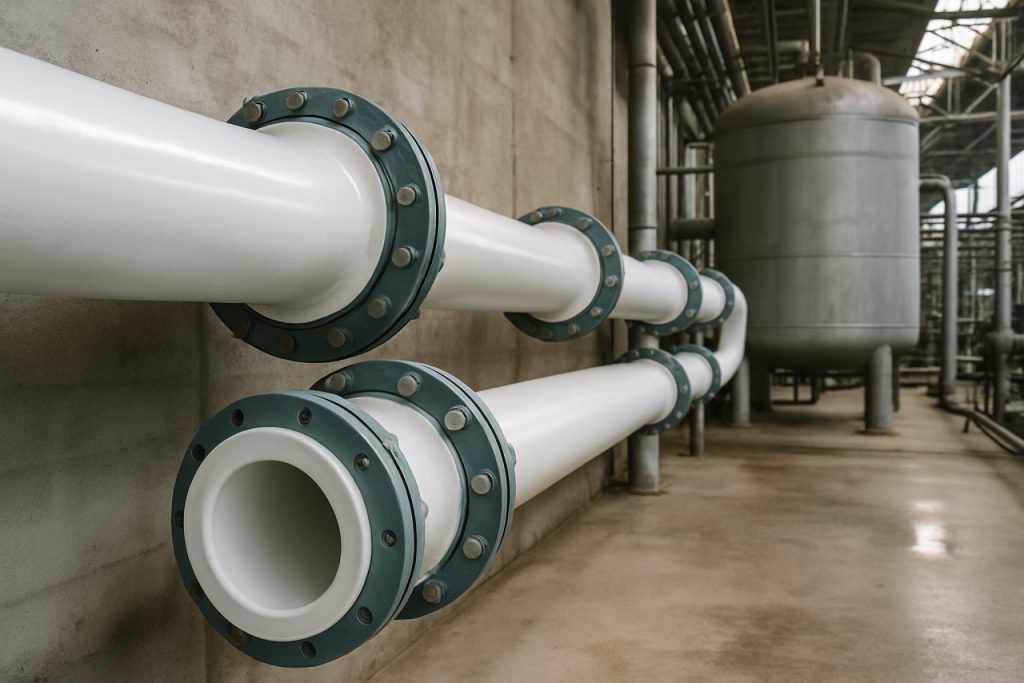
Polytetrafluoroethylene (PTFE) Lining Technology in 2025: Transforming Industrial Durability and Efficiency. Explore How Advanced PTFE Solutions Are Shaping the Next Era of Chemical and Process Industries.
- Executive Summary: PTFE Lining Market at a Glance (2025)
- Market Size, Growth Rate, and Forecasts Through 2029
- Key Drivers: Corrosion Resistance, Chemical Compatibility, and Regulatory Compliance
- Emerging Applications in Chemical, Pharmaceutical, and Food Processing Industries
- Technological Innovations: Advanced PTFE Lining Methods and Materials
- Competitive Landscape: Leading Manufacturers and Strategic Initiatives
- Sustainability and Environmental Impact of PTFE Linings
- Regional Analysis: Growth Hotspots and Investment Opportunities
- Challenges: Supply Chain, Cost, and Technical Barriers
- Future Outlook: Trends, Opportunities, and Strategic Recommendations
- Sources & References
Executive Summary: PTFE Lining Market at a Glance (2025)
The global market for Polytetrafluoroethylene (PTFE) lining technology is poised for robust activity in 2025, driven by increasing demand for corrosion-resistant and chemically inert solutions across industries such as chemicals, pharmaceuticals, food processing, and water treatment. PTFE, renowned for its exceptional non-stick and anti-corrosive properties, continues to be the material of choice for lining tanks, pipes, valves, and reactors exposed to aggressive chemicals and high temperatures.
Key industry players, including Chemours, a leading PTFE resin producer and the original inventor of Teflon™, and Daikin Industries, a major global supplier of fluoropolymers, are expanding their PTFE product portfolios and investing in advanced processing technologies. These companies are focusing on innovations such as improved paste extrusion techniques and enhanced bonding methods to meet the evolving requirements of end-users for durability and performance.
In 2025, the chemical processing sector remains the largest consumer of PTFE linings, with companies like DuPont and 3M (through its Dyneon™ brand) supplying high-purity PTFE materials for critical containment applications. The pharmaceutical and food industries are also increasing adoption, driven by stringent hygiene standards and the need for contamination-free processing environments. Notably, Saint-Gobain and Reliance Industries Limited are recognized for their extensive PTFE lining solutions tailored to these sectors.
