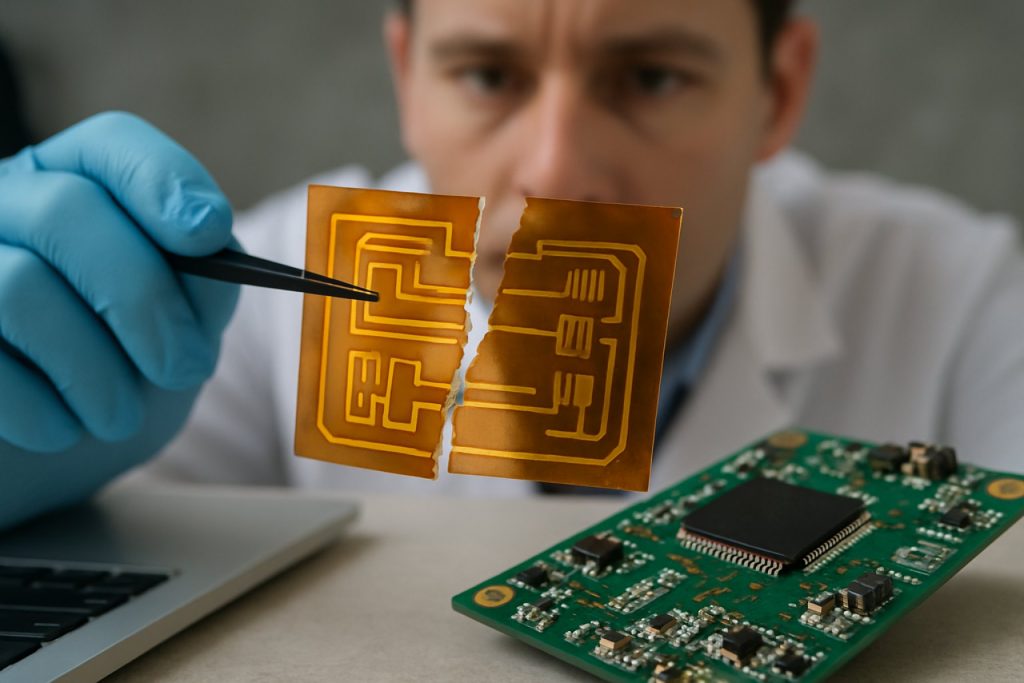
Self-Healing Polymer Electronics in 2025: Transforming Reliability and Longevity in Next-Gen Devices. Explore How This Game-Changing Technology Is Set to Redefine the Electronics Industry Over the Next Five Years.
- Executive Summary: 2025 Market Snapshot & Key Trends
- Technology Overview: Mechanisms of Self-Healing Polymers
- Major Players & Innovators: Company Strategies and Partnerships
- Current Applications: Wearables, Flexible Displays, and Sensors
- Emerging Use Cases: Automotive, Medical Devices, and IoT Integration
- Market Size & Forecast: 2025–2030 Growth Projections (CAGR ~28%)
- Supply Chain & Manufacturing Challenges
- Regulatory Landscape and Industry Standards
- Competitive Analysis: Differentiators and Barriers to Entry
- Future Outlook: R&D Directions and Commercialization Roadmap
- Sources & References
Executive Summary: 2025 Market Snapshot & Key Trends
The self-healing polymer electronics sector is poised for significant advancements and market expansion in 2025, driven by the convergence of material science innovation and the growing demand for resilient, long-lasting electronic devices. Self-healing polymers—engineered to autonomously repair micro-cracks and mechanical damage—are increasingly being integrated into flexible circuits, wearable devices, and next-generation sensors. This technology addresses critical challenges in device durability and lifecycle, particularly as electronics become thinner, more flexible, and more embedded in everyday environments.
In 2025, leading electronics manufacturers and material suppliers are accelerating the commercialization of self-healing polymer solutions. Companies such as LG Electronics and Samsung Electronics have publicly demonstrated prototypes of flexible displays and wearable devices utilizing self-healing coatings and substrates, aiming to reduce screen scratches and extend product lifespans. Meanwhile, specialty chemical producers like DuPont and Covestro are scaling up production of advanced polymer formulations with intrinsic self-repair capabilities, targeting both consumer electronics and industrial applications.
