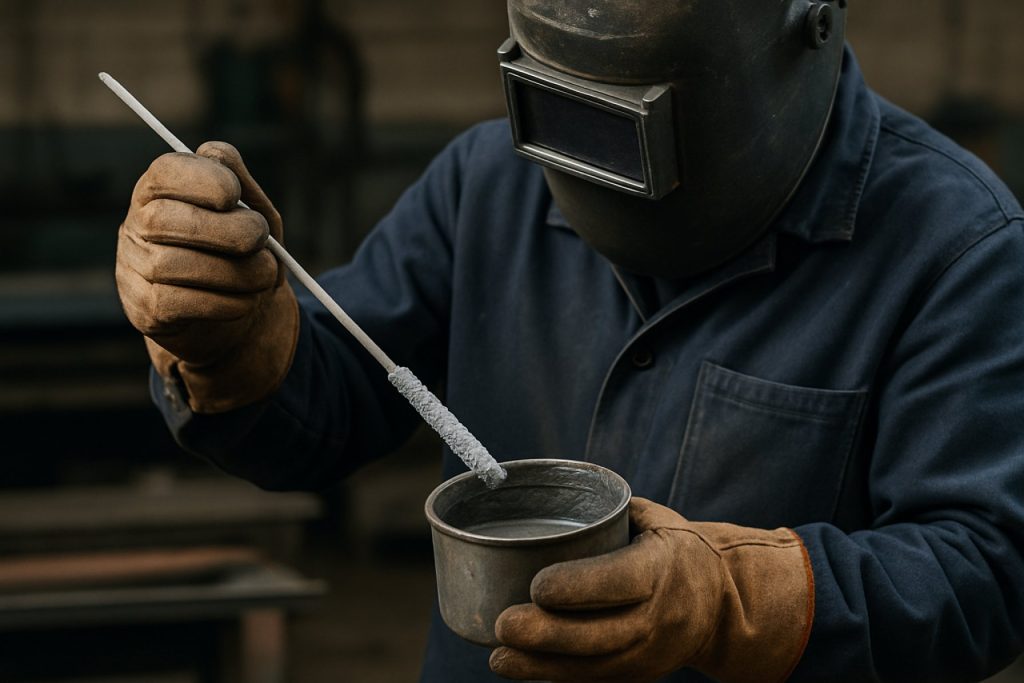
Tabla de Contenidos
- Resumen Ejecutivo: Tendencias Clave y Perspectivas del Mercado (2025–2030)
- Pronóstico del Mercado Global: Factores de Crecimiento y Puntos Calientes Regionales
- Tecnologías Emergentes en Formulación de Revestimiento de Electrodos
- Materias Primas: Abastecimiento, Sostenibilidad y Dinámicas de la Cadena de Suministro
- Cumplimiento Regulatorio y Normas Industriales (AWS, ISO)
- Principales Manufacturers y Asociaciones Estratégicas (ESAB, Lincoln Electric, Bohler Welding)
- Pipeline de I+D: Innovaciones en Rendimiento y Eficiencia de Costos
- Aplicaciones en Diferentes Sectores: Construcción, Energía, Automotor, y Más
- Desafíos: Impacto Ambiental, Costos y Garantía de Calidad
- Perspectiva Futura: Ventaja Competitiva y Oportunidades a Largo Plazo
- Fuentes y Referencias
Resumen Ejecutivo: Tendencias Clave y Perspectivas del Mercado (2025–2030)
El mercado de formulación de revestimientos de electrodos de soldadura está en camino de una evolución significativa de 2025 a 2030, impulsado por los avances en la ciencia de materiales, imperativos de sostenibilidad y la creciente demanda de la industria por soluciones de soldadura de alto rendimiento. Los revestimientos de electrodos, que juegan un papel vital en proteger la zona de soldadura, estabilizar el arco y mejorar la calidad de la soldadura, están experimentando innovaciones a medida que los fabricantes buscan equilibrar el rendimiento, la eficiencia de costos y las preocupaciones ambientales.
