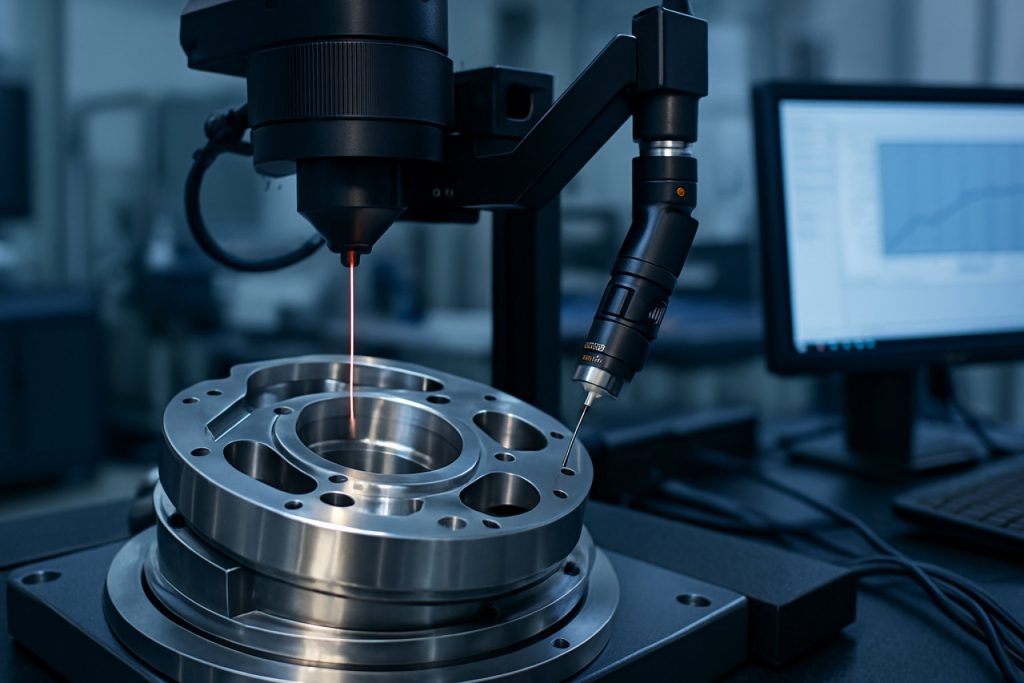
Optomechanical Metrology Systems in 2025: Driving Unprecedented Precision and Growth. Explore How Next-Gen Technologies Are Shaping the Future of Industrial Measurement.
- Executive Summary & Key Findings
- Market Size, Growth Rate, and 2025–2029 Forecast (12% CAGR)
- Core Technologies: Innovations in Optomechanical Metrology
- Major Industry Players and Strategic Initiatives
- Emerging Applications Across Manufacturing, Aerospace, and Semiconductors
- Regional Analysis: North America, Europe, Asia-Pacific, and Rest of World
- Competitive Landscape and Recent M&A Activity
- Challenges: Technical Barriers, Standardization, and Supply Chain Risks
- Future Outlook: AI Integration, Automation, and Digital Twins
- References (e.g., zeiss.com, hexagon.com, asme.org, mitutoyo.com, olympus-lifescience.com)
- Sources & References
Executive Summary & Key Findings
Optomechanical metrology systems, which integrate optical and mechanical measurement techniques, are experiencing rapid advancements and growing adoption across high-precision industries in 2025. These systems are critical for applications requiring nanometer-scale accuracy, such as semiconductor manufacturing, aerospace engineering, and advanced materials research. The current landscape is shaped by the convergence of laser interferometry, high-speed photonics, and precision motion control, enabling unprecedented measurement capabilities.
Key industry players, including Carl Zeiss AG, KEYENCE CORPORATION, and Renishaw plc, are at the forefront of innovation, offering systems that deliver sub-micron and even nanometer-level resolution. Carl Zeiss AG continues to expand its portfolio of coordinate measuring machines (CMMs) and optical profilers, integrating AI-driven data analysis for real-time process control. KEYENCE CORPORATION is notable for its compact, user-friendly optical measurement systems, which are increasingly adopted in electronics and automotive manufacturing for inline quality assurance. Renishaw plc specializes in laser interferometry and encoders, supporting the precision requirements of semiconductor lithography and advanced robotics.
