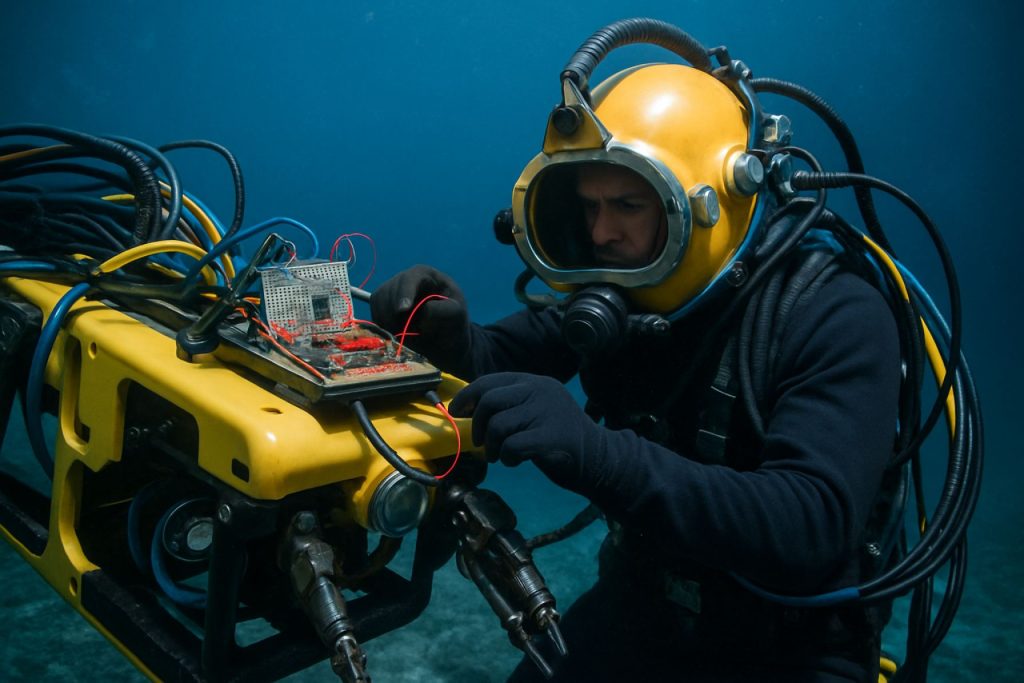
Table of Contents
- Executive Summary: The Rise of Jury-Rigged Subsea Robotics
- Market Overview & 2025–2030 Growth Forecast
- Core Drivers: Cost, Agility, and Innovation Pressures
- Emerging DIY Fabrication Techniques and Toolkits
- Key Players and Noteworthy Projects (2025 Spotlight)
- Risks, Regulatory Gaps, and Safety Challenges
- Case Studies: Successes and Failures in Jury-Rigged Deployments
- Materials, Components, and Open-Source Hardware Trends
- Investment, Collaboration, and Industry Response
- Future Outlook: How Jury-Rigging Could Redefine Subsea Robotics by 2030
- Sources & References
Executive Summary: The Rise of Jury-Rigged Subsea Robotics
The landscape of subsea robotics fabrication is undergoing a marked transformation in 2025, characterized by the proliferation of “jury-rigged” or improvised robotic solutions. As offshore energy operations, marine research, and underwater infrastructure projects expand globally, there is a growing emphasis on rapid, adaptable, and cost-effective robotics fabrication. Traditional subsea robotics manufacturers, such as Saab and Oceaneering International, have historically dominated the field, delivering highly engineered, reliable Remotely Operated Vehicles (ROVs) and Autonomous Underwater Vehicles (AUVs). However, recent supply chain disruptions, budget constraints, and urgent operational needs have driven operators and smaller manufacturers to devise makeshift robotic solutions using off-the-shelf components, 3D-printed parts, and repurposed electronics.
Key events in 2025 highlight this shift. In the wake of critical component shortages, several offshore operators have documented successful missions using customized ROVs assembled from modular parts sourced from suppliers such as Blue Robotics and Teledyne Marine. These jury-rigged systems, though lacking the refined engineering of legacy platforms, have demonstrated surprising resilience and adaptability in tasks ranging from subsea inspection to emergency pipeline interventions. According to data released by Subsea UK, there has been a 30% increase in reported deployments of non-standard or custom-fabricated subsea vehicles over the past 18 months, underscoring the accelerating trend towards flexible fabrication approaches.
