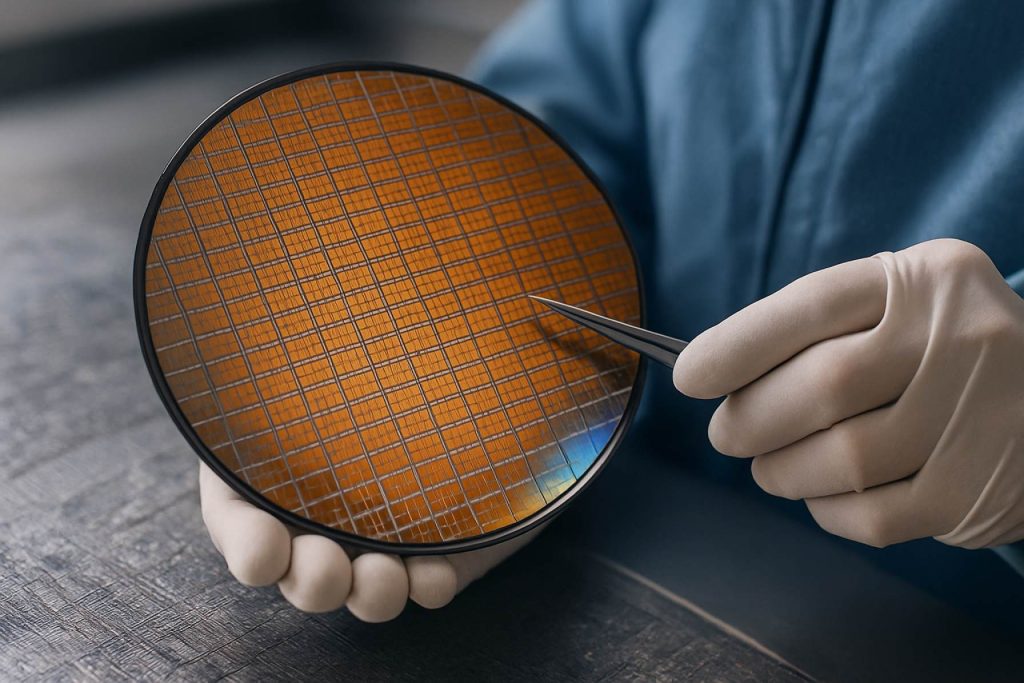
Ferroelectric Random-Access Memory (FeRAM) Circuit Fabrication in 2025: Unleashing Ultra-Fast, Low-Power Memory for the Future. Explore Market Growth, Technological Breakthroughs, and Strategic Opportunities.
- Executive Summary: FeRAM Circuit Fabrication Market Outlook 2025–2030
- Market Size, Share, and 18% CAGR Forecast Analysis
- Key Drivers: Demand for Low-Power, High-Speed Non-Volatile Memory
- Technological Innovations in FeRAM Materials and Processes
- Competitive Landscape: Leading Manufacturers and New Entrants
- Supply Chain Dynamics and Strategic Partnerships
- Application Trends: IoT, Automotive, Industrial, and Consumer Electronics
- Regulatory Standards and Industry Initiatives (e.g., IEEE, JEDEC)
- Challenges: Scalability, Cost, and Integration with CMOS
- Future Outlook: Roadmap for FeRAM Circuit Fabrication to 2030
- Sources & References
Executive Summary: FeRAM Circuit Fabrication Market Outlook 2025–2030
The global market for Ferroelectric Random-Access Memory (FeRAM) circuit fabrication is poised for significant transformation between 2025 and 2030, driven by the convergence of advanced materials research, scaling demands in semiconductor manufacturing, and the growing need for low-power, high-endurance non-volatile memory solutions. FeRAM, leveraging ferroelectric materials such as lead zirconate titanate (PZT) and hafnium oxide (HfO2), offers unique advantages over traditional flash and DRAM technologies, including faster write speeds, lower power consumption, and superior endurance.
As of 2025, the FeRAM fabrication landscape is characterized by a limited but expanding group of specialized manufacturers and foundries. Fujitsu remains a global leader, with decades of experience in FeRAM integration and a robust portfolio of discrete and embedded FeRAM products. Texas Instruments continues to supply FeRAM-based memory solutions, particularly for industrial and automotive applications, leveraging its expertise in analog and embedded processing. Infineon Technologies is also active in the sector, focusing on secure and energy-efficient memory for IoT and security applications.
Recent years have seen a shift toward the adoption of hafnium oxide-based ferroelectric materials, which are compatible with standard CMOS processes and enable further scaling. This transition is supported by collaborative efforts between memory manufacturers and foundry partners. For example, GlobalFoundries has announced initiatives to integrate ferroelectric HfO2 into its advanced process nodes, aiming to facilitate embedded FeRAM for edge AI and automotive microcontrollers. Similarly, TSMC and Samsung Electronics are reported to be exploring ferroelectric memory integration as part of their next-generation logic and memory platforms.
