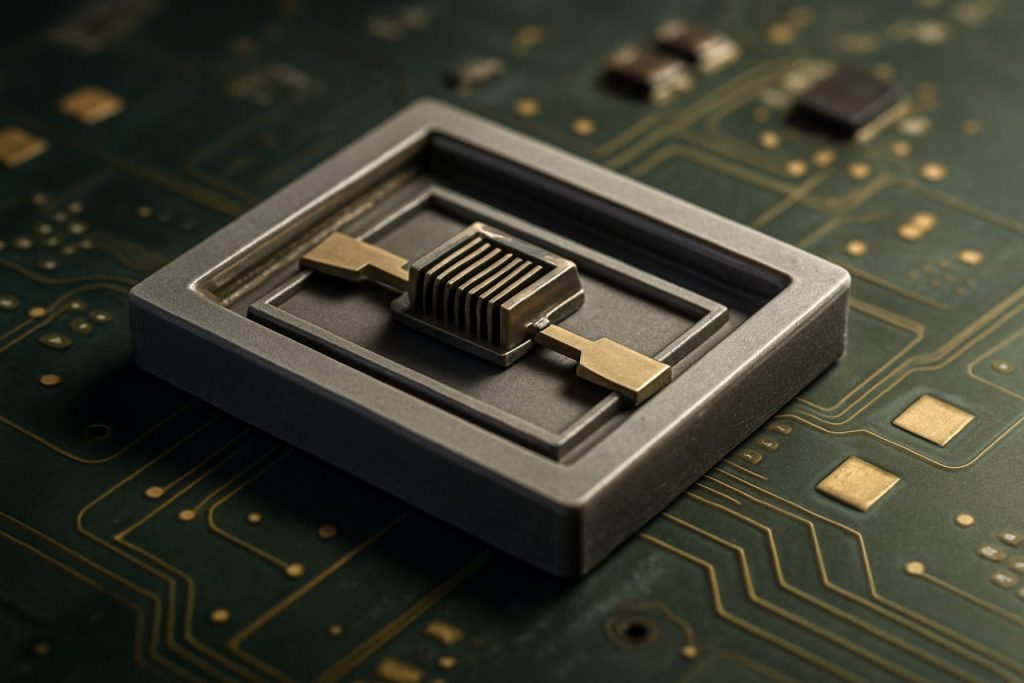
Table of Contents
- Executive Summary: The State of MEMS Relay Reliability in 2025
- Market Outlook: Forecasts and Growth Drivers Through 2030
- Key Applications: Industrial, Automotive, and IoT Innovations
- Emerging Thermo-Mechanical Testing Methodologies
- Material Science Advances Impacting MEMS Relay Endurance
- Leading Companies and Industry Collaborations
- Challenges: Failure Mechanisms and Reliability Bottlenecks
- Regulatory Standards and Testing Protocols
- Case Studies: Breakthroughs from Top MEMS Manufacturers
- Future Roadmap: Next-Gen Reliability Solutions and Market Impact
- Sources & References
Executive Summary: The State of MEMS Relay Reliability in 2025
Thermo-mechanical reliability remains a pivotal concern in the deployment of microelectromechanical system (MEMS) relay devices, especially as their integration into high-reliability markets intensifies in 2025. MEMS relays, which leverage micromachined structures to perform electrical switching, are increasingly utilized in aerospace, telecommunications, automotive, and test instrumentation due to their low power consumption and precise actuation capabilities. However, the mechanical and thermal stresses encountered during operation and environmental cycling continue to challenge both device longevity and performance consistency.
In 2025, leading manufacturers such as Teledyne and Omron Corporation are advancing comprehensive thermo-mechanical reliability testing protocols. These tests, which include temperature cycling, power cycling, and mechanical shock assessments, are designed to simulate the harsh environments that MEMS relays face in real-world applications. For instance, Teledyne employs accelerated life testing to evaluate the endurance of their MEMS relays under repeated thermal and mechanical loads, reporting operational lifetimes exceeding one billion cycles under controlled test conditions.
Current data indicates that improvements in materials—such as the adoption of advanced silicon-on-insulator (SOI) substrates and hermetic wafer-level packaging—are yielding measurable gains in both mechanical fatigue resistance and thermal stability. Omron Corporation has published findings on their MEMS relay portfolio demonstrating stable contact resistance and negligible stiction even after prolonged temperature cycling between -40°C and 125°C, a key criterion for automotive and industrial applications.