The outlook for the next few years suggests continued momentum in this direction. The democratization of fabrication technologies—particularly additive manufacturing and open-source hardware—enables smaller players and even research groups to develop bespoke robotics platforms tailored to specific operational challenges. Organizations like OpenROV have played a role in proliferating accessible, modifiable vehicle designs, further lowering entry barriers. Simultaneously, major industry actors are responding by introducing more modular, user-serviceable systems, as seen in the latest product lines from Saab and Oceaneering International.
While concerns remain regarding regulatory compliance, reliability, and safety, especially for makeshift systems operating in critical environments, the rise of jury-rigged subsea robotics fabrication is poised to reshape the sector. This evolution promises to enhance operational agility, reduce costs, and foster innovation, setting the stage for a more distributed and responsive approach to subsea challenges through 2025 and beyond.
Market Overview & 2025–2030 Growth Forecast
The market for jury-rigged subsea robotics fabrication—referring to the improvised or rapidly customized assembly of underwater robotic systems—has gained renewed attention as offshore exploration, decommissioning, and renewable energy projects face increasingly complex and unpredictable operational environments. In 2025, this niche is defined by a combination of necessity-driven innovation and the practical constraints of remote or austere marine settings, where standard supply chains and spare parts are often unavailable.
Current data from major subsea robotics manufacturers and offshore operators indicate that ad hoc fabrication practices are most prevalent in regions with active oil and gas decommissioning, such as the North Sea and Gulf of Mexico, as well as in expanding offshore wind farm installations. Companies like Saab and Swire Energy Services have reported increasing demand for modular, reconfigurable ROV (remotely operated vehicle) platforms and rapid-deployment toolkits, reflecting a shift toward field-adaptable solutions capable of being modified or repaired on-site.
As of 2025, the global subsea robotics market is estimated to exceed $6 billion, with a CAGR of approximately 8% projected through 2030, according to industry associations and direct disclosures from key suppliers. The jury-rigged fabrication segment, while not formally tracked as a separate category, is believed to constitute a growing share, particularly in support of emergent blue economy sectors and humanitarian subsea response operations (Oceanology International).
Several drivers are influencing this trend. First, the proliferation of open-source hardware and 3D printing technologies has made it feasible to fabricate custom parts and housings offshore, reducing downtime and costs (Teledyne Marine). Second, the increasing technical complexity and mission diversity of subsea tasks require flexible solutions that can be assembled or modified using locally available components. Finally, sustainability imperatives are pushing operators to extend the service lives of existing assets, often leading to creative retrofits and hybridization of legacy systems.
Looking ahead to 2030, industry leaders expect jury-rigged fabrication to further integrate with mainstream subsea robotics workflows. Partnerships between robotics suppliers and offshore operators are anticipated to result in standardized modular interfaces, certified quick-fix kits, and expanded field training programs, balancing the need for innovation with safety and regulatory compliance (Oceaneering International). As the offshore sector diversifies and remote operations become the norm, the outlook is for jury-rigged subsea robotics fabrication to evolve from a stopgap measure to an established, value-adding practice within the global blue economy.
Core Drivers: Cost, Agility, and Innovation Pressures
The subsea robotics sector is experiencing notable shifts in fabrication strategies, driven by intensifying pressures around cost, agility, and technological innovation. As of 2025, operators and service providers in offshore energy, marine research, and defense are increasingly resorting to jury-rigged, or improvised, approaches in the construction and adaptation of subsea robotic systems. This trend is especially pronounced in regions and applications where supply chain constraints, budget limitations, or the need for rapid deployment outweigh the preference for standardized, commercial-off-the-shelf (COTS) solutions.
Cost remains a primary driver. The price of purpose-built remotely operated vehicles (ROVs) and autonomous underwater vehicles (AUVs) has remained high, with advanced models often exceeding several hundred thousand dollars per unit. The expense is compounded by custom sensor payloads, proprietary software, and specialized launch and recovery equipment. In response, smaller operators and research institutions are increasingly repurposing consumer-grade or legacy hardware, integrating open-source electronics, and employing 3D-printed mechanical components to fabricate fit-for-purpose subsea robots at a fraction of the conventional cost. Companies such as Blue Robotics are supporting this shift by supplying modular, low-cost components, while also publishing open hardware and software documentation to foster community-driven innovation.
