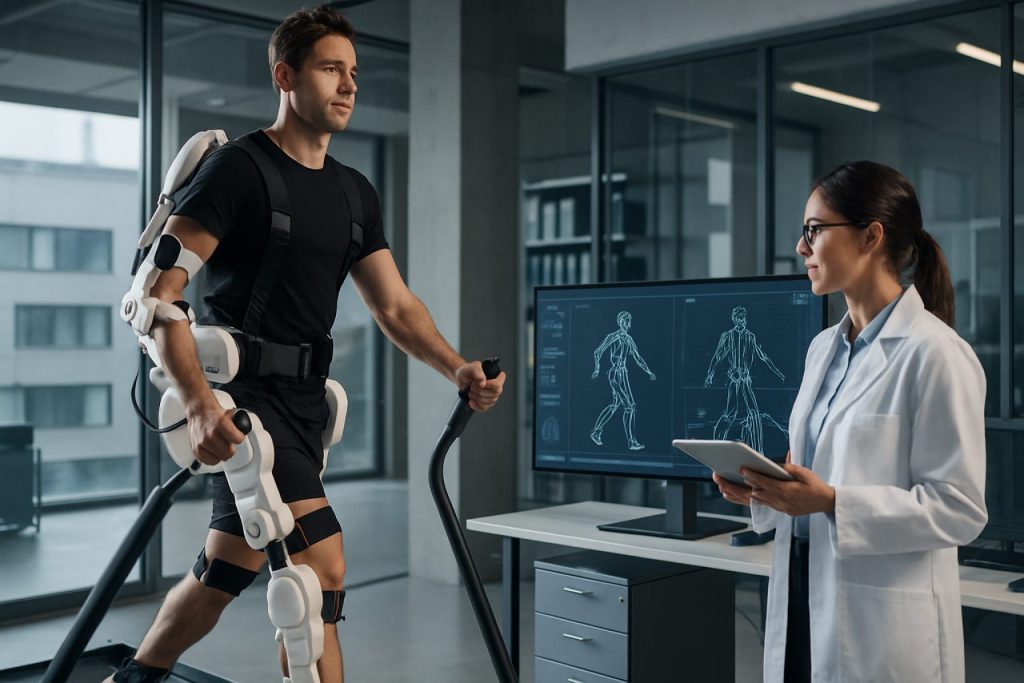
Robotic Exoskeleton Biomechanics in 2025: Unleashing the Next Wave of Human-Machine Synergy. Explore How Advanced Biomechanics Are Shaping the Future of Wearable Robotics and Transforming Industries.
- Executive Summary: Key Trends and Market Drivers in 2025
- Biomechanical Innovations: State-of-the-Art Exoskeleton Technologies
- Market Size and Growth Forecast (2025–2029): CAGR and Revenue Projections
- Industrial Applications: Enhancing Workforce Safety and Productivity
- Medical and Rehabilitation Exoskeletons: Clinical Impact and Adoption
- Military and Defense: Performance Augmentation and Tactical Advantages
- Key Players and Strategic Partnerships (e.g., eksoBionics.com, suitx.com, rewalk.com)
- Regulatory Landscape and Standards (e.g., ieee.org, asme.org)
- Challenges: Biomechanical Integration, User Acceptance, and Cost Barriers
- Future Outlook: Emerging Technologies and Long-Term Market Opportunities
- Sources & References
Executive Summary: Key Trends and Market Drivers in 2025
The field of robotic exoskeleton biomechanics is poised for significant advancement in 2025, driven by rapid technological innovation, increased clinical adoption, and expanding industrial applications. Key trends shaping the sector include the integration of advanced sensor technologies, artificial intelligence (AI)-driven control systems, and the development of lightweight, ergonomic materials. These innovations are enabling exoskeletons to deliver more natural, adaptive, and efficient biomechanical support for users across medical, industrial, and military domains.
A major driver in 2025 is the growing demand for rehabilitation and mobility assistance devices, particularly as global populations age and the prevalence of mobility-impairing conditions rises. Medical exoskeletons are increasingly being adopted in hospitals and rehabilitation centers, with companies such as Ekso Bionics and ReWalk Robotics leading the way in FDA-cleared devices for gait training and spinal cord injury recovery. These systems leverage real-time biomechanical feedback and adaptive algorithms to personalize therapy, improving patient outcomes and reducing recovery times.