Recent events in 2024 and early 2025 highlight a surge in demand for optomechanical metrology driven by the miniaturization of electronic components and the transition to advanced semiconductor nodes (3 nm and below). The global push for smart manufacturing and Industry 4.0 integration is accelerating the deployment of automated, networked metrology solutions. Companies are investing in systems that offer not only high accuracy but also high throughput and seamless integration with digital manufacturing platforms.
Data from industry sources indicate that the adoption of non-contact, optical-based metrology is outpacing traditional tactile methods, particularly in sectors where surface integrity and speed are paramount. For example, the automotive and aerospace industries are leveraging 3D optical scanners and laser trackers for rapid prototyping and in-line inspection, reducing cycle times and improving product quality.
Looking ahead to the next few years, the outlook for optomechanical metrology systems is robust. Continued advancements in photonic components, such as ultrafast lasers and high-sensitivity detectors, are expected to further enhance measurement speed and precision. The integration of AI and machine learning for automated defect detection and predictive maintenance is poised to become standard. As manufacturing tolerances tighten and the demand for digital twins grows, optomechanical metrology will remain a cornerstone technology for quality assurance and process optimization across advanced industries.
Market Size, Growth Rate, and 2025–2029 Forecast (12% CAGR)
The global market for optomechanical metrology systems is experiencing robust growth, driven by increasing demand for high-precision measurement solutions in semiconductor manufacturing, aerospace, automotive, and advanced materials industries. As of 2025, the market is estimated to be valued at approximately USD 2.1 billion, with a projected compound annual growth rate (CAGR) of around 12% through 2029. This expansion is underpinned by rapid technological advancements, miniaturization of components, and the integration of automation and artificial intelligence into metrology workflows.
Key industry players such as Carl Zeiss AG, KEYENCE CORPORATION, and Hexagon AB are at the forefront of innovation, offering a range of optomechanical metrology solutions including coordinate measuring machines (CMMs), laser interferometers, and optical profilers. Carl Zeiss AG continues to expand its portfolio with advanced optical and multisensor CMMs, targeting semiconductor and electronics applications where nanometer-level accuracy is critical. KEYENCE CORPORATION is recognized for its compact, high-speed optical measurement systems, which are increasingly adopted in automated production lines for real-time quality control. Hexagon AB leverages its expertise in metrology software and hardware integration, supporting digital transformation initiatives across manufacturing sectors.
The Asia-Pacific region, led by China, Japan, and South Korea, is expected to maintain the highest growth rate, fueled by substantial investments in semiconductor fabrication and electronics manufacturing. North America and Europe remain significant markets, with ongoing upgrades in aerospace and automotive production facilities to meet stringent quality and traceability standards. The adoption of Industry 4.0 practices, including the deployment of smart sensors and cloud-based data analytics, is further accelerating the uptake of optomechanical metrology systems globally.
Looking ahead to 2029, the market is forecast to surpass USD 3.3 billion, with growth opportunities emerging from the integration of machine learning algorithms for predictive maintenance and process optimization. The transition toward fully automated, in-line metrology solutions is expected to reduce inspection times and enhance throughput, particularly in high-volume manufacturing environments. Strategic collaborations between equipment manufacturers and end-users are anticipated to drive the development of customized solutions tailored to specific industry requirements.
Overall, the outlook for optomechanical metrology systems remains highly positive, with sustained double-digit growth anticipated as industries prioritize precision, efficiency, and digitalization in their quality assurance processes.
Core Technologies: Innovations in Optomechanical Metrology
Optomechanical metrology systems, which integrate optical measurement techniques with precision mechanical components, are at the forefront of high-accuracy dimensional and surface characterization in advanced manufacturing, semiconductor, and scientific research sectors. As of 2025, the field is witnessing rapid innovation driven by the need for higher throughput, sub-nanometer resolution, and robust automation in both laboratory and industrial environments.