The outlook for 2025–2030 anticipates increased commercialization of FeRAM circuits, particularly in sectors demanding instant-on capability, data integrity, and ultra-low power operation. The automotive, industrial automation, and IoT markets are expected to be primary growth drivers, as FeRAM’s endurance and speed address the limitations of flash and EEPROM in mission-critical environments. Furthermore, the ongoing miniaturization of devices and the proliferation of edge computing are likely to accelerate the adoption of embedded FeRAM solutions.
Challenges remain, including the need for further cost reduction, process integration with advanced nodes, and scaling of ferroelectric materials. However, with continued investment from leading semiconductor companies and the maturation of hafnium oxide-based processes, FeRAM circuit fabrication is positioned for robust growth and technological advancement through 2030.
Market Size, Share, and 18% CAGR Forecast Analysis
The global market for Ferroelectric Random-Access Memory (FeRAM) circuit fabrication is poised for robust growth in 2025 and the following years, driven by increasing demand for low-power, high-speed, and non-volatile memory solutions across diverse sectors such as automotive, industrial automation, and consumer electronics. FeRAM’s unique combination of fast write/read speeds, low power consumption, and high endurance positions it as a compelling alternative to traditional non-volatile memories like EEPROM and Flash.
In 2025, the FeRAM market is projected to reach a significant valuation, with leading manufacturers such as Fujitsu, Texas Instruments, and Infineon Technologies playing pivotal roles in both circuit fabrication and end-product integration. Fujitsu has been a pioneer in FeRAM technology, offering a range of discrete and embedded FeRAM products, while Texas Instruments continues to expand its FeRAM portfolio for industrial and automotive applications. Infineon Technologies is also investing in FeRAM as part of its broader non-volatile memory strategy, targeting secure microcontrollers and IoT devices.
The market is expected to register a compound annual growth rate (CAGR) of approximately 18% from 2025 through the end of the decade. This growth is underpinned by several factors:
- Rising adoption of FeRAM in automotive electronics, where instant data retention and high endurance are critical for safety and reliability.
- Expansion of industrial IoT and smart factory applications, which require robust, low-power memory for sensor nodes and edge devices.
- Continued miniaturization and integration of FeRAM into advanced semiconductor processes, enabling new use cases in wearables and medical devices.
Geographically, Asia-Pacific remains the dominant region for FeRAM circuit fabrication, with significant manufacturing and R&D activities concentrated in Japan, South Korea, and China. Companies such as Fujitsu and Infineon Technologies maintain advanced fabrication facilities and partnerships in these regions, supporting both discrete FeRAM chips and embedded solutions.
Looking ahead, the FeRAM market is expected to benefit from ongoing process innovations, such as the integration of hafnium oxide-based ferroelectric materials, which promise further scaling and compatibility with mainstream CMOS processes. As a result, FeRAM circuit fabrication is set to capture a growing share of the non-volatile memory market, with the 18% CAGR forecast reflecting both expanding application domains and technological advancements by industry leaders.
Key Drivers: Demand for Low-Power, High-Speed Non-Volatile Memory
The fabrication of Ferroelectric Random-Access Memory (FeRAM) circuits is experiencing renewed momentum in 2025, driven by escalating demand for low-power, high-speed, and non-volatile memory solutions across diverse sectors. FeRAM’s unique combination of fast write/read speeds, low power consumption, and non-volatility positions it as a compelling alternative to traditional memory technologies such as EEPROM and Flash, particularly in applications where energy efficiency and endurance are critical.
A primary driver is the proliferation of edge computing and Internet of Things (IoT) devices, which require memory components that can operate reliably with minimal energy budgets. FeRAM’s ability to retain data without power and its rapid access times make it ideal for battery-powered sensors, medical implants, and industrial automation systems. In 2025, leading manufacturers such as ROHM Semiconductor and Infineon Technologies AG are actively expanding their FeRAM portfolios, targeting these high-growth markets with new product lines that emphasize ultra-low power operation and robust data retention.
Another significant factor is the automotive sector’s transition toward electrification and advanced driver-assistance systems (ADAS). Automotive-grade FeRAM, with its high endurance and resistance to radiation and temperature extremes, is increasingly being adopted for event data recorders, electronic control units, and secure key storage. Fujitsu, a longstanding pioneer in FeRAM technology, continues to supply FeRAM solutions tailored for automotive and industrial applications, leveraging its expertise in ferroelectric material integration and high-volume manufacturing.
On the fabrication front, advances in process integration are enabling the scaling of FeRAM cells to smaller technology nodes, improving density and reducing costs. The adoption of hafnium oxide (HfO2)-based ferroelectric materials, compatible with standard CMOS processes, is a notable trend, facilitating the integration of FeRAM with logic circuits on a single chip. Companies such as Texas Instruments and Micron Technology are investing in research and pilot production lines to commercialize next-generation FeRAM products that leverage these material innovations.
Looking ahead, the outlook for FeRAM circuit fabrication remains robust. The convergence of market demand for energy-efficient, high-speed non-volatile memory and ongoing process innovations is expected to drive further adoption in embedded systems, wearables, and secure identification devices. As more semiconductor foundries and integrated device manufacturers refine their ferroelectric material deposition and patterning techniques, FeRAM is poised to capture a larger share of the non-volatile memory market in