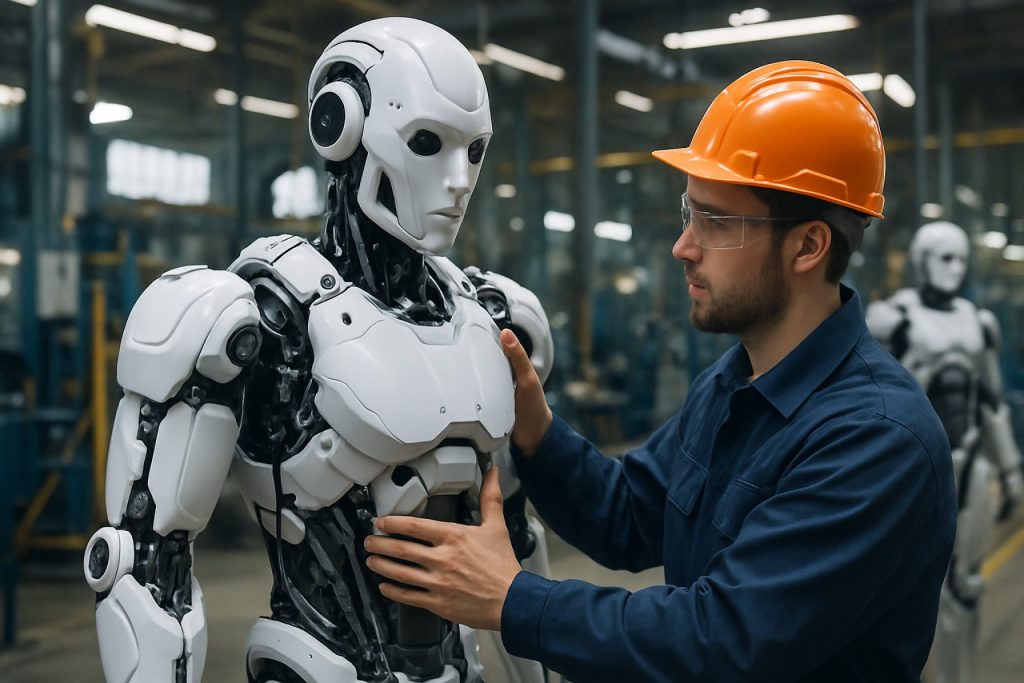
Humanoid Exoskeleton Manufacturing in 2025: How Next-Gen Robotics Are Accelerating Human Performance and Transforming Industry. Explore the Breakthroughs, Market Growth, and Strategic Shifts Shaping the Future.
- Executive Summary: 2025 Market Snapshot and Key Drivers
- Global Market Size, Growth Rate, and 2029 Forecast
- Technological Innovations: Materials, Sensors, and AI Integration
- Leading Manufacturers and Industry Collaborations
- Key Application Sectors: Healthcare, Defense, and Industrial
- Regulatory Landscape and Safety Standards
- Supply Chain Dynamics and Component Sourcing
- Investment Trends and Funding Landscape
- Challenges: Scalability, Cost, and User Adoption
- Future Outlook: Strategic Opportunities and Disruptive Trends
- Sources & References
Executive Summary: 2025 Market Snapshot and Key Drivers
The global humanoid exoskeleton manufacturing sector is poised for significant growth in 2025, driven by rapid advancements in robotics, materials science, and artificial intelligence. Humanoid exoskeletons—wearable robotic systems designed to augment human movement and strength—are increasingly being adopted across medical rehabilitation, industrial, defense, and personal mobility applications. The market is characterized by a surge in R&D investments, strategic partnerships, and a growing number of regulatory approvals, all of which are accelerating commercialization and deployment.
Key industry players such as CYBERDYNE Inc., a pioneer in medical and assistive exoskeletons, and SUITX (now part of Ottobock), are expanding their product portfolios to address both clinical and industrial needs. CYBERDYNE Inc.’s HAL (Hybrid Assistive Limb) system continues to gain traction in rehabilitation centers, while SUITX focuses on modular exoskeletons for workplace injury prevention. Meanwhile, Sarcos Technology and Robotics Corporation is advancing the commercialization of its Guardian XO, a full-body, battery-powered exoskeleton designed for heavy industrial tasks, with pilot deployments in logistics and manufacturing sectors.
