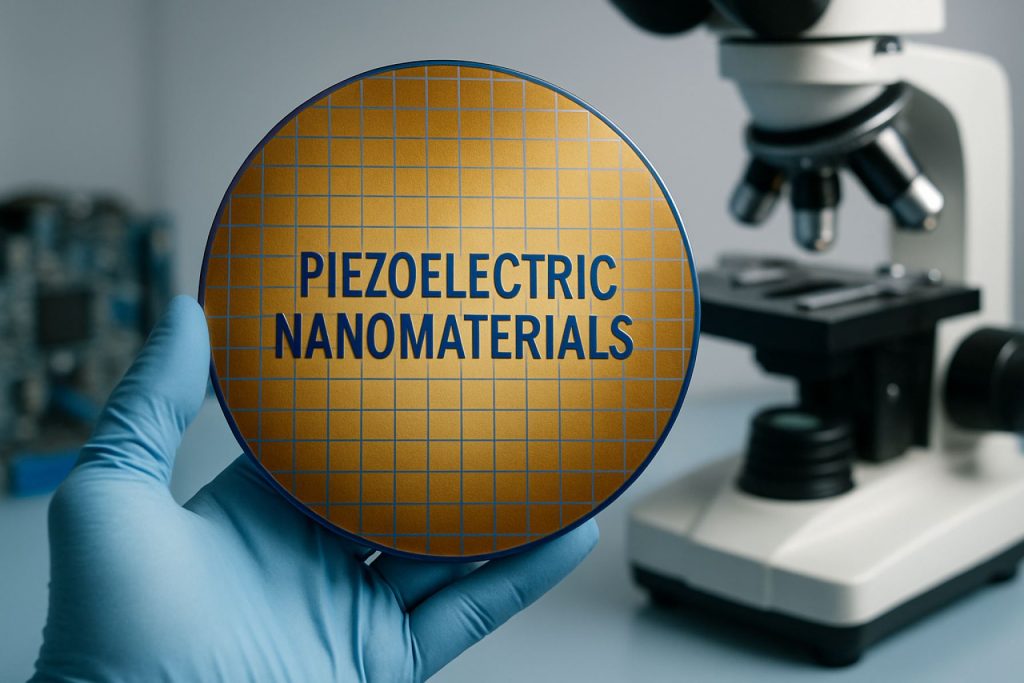
Piezoelectric Nanomaterials Engineering in 2025: Transforming Sensing, Energy Harvesting, and Smart Devices. Explore Breakthroughs, Market Expansion, and the Roadmap to 2030.
- Executive Summary: 2025 Market Outlook and Key Drivers
- Technology Overview: Fundamentals of Piezoelectric Nanomaterials
- Recent Innovations: Materials, Synthesis, and Device Integration
- Market Size and Forecast (2025–2030): Growth Trajectory and Segmentation
- Key Application Areas: Sensors, Actuators, and Energy Harvesting
- Competitive Landscape: Leading Companies and Strategic Initiatives
- Regulatory Environment and Industry Standards
- Emerging Trends: Flexible Electronics, Wearables, and IoT Integration
- Challenges and Barriers: Scalability, Cost, and Material Stability
- Future Outlook: R&D Directions and Commercialization Opportunities
- Sources & References
Executive Summary: 2025 Market Outlook and Key Drivers
The global landscape for piezoelectric nanomaterials engineering in 2025 is characterized by rapid technological advancements, increased commercialization, and expanding application domains. Piezoelectric nanomaterials—engineered at the nanoscale to convert mechanical energy into electrical energy and vice versa—are at the forefront of innovation in sectors such as medical devices, consumer electronics, automotive systems, and energy harvesting. The market outlook for 2025 is shaped by several key drivers: miniaturization trends, demand for self-powered devices, and the integration of smart materials into next-generation products.