Una tendencia clave en 2025 es la creciente adopción de revestimientos de bajo hidrógeno y amigables con el medio ambiente. Los principales fabricantes de electrodos están invirtiendo en nuevas formulaciones que minimizan las emisiones peligrosas durante las operaciones de soldadura y reducen el riesgo de defectos en la soldadura, como la porosidad y las grietas. El desarrollo y la implementación de revestimientos basados en rutilo, básicos y celulosa se están refinando con aditivos y aglutinantes avanzados, proporcionando propiedades mecánicas mejoradas y un mejor aspecto de la soldadura. Por ejemplo, productores líderes como Lincoln Electric y ESAB han destacado su enfoque en soluciones de electrodos sostenibles, respondiendo a las regulaciones más estrictas sobre seguridad en el lugar de trabajo y medio ambiente en América del Norte, Europa y Asia.
La integración de sistemas de control de calidad digitalmente habilitados y la automatización de procesos se espera que formen la producción de revestimientos de electrodos. Las empresas están implementando sistemas de monitoreo en tiempo real y análisis de datos para asegurar un grosor de revestimiento uniforme, mejor adhesión y una composición química consistente. Este cambio digital no solo mejora la confiabilidad del producto, sino que también reduce el desperdicio de material y los costos operativos. Jugadores globales como voestalpine y Kobe Steel están incorporando tecnologías de la Industria 4.0 para modernizar sus líneas de fabricación de electrodos y satisfacer la creciente demanda de consumibles de soldadura de alta calidad.
Otra perspectiva notable para los próximos años es la diversificación de los revestimientos de electrodos adaptados a aplicaciones especializadas, que incluyen aceros de alta resistencia, soldadura de metales disímiles y estructuras en alta mar. Hay un creciente interés en revestimientos aleados que proporcionan resistencia a la corrosión superior y resistencia mecánica, especialmente para los sectores de petróleo y gas, construcción naval e infraestructura. A medida que las industrias continúan empujando los límites del rendimiento de los materiales, se espera que los productores de electrodos intensifiquen su investigación en ingredientes de flujo novedosos y mejoras de nanomateriales.
En general, la industria de formulación de revestimientos de electrodos de soldadura entre 2025 y 2030 se caracteriza por la innovación, la adaptación regulatoria y la búsqueda de productos sostenibles y de alto rendimiento. Con inversiones continuas de fabricantes establecidos y una clara tendencia hacia la digitalización y la personalización, el sector está bien posicionado para un crecimiento robusto y un avance tecnológico en el futuro cercano.
Pronóstico del Mercado Global: Factores de Crecimiento y Puntos Calientes Regionales
El mercado global para formulación de revestimientos de electrodos de soldadura está preparado para un crecimiento constante a través de 2025 y en los años posteriores, impulsado por el aumento de la industrialización, la expansión de infraestructura y la evolución de los estándares de manufactura. La creciente demanda de juntas de soldadura de calidad en la construcción, la construcción naval, la industria automotriz y el sector energético está promoviendo avances en los revestimientos de electrodos, principalmente para mejorar la estabilidad del arco, tasas de deposición e integridad de la soldadura.
Asia-Pacífico continúa dominando como el punto caliente regional más grande y de más rápido crecimiento, liderado por países como China, India y las economías del sudeste asiático. Las actividades de construcción y manufactura en auge de la región están alimentando la necesidad de tecnologías de electrodos sofisticadas y materiales de revestimiento confiables. Los principales jugadores de la industria como Lincoln Electric, ESAB y voestalpine Böhler Welding han aumentado su presencia e inversiones en la región para atender la demanda creciente y localizar las cadenas de suministro.
En América del Norte y Europa, el mercado está moldeado por un enfoque en la automatización, materiales de alto rendimiento y cumplimiento con rigurosos estándares ambientales, especialmente en relación con las emisiones de ingredientes de flujo y sustancias peligrosas en los revestimientos de electrodos. Las innovaciones en electrodos de bajo hidrógeno y revestidos de rutilo están ganando tracción, ya que los usuarios finales buscan formulaciones que minimicen los defectos y mejoren la calidad de la soldadura en aplicaciones de infraestructura crítica y energía. Según actualizaciones técnicas de ESAB y Lincoln Electric, la I+D se está enfocando cada vez más en aglutinantes amigables con el medio ambiente y aditivos de aleación avanzados que optimizan el rendimiento del arco mientras reducen el impacto ecológico.
Se espera que América Latina, liderada por Brasil y México, experimente un crecimiento moderado, impulsada por los sectores de petróleo y gas y de ingeniería pesada. Mientras tanto, en Oriente Medio y África, se espera que los proyectos de infraestructura y un cambio gradual hacia la manufactura local generen nueva demanda de electrodos de soldadura recubiertos, especialmente aquellos adaptados a entornos operativos difíciles y diversos metales base.
