook for 2025 and beyond is marked by cautious optimism and a steady pace of technical advancement.
Current State of Auxetic Polymer Manufacturing Technologies
Auxetic polymers—materials exhibiting a negative Poisson’s ratio—have advanced from laboratory curiosities to emerging industrial candidates, owing to their unique mechanical properties such as enhanced energy absorption and fracture resistance. As of 2025, manufacturing technologies for auxetic polymers are rapidly evolving, driven by both academic research and increasing interest from industry sectors including medical devices, protective equipment, and flexible electronics.
The most established manufacturing routes for auxetic polymers involve both direct synthesis approaches and post-processing of conventional polymers. Direct synthesis typically employs molecular design, as seen in the development of auxetic polyurethane foams and thermoplastic elastomers. This method enables fine control over the polymer’s microstructure, but scaling up for industrial production remains challenging due to process complexity and cost.
A widely adopted method is the thermomechanical processing of conventional foams, where polymers like polyurethane are subjected to a controlled compression and heating cycle. This technique is currently used on a commercial scale by several foam specialists, such as Recticel, a leading European polyurethane foam manufacturer, which has explored auxetic structures for advanced protective applications. These methods allow for the retrofit of existing production lines, facilitating incremental entry into the auxetic market.
Additive manufacturing (AM), particularly 3D printing, has emerged as a transformative technology for producing auxetic polymer structures with intricate geometries. Companies such as Stratasys and 3D Systems, major players in the polymer AM space, have demonstrated the feasibility of printing auxetic lattice structures using flexible filaments and photopolymer resins. The precision of AM enables the customization of auxetic architectures for specific applications, though throughput and material compatibility remain areas for development.
Material suppliers are also beginning to offer polymer grades optimized for auxetic processing. For instance, BASF and Evonik, two prominent chemical companies, have portfolios of thermoplastic polyurethanes and polyamides that are being tailored through molecular engineering and compounding for enhanced auxetic behavior. Collaboration between chemical manufacturers and end-users is expected to accelerate the commercialization of new auxetic polymer formulations over the next several years.
Looking forward, the sector’s outlook is underpinned by continuous innovation in fabrication techniques, including roll-to-roll processing for thin films and hybrid approaches that combine molecular design with advanced manufacturing. As prototype-to-production pathways mature and as regulatory approvals for medical and protective products are secured, the adoption of auxetic polymers is projected to increase through 2027, with broader integration into high-performance and consumer applications.
Emerging Production Methods and Scalability Challenges
Auxetic polymer manufacturing is advancing rapidly in 2025, driven by the promise of applications in protective equipment, biomedical devices, and flexible electronics. However, transitioning from laboratory-scale prototypes to scalable, commercially viable production remains a significant hurdle. The sector is characterized by ongoing experimentation with both established and novel manufacturing methods, as well as a growing focus on cost-efficiency and reproducibility.
Traditionally, auxetic polymers have been fabricated using techniques such as extrusion, injection molding, and thermomechanical processing. Recently, additive manufacturing—especially 3D printing—has gained momentum due to its ability to precisely control internal architectures responsible for the auxetic effect. Companies like Evonik Industries and BASF have invested in advanced polymer formulations compatible with 3D printing, targeting specialty markets that require customizable mechanical properties. These investments aim to address both the microstructural design and scalability, ensuring consistent auxetic behavior across larger volumes of material.
Emerging methods in 2025 focus on process automation and in-line quality assurance. For example, continuous roll-to-roll processing of auxetic films is under investigation by leading technical polymer suppliers, including DuPont, to enable higher throughput and reduce per-unit costs. Such methods are essential for applications in sports equipment and medical padding, where sheet or film formats are preferred. Meanwhile, companies such as Covestro are exploring solvent-free manufacturing and bio-based feedstocks to improve sustainability alongside scalability—an increasingly important factor in global supply chains.
Despite these advances, challenges persist. Achieving uniform auxetic structure over large areas or volumes is technically demanding, as microstructural inconsistencies can compromise performance. Moreover, upscaling from bespoke, small-batch production to industrial volumes often necessitates re-engineering of both materials and equipment. Leading firms are collaborating with research institutions and machine manufacturers to develop dedicated tooling for high-precision patterning and multi-material integration.