Key trends shaping the 2025 landscape include the integration of self-healing polymers into printed circuit boards (PCBs) and interconnects, where micro-damage can lead to device failure. Companies such as DuPont are collaborating with electronics manufacturers to develop self-healing dielectric materials for high-density, flexible PCBs. In parallel, the automotive and medical device sectors are exploring self-healing electronics for safety-critical and wearable applications, with suppliers like Covestro and BASF investing in R&D partnerships to tailor polymer properties for specific use cases.
Data from industry sources indicate that the adoption of self-healing polymer electronics is expected to accelerate over the next few years, with pilot projects transitioning to mass production by 2026–2027. The focus is on improving healing efficiency at room temperature, reducing material costs, and ensuring compatibility with existing manufacturing processes. The outlook for 2025 and beyond suggests that self-healing polymer electronics will move from niche applications to broader market segments, supported by ongoing investments from major electronics brands and material science leaders.
As the sector matures, collaboration between electronics OEMs, polymer suppliers, and research institutions will be critical to overcoming technical barriers and standardizing performance metrics. The next few years are likely to see the emergence of industry standards and certification programs, further accelerating the adoption of self-healing technologies in mainstream electronic products.
Technology Overview: Mechanisms of Self-Healing Polymers
Self-healing polymer electronics represent a rapidly advancing frontier in materials science, aiming to extend device lifespans, improve reliability, and reduce maintenance costs by enabling electronic components to autonomously repair damage. The core mechanisms underpinning self-healing in polymer electronics can be broadly categorized into intrinsic and extrinsic approaches, each leveraging distinct chemical and physical principles.
Intrinsic self-healing relies on the inherent properties of the polymer matrix. This typically involves dynamic covalent bonds (such as Diels-Alder reactions, disulfide bonds, or imine bonds) or supramolecular interactions (hydrogen bonding, metal-ligand coordination, π-π stacking) that can reversibly break and reform under specific stimuli like heat, light, or pressure. For example, dynamic Diels-Alder chemistry has been widely adopted in flexible circuit substrates, allowing microcracks to close and restore conductivity when heated to moderate temperatures. In 2025, research groups and industry players are increasingly focusing on optimizing these chemistries for ambient or low-temperature healing, which is crucial for practical electronics applications.
Extrinsic self-healing, on the other hand, incorporates microcapsules or vascular networks filled with healing agents into the polymer matrix. When damage occurs, these reservoirs rupture, releasing the healing agent to the affected area, where it polymerizes and restores the material’s integrity. While this approach has seen success in coatings and structural composites, its integration into thin-film electronics remains challenging due to the need for miniaturization and compatibility with electronic performance.
A significant technological milestone in recent years has been the development of conductive self-healing polymers. These materials combine electrical conductivity with self-repair capabilities, often by embedding conductive fillers (such as silver nanowires, carbon nanotubes, or graphene) within a dynamic polymer matrix. Companies like DuPont and Kuraray are actively exploring advanced polymer formulations for flexible and wearable electronics, with a focus on maintaining conductivity after repeated damage and healing cycles. Additionally, SABIC is investing in specialty polymers that exhibit both mechanical and electrical self-healing, targeting applications in sensors and soft robotics.
Looking ahead to the next few years, the outlook for self-healing polymer electronics is promising. The convergence of advanced polymer chemistry, nanomaterials, and device engineering is expected to yield materials that heal at room temperature, operate under real-world mechanical stresses, and are compatible with scalable manufacturing processes. Industry collaborations and pilot-scale demonstrations are anticipated, particularly in sectors such as flexible displays, medical wearables, and soft robotics, where durability and reliability are paramount. As the field matures, standardization efforts and performance benchmarks will likely be established by industry bodies to accelerate commercialization and adoption.
Major Players & Innovators: Company Strategies and Partnerships
The self-healing polymer electronics sector is rapidly evolving, with a growing number of established electronics manufacturers, chemical companies, and innovative startups driving advancements through strategic partnerships and targeted R&D investments. As of 2025, the competitive landscape is shaped by a blend of global corporations and agile newcomers, each leveraging unique capabilities to address the technical and commercial challenges of self-healing materials in electronic applications.
Among the most prominent players, BASF stands out for its extensive portfolio in advanced polymers and ongoing research into self-healing materials. BASF’s strategy involves close collaboration with electronics manufacturers to tailor polymer formulations for flexible circuits, sensors, and wearable devices. The company’s open innovation approach includes partnerships with universities and technology incubators, aiming to accelerate the commercialization of self-healing solutions.