Los factores de crecimiento en todas las regiones incluyen la continua transición hacia infraestructura de energía renovable (eólica, solar, hidroeléctrica), que requiere consumibles de soldadura avanzados para fabricación y mantenimiento. Además, la adopción de prácticas de Industria 4.0 y la digitalización de las operaciones de soldadura están influyendo indirectamente en los requisitos de formulación de electrodos, con un énfasis en la consistencia, trazabilidad y adaptabilidad a los sistemas de soldadura automatizados (voestalpine Böhler Welding).
Mirando hacia adelante, con las inversiones en infraestructura e industriales proyectadas para aumentar a nivel mundial, se espera que el mercado de formulaciones de revestimientos de electrodos de soldadura sea testigo de una innovación incremental, diversificación regional y un crecimiento sostenido a través de 2025 y más allá.
Tecnologías Emergentes en Formulación de Revestimiento de Electrodos
El campo de la formulación de revestimientos de electrodos de soldadura está experimentando cambios significativos en 2025, impulsados por avances en la ciencia de materiales, automatización y exigencias de sostenibilidad. Tradicionalmente, los revestimientos de electrodos se han basado en formulaciones de rutilo, básicas (cal) o celulosa, cada una ofreciendo características de soldadura y aplicaciones únicas. Sin embargo, la demanda de un mejor rendimiento, menores emisiones y rentabilidad está impulsando la adopción de nuevas tecnologías y enfoques en este sector.
Un desarrollo importante es la integración de nanomateriales y aditivos avanzados en las formulaciones de revestimiento. La adición de óxidos de tamaño nano y elementos de tierras raras ha demostrado mejorar la estabilidad del arco, aumentar las tasas de deposición y mejorar la despegabilidad de la escoria, lo cual es especialmente relevante para sectores de especificaciones altas como la soldadura en alta mar o tuberías. Fabricantes líderes como Lincoln Electric y ESAB están invirtiendo en investigación sobre dichos aditivos para optimizar el rendimiento del electrodo y la calidad de la soldadura mientras reducen las proyecciones y humos.
La automatización y digitalización también están moldeando la producción de revestimientos de electrodos. Se están implementando sistemas de dosificación de precisión y tecnologías de mezcla automatizada para asegurar un grosor y composición de revestimiento consistentes. Empresas como voestalpine están incorporando controles de proceso digitales para mejorar la uniformidad del revestimiento y reducir el desperdicio de materiales, lo que no solo mejora la calidad del producto final, sino que también se alinea con el creciente énfasis en la sostenibilidad en toda la industria de la soldadura.
Las regulaciones ambientales continúan influyendo en la formulación de revestimientos de electrodos de soldadura. Hay una clara tendencia hacia la reducción de emisiones peligrosas, particularmente de cromo hexavalente y otros elementos potencialmente tóxicos. Los fabricantes están respondiendo reformulando revestimientos para excluir o minimizar tales sustancias, en línea con las normas en evolución establecidas por organizaciones como American Welding Society. Esto está impulsando la adopción de aglutinantes y agentes de flujo alternativos que mantienen el rendimiento de la soldadura mientras abordan preocupaciones de salud y seguridad.
Mirando hacia adelante en los próximos años, las perspectivas para la formulación de revestimientos de electrodos de soldadura incluyen una mayor investigación en materiales ecológicos, como aglutinantes de base biológica y minerales reciclados, y el desarrollo de revestimientos «inteligentes» que pueden adaptarse a las condiciones de soldadura. A medida que la industria continúa convergiendo en estándares de calidad y ambientales más estrictos, se espera que la integración de materiales avanzados y tecnologías de fabricación acelere, reforzando el papel de la innovación en satisfacer las necesidades evolutivas de los profesionales de la soldadura en todo el mundo.
Materias Primas: Abastecimiento, Sostenibilidad y Dinámicas de la Cadena de Suministro
La formulación de revestimientos de electrodos de soldadura depende en gran medida de la disponibilidad continua y la calidad de materias primas específicas, como rutilo, ilmenita, calcita, feldespato, mineral de manganeso y varios aglutinantes. En 2025, las dinámicas de suministro global de estos minerales están siendo moldeadas por alineaciones geopolíticas cambiantes, requisitos de sostenibilidad y la creciente demanda de proyectos de infraestructura y manufactura. Los principales fabricantes de electrodos están priorizando cadenas de suministro seguras y trazables, a menudo diversificando sus estrategias de abastecimiento para mitigar los riesgos asociados con interrupciones regionales y la volatilidad de precios.