A key trend is the increasing adoption of interferometric and laser-based systems for non-contact, high-speed measurements. Companies such as Zygo Corporation and Keyence Corporation are leading the market with advanced white-light interferometers, laser displacement sensors, and 3D optical profilers. These systems are now capable of real-time surface topography mapping and in-line process control, essential for semiconductor wafer inspection and precision optics manufacturing.
Another significant development is the integration of optomechanical metrology with automated robotics and artificial intelligence (AI). Renishaw plc, a major player in metrology, has expanded its portfolio to include automated coordinate measuring machines (CMMs) equipped with optical sensors, enabling faster and more flexible quality assurance workflows. Similarly, Hexagon AB is advancing the field with multi-sensor platforms that combine tactile and optical measurement heads, supported by AI-driven data analysis for predictive maintenance and process optimization.
In the realm of ultra-precision applications, such as gravitational wave detection and quantum technology, optomechanical systems are being pushed to new limits. Thorlabs, Inc. and Newport Corporation supply high-stability optomechanical mounts, vibration isolation platforms, and custom optical assemblies that are critical for minimizing environmental noise and achieving picometer-level measurement stability.
Looking ahead, the next few years are expected to see further miniaturization and integration of optomechanical metrology systems, with a focus on embedded sensors for smart manufacturing and the Industrial Internet of Things (IIoT). The convergence of photonics, precision mechanics, and digital connectivity is anticipated to enable real-time, in-situ monitoring of complex manufacturing processes, supporting the transition to fully autonomous factories. As these technologies mature, industry leaders such as Zygo Corporation, Renishaw plc, and Hexagon AB are poised to play pivotal roles in shaping the future landscape of optomechanical metrology.
Major Industry Players and Strategic Initiatives
The optomechanical metrology systems sector in 2025 is characterized by a dynamic landscape of established leaders and innovative entrants, each advancing precision measurement technologies for applications spanning semiconductor manufacturing, aerospace, automotive, and scientific research. The industry is witnessing intensified strategic initiatives, including product launches, partnerships, and capacity expansions, as demand for higher accuracy and automation in metrology accelerates.
Among the most prominent players, Carl Zeiss AG continues to set benchmarks in optical and coordinate metrology. In 2024 and early 2025, Zeiss has expanded its portfolio with advanced 3D optical scanners and non-contact measurement systems, targeting both industrial and research markets. The company’s focus on integrating AI-driven data analysis and automation into its metrology solutions is evident in its latest product lines, which are designed to support smart manufacturing and digital twin initiatives.
KEYENCE CORPORATION, renowned for its high-speed, high-precision measurement instruments, has maintained its momentum by introducing compact, user-friendly optomechanical systems suitable for in-line quality control. In 2025, Keyence is emphasizing plug-and-play solutions that reduce setup time and operator dependency, aligning with the broader industry trend toward Industry 4.0 compatibility.
Hexagon AB remains a global force in metrology, leveraging its expertise in both hardware and software. The company’s recent strategic initiatives include the integration of advanced sensor technologies and cloud-based data platforms, enabling real-time analytics and remote monitoring. Hexagon’s collaborations with semiconductor and electronics manufacturers are particularly notable, as these sectors demand ever-tighter tolerances and process control.
In the United States, Nikon Corporation and Bruker Corporation are key contributors. Nikon’s metrology division has focused on high-throughput, non-contact measurement systems for semiconductor wafer inspection, while Bruker continues to innovate in surface metrology and nanomechanical testing, supporting both industrial and academic research.
Strategic partnerships and acquisitions are shaping the competitive landscape. For example, several leading players have announced collaborations with automation and robotics firms to develop fully integrated, autonomous metrology cells. Additionally, investments in R&D for quantum-enhanced and photonic-based measurement technologies are expected to yield commercial products within the next few years, further pushing the boundaries of precision and speed.