Another key innovator is Dow, which has invested heavily in the development of self-healing silicones and polyurethanes for use in flexible displays and protective coatings. Dow’s recent alliances with Asian consumer electronics firms underscore its commitment to integrating self-healing polymers into next-generation smartphones and IoT devices. The company’s focus on scalable manufacturing processes is expected to be a differentiator as demand for robust, long-lasting electronics grows.
In Asia, Samsung Electronics is actively exploring self-healing materials for foldable and flexible devices. Samsung’s R&D division has filed multiple patents related to self-repairing display substrates and encapsulants, and the company is reportedly collaborating with specialty chemical suppliers to bring these innovations to market in the near term. This aligns with Samsung’s broader strategy to maintain leadership in advanced display technologies.
Startups are also making significant contributions. Companies such as Arkema are leveraging proprietary polymer chemistries to develop self-healing coatings and adhesives for printed electronics. Arkema’s partnerships with European research consortia and electronics OEMs are aimed at accelerating pilot-scale demonstrations and early commercial deployments.
Looking ahead, the next few years are expected to see intensified collaboration between material suppliers, device manufacturers, and research institutions. Industry alliances, such as those fostered by SEMI, are likely to play a pivotal role in setting standards and facilitating technology transfer. As self-healing polymer electronics move from laboratory prototypes to commercial products, the ability of major players to form effective partnerships and scale production will be critical to widespread adoption.
Current Applications: Wearables, Flexible Displays, and Sensors
Self-healing polymer electronics are rapidly transitioning from laboratory prototypes to real-world applications, particularly in wearables, flexible displays, and sensor technologies. As of 2025, the integration of self-healing capabilities into electronic devices is being driven by the demand for longer-lasting, more reliable, and flexible products that can withstand mechanical stress and minor damage without performance loss.
In the wearables sector, self-healing polymers are being incorporated into smartwatches, fitness bands, and health-monitoring patches. These materials enable devices to recover from scratches, cuts, and even partial breaks, extending their operational life and reducing electronic waste. Companies such as Samsung Electronics and LG Electronics have demonstrated interest in self-healing materials for next-generation wearable devices, focusing on both comfort and durability. For instance, self-healing elastomers and conductive inks are being used in flexible circuit boards and skin-contact sensors, allowing for repeated bending and stretching without loss of function.
Flexible displays represent another major application area. The push for foldable smartphones and rollable screens has accelerated the adoption of self-healing polymers that can repair surface scratches and microcracks autonomously. LG Electronics has previously showcased self-healing coatings in its flexible display prototypes, and ongoing research suggests that commercial devices with advanced self-healing layers could reach the market within the next few years. These developments are crucial for improving the longevity and user experience of foldable and rollable devices, which are otherwise prone to mechanical damage.
In the field of sensors, self-healing polymers are being utilized in both consumer and industrial applications. Wearable health sensors, environmental monitors, and soft robotics benefit from self-healing materials that maintain electrical conductivity and sensitivity after damage. Companies like DuPont are actively developing self-healing conductive materials for printed electronics, targeting applications in flexible sensors and smart textiles. These innovations are expected to enhance the reliability of sensor networks in harsh or dynamic environments, such as medical monitoring or industrial automation.
Looking ahead, the next few years are likely to see broader commercialization of self-healing polymer electronics, with ongoing improvements in healing speed, mechanical strength, and electrical performance. As manufacturing processes mature and costs decrease, self-healing features are expected to become standard in high-end wearables, flexible displays, and sensor platforms, further driving adoption across consumer and industrial markets.
Emerging Use Cases: Automotive, Medical Devices, and IoT Integration
Self-healing polymer electronics are rapidly transitioning from laboratory prototypes to real-world applications, with 2025 marking a pivotal year for their integration into automotive, medical device, and IoT sectors. These advanced materials, capable of autonomously repairing mechanical or electrical damage, are poised to address critical reliability and longevity challenges in next-generation electronic systems.
