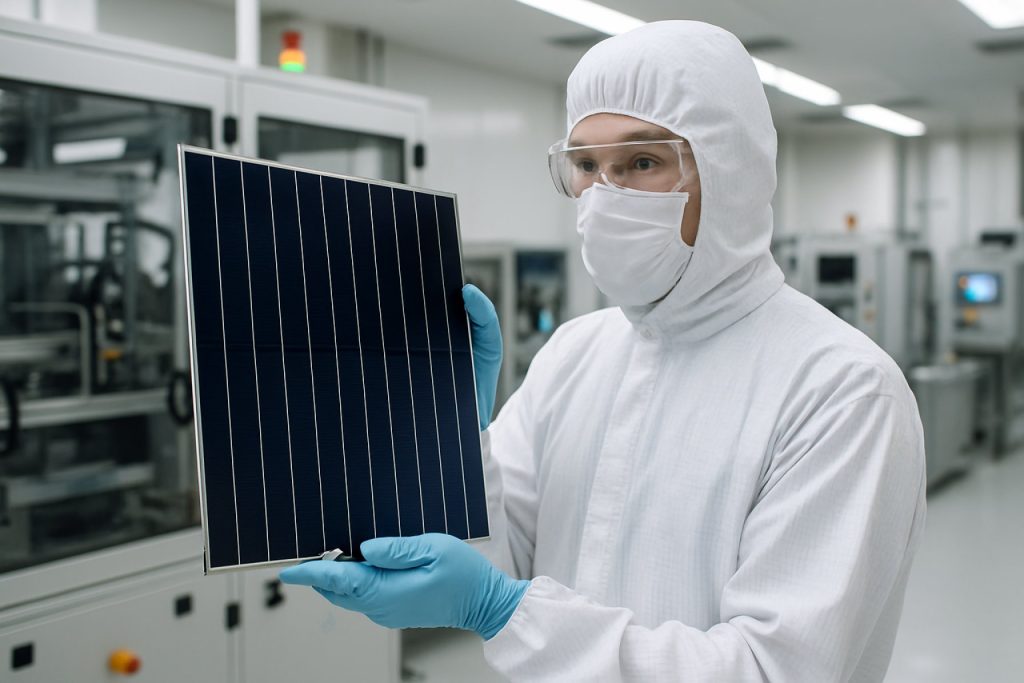
High-Efficiency Perovskite Photovoltaic Manufacturing in 2025: The Breakthrough Era for Solar Power. How Next-Gen Production is Driving Unprecedented Efficiency and Market Expansion.
- Executive Summary: 2025 Market Snapshot & Key Drivers
- Technology Overview: Perovskite Photovoltaics and Efficiency Milestones
- Manufacturing Innovations: Scaling High-Efficiency Production
- Competitive Landscape: Leading Companies and Strategic Partnerships
- Cost Analysis: CapEx, OpEx, and LCOE Trends
- Market Forecast 2025–2030: CAGR, Volume, and Revenue Projections
- Supply Chain and Raw Materials: Sourcing, Sustainability, and Bottlenecks
- Regulatory Environment and Industry Standards
- Emerging Applications: Tandem Cells, BIPV, and Flexible Modules
- Future Outlook: Challenges, Opportunities, and Roadmap to 2030
- Sources & References
Executive Summary: 2025 Market Snapshot & Key Drivers
The global market for high-efficiency perovskite photovoltaic (PV) manufacturing is poised for significant transformation in 2025, driven by rapid technological advancements, increased investment, and the urgent demand for scalable, cost-effective solar solutions. Perovskite solar cells, known for their high power conversion efficiencies and potential for low-cost production, are transitioning from laboratory-scale breakthroughs to commercial-scale manufacturing. In 2025, several industry leaders and consortia are accelerating the deployment of perovskite PV technologies, with pilot lines and early commercial modules entering the market.
Key drivers in 2025 include the need for higher efficiency solar modules to meet global decarbonization targets, the flexibility of perovskite materials for tandem and lightweight applications, and the potential for roll-to-roll manufacturing processes that promise lower capital expenditure compared to traditional silicon PV. Companies such as Oxford PV are at the forefront, having announced the ramp-up of their perovskite-on-silicon tandem cell production lines in Germany, targeting commercial module efficiencies above 25%. Similarly, Meyer Burger Technology AG is investing in perovskite tandem technology, leveraging its expertise in heterojunction and advanced cell manufacturing to scale up next-generation modules.