In 2025, the sector is witnessing increased collaboration between exoskeleton manufacturers and major healthcare providers, automotive OEMs, and defense agencies. For example, Lockheed Martin continues to develop exoskeleton solutions for military applications, focusing on soldier endurance and load-carrying capacity. Simultaneously, regulatory bodies in North America, Europe, and Asia are streamlining approval pathways, enabling faster market entry for new devices.
Key drivers for the market in 2025 include the rising prevalence of musculoskeletal disorders, an aging global population, and the need for enhanced worker safety and productivity. The integration of advanced sensors, lightweight composite materials, and AI-driven control systems is making humanoid exoskeletons more ergonomic, affordable, and adaptable to diverse user needs. Additionally, government funding and public-private partnerships are supporting pilot programs and large-scale deployments, particularly in rehabilitation and eldercare.
Looking ahead, the outlook for humanoid exoskeleton manufacturing remains robust, with expectations of double-digit annual growth rates over the next few years. As manufacturing processes mature and economies of scale are realized, costs are projected to decrease, further expanding adoption across sectors. The convergence of robotics, healthcare, and industrial automation is set to redefine human augmentation, positioning humanoid exoskeletons as a transformative technology in the coming years.
Global Market Size, Growth Rate, and 2029 Forecast
The global market for humanoid exoskeleton manufacturing is poised for significant expansion in 2025 and the years immediately following, driven by advances in robotics, materials science, and the growing demand for assistive and augmentative technologies. As of 2025, the sector is characterized by a mix of established robotics firms, specialized exoskeleton manufacturers, and new entrants leveraging artificial intelligence and lightweight materials to enhance product capabilities and accessibility.
Key industry players include CYBERDYNE Inc., a Japanese pioneer known for its HAL (Hybrid Assistive Limb) exoskeletons, and SUITX (now part of Ottobock), which has developed modular exoskeletons for both industrial and medical applications. Sarcos Technology and Robotics Corporation in the United States is also notable for its Guardian XO, a full-body, battery-powered exoskeleton designed for industrial and defense use. European companies such as Ottobock and ReWalk Robotics are further expanding their portfolios to include more humanoid and lower-limb exoskeletons, targeting rehabilitation and mobility markets.
In 2025, the global humanoid exoskeleton market is estimated to be valued in the low-to-mid single-digit billions (USD), with annual growth rates projected in the range of 20–30% through the end of the decade. This robust growth is fueled by increasing adoption in healthcare—particularly for rehabilitation and mobility assistance—as well as in industrial settings where exoskeletons are used to reduce worker fatigue and injury. The defense sector is also a significant driver, with ongoing investments in powered exoskeletons for enhanced soldier performance and logistics support.
Looking ahead to 2029, the market is expected to surpass the USD 5 billion mark, with some forecasts suggesting even higher figures as technology matures and costs decrease. The Asia-Pacific region, led by Japan, South Korea, and China, is anticipated to see the fastest growth due to strong government support, rapid industrialization, and an aging population driving demand for assistive devices. North America and Europe will continue to be major markets, supported by established healthcare infrastructure and ongoing R&D investments.
Overall, the outlook for humanoid exoskeleton manufacturing is highly positive, with technological innovation, regulatory approvals, and broader insurance coverage likely to accelerate adoption rates. As companies like CYBERDYNE Inc., Sarcos Technology and Robotics Corporation, and Ottobock continue to scale production and expand their product lines, the sector is set to become a cornerstone of the next generation of wearable robotics.
Technological Innovations: Materials, Sensors, and AI Integration
The field of humanoid exoskeleton manufacturing is undergoing rapid technological transformation, driven by advances in materials science, sensor technology, and artificial intelligence (AI) integration. As of 2025, manufacturers are prioritizing lightweight, durable materials, sophisticated sensor arrays, and AI-powered control systems to enhance exoskeleton performance, comfort, and adaptability.
Material innovation remains a cornerstone of exoskeleton development. Leading manufacturers are increasingly adopting advanced composites, such as carbon fiber-reinforced polymers and aerospace-grade aluminum alloys, to reduce device weight while maintaining structural integrity. For example, SUITX and Samsung have both highlighted the use of lightweight materials in their latest exoskeleton prototypes, aiming to improve user mobility and reduce fatigue. Additionally, the integration of soft robotics—using flexible, textile-based actuators—has gained traction, allowing for more natural movement and improved user comfort.
