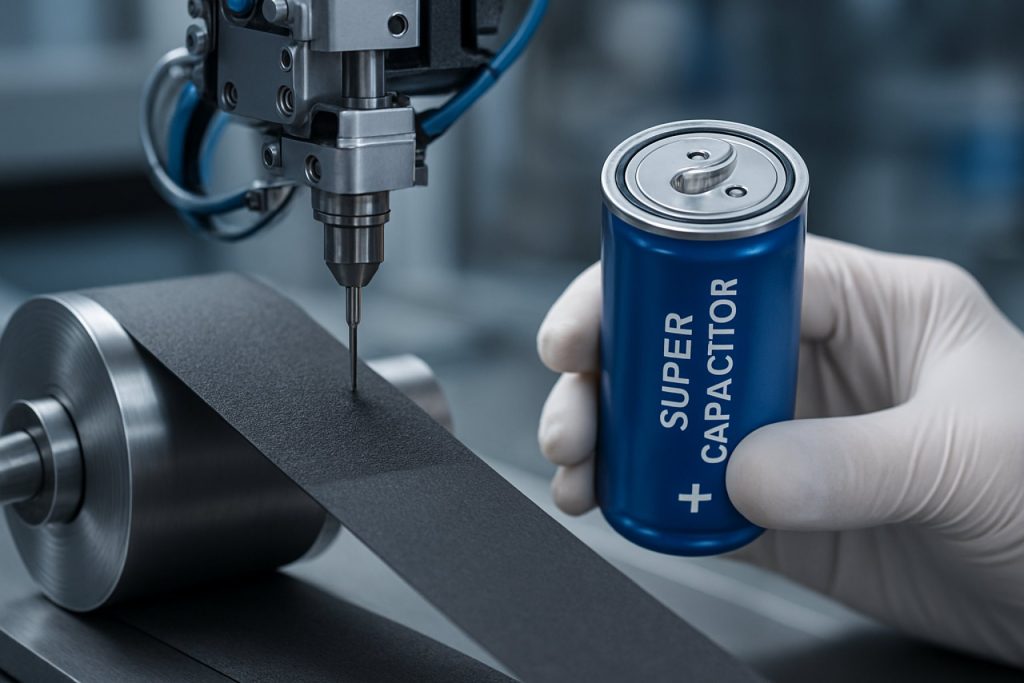
Supercapacitor Electrode Manufacturing in 2025: Unleashing Rapid Market Expansion and Advanced Material Breakthroughs. Explore How Cutting-Edge Technologies and Strategic Investments Are Shaping the Industry’s Future.
- Executive Summary: 2025 Market Snapshot & Key Trends
- Global Market Size, Growth Rate, and Forecasts to 2030
- Emerging Electrode Materials: Graphene, Carbon Nanotubes, and Beyond
- Manufacturing Innovations: Automation, Scalability, and Cost Reduction
- Key Players and Strategic Partnerships (e.g., Skeleton Technologies, Maxwell Technologies, Panasonic)
- Supply Chain Dynamics and Raw Material Sourcing
- Application Expansion: Automotive, Grid Storage, Consumer Electronics
- Sustainability Initiatives and Environmental Impact
- Regulatory Landscape and Industry Standards (e.g., ieee.org, iec.ch)
- Future Outlook: Investment Hotspots and Disruptive Technologies
- Sources & References
Executive Summary: 2025 Market Snapshot & Key Trends
The supercapacitor electrode manufacturing sector is poised for significant growth and transformation in 2025, driven by surging demand for high-power energy storage across automotive, grid, and consumer electronics applications. The market is characterized by rapid advancements in electrode materials, scaling of production capacities, and increasing integration of sustainable manufacturing practices.
Key industry leaders such as Maxwell Technologies (a subsidiary of Tesla), Skeleton Technologies, and Panasonic Corporation are actively expanding their electrode manufacturing capabilities. Skeleton Technologies has announced the commissioning of a new automated supercapacitor production facility in Germany, aiming to scale up the output of their patented curved graphene-based electrodes, which are reported to deliver higher energy and power densities compared to conventional activated carbon materials. Maxwell Technologies continues to focus on advanced dry electrode processes, which promise reduced manufacturing costs and improved environmental performance.