In the automotive industry, the push toward electrification and autonomous driving is intensifying the demand for robust, maintenance-free electronics. Self-healing polymers are being explored for use in flexible sensors, wiring harnesses, and touch interfaces, where microcracks or physical stress can otherwise lead to costly failures. Major automotive suppliers such as Continental AG and Robert Bosch GmbH have publicly highlighted research into advanced materials, including self-healing polymers, for future vehicle interiors and sensor systems. These materials promise to extend the service life of critical components, reduce warranty costs, and improve safety by maintaining sensor integrity in harsh environments.
In medical devices, the integration of self-healing polymer electronics is particularly promising for wearable and implantable technologies. The ability of these materials to recover from mechanical deformation or micro-damage is crucial for devices that must conform to dynamic biological tissues. Companies such as Medtronic and Boston Scientific are actively investigating flexible, biocompatible electronics for next-generation health monitoring and therapeutic devices. Self-healing capabilities could enable longer device lifespans, reduce the need for surgical replacements, and enhance patient safety by ensuring continuous operation even after minor damage.
The Internet of Things (IoT) sector stands to benefit significantly from self-healing polymer electronics, particularly as the number of connected devices is projected to surpass 30 billion globally by 2025. The distributed and often inaccessible nature of IoT nodes makes maintenance challenging. Self-healing materials can help ensure the reliability of flexible sensors, antennas, and energy-harvesting components deployed in smart infrastructure, agriculture, and industrial monitoring. Leading electronics manufacturers such as Samsung Electronics and LG Electronics have demonstrated interest in self-healing materials for flexible displays and wearable devices, signaling a broader industry shift toward resilient, low-maintenance electronics.
Looking ahead, the next few years are expected to see pilot deployments and early commercialization of self-healing polymer electronics across these sectors. As manufacturing processes mature and material costs decrease, adoption is likely to accelerate, driven by the need for durable, reliable, and maintenance-free electronic systems in increasingly demanding environments.
Market Size & Forecast: 2025–2030 Growth Projections (CAGR ~28%)
The global market for self-healing polymer electronics is poised for robust expansion between 2025 and 2030, with industry consensus projecting a compound annual growth rate (CAGR) of approximately 28%. This surge is driven by escalating demand for flexible, durable, and reliable electronic components across sectors such as consumer electronics, automotive, healthcare, and emerging IoT applications. The integration of self-healing polymers into electronic devices addresses critical challenges related to device longevity, maintenance costs, and sustainability, positioning the technology as a key enabler for next-generation electronics.
In 2025, the market is expected to reach a valuation in the low hundreds of millions USD, with rapid scaling anticipated as commercialization efforts intensify. Leading materials suppliers and electronics manufacturers are accelerating R&D and pilot-scale production. For instance, Dow and DuPont—both global leaders in advanced materials—have announced initiatives to develop and supply self-healing polymer formulations tailored for flexible circuits, wearable sensors, and protective coatings. These companies leverage their extensive polymer science expertise and global manufacturing footprints to support the transition from laboratory-scale innovation to industrial-scale deployment.
In Asia, major electronics manufacturers such as Samsung Electronics and LG Electronics are actively exploring the integration of self-healing materials into flexible displays, batteries, and smart device casings. These efforts are supported by collaborations with regional chemical giants and research institutes, aiming to secure early-mover advantages in high-growth segments like foldable smartphones and wearable health monitors. Meanwhile, European firms including BASF are investing in the development of self-healing coatings and encapsulants for automotive electronics and energy storage systems, targeting enhanced reliability and reduced lifecycle costs.
The outlook for 2025–2030 is characterized by a transition from niche, high-value applications to broader adoption in mainstream electronics. Key growth drivers include the proliferation of connected devices, increasing miniaturization, and regulatory pressures for sustainable materials. As manufacturing processes mature and costs decline, self-healing polymer electronics are expected to penetrate mass-market applications, with Asia-Pacific and North America leading demand growth. Strategic partnerships between material suppliers, OEMs, and device integrators will be critical to overcoming technical and scalability challenges, ensuring that the sector sustains its projected high growth trajectory through the end of the decade.
Supply Chain & Manufacturing Challenges
The supply chain and manufacturing landscape for self-healing polymer electronics in 2025 is characterized by both rapid innovation and significant hurdles. As demand for flexible, durable, and repairable electronic devices grows—spanning applications from wearable health monitors to automotive sensors—manufacturers are racing to scale up production of self-healing materials and integrate them into complex electronic assemblies.