In Asia, Microquanta Semiconductor is advancing large-area perovskite module production, reporting certified module efficiencies exceeding 17% and aiming for further improvements through 2025. Meanwhile, GCL Technology Holdings is exploring perovskite-silicon tandem integration within its established PV manufacturing ecosystem. These efforts are supported by collaborative initiatives such as the European Perovskite Initiative (EPKI), which brings together industry and research stakeholders to address challenges in stability, scalability, and standardization.
The 2025 market snapshot indicates that perovskite PV manufacturing is moving from pilot to early commercial phases, with initial production capacities in the tens of megawatts and plans for gigawatt-scale expansion by 2027–2028. Key challenges remain, particularly in long-term operational stability and supply chain development for critical materials. However, the sector is buoyed by strong policy support in Europe, China, and the United States, as well as growing interest from established PV manufacturers seeking to diversify their technology portfolios.
Looking ahead, the outlook for high-efficiency perovskite PV manufacturing is optimistic. As companies demonstrate bankable module lifetimes and scale up production, perovskite technologies are expected to play a pivotal role in the next wave of solar deployment, offering higher efficiencies and new form factors that can accelerate the global energy transition.
Technology Overview: Perovskite Photovoltaics and Efficiency Milestones
Perovskite photovoltaics have rapidly emerged as a transformative technology in the solar energy sector, primarily due to their remarkable power conversion efficiencies and potential for low-cost, scalable manufacturing. The perovskite structure, typically based on hybrid organic-inorganic lead halides, enables strong light absorption and efficient charge transport, making it highly suitable for next-generation solar cells. Since their introduction, perovskite solar cells (PSCs) have seen a dramatic increase in certified power conversion efficiencies, rising from below 4% in 2009 to over 26% in laboratory settings by 2024. This trajectory rivals, and in some cases surpasses, the performance improvements seen in traditional silicon photovoltaics over comparable timeframes.
As of 2025, the focus within the industry has shifted from laboratory-scale breakthroughs to the development of high-efficiency, stable, and scalable manufacturing processes. Several companies are at the forefront of this transition. Oxford PV, a UK-German company, has been a pioneer in commercializing perovskite-on-silicon tandem cells, achieving certified efficiencies above 28% and targeting mass production at its Brandenburg facility. Their approach leverages existing silicon cell infrastructure, integrating a perovskite layer to boost overall module efficiency. Similarly, Meyer Burger Technology AG, a Swiss manufacturer, has announced plans to integrate perovskite technology into its product roadmap, aiming to deliver high-efficiency modules for both rooftop and utility-scale applications.
In Asia, TCL and its subsidiary TCL Zhonghuan Renewable Energy Technology are investing in perovskite R&D and pilot production lines, with a focus on scaling up roll-to-roll and inkjet printing techniques for large-area modules. These methods promise significant reductions in manufacturing costs and material usage compared to conventional silicon wafer processes. Meanwhile, Hanwha Solutions is exploring perovskite-silicon tandem architectures, leveraging its established presence in the global solar market to accelerate commercialization.
Industry bodies such as the International Energy Agency (IEA) and Fraunhofer Institute for Solar Energy Systems are closely monitoring perovskite developments, highlighting the technology’s potential to surpass 30% efficiency in tandem configurations within the next few years. The outlook for 2025 and beyond is characterized by rapid progress in stability, upscaling, and integration with existing photovoltaic manufacturing lines. As leading manufacturers move from pilot to gigawatt-scale production, perovskite photovoltaics are poised to play a pivotal role in the global transition to high-efficiency, cost-effective solar energy.
Manufacturing Innovations: Scaling High-Efficiency Production
The year 2025 marks a pivotal period for high-efficiency perovskite photovoltaic (PV) manufacturing, as the sector transitions from laboratory-scale breakthroughs to industrial-scale production. Recent advances in scalable deposition techniques, tandem cell integration, and process automation are driving this shift, with several industry leaders and consortia spearheading commercialization efforts.
One of the most significant manufacturing innovations is the adoption of roll-to-roll (R2R) and slot-die coating processes, which enable continuous, high-throughput fabrication of perovskite layers on flexible substrates. Companies such as Oxford PV and Saule Technologies have demonstrated pilot lines utilizing these methods, achieving module efficiencies exceeding 25% in tandem configurations. Oxford PV, in particular, has scaled up its perovskite-silicon tandem cell production at its Brandenburg, Germany facility, targeting gigawatt-scale output by 2025 and beyond.