Geographically, Asia-Pacific continues to lead in both production and consumption, with significant investments in PTFE lining capacity by regional manufacturers. India and China, in particular, are witnessing rapid growth due to expanding chemical and pharmaceutical manufacturing bases. European and North American markets, while mature, are seeing steady demand for PTFE retrofitting and replacement in aging infrastructure.
Looking ahead to the next few years, the PTFE lining market is expected to benefit from ongoing industrial expansion, stricter environmental regulations, and the push for longer equipment lifespans. Sustainability trends are prompting manufacturers to optimize PTFE usage and recycling, while research into modified PTFE compounds aims to further enhance performance characteristics. As a result, the outlook for PTFE lining technology remains positive, with continued innovation and market expansion anticipated through 2025 and beyond.
Market Size, Growth Rate, and Forecasts Through 2029
The global market for Polytetrafluoroethylene (PTFE) lining technology is poised for steady growth through 2029, driven by increasing demand for corrosion-resistant and chemically inert lining solutions across industries such as chemicals, pharmaceuticals, food processing, and water treatment. As of 2025, the market is characterized by robust investments in infrastructure upgrades and stringent regulatory requirements for process safety, particularly in regions with expanding industrial bases.
Key manufacturers and suppliers, including Chemours, Daikin Industries, 3M (notably through its Dyneon brand), and AGC Inc., continue to expand their PTFE product portfolios and global reach. These companies are recognized for their vertically integrated operations, advanced compounding technologies, and extensive technical support, which are critical for large-scale PTFE lining projects in aggressive chemical environments.
Recent data from industry sources and company reports indicate that the PTFE lining market is expected to grow at a compound annual growth rate (CAGR) in the mid-single digits through 2029. This growth is underpinned by the increasing adoption of PTFE-lined pipes, tanks, valves, and fittings in sectors where process purity and equipment longevity are paramount. For example, Chemours has highlighted ongoing investments in capacity expansion and innovation in PTFE materials to meet rising global demand, particularly in Asia-Pacific and North America.
The Asia-Pacific region is projected to remain the fastest-growing market, fueled by rapid industrialization in China, India, and Southeast Asia. Local and multinational suppliers are expanding their manufacturing footprints and distribution networks to capture this growth. Meanwhile, established markets in Europe and North America are seeing increased replacement demand and upgrades to comply with evolving environmental and safety standards.
Looking ahead to 2029, the outlook for PTFE lining technology remains positive, with further advancements anticipated in processing techniques, composite linings, and sustainability initiatives. Companies such as Daikin Industries and AGC Inc. are investing in R&D to develop PTFE linings with enhanced performance characteristics, including improved thermal stability and reduced environmental impact. The market is also expected to benefit from the growing emphasis on circular economy principles and the recyclability of fluoropolymer materials.
- Steady CAGR in the mid-single digits forecasted through 2029
- Asia-Pacific leading in new installations; Europe and North America focused on upgrades
- Major players: Chemours, Daikin Industries, 3M, AGC Inc.
- Innovation in sustainability and advanced PTFE composites expected to shape future market dynamics
Key Drivers: Corrosion Resistance, Chemical Compatibility, and Regulatory Compliance
Polytetrafluoroethylene (PTFE) lining technology continues to gain traction in 2025, driven by its exceptional corrosion resistance, broad chemical compatibility, and the increasing stringency of regulatory compliance across industries. PTFE’s unique molecular structure imparts outstanding inertness, making it the material of choice for lining vessels, pipes, valves, and fittings exposed to aggressive chemicals and extreme operating conditions. This is particularly critical in sectors such as chemicals, pharmaceuticals, food processing, and water treatment, where process integrity and safety are paramount.
Corrosion resistance remains the primary driver for PTFE lining adoption. Traditional metallic equipment, even when alloyed, is susceptible to degradation from acids, alkalis, and solvents. PTFE linings, by contrast, provide a robust barrier that significantly extends equipment lifespan and reduces maintenance costs. Leading manufacturers such as DuPont and 3M (through its Dyneon brand) have continued to innovate in PTFE resin formulations and processing techniques, enabling more reliable and cost-effective linings for both new installations and retrofits.