A primary challenge lies in the synthesis and consistent quality control of self-healing polymers. These materials often require precise formulation of dynamic covalent bonds or supramolecular interactions, which can be sensitive to impurities and process variations. Leading chemical suppliers such as BASF and Dow have invested in advanced polymerization techniques and real-time monitoring systems to ensure batch-to-batch consistency, but scaling these processes from laboratory to industrial volumes remains a bottleneck. The need for specialized monomers and crosslinkers, not always available in bulk, further complicates procurement and cost structures.
Integration of self-healing polymers into electronic devices introduces additional manufacturing complexities. Unlike conventional rigid substrates, self-healing materials often exhibit viscoelasticity and thermal sensitivity, requiring adaptation of standard electronics assembly lines. Companies such as Samsung Electronics and LG Electronics—both active in flexible and wearable electronics—are reportedly developing proprietary lamination and encapsulation techniques to accommodate these novel materials. However, ensuring reliable electrical performance after repeated self-healing cycles is an ongoing concern, necessitating new testing protocols and quality assurance standards.
Supply chain resilience is another pressing issue. The global electronics industry has faced disruptions in recent years due to geopolitical tensions and raw material shortages. For self-healing electronics, the reliance on specialty chemicals and advanced manufacturing equipment—often sourced from a limited number of suppliers—exacerbates vulnerability to such disruptions. Industry groups like the SEMI are advocating for greater supply chain transparency and regional diversification to mitigate these risks.
Looking ahead, the outlook for self-healing polymer electronics manufacturing is cautiously optimistic. Major material suppliers are expanding production capacity, and electronics manufacturers are investing in pilot lines to refine integration processes. Collaborative efforts between material scientists, equipment makers, and end-users are expected to accelerate standardization and cost reduction. Nevertheless, widespread commercialization will depend on overcoming persistent challenges in material scalability, process compatibility, and supply chain robustness over the next several years.
Regulatory Landscape and Industry Standards
The regulatory landscape and industry standards for self-healing polymer electronics are rapidly evolving as the technology matures and moves toward commercialization. In 2025, the sector is witnessing increased attention from both international standards organizations and national regulatory bodies, driven by the growing integration of self-healing materials in consumer electronics, automotive, and medical devices.
Currently, there is no single, unified global standard specifically dedicated to self-healing polymer electronics. However, existing frameworks for electronic materials and flexible electronics are being adapted to accommodate the unique properties of self-healing systems. The International Organization for Standardization (ISO) and the International Electrotechnical Commission (IEC) are actively reviewing standards related to polymeric materials, reliability testing, and safety protocols, with working groups considering amendments to address self-healing functionalities. For example, ISO/TC 61 (Plastics) and IEC TC 119 (Printed Electronics) are both relevant committees where discussions on self-healing materials are taking place.
In the United States, the ASTM International Committee D20 on Plastics and Committee F42 on Additive Manufacturing are evaluating test methods for mechanical and electrical self-repair in polymers. These efforts aim to establish reproducible benchmarks for healing efficiency, durability, and environmental stability, which are critical for regulatory approval in safety-sensitive applications such as medical implants and automotive electronics.
Industry consortia, such as the SEMI (Semiconductor Equipment and Materials International), are also engaging with manufacturers and research institutions to develop pre-competitive standards for integration, reliability, and lifecycle assessment of self-healing electronic components. These initiatives are expected to accelerate in the next few years as leading companies—including BASF, a major supplier of advanced polymers, and Dow, which is investing in smart materials—push for clearer regulatory pathways to market.
Looking ahead, the regulatory outlook for self-healing polymer electronics is likely to be shaped by the convergence of flexible electronics, sustainability mandates, and the need for robust performance in critical applications. As adoption grows, regulators are expected to introduce more specific guidelines addressing the unique failure modes and repair mechanisms of self-healing systems. Industry stakeholders anticipate that by 2027, harmonized standards will emerge, facilitating broader commercialization and cross-border trade of self-healing electronic products.
Competitive Analysis: Differentiators and Barriers to Entry
The competitive landscape for self-healing polymer electronics in 2025 is shaped by a combination of technological innovation, intellectual property, manufacturing capabilities, and strategic partnerships. Key differentiators among market participants include the maturity of self-healing mechanisms, integration with existing electronic manufacturing processes, and the ability to scale production while maintaining performance and reliability.