Automation and in-line quality control are also being integrated into perovskite PV manufacturing lines. Meyer Burger Technology AG, a Swiss photovoltaics equipment manufacturer, is collaborating with perovskite developers to adapt its precision coating and laser structuring tools for perovskite-silicon tandem modules. These innovations are expected to reduce defect rates and improve yield, addressing one of the key challenges in scaling perovskite production.
Material supply chain development is another area of focus. Companies like Dyesol (now Greatcell Solar) and Saule Technologies are investing in the synthesis and purification of perovskite precursors at industrial scale, ensuring consistent quality and environmental compliance. Efforts to replace lead with less toxic alternatives are ongoing, with several pilot projects underway in 2025.
Looking ahead, the outlook for high-efficiency perovskite PV manufacturing is robust. Industry roadmaps anticipate the first commercial installations of perovskite-silicon tandem modules in Europe and Asia by late 2025, with rapid capacity expansion projected through 2027. The International PV Quality Assurance Task Force and other industry bodies are working to standardize testing and certification protocols, further supporting market adoption.
In summary, 2025 is set to be a breakthrough year for perovskite PV manufacturing, with innovations in scalable processing, automation, and supply chain integration positioning the technology for mainstream deployment in the global solar market.
Competitive Landscape: Leading Companies and Strategic Partnerships
The competitive landscape for high-efficiency perovskite photovoltaic (PV) manufacturing in 2025 is characterized by rapid technological advancements, strategic partnerships, and the emergence of key players transitioning from laboratory-scale innovation to commercial-scale production. Several companies are at the forefront, leveraging proprietary processes and forming alliances to accelerate the commercialization of perovskite solar cells.
One of the most prominent players is Oxford PV, a UK-German company recognized for its pioneering work in perovskite-silicon tandem solar cells. In 2024, Oxford PV announced the completion of its first volume manufacturing line in Germany, targeting module efficiencies above 25%. The company’s strategic partnership with Meyer Burger Technology AG, a Swiss PV equipment manufacturer, is pivotal for scaling up production and integrating perovskite technology into established silicon module lines. Meyer Burger, known for its expertise in heterojunction and SmartWire technologies, is actively exploring perovskite integration to maintain its competitive edge.
In Asia, TCL and its subsidiary TCL Zhonghuan Renewable Energy Technology have invested heavily in perovskite R&D, aiming to leverage their large-scale manufacturing capabilities. TCL Zhonghuan, a major supplier of silicon wafers, is collaborating with research institutes to develop tandem modules that combine perovskite and silicon, with pilot lines expected to be operational by 2025.
China’s GCL Technology Holdings is also entering the perovskite market, building on its established position in polysilicon and wafer manufacturing. GCL is investing in pilot production lines and has announced intentions to commercialize perovskite modules, focusing on cost reduction and scalability.
In the United States, First Solar—a leader in thin-film PV—has signaled interest in perovskite research, exploring hybrid approaches that could complement its cadmium telluride (CdTe) technology. While First Solar’s commercial perovskite products are not yet on the market, its R&D activities and potential for partnerships position it as a future contender.
Strategic partnerships are a defining feature of the sector. Collaborations between technology developers, equipment manufacturers, and material suppliers are essential for overcoming challenges related to stability, scalability, and cost. As of 2025, the competitive landscape is expected to intensify, with new entrants and established PV giants racing to achieve commercial viability and secure market share in the high-efficiency perovskite segment.
Cost Analysis: CapEx, OpEx, and LCOE Trends
The cost structure of high-efficiency perovskite photovoltaic (PV) manufacturing is rapidly evolving as the technology transitions from laboratory-scale breakthroughs to commercial-scale production. In 2025, capital expenditures (CapEx) for perovskite PV manufacturing lines are notably lower than those for traditional silicon-based PV, primarily due to the simpler deposition processes and reduced material requirements. For example, roll-to-roll and slot-die coating techniques, which are compatible with perovskite materials, enable high-throughput production with less energy and fewer processing steps compared to silicon wafer fabrication. Companies such as Oxford PV and Saule Technologies are actively scaling up manufacturing, with pilot lines demonstrating CapEx advantages by leveraging existing infrastructure and low-temperature processing.
Operational expenditures (OpEx) are also favorably impacted by the inherent properties of perovskite materials. The ability to process perovskites at ambient or low temperatures reduces energy consumption, while the use of abundant and inexpensive precursor materials further lowers costs. Additionally, the modularity of perovskite manufacturing lines allows for flexible scaling, minimizing downtime and maintenance costs. Saule Technologies, for instance, has highlighted the cost-effectiveness of their inkjet printing approach, which reduces material waste and enables rapid production cycles.