Chemical compatibility is another crucial factor. PTFE’s resistance to nearly all industrial chemicals, including highly reactive and corrosive substances like hydrofluoric acid, chlorine, and strong oxidizers, ensures process purity and minimizes the risk of contamination. This property is especially valued in the pharmaceutical and food industries, where product quality and safety are tightly regulated. Companies such as Chemours (a DuPont spin-off and major PTFE producer) and Saint-Gobain have expanded their PTFE lining solutions to meet the evolving needs of these sectors, offering custom-fabricated linings and advanced quality assurance protocols.
Regulatory compliance is increasingly shaping the PTFE lining market outlook. Environmental and safety regulations, such as those enforced by the U.S. Environmental Protection Agency (EPA) and the European Chemicals Agency (ECHA), are pushing industries to adopt materials that minimize emissions, leaks, and contamination risks. PTFE’s inertness and non-leaching properties help facilities meet these requirements, while also supporting certifications for food contact and pharmaceutical use. Major suppliers like Reliance Industries Limited (a significant PTFE resin producer in Asia) and Asahi Kasei are actively promoting PTFE linings as part of comprehensive compliance solutions.
Looking ahead, the demand for PTFE lining technology is expected to remain robust through the next several years, as industries prioritize operational reliability, product safety, and regulatory adherence. Ongoing advancements in PTFE processing and composite technologies are likely to further enhance performance and expand application possibilities, reinforcing PTFE’s position as a cornerstone of modern corrosion management strategies.
Emerging Applications in Chemical, Pharmaceutical, and Food Processing Industries
Polytetrafluoroethylene (PTFE) lining technology is experiencing significant advancements and adoption across the chemical, pharmaceutical, and food processing industries in 2025, driven by its exceptional chemical resistance, non-stick properties, and thermal stability. As regulatory standards for safety and purity become increasingly stringent, industries are turning to PTFE linings to ensure product integrity, minimize contamination, and extend equipment lifespan.
In the chemical processing sector, PTFE linings are being widely implemented in reactors, storage tanks, pipelines, and valves to handle highly corrosive substances such as acids, alkalis, and solvents. Leading manufacturers like DuPont and 3M continue to innovate in PTFE resin formulations, offering enhanced durability and processability for custom lining solutions. Companies such as Crane ChemPharma & Energy and Fluoroseals are expanding their portfolios of PTFE-lined piping systems and components, responding to the growing demand for reliable corrosion protection in aggressive chemical environments.
The pharmaceutical industry is increasingly adopting PTFE lining technology to meet the rigorous requirements for cleanliness, sterility, and resistance to cross-contamination. PTFE-lined vessels, hoses, and fittings are now standard in the manufacture and transfer of active pharmaceutical ingredients (APIs) and high-purity chemicals. Companies like W. L. Gore & Associates and Saint-Gobain are recognized for their high-performance PTFE products, which are engineered to comply with global pharmacopeia standards and Good Manufacturing Practices (GMP).
In the food processing industry, PTFE linings are being utilized in mixing tanks, conveyor belts, and filling equipment to prevent product adhesion, facilitate easy cleaning, and ensure compliance with food safety regulations. Chemours, a major PTFE producer, supplies food-grade PTFE materials that meet FDA and EU food contact requirements, supporting the industry’s shift toward hygienic and low-maintenance processing lines.
Looking ahead, the outlook for PTFE lining technology remains robust. Ongoing research into advanced PTFE composites and multilayer linings is expected to further enhance mechanical strength and reduce permeation rates, broadening the scope of applications. As sustainability becomes a priority, manufacturers are also exploring recycling and reprocessing methods for PTFE-lined equipment. With the continued push for operational efficiency and regulatory compliance, PTFE lining technology is poised for sustained growth and innovation across these critical industries in the coming years.
Technological Innovations: Advanced PTFE Lining Methods and Materials
Polytetrafluoroethylene (PTFE) lining technology continues to evolve rapidly in 2025, driven by the demand for enhanced chemical resistance, durability, and operational efficiency in industries such as chemical processing, pharmaceuticals, and food production. Recent years have seen significant advancements in both the materials used and the methods of applying PTFE linings, with a focus on improving performance in increasingly aggressive environments.