Sensor technology is another area of significant progress. Modern humanoid exoskeletons are equipped with a network of sensors, including inertial measurement units (IMUs), force sensors, and electromyography (EMG) sensors, to monitor user intent and biomechanical parameters in real time. Panasonic and CYBERDYNE Inc. have incorporated multi-modal sensor systems into their exoskeletons, enabling precise motion tracking and adaptive assistance. These sensors not only enhance safety by detecting abnormal gait or posture but also facilitate personalized support tailored to individual users.
AI integration is rapidly redefining the capabilities of humanoid exoskeletons. Machine learning algorithms process sensor data to predict user movements, optimize actuator responses, and adapt to changing environments. ReWalk Robotics and Ekso Bionics are actively developing AI-driven control systems that enable smoother, more intuitive interactions between the user and the exoskeleton. These systems can learn from user behavior over time, offering increasingly refined assistance and reducing the cognitive load on the wearer.
Looking ahead, the convergence of advanced materials, sensor fusion, and AI is expected to yield exoskeletons that are lighter, smarter, and more accessible. Industry leaders are investing in modular designs and cloud-based analytics to support remote diagnostics and continuous improvement. As these innovations mature, the next few years are likely to see broader adoption of humanoid exoskeletons in rehabilitation, industrial, and assistive applications, with ongoing collaboration between manufacturers, research institutions, and healthcare providers driving further breakthroughs.
Leading Manufacturers and Industry Collaborations
The landscape of humanoid exoskeleton manufacturing in 2025 is characterized by a dynamic interplay between established robotics firms, innovative startups, and cross-industry collaborations. The sector is witnessing rapid technological advancements, with a focus on enhancing mobility, strength augmentation, and rehabilitation capabilities for both medical and industrial applications.
Among the leading manufacturers, CYBERDYNE Inc. of Japan continues to be a global pioneer, particularly with its HAL (Hybrid Assistive Limb) exoskeletons. These devices are deployed in hospitals and rehabilitation centers across Asia and Europe, and the company is expanding its manufacturing capacity to meet growing demand in North America. CYBERDYNE Inc. is also engaged in partnerships with medical institutions and universities to further refine its humanoid exoskeleton technologies.
In the United States, Ekso Bionics Holdings, Inc. remains at the forefront, supplying exoskeletons for both clinical rehabilitation and industrial workforce support. Their EksoNR and EksoVest models are widely adopted in hospitals and manufacturing plants, respectively. The company has recently announced collaborations with major automotive and aerospace manufacturers to co-develop exoskeletons tailored for assembly line workers, aiming to reduce workplace injuries and improve productivity.
Europe’s Ottobock SE & Co. KGaA, renowned for its expertise in prosthetics and orthotics, has expanded its exoskeleton portfolio with the Paexo series. These lightweight exoskeletons are designed for industrial use, particularly in logistics and construction. Ottobock is actively collaborating with research institutes and industrial partners to integrate advanced sensor technologies and AI-driven motion control into its next-generation humanoid exoskeletons.
China’s SUITX (now part of Bioservo Technologies AB) is making significant strides in both medical and industrial exoskeletons, leveraging the country’s robust manufacturing infrastructure. The company is focusing on scalable production and cost reduction, aiming to make exoskeletons more accessible for rehabilitation centers and factories across Asia.
Industry collaborations are intensifying, with joint ventures between robotics firms, healthcare providers, and industrial conglomerates. For example, CYBERDYNE Inc. and Ottobock have both entered into research partnerships with leading universities to accelerate the development of AI-powered exoskeletons. These collaborations are expected to yield more adaptive, user-friendly, and affordable humanoid exoskeletons in the coming years, driving broader adoption across sectors.
Key Application Sectors: Healthcare, Defense, and Industrial
The manufacturing of humanoid exoskeletons is rapidly advancing, with significant momentum in three primary application sectors: healthcare, defense, and industrial environments. As of 2025, these sectors are driving both technological innovation and commercial adoption, shaping the direction of exoskeleton development and production.
Healthcare remains the most mature and widely adopted sector for humanoid exoskeletons. Devices are increasingly used for rehabilitation, mobility assistance, and physical therapy, particularly for patients with spinal cord injuries, stroke, or age-related mobility loss. Leading manufacturers such as Ekso Bionics and ReWalk Robotics have established FDA-cleared exoskeletons for clinical and personal use. In 2025, production is scaling to meet growing demand from hospitals and rehabilitation centers, with a focus on lighter materials, improved battery life, and enhanced user interfaces. The integration of AI-driven gait analysis and remote monitoring is also becoming standard, enabling more personalized therapy and data-driven outcomes.