Material innovation remains a central trend. The adoption of graphene, carbon nanotubes, and hybrid composites is accelerating, with companies like Skeleton Technologies and Panasonic Corporation investing in R&D to enhance electrode conductivity and surface area. These advancements are expected to push supercapacitor energy densities closer to those of lithium-ion batteries, broadening their application scope.
Sustainability is increasingly influencing manufacturing decisions. Electrode producers are implementing greener processes, such as water-based slurries and solvent recovery systems, to minimize environmental impact. Panasonic Corporation has publicly committed to reducing carbon emissions across its energy device manufacturing lines, including supercapacitor electrodes.
Geographically, Europe and Asia-Pacific are leading in capacity expansion and technology deployment. European Union initiatives are supporting local supply chains and advanced material development, while major Asian manufacturers are scaling up to meet domestic and export demand.
- Automated, high-throughput electrode production lines are coming online, reducing unit costs and improving consistency.
- Material breakthroughs—especially in graphene and hybrid carbons—are expected to reach commercial scale by 2025-2027.
- Strategic partnerships between automotive OEMs and electrode manufacturers are accelerating technology transfer and market adoption.
Looking ahead, the supercapacitor electrode manufacturing sector in 2025 is set to benefit from both technological innovation and market pull, with leading companies leveraging advanced materials, automation, and sustainability to capture emerging opportunities in electrification and renewable energy integration.
Global Market Size, Growth Rate, and Forecasts to 2030
The global market for supercapacitor electrode manufacturing is poised for robust growth in 2025 and the following years, driven by accelerating demand for energy storage solutions in automotive, grid, and consumer electronics sectors. As of 2025, the market is characterized by increasing investments in advanced materials, scaling of production capacities, and strategic partnerships among key industry players.
Major manufacturers such as Maxwell Technologies (a subsidiary of Tesla), Skeleton Technologies, and Panasonic Corporation are expanding their electrode production lines to meet the surging requirements for high-performance supercapacitors. Skeleton Technologies has announced significant capacity expansions in Europe, leveraging its proprietary curved graphene material to enhance energy density and cycle life. Similarly, Maxwell Technologies continues to innovate in electrode design, focusing on automotive and grid storage applications.
In Asia, Panasonic Corporation and LG Corporation are investing in next-generation electrode materials and automated manufacturing processes to improve scalability and cost-effectiveness. These companies are also collaborating with automotive OEMs to integrate supercapacitor modules into electric vehicles and hybrid systems, further fueling market growth.
According to industry data from leading manufacturers, the global supercapacitor market—including electrode manufacturing—is expected to achieve a compound annual growth rate (CAGR) exceeding 15% through 2030. This growth is underpinned by the rapid electrification of transportation, the proliferation of renewable energy installations, and the need for fast-charging, long-life energy storage devices. The Asia-Pacific region, led by China, Japan, and South Korea, is projected to remain the largest and fastest-growing market, supported by strong government policies and a robust electronics manufacturing ecosystem.
Looking ahead, the next few years will see further advancements in electrode materials, such as graphene, carbon nanotubes, and hybrid composites, which promise to significantly boost the energy and power density of supercapacitors. Companies like Skeleton Technologies and Panasonic Corporation are at the forefront of these innovations, with pilot projects and commercial deployments already underway.
In summary, the supercapacitor electrode manufacturing sector is set for dynamic expansion through 2030, with leading companies scaling up production, investing in R&D, and forging strategic alliances to capture emerging opportunities in mobility, grid, and industrial applications.
Emerging Electrode Materials: Graphene, Carbon Nanotubes, and Beyond
The landscape of supercapacitor electrode manufacturing is undergoing rapid transformation in 2025, driven by the integration of advanced materials such as graphene, carbon nanotubes (CNTs), and novel hybrid composites. These materials are being adopted to address the limitations of traditional activated carbon electrodes, particularly in terms of energy density, power delivery, and cycle life.
Graphene, with its exceptional electrical conductivity and high surface area, has become a focal point for electrode innovation. Companies like Directa Plus and First Graphene are scaling up the production of high-purity graphene powders and inks specifically tailored for energy storage applications. In 2025, these firms are collaborating with supercapacitor manufacturers to integrate graphene into commercial-scale electrode fabrication, leveraging roll-to-roll coating and printing techniques to ensure uniformity and scalability.