Looking ahead, the industry outlook for optomechanical metrology systems is robust, with sustained growth anticipated as manufacturers across sectors prioritize quality assurance, traceability, and digital transformation. The convergence of optics, mechanics, and digital technologies will continue to drive innovation, with major industry players at the forefront of this evolution.
Emerging Applications Across Manufacturing, Aerospace, and Semiconductors
Optomechanical metrology systems, which integrate optical measurement techniques with precision mechanical components, are rapidly advancing as critical enablers across manufacturing, aerospace, and semiconductor industries. In 2025, these systems are increasingly deployed for their ability to deliver non-contact, high-resolution, and real-time measurements, supporting the stringent quality and process control demands of next-generation technologies.
In manufacturing, optomechanical metrology is central to the evolution of smart factories and Industry 4.0 initiatives. Automated in-line inspection systems, leveraging laser interferometry, structured light, and confocal microscopy, are now standard in high-precision assembly lines. Companies such as Carl Zeiss AG and Keyence Corporation are at the forefront, offering systems capable of sub-micron accuracy for dimensional and surface characterization of components ranging from automotive parts to medical devices. These solutions are increasingly integrated with robotics and AI-driven analytics, enabling adaptive manufacturing and predictive maintenance.
In aerospace, the demand for lightweight, high-performance materials and complex geometries has driven adoption of advanced optomechanical metrology. Aircraft manufacturers and suppliers utilize laser trackers, photogrammetry, and white light scanning to ensure the integrity of large-scale structures and composite assemblies. Hexagon AB and FARO Technologies, Inc. are notable for their portable coordinate measuring machines (CMMs) and 3D laser scanning solutions, which are now essential for both production and maintenance, repair, and overhaul (MRO) operations. The ability to rapidly verify tolerances and detect defects in situ is reducing downtime and improving safety margins.
The semiconductor sector, facing ever-shrinking device geometries and complex multilayer architectures, is a major driver of optomechanical metrology innovation. Wafer inspection, overlay metrology, and critical dimension (CD) measurement increasingly rely on advanced optical techniques such as scatterometry and ellipsometry, often combined with precision motion stages and environmental controls. KLA Corporation and ASML Holding NV are global leaders, providing metrology platforms that support process nodes below 5 nm and enable yield optimization in high-volume manufacturing.
Looking ahead, the next few years will see further convergence of optomechanical metrology with AI, edge computing, and digital twin technologies. This will enable real-time, closed-loop process control and deeper integration into cyber-physical production systems. As manufacturing, aerospace, and semiconductor industries push toward higher precision, automation, and sustainability, optomechanical metrology systems are poised to become even more indispensable.
Regional Analysis: North America, Europe, Asia-Pacific, and Rest of World
The global landscape for optomechanical metrology systems in 2025 is characterized by robust activity across North America, Europe, Asia-Pacific, and the Rest of World, each region exhibiting distinct drivers and adoption patterns. These systems, which integrate optical and mechanical components for high-precision measurement, are increasingly vital in semiconductor manufacturing, aerospace, automotive, and advanced research sectors.
North America remains a leader in optomechanical metrology innovation, propelled by the presence of major semiconductor and aerospace manufacturers. The United States, in particular, is home to key players such as Zygo Corporation (a division of AMETEK), which specializes in optical metrology instruments, and Keysight Technologies, known for precision measurement solutions. The region benefits from strong R&D investment and collaborations between industry and research institutions, supporting the development of next-generation systems for nanometrology and surface characterization. The ongoing expansion of advanced manufacturing and the push for domestic semiconductor production, spurred by government initiatives, are expected to further drive demand through 2025 and beyond.
Europe is distinguished by its focus on high-precision engineering and quality standards, with Germany, the UK, and France at the forefront. Companies such as Carl Zeiss AG and Renishaw plc are prominent, offering a range of metrology solutions for industrial and scientific applications. The European Union’s emphasis on Industry 4.0 and digital manufacturing is accelerating the integration of optomechanical metrology into smart factories. Additionally, the region’s strong automotive and aerospace sectors are key adopters, leveraging these systems for quality assurance and process optimization.