Levelized cost of electricity (LCOE) is a critical metric for assessing the competitiveness of perovskite PV. In 2025, LCOE for high-efficiency perovskite modules is projected to be highly competitive with, and in some cases lower than, that of conventional silicon PV, especially as module efficiencies surpass 25% in commercial settings. The tandem architecture, combining perovskite with silicon, as pursued by Oxford PV, further enhances energy yield and reduces LCOE by maximizing the utilization of the solar spectrum. As manufacturing yields improve and economies of scale are realized, industry bodies such as International Energy Agency (IEA) anticipate continued downward pressure on LCOE for perovskite-based systems through the late 2020s.
Looking ahead, the outlook for cost reduction in perovskite PV manufacturing remains strong. Ongoing investments in automation, materials optimization, and process integration are expected to further decrease both CapEx and OpEx. As more companies, including Oxford PV and Saule Technologies, move toward gigawatt-scale production, the perovskite sector is poised to deliver some of the lowest LCOE figures in the solar industry, accelerating the adoption of high-efficiency PV worldwide.
Market Forecast 2025–2030: CAGR, Volume, and Revenue Projections
The global market for high-efficiency perovskite photovoltaic (PV) manufacturing is poised for significant expansion between 2025 and 2030, driven by rapid technological advancements, increasing investments, and the urgent need for scalable, cost-effective solar solutions. As of 2025, several leading companies have transitioned from pilot-scale to early commercial-scale production, with a focus on tandem perovskite-silicon modules and all-perovskite architectures. This shift is expected to catalyze robust compound annual growth rates (CAGR) and substantial increases in both production volume and market revenue.
Industry projections for 2025–2030 indicate a CAGR in the range of 35–45% for high-efficiency perovskite PV manufacturing, outpacing traditional silicon PV growth rates. This acceleration is underpinned by the entry of major players such as Oxford PV, which has commenced commercial production of perovskite-on-silicon tandem cells in Germany, targeting module efficiencies above 25%. Similarly, Meyer Burger Technology AG is investing in perovskite tandem cell lines, aiming to scale up manufacturing capacity in Europe. In Asia, Microquanta Semiconductor is advancing roll-to-roll perovskite module production, with pilot lines already operational and plans for gigawatt-scale facilities by 2027.
By 2025, global annual production capacity for high-efficiency perovskite PV modules is estimated to reach 500–700 MW, with projections suggesting a surge to 5–8 GW by 2030 as new manufacturing plants come online and existing lines are upgraded. Revenue from perovskite PV modules is expected to grow from under $500 million in 2025 to over $4 billion by 2030, assuming continued improvements in module stability, certification, and bankability. The European Union’s Green Deal and the U.S. Inflation Reduction Act are anticipated to further stimulate demand and investment in domestic perovskite PV manufacturing, supporting regional supply chains and job creation.
Key market drivers include the superior power conversion efficiencies of perovskite-based modules, lower energy payback times, and the potential for lightweight, flexible, and semi-transparent applications. However, the market outlook is contingent on overcoming challenges related to long-term stability, lead management, and large-scale process standardization. Industry consortia such as Heliatek and Solliance are actively collaborating with manufacturers to address these hurdles and accelerate commercialization.
In summary, the period from 2025 to 2030 is expected to mark the transition of high-efficiency perovskite PV from niche pilot projects to a mainstream, multi-gigawatt market segment, with strong growth prospects and increasing contributions to the global renewable energy mix.
Supply Chain and Raw Materials: Sourcing, Sustainability, and Bottlenecks
The supply chain for high-efficiency perovskite photovoltaic (PV) manufacturing in 2025 is characterized by both rapid innovation and emerging challenges, particularly in the sourcing and sustainability of raw materials. Perovskite solar cells rely on a unique class of materials—typically hybrid organic-inorganic lead or tin halide compounds—which offer high power conversion efficiencies and compatibility with scalable manufacturing processes. However, the sector’s growth is closely tied to the availability, cost, and environmental impact of these materials.
Key raw materials include lead iodide, methylammonium or formamidinium salts, tin compounds (for lead-free variants), and specialty solvents. The supply of high-purity lead iodide and organic cations is currently dominated by a handful of chemical suppliers, with Merck KGaA (also known as EMD Electronics in North America) and Alfa Laval among the notable providers of specialty chemicals and process solutions for the PV industry. These companies are investing in expanding their production capacities and improving the sustainability of their supply chains, including the implementation of green chemistry principles and closed-loop recycling for solvents and precursors.
