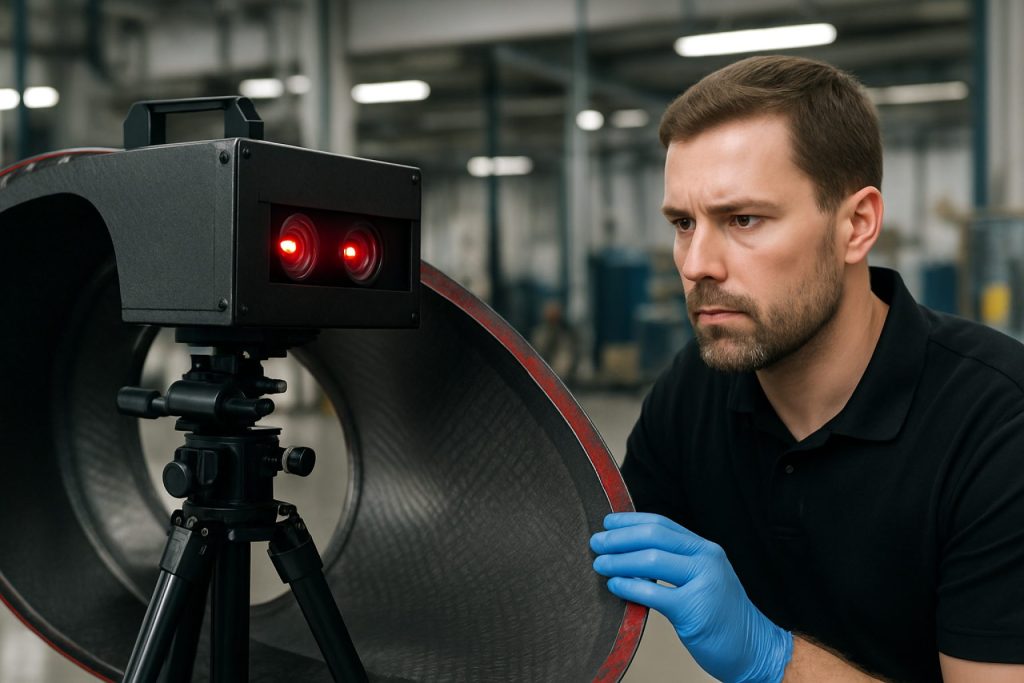
Shearography-Based Composite Material Inspection in 2025: Unveiling the Next Wave of Non-Destructive Testing Innovation. Explore Market Growth, Technology Shifts, and Strategic Opportunities.
- Executive Summary: Shearography in Composite Inspection (2025–2030)
- Market Size, Growth Rate, and Forecasts (2025–2030)
- Key Drivers: Aerospace, Automotive, and Wind Energy Adoption
- Technological Advancements in Shearography Systems
- Competitive Landscape: Leading Companies and Innovators
- Regulatory Standards and Industry Guidelines
- Integration with Automation and Digitalization Trends
- Challenges: Technical, Economic, and Adoption Barriers
- Case Studies: Real-World Applications and ROI
- Future Outlook: Emerging Opportunities and Strategic Recommendations
- Sources & References
Executive Summary: Shearography in Composite Inspection (2025–2030)
Shearography-based inspection is rapidly consolidating its position as a critical non-destructive testing (NDT) method for composite materials, particularly in high-value sectors such as aerospace, automotive, wind energy, and advanced manufacturing. As of 2025, the technology is recognized for its ability to detect subsurface defects—such as delaminations, disbonds, and core damage—in complex composite structures with high sensitivity and speed. The method’s full-field, non-contact nature makes it especially suitable for inspecting large or intricately shaped components, where traditional ultrasonic or radiographic techniques may be less effective or more time-consuming.
Key industry players, including Dantec Dynamics, Laser Technology Inc., and isi-sys, are actively advancing shearography systems, integrating high-resolution digital cameras, advanced phase-shifting algorithms, and robust automation features. These enhancements are enabling faster inspection cycles and improved defect characterization, which are crucial for the growing adoption of composites in safety-critical applications. For example, Dantec Dynamics has developed turnkey shearography solutions tailored for both laboratory and in-field inspections, supporting major aerospace OEMs and MRO providers.