Uno de los materiales principales, el rutilo (un mineral de dióxido de titanio), está experimentando un escrutinio creciente debido a las regulaciones ambientales en los principales países productores. Esto ha llevado a fabricantes como Lincoln Electric y ESAB a explorar ubicaciones de abastecimiento alternativas y aumentar el contenido reciclado en sus revestimientos de electrodos. El mineral de manganeso, esencial para ciertos tipos de electrodos de bajo hidrógeno y alta resistencia, enfrenta desafíos similares, lo que impulsa a las empresas a implementar un mejor filtrado de proveedores e invertir en resiliencia logística.
La sostenibilidad es una prioridad creciente, con productores de electrodos adoptando protocolos de abastecimiento responsable alineados con estándares globales como ISO 14001. Por ejemplo, voestalpine ha publicitado su compromiso de reducir la huella de carbono de sus consumibles de soldadura integrando materias primas recicladas y de bajo impacto. El uso de aglutinantes y flujos de base biológica también está bajo investigación, ya que los fabricantes buscan reducir emisiones y abordar las demandas de los usuarios finales por productos más ecológicos.
La transparencia de la cadena de suministro se está volviendo más sofisticada, con herramientas digitales que permiten el seguimiento en tiempo real de materias primas desde la mina hasta la instalación de fabricación. Esta digitalización está ayudando a empresas como Böhler Welding a adaptarse rápidamente a cambios en el mercado y mantener una calidad constante en las mezclas de revestimiento de electrodos. La tendencia hacia la localización de cadenas de suministro, particularmente para minerales críticos, continúa, con varios fabricantes invirtiendo en capacidades de procesamiento regional para reducir las emisiones de transporte y aumentar la resiliencia ante incertidumbres en el comercio internacional.
Mirando hacia adelante, las perspectivas para el abastecimiento de materias primas en la formulación de revestimientos de electrodos de soldadura están estrechamente relacionadas con los avances en tecnologías de reciclaje, desarrollos regulatorios y las demandas cambiantes de la manufactura global. Se espera que las empresas activamente involucradas en la producción de electrodos profundicen colaboraciones con empresas mineras y de procesamiento de minerales para asegurar insumos sostenibles y de alta pureza y para reducir aún más el impacto ambiental a lo largo de sus cadenas de suministro.
Cumplimiento Regulatorio y Normas Industriales (AWS, ISO)
La formulación de revestimientos de electrodos de soldadura en 2025 está intrínsecamente gobernada por una matriz de requisitos de cumplimiento regulatorio y normas industriales, especialmente las establecidas por la American Welding Society (AWS) y la Organización Internacional de Normalización (ISO). Estas normas aseguran que los revestimientos de electrodos cumplan con los criterios estrictos de seguridad, rendimiento e impacto ambiental. Las empresas y los fabricantes deben mantenerse al tanto de las regulaciones en evolución para mantener el acceso al mercado y asegurar la confiabilidad del producto.
En los Estados Unidos, la American Welding Society mantiene un conjunto integral de normas como AWS A5.1 (para electrodos de acero carbono) y AWS A5.4 (para electrodos de acero inoxidable), que especifican composiciones químicas permisibles, tipos de revestimiento, propiedades mecánicas y métodos de prueba. Estos requisitos se actualizan regularmente para reflejar los avances en la metalurgia de soldadura, cambios en las normas de seguridad laboral y la introducción de nuevas tecnologías de revestimiento, tales como formulaciones de bajo hidrógeno y amigables con el medio ambiente. Las normas de AWS son ampliamente reconocidas en América del Norte y a menudo sirven como punto de referencia para los fabricantes que exportan a otras regiones.
A nivel global, las normas de ISO—particularmente ISO 2560 (electrodos revestidos para soldadura por arco metálico manual de aceros no aleados y de grano fino) y ISO 3580 (electrodos revestidos para soldadura por arco metálico manual de aceros resistentes a la deformación)—proporcionan un marco armonizado para las formulaciones de revestimientos de electrodos. Estas normas están siendo adoptadas cada vez más en Europa, Asia y mercados emergentes, requiriendo a los fabricantes sincronizar el desarrollo de productos y los sistemas de control de calidad en consecuencia. Las normas ISO también enfatizan la trazabilidad, calidad de lote consistente y requisitos de etiquetado, que se están volviendo más críticos a medida que las cadenas de suministro se globalizan.