Carbon nanotubes are also gaining traction as both primary and additive materials in electrode formulations. OCSiAl, a global leader in single-wall carbon nanotube production, is supplying CNTs to supercapacitor manufacturers aiming to enhance electrode conductivity and mechanical strength. The company’s large-scale synthesis capabilities are enabling cost reductions, making CNT-enhanced electrodes more commercially viable. Additionally, Nanocyl is providing multiwall CNTs for hybrid electrode designs, which combine the high surface area of activated carbon with the superior conductivity of nanotubes.
Beyond graphene and CNTs, hybrid materials and composites are emerging as the next frontier. Companies such as Arkema are developing advanced polymer-graphene composites, while Cabot Corporation is focusing on engineered carbon blacks and conductive additives to further optimize electrode performance. These innovations are being integrated into pilot production lines, with several manufacturers targeting automotive and grid storage applications where high power and long cycle life are critical.
Looking ahead, the outlook for supercapacitor electrode manufacturing is marked by increasing collaboration between material suppliers and device manufacturers. The focus is on scaling up production processes, improving material consistency, and reducing costs. As regulatory and sustainability pressures mount, there is also a growing emphasis on green synthesis methods and the recyclability of advanced electrode materials. The next few years are expected to see the commercialization of supercapacitors with significantly improved energy and power densities, enabled by these emerging electrode technologies.
Manufacturing Innovations: Automation, Scalability, and Cost Reduction
The supercapacitor industry is undergoing significant transformation in electrode manufacturing, driven by the need for higher performance, cost efficiency, and scalable production. As of 2025, leading manufacturers are investing heavily in automation and advanced material processing to meet the growing demand for energy storage solutions in automotive, grid, and consumer electronics sectors.
Automation is at the forefront of manufacturing innovation. Companies such as Maxwell Technologies (a subsidiary of Tesla) and Skeleton Technologies have implemented robotic systems for electrode coating, drying, and assembly, reducing human error and increasing throughput. These automated lines enable precise control over electrode thickness and uniformity, which are critical for device performance and longevity. Skeleton Technologies has also pioneered the use of patented “curved graphene” materials, which require specialized roll-to-roll processing equipment, further emphasizing the role of automation in handling next-generation materials.
Scalability remains a key challenge, particularly as supercapacitor applications expand into electric vehicles and grid storage. CAP-XX, an established manufacturer, has expanded its production facilities to accommodate large-scale orders, leveraging modular manufacturing lines that can be rapidly reconfigured for different electrode chemistries and formats. Meanwhile, Eaton has integrated digital manufacturing platforms to monitor and optimize production in real time, ensuring consistent quality as volumes increase.
Cost reduction is being addressed through both process and material innovations. The adoption of water-based electrode slurries, as seen in the operations of Maxwell Technologies and Skeleton Technologies, reduces reliance on expensive and hazardous organic solvents, lowering both material costs and environmental compliance expenses. Additionally, the use of abundant carbon-based materials, such as activated carbon and graphene derivatives, is helping to drive down raw material costs. Companies are also exploring recycling and reprocessing of electrode materials to further reduce expenses and environmental impact.
Looking ahead to the next few years, the industry is expected to see further integration of artificial intelligence and machine learning in process control, enabling predictive maintenance and adaptive manufacturing. Partnerships between material suppliers and equipment manufacturers are likely to accelerate the adoption of new electrode architectures, such as hybrid and asymmetric designs, which promise improved energy and power densities. As regulatory and market pressures for sustainable manufacturing intensify, companies with advanced, automated, and flexible electrode production capabilities are poised to lead the supercapacitor sector.
Key Players and Strategic Partnerships (e.g., Skeleton Technologies, Maxwell Technologies, Panasonic)
The supercapacitor electrode manufacturing sector in 2025 is characterized by a dynamic interplay of established industry leaders, emerging innovators, and a growing web of strategic partnerships. This landscape is shaped by the increasing demand for high-performance energy storage solutions across automotive, grid, and industrial applications.
Among the most prominent players, Skeleton Technologies stands out for its proprietary “curved graphene” material, which underpins its ultracapacitor electrodes. The company has invested heavily in scaling up its manufacturing capacity in Europe, with a new factory in Germany expected to be operational by 2025. Skeleton’s partnerships with automotive OEMs and grid solution providers are aimed at integrating its electrodes into next-generation modules, with a focus on both performance and sustainability.
Panasonic Corporation remains a global heavyweight in the supercapacitor field, leveraging decades of expertise in electrode materials and automated manufacturing. Panasonic’s electrode technology is widely used in consumer electronics and industrial backup systems. The company continues to invest in R&D for advanced carbon-based electrodes, and has signaled intentions to expand its supercapacitor production lines in Asia to meet growing demand.