Asia-Pacific is experiencing the fastest growth, driven by the rapid expansion of electronics, semiconductor, and display manufacturing in countries such as China, Japan, South Korea, and Taiwan. Leading regional suppliers include Keyence Corporation and Olympus Corporation, both of which provide advanced optical measurement and inspection systems. Government support for high-tech manufacturing and the localization of semiconductor supply chains are major factors fueling adoption. The region’s competitive manufacturing environment is also pushing for greater automation and precision, further boosting demand for optomechanical metrology.
Rest of World markets, including Latin America and the Middle East, are gradually increasing their adoption of optomechanical metrology systems, primarily in response to the globalization of manufacturing and the need to meet international quality standards. While these regions currently represent a smaller share of the market, investments in industrial infrastructure and technology transfer are expected to create new opportunities over the next few years.
Overall, the outlook for optomechanical metrology systems is positive across all regions, with technological advancements, industry digitization, and the proliferation of precision manufacturing serving as key growth catalysts through 2025 and beyond.
Competitive Landscape and Recent M&A Activity
The competitive landscape for optomechanical metrology systems in 2025 is characterized by a blend of established precision engineering firms, innovative startups, and strategic mergers and acquisitions (M&A) that are reshaping the sector. The market is driven by increasing demand for high-precision measurement in semiconductor manufacturing, photonics, aerospace, and advanced materials, with a focus on nanometer-scale accuracy and automation.
Key industry players include Carl Zeiss AG, KEYENCE CORPORATION, Renishaw plc, and Hexagon AB. Carl Zeiss AG continues to lead in high-end optical metrology, leveraging its expertise in microscopy and industrial quality solutions. KEYENCE CORPORATION is recognized for its rapid innovation cycles and user-friendly, automated measurement systems, while Renishaw plc specializes in precision encoders and laser interferometry for coordinate measuring machines (CMMs) and additive manufacturing. Hexagon AB maintains a strong presence through its broad portfolio of metrology hardware and software, serving automotive, aerospace, and electronics sectors.
Recent years have seen notable M&A activity as companies seek to expand their technological capabilities and global reach. In 2023, Hexagon AB acquired several niche metrology firms to enhance its automation and data analytics offerings, consolidating its position in smart manufacturing. Renishaw plc has also pursued strategic partnerships to integrate advanced optical sensors into its product lines, responding to the growing demand for inline, real-time quality control in semiconductor and electronics fabrication.
Startups and smaller innovators are also attracting attention, particularly those developing compact, AI-driven optomechanical systems for in-situ and non-contact measurement. Larger incumbents are increasingly targeting these firms for acquisition or collaboration, aiming to accelerate the adoption of machine learning and cloud connectivity in metrology workflows.
Looking ahead to the next few years, the sector is expected to see continued consolidation, with major players seeking to fill technology gaps in areas such as quantum metrology, ultrafast laser measurement, and integrated photonics. The competitive landscape will likely be shaped by the race to deliver higher throughput, sub-nanometer accuracy, and seamless integration with digital manufacturing platforms. As the boundaries between optical, mechanical, and computational metrology blur, companies with strong R&D pipelines and agile M&A strategies are poised to lead the market.
Challenges: Technical Barriers, Standardization, and Supply Chain Risks
Optomechanical metrology systems, which integrate optical and mechanical components for high-precision measurement, are increasingly vital in semiconductor manufacturing, aerospace, and advanced materials research. However, as the sector advances into 2025, several technical, standardization, and supply chain challenges persist, potentially impacting the pace of innovation and deployment.
Technical Barriers: The drive for higher resolution and accuracy in optomechanical metrology is pushing the limits of current technology. Achieving sub-nanometer precision requires not only advanced optical components but also ultra-stable mechanical assemblies and sophisticated environmental controls. For example, leading manufacturers such as Carl Zeiss AG and Keyence Corporation are investing heavily in vibration isolation, thermal management, and adaptive optics to minimize measurement errors. However, integrating these technologies into compact, user-friendly systems remains a significant hurdle. Additionally, the increasing complexity of materials and device architectures—such as 3D semiconductor structures—demands new metrology approaches that can probe buried features without destructive sample preparation.