Industry standards from organizations such as the JEDEC Solid State Technology Association and IEEE continue to shape the methodologies and requirements for MEMS relay qualification. In 2025, new test protocols emphasize not only the number of switching cycles but also the impact of rapid temperature transitions and vibration—a response to the demand for more robust relays in 5G infrastructure and autonomous vehicle systems.
Looking forward, the outlook is for continued refinement of test methodologies and further collaboration between device makers, end-users, and standards bodies. The goal is to ensure that MEMS relays can reliably meet the stringent demands of next-generation electronic systems. Advances in MEMS design, encapsulation, and real-time health monitoring are expected to further boost confidence in the thermo-mechanical reliability of these critical components over the next several years.
Market Outlook: Forecasts and Growth Drivers Through 2030
The market for thermo-mechanical reliability testing in microelectromechanical relay devices (MEMS relays) is poised for significant advancement through 2030, propelled by increased integration of MEMS switches and relays in automotive, industrial, and communications electronics. As MEMS relays are deployed in mission-critical environments—such as automotive safety systems, 5G infrastructure, and industrial automation—their operational reliability under varied thermal and mechanical stresses has become a decisive factor for adoption. This is intensifying demand for advanced reliability testing services and solutions.
Since 2023, industry leaders have reported rapid growth in MEMS relay applications requiring high endurance to temperature cycling, vibration, and shock, driving the adoption of comprehensive reliability qualification protocols in line with standards such as AEC-Q100 and MIL-STD-883. For instance, TE Connectivity and Coto Technology have expanded their MEMS relay portfolios and focus on rigorous thermo-mechanical validation processes to meet automotive and telecom reliability benchmarks.
Automotive OEMs and Tier 1 suppliers are increasingly emphasizing zero-defect strategies, mandating greater transparency in reliability data and traceability throughout the MEMS relay supply chain. This has led to partnerships with testing solution providers and the adoption of automated test systems capable of large-scale, real-time monitoring of MEMS relay performance under simulated field conditions. For example, Rohde & Schwarz has introduced test platforms tailored for MEMS device reliability, supporting temperature cycling, humidity, and vibration testing.
Through 2030, the proliferation of electric vehicles, industrial IoT, and high-frequency wireless infrastructure is projected to sustain double-digit annual growth in the MEMS relay sector. This expansion will, in turn, amplify the need for advanced thermo-mechanical reliability testing technologies, such as in-situ monitoring, MEMS-specific failure analysis, and accelerated life testing platforms. Industry groups like SEMI are expected to further refine best practices and establish new guidelines for MEMS relay qualification.
Looking ahead, the integration of AI-driven data analytics and digital twins in reliability testing is anticipated to become a key differentiator. This will enable predictive maintenance, faster qualification cycles, and reduced product development timelines. As the complexity and performance requirements of MEMS relays increase, investment in automated, high-throughput thermo-mechanical reliability testing solutions will be crucial for suppliers aiming to capture emerging market opportunities in automotive, industrial, and next-generation communications sectors.
Key Applications: Industrial, Automotive, and IoT Innovations
The adoption of microelectromechanical relay devices (MEMS relays) continues to expand across key sectors such as industrial automation, automotive systems, and the Internet of Things (IoT). As these applications demand high reliability under varying environmental and operational stresses, thermo-mechanical reliability testing has become a cornerstone in device qualification and lifecycle prediction for 2025 and the immediate future.
In the industrial domain, MEMS relays are increasingly utilized for precision switching in harsh environments, including manufacturing robotics, process control, and high-voltage circuit protection. Thermo-mechanical tests—such as thermal cycling, power cycling, and mechanical shock—are vital to ensure the devices maintain low contact resistance and stable actuation over millions of cycles. For instance, TE Connectivity reports ongoing qualification of MEMS relays using accelerated life testing protocols tailored for industrial-grade reliability, simulating decades of operational wear in months.