En 2025, las tendencias regulatorias también están siendo moldeadas por una mayor atención a consideraciones ambientales, de salud y seguridad (EHS). Por ejemplo, la reducción de sustancias peligrosas—como el cromo hexavalente o ciertos fluorados—en los revestimientos de electrodos es un mandato creciente, alineándose con iniciativas globales como REACH en Europa. Fabricantes como Lincoln Electric y ESAB continúan innovando en el desarrollo de revestimientos que cumplen con estas directrices ambientales mientras mantienen la calidad de la soldadura y la eficiencia operativa.
Mirando hacia adelante, las partes interesadas de la industria anticipan un mayor endurecimiento de los estándares, particularmente en lo que respecta a la trazabilidad de materias primas, emisiones durante la soldadura y reciclabilidad de electrodos agotados. Esto probablemente impulsará una mayor colaboración entre organismos de normalización, fabricantes y usuarios finales para desarrollar revestimientos que no solo sean conformes, sino también optimizados para aplicaciones emergentes, como la manufactura aditiva y aceros avanzados de alta resistencia.
Principales Manufacturers y Asociaciones Estratégicas (ESAB, Lincoln Electric, Bohler Welding)
En 2025, el mercado global de electrodos de soldadura está siendo significativamente moldeado por las estrategias de innovación y colaboración de los principales fabricantes, particularmente en el área de formulaciones de revestimiento de electrodos. Empresas como ESAB, Lincoln Electric y Bohler Welding (una marca de voestalpine Böhler Welding) están a la vanguardia del desarrollo de revestimientos avanzados que mejoran la calidad de la soldadura, aumentan la productividad y abordan las cambiantes exigencias regulatorias y ambientales.
Las últimas tendencias en la formulación de revestimientos de electrodos se centran en aumentar la eficiencia de deposición, reducir el salpicado y lograr propiedades mecánicas específicas mientras minimizan las emisiones peligrosas. Por ejemplo, ESAB continúa invirtiendo en composiciones de flujo propietarias, con un creciente énfasis en recubrimientos de bajo hidrógeno y basados en rutilo destinados a cumplir con estándares más estrictos para la integridad de la soldadura y la seguridad del operador. Sus esfuerzos de I+D están cada vez más dirigidos hacia la sostenibilidad, incluida la reducción del cromo hexavalente y otros elementos potencialmente peligrosos en los materiales de revestimiento.
Lincoln Electric también ha intensificado sus esfuerzos en innovación de revestimientos de electrodos, centrándose en formular revestimientos que permiten soldaduras de alto rendimiento en sectores exigentes como el offshore, energía e infraestructura. Los recientes avances de la empresa incluyen el desarrollo de electrodos con estabilidad de arco mejorada y liberación de escoria optimizada, lo que mejora la eficiencia del flujo de trabajo y reduce el tiempo de limpieza posterior a la soldadura. Las colaboraciones continuas de Lincoln Electric con productores de acero y usuarios finales permiten la prototipación rápida y validación de campo de nuevas tecnologías de revestimiento, reforzando su posición como líder tecnológico en el sector.
Mientras tanto, Bohler Welding enfatiza soluciones personalizadas en revestimientos de electrodos, dirigiéndose tanto a aplicaciones comunes como altamente especializadas. A través de asociaciones estratégicas con importantes empresas de fabricación y consorcios industriales, Bohler ha introducido electrodos con elementos de aleación avanzados en el revestimiento, apoyando aplicaciones críticas como soldadura nuclear y criogénica. Su enfoque en la digitalización y la automatización de procesos se extiende a la fabricación de electrodos, permitiendo un control preciso sobre el grosor y la composición del revestimiento.
Mirando hacia adelante, los próximos años probablemente verán más asociaciones estratégicas a lo largo de la cadena de suministro, a medida que los proveedores de materiales, instituciones de investigación y fabricantes trabajen en conjunto para co-desarrollar revestimientos que cumplan con los estándares emergentes de resistencia, resistencia a la corrosión y seguridad ambiental. Con jugadores importantes como ESAB, Lincoln Electric y Bohler Welding invirtiendo fuertemente tanto en ciencia de formulación como en innovación colaborativa, se espera que el segmento de revestimiento de electrodos siga avanzando en rendimiento y sostenibilidad.