Maxwell Technologies, now a subsidiary of Tesla, Inc., is another key player, particularly in the automotive and grid storage sectors. Maxwell’s dry electrode technology, originally developed for supercapacitors, is being adapted for both ultracapacitor and lithium-ion battery applications. The integration of Maxwell’s expertise into Tesla’s broader energy storage strategy is expected to accelerate innovation in electrode manufacturing processes, with a focus on scalability and cost reduction.
Strategic partnerships are increasingly central to the sector’s evolution. For example, Skeleton Technologies has entered into collaborations with European automotive suppliers and energy infrastructure companies to co-develop tailored electrode solutions. Similarly, Panasonic is working with component manufacturers and system integrators to optimize electrode performance for specific use cases. These alliances are often aimed at accelerating the commercialization of new electrode materials, such as graphene and hybrid composites, and at streamlining supply chains.
Looking ahead, the next few years are likely to see further consolidation among electrode manufacturers, as well as increased cross-sector collaboration. The push for greener, more efficient manufacturing processes is expected to drive joint ventures focused on sustainable raw materials and recycling. As supercapacitor adoption broadens, the role of these key players and their strategic partnerships will be pivotal in shaping the future of electrode manufacturing.
Supply Chain Dynamics and Raw Material Sourcing
The supply chain dynamics and raw material sourcing for supercapacitor electrode manufacturing are undergoing significant transformation as the sector scales to meet growing demand in energy storage, automotive, and grid applications. In 2025, the focus is on securing reliable access to high-purity carbon materials, optimizing processing technologies, and establishing resilient supply networks amid geopolitical and environmental pressures.
Activated carbon, carbon nanotubes (CNTs), and graphene remain the dominant materials for supercapacitor electrodes. The majority of activated carbon is sourced from coconut shells and other biomass, with leading suppliers in Asia, particularly in China and India. Companies such as Cabot Corporation and Kuraray are recognized for their advanced activated carbon products tailored for energy storage. For CNTs and graphene, manufacturers like OCSiAl and First Graphene are expanding production capacities to address the surge in demand from supercapacitor and hybrid device manufacturers.
Supply chain resilience is a key concern in 2025, as the industry faces potential bottlenecks in raw material availability and price volatility. The concentration of precursor supply—such as pitch, petroleum coke, and specialty chemicals—remains a vulnerability. To mitigate risks, supercapacitor manufacturers are increasingly pursuing vertical integration and long-term contracts with raw material suppliers. For example, Maxwell Technologies (a subsidiary of Tesla) has invested in upstream partnerships to secure consistent supplies of electrode-grade carbon materials.
Sustainability and traceability are also shaping sourcing strategies. There is a growing emphasis on bio-based carbons and recycled materials, driven by both regulatory requirements and customer expectations. Companies like Kuraray are developing sustainable activated carbon lines, while others are piloting closed-loop recycling of electrode materials to reduce environmental impact and dependence on virgin resources.
Looking ahead, the next few years will likely see further diversification of supply sources, with new entrants in Southeast Asia and Europe aiming to localize production and reduce reliance on single-region suppliers. Strategic investments in raw material processing—such as advanced purification and functionalization—are expected to enhance electrode performance and cost competitiveness. Industry collaborations, such as those led by Saft and Maxwell Technologies, are fostering innovation in both materials and supply chain logistics, positioning the sector for robust growth and greater supply security through 2025 and beyond.
Application Expansion: Automotive, Grid Storage, Consumer Electronics
Supercapacitor electrode manufacturing is experiencing significant momentum in 2025, driven by expanding applications across automotive, grid storage, and consumer electronics sectors. The demand for high-performance, scalable, and cost-effective electrode materials is shaping both technological innovation and industrial investment.
In the automotive sector, the push for electrification and hybridization is accelerating the adoption of supercapacitors, particularly for start-stop systems, regenerative braking, and power buffering. Leading automotive suppliers and OEMs are collaborating with supercapacitor manufacturers to integrate advanced electrode materials, such as activated carbon, graphene, and carbon nanotubes, into next-generation modules. For example, Maxwell Technologies (now part of Tesla) has been a pioneer in developing electrode manufacturing processes that enable high energy and power densities, supporting automotive-grade reliability. Similarly, Skeleton Technologies is scaling up production of its patented curved graphene-based electrodes, targeting both passenger and commercial vehicle applications.