Looking ahead, the next few years are expected to see further convergence of digital design, materials science, and automated manufacturing. Industry consortia and standards bodies are beginning to address the lack of unified quality metrics for auxetic polymers, which is anticipated to accelerate adoption in regulated sectors such as medical and automotive. As industrial partners like SABIC and DSM continue to scale up pilot lines, the industry outlook is increasingly optimistic for overcoming current scalability barriers and unlocking new commercial opportunities.
Industry Applications: Aerospace, Medical Devices, Sports, and Beyond
Auxetic polymer manufacturing is emerging as a transformative force across high-performance industries, including aerospace, medical devices, and sports equipment, with 2025 marking a pivotal year in commercial scalability and adoption. Auxetic materials, characterized by their negative Poisson’s ratio, display the unique ability to become thicker perpendicular to applied force, imparting remarkable energy absorption, fracture resistance, and tailored mechanical properties.
In the aerospace sector, manufacturers are increasingly exploring auxetic polymers for lightweight, impact-resistant components. The European aerospace giant Airbus has publicized ongoing research collaborations focused on integrating auxetic structures into aircraft panels and seating to enhance crashworthiness and vibration damping. Similarly, auxiliary suppliers such as Safran are investigating auxetic foams for advanced cabin interiors and noise attenuation, with pilot projects expected to move toward certification phases within the next two years.
Medical device innovation is accelerating through partnerships between polymer manufacturers and healthcare providers. Companies such as Carl Zeiss Meditec are evaluating auxetic polymer scaffolds for next-generation stents and prosthetics, leveraging the materials’ conformability and improved biomechanical compatibility. In orthopedic implants and surgical meshes, the adaptability and shock-dissipating qualities of auxetic polymers are anticipated to reduce complications and improve patient outcomes, with early-stage clinical trials underway in Europe and North America.
The sports equipment sector is another early adopter. Brands like Adidas and Nike have made public their investments in auxetic-based midsoles and protective gear, aiming for enhanced cushioning and injury prevention. Auxetic foams and fabrics are being integrated into running shoes, helmets, and body armor, with commercial launches scheduled for the 2025-2026 product cycles.
Beyond these primary industries, auxetic manufacturing is gaining traction in civil engineering for vibration-damping concrete reinforcements and in flexible electronics, where companies such as Samsung Electronics are investigating stretchable displays and wearable sensors. The outlook for 2025 and beyond is one of diversification, as advancements in additive manufacturing and polymer processing—championed by suppliers like BASF—enable scalable, cost-effective auxetic component production.
With technical milestones being reached in both material science and process engineering, auxetic polymer manufacturing is poised to transition from niche applications to broader industrial adoption, driven by collaborative efforts among OEMs, material innovators, and end-users.
Global Market Size, 2025 Forecasts, and Growth Drivers
The global market for auxetic polymer manufacturing is poised for notable growth heading into 2025 and the following several years, propelled by advances in materials science, expanding application fields, and increased industry investment. Auxetic polymers—materials that exhibit a negative Poisson’s ratio and become thicker perpendicular to applied force—are gaining traction in industries such as medical devices, sports equipment, automotive, aerospace, and advanced protective gear.
While precise market size figures for auxetic polymers remain limited due to their emerging status, sector momentum is evidenced by expanding R&D and commercialization activities from leading chemical and materials manufacturers. Companies such as BASF and Covestro have documented ongoing research into advanced polymer structures, including auxetic foams and films, with pilot-scale production and collaborations with academic institutions. Dow has highlighted the potential of novel polymer architectures for next-generation flexible and impact-resistant materials, aligning with auxetic design principles.
Growth in the market is being driven by several factors:
- Technological Innovation: Improvements in additive manufacturing (3D printing), extrusion, and polymer processing have enabled scalable and reproducible auxetic structures. Companies like Evonik Industries are investing in advanced fabrication methods to meet commercial demands for customized auxetic components.