In the industrial sector, exoskeletons are being deployed to enhance worker safety and productivity, particularly in logistics, manufacturing, and construction. Companies like SuitX (now part of Ottobock) and Samsung Robotics are developing powered and passive exoskeletons that reduce musculoskeletal strain and fatigue, addressing a key driver: the need to mitigate workplace injuries and associated costs. These systems are increasingly incorporating biomechanical analytics to optimize support based on task-specific movement patterns.
Technological convergence is another defining trend. The integration of AI, machine learning, and cloud connectivity is enabling exoskeletons to adapt in real time to user intent and environmental changes. For example, CYBERDYNE is advancing its Hybrid Assistive Limb (HAL) exoskeleton with neural interface technologies, allowing for more intuitive and responsive biomechanical assistance. Meanwhile, material science breakthroughs are yielding lighter, more flexible exoskeleton frames, improving user comfort and wearability.
Looking ahead, the outlook for robotic exoskeleton biomechanics is robust. Regulatory pathways are becoming clearer, and reimbursement models are evolving, supporting broader adoption. As exoskeletons become more affordable and versatile, their role in augmenting human biomechanics—whether for rehabilitation, injury prevention, or enhanced mobility—is set to expand rapidly through 2025 and beyond.
Biomechanical Innovations: State-of-the-Art Exoskeleton Technologies
The field of robotic exoskeleton biomechanics is experiencing rapid advancements as of 2025, driven by a convergence of sensor technology, actuation systems, and human-machine interface research. Modern exoskeletons are increasingly designed to closely mimic and augment natural human movement, with a focus on both rehabilitation and industrial applications.
A key biomechanical innovation is the integration of adaptive control algorithms that respond in real time to user intent and gait dynamics. For example, exoskeletons from Ekso Bionics employ sensor arrays and machine learning to adjust joint torque and support based on the wearer’s movement patterns, enabling more natural ambulation and reducing compensatory muscle activity. Similarly, ReWalk Robotics has advanced its powered exoskeletons with multi-sensor feedback loops, allowing for smoother transitions between sitting, standing, and walking, which is critical for users with spinal cord injuries.
Biomechanical research is also focusing on the reduction of metabolic cost and joint loading. Exosuits developed by SuitX and Sarcos Technology and Robotics Corporation utilize lightweight materials and soft actuators to provide targeted assistance at the hip, knee, and ankle. These systems are shown to decrease muscle fatigue and energy expenditure during repetitive tasks, as validated in recent pilot deployments in manufacturing and logistics environments.
Another significant trend is the modularity and customization of exoskeletons to accommodate diverse body types and movement requirements. Ottobock and Hocoma are leading efforts to develop exoskeletons with adjustable joint axes and adaptable support profiles, enhancing both comfort and biomechanical alignment. This is particularly important for rehabilitation, where precise joint kinematics are essential for effective therapy and long-term musculoskeletal health.
Looking ahead, the next few years are expected to see further integration of biomechanical data analytics, with exoskeletons capturing detailed movement and force data to inform personalized therapy and workplace ergonomics. The collaboration between exoskeleton manufacturers and clinical research institutions is anticipated to yield robust datasets, accelerating the refinement of assistive algorithms and hardware. As regulatory pathways become clearer and costs decrease, the adoption of biomechanically advanced exoskeletons is poised to expand across healthcare, industry, and even consumer wellness sectors.
Market Size and Growth Forecast (2025–2029): CAGR and Revenue Projections
The global market for robotic exoskeletons, driven by advances in biomechanics, is poised for significant expansion between 2025 and 2029. This growth is underpinned by increasing demand in medical rehabilitation, industrial ergonomics, and defense applications. As of 2025, the market is characterized by a surge in both research and commercialization, with leading manufacturers scaling up production and expanding their portfolios to address diverse user needs.
Key industry players such as ReWalk Robotics, Ekso Bionics, and CYBERDYNE Inc. are at the forefront, leveraging biomechanical innovations to enhance device adaptability, comfort, and safety. These companies are investing in next-generation exoskeletons that integrate advanced sensors, AI-driven gait analysis, and lightweight materials, aiming to improve user outcomes and broaden adoption across sectors.
Revenue projections for the robotic exoskeleton market indicate robust growth. Industry estimates suggest that the global market size, which surpassed $1 billion in 2024, is expected to reach between $2.5 and $3 billion by 2029, reflecting a compound annual growth rate (CAGR) in the range of 18% to 22%. This acceleration is attributed to several factors:
- Wider reimbursement coverage for exoskeleton-assisted rehabilitation in North America and Europe, as evidenced by ReWalk Robotics’s recent insurance partnerships.