Automotive applications present even stricter requirements, with MEMS relays facing wide temperature swings, vibration, and humidity in advanced driver-assistance systems (ADAS), powertrains, and battery management systems. Industry leaders such as NXP Semiconductors and STMicroelectronics are advancing their automotive MEMS portfolios, subjecting devices to automotive standard tests like AEC-Q100 thermal shock and high-temperature operating life (HTOL). Recent data from these manufacturers highlights that MEMS relays now reliably endure 1,000+ temperature cycles between -40°C and 125°C, meeting the requirements for next-generation electric vehicles.
IoT innovations push the boundaries of MEMS relay miniaturization and energy efficiency, with billions of connected sensors and actuators deployed in fluctuating indoor and outdoor environments. Companies such as CANTIME Microelectronics are combining advanced packaging and robust thermo-mechanical testing to guarantee relay integrity in edge devices, wearables, and smart infrastructure. The goal is to ensure consistent performance despite frequent thermal cycling due to rapid on/off switching and variable ambient conditions.
Looking ahead, the trajectory for 2025 and beyond points to the integration of AI-driven reliability monitoring, real-time in-system stress testing, and further harmonization of industry standards for MEMS relay qualification. As device geometries scale down and application environments grow harsher, collaborative efforts between semiconductor manufacturers and end users will be critical for advancing thermo-mechanical reliability. The continued refinement of accelerated testing methods, coupled with robust feedback from field data, is expected to drive further improvements in MEMS relay durability and enable their broader adoption in critical, mission-dependent applications.
Emerging Thermo-Mechanical Testing Methodologies
Thermo-mechanical reliability testing has become a critical focus for advancing microelectromechanical relay (MEM relay) devices, particularly as these components find increasing use in harsh environments and miniaturized electronics. In 2025, the industry is seeing a shift toward more comprehensive and accelerated testing protocols that address the unique failure modes associated with the interplay of thermal and mechanical stresses at the micro-scale. Key industry players are incorporating a combination of traditional cycling tests and novel real-time monitoring techniques to ensure long-term reliability.
A primary methodology gaining traction involves highly accelerated life testing (HALT) adapted for MEM relays, which subjects devices to rapid temperature and mechanical cycling to precipitate early-life failures and assess robustness. For instance, STMicroelectronics has detailed initiatives in deploying multi-axis mechanical shock and thermal ramping protocols in their MEMS R&D, aiming to better simulate real-world stresses encountered by relay devices in automotive and industrial settings.
In parallel, micro-scale digital image correlation (DIC) and laser Doppler vibrometry are increasingly used to monitor deformation and dynamic response under thermal load, providing high-resolution insights into failure mechanisms such as stiction, fatigue, and contact degradation. Texas Instruments reports the integration of in-situ optical measurement systems in their MEM relay reliability labs, enabling real-time tracking of microstructure response to thermal cycling and mechanical actuation.
Another emerging methodology is the use of wafer-level reliability testing, which allows simultaneous evaluation of large numbers of relays under controlled thermal and mechanical stress conditions. This approach, as highlighted by Bosch Sensortec, enhances statistical confidence and reduces time-to-qualification for MEM relay products destined for safety-critical applications.
Looking ahead, the next few years will likely see the adoption of hybrid testing platforms that combine electrical, thermal, and mechanical stressors in a single automated environment. Collaborative efforts between semiconductor manufacturers and equipment suppliers are underway to develop standardized protocols, with organizations like MEMS & Sensors Industry Group promoting guidelines for cross-industry acceptance of thermo-mechanical reliability benchmarks.
Overall, the trajectory for thermo-mechanical reliability testing in MEM relay devices is toward more predictive, data-rich methodologies that accelerate failure detection and qualification—essential for meeting the stringent demands of next-generation electronics in automotive, industrial, and aerospace sectors.
Material Science Advances Impacting MEMS Relay Endurance
The thermo-mechanical reliability of microelectromechanical system (MEMS) relay devices is intrinsically linked to advancements in material science, particularly as these devices face increasingly stringent operational and environmental requirements in 2025 and the coming years. MEMS relays, which rely on the deformation and movement of microscale structures for switching, are susceptible to failure mechanisms such as stiction, fatigue, creep, and wear, all of which are exacerbated by thermal and mechanical cycling. Consequently, rigorous thermo-mechanical reliability testing has become a focal point in both academic and industrial settings.