Recent years have seen a marked increase in the deployment of shearography for in-service inspection of aircraft components, wind turbine blades, and automotive parts. The technology’s ability to provide rapid, reliable assessments is driving its integration into quality assurance protocols and predictive maintenance programs. Notably, organizations such as Airbus and Boeing have referenced the use of shearography in their composite inspection guidelines, underscoring its growing acceptance in global supply chains.
Looking ahead to 2030, the outlook for shearography-based composite inspection is strongly positive. Ongoing R&D is focused on further automating the inspection process, leveraging artificial intelligence for defect recognition, and enhancing portability for field applications. The increasing complexity and volume of composite structures—driven by trends in lightweighting and sustainability—are expected to fuel demand for advanced NDT solutions. Industry collaborations and standardization efforts, led by bodies such as the American Society for Nondestructive Testing, are likely to accelerate the adoption of shearography, ensuring consistent quality and safety across sectors.
In summary, shearography is set to play an increasingly vital role in composite material inspection through 2025 and beyond, offering a unique combination of speed, sensitivity, and adaptability that aligns with the evolving needs of modern manufacturing and maintenance environments.
Market Size, Growth Rate, and Forecasts (2025–2030)
The global market for shearography-based composite material inspection is poised for robust growth from 2025 through 2030, driven by increasing adoption in aerospace, automotive, wind energy, and advanced manufacturing sectors. Shearography, a laser-based non-destructive testing (NDT) technique, is valued for its ability to rapidly detect subsurface defects such as delaminations, disbonds, and impact damage in composite structures—capabilities that are critical as composite usage expands in high-performance applications.
In 2025, the market is estimated to be valued in the low hundreds of millions USD, with North America and Europe representing the largest regional shares due to their concentration of aerospace and wind turbine manufacturing. The Asia-Pacific region is expected to see the fastest growth, propelled by expanding aerospace and automotive industries, particularly in China and India. The compound annual growth rate (CAGR) for shearography-based inspection systems is projected to be in the range of 7–10% through 2030, outpacing some other NDT modalities due to the increasing complexity and volume of composite components in critical infrastructure.
Key industry players such as LAEVO, a specialist in advanced NDT solutions, and Laser Technology Inc., which focuses on laser shearography systems, are expanding their product portfolios to address the growing demand for automated, high-throughput inspection solutions. Vishay Precision Group (through its Micro-Measurements division) and HELLING GmbH are also notable for their contributions to shearography equipment and services, supporting both OEMs and maintenance providers.
Recent years have seen a shift toward integration of shearography with robotics and digital data management, enabling in-line inspection and real-time defect analytics. This trend is expected to accelerate, with manufacturers such as HELLING GmbH and LAEVO investing in R&D for portable and automated systems tailored to large-scale composite structures, such as aircraft fuselages and wind turbine blades.
Looking ahead, regulatory requirements for composite inspection in aerospace (e.g., by EASA and FAA) and the push for higher reliability in renewable energy infrastructure are anticipated to further drive market expansion. The outlook for 2025–2030 is characterized by increasing standardization, broader adoption in emerging markets, and continued innovation in system automation and defect characterization, positioning shearography as a key technology in the evolving landscape of composite material inspection.
Key Drivers: Aerospace, Automotive, and Wind Energy Adoption
Shearography-based composite material inspection is experiencing accelerated adoption across key industrial sectors, notably aerospace, automotive, and wind energy, as these industries intensify their reliance on advanced composites for lightweighting and performance. The year 2025 marks a pivotal period, with several drivers converging to expand the use of shearography as a preferred non-destructive testing (NDT) method.
In aerospace, the demand for rapid, reliable, and non-contact inspection of large composite structures is paramount. Aircraft manufacturers and maintenance organizations are increasingly integrating shearography to detect subsurface defects such as delaminations, disbonds, and impact damage in components like fuselage panels, control surfaces, and engine nacelles. The technology’s ability to inspect large areas quickly, with minimal surface preparation, aligns with the sector’s push for higher throughput and reduced downtime. Leading aerospace suppliers, including Airbus and Boeing, have publicly documented the use of shearography in their composite inspection protocols, particularly for in-service maintenance and quality assurance of new builds.