Pipeline de I+D: Innovaciones en Rendimiento y Eficiencia de Costos
En 2025, el pipeline de investigación y desarrollo (I+D) para formulaciones de revestimientos de electrodos de soldadura está caracterizado por una mezcla dinámica de mejoras incrementales e innovaciones disruptivas. Los objetivos principales de la industria siguen siendo la mejora de la calidad de la soldadura, la reducción de los costos de producción y la alineación con estándares de seguridad y medio ambiente cada vez más estrictos. Los fabricantes líderes en el mercado y los consorcios de la industria están enfocándose tanto en el refinamiento de los revestimientos tradicionales como en la exploración de nuevos materiales para electrodos preparados para el futuro.
Una tendencia significativa en el pipeline de I+D involucra la optimización de composiciones de flujo. Los revestimientos tradicionales—como formulaciones de rutilo, básicas y de celulosa—se están modificando sistemáticamente para mejorar la estabilidad del arco, reducir el salpicado y mejorar la despegabilidad de la escoria. Por ejemplo, fabricantes como Lincoln Electric y ESAB están involucrados activamente en el desarrollo de recetas de flujo avanzadas que incorporan elementos de microaleación y mezclas minerales diseñadas. Estos ajustes no solo incrementan propiedades mecánicas como la resistencia a la tracción y la resistencia al impacto, sino que también ofrecen un mejor aspecto de la soldadura y reducen el tiempo de limpieza posterior a la soldadura.
Otro foco es la integración de materiales sostenibles y amigables con el medio ambiente en los revestimientos de electrodos. Con los marcos regulatorios volviéndose más estrictos en torno a sustancias peligrosas, los equipos de I+D están evaluando alternativas a compuestos tradicionales como aglutinantes de silicato potásico y fluorados. Por ejemplo, Böhler Welding está experimentando con aglutinantes de base biológica y formulaciones de bajo polvo que minimizan las partículas en el aire durante la soldadura, abordando tanto la seguridad laboral como el impacto ambiental.
La eficiencia de costos sigue siendo un motor crítico, lo que impulsa la búsqueda de minerales de abastecimiento local y materias primas recicladas para reducir la dependencia de productos importados o volátiles. Varios proveedores líderes están invirtiendo en innovaciones de proceso que permiten el uso de aditivos de menor costo sin comprometer el rendimiento del electrodo. Este enfoque es especialmente relevante en regiones donde las interrupciones en la cadena de suministro o factores geopolíticos impactan el acceso a materias primas tradicionales.
Mirando hacia adelante, las perspectivas para I+D en la formulación de revestimientos de electrodos de soldadura en los próximos años apuntan hacia una mayor digitalización y la adopción de diseño basado en datos. Los fabricantes están aprovechando herramientas de simulación avanzadas y plataformas de formulación asistida por IA para prototipar y probar rápidamente nuevas composiciones, acortando ciclos de desarrollo y facilitando la personalización para aplicaciones específicas. Las colaboraciones estratégicas entre fabricantes, instituciones de investigación y organismos de la industria, como las promovidas por la American Welding Society, se espera que aceleren la innovación y la estandarización en todo el sector. En conjunto, estos avances señalan un paisaje robusto y orientado al futuro de I+D dedicado a combinar el rendimiento con los imperativos de costos y sostenibilidad.
Aplicaciones en Diferentes Sectores: Construcción, Energía, Automotor, y Más
La formulación de revestimientos de electrodos de soldadura juega un rol crucial en determinar el rendimiento y la idoneidad de los electrodos en varios sectores industriales. En 2025 y en los próximos años, se espera que los avances en tecnologías de revestimiento influyan significativamente en aplicaciones en construcción, energía, automotriz y otras industrias. La formulación de revestimientos de electrodos está adaptada para cumplir con los requisitos específicos de cada sector, como la resistencia mecánica, resistencia a la corrosión y calidad de la soldadura.
En el sector de la construcción, la demanda de aceros de alta resistencia y bajo aleación y técnicas de fabricación avanzadas ha impulsado a los fabricantes a desarrollar revestimientos de electrodos que mejoren la tenacidad del metal de soldadura y minimicen la formación de grietas inducidas por hidrógeno. Las innovaciones en formulaciones de revestimiento básico y de rutilo están permitiendo un rendimiento más confiable en infraestructuras críticas, como puentes y edificios de gran altura. Productores principales de electrodos como Lincoln Electric y ESAB están introduciendo activamente electrodos con mejor resistencia a la humedad y estabilidad del arco para abordar las necesidades de la industria de la construcción, particularmente en regiones con condiciones climáticas variables.