Recent developments in thin-film deposition and surface engineering have led to the use of robust materials such as tungsten, ruthenium, and silicon carbide for relay contacts and structural elements. These materials exhibit high melting points, low adhesion, and excellent resistance to electromigration and oxidation, which are critical factors during high-temperature cycling and prolonged actuation. For instance, Coventor (a Lam Research company) has highlighted the integration of advanced materials with predictive finite element modeling to simulate and test MEMS device endurance under coupled thermal and mechanical stresses.
To address the challenge of repeated cycling, manufacturers are increasingly employing automated, accelerated life testing protocols. These protocols expose MEMS relays to millions or even billions of actuation cycles at elevated temperatures, often ranging from -40°C to 150°C, to simulate decades of operational life in condensed timeframes. Data from Teledyne—a recognized supplier of MEMS relays—demonstrates the importance of such testing, showing that optimized material stacks can yield relays with mean-time-to-failure (MTTF) values exceeding 1010 cycles under harsh thermal conditions.
Looking forward, the increasing adoption of MEMS relays in automotive, aerospace, and telecommunications sectors—where devices are exposed to aggressive environments—will drive further innovation in materials and reliability testing. Industry bodies such as MEMS & Sensors Industry Group are actively fostering collaboration between material suppliers, device manufacturers, and test equipment providers to standardize thermo-mechanical reliability benchmarks for next-generation MEMS relays.
In summary, as the operational envelope for MEMS relays expands, advances in material science and more sophisticated thermo-mechanical reliability testing methodologies are expected to play a pivotal role in ensuring device endurance, with robust, standardized testing becoming increasingly critical through 2025 and beyond.
Leading Companies and Industry Collaborations
The expanding adoption of microelectromechanical systems (MEMS) relays in automotive, aerospace, and industrial applications has accelerated the demand for robust thermo-mechanical reliability testing. In 2025, leading MEMS relay manufacturers and research-oriented organizations continue to prioritize collaborative efforts to ensure device longevity under combined thermal and mechanical stress conditions.
One of the industry’s foremost players, CANTIMEMS, has invested in comprehensive reliability protocols that simulate real-world thermal cycling and vibration scenarios for their MEMS relay products. Their published technical documentation details internal stress analyses and accelerated life testing, providing transparency for automotive and industrial customers seeking high-reliability switching solutions.
Another significant contributor, OMRON Corporation, has established in-house environmental testing facilities where MEMS relays undergo high-temperature operating life (HTOL) and mechanical shock tests. OMRON’s reliability data, presented in their latest product specifications, demonstrates continued improvements in contact resistance stability and switching endurance even after extensive thermal-mechanical cycling.
Collaborative efforts are also prominent. STMicroelectronics has actively partnered with automotive OEMs and Tier 1 suppliers to develop standardized reliability protocols tailored to the harsh operating environments of electric vehicles. These partnerships have led to the implementation of joint qualification programs, ensuring MEMS relay components meet or surpass automotive-grade requirements.
Industry bodies such as SEMI play a crucial role by facilitating working groups focused on MEMS device reliability standards. In 2025, SEMI’s MEMS & Sensors Industry Group is spearheading initiatives to harmonize thermo-mechanical test methodologies, encouraging data sharing among member companies to accelerate device qualification and reduce time-to-market.
Looking ahead, further collaborations are expected to focus on real-time in situ monitoring of MEMS relay performance during reliability testing, leveraging advanced sensor feedback and AI-driven data analytics. These advancements are anticipated to be piloted by consortia involving leading players such as Bosch and TE Connectivity, with the aim of enabling predictive maintenance and extending relay lifetimes in mission-critical applications.
Overall, 2025 marks a period of intensified joint activity among manufacturers, OEMs, and standards organizations. This collaborative ecosystem is set to drive further innovation in thermo-mechanical reliability, building customer confidence and paving the way for broader MEMS relay deployment in emerging sectors.
Challenges: Failure Mechanisms and Reliability Bottlenecks
Thermo-mechanical reliability testing is a critical aspect in the development and qualification of microelectromechanical relay devices (MEM Relays), as these components are increasingly deployed in demanding environments such as automotive, aerospace, and industrial applications. The main challenges stem from the complex interplay of thermal cycling, mechanical stress, and material fatigue, which collectively influence device longevity and operational integrity.