Major manufacturers and suppliers are scaling up production capacities and investing in R&D to meet the growing demand for high-performance piezoelectric nanomaterials. Companies such as Murata Manufacturing Co., Ltd. and TDK Corporation are recognized leaders in the development and supply of advanced piezoelectric ceramics and films, with ongoing efforts to enhance material sensitivity, flexibility, and integration with microelectromechanical systems (MEMS). Murata Manufacturing Co., Ltd. has announced new product lines targeting wearable health monitors and IoT sensors, leveraging their expertise in multilayer ceramic technology. Similarly, TDK Corporation is expanding its piezoelectric device portfolio, focusing on miniaturized actuators and sensors for automotive and industrial automation.
In the United States, Piezo Systems, Inc. continues to supply custom piezoelectric components for research and industrial applications, with a particular emphasis on nanostructured materials for precision actuation and sensing. European players, including Piezomechanik GmbH, are advancing the engineering of piezoelectric thin films and nanocomposites, supporting the region’s strong presence in scientific instrumentation and medical diagnostics.
The outlook for 2025 and the following years is optimistic, with industry bodies such as the IEEE highlighting the role of piezoelectric nanomaterials in enabling energy-autonomous systems and next-generation robotics. Key challenges remain in scaling up nanomaterial synthesis, ensuring long-term reliability, and achieving cost-effective mass production. However, ongoing collaborations between manufacturers, research institutes, and end-users are expected to accelerate the transition from laboratory-scale innovations to commercial products.
In summary, the piezoelectric nanomaterials engineering sector in 2025 is poised for robust growth, driven by technological breakthroughs, expanding industrial adoption, and the strategic initiatives of leading global companies. The next few years will likely see further integration of these materials into smart, connected devices, underpinning advances in healthcare, mobility, and sustainable energy solutions.
Technology Overview: Fundamentals of Piezoelectric Nanomaterials
Piezoelectric nanomaterials engineering is a rapidly advancing field, leveraging the unique electromechanical coupling properties of materials at the nanoscale. The fundamental principle involves the generation of an electric charge in response to applied mechanical stress, a phenomenon that becomes significantly enhanced as material dimensions shrink to the nanometer regime. In 2025, the focus is on optimizing material composition, nanostructure morphology, and integration techniques to maximize piezoelectric performance for next-generation applications.
The most widely studied piezoelectric nanomaterials include lead zirconate titanate (PZT), barium titanate (BaTiO3), zinc oxide (ZnO), and emerging lead-free alternatives such as potassium sodium niobate (KNN). Nanostructures—such as nanowires, nanorods, and thin films—are engineered to exploit size-dependent effects, including increased surface-to-volume ratio and domain wall mobility, which can enhance piezoelectric coefficients beyond their bulk counterparts. For example, ZnO nanowires have demonstrated high piezoelectric output and are being actively developed for energy harvesting and sensor applications.
Recent advances in synthesis techniques, such as hydrothermal growth, sol-gel processing, and atomic layer deposition, have enabled precise control over nanomaterial morphology and crystallinity. Companies like Kyocera Corporation and Murata Manufacturing Co., Ltd. are at the forefront of commercializing piezoelectric ceramics and thin films, with ongoing research into nanostructured variants for miniaturized devices. TDK Corporation is also investing in advanced piezoelectric materials for microelectromechanical systems (MEMS) and nanoelectromechanical systems (NEMS), targeting applications in medical ultrasound, precision actuators, and energy harvesting.
A key engineering challenge in 2025 is the integration of piezoelectric nanomaterials with flexible substrates and electronic circuits, enabling the development of wearable sensors, implantable medical devices, and self-powered systems. The compatibility of nanomaterials with silicon and polymer platforms is being addressed through innovations in low-temperature processing and surface functionalization. Additionally, the industry is responding to environmental concerns by accelerating the transition to lead-free piezoelectric nanomaterials, with companies such as Murata Manufacturing Co., Ltd. and TDK Corporation actively developing and commercializing lead-free alternatives.