Agility—both in terms of fabrication speed and operational flexibility—is another key motivator. Delays in global supply chains, notably for specialized subsea connectors and pressure housings, have prompted teams to develop rapid prototyping capabilities and in-field repair kits. For instance, organizations like Schilling Robotics (now part of TechnipFMC) and Saab have reported increased customer interest in adaptable platforms that can be quickly modified or repaired using locally available materials. The ability to improvise with what’s on hand—jury-rigging—has become a competitive advantage, especially for operations in remote or logistically challenging environments.
Innovation pressures are further accelerating this movement. The integration of open-source control systems and edge AI modules, as exemplified by collaborations with organizations like OpenROV, is enabling teams to experiment with new capabilities—such as real-time adaptive navigation or novel inspection payloads—without long development cycles. This approach not only democratizes access to advanced robotics but also fosters a culture of rapid iteration and field-driven improvement.
Looking forward to the next few years, the outlook suggests continued growth in jury-rigged fabrication practices. As the subsea sector faces ongoing resource constraints and rising demand for flexible, mission-specific systems, the balance of innovation is likely to shift further toward open, modular, and improvisational design philosophies. This evolution is expected to be supported by expanding ecosystems of component suppliers, shared technical knowledge bases, and industry-led standardization efforts on modular interfaces and interoperable controls.
Emerging DIY Fabrication Techniques and Toolkits
As subsea robotics operations become more widespread across marine science, offshore energy, and exploration sectors, a parallel movement has emerged: the development and adoption of do-it-yourself (DIY) and jury-rigged fabrication techniques. This trend is fueled by the high costs and long lead times of commercial remotely operated vehicles (ROVs) and autonomous underwater vehicles (AUVs), as well as the increasing availability of modular electronics, affordable sensors, and open-source control systems in 2025.
One of the most prominent forces in this space is Blue Robotics, whose modular ROV thrusters and watertight enclosures have become foundational components for DIY subsea vehicle builders. Their products are widely used in university labs, citizen science groups, and offshore startups seeking rapid prototyping without the expense of custom fabrication. In 2024 and 2025, Blue Robotics has expanded its range of open-source hardware and documentation, further lowering barriers to entry for non-traditional innovators.
Similarly, the Marine Advanced Technology Education (MATE) Center continues to foster grassroots innovation through international competitions and extensive educational materials. Their annual ROV competition challenges teams to design and build functional underwater robots using commercial-off-the-shelf (COTS) parts, recycled materials, and 3D-printed components. The 2025 guidelines emphasize repairability and field improvisation, reflecting real-world conditions where access to spares is limited.
The proliferation of accessible 3D printing and rapid prototyping toolkits has also transformed field fabrication. Open-source projects like the OpenROV initiative provide comprehensive build guides, downloadable CAD files, and community support for constructing functional ROVs from commonly available materials. Recent years have seen a surge in custom end-effectors, sensor mounts, and housings, printed on-demand to adapt to specific mission requirements or repair damage sustained in harsh subsea environments.
Additionally, the integration of off-the-shelf microcontrollers and open-source robotics software, such as the Robot Operating System (ROS), has enabled sophisticated control and navigation capabilities without the need for proprietary systems. This democratization of subsea robotics is expected to accelerate, with more toolkits and open-source hardware platforms projected to enter the market through 2026.
Looking ahead, the convergence of modular hardware ecosystems, open-source software, and affordable rapid prototyping tools is set to further empower field teams and independent developers. These emerging DIY and jury-rigged approaches are not only reducing costs and lead times, but also fostering a culture of experimentation, resilience, and accessibility within the subsea robotics community.
Key Players and Noteworthy Projects (2025 Spotlight)
2025 is set to be a pivotal year for the development and deployment of jury-rigged subsea robotics fabrication, as key players across the marine technology sector accelerate innovation in response to escalating demands for rapid, cost-effective underwater interventions. Major advances are being driven by a blend of established subsea robotics firms and agile startups, each leveraging unconventional fabrication and retrofitting methods to meet the growing need for adaptable solutions in offshore energy, marine research, and defense.