As of 2025, the primary failure mechanisms observed in MEM relay devices include stiction (adhesion of contact surfaces), mechanical wear, thermally induced stress cracking, and contact degradation due to micro-welding or fretting corrosion. For instance, stiction remains a persistent challenge, particularly under elevated temperature and humidity conditions, which can degrade relay actuation performance over time. Industry leaders such as Coventor and STMicroelectronics have reported that even minor surface contamination or variations in the contact geometry can significantly accelerate stiction and increase switching failure rates.
Mechanical wear is exacerbated by repeated cycling, especially in high-frequency switching applications. The continuous actuation of MEM relay arms can lead to microstructural fatigue, ultimately resulting in fractures or permanent deformation. Thermal cycling, commonly simulated in reliability tests ranging from -40°C to +125°C, can induce material expansion and contraction mismatches between different layers or interfaces, leading to delamination or cracking. Texas Instruments highlights the importance of robust packaging solutions and stress-relief structures to mitigate cracking and delamination under accelerated thermal cycling protocols.
Contact degradation, particularly at the metal interface, poses another critical bottleneck. Micro-welding can occur due to high current densities during switching, while fretting corrosion is accelerated by environmental exposure and mechanical vibrations. These issues can induce increased contact resistance, intermittent open circuits, or even catastrophic failure. According to Analog Devices, ongoing research focuses on advanced contact materials, such as noble metal alloys and engineered surface coatings, to extend device lifetimes and resist environmental degradation.
Looking forward, the outlook for MEM relay reliability testing involves the adoption of more sophisticated in-situ monitoring systems and machine learning algorithms to predict failure onset based on real-time performance data. Standardization efforts led by organizations like the SEMI consortium are underway to harmonize accelerated lifetime testing protocols, addressing the increasing complexity and diversity of MEM relay applications. The next few years will likely see the integration of predictive analytics and self-diagnostic capabilities into MEM relay modules, enhancing reliability assurance and reducing field failures in mission-critical systems.
Regulatory Standards and Testing Protocols
Thermo-mechanical reliability testing for microelectromechanical relay devices (MEM relays) is becoming increasingly standardized as these components are integrated into mission-critical applications across automotive, aerospace, and telecommunications industries. In 2025, regulatory standards and industry-driven protocols are evolving to address the unique challenges posed by the miniaturized, moving structures within MEM relays, which are subject to thermal cycling, mechanical shock, and prolonged operational stresses.
Internationally recognized standards, such as those from the JEDEC Solid State Technology Association and International Electrotechnical Commission (IEC), provide foundational frameworks for environmental and mechanical reliability testing. For MEMS devices, the application of JEDEC JESD22 standards (including mechanical shock, vibration, and temperature cycling) is now common practice, with additional MEMS-specific protocols being developed to capture the nuances of relay operation. For instance, the IEC 60749 series, which covers semiconductor reliability, is frequently adapted by manufacturers to extend coverage to MEM relays.
Leading MEMS relay manufacturers such as MEMSIC and Cantilever Sensors are actively participating in the definition and refinement of these testing protocols, ensuring that test methodologies reflect real-world use cases. Their published reliability data often include results from accelerated life testing—thermal cycling between -40°C and +125°C, high-temperature operating life (HTOL) assessments, and mechanical actuation endurance exceeding one billion cycles, as reported in their technical documentation.
Automotive sector requirements, as outlined by the Automotive Industry Action Group (AIAG) and detailed in AEC-Q100 standards, are being extended to MEM relay devices, compelling suppliers to adopt rigorous qualification flows. In addition to environmental and mechanical stress screening, manufacturers are integrating failure analysis protocols, such as scanning electron microscopy and in-situ monitoring, to pinpoint failure mechanisms unique to MEMS relay architectures.
Looking ahead to the next several years, regulatory bodies and industry consortia are expected to further harmonize MEM relay reliability testing with broader semiconductor device standards, while introducing MEMS-specific amendments. The rise of digital twin and machine learning techniques for predictive reliability modeling is also anticipated to influence future protocol development. Collaboration between standards organizations and MEMS foundries will be crucial to ensure that reliability testing evolves in step with device complexity and market demands.
Case Studies: Breakthroughs from Top MEMS Manufacturers
Thermo-mechanical reliability testing is a critical process in the qualification and mass adoption of microelectromechanical relay (MEMS relay) devices, with leading MEMS manufacturers pioneering new methodologies and reporting significant breakthroughs in 2025. This section explores recent advances and case studies from top industry players, focusing on real-world performance, accelerated testing protocols, and insights into future directions.