Grid storage is another rapidly growing application area, where supercapacitors are valued for their ability to deliver fast response times and high cycle life. Utilities and grid operators are increasingly deploying supercapacitor banks for frequency regulation, voltage stabilization, and renewable integration. This trend is prompting manufacturers to invest in automated electrode coating, calendaring, and assembly lines to meet the stringent quality and volume requirements of the energy sector. Companies like Skeleton Technologies and Eaton are actively expanding their supercapacitor offerings for grid-scale solutions, with a focus on robust electrode manufacturing and quality control.
In consumer electronics, the miniaturization of devices and the need for rapid charging are driving the adoption of supercapacitors in wearables, IoT sensors, and portable gadgets. Manufacturers are refining electrode fabrication techniques—such as roll-to-roll coating and laser patterning—to produce thin, flexible, and high-surface-area electrodes. Panasonic and Nesscap Energy (now part of Maxwell Technologies) are notable for their ongoing development of compact supercapacitor modules, leveraging advanced electrode materials and precision manufacturing.
Looking ahead, the outlook for supercapacitor electrode manufacturing is robust. Industry players are expected to further automate production, adopt greener and more sustainable materials, and enhance electrode architectures to meet the evolving demands of automotive electrification, grid modernization, and next-generation consumer devices. Strategic partnerships between material suppliers, equipment manufacturers, and end-users will likely accelerate the commercialization of novel electrode technologies over the next few years.
Sustainability Initiatives and Environmental Impact
Sustainability is rapidly becoming a central focus in supercapacitor electrode manufacturing, as the industry responds to both regulatory pressures and growing customer demand for greener energy storage solutions. In 2025, leading manufacturers are intensifying efforts to reduce the environmental footprint of electrode production, with a particular emphasis on raw material sourcing, process efficiency, and end-of-life management.
A significant trend is the shift toward bio-based and recycled carbon materials for electrode fabrication. Companies such as Skeleton Technologies and Maxwell Technologies are exploring the use of renewable precursors like lignin, cellulose, and coconut shells to produce activated carbon, which can significantly lower greenhouse gas emissions compared to traditional fossil-derived sources. This approach not only reduces reliance on non-renewable resources but also leverages agricultural waste, contributing to circular economy principles.
Process innovation is another area of focus. Manufacturers are investing in water-based electrode slurry formulations to replace toxic organic solvents, thereby minimizing hazardous waste and improving worker safety. For example, CAP-XX has reported progress in adopting solvent-free coating techniques, which can cut energy consumption and emissions during electrode drying. Additionally, companies are optimizing electrode thickness and porosity to maximize energy density while reducing material usage, further enhancing sustainability.
Life cycle assessments (LCAs) are increasingly being conducted to quantify the environmental impact of supercapacitor electrodes from cradle to grave. Organizations such as Eaton are publishing sustainability reports that detail reductions in water use, waste generation, and carbon emissions across their energy storage product lines. These assessments are guiding the selection of greener materials and more efficient manufacturing routes.
Looking ahead, regulatory frameworks in the EU, US, and Asia are expected to tighten, with stricter requirements for hazardous substance management and carbon disclosure. This is likely to accelerate the adoption of sustainable practices across the sector. Industry collaborations and consortia are also emerging to standardize green manufacturing metrics and share best practices, as seen in initiatives supported by International Electrotechnical Commission (IEC) standards.
In summary, 2025 marks a pivotal year for sustainability in supercapacitor electrode manufacturing. The convergence of material innovation, process optimization, and regulatory momentum is setting the stage for a new generation of environmentally responsible energy storage devices, with leading companies actively shaping this transition.
Regulatory Landscape and Industry Standards (e.g., ieee.org, iec.ch)
The regulatory landscape and industry standards for supercapacitor electrode manufacturing are evolving rapidly as the sector matures and global demand for high-performance energy storage grows. In 2025, regulatory frameworks are increasingly focused on ensuring product safety, environmental sustainability, and interoperability, while also supporting innovation in materials and manufacturing processes.