En el sector energético, incluyendo petróleo y gas, energía renovable y generación de electricidad, el enfoque está en electrodos que puedan resistir ambientes duros y condiciones de servicio críticas. Se están formulando revestimientos que incorporan elementos de aleación para mejorar la resistencia a la corrosión y al calor para cumplir con estrictos estándares industriales. Por ejemplo, Böhler Welding está desarrollando revestimientos de electrodos especializados para el mantenimiento de plantas de energía y plataformas en alta mar, abordando los requerimientos materiales y regulatorios en evolución del sector.
La industria automotriz está experimentando una adopción rápida de aceros avanzados de alta resistencia y materiales ligeros, lo que requiere revestimientos de electrodos que ofrezcan perfiles de cordones de soldadura precisos y un mínimo de salpicaduras. Las formulaciones de revestimiento se están optimizando cada vez más para sistemas de soldadura robótica y automatizada, apoyando entornos de fabricación de alto rendimiento. Empresas como Kobe Steel (KOBELCO) se están enfocando en revestimientos de bajo humo y amigables con el medio ambiente para alinearse con iniciativas de sostenibilidad automotriz y regulaciones de seguridad laboral.
Más allá de estos sectores, las aplicaciones en la construcción naval, ferrocarriles y fabricación de maquinaria pesada también se benefician de formulaciones de revestimiento de electrodos adaptadas. La evolución continua en la química de los electrodos permite a los fabricantes abordar diversos desafíos de soldadura, desde unir metales disímiles hasta lograr propiedades mecánicas superiores en secciones gruesas. Con inversiones continuas en I+D y una creciente demanda de calidad y sostenibilidad, se espera que los próximos años vean más innovaciones específicas por sector en los revestimientos de electrodos de soldadura, apoyando la productividad y el cumplimiento en todas las industrias.
Desafíos: Impacto Ambiental, Costos y Garantía de Calidad
La formulación de revestimientos de electrodos de soldadura en 2025 enfrenta un conjunto complejo de desafíos, centrándose principalmente en la reducción del impacto ambiental, el control de costos y la garantía de calidad consistente. A medida que las regulaciones ambientales globales se endurecen, especialmente en relación con sustancias peligrosas en los procesos de manufactura, la industria de la soldadura está bajo una creciente presión para reformular revestimientos con el fin de minimizar emisiones de gases nocivos, metales pesados y partículas. Por ejemplo, la restricción de ciertos elementos como el cromo y el fluor—comúnmente encontrados en algunos revestimientos de electrodos debido a sus propiedades de soldadura beneficiosas—requiere la búsqueda de materiales alternativos o tecnologías de captura avanzadas que no comprometan la calidad de la soldadura.
La gestión de costos es otro obstáculo significativo. Los precios de materias primas clave, como rutilo, polvo de hierro y varios aglutinantes minerales, han experimentado volatilidad debido a interrupciones en la cadena de suministro y el aumento de la demanda a través de diferentes sectores. Esta volatilidad impacta directamente en la estructura de costos de los electrodos recubiertos. Los fabricantes están explorando el reciclaje y reprocesamiento de materiales en desecho para amortiguar estas fluctuaciones, pero la integración de contenido reciclado debe equilibrarse con los estrictos estándares de calidad requeridos por los usuarios finales en industrias críticas como la automotriz, la construcción naval y la infraestructura.
La garantía de calidad sigue siendo primordial, ya que incluso pequeñas inconsistencias en el grosor del revestimiento, la composición o el contenido de humedad pueden resultar en defectos de soldadura, reducción del rendimiento mecánico e incrementos en los costos de retrabajo. Para abordar esto, las empresas están invirtiendo en automatización, monitoreo en tiempo real de procesos y técnicas avanzadas de caracterización de materiales. La adopción de visión artificial y sensores en línea está mejorando gradualmente la consistencia de lote a lote, permitiendo un mejor control sobre la aplicación y procesos de secado del revestimiento. Por ejemplo, los principales fabricantes como ESAB y Lincoln Electric están integrando sistemas de gestión de calidad digitales para asegurar que los electrodos de soldadura cumplan con los estándares globales como AWS y EN ISO.