In the defense sector, exoskeleton manufacturing is driven by the need to augment soldier strength, endurance, and injury prevention. Organizations such as Lockheed Martin are actively developing and testing exoskeleton prototypes for military applications, including load carriage and fatigue reduction. The ONYX exoskeleton, for example, is designed to support soldiers during physically demanding tasks. In 2025 and beyond, defense contracts are expected to accelerate production, with a focus on ruggedization, rapid donning/doffing, and seamless integration with existing military gear. Collaboration between defense agencies and private manufacturers is fostering rapid prototyping and field trials, with the goal of operational deployment within the next few years.
The industrial sector is witnessing a surge in exoskeleton adoption for workplace safety and productivity. Companies such as SuitX (now part of Ottobock) and Sarcos Technology and Robotics Corporation are manufacturing exoskeletons tailored for logistics, manufacturing, and construction. These devices are engineered to reduce musculoskeletal injuries, support repetitive lifting, and extend worker stamina. In 2025, manufacturers are focusing on modular designs, cost reduction, and ergonomic improvements to facilitate broader deployment across diverse industries. Partnerships with major automotive and logistics firms are driving pilot programs and scaling up production lines.
Looking ahead, the convergence of advanced materials, robotics, and AI is expected to further blur the lines between these sectors, with cross-sector innovations accelerating the pace of humanoid exoskeleton manufacturing and adoption through 2025 and the following years.
Regulatory Landscape and Safety Standards
The regulatory landscape for humanoid exoskeleton manufacturing is rapidly evolving as these devices transition from research prototypes to commercial products in medical, industrial, and military sectors. In 2025, regulatory bodies are intensifying their focus on safety, efficacy, and interoperability, reflecting the growing adoption of exoskeletons in rehabilitation, workplace assistance, and mobility enhancement.
In the medical domain, exoskeletons are increasingly classified as medical devices, subject to rigorous approval processes. The U.S. Food and Drug Administration (FDA) continues to require premarket notification (510(k)) or premarket approval (PMA) for powered exoskeletons intended for rehabilitation or mobility assistance. Companies such as Ekso Bionics and ReWalk Robotics have obtained FDA clearances for their lower-limb exoskeletons, setting precedents for safety and performance standards. The FDA emphasizes requirements for clinical data, biocompatibility, electrical safety, and software validation, and is expected to update its guidance as more advanced, AI-driven exoskeletons enter the market.
In Europe, the European Medicines Agency and national notified bodies enforce the Medical Device Regulation (MDR 2017/745), which mandates conformity assessment, CE marking, and post-market surveillance for exoskeletons. Manufacturers like Hocoma and CYBERDYNE have achieved CE certification for their devices, demonstrating compliance with essential health and safety requirements. The MDR’s focus on risk management, usability engineering, and clinical evaluation is shaping design and documentation practices across the industry.
For industrial exoskeletons, regulatory frameworks are less mature but developing. Organizations such as the International Organization for Standardization (ISO) and the IEEE are working on standards addressing ergonomics, mechanical safety, and human-robot interaction. ISO 13482:2014, which covers safety requirements for personal care robots, is being referenced and adapted for exoskeletons, while new standards specific to wearable robotics are under discussion. Leading manufacturers like SuitX (now part of Ottobock) and Sarcos Technology and Robotics Corporation are actively participating in these standardization efforts.
Looking ahead, the next few years will likely see the introduction of harmonized global standards, particularly as exoskeletons become more autonomous and interconnected. Regulatory agencies are expected to address emerging concerns such as cybersecurity, data privacy, and AI-driven decision-making in exoskeletons. Manufacturers will need to invest in compliance infrastructure and collaborate with regulators to ensure safe, effective, and widely accepted humanoid exoskeletons.
Supply Chain Dynamics and Component Sourcing
The supply chain dynamics and component sourcing for humanoid exoskeleton manufacturing in 2025 are characterized by increasing complexity, strategic partnerships, and a growing emphasis on localization and resilience. As demand for exoskeletons rises in sectors such as healthcare, industrial labor, and defense, manufacturers are navigating a landscape shaped by both technological innovation and global supply chain pressures.