Among the leaders, Saab has continued to evolve its Sabertooth hybrid AUV/ROV platform, with recent operational case studies highlighting rapid field-modular upgrades using locally sourced parts and on-the-spot 3D printing of custom end effectors. This approach has been particularly effective in remote operations, where traditional supply chains are disrupted. Similarly, Oceaneering International has reported field deployments in which standard ROVs were jury-rigged with improvised tooling and sensor arrays fabricated using compact CNC machines aboard support vessels, reducing mission downtime and enabling real-time adaptation to unforeseen subsea environments.
Startups are also shaping the field through grassroots, open-source fabrication initiatives. Notably, Blue Robotics has fostered a global community focused on rapid prototyping and field repairs, with shared designs and collaborative troubleshooting driving a surge in do-it-yourself subsea robotics. In 2025, several pilot programs are underway using Blue Robotics’ open hardware as a backbone for custom missions where jury-rigging is essential—such as urgent environmental monitoring deployments following marine accidents.
On the research front, Woods Hole Oceanographic Institution (WHOI) has spotlighted adaptive fabrication as a cornerstone of its 2025 deep-ocean exploration missions. WHOI’s field teams have demonstrated the integration of scavenged electronics and modular 3D-printed structures to rapidly reconfigure vehicles for specific science targets, a practice that will likely become more common as mission profiles diversify.
Looking forward, the outlook for jury-rigged subsea robotics fabrication is robust. Industry conferences such as the upcoming Oceanology International are dedicating expanded tracks to modular, field-adaptable robotics, signaling mainstream acceptance. As supply chain unpredictability, cost pressures, and new regulatory requirements converge, the capacity to improvise and fabricate subsea components on demand is expected to move from the margins to the core of industry best practices, fundamentally reshaping operational paradigms through 2026 and beyond.
Risks, Regulatory Gaps, and Safety Challenges
As jury-rigged subsea robotics fabrication proliferates in 2025, significant risks, regulatory gaps, and safety challenges are emerging in the underwater robotics ecosystem. The flexibility and rapid deployment associated with makeshift and improvised design approaches—often spurred by supply chain disruptions or urgent operational needs—have outpaced the capacity of existing standards and oversight frameworks to ensure safety and reliability.
A core risk arises from the use of non-standard components and untested integration methods. Improvised builds frequently substitute certified parts with available alternatives, or 3D-print critical elements, resulting in unpredictable performance and reliability. Notably, organizations such as Saab and Oceaneering International emphasize adherence to strict quality control and traceability for subsea robotic systems; deviations from these protocols can lead to catastrophic failures, especially in high-pressure or hazardous environments.
Regulatory oversight has struggled to keep pace. While bodies like the International Marine Contractors Association (IMCA) provide baseline operational and safety guidelines for commercial Remotely Operated Vehicles (ROVs), these are largely predicated on factory-built equipment and established engineering practices. Jury-rigged fabrication, by its nature, often sidesteps standard documentation, approval, and traceability processes, creating loopholes where liability and compliance are unclear. As of 2025, IMCA and similar organizations are only beginning to address improvised builds, with formal guidance still in development.
Safety challenges are especially acute when jury-rigged systems are deployed for critical operations such as deepwater inspection, salvage, or intervention on subsea infrastructure. Improperly shielded electronics, inadequate pressure housings, and non-compliant hydraulics have resulted in notable near-misses and some system losses, as referenced in incident data maintained by IMCA. Furthermore, in the absence of standardized testing, these systems present unknown hazards to human divers, marine habitats, and critical assets should a malfunction occur.
Looking forward, the outlook for regulatory harmonization and risk mitigation is mixed. Industry leaders, including Saab and Oceaneering International, are advocating for expanded certification schemes and modular safety audits tailored to rapid or field-based fabrication scenarios. However, given the global and often decentralized nature of subsea operations, enforcement remains a challenge. Without a concerted effort to close regulatory gaps and embed safety culture at all fabrication levels, jury-rigged robotics may continue to introduce systemic vulnerabilities to subsea operations in the coming years.
Case Studies: Successes and Failures in Jury-Rigged Deployments
The period leading up to 2025 has seen several notable case studies highlighting both successes and failures in jury-rigged subsea robotics fabrication. “Jury-rigged” in this context refers to the rapid or improvised construction and adaptation of subsea robotic systems, often under the pressure of urgent operational demands or in resource-limited environments.