Key international standards bodies such as the IEEE and the International Electrotechnical Commission (IEC) play central roles in shaping the technical requirements for supercapacitor electrodes. The IEC’s TC 21 and SC 21A committees, for example, are responsible for standards related to secondary cells and batteries, including electrochemical capacitors (supercapacitors). The IEC 62391 series, which covers fixed electric double-layer capacitors for use in electronic equipment, is being updated to reflect advances in electrode materials, such as graphene and carbon nanotubes, and to address new manufacturing techniques like roll-to-roll coating and automated slurry casting.
In parallel, the IEEE continues to develop and refine standards for performance testing, safety, and reliability of supercapacitors, with particular attention to electrode composition and lifecycle assessment. The IEEE 1650 standard, for instance, specifies test methods for electric double-layer capacitors, and ongoing revisions are expected to incorporate new metrics for environmental impact and recyclability, reflecting the industry’s shift toward greener manufacturing.
Regionally, regulatory agencies are also tightening requirements. The European Union’s Battery Regulation, which will be fully enforced by 2027, includes provisions for carbon footprint disclosure, recycled content, and end-of-life management that directly impact electrode material sourcing and processing. In the United States, the Department of Energy and the Environmental Protection Agency are collaborating with industry to establish best practices for the safe handling of nanomaterials and solvents used in electrode fabrication.
Industry consortia and leading manufacturers are proactively engaging in standardization efforts. Companies such as Maxwell Technologies (a subsidiary of Tesla), Skeleton Technologies, and Panasonic are participating in working groups to harmonize testing protocols and quality benchmarks. These collaborations aim to accelerate certification processes and facilitate global market access for next-generation supercapacitor products.
Looking ahead, the regulatory environment is expected to become more stringent, with increased emphasis on traceability of raw materials, lifecycle emissions, and circular economy principles. Manufacturers will need to invest in compliance infrastructure and transparent supply chains to meet evolving standards, while ongoing dialogue between industry and standards bodies will be crucial to ensure that regulations keep pace with technological innovation in supercapacitor electrode manufacturing.
Future Outlook: Investment Hotspots and Disruptive Technologies
The supercapacitor electrode manufacturing sector is poised for significant transformation in 2025 and the following years, driven by both surging investment and the emergence of disruptive technologies. As global demand for high-power energy storage solutions intensifies—particularly in automotive, grid stabilization, and consumer electronics—manufacturers are accelerating efforts to scale up production and enhance electrode performance.
A key investment hotspot is the development and commercialization of advanced carbon materials, such as graphene and carbon nanotubes, which offer superior surface area and conductivity compared to traditional activated carbon. Companies like Skeleton Technologies are at the forefront, leveraging proprietary curved graphene materials to manufacture electrodes with higher energy and power densities. Their recent expansion of manufacturing capacity in Europe signals both confidence in market growth and a commitment to next-generation electrode technologies.
Another area attracting substantial investment is the automation and digitalization of electrode production lines. Industry leaders such as Maxwell Technologies (a subsidiary of Tesla, Inc.) are integrating advanced roll-to-roll coating, precision slurry mixing, and in-line quality control systems to boost throughput and consistency. These process innovations are expected to reduce costs and enable mass production, a critical factor as supercapacitors move from niche to mainstream applications.
Disruptive technologies on the horizon include the adoption of hybrid electrode architectures, combining carbon with metal oxides or conducting polymers to achieve higher capacitance and voltage windows. Companies like CAP-XX Limited are actively developing such hybrid solutions, targeting markets where both energy and power density are essential. Additionally, the use of bio-derived carbons and sustainable precursors is gaining traction, with several manufacturers exploring waste biomass as a feedstock to reduce environmental impact and supply chain risks.
Geographically, Asia-Pacific remains a dominant investment region, with major players such as Panasonic Corporation and LG Corporation expanding their electrode manufacturing capabilities to serve both domestic and global markets. However, Europe and North America are rapidly catching up, spurred by policy incentives and the localization of supply chains for electric vehicles and renewable energy storage.
Looking ahead, the convergence of material innovation, process automation, and sustainability is expected to define the competitive landscape of supercapacitor electrode manufacturing. Companies that can rapidly scale disruptive technologies while ensuring cost-effectiveness and environmental compliance are likely to capture significant market share in the coming years.
Sources & References
- Maxwell Technologies
- Skeleton Technologies
- LG Corporation
- Directa Plus
- First Graphene
- OCSiAl
- Arkema
- Cabot Corporation
- CAP-XX
- Eaton
- Cabot Corporation
- Kuraray
- First Graphene
- Maxwell Technologies
- IEEE