Key components for humanoid exoskeletons include high-torque electric actuators, lightweight structural materials (such as advanced aluminum alloys, carbon fiber composites, and titanium), precision sensors, embedded control electronics, and high-density batteries. Sourcing these components requires close collaboration with specialized suppliers. For example, Sarcos Technology and Robotics Corporation—a leading U.S.-based exoskeleton manufacturer—has established partnerships with suppliers of industrial-grade actuators and sensor systems to ensure reliability and scalability in its Guardian XO and Guardian XT platforms. Similarly, CYBERDYNE Inc. in Japan sources proprietary actuator and sensor technologies for its HAL exoskeletons, often working with domestic suppliers to maintain quality and supply chain security.
The global semiconductor shortage that began in 2021 continues to influence sourcing strategies in 2025, particularly for microcontrollers and power management ICs critical to exoskeleton control systems. Manufacturers are increasingly diversifying their supplier base and investing in inventory buffers to mitigate risks. In addition, there is a trend toward vertical integration, with companies like Ottobock—a major player in medical exoskeletons—expanding in-house capabilities for key components such as custom joint modules and embedded electronics.
Geopolitical factors and trade tensions have prompted a shift toward regionalized supply chains, especially in North America, Europe, and East Asia. This is evident in the efforts of SuitX (now part of Ottobock) to source more components domestically within the United States, and in European initiatives to foster local suppliers for critical exoskeleton parts. The European Union’s focus on strategic autonomy in advanced manufacturing is expected to further bolster local sourcing and reduce dependency on overseas suppliers.
Looking ahead, the outlook for exoskeleton supply chains in the next few years includes increased adoption of digital supply chain management tools, greater use of additive manufacturing for rapid prototyping and small-batch production, and a continued push for sustainable sourcing of materials. As the market matures, manufacturers are expected to prioritize supplier relationships that offer both technological innovation and supply chain resilience, ensuring the steady growth of the humanoid exoskeleton sector.
Investment Trends and Funding Landscape
The investment landscape for humanoid exoskeleton manufacturing in 2025 is characterized by a surge in both private and public funding, reflecting the sector’s growing strategic importance in healthcare, industrial, and defense applications. Venture capital and corporate investments have accelerated, driven by the promise of exoskeletons to address labor shortages, enhance worker safety, and improve mobility for individuals with disabilities.
Leading manufacturers such as SuitX (now part of Ottobock), Ottobock, and CYBERDYNE Inc. have attracted significant funding rounds in recent years, enabling them to scale production and expand R&D. Ottobock, a global leader in prosthetics and exoskeletons, continues to invest heavily in its exoskeleton division, leveraging its established medical device infrastructure to accelerate commercialization. CYBERDYNE Inc., known for its HAL (Hybrid Assistive Limb) exoskeleton, has benefited from both government grants and private investment, particularly in Japan’s aging society context.
In the United States, Ekso Bionics has secured funding from both the Department of Defense and private investors to develop exoskeletons for rehabilitation and industrial use. The company’s partnerships with major healthcare providers and industrial firms have further bolstered investor confidence. Similarly, ReWalk Robotics has continued to attract capital for its FDA-cleared exoskeletons, focusing on expanding its product line and entering new markets.
Government support remains a critical driver, with agencies in the EU, US, and Asia funding research and pilot programs to integrate exoskeletons into public health and workplace safety initiatives. For example, the European Union’s Horizon programs and Japan’s METI have provided grants to accelerate the adoption of assistive robotics, including exoskeletons.
Looking ahead, the funding landscape is expected to remain robust through the late 2020s, with increased interest from strategic investors in the automotive, logistics, and construction sectors. The entry of large industrial players, such as Panasonic and Daiwa House Industry, signals a maturing market and a shift toward mass production and broader deployment. As regulatory pathways become clearer and real-world efficacy is demonstrated, further capital inflows are anticipated, supporting both established manufacturers and innovative startups in the humanoid exoskeleton space.
Challenges: Scalability, Cost, and User Adoption
The manufacturing of humanoid exoskeletons in 2025 faces significant challenges related to scalability, cost, and user adoption, despite notable technological progress. One of the primary hurdles is the transition from small-batch, custom-built prototypes to mass production. Most current manufacturers, such as SuitX (now part of Ottobock), CYBERDYNE Inc., and Sarcos Technology and Robotics Corporation, have focused on specialized industrial, medical, or military applications, where units are produced in limited quantities. Scaling up production to meet broader commercial or consumer demand requires significant investment in automated assembly lines, supply chain optimization, and quality control systems—areas where the industry is still maturing.