- Expanding Applications: Auxetic polymers are increasingly adopted in filtration membranes, wearable sensors, cushioning foams, and lightweight composites, offering superior mechanical resilience and energy absorption.
- Regulatory and Safety Standards: Enhanced focus on workplace and consumer safety is boosting adoption in protective equipment, with materials suppliers working alongside standards bodies to validate performance metrics.
- Sustainability Initiatives: The shift toward recyclable and bio-based polymers is opening opportunities for auxetic materials in sustainable product design, as evidenced by development programs at SABIC and Solvay.
The outlook for 2025 and beyond suggests a robust compound annual growth rate as commercialization accelerates. Strategic partnerships between polymer manufacturers, end-user industries, and research consortia are expected to shorten time-to-market for novel auxetic products. With ongoing investment and the resolution of scale-up challenges, auxetic polymer manufacturing is transitioning from a niche research domain to a dynamic segment of the advanced materials industry.
Competitive Landscape and Strategic Partnerships
The competitive landscape of auxetic polymer manufacturing in 2025 is characterized by a dynamic interplay among established chemical conglomerates, specialized advanced materials firms, and emerging startups. The sector is witnessing significant momentum, driven by advances in additive manufacturing, increased demand from high-performance industries, and strategic collaborations aimed at accelerating commercialization.
Major global players with established polymer portfolios are actively exploring auxetic materials. BASF and Dow, for example, are leveraging their expertise in polymer synthesis and processing to investigate scalable auxetic solutions, particularly for automotive, sports, and packaging applications. Both companies have expanded research collaborations with academic institutions and are participating in industry consortia focused on advanced polymeric materials. Their strategic alliances are designed to bridge the gap between laboratory-scale innovation and high-volume manufacturing.
Specialty materials companies are also becoming increasingly prominent in the auxetic polymer space. Evonik Industries, with its focus on high-performance polymers, has announced investments into the development of auxetic foams and films for protective equipment and filtration. Similarly, Arkema is leveraging its expertise in specialty chemicals and advanced composites to partner with equipment manufacturers and application developers, aiming to tailor auxetic polymer properties for aerospace and medical uses.
Startups and spin-offs from academic research are playing a pivotal role by introducing innovative manufacturing techniques such as 3D printing and microstructural engineering. These companies are frequently entering into licensing agreements or joint ventures with larger players to gain access to capital and production infrastructure. Notably, several have secured pilot production contracts with major sportswear brands and consumer electronics firms.
Strategic partnerships are a defining trend in 2025. Collaborative efforts are taking shape in the form of joint research projects, co-development agreements, and public-private initiatives. For instance, materials manufacturers are working closely with automotive OEMs and medical device companies to design application-specific auxetic components, backed by shared intellectual property arrangements. These alliances are expected to accelerate the path to market for novel auxetic polymer products and to foster standardization across the industry.
Looking ahead, the competitive landscape is likely to intensify over the next few years as proprietary manufacturing processes mature and as end-user industries validate the performance and cost-effectiveness of auxetic polymers. The sector’s evolution will depend heavily on the ability of manufacturers to scale production, ensure material consistency, and respond swiftly to bespoke application demands.
Regulatory and Environmental Considerations
Regulatory and environmental considerations are becoming increasingly significant for auxetic polymer manufacturing as the sector moves into 2025 and beyond. As auxetic materials—polymers that exhibit a negative Poisson’s ratio and unusual mechanical properties—transition from laboratories to industrial-scale production, manufacturers must align with evolving standards for chemical safety, waste management, and sustainability.
In the European Union, the regulatory landscape is primarily guided by the REACH Regulation, which governs the Registration, Evaluation, Authorisation and Restriction of Chemicals. Auxetic polymer manufacturers working with novel chemical formulations must ensure compliance with REACH, which requires comprehensive data on chemical safety, responsible usage, and environmental impact. Additionally, the EU’s increasingly stringent environmental directives, such as the Circular Economy Action Plan, are pushing manufacturers to design auxetic polymers with recyclability and minimal environmental footprint in mind. Major European chemical conglomerates with active polymer divisions, including BASF and Evonik Industries, are leading efforts to integrate sustainable practices and are deeply involved in the development of next-generation, eco-friendly polymers.