One successful example emerged during the 2024 North Sea pipeline incident, where a rapid response required the modification of available remotely operated vehicles (ROVs) to perform unanticipated inspection and patching tasks. Technicians from Saab adapted their Seaeye Falcon ROVs with custom-fabricated grippers and inspection modules using 3D-printed components and off-the-shelf electronics. These modifications enabled real-time, on-site repair and inspection, preventing escalation of the leak and highlighting the potential for flexible, field-deployable fabrication techniques.
Similarly, during the 2023 deployment in the Gulf of Mexico, engineers at Oceaneering International faced an unexpected thruster failure on their Millennium ROV series during a deepwater cable lay operation. With limited spares, the team constructed a substitute thruster mount using locally available materials and reconfigured control software to accommodate the non-standard component. The mission was completed successfully, demonstrating the value of adaptive engineering and the importance of robust, modular system design for field reparability.
However, not all jury-rigged efforts have succeeded. In late 2023, a smaller operator in Southeast Asia attempted to retrofit a commercial drone with waterproofing and buoyancy modules fabricated from non-rated plastics and adhesives for a shallow pipeline survey. The system, lacking proper sealing protocols and pressure testing, suffered catastrophic electronic failure within hours of submersion. This incident, reviewed by International Marine Contractors Association, underscored the critical importance of adhering to minimum industry standards even in improvised builds, especially for subsea operations where failures can be costly and dangerous.
Looking ahead, the outlook for jury-rigged subsea robotics fabrication is mixed. Operators and manufacturers are increasingly recognizing the need for modularity and field-serviceability in ROV and AUV designs. Companies like Sonardyne are investing in adaptive sensor packages and open architecture platforms to facilitate rapid, on-site customization, while industry bodies push for better field repair protocols. However, the limitations imposed by environmental conditions and safety standards remain significant, and the balance between innovation and risk management will shape the next phase of field-deployable subsea robotics.
Materials, Components, and Open-Source Hardware Trends
Jury-rigged subsea robotics fabrication, characterized by the innovative use of readily available or repurposed materials and components, is seeing increased adoption as organizations seek cost-effective and flexible solutions for underwater exploration and intervention. In 2025, this trend is being propelled by several factors: supply chain constraints, the proliferation of open-source hardware platforms, and a growing ecosystem of community-driven design repositories. These drivers are reshaping how subsea roboticists and field engineers approach rapid prototyping and deployment in challenging marine environments.
The global shortage of specialized subsea components—such as pressure housings, underwater connectors, and thrusters—has prompted many teams to adapt consumer-grade or industrial hardware for subsea use. For example, off-the-shelf electronics enclosures, originally intended for terrestrial use, are being retrofitted with custom gaskets and sealants to withstand short-duration submersion. Similarly, high-strength polymers and composite materials, widely available from industrial suppliers, are replacing traditional titanium or stainless steel parts in non-critical structural areas, reducing both cost and lead times. Manufacturers like TE Connectivity and Amphenol have responded by broadening their catalogs to include more modular, adaptable connector systems suitable for DIY and semi-professional subsea applications.
Open-source hardware and software platforms are playing a pivotal role in this landscape. The continued evolution of projects such as the BlueROV2 by Blue Robotics has fostered a thriving community of makers, researchers, and educators who share modifications and workarounds for field fabrication. In particular, the availability of 3D-printable part files, open schematics, and firmware has made it feasible to assemble functional ROVs and sensor payloads using locally sourced or repurposed components. The OpenROV initiative, supported by organizations like OpenROV, continues to democratize subsea robotics by providing accessible designs and real-world case studies.
Looking ahead to the remainder of 2025 and beyond, jury-rigged fabrication is expected to become even more sophisticated, as collaborative design platforms and distributed manufacturing (e.g., local 3D printing hubs) reduce the barriers to experimentation. Industry bodies such as the Marine Technology Society are increasingly spotlighting grassroots innovation at technical conferences, while suppliers introduce ruggedized DIY kits targeting educational, research, and light commercial markets. As supply chains normalize, the cross-pollination between professional and hobbyist communities will likely yield hybrid fabrication models—combining certified critical components with custom, jury-rigged assemblies—for agile, mission-specific subsea deployments.