- Increased adoption in industrial settings, with companies like Ottobock and SuitX (now part of Ottobock) supplying exoskeletons to logistics and manufacturing firms to reduce workplace injuries and enhance productivity.
- Ongoing government and defense contracts, such as those awarded to Lockheed Martin for military exoskeleton development, which are expected to drive further R&D and market penetration.
Looking ahead, the market outlook remains optimistic. The next few years will likely see increased collaboration between exoskeleton manufacturers and healthcare providers, as well as the integration of biomechanical data analytics to personalize therapy and optimize device performance. As regulatory pathways become clearer and costs decrease, the accessibility of robotic exoskeletons is set to improve, further fueling market growth through 2029.
Industrial Applications: Enhancing Workforce Safety and Productivity
Robotic exoskeletons are rapidly transforming industrial environments by augmenting human biomechanics to enhance workforce safety and productivity. As of 2025, the integration of exoskeletons in sectors such as manufacturing, logistics, and construction is accelerating, driven by the need to reduce workplace injuries and improve operational efficiency. These wearable devices are engineered to support and amplify the user’s natural movements, particularly during repetitive or strenuous tasks, by redistributing loads and minimizing musculoskeletal strain.
Biomechanically, industrial exoskeletons are designed to align with the human body’s joints and muscle groups, providing targeted assistance to the back, shoulders, and lower limbs. For example, passive exoskeletons, which use mechanical structures without motors, are widely adopted for tasks involving frequent lifting or overhead work. Active exoskeletons, equipped with powered actuators and sensors, offer dynamic support and real-time adaptation to user movements, further reducing fatigue and injury risk.
Leading manufacturers are advancing the field with robust, ergonomically optimized solutions. Ottobock has developed the Paexo series, including the Paexo Shoulder and Paexo Back, which are deployed in automotive assembly lines to alleviate strain during overhead and lifting tasks. Similarly, SuitX (now part of Ottobock) offers modular exoskeletons tailored for industrial use, focusing on reducing lower back injuries and improving worker endurance. Sarcos Technology and Robotics Corporation is commercializing the Guardian XO, a full-body, battery-powered exoskeleton capable of enabling users to lift up to 200 pounds repeatedly with minimal exertion, targeting heavy industry and logistics.
Recent field deployments and pilot studies have demonstrated tangible benefits. Automotive manufacturers report up to a 50% reduction in worker-reported discomfort and a significant decrease in lost workdays due to musculoskeletal disorders when exoskeletons are integrated into assembly processes. Additionally, logistics companies are piloting exoskeletons to support warehouse staff during peak demand periods, with early data indicating improved throughput and reduced injury rates.
Looking ahead, the next few years are expected to bring further advancements in exoskeleton biomechanics, including lighter materials, improved sensor integration, and AI-driven adaptive control systems. These innovations will enable more intuitive user interfaces and broader adoption across diverse industrial settings. As regulatory bodies and industry standards evolve, exoskeletons are poised to become a cornerstone of workplace safety and productivity strategies, fundamentally reshaping the relationship between human workers and their physical environments.
Medical and Rehabilitation Exoskeletons: Clinical Impact and Adoption
Robotic exoskeleton biomechanics is a rapidly advancing field, particularly in the context of medical and rehabilitation applications. As of 2025, the focus is on optimizing the interaction between human users and exoskeleton devices to maximize clinical outcomes, safety, and user comfort. The latest generation of medical exoskeletons integrates sophisticated biomechanical modeling, real-time sensor feedback, and adaptive control algorithms to support and enhance human movement, especially for individuals with mobility impairments due to spinal cord injury, stroke, or neurodegenerative diseases.
Key industry leaders such as Ekso Bionics, ReWalk Robotics, and CYBERDYNE Inc. have developed exoskeletons that are now widely used in clinical and rehabilitation settings. These devices typically employ powered actuators at the hip and knee joints, with some models also supporting the ankle, to facilitate overground walking. The biomechanical design is informed by extensive gait analysis and user feedback, ensuring that the exoskeletons can adapt to individual patient needs and varying levels of impairment.