In the United States, the Environmental Protection Agency (EPA) continues to update its Toxic Substances Control Act (TSCA) inventory and review processes, impacting the approval and monitoring of new polymer materials. U.S.-based companies with significant polymer R&D portfolios such as Dow and DuPont are engaging with regulators to ensure that new auxetic products meet all federal requirements regarding chemical safety, emissions, and lifecycle assessments.
On a global scale, the International Organization for Standardization (ISO) is developing and refining standards relevant to advanced functional polymers, including those with auxetic properties. These standards are expected to influence manufacturing and testing protocols, particularly in industries such as medical devices, aerospace, and automotive, where auxetic polymers are gaining interest due to their enhanced mechanical resilience and shock absorption.
From an environmental perspective, the challenge for the next few years will be to scale up auxetic polymer production without increasing the sector’s carbon footprint or generating persistent microplastics. Companies are investing in bio-based feedstocks and closed-loop manufacturing techniques. For example, Borealis and others are publicly committing to circular solutions for specialty polymers, a trend expected to shape the auxetic segment as well.
In summary, as regulatory frameworks tighten and environmental scrutiny intensifies through 2025 and beyond, auxetic polymer manufacturers are compelled to innovate not only in material properties but also in sustainable and compliant production methods.
Future Outlook: Innovation Pipelines and Market Opportunities to 2029
Auxetic polymer manufacturing is poised for notable advances through 2025 and into the latter part of the decade, driven by intensifying R&D activity and nascent commercialization efforts from prominent chemical and advanced materials companies. Auxetic polymers—materials that exhibit a negative Poisson’s ratio, becoming thicker perpendicular to applied force—promise disruptive applications in protective equipment, medical devices, flexible electronics, and filtration systems. The next few years are characterized by a transition from laboratory-scale innovation to early-stage industrial scaling, with several industry leaders and consortia accelerating productization efforts.
A key area of focus is scalable additive manufacturing (AM) and extrusion techniques that can precisely control microstructures necessary for auxetic behavior. Companies such as Evonik Industries AG and BASF SE are expanding their portfolios of thermoplastic elastomers and polyurethanes, with ongoing research into formulations that can be extruded or 3D-printed with auxetic geometries. Both organizations maintain dedicated innovation pipelines in advanced polymers, seeking to address technical barriers such as reproducibility, cost-effective manufacturing, and integration with existing composite systems.
Industry consortia, including members of PlasticsEurope, are fostering collaborations across the supply chain to standardize test methods and accelerate regulatory acceptance for auxetic materials in safety-critical applications. Notably, the European automotive and aerospace sectors are evaluating prototype auxetic polymer components for impact-resistant panels and energy-absorbing structures, with pilot projects expected to deliver validation data by 2026.
Medical device manufacturers, such as Smith+Nephew, are also exploring auxetic foams and membranes for wound care and orthopedic devices, leveraging improved conformability and cushioning. Early-stage commercialization of auxetic wound dressings and sports padding is anticipated as process reliability improves and suppliers scale up. Additionally, filtration and separation system specialists, including Merck KGaA, are investigating auxetic polymer membranes to enhance selectivity and anti-fouling properties, a trend expected to gain momentum through 2027.
Looking ahead to 2029, the outlook for auxetic polymer manufacturing is optimistic, predicated on sustained investment in process innovation, further demonstration of superior end-use performance, and growing demand across medical, industrial, and protective markets. The maturation of scalable manufacturing protocols, coupled with the entry of global suppliers and OEMs, is likely to transform auxetic polymers from niche materials into widely adopted solutions for next-generation product design.
Sources & References
- Arkema
- Evonik Industries
- Covestro
- BASF
- Teijin Limited
- Recticel
- Stratasys
- 3D Systems
- BASF
- Evonik
- DuPont
- DSM
- Airbus
- Carl Zeiss Meditec
- Nike
- Borealis
- PlasticsEurope
- Smith+Nephew