Cost remains a major barrier to widespread adoption. As of 2025, the price of advanced humanoid exoskeletons often exceeds $50,000 per unit, with some medical and industrial models reaching upwards of $100,000. This high cost is driven by the use of advanced lightweight materials, custom actuators, and sophisticated control electronics. Companies like ReWalk Robotics and Ekso Bionics have made strides in reducing costs through modular designs and off-the-shelf components, but affordability for individual consumers or smaller businesses remains out of reach. Efforts to lower costs are ongoing, with manufacturers exploring additive manufacturing, standardized parts, and partnerships with automotive and aerospace suppliers to leverage economies of scale.
User adoption is another critical challenge. For exoskeletons to be widely accepted, they must be comfortable, intuitive to use, and seamlessly integrate into users’ daily routines or workflows. Feedback from pilot programs in logistics and healthcare has highlighted issues such as device weight, limited battery life, and the need for extensive user training. Companies like Honda Motor Co., Ltd. and Panasonic Corporation are investing in ergonomic research and user-centered design to address these concerns, but achieving the necessary balance between functionality and usability is an ongoing process.
Looking ahead, the outlook for overcoming these challenges is cautiously optimistic. Industry leaders are forming collaborations with research institutions and government agencies to accelerate innovation and standardization. As manufacturing techniques mature and component costs decrease, the sector is expected to move closer to scalable, cost-effective production. However, widespread user adoption will depend not only on technical improvements but also on regulatory approvals, insurance reimbursement policies, and demonstrable long-term benefits for end users.
Future Outlook: Strategic Opportunities and Disruptive Trends
The future of humanoid exoskeleton manufacturing in 2025 and the following years is poised for significant transformation, driven by rapid technological advancements, strategic investments, and evolving market demands. The sector is witnessing a convergence of robotics, advanced materials, and artificial intelligence, which is enabling the development of more capable, lightweight, and user-friendly exoskeletons for both industrial and medical applications.
Key industry players are scaling up their manufacturing capabilities to meet anticipated demand. SuitX, a California-based company now part of Ottobock, continues to refine modular exoskeletons for industrial use, focusing on ergonomic support and injury reduction. Meanwhile, CYBERDYNE Inc. in Japan is expanding its production of the HAL (Hybrid Assistive Limb) exoskeleton, targeting both rehabilitation and labor support markets. Sarcos Technology and Robotics Corporation is advancing the commercialization of its Guardian XO full-body exoskeleton, with pilot deployments in logistics and manufacturing sectors.
Manufacturing trends are shifting toward greater automation and the use of advanced composites and lightweight alloys, which are essential for improving exoskeleton efficiency and comfort. Companies are investing in scalable production lines and digital twins to optimize assembly and quality control. For example, Lockheed Martin is leveraging its expertise in aerospace manufacturing to develop exoskeletons for military and industrial applications, integrating sensor fusion and real-time data analytics.
Strategic opportunities are emerging in the integration of exoskeletons with Industry 4.0 ecosystems. Manufacturers are exploring partnerships with wearable sensor companies and cloud computing providers to enable predictive maintenance, remote monitoring, and data-driven performance optimization. The adoption of open architecture platforms is expected to accelerate, allowing for easier customization and interoperability with other robotic systems.
Disruptive trends include the miniaturization of actuators and power sources, which will enable more agile and energy-efficient exoskeletons. The use of artificial intelligence for adaptive control and personalized assistance is set to become a standard feature, as seen in ongoing R&D by Panasonic Corporation and Honda Motor Co., Ltd. These innovations are likely to lower costs and expand accessibility, particularly in healthcare and eldercare sectors.
Looking ahead, the exoskeleton manufacturing landscape will be shaped by regulatory harmonization, increased standardization, and the entry of new players from adjacent industries. As the technology matures, manufacturers that can deliver scalable, affordable, and intelligent exoskeleton solutions will be well-positioned to capture emerging opportunities across global markets.
Sources & References
- CYBERDYNE Inc.
- SUITX
- Sarcos Technology and Robotics Corporation
- Lockheed Martin
- Ottobock
- ReWalk Robotics
- SUITX
- Panasonic
- CYBERDYNE Inc.
- ReWalk Robotics
- Ekso Bionics Holdings, Inc.
- European Medicines Agency
- Hocoma
- International Organization for Standardization
- IEEE