Looking ahead, the outlook for piezoelectric nanomaterials engineering is robust, with anticipated breakthroughs in scalable manufacturing, enhanced material performance, and broader adoption in consumer electronics, healthcare, and industrial automation. The convergence of nanomaterial science, device engineering, and sustainable manufacturing practices is expected to drive significant innovation and market growth through the remainder of the decade.
Recent Innovations: Materials, Synthesis, and Device Integration
The field of piezoelectric nanomaterials engineering has witnessed significant advancements in recent years, with 2025 marking a period of accelerated innovation in materials development, synthesis techniques, and device integration. The drive for miniaturized, high-performance, and environmentally friendly piezoelectric devices has spurred both academic and industrial research, leading to the emergence of novel nanostructures and scalable manufacturing processes.
A major trend in 2025 is the shift towards lead-free piezoelectric nanomaterials, motivated by environmental regulations and the need for biocompatibility in medical and wearable applications. Companies such as Murata Manufacturing Co., Ltd. and TDK Corporation have expanded their portfolios to include barium titanate (BaTiO3) and potassium sodium niobate (KNN) based nanomaterials, which offer promising piezoelectric coefficients while eliminating toxic lead content. These materials are being engineered at the nanoscale to enhance their electromechanical coupling and flexibility, enabling their integration into next-generation sensors and energy harvesters.
On the synthesis front, scalable bottom-up approaches such as hydrothermal and sol-gel methods are being refined to produce uniform nanowires, nanorods, and thin films with controlled crystallinity and orientation. NGK Insulators, Ltd. has reported progress in the mass production of piezoelectric nanoceramics using advanced sintering techniques, which improve grain boundary engineering and reduce defect densities. These advances are critical for achieving consistent device performance and reliability at commercial scales.
Device integration has also seen notable breakthroughs. Flexible and stretchable piezoelectric nanogenerators, leveraging polymer-ceramic nanocomposites, are being developed for self-powered wearable electronics and biomedical implants. Samsung Electronics has demonstrated prototypes of flexible piezoelectric sensors embedded in smart textiles, utilizing aligned nanofiber arrays for enhanced sensitivity and durability. Meanwhile, STMicroelectronics is actively incorporating piezoelectric nanomaterials into MEMS (Micro-Electro-Mechanical Systems) platforms, targeting applications in precision actuators and vibration energy harvesting.
Looking ahead, the outlook for piezoelectric nanomaterials engineering remains robust. The convergence of advanced materials synthesis, scalable manufacturing, and seamless device integration is expected to drive the commercialization of high-performance, eco-friendly piezoelectric devices across consumer electronics, healthcare, and industrial IoT sectors. Continued collaboration between material suppliers, device manufacturers, and end-users will be pivotal in overcoming remaining challenges related to long-term stability, large-area fabrication, and cost-effectiveness.
Market Size and Forecast (2025–2030): Growth Trajectory and Segmentation
The global market for piezoelectric nanomaterials engineering is poised for robust growth from 2025 through 2030, driven by expanding applications in electronics, healthcare, energy harvesting, and advanced sensors. The increasing demand for miniaturized, high-performance devices is accelerating the adoption of nanostructured piezoelectric materials, particularly in sectors such as medical diagnostics, wearable technology, and precision actuators.
Key industry players are scaling up production and investing in research to enhance the efficiency and versatility of piezoelectric nanomaterials. Companies like PI Ceramic and Murata Manufacturing Co., Ltd. are recognized for their advanced piezoelectric ceramics and thin-film technologies, which are foundational to the development of next-generation nanoscale devices. Murata Manufacturing Co., Ltd. in particular has expanded its portfolio to include piezoelectric MEMS and nanomaterial-based components for consumer electronics and automotive applications.
Segmentation of the market reveals several high-growth areas:
- Material Type: Lead zirconate titanate (PZT) nanomaterials remain dominant due to their high piezoelectric coefficients, but lead-free alternatives such as barium titanate and potassium sodium niobate are gaining traction, especially in regions with stringent environmental regulations.