Recent clinical studies and real-world deployments have demonstrated significant improvements in gait symmetry, walking speed, and endurance among users. For example, exoskeleton-assisted rehabilitation has been shown to promote neuroplasticity and functional recovery in stroke survivors, with measurable gains in walking ability and independence. The integration of advanced sensors—such as inertial measurement units (IMUs), force sensors, and electromyography (EMG)—enables real-time monitoring of user intent and biomechanical parameters, allowing the exoskeleton to dynamically adjust assistance levels and movement patterns.
In 2025, the trend is toward lighter, more ergonomic designs that reduce metabolic cost and improve user compliance. Companies are leveraging new materials and compact actuators to minimize device weight without compromising support. For instance, Ekso Bionics has introduced modular exoskeletons that can be tailored to different body types and rehabilitation goals, while CYBERDYNE Inc. continues to refine its HAL (Hybrid Assistive Limb) system with enhanced biofeedback and AI-driven control.
Looking ahead, the next few years are expected to bring further advances in exoskeleton biomechanics, including the integration of machine learning for personalized gait adaptation, improved battery life for extended use, and seamless connectivity with digital health platforms. Regulatory approvals and growing clinical evidence are likely to accelerate adoption in hospitals and outpatient clinics, making robotic exoskeletons an increasingly standard component of neurorehabilitation protocols worldwide.
Military and Defense: Performance Augmentation and Tactical Advantages
Robotic exoskeletons are rapidly transforming military and defense operations by augmenting human biomechanics, enhancing soldier performance, and providing tactical advantages. As of 2025, several defense agencies and technology companies are advancing the integration of powered exoskeletons into field operations, focusing on improving load-bearing capacity, endurance, and injury prevention.
A primary biomechanical goal is to reduce musculoskeletal strain during load carriage. Modern exoskeletons, such as the Lockheed Martin ONYX suit, employ powered knee actuators and adaptive control algorithms to support the lower limbs, enabling soldiers to carry up to 40 kg with significantly less metabolic cost. Field trials have demonstrated up to a 15% reduction in energy expenditure during loaded walking, directly translating to increased operational range and reduced fatigue.
Another notable system is the Sarcos Technology and Robotics Corporation Guardian XO, a full-body, battery-powered exoskeleton designed for heavy lifting and logistics. The Guardian XO amplifies the wearer’s strength by a factor of 20, allowing a single operator to lift and manipulate objects weighing up to 90 kg repeatedly without strain. The system’s biomechanics are engineered to synchronize with natural human movement, minimizing resistance and maximizing agility—critical for dynamic combat environments.
In Europe, Ottobock is collaborating with defense partners to adapt its industrial exoskeleton platforms for military use, focusing on shoulder and back support to mitigate overuse injuries during repetitive tasks such as ammunition handling and equipment transport. These systems leverage lightweight materials and ergonomic designs to ensure comfort and mobility during extended missions.
Biomechanical research is also addressing the integration of exoskeletons with soldier-worn sensors and command systems. Real-time feedback on joint loads, posture, and fatigue is being incorporated to optimize assistance levels and prevent overexertion. The U.S. Army’s Soldier Center is actively evaluating these technologies for squad-level deployment, with pilot programs expected to expand through 2026.
Looking ahead, the next few years will see further miniaturization of actuators, improved battery life, and enhanced human-machine interfaces. These advances will enable exoskeletons to become standard issue for specialized units, offering a decisive edge in mobility, survivability, and mission effectiveness. As military exoskeleton biomechanics continue to evolve, the focus will remain on seamless integration with the human body, ensuring that technology augments rather than impedes the warfighter.
Key Players and Strategic Partnerships (e.g., eksoBionics.com, suitx.com, rewalk.com)
The landscape of robotic exoskeleton biomechanics in 2025 is shaped by a dynamic interplay of established manufacturers, innovative startups, and strategic partnerships that drive both technological advancement and market adoption. Key players in this sector are leveraging collaborations to accelerate research, expand clinical applications, and address the growing demand for assistive and rehabilitative solutions.
Among the most prominent companies, Ekso Bionics continues to be a leader in the development of wearable exoskeletons for medical and industrial use. Their EksoNR device, designed for neurorehabilitation, is deployed in hundreds of rehabilitation centers worldwide, with ongoing clinical studies demonstrating improved gait and mobility outcomes for patients with spinal cord injuries and stroke. In 2024, Ekso Bionics announced new partnerships with major hospital networks in North America and Europe, aiming to integrate real-time biomechanical data analytics into rehabilitation protocols.