The automotive industry, facing stringent emissions regulations and consumer demand for fuel efficiency, is expanding its use of composite materials in structural and body components. Shearography’s speed and sensitivity to manufacturing defects—such as voids, wrinkles, and incomplete bonding—make it attractive for high-volume production environments. Tier-1 suppliers and OEMs are piloting automated shearography systems on production lines, aiming to ensure quality without impeding cycle times. Companies like BMW Group and Tesla, Inc. are known to invest in advanced NDT solutions, including shearography, to support their composite-intensive vehicle platforms.
Wind energy is another sector where shearography is gaining traction, driven by the need to inspect increasingly large and complex composite blades. Blade manufacturers and service providers are adopting portable and robotic shearography systems to detect flaws such as core disbonds, adhesive failures, and impact damage, both during manufacturing and in-field maintenance. The scalability and non-contact nature of shearography are critical as blade lengths surpass 100 meters. Major wind turbine manufacturers, such as Siemens Gamesa Renewable Energy and GE Vernova, are actively exploring or deploying shearography-based inspection to enhance reliability and reduce lifecycle costs.
Looking ahead, the outlook for shearography-based composite inspection is robust. Ongoing advancements in digital imaging, automation, and data analytics are expected to further improve defect detection sensitivity and integration with smart manufacturing systems. As regulatory standards tighten and the economic imperative for defect-free composites grows, adoption across these sectors is set to accelerate through 2025 and beyond.
Technological Advancements in Shearography Systems
Shearography, a laser-based non-destructive testing (NDT) technique, has seen significant technological advancements in recent years, particularly for the inspection of composite materials in aerospace, automotive, and wind energy sectors. As of 2025, the focus is on enhancing system automation, portability, and data analytics to meet the growing demand for rapid, reliable, and cost-effective composite inspection.
One of the most notable trends is the integration of advanced digital cameras and high-power diode lasers, which have improved the sensitivity and resolution of shearography systems. Companies such as Laser NDT and Stresstech are at the forefront, offering turnkey shearography solutions capable of detecting minute subsurface defects like delaminations, disbonds, and core crush in complex composite structures. These systems now often feature real-time defect visualization and automated defect recognition, reducing the need for operator expertise and minimizing human error.
Portability and field-deployability have also advanced, with manufacturers introducing compact, ruggedized shearography units suitable for in-situ inspections. For example, Laser NDT has developed mobile platforms that can be deployed directly on aircraft or wind turbine blades, enabling rapid inspection without the need for disassembly. This is particularly valuable for maintenance, repair, and overhaul (MRO) operations, where downtime must be minimized.
Another key development is the integration of artificial intelligence (AI) and machine learning algorithms for automated defect classification and reporting. These capabilities are being embedded into software suites provided by leading vendors, allowing for faster data interpretation and more consistent results. The use of cloud-based data management is also emerging, enabling remote expert review and long-term trend analysis across fleets or asset portfolios.
Industry standards and qualification processes are evolving in parallel. Organizations such as NASA and Airbus are actively involved in validating and standardizing shearography techniques for composite inspection, ensuring that new systems meet stringent aerospace quality requirements. Collaborative projects between equipment manufacturers and end-users are expected to accelerate the adoption of next-generation shearography systems in both production and service environments.
Looking ahead, the outlook for shearography-based composite inspection is robust. Continued investment in automation, AI-driven analytics, and system miniaturization is anticipated to further expand the applicability of shearography, particularly as composite materials become more prevalent in critical infrastructure. The next few years are likely to see broader industry acceptance, with shearography playing a central role in ensuring the integrity and safety of advanced composite structures.
Competitive Landscape: Leading Companies and Innovators
The competitive landscape for shearography-based composite material inspection is characterized by a select group of specialized technology providers, instrumentation manufacturers, and integrators, each advancing the field through proprietary hardware, software, and application expertise. As of 2025, the market is shaped by increasing demand from aerospace, automotive, wind energy, and defense sectors, all of which require rapid, non-contact, and reliable inspection of advanced composite structures.
A leading player is Laser NDT, a Germany-based company recognized for its turnkey shearography systems. Their solutions are widely adopted in aerospace MRO (maintenance, repair, and overhaul) and production lines, offering high-throughput inspection of large composite panels and bonded structures. Laser NDT continues to innovate with portable and automated robotic shearography platforms, addressing the need for in-situ and inline inspection.