Mirando hacia el futuro, las perspectivas de la industria para los próximos años sugieren una aceleración en la investigación y desarrollo centrada en materiales de revestimiento sostenibles, como aglutinantes de base biológica y flujos de baja toxicidad. La colaboración de la industria y asociaciones con instituciones académicas se espera que jueguen un papel clave en el desarrollo de nuevas químicas que sean tanto ecológicas como rentables, sin sacrificar la calidad de la soldadura. Al mismo tiempo, se espera que las agencias regulatorias y los organismos de la industria—incluyendo la American Welding Society—actualicen los estándares para reflejar avances en la ciencia de formulación, empujando a los fabricantes a adaptarse continuamente. Estos impulsores convergentes subrayan la necesidad de un enfoque equilibrado en la formulación de revestimientos de electrodos, uno que alinee la responsabilidad ambiental con la eficiencia operativa y el rendimiento de alta calidad.
Perspectiva Futura: Ventaja Competitiva y Oportunidades a Largo Plazo
La perspectiva futura para la formulación de revestimientos de electrodos de soldadura en 2025 y los años siguientes está caracterizada por una creciente sofisticación tecnológica, demandas regulatorias y requisitos cambiantes de los usuarios finales, todos los cuales están dando forma a la dinámica competitiva del sector y oportunidades a largo plazo. A medida que sectores clave como la construcción, la automoción, la construcción naval y la infraestructura energética continúan demandando una mayor productividad y una mejor calidad de soldadura, los fabricantes de electrodos se están enfocando en químicas de revestimiento avanzadas que brindan un rendimiento mejorado y cumplen con estándares ambientales más estrictos.
Una de las tendencias más significativas es el desarrollo acelerado de revestimientos de bajo hidrógeno y amigables con el medio ambiente. Estas formulaciones ayudan a mitigar la formación de grietas inducidas por hidrógeno y reducen las emisiones de humos peligrosos, alineándose con regulaciones de seguridad ocupacional y ambientales más estrictas que se anticipan en los principales mercados. Los principales productores de electrodos están invirtiendo en investigación para desarrollar recubrimientos con estabilidad de arco mejorada, menor salpicado y mejor desprendimiento de escoria, proporcionando beneficios tangibles de productividad para los fabricantes. Por ejemplo, Lincoln Electric Holdings y ESAB han discutido públicamente su compromiso con la innovación en electrodos, incluyendo composiciones de flujo diseñadas para aplicaciones de alta resistencia y especiales.
La digitalización y la automatización en los procesos de soldadura también están influyendo en el desarrollo de revestimientos de electrodos. La integración de soluciones de Industria 4.0—como monitoreo de calidad en tiempo real y sistemas automatizados de almacenamiento/manejo—requiere electrodos con integridad de revestimiento consistente y características de fusión predecibles. Esto está impulsando a los fabricantes a refinar sus métodos de mezcla de polvo, extrusión y curado para lograr tolerancias de calidad más estrictas, como lo han señalado empresas como voestalpine Böhler Welding.
Las oportunidades a largo plazo probablemente surgirán de la creciente adopción de aleaciones de alto rendimiento y unión de materiales disímiles, especialmente a medida que las industrias se transiten hacia estructuras más ligeras y más resistentes a la corrosión. Los revestimientos de electrodos optimizados para tales materiales—por ejemplo, aceros inoxidables, aleaciones a base de níquel y aceros avanzados de alta resistencia—se espera que vean una mayor demanda. Las empresas con robustas capacidades de I+D y cadenas de suministro verticalmente integradas están en una buena posición para obtener una ventaja competitiva, ya que pueden adaptar más rápidamente las formulaciones para cumplir con requisitos específicos de clientes y regulaciones.
Geográficamente, Asia-Pacífico sigue siendo un motor importante para el crecimiento en volumen, con inversiones en infraestructura y manufactura. Sin embargo, América del Norte y Europa están marcando el rumbo para el cumplimiento regulatorio y la manufactura sostenible, lo que está impulsando a los proveedores globales a innovar en consecuencia. El panorama competitivo recompensará cada vez más a aquellos capaces de ofrecer revestimientos de electrodos de alto rendimiento, conformes y rentables, subrayando la importancia de los avances continuos en la formulación para mantener un liderazgo sostenido en el sector de consumibles de soldadura.