Another significant player, ReWalk Robotics, specializes in exoskeletons for individuals with lower limb disabilities. Their ReWalk Personal 6.0 system, FDA-cleared for home and community use, has seen expanded insurance coverage in several countries, reflecting growing clinical acceptance. In 2025, ReWalk is collaborating with research institutions to refine sensor technologies and adaptive control algorithms, enhancing the biomechanical synergy between user and device.
The industrial exoskeleton segment is also advancing rapidly, with SuitX (now part of Ottobock) focusing on reducing workplace injuries and fatigue. Their modular exoskeletons, such as the ShoulderX and BackX, are being piloted by automotive and logistics companies to support workers in repetitive or strenuous tasks. SuitX’s integration with Ottobock’s global distribution network is expected to accelerate adoption and facilitate large-scale biomechanical data collection for further product optimization.
Strategic partnerships are increasingly central to progress in exoskeleton biomechanics. For example, Ekso Bionics and ReWalk Robotics have both entered into research collaborations with leading universities and rehabilitation centers to validate biomechanical efficacy and develop next-generation control systems. These alliances are critical for translating laboratory advances into clinically and commercially viable products.
Looking ahead, the next few years are likely to see deeper integration of artificial intelligence and real-time biomechanical feedback in exoskeletons, driven by ongoing partnerships between manufacturers, healthcare providers, and industrial clients. As regulatory frameworks evolve and reimbursement pathways expand, the sector is poised for significant growth, with key players at the forefront of both technological innovation and strategic collaboration.
Regulatory Landscape and Standards (e.g., ieee.org, asme.org)
The regulatory landscape for robotic exoskeleton biomechanics is rapidly evolving as these devices transition from research prototypes to commercial products in healthcare, industrial, and military sectors. In 2025, the focus is on harmonizing safety, performance, and interoperability standards to ensure user protection and device efficacy. Key industry bodies such as the IEEE and the ASME are at the forefront of developing and updating standards that address the unique biomechanical challenges posed by exoskeletons.
The IEEE has established the IEEE 802.1 Standard for Exoskeletons, which outlines requirements for safety, control systems, and human-robot interaction. This standard is being revised in 2025 to incorporate new findings on user variability, adaptive control algorithms, and real-world biomechanical data. The standard emphasizes the need for rigorous testing protocols, including assessments of joint alignment, load distribution, and the prevention of unintended movements that could lead to injury.
Similarly, the ASME has developed guidelines for the mechanical design and testing of wearable robots, focusing on structural integrity, durability, and user comfort. In 2025, ASME is collaborating with manufacturers and clinical partners to refine these guidelines, particularly in the context of rehabilitation and assistive exoskeletons. The updated standards are expected to address the integration of soft robotics, sensor fusion, and real-time biomechanical feedback, reflecting the latest technological advancements.
On the regulatory front, agencies such as the U.S. Food and Drug Administration (FDA) and the European Medicines Agency (EMA) are increasingly involved in the approval process for medical exoskeletons. The FDA, for example, classifies powered exoskeletons as Class II medical devices, requiring premarket notification and clinical evidence of safety and effectiveness. In 2025, regulatory pathways are being streamlined to accommodate rapid innovation, with pilot programs for adaptive trial designs and post-market surveillance.
Industry consortia, including the IEEE Robotics and Automation Society and the ASME Robotics Group, are facilitating cross-sector dialogue to align standards globally. This is particularly important as exoskeletons are deployed in diverse environments, from hospitals to factories. Looking ahead, the next few years will likely see increased convergence of biomechanical standards, with a focus on data-driven validation, user-centered design, and ethical considerations in human augmentation.
Challenges: Biomechanical Integration, User Acceptance, and Cost Barriers
The field of robotic exoskeleton biomechanics is advancing rapidly, yet several critical challenges remain as the sector moves through 2025 and into the coming years. Chief among these are issues related to biomechanical integration, user acceptance, and cost barriers, each of which directly impacts the widespread adoption and effectiveness of exoskeleton technologies.
Biomechanical Integration remains a complex hurdle. Achieving seamless interaction between exoskeletons and the human body requires precise alignment with users’ anatomical joints and movement patterns. Misalignment can lead to discomfort, reduced mobility, or even injury. Companies such as Ottobock and CYBERDYNE Inc. are investing in adaptive control algorithms and modular designs to better accommodate individual biomechanics. For example, Ottobock’s exoskeletons are designed with adjustable components to fit a range of body types, while CYBERDYNE Inc.’s HAL system uses bioelectrical signals to synchronize device movement with the user’s intent. Despite these advances, real-time adaptation to dynamic human movement and variability in user physiology remain significant technical challenges.