- Application: The healthcare sector is expected to see the fastest growth, with piezoelectric nanomaterials enabling innovations in ultrasound imaging, implantable sensors, and drug delivery systems. Energy harvesting—particularly for IoT and wireless sensor networks—is another rapidly expanding segment, with companies like PI Ceramic and Murata Manufacturing Co., Ltd. developing solutions for self-powered devices.
- Geography: Asia-Pacific leads in both production and consumption, driven by the presence of major electronics manufacturers and robust R&D investment. Europe and North America are also significant markets, with a focus on automotive, aerospace, and medical device applications.
Looking ahead to 2030, the market outlook remains highly positive. Ongoing advancements in nanofabrication and material synthesis are expected to lower costs and improve performance, further broadening the scope of piezoelectric nanomaterials. Strategic collaborations between manufacturers, research institutes, and end-users will likely accelerate commercialization and adoption across diverse industries. As regulatory frameworks evolve and sustainability becomes a priority, the shift toward lead-free and environmentally friendly nanomaterials is anticipated to intensify, shaping the competitive landscape and innovation trajectory in the coming years.
Key Application Areas: Sensors, Actuators, and Energy Harvesting
Piezoelectric nanomaterials engineering is rapidly advancing the capabilities of sensors, actuators, and energy harvesting devices, with 2025 marking a pivotal year for commercial and research-driven innovation. The unique properties of nanostructured piezoelectric materials—such as enhanced surface area, tunable mechanical flexibility, and superior electromechanical coupling—are enabling new applications and improving the performance of established technologies.
In the sensor domain, piezoelectric nanomaterials are being integrated into highly sensitive pressure, vibration, and biosensors. Companies like Murata Manufacturing Co., Ltd. and TDK Corporation are at the forefront, leveraging advanced thin-film and nanowire technologies to produce miniaturized sensors for automotive, medical, and industrial applications. For example, nanostructured lead zirconate titanate (PZT) and zinc oxide (ZnO) are being used to fabricate flexible and wearable sensors capable of detecting minute physiological signals, supporting the growth of remote health monitoring and smart textiles.
Actuator technology is also benefiting from piezoelectric nanomaterials, with a focus on precision and miniaturization. PiezoMotor Uppsala AB and Physik Instrumente (PI) are developing nanopositioning systems and micro-actuators for applications in optics, robotics, and semiconductor manufacturing. The use of nanostructured ceramics and composites allows for faster response times, lower power consumption, and greater mechanical durability, which are critical for next-generation microelectromechanical systems (MEMS).
Energy harvesting is a particularly dynamic area, with piezoelectric nanomaterials enabling the conversion of ambient mechanical energy into usable electrical power. NGK Insulators, Ltd. and Kyocera Corporation are investing in the development of nanogenerators based on flexible piezoelectric films and nanowires. These devices are being deployed in wireless sensor networks, wearable electronics, and self-powered IoT devices, addressing the growing demand for sustainable, maintenance-free power sources. Recent demonstrations of hybrid nanogenerators—combining piezoelectric, triboelectric, and photovoltaic effects—are expected to reach commercial maturity by 2026, further expanding the market potential.
Looking ahead, the convergence of advanced manufacturing techniques, such as atomic layer deposition and 3D nanoprinting, with scalable nanomaterial synthesis is set to accelerate the deployment of piezoelectric nanomaterials across these key application areas. Industry leaders and research consortia are collaborating to address challenges related to material stability, integration, and cost, ensuring that piezoelectric nanomaterials will play a central role in the evolution of smart, connected, and energy-efficient systems through 2025 and beyond.
Competitive Landscape: Leading Companies and Strategic Initiatives
The competitive landscape of piezoelectric nanomaterials engineering in 2025 is characterized by a dynamic interplay between established multinational corporations, innovative startups, and research-driven organizations. The sector is witnessing accelerated activity as demand surges for advanced sensors, energy harvesting devices, and next-generation medical and wearable technologies. Key players are leveraging strategic partnerships, expanding manufacturing capabilities, and investing in R&D to maintain technological leadership.