One of the most notable innovations is the development of multi-layer PTFE lining systems, which combine PTFE with other fluoropolymers or reinforcement materials to achieve superior mechanical strength and longer service life. These composite linings are particularly valuable in applications where traditional single-layer PTFE might be susceptible to permeation or mechanical damage. Companies such as DuPont and Chemours—both with extensive histories in fluoropolymer technology—have been at the forefront of introducing advanced PTFE blends and co-extrusion techniques that enhance the lining’s resistance to high temperatures and aggressive chemicals.
In terms of application methods, 2025 sees a growing adoption of isostatic molding and paste extrusion processes, which allow for the production of seamless, high-integrity PTFE linings for complex geometries such as pipes, valves, and storage vessels. These methods minimize the risk of weak points or joints that could compromise the lining’s integrity. Reliance Industries Limited and Saint-Gobain are among the manufacturers investing in automated, precision-controlled lining technologies that ensure consistent thickness and adhesion, even in large-scale industrial components.
Another area of innovation is the integration of PTFE linings with smart monitoring systems. Embedded sensors can now be incorporated into the lining structure to provide real-time data on temperature, pressure, and potential wear, enabling predictive maintenance and reducing the risk of unplanned downtime. This digitalization trend is being explored by major process equipment suppliers and is expected to become more widespread over the next few years.
Looking ahead, the outlook for PTFE lining technology is shaped by ongoing research into new PTFE formulations with enhanced anti-static, anti-microbial, and permeation-resistant properties. The push for sustainability is also influencing material choices, with some manufacturers exploring partially bio-based PTFE alternatives. As regulatory requirements for safety and environmental performance tighten, the industry is poised for further innovation, with leading players such as 3M and AGC Inc. expected to introduce next-generation PTFE lining solutions tailored to the evolving needs of global industries.
Competitive Landscape: Leading Manufacturers and Strategic Initiatives
The competitive landscape for Polytetrafluoroethylene (PTFE) lining technology in 2025 is characterized by the presence of several global manufacturers with established expertise in fluoropolymer processing, as well as a growing number of regional players expanding their capabilities. The market is driven by increasing demand for corrosion-resistant, chemically inert lining solutions in industries such as chemicals, pharmaceuticals, food processing, and water treatment.
Among the leading manufacturers, The Chemours Company stands out as a key innovator, leveraging its legacy as the original inventor of Teflon™ PTFE. Chemours continues to invest in advanced PTFE lining materials and technologies, focusing on improved durability and processability for critical containment applications. Another major player, AGC Inc. (formerly Asahi Glass Company), offers a broad portfolio of PTFE products under the Fluon™ brand, with a strong emphasis on high-purity linings for semiconductor and pharmaceutical sectors.
European manufacturers such as Solvay and Arkema are also prominent, with Solvay’s Solef® and Algoflon® PTFE grades widely adopted for lining tanks, pipes, and valves in aggressive chemical environments. Arkema, through its Kynar® and other fluoropolymer lines, is investing in process innovation to enhance the efficiency and environmental profile of PTFE lining solutions.
In Asia, Daikin Industries, Ltd. is a significant force, offering a comprehensive range of PTFE resins and lining technologies. Daikin’s strategic initiatives include expanding production capacity and developing new grades tailored for emerging applications, such as green hydrogen and battery manufacturing. Regional suppliers in China and India are also increasing their market share by offering cost-competitive PTFE lining services and materials, though global players maintain an edge in quality and technical support.
Strategic initiatives across the industry in 2025 focus on sustainability, digitalization, and supply chain resilience. Leading companies are investing in recycling technologies for PTFE scrap, reducing the environmental impact of production, and developing linings with enhanced lifecycle performance. Digital tools for predictive maintenance and remote monitoring of lined equipment are being introduced to improve operational reliability and reduce downtime.
Looking ahead, the competitive landscape is expected to remain dynamic, with ongoing investments in R&D, capacity expansions, and strategic partnerships. The push for decarbonization and stricter regulatory standards in process industries will further drive innovation in PTFE lining technology, favoring manufacturers with advanced technical capabilities and robust global supply networks.
Sustainability and Environmental Impact of PTFE Linings
Polytetrafluoroethylene (PTFE) lining technology continues to play a pivotal role in industries requiring high chemical resistance and non-stick properties, such as chemical processing, pharmaceuticals, and food production. As of 2025, the sustainability and environmental impact of PTFE linings are under increasing scrutiny, driven by global regulatory trends and the growing emphasis on circular economy principles.