Another key innovator is Stress Photonics, a division of Stresstech, which has developed advanced digital shearography systems for both laboratory and field use. Their technology is notable for its integration of high-resolution digital cameras and proprietary phase-stepping algorithms, enabling detection of subsurface defects such as delaminations, disbonds, and impact damage in composite materials. Stress Photonics has established partnerships with major aerospace OEMs and is expanding into wind turbine blade inspection.
In France, Dantec Dynamics stands out for its modular shearography solutions, which are used in both R&D and industrial quality assurance. Their systems are designed for flexibility, supporting both manual and automated inspection workflows. Dantec Dynamics is also active in standardization efforts, collaborating with industry bodies to define best practices for composite inspection.
Emerging players include isi-sys, which focuses on digital image correlation and shearography for composite testing, and HELLING GmbH, which supplies shearography equipment tailored for the wind energy sector. These companies are investing in user-friendly interfaces, AI-driven defect recognition, and integration with factory automation systems.
Looking ahead, the competitive landscape is expected to intensify as demand for automated, high-speed, and data-rich inspection grows. Companies are likely to focus on enhancing system portability, real-time analytics, and compatibility with Industry 4.0 environments. Strategic collaborations between equipment manufacturers, composite producers, and end-users will be crucial for advancing adoption and addressing evolving industry requirements.
Regulatory Standards and Industry Guidelines
Shearography-based inspection of composite materials is increasingly governed by evolving regulatory standards and industry guidelines, reflecting the technology’s growing adoption in critical sectors such as aerospace, automotive, and wind energy. As of 2025, regulatory bodies and industry consortia are actively updating and harmonizing requirements to ensure the reliability and repeatability of shearography as a nondestructive testing (NDT) method.
The Performance Review Institute (Nadcap) continues to play a central role in accrediting suppliers for advanced NDT methods, including shearography, particularly for aerospace applications. Nadcap’s checklists and audit criteria are being updated to reflect the latest best practices, with a focus on operator qualification, equipment calibration, and data traceability. In parallel, the SAE International is reviewing and revising standards such as AMS 2630, which covers shearography for aerospace composite structures, to address new material systems and inspection scenarios.
The ASTM International Committee E07 on Nondestructive Testing is also active in this space, with standards like ASTM E2581—Standard Practice for Shearography Testing of Polymer Matrix Composites—undergoing periodic review. Recent revisions emphasize digital image processing, environmental controls, and documentation requirements, aligning with the increasing automation and digitalization of inspection processes. These updates are informed by input from major aerospace manufacturers and NDT equipment suppliers, such as Vishay Precision Group (through its Micro-Measurements division) and Dantec Dynamics, both of which supply shearography systems and actively participate in standards development.
In the wind energy sector, organizations like the DNV are incorporating shearography into recommended practices for blade inspection, recognizing its ability to detect subsurface defects in large composite structures. DNV’s guidelines are expected to be updated in the next few years to reflect field experience and advances in portable shearography equipment.
Looking ahead, regulatory convergence is anticipated as international bodies such as the International Organization for Standardization (ISO) work to harmonize NDT standards across regions. The next few years will likely see increased emphasis on digital record-keeping, remote inspection capabilities, and integration with other NDT modalities. As composite materials become more prevalent in safety-critical applications, adherence to robust, up-to-date standards for shearography-based inspection will remain a top priority for manufacturers and regulators alike.
Integration with Automation and Digitalization Trends
The integration of shearography-based composite material inspection with automation and digitalization is accelerating rapidly as industries seek higher throughput, reliability, and traceability in non-destructive testing (NDT). In 2025, this trend is particularly evident in aerospace, automotive, and wind energy sectors, where composite materials are critical for lightweight, high-performance structures.
Shearography, a laser-based interferometric technique, is valued for its ability to detect subsurface defects such as delaminations, disbonds, and impact damage in composites. Recent years have seen a shift from manual, stand-alone shearography systems to fully automated, robot-integrated solutions. Companies like Vishay Precision Group (through its Micro-Measurements and Stress Photonics brands) and Laser Technology Inc. are at the forefront, offering systems that can be mounted on robotic arms or gantries for in-line inspection during manufacturing or maintenance cycles.
Digitalization is further enhancing the value of shearography by enabling real-time data acquisition, automated defect recognition, and seamless integration with manufacturing execution systems (MES). For example, isi-sys GmbH provides shearography solutions with advanced software for automated defect analysis and digital reporting, supporting Industry 4.0 initiatives. These systems can generate digital twins of inspected components, allowing for predictive maintenance and lifecycle management.