Among the global leaders, Murata Manufacturing Co., Ltd. stands out for its extensive portfolio of piezoelectric ceramics and ongoing development of nanomaterial-based components. Murata’s focus on miniaturization and integration of piezoelectric elements into IoT and automotive applications has positioned it at the forefront of the industry. Similarly, TDK Corporation is advancing the field through its subsidiary EPCOS, with a strong emphasis on multilayer piezoelectric devices and thin-film technologies. TDK’s recent investments in expanding its production lines for piezoelectric MEMS sensors underscore its commitment to scaling up nanomaterial-enabled solutions.
In the United States, PI Ceramic (a division of Physik Instrumente) and Kyocera Corporation are notable for their high-precision piezoelectric components, with both companies actively exploring nanostructured materials to enhance device sensitivity and durability. Kyocera’s strategic collaborations with academic institutions and its proprietary synthesis methods for lead-free piezoelectric nanomaterials are expected to yield commercial products within the next few years.
Emerging players are also shaping the competitive landscape. Noliac (a part of CTS Corporation) specializes in custom piezoelectric solutions, including multilayer and single-crystal nanomaterial actuators, targeting aerospace and medical device markets. Meanwhile, NGK Insulators, Ltd. is leveraging its expertise in ceramics to develop piezoelectric nanomaterials for energy harvesting and environmental monitoring applications.
Strategic initiatives in 2025 include joint ventures between material suppliers and electronics manufacturers to accelerate commercialization. Companies are increasingly investing in sustainable and lead-free piezoelectric nanomaterials, responding to regulatory pressures and market demand for eco-friendly solutions. The next few years are expected to see intensified competition as firms race to patent novel nanostructures and scale up production, with Asia-Pacific companies likely to maintain a dominant position due to robust manufacturing infrastructure and government support.
Regulatory Environment and Industry Standards
The regulatory environment and industry standards for piezoelectric nanomaterials engineering are evolving rapidly as the sector matures and applications proliferate across electronics, healthcare, and energy harvesting. In 2025, regulatory frameworks are primarily shaped by international standards organizations and national agencies, with a growing emphasis on safety, environmental impact, and interoperability.
The International Electrotechnical Commission (IEC) remains central in developing standards for piezoelectric materials, including nanostructured variants. The IEC’s Technical Committee 49 (Piezoelectric and dielectric devices for frequency control and selection) and its subcommittees are actively updating standards to address the unique properties and testing requirements of nanomaterials. These updates include protocols for characterizing nanoscale piezoelectric coefficients, durability, and integration into microelectromechanical systems (MEMS).
In parallel, the International Organization for Standardization (ISO) is expanding its portfolio of nanotechnology standards, with ISO/TC 229 focusing on terminology, measurement, and health and safety aspects of nanomaterials. Recent ISO standards address the safe handling, labeling, and lifecycle assessment of engineered nanomaterials, which are directly relevant to piezoelectric nanomaterials used in consumer and medical devices.
National regulatory bodies, such as the U.S. Food and Drug Administration (FDA) and the European Chemicals Agency (ECHA), are increasingly scrutinizing the use of piezoelectric nanomaterials in biomedical implants, sensors, and wearable devices. In 2025, the FDA continues to require premarket notification and risk assessment for devices incorporating novel nanomaterials, emphasizing biocompatibility and long-term stability. ECHA, under the EU’s REACH regulation, mandates registration and risk evaluation for nanomaterial imports and manufacturing, with specific guidance for substances at the nanoscale.
Industry consortia, such as the NanoBusiness Commercialization Association and the Nanotechnology Industries Association, are collaborating with standards bodies to harmonize requirements and facilitate global market access. Leading manufacturers, including Murata Manufacturing Co., Ltd. and TDK Corporation, are actively participating in standards development and compliance initiatives, ensuring their piezoelectric nanomaterial products meet evolving regulatory expectations.