One notable example is CANTIME MEMS, which in early 2025 announced the successful qualification of its next-generation MEMS relays for high-reliability industrial automation and automotive applications. Their approach relied on a suite of accelerated life tests, including temperature cycling between -40°C and +125°C and high-G mechanical shock events. CANTIME MEMS reported that their relays consistently surpassed industry standards for contact resistance stability and endured over 109 switching cycles without measurable degradation, highlighting robust packaging and contact metallurgies as key factors.
Similarly, Teledyne has highlighted new reliability protocols for its MEMS-based relay products. In 2025, Teledyne implemented advanced in-situ monitoring during thermal shock and vibration testing, enabling real-time detection of mechanical fatigue and stiction phenomena. Their MEMS relays, designed for aerospace and defense, underwent rigorous JEDEC-compliant thermal cycling and mechanical load tests, achieving mean time to failure (MTTF) values exceeding 10 years under mission profiles typical of satellite and avionics systems.
Meanwhile, Carnegie Mellon University in partnership with Qorvo has advanced reliability research on microelectromechanical relays for RF switching. In 2025, their collaborative case study demonstrated that new hermetic sealing techniques and low-thermal-expansion substrates can reduce mechanical stress concentrations during temperature cycling, resulting in improved device longevity and lower failure rates across repeated power cycling and environmental stress screening.
Looking ahead, MEMS manufacturers are actively developing digital twin models and AI-based predictive analytics to further enhance reliability assessments, aiming to accelerate qualification cycles and anticipate failure modes before physical testing. As MEMS relays are increasingly adopted in automotive, industrial, and communication sectors, the outlook for 2025 and beyond includes expanded use of real-world mission-profile testing, broader deployment in safety-critical systems, and continued collaboration between industry leaders and research institutions to set new benchmarks in thermo-mechanical reliability.
Future Roadmap: Next-Gen Reliability Solutions and Market Impact
Thermo-mechanical reliability testing for microelectromechanical relay (MEM relay) devices is entering a pivotal phase as the industry demands higher robustness, longer operational lifetimes, and broader deployment in mission-critical electronics. In 2025, several leading MEMS relay manufacturers and semiconductor consortia are intensifying efforts to develop advanced testing protocols and predictive reliability models that address the unique challenges of these electromechanical systems.
A central focus for 2025 is the integration of high-throughput, in-situ reliability screening to capture both thermal cycling and mechanical actuation effects in real-world conditions. For example, Teledyne and Cantilever Labs, recognized pioneers in MEM relay development, are collaborating with OEMs to standardize accelerated life testing that simulates harsh automotive and industrial environments. These protocols subject devices to thousands of temperature cycles and millions of actuation events, measuring contact resistance drift, stiction, and failure rates to ensure sub-ppm defectivity.
In parallel, organizations like Semiconductor Industry Association are driving cross-industry working groups to harmonize reliability metrics and reporting for MEM relays. This includes establishing agreed-upon definitions for failure modes such as welding, bounce, and micro-wear, and deploying advanced metrology tools to quantify sub-micron deformations during testing. Such initiatives are crucial as MEM relays are increasingly integrated into automotive safety systems, 5G infrastructure, and next-gen medical devices, where zero-defect reliability is paramount.
On the technology front, new solutions are emerging to address the limitations of traditional thermal shock and mechanical fatigue testers. Kistler and Keysight Technologies are rolling out modular, high-sensitivity testing platforms that combine real-time electrical monitoring with nano-scale force/displacement sensing. This enables predictive maintenance and root-cause analysis, significantly reducing development cycles for MEM relay manufacturers.
Looking ahead to the next few years, the roadmap points toward greater adoption of digital twins and AI-driven analytics for reliability assessment. Companies like Texas Instruments are investing in simulation environments that mirror the coupled thermo-mechanical behavior of MEM relays under diverse use cases, enabling virtual qualification and faster go-to-market times.
In summary, the sector is on the cusp of a significant transformation in thermo-mechanical reliability testing for MEM relay devices. The convergence of advanced hardware, standardized testing frameworks, and AI-enhanced analytics is expected to deliver unprecedented levels of quality assurance, paving the way for broader market penetration in safety-critical and high-performance applications.