Standardization Issues: The lack of universally accepted standards for optomechanical metrology, especially in emerging applications, complicates interoperability and data comparability. Industry bodies like SEMI and ISO are working to develop and update standards for optical measurement techniques, calibration procedures, and data formats. However, the rapid evolution of both hardware and software in this field often outpaces the standardization process. This can lead to fragmentation, where proprietary solutions from major suppliers such as Olympus Corporation and Nikon Corporation may not be fully compatible with each other or with third-party analysis tools, increasing integration costs for end users.
Supply Chain Risks: The global supply chain for optomechanical metrology systems is highly specialized and sensitive to disruptions. Critical components such as high-purity optical glass, precision actuators, and advanced sensors are sourced from a limited number of suppliers. Geopolitical tensions, export controls, and logistical bottlenecks—exacerbated by recent global events—pose risks to timely delivery and cost stability. Companies like Thorlabs, Inc. and Edmund Optics Inc. are expanding their manufacturing footprints and diversifying supplier bases to mitigate these risks, but vulnerabilities remain, particularly for custom or high-specification parts.
Looking ahead, addressing these challenges will require coordinated efforts between manufacturers, standards organizations, and end users. Advances in automation, digital twins, and AI-driven calibration may help overcome technical and standardization barriers, while greater supply chain transparency and regionalization could reduce risk exposure in the coming years.
Future Outlook: AI Integration, Automation, and Digital Twins
The future of optomechanical metrology systems is being shaped by the rapid integration of artificial intelligence (AI), advanced automation, and digital twin technologies. As of 2025, these trends are accelerating the evolution of precision measurement in manufacturing, semiconductor, and research environments. AI-driven data analysis is enabling metrology systems to process vast datasets in real time, improving both the speed and accuracy of defect detection, surface characterization, and dimensional analysis. For example, leading manufacturers such as Carl Zeiss AG and Keyence Corporation are embedding machine learning algorithms into their optical and coordinate measuring machines, allowing for adaptive measurement strategies and predictive maintenance capabilities.
Automation is another key driver, with robotic handling and closed-loop feedback systems becoming standard in high-throughput production lines. Companies like Renishaw plc are advancing automated metrology solutions that seamlessly integrate with industrial robots, reducing human intervention and minimizing measurement errors. This trend is particularly evident in the semiconductor sector, where sub-nanometer accuracy is required for next-generation device fabrication. KLA Corporation, a major supplier of process control and metrology equipment, is actively developing automated optical inspection systems that leverage AI for real-time process optimization.
Digital twin technology is poised to further transform optomechanical metrology by creating virtual replicas of physical assets and measurement environments. These digital twins enable continuous monitoring, simulation, and optimization of metrology processes, supporting predictive quality control and faster product development cycles. Hexagon AB, a global leader in metrology and manufacturing intelligence, is investing in digital twin platforms that connect metrology data with manufacturing execution systems, enabling closed-loop quality assurance and remote diagnostics.
Looking ahead to the next few years, the convergence of AI, automation, and digital twins is expected to drive significant improvements in measurement throughput, traceability, and process adaptability. Industry stakeholders anticipate that optomechanical metrology systems will become increasingly autonomous, with self-calibrating and self-optimizing capabilities. This will be critical for emerging applications such as advanced packaging, additive manufacturing, and quantum device fabrication, where measurement precision and flexibility are paramount. As these technologies mature, collaboration between metrology equipment providers, automation specialists, and AI developers will be essential to realize the full potential of intelligent, connected metrology ecosystems.
References (e.g., zeiss.com, hexagon.com, asme.org, mitutoyo.com, olympus-lifescience.com)
Sources & References
- Carl Zeiss AG
- Renishaw plc
- Hexagon AB
- Thorlabs, Inc.
- Nikon Corporation
- Bruker Corporation
- FARO Technologies, Inc.
- KLA Corporation
- ASML Holding NV
- Olympus Corporation
- ISO
- ASME (American Society of Mechanical Engineers)
- Mitutoyo
- Olympus Life Science