In 2025, the adoption of artificial intelligence (AI) and machine learning (ML) algorithms is expected to become standard in shearography-based inspection. These technologies enable automated interpretation of complex fringe patterns, reducing the need for expert operators and minimizing false positives. Companies such as isi-sys GmbH and Vishay Precision Group are investing in AI-driven software modules that can be updated remotely, ensuring continuous improvement and adaptation to new composite materials and defect types.
Looking ahead, the outlook for shearography-based inspection is closely tied to broader digital transformation trends. The push for smart factories and digital thread connectivity will likely drive further integration of shearography systems with cloud-based analytics, remote monitoring, and automated process control. As regulatory requirements for traceability and quality assurance tighten, especially in aerospace and energy, the demand for fully digital, automated shearography solutions is set to grow. Industry leaders are expected to focus on interoperability, cybersecurity, and user-friendly interfaces to facilitate widespread adoption across global supply chains.
Challenges: Technical, Economic, and Adoption Barriers
Shearography-based inspection of composite materials, while increasingly recognized for its non-contact, full-field, and rapid defect detection capabilities, faces several technical, economic, and adoption barriers as of 2025. These challenges are shaping the pace and scope of its integration into industries such as aerospace, automotive, wind energy, and advanced manufacturing.
Technical Challenges
- Surface Preparation and Environmental Sensitivity: Shearography is highly sensitive to surface conditions and environmental factors such as vibration, temperature fluctuations, and ambient light. In field applications, especially on large or complex structures, maintaining stable conditions for accurate measurements remains a significant hurdle. Companies like Dantec Dynamics and Laser NDT are actively developing more robust systems with improved environmental compensation, but real-world deployment still requires careful setup and sometimes additional shielding or stabilization.
- Complexity of Data Interpretation: The full-field data generated by shearography systems can be complex to interpret, particularly for multi-layered or thick composite structures. Advanced algorithms and AI-driven analysis are being introduced, but the need for highly trained operators persists. This limits widespread adoption in sectors lacking specialized NDT personnel.
- Detection Limits: While shearography excels at identifying delaminations, disbonds, and impact damage, its sensitivity to certain defect types—such as very small cracks or deep subsurface flaws—can be lower compared to other NDT methods. Ongoing R&D by manufacturers like Stresstech and Shearing Technologies is focused on enhancing detection depth and resolution.
Economic Barriers
- High Initial Investment: The cost of shearography equipment, including lasers, cameras, and vibration isolation systems, remains high relative to more established NDT methods. This is a deterrent for small and medium-sized enterprises (SMEs), despite the potential for long-term savings through faster inspections and reduced downtime.
- Integration with Production Lines: Retrofitting existing manufacturing or maintenance lines with shearography systems can require significant capital and process redesign. Companies such as Dantec Dynamics are working on more compact and automated solutions, but cost and complexity remain concerns for many end-users.
Adoption Barriers and Outlook
- Standardization and Certification: The lack of universally accepted standards for shearography-based inspection in composites, especially in highly regulated sectors like aerospace, slows adoption. Industry bodies and leading manufacturers are collaborating to develop guidelines and certification pathways, but widespread acceptance is still in progress.
- Training and Workforce Development: The specialized nature of shearography demands targeted training programs. Efforts by equipment suppliers and industry groups to provide certification and education are ongoing, but workforce readiness remains a bottleneck.
Looking ahead, the next few years are expected to see incremental improvements in system robustness, automation, and cost-effectiveness, driven by continued innovation from key players such as Dantec Dynamics, Laser NDT, and Stresstech. However, overcoming the outlined barriers will be essential for shearography to achieve broader industrial adoption and realize its full potential in composite material inspection.
Case Studies: Real-World Applications and ROI
Shearography-based inspection has rapidly advanced from laboratory research to real-world deployment, particularly in industries where composite materials are critical for safety and performance. In 2025, aerospace, wind energy, and automotive sectors are at the forefront of adopting shearography for non-destructive testing (NDT) of composite structures, driven by the need for reliable defect detection and cost-effective maintenance.