PTFE is valued for its inertness and durability, which contribute to extended equipment lifespans and reduced maintenance frequency. This longevity can indirectly lower the environmental footprint by minimizing the need for frequent replacements and associated resource consumption. Leading manufacturers such as Chemours and Daikin Industries have highlighted the role of PTFE linings in enhancing process efficiency and reducing waste in corrosive environments, which aligns with broader sustainability goals.
However, the environmental profile of PTFE is complex. The production of PTFE involves the use of fluorinated compounds, some of which have been associated with persistent environmental pollutants. In response, major producers are investing in process improvements and emissions controls. For example, Chemours has committed to reducing process emissions of fluorinated organic chemicals and is developing new manufacturing technologies to minimize environmental impact. Similarly, AGC Inc. (Asahi Glass Company), another significant PTFE supplier, is advancing initiatives to improve the recyclability of fluoropolymer products and reduce waste generation.
Recycling and end-of-life management of PTFE linings remain challenging due to the material’s chemical stability and high melting point. Nevertheless, industry efforts are underway to develop mechanical and chemical recycling methods. Companies like Saint-Gobain are exploring closed-loop recycling systems for PTFE scrap generated during manufacturing, aiming to reintroduce recovered material into new products. These initiatives are expected to gain momentum in the next few years as regulatory pressures mount and customers demand more sustainable solutions.
Looking ahead, the outlook for PTFE lining technology is shaped by a dual focus: maintaining the material’s performance advantages while addressing environmental concerns. Innovations in greener production processes, increased transparency in supply chains, and the development of recycling infrastructure are likely to define the sector’s sustainability trajectory through 2025 and beyond. As regulatory frameworks evolve, collaboration between manufacturers, end-users, and industry bodies will be essential to ensure that PTFE linings continue to deliver value with reduced environmental impact.
Regional Analysis: Growth Hotspots and Investment Opportunities
The global landscape for Polytetrafluoroethylene (PTFE) lining technology is experiencing dynamic shifts in 2025, with distinct regional growth hotspots and emerging investment opportunities. PTFE lining, prized for its exceptional chemical resistance and non-stick properties, is increasingly adopted in industries such as chemicals, pharmaceuticals, food processing, and water treatment. The demand is being propelled by stricter environmental regulations, the need for corrosion-resistant infrastructure, and the expansion of process industries.
Asia-Pacific remains the dominant region, both in production and consumption of PTFE lining solutions. China, in particular, is home to major manufacturers such as Suzhou SuSong Polymer Materials and Sinopec, which are expanding their PTFE lining capacities to meet domestic and export demand. India is also emerging as a significant player, with companies like Gujarat Fluorochemicals Limited investing in new PTFE processing lines and targeting the growing chemical and pharmaceutical sectors. Southeast Asia is witnessing increased adoption, especially in water treatment and food processing, as governments invest in modernizing industrial infrastructure.
North America continues to be a lucrative market, driven by the presence of established process industries and a strong focus on safety and compliance. Leading suppliers such as The Chemours Company and 3M are investing in R&D to develop advanced PTFE lining materials with improved durability and performance. The United States, in particular, is seeing investments in PTFE-lined piping and vessels for the oil & gas, chemical, and semiconductor sectors, with a focus on reducing maintenance costs and extending equipment lifespans.
Europe is characterized by stringent environmental and safety regulations, which are driving the adoption of PTFE lining in chemical processing, pharmaceuticals, and food industries. Companies such as Solvay and LANXESS are at the forefront, offering high-performance PTFE lining solutions tailored to European standards. Investment is also being channeled into retrofitting aging infrastructure with PTFE linings to ensure compliance and operational efficiency.
Looking ahead to the next few years, investment opportunities are expected to intensify in regions with expanding industrial bases and tightening regulatory frameworks. The Middle East is emerging as a promising market, particularly in petrochemicals and water desalination, with local and international suppliers seeking to establish a foothold. Latin America, led by Brazil, is also witnessing gradual uptake as industries modernize and seek cost-effective corrosion protection solutions. Overall, the outlook for PTFE lining technology is robust, with regional growth driven by a combination of regulatory, economic, and technological factors.
Challenges: Supply Chain, Cost, and Technical Barriers
Polytetrafluoroethylene (PTFE) lining technology, widely used for its exceptional chemical resistance and non-stick properties, faces several challenges in 2025 and the coming years. These challenges are primarily centered around supply chain vulnerabilities, cost pressures, and technical barriers that impact both manufacturers and end-users across industries such as chemical processing, pharmaceuticals, and food production.