Investment, Collaboration, and Industry Response
The landscape of subsea robotics fabrication is undergoing notable transformation as industry players respond to the rise of jury-rigged and improvised solutions. In 2025, investment in subsea robotics remains robust but is increasingly shaped by the need to balance rapid innovation with reliability and regulatory compliance. Several leading subsea technology firms are reporting a surge in partnerships aimed at addressing the proliferation of makeshift robotics, which are often deployed in urgent offshore energy, salvage, or inspection scenarios.
Major manufacturers such as Saab and Oceaneering International are collaborating with smaller engineering firms and offshore service providers to develop toolkits and modular components specifically designed for rapid, field-based assembly. These initiatives are seen as a direct response to the challenges and risks associated with jury-rigged robotics, including safety concerns and variable operational reliability. For instance, Saab has launched pilot programs in 2025 to support field technicians with standardized, adaptable components, aiming to reduce the frequency of entirely improvised builds.
Industry bodies such as the International Marine Contractors Association (IMCA) have also increased their focus on documenting best practices and issuing updated guidance on the use of ad-hoc robotics solutions. These efforts reflect a broader industry consensus that while jury-rigged fabrication can provide critical stopgaps—particularly in remote environments—the long-term outlook requires more structured frameworks to mitigate risk and ensure quality.
Investment trends indicate growing interest in digital platforms for remote diagnostics and rapid prototyping. Companies like Fugro are exploring cloud-based collaboration environments, where design iterations and assembly procedures for subsea robots can be shared and vetted in real time across geographically dispersed teams. This collaborative approach is expected to reduce the likelihood of unsafe improvisation and accelerate the deployment of reliable, fit-for-purpose subsea robots.
Looking ahead, industry observers expect increased merger and acquisition activity as established players seek to acquire startups specializing in modular robotics and rapid prototyping technologies. The consensus is that the next few years will see a convergence between the agility of field-based jury-rigging and the rigor of industrial-grade engineering, supported by ongoing cross-sector investment and a tightening regulatory environment.
Future Outlook: How Jury-Rigging Could Redefine Subsea Robotics by 2030
Jury-rigged subsea robotics fabrication—improvised, on-the-spot construction and repair of underwater robots using available materials and non-standard solutions—is gaining traction as industries adapt to increasingly complex and dynamic offshore environments. As of 2025, the rising demand for rapid deployment and reduced downtime in subsea operations is driving innovation in this area. Traditional subsea robotic systems, while robust, often require lengthy maintenance cycles and specialized parts. In contrast, jury-rigging offers a pragmatic approach to keep operations running, especially in remote or high-risk locations where logistics are challenging.
Energy companies such as Shell and subsea engineering specialists like Saab are actively exploring modular, field-adaptable robotic platforms. These systems are intentionally designed for ease of modification and repair, providing crews with the flexibility to implement field fixes using locally sourced components or 3D-printed parts. As additive manufacturing technologies mature, the ability to fabricate bespoke parts on-site is becoming an operational reality. For example, Baker Hughes has demonstrated the use of portable additive manufacturing units for rapid repair and customization of subsea tools during field trials.
The next few years are expected to see an expansion of open-source and standardized hardware initiatives, enabling broader sharing of repair methods and modular designs applicable to jury-rigged fabrication. Organizations such as Oceanic are facilitating collaboration among operators to establish best practices for safe and effective improvisational repairs, further legitimizing jury-rigging within industry norms.
By 2030, industry experts anticipate that jury-rigged approaches will be routinely integrated into offshore maintenance strategies, particularly in deepwater oil & gas, offshore wind, and subsea mining sectors. The proliferation of digital twins and real-time diagnostics—tools provided by companies like SLB (Schlumberger)—will further empower remote crews to diagnose failures and improvise solutions with increased confidence and precision.
Ultimately, as regulatory perspectives evolve and risk tolerance is better quantified, jury-rigged subsea robotics fabrication could shift from a last-resort measure to a valued operational asset. This transformation is likely to accelerate as more operators, manufacturers, and service providers formalize training and certification processes for field improvisation, making the practice safer, more reliable, and a standard part of the subsea robotics toolkit by the end of the decade.