Aerospace manufacturers and maintenance organizations have integrated shearography into their inspection protocols for aircraft composite components, such as fuselage panels, control surfaces, and radomes. Airbus has publicly demonstrated the use of shearography for rapid detection of disbonds, delaminations, and impact damage in carbon fiber reinforced polymer (CFRP) structures. The technology’s ability to inspect large areas quickly—often in minutes—has reduced aircraft downtime and improved maintenance planning. Similarly, Boeing has incorporated shearography into its composite repair and quality assurance processes, citing its sensitivity to subsurface defects and minimal surface preparation requirements.
In the wind energy sector, shearography is increasingly used for in-situ inspection of wind turbine blades, which are predominantly made from glass and carbon fiber composites. Companies such as Siemens Gamesa Renewable Energy have adopted portable shearography systems to detect manufacturing defects and in-service damage, including debonding and core disintegration. Field data from 2024–2025 indicate that shearography can reduce inspection times by up to 60% compared to traditional ultrasonic methods, while also enabling earlier detection of critical flaws that could lead to blade failure.
Automotive manufacturers, particularly those producing electric vehicles and high-performance sports cars, are piloting shearography for quality control of composite body panels and structural components. BMW Group has reported successful trials of shearography for detecting voids and delaminations in carbon fiber parts, contributing to improved product reliability and reduced warranty claims.
Return on investment (ROI) analyses from these sectors highlight several key benefits: reduced inspection and maintenance costs, minimized production bottlenecks, and enhanced safety margins. The non-contact, full-field nature of shearography is especially valued for inspecting complex geometries and large surfaces. Looking ahead, ongoing improvements in automation, portability, and data analytics are expected to further increase adoption rates and ROI, with industry leaders such as Laser Technology Inc. and isi-sys GmbH developing next-generation shearography systems tailored for high-throughput industrial environments.
Future Outlook: Emerging Opportunities and Strategic Recommendations
Shearography-based inspection of composite materials is poised for significant growth and technological advancement in 2025 and the following years, driven by the increasing adoption of composites in aerospace, automotive, wind energy, and civil infrastructure. As industries demand faster, more reliable, and non-contact inspection methods, shearography is emerging as a preferred solution due to its ability to detect subsurface defects such as delaminations, disbonds, and impact damages with high sensitivity and speed.
Key industry players are investing in the development of portable, automated, and AI-enhanced shearography systems. For example, Laser NDT and Stresstech are actively expanding their product lines to include advanced digital shearography systems tailored for both in-line and field inspections. These systems are increasingly integrated with robotics and automated scanning platforms, enabling rapid inspection of large and complex composite structures, such as aircraft fuselages and wind turbine blades.
The aerospace sector remains a primary driver, with major manufacturers and maintenance organizations seeking to comply with stringent safety standards while reducing inspection times. The adoption of shearography is expected to accelerate as companies like Airbus and Boeing continue to expand their use of composite materials in next-generation aircraft. Additionally, the wind energy sector is embracing shearography for the inspection of turbine blades, as evidenced by collaborations between inspection technology providers and leading wind turbine manufacturers.
Emerging opportunities are also present in the automotive industry, where lightweight composite components are increasingly used to improve fuel efficiency and reduce emissions. Shearography’s ability to provide rapid, full-field inspection aligns with the industry’s need for high-throughput quality control. Furthermore, the integration of machine learning algorithms for defect recognition and data analysis is expected to enhance the reliability and repeatability of inspections, reducing the reliance on operator expertise.
Strategic recommendations for stakeholders include investing in R&D for miniaturized and user-friendly shearography devices, fostering partnerships with composite manufacturers, and developing training programs to address the skills gap in advanced NDT techniques. Standardization efforts, led by organizations such as the American Society for Nondestructive Testing, will be crucial in ensuring widespread adoption and interoperability of shearography systems across industries.
In summary, the outlook for shearography-based composite material inspection is robust, with technological innovation, cross-sector adoption, and standardization efforts set to drive market expansion and operational efficiency through 2025 and beyond.
Sources & References
- isi-sys
- Airbus
- Boeing
- American Society for Nondestructive Testing
- Vishay Precision Group
- Siemens Gamesa Renewable Energy
- GE Vernova
- Laser NDT
- Stresstech
- NASA
- HELLING GmbH
- ASTM International
- DNV
- International Organization for Standardization (ISO)