A significant challenge is the global supply chain for PTFE raw materials, particularly fluorspar, which is a critical precursor in PTFE production. The majority of fluorspar mining and hydrofluoric acid production is concentrated in a few countries, notably China, which has led to periodic supply disruptions and price volatility. In recent years, geopolitical tensions and export restrictions have exacerbated these issues, causing uncertainty for PTFE manufacturers such as Chemours and Daikin Industries, both of which are leading global suppliers of PTFE resins and linings. These companies have reported increased efforts to diversify sourcing and invest in supply chain resilience, but the risk of bottlenecks remains a concern.
Cost is another persistent barrier. The price of PTFE linings is influenced not only by raw material costs but also by energy-intensive manufacturing processes and stringent environmental regulations. The production of PTFE involves the use of perfluorooctanoic acid (PFOA) and other fluorinated compounds, which are subject to tightening environmental controls in the US, EU, and Asia. Compliance with these regulations requires significant investment in emissions abatement and waste management technologies, further increasing operational costs for manufacturers such as 3M and Saint-Gobain. As a result, end-users in sectors like chemical processing and pharmaceuticals are experiencing higher procurement costs for PTFE-lined equipment and components.
Technical barriers also persist, particularly in the application and longevity of PTFE linings. While PTFE offers outstanding chemical resistance, it can be susceptible to mechanical damage, permeation by certain aggressive chemicals, and challenges in bonding to metal substrates. Companies such as Garlock and Crane ChemPharma & Energy are actively developing advanced PTFE formulations and improved lining techniques to address these issues, but widespread adoption of these innovations is gradual due to the conservative nature of industries reliant on proven materials.
Looking ahead, the PTFE lining technology sector is expected to continue grappling with these supply chain, cost, and technical challenges. However, ongoing investments in raw material sourcing, process innovation, and regulatory compliance are likely to yield incremental improvements, supporting the sustained use of PTFE linings in critical industrial applications.
Future Outlook: Trends, Opportunities, and Strategic Recommendations
The future outlook for Polytetrafluoroethylene (PTFE) lining technology in 2025 and the coming years is shaped by a convergence of industrial demand, regulatory pressures, and technological innovation. As industries such as chemical processing, pharmaceuticals, food and beverage, and water treatment continue to prioritize corrosion resistance, chemical inertness, and operational longevity, PTFE linings are expected to remain a critical solution.
A key trend is the increasing adoption of PTFE lining in emerging markets, particularly in Asia-Pacific, where rapid industrialization and stricter environmental regulations are driving upgrades in plant infrastructure. Major manufacturers such as Chemours and Daikin Industries—both recognized as global leaders in PTFE production—are expanding their presence and capacity in these regions to meet growing demand. Chemours, for example, continues to invest in advanced fluoropolymer technologies and has highlighted the importance of PTFE in its product portfolio for high-performance applications.
Technological advancements are also shaping the market. Innovations in PTFE processing, such as improved paste extrusion and isostatic molding techniques, are enabling the production of more complex and reliable linings for vessels, pipes, and fittings. Companies like Gujarat Fluorochemicals and 3M are actively developing new PTFE grades and composite materials to enhance mechanical strength, reduce permeation, and extend service life in aggressive environments.
Sustainability is emerging as a strategic priority. With increasing scrutiny on per- and polyfluoroalkyl substances (PFAS), of which PTFE is a member, manufacturers are investing in cleaner production processes and recycling initiatives. Solvay and AGC Inc. are notable for their commitments to responsible fluoropolymer manufacturing and for supporting industry efforts to address environmental concerns.
Looking ahead, opportunities for PTFE lining technology are expected to expand in sectors requiring ultra-pure and contamination-free environments, such as semiconductor manufacturing and biotechnology. Strategic recommendations for stakeholders include investing in R&D for next-generation PTFE composites, forming partnerships with end-users to tailor solutions, and proactively addressing regulatory developments related to PFAS. Companies that can combine technical innovation with sustainability and regulatory compliance are likely to secure a competitive advantage in the evolving PTFE lining market.
Sources & References
- Daikin Industries
- DuPont
- Reliance Industries Limited
- AGC Inc.
- Asahi Kasei
- Crane ChemPharma & Energy
- Fluoroseals
- W. L. Gore & Associates
- Arkema
- Gujarat Fluorochemicals Limited
- LANXESS
- Garlock