Leading companies such as LG Electronics and Samsung Electronics have demonstrated early prototypes of self-healing displays and flexible devices, leveraging their established expertise in polymer chemistry and large-scale electronics manufacturing. These firms benefit from robust R&D pipelines and extensive patent portfolios, which serve as significant barriers to entry for smaller competitors. For example, LG Electronics has filed patents related to self-healing coatings for OLED displays, aiming to extend device lifespans and reduce maintenance costs.
Material suppliers such as Dow and DuPont are also critical players, providing advanced polymer formulations that enable self-healing properties. Their ability to tailor polymer chemistry for specific electronic applications—such as stretchable conductors or encapsulants—gives them a competitive edge. These companies often collaborate with device manufacturers to co-develop materials that meet stringent electronic performance and durability requirements.
Startups and university spin-offs are contributing to the competitive dynamics by introducing novel self-healing mechanisms, such as microencapsulated healing agents or dynamic covalent bonds. However, these entrants face significant barriers, including the need for high-throughput, defect-free manufacturing and compliance with industry reliability standards. The transition from laboratory-scale demonstrations to commercial-scale production remains a major hurdle, often requiring partnerships with established manufacturers or licensing agreements.
Barriers to entry are further reinforced by the capital-intensive nature of electronics manufacturing and the need for integration with existing supply chains. Certification and qualification processes for new materials in consumer electronics, automotive, and medical devices are rigorous, often taking several years. Companies with established relationships and proven track records, such as Samsung Electronics and LG Electronics, are better positioned to navigate these requirements.
Looking ahead, the competitive advantage will likely hinge on the ability to deliver self-healing polymer electronics that combine high performance, cost-effectiveness, and seamless integration into mainstream products. Strategic alliances between material innovators and device manufacturers are expected to accelerate commercialization, while ongoing advances in polymer science will continue to raise the bar for new entrants.
Future Outlook: R&D Directions and Commercialization Roadmap
The future of self-healing polymer electronics is poised for significant advancements in both research and commercialization as we move through 2025 and into the latter part of the decade. The convergence of materials science, flexible electronics, and smart manufacturing is driving a new generation of devices capable of autonomously repairing mechanical and electrical damage, thereby extending operational lifespans and reducing maintenance costs.
In 2025, leading research institutions and industry players are intensifying efforts to address key challenges such as healing speed, repeatability, and integration with existing electronic manufacturing processes. For instance, LG Electronics has publicly demonstrated interest in flexible and self-healing display technologies, with ongoing R&D into polymer substrates that can recover from scratches and minor tears. Similarly, Samsung Electronics continues to invest in advanced materials for foldable and wearable devices, with patents and prototypes indicating a focus on self-healing coatings and encapsulants for next-generation consumer electronics.
On the materials front, companies like DuPont and DSM are developing new classes of self-healing polymers with tunable mechanical and electrical properties. These materials are being tailored for use in flexible printed circuit boards, sensors, and energy storage devices. The integration of microencapsulated healing agents and dynamic covalent bonds is enabling repeated healing cycles, a critical requirement for commercial viability in high-wear applications.
The commercialization roadmap is also being shaped by collaborations between electronics manufacturers and specialty chemical suppliers. For example, BASF is working with device makers to scale up production of self-healing elastomers and conductive polymers, targeting applications in automotive touch panels, medical wearables, and soft robotics. Meanwhile, Toray Industries is leveraging its expertise in polymer chemistry to develop self-healing films for flexible displays and electronic skins.
Looking ahead, the next few years are expected to see the first wave of commercial products incorporating self-healing polymer electronics, particularly in niche markets where durability and reliability are paramount. Industry analysts anticipate that by 2027, self-healing features will become a standard offering in premium flexible devices and smart textiles. The ongoing miniaturization of electronics, coupled with the rise of the Internet of Things (IoT), will further accelerate demand for robust, self-repairing materials. As R&D matures and manufacturing costs decrease, broader adoption across consumer, industrial, and healthcare sectors is likely, marking a transformative shift in the electronics landscape.
Sources & References
- LG Electronics
- DuPont
- Covestro
- BASF
- Kuraray
- Arkema
- Robert Bosch GmbH
- Medtronic
- Boston Scientific
- International Organization for Standardization
- ASTM International
- DSM