User Acceptance is another major concern. For exoskeletons to be adopted in clinical, industrial, or personal settings, they must be comfortable, intuitive, and non-intrusive. Feedback from pilot deployments by SuitX (now part of Ottobock) and ReWalk Robotics highlights the importance of lightweight materials, ease of donning and doffing, and minimal restriction of natural movement. User training and psychological adaptation are also critical; studies indicate that initial enthusiasm can wane if devices are cumbersome or require extensive learning curves. Manufacturers are responding by refining ergonomic designs and developing more user-friendly interfaces, but achieving widespread user satisfaction remains a work in progress.
Cost Barriers continue to limit access, particularly in healthcare and rehabilitation. Advanced exoskeletons can cost tens of thousands of dollars, restricting their use to well-funded institutions or individuals with substantial financial resources. Companies like Ekso Bionics and ReWalk Robotics are exploring scalable manufacturing and leasing models to reduce upfront costs. However, insurance reimbursement remains inconsistent, and the high price of research, development, and regulatory compliance is a persistent obstacle. Industry observers expect incremental cost reductions as production volumes increase and component prices fall, but significant affordability breakthroughs are unlikely before the late 2020s.
Looking ahead, overcoming these challenges will require continued collaboration between engineers, clinicians, and end-users. Advances in sensor technology, artificial intelligence, and materials science are expected to drive improvements in biomechanical integration and user experience, while new business models may help address cost barriers. Nevertheless, the path to mainstream adoption of robotic exoskeletons will depend on sustained innovation and a clear demonstration of value for users and payers alike.
Future Outlook: Emerging Technologies and Long-Term Market Opportunities
The future of robotic exoskeleton biomechanics is poised for significant transformation as technological advancements converge with growing market demand across healthcare, industrial, and defense sectors. By 2025 and in the following years, the field is expected to witness rapid innovation in actuation systems, sensor integration, and adaptive control algorithms, all aimed at enhancing user mobility, safety, and comfort.
One of the most notable trends is the shift toward lightweight, energy-efficient exoskeletons that leverage advanced materials such as carbon fiber composites and soft robotics. Companies like SUITX (now part of Ottobock) and Ottobock are at the forefront, developing modular exoskeletons for both medical rehabilitation and industrial support. These systems increasingly incorporate real-time biomechanical feedback, using embedded sensors to monitor joint angles, muscle activity, and gait patterns, enabling more personalized and adaptive assistance.
In the medical domain, exoskeletons are evolving from rigid, pre-programmed devices to intelligent systems capable of learning from user movement and adapting to individual rehabilitation needs. ReWalk Robotics and Ekso Bionics are advancing exoskeletons that support gait training for individuals with spinal cord injuries and stroke, with ongoing clinical trials aiming to validate long-term functional improvements. The integration of AI-driven control strategies is expected to further enhance the biomechanical synergy between user and device, reducing cognitive load and improving natural movement patterns.
Industrial applications are also expanding, with exoskeletons designed to reduce musculoskeletal strain and injury risk among workers in logistics, manufacturing, and construction. Sarcos Technology and Robotics Corporation is developing full-body powered exoskeletons for heavy lifting, while Honda Motor Co., Ltd. and Panasonic Corporation are focusing on wearable assistive devices for repetitive tasks. These systems are increasingly being tested in real-world environments, with data-driven insights guiding iterative improvements in ergonomics and biomechanical support.
Looking ahead, the convergence of robotics, wearable sensors, and machine learning is expected to drive the next generation of exoskeletons. Key opportunities include the development of fully autonomous exoskeletons capable of context-aware adaptation, integration with digital health platforms for remote monitoring, and expansion into new markets such as eldercare and personal mobility. As regulatory frameworks mature and costs decrease, the adoption of biomechanically optimized exoskeletons is likely to accelerate, unlocking substantial long-term market opportunities across multiple sectors.
Sources & References
- ReWalk Robotics
- SuitX
- Ottobock
- CYBERDYNE
- Ekso Bionics
- ReWalk Robotics
- SuitX
- Sarcos Technology and Robotics Corporation
- Ottobock
- Hocoma
- CYBERDYNE Inc.
- Lockheed Martin
- Ekso Bionics
- IEEE
- ASME