Looking ahead, the regulatory landscape is expected to become more stringent, particularly regarding environmental and occupational health. Anticipated developments include stricter limits on nanoparticle emissions during manufacturing, enhanced end-of-life management protocols, and mandatory disclosure of nanomaterial content in consumer products. As the industry grows, proactive engagement with standards organizations and regulatory agencies will be critical for manufacturers and developers to ensure compliance and foster innovation in piezoelectric nanomaterials engineering.
Emerging Trends: Flexible Electronics, Wearables, and IoT Integration
The integration of piezoelectric nanomaterials into flexible electronics, wearables, and Internet of Things (IoT) devices is accelerating rapidly in 2025, driven by advances in material synthesis, device miniaturization, and scalable manufacturing. Piezoelectric nanomaterials—such as lead zirconate titanate (PZT) nanowires, barium titanate (BaTiO3) nanoparticles, and emerging lead-free alternatives—are being engineered to convert mechanical energy from motion, pressure, or vibration into electrical signals, enabling self-powered and highly sensitive devices.
A key trend is the development of flexible and stretchable piezoelectric films that can be seamlessly integrated into wearable health monitors, smart textiles, and soft robotics. Companies like Murata Manufacturing Co., Ltd. are advancing the fabrication of ultra-thin piezoelectric sensors and actuators, leveraging their expertise in multilayer ceramic technology to produce components that maintain high sensitivity even when bent or stretched. Similarly, TDK Corporation is focusing on miniaturized piezoelectric elements for IoT sensor nodes and energy harvesting modules, targeting applications in smart homes, industrial monitoring, and medical devices.
In the wearables sector, piezoelectric nanomaterials are enabling new generations of self-powered fitness trackers, electronic skin patches, and implantable biosensors. For example, Samsung Electronics has demonstrated interest in integrating piezoelectric nanogenerators into flexible displays and wearable devices, aiming to extend battery life and enable continuous health monitoring. The ability of these materials to harvest biomechanical energy from body movements is particularly attractive for medical wearables, where battery replacement is challenging.
IoT integration is another major driver, with piezoelectric nanomaterials being engineered for wireless sensor networks that require ultra-low power consumption and long-term autonomy. STMicroelectronics is developing piezoelectric MEMS (Micro-Electro-Mechanical Systems) for vibration sensing and energy harvesting, supporting predictive maintenance and asset tracking in industrial IoT environments. These solutions are expected to proliferate as the demand for distributed, maintenance-free sensors grows.
Looking ahead, the outlook for piezoelectric nanomaterials engineering in flexible electronics and IoT is robust. Ongoing research is focused on improving the environmental stability, biocompatibility, and lead-free composition of these materials, with several industry collaborations and pilot production lines already underway. As manufacturing processes mature and costs decrease, widespread adoption in consumer electronics, healthcare, and smart infrastructure is anticipated over the next few years, positioning piezoelectric nanomaterials as a cornerstone of the next wave of intelligent, energy-autonomous devices.
Challenges and Barriers: Scalability, Cost, and Material Stability
The engineering of piezoelectric nanomaterials is advancing rapidly, yet several critical challenges persist as the field moves into 2025 and beyond. Chief among these are issues of scalability, cost, and material stability, which collectively hinder the widespread adoption of nanostructured piezoelectric devices in commercial and industrial applications.
Scalability remains a significant barrier. While laboratory-scale synthesis of piezoelectric nanomaterials—such as nanowires, nanoparticles, and thin films—has demonstrated promising results, translating these methods to industrial-scale production is complex. Techniques like hydrothermal synthesis and chemical vapor deposition, though effective at small scales, often face reproducibility and uniformity issues when scaled up. Leading manufacturers such as PI Ceramic and Murata Manufacturing Co., Ltd. are investing in process optimization and automation to address these challenges, but consistent, high-throughput production of defect-free nanomaterials remains elusive.