Sustainability concerns are driving efforts to reduce or eliminate toxic lead content in perovskite formulations. Several manufacturers, such as Oxford PV and Saule Technologies, are actively developing lead-free or lead-reduced perovskite cells, exploring tin-based alternatives and encapsulation strategies to mitigate environmental risks. These companies are also working to ensure responsible sourcing of tin, which is subject to scrutiny due to potential links with conflict minerals.
Bottlenecks in the supply chain are emerging as pilot lines scale to gigawatt-level production. The availability of high-purity precursors, especially for large-area modules, is a critical constraint. Additionally, the supply of specialty substrates (such as flexible polymers and transparent conductive oxides) and encapsulation materials is under pressure as demand rises. Saint-Gobain and AGC Inc. are among the major suppliers of advanced glass and substrate materials, investing in new product lines tailored for perovskite PV applications.
Looking ahead, the industry is expected to prioritize vertical integration and local sourcing to reduce geopolitical risks and carbon footprints. Initiatives for recycling perovskite modules and reclaiming valuable materials are gaining traction, with several pilot projects underway in Europe and Asia. As perovskite PV manufacturing moves toward commercialization, robust supply chain management and sustainable sourcing will be essential to support the sector’s anticipated growth through 2025 and beyond.
Regulatory Environment and Industry Standards
The regulatory environment for high-efficiency perovskite photovoltaic (PV) manufacturing is rapidly evolving in 2025, reflecting both the technology’s maturation and its increasing commercial relevance. As perovskite solar cells transition from laboratory-scale breakthroughs to industrial-scale production, regulatory bodies and industry organizations are intensifying efforts to establish robust standards for safety, performance, and environmental impact.
A key focus in 2025 is the harmonization of international standards for perovskite PV modules. The International Electrotechnical Commission (IEC) is actively developing and updating test protocols specific to perovskite technologies, building on its established IEC 61215 and IEC 61730 standards for crystalline silicon modules. These efforts aim to address the unique stability and degradation challenges associated with perovskite materials, particularly under real-world operating conditions. The IEC is collaborating with leading manufacturers and research institutes to ensure that new standards reflect the latest advances in encapsulation, lead management, and accelerated aging tests.
In parallel, the UL Solutions (formerly Underwriters Laboratories) is working with perovskite PV producers to adapt its certification schemes for module safety and fire resistance, which are prerequisites for market entry in North America and other regions. These certifications are increasingly important as companies such as Oxford PV and Meyer Burger Technology AG move toward commercial-scale production of perovskite-silicon tandem modules, targeting both utility-scale and residential markets.
Environmental regulations are also tightening, particularly regarding the use of lead in perovskite formulations. The European Union’s European Commission is reviewing the applicability of the Restriction of Hazardous Substances (RoHS) directive to perovskite PV, with potential implications for allowable lead content and end-of-life recycling requirements. Manufacturers are responding by investing in lead-sequestration technologies and exploring lead-free perovskite alternatives, as seen in pilot lines operated by Saule Technologies and others.
Industry consortia such as the Solar Energy Industries Association (SEIA) and the SolarPower Europe are facilitating dialogue between manufacturers, regulators, and stakeholders to ensure that new standards support both innovation and public trust. Looking ahead, the next few years are expected to see the formal adoption of perovskite-specific standards, increased regulatory scrutiny of material safety, and the integration of circular economy principles into perovskite PV manufacturing.
Emerging Applications: Tandem Cells, BIPV, and Flexible Modules
The landscape of high-efficiency perovskite photovoltaic (PV) manufacturing in 2025 is rapidly evolving, with emerging applications such as tandem cells, building-integrated photovoltaics (BIPV), and flexible modules driving innovation and commercial interest. These applications leverage the unique properties of perovskite materials—such as tunable bandgaps, lightweight form factors, and compatibility with low-temperature processing—to address limitations of conventional silicon PV and unlock new market segments.
Tandem solar cells, which stack perovskite layers atop silicon or other established PV technologies, are at the forefront of efficiency gains. In 2024, several manufacturers reported certified tandem cell efficiencies exceeding 29%, with pilot production lines targeting module efficiencies above 25% for commercial deployment in 2025 and beyond. Oxford PV, a leading UK-German company, has announced plans to scale up its perovskite-on-silicon tandem technology, aiming for gigawatt-scale manufacturing at its Brandenburg facility. The company’s roadmap includes integration into existing silicon module lines, with initial commercial modules expected to reach the market in 2025. Similarly, Meyer Burger Technology AG, a Swiss PV equipment manufacturer, is collaborating with perovskite developers to adapt its production lines for tandem cell assembly, signaling broader industry adoption.
Building-integrated photovoltaics (BIPV) represent another promising avenue, as perovskite modules can be engineered for semi-transparency, color tunability, and lightweight construction. This enables seamless integration into windows, façades, and other architectural elements. Companies such as Solaronix and Energies SA are actively developing perovskite-based BIPV prototypes, with pilot installations underway in Europe. These efforts are supported by collaborations with construction and glass manufacturers, aiming to demonstrate long-term stability and aesthetic versatility in real-world environments.
Flexible perovskite modules are also gaining traction, particularly for portable electronics, wearables, and off-grid applications. The ability to deposit perovskite layers on plastic or metal foils using roll-to-roll processes offers significant cost and weight advantages. GCL Technology Holdings, a major Chinese PV manufacturer, has announced R&D initiatives focused on flexible perovskite modules, targeting commercial samples for field testing in 2025. These developments are complemented by ongoing efforts from academic spin-offs and startups across Asia, Europe, and North America.
Looking ahead, the next few years are expected to see accelerated commercialization of these emerging applications, driven by continued improvements in perovskite stability, scalable manufacturing, and integration with existing PV infrastructure. As leading manufacturers ramp up pilot lines and forge partnerships across the value chain, perovskite-based tandem, BIPV, and flexible modules are poised to play a transformative role in the global solar market.
Future Outlook: Challenges, Opportunities, and Roadmap to 2030
As of 2025, the future outlook for high-efficiency perovskite photovoltaic (PV) manufacturing is marked by both significant promise and notable challenges. The sector is transitioning from laboratory-scale breakthroughs to industrial-scale production, with several key players and consortia driving this evolution. Companies such as Oxford PV and Saule Technologies are at the forefront, having demonstrated perovskite-silicon tandem cells with certified efficiencies exceeding 28%, and are now scaling up pilot manufacturing lines. Oxford PV in particular has announced plans to ramp up commercial production in Germany, targeting the building-integrated photovoltaics (BIPV) and rooftop solar markets.
Despite these advances, several challenges remain on the path to widespread adoption by 2030. The most pressing technical hurdle is the long-term operational stability of perovskite materials under real-world conditions, including exposure to moisture, heat, and ultraviolet light. Efforts to address these issues are ongoing, with encapsulation technologies and compositional engineering being actively developed by industry leaders. Additionally, the supply chain for key precursor materials, such as lead and specialty organic compounds, must be secured and made sustainable to support gigawatt-scale manufacturing.
On the regulatory and environmental front, the presence of lead in most high-efficiency perovskite formulations has prompted scrutiny. Industry groups and manufacturers are collaborating to develop recycling protocols and explore lead-free alternatives, though the latter currently lag behind in efficiency. Organizations such as Fraunhofer ISE are working with manufacturers to establish best practices for lifecycle management and environmental safety.
Opportunities abound as perovskite PV technologies offer the potential for lightweight, flexible, and semi-transparent modules, opening new markets in portable electronics, vehicle integration, and urban infrastructure. The relatively low-temperature, solution-based manufacturing processes promise lower capital expenditure and energy use compared to traditional silicon PV, which could accelerate global deployment, especially in emerging markets.
Looking ahead to 2030, the roadmap for high-efficiency perovskite PV manufacturing will likely involve hybrid tandem modules, further improvements in stability, and the establishment of robust recycling and end-of-life management systems. Strategic partnerships between technology developers, material suppliers, and established PV manufacturers—such as those between Oxford PV and Meyer Burger Technology AG—are expected to play a pivotal role in scaling up production and reducing costs. If current trends continue, perovskite PV could capture a significant share of new solar installations by the end of the decade, provided that technical and regulatory challenges are effectively addressed.
Sources & References
- Oxford PV
- Meyer Burger Technology AG
- Microquanta Semiconductor
- International Energy Agency
- Fraunhofer Institute for Solar Energy Systems
- Saule Technologies
- First Solar
- Heliatek
- Solliance
- Alfa Laval
- AGC Inc.
- UL Solutions
- European Commission
- Solaronix