Cost is closely tied to scalability. The high purity precursors, specialized equipment, and stringent environmental controls required for nanomaterial synthesis drive up production expenses. For example, the fabrication of lead-free piezoelectric nanomaterials, which are increasingly favored due to environmental regulations, often involves rare or expensive elements and complex processing steps. Companies like TDK Corporation and KEMET Corporation are exploring alternative materials and streamlined manufacturing techniques to reduce costs, but price competitiveness with conventional bulk piezoelectric ceramics is not yet fully realized.
Material stability is another pressing concern, particularly for nanostructured piezoelectrics exposed to real-world operating conditions. Nanomaterials can be more susceptible to degradation from moisture, temperature fluctuations, and mechanical fatigue compared to their bulk counterparts. This impacts device reliability and lifespan, especially in demanding applications such as wearable electronics and energy harvesting. To address this, companies like Murata Manufacturing Co., Ltd. are developing advanced encapsulation techniques and composite structures to enhance environmental resistance and mechanical robustness.
Looking ahead, the outlook for overcoming these barriers is cautiously optimistic. Industry leaders are collaborating with academic institutions to develop scalable synthesis methods, such as roll-to-roll processing and inkjet printing, which promise to lower costs and improve uniformity. Additionally, the push for sustainable, lead-free materials is driving innovation in both material science and device engineering. As these efforts mature, the next few years are likely to see incremental but meaningful progress toward the commercialization of robust, cost-effective piezoelectric nanomaterials.
Future Outlook: R&D Directions and Commercialization Opportunities
The future of piezoelectric nanomaterials engineering is poised for significant advancements in both research and commercialization as we move through 2025 and beyond. The convergence of nanotechnology, materials science, and electronics is driving the development of next-generation piezoelectric devices with enhanced sensitivity, flexibility, and integration capabilities. Key R&D directions include the synthesis of lead-free piezoelectric nanomaterials, scalable fabrication methods, and the integration of these materials into flexible and wearable electronics.
A major focus is on environmentally friendly alternatives to traditional lead-based piezoelectrics. Companies such as TDK Corporation and Murata Manufacturing Co., Ltd. are actively developing lead-free ceramics and thin films, responding to regulatory pressures and market demand for sustainable solutions. These efforts are complemented by academic and industrial collaborations targeting the optimization of barium titanate (BaTiO3), potassium sodium niobate (KNN), and other perovskite-based nanomaterials for high-performance applications.
Scalable manufacturing remains a critical challenge and opportunity. Companies like Piezotech (an Arkema subsidiary) are pioneering printable piezoelectric polymers, enabling roll-to-roll production of flexible sensors and actuators. This approach is expected to accelerate the commercialization of piezoelectric nanomaterials in sectors such as healthcare, where wearable biosensors and self-powered medical devices are gaining traction. Similarly, PI Ceramic is expanding its portfolio of piezoelectric components, focusing on miniaturized and high-precision devices for industrial and automotive applications.
The integration of piezoelectric nanomaterials with microelectromechanical systems (MEMS) and the Internet of Things (IoT) is another promising avenue. STMicroelectronics and Robert Bosch GmbH are investing in MEMS-based energy harvesters and sensors that leverage nanostructured piezoelectric films for ultra-low-power operation. These developments are expected to support the proliferation of autonomous wireless sensors in smart infrastructure, environmental monitoring, and industrial automation.
Looking ahead, the commercialization landscape is likely to be shaped by advances in material durability, cost-effective processing, and device integration. Strategic partnerships between material suppliers, device manufacturers, and end-users will be crucial for scaling up production and meeting the stringent requirements of emerging markets. As regulatory frameworks evolve and demand for sustainable, high-performance materials grows, piezoelectric nanomaterials are set to play a pivotal role in the next wave of smart, connected technologies.
Sources & References
- Murata Manufacturing Co., Ltd.
- Piezomechanik GmbH
- IEEE
- NGK Insulators, Ltd.
- STMicroelectronics
- PI Ceramic
- PiezoMotor Uppsala AB
- Physik Instrumente (PI)
- NGK Insulators, Ltd.
- ISO
- ECHA
- KEMET Corporation
- Piezotech
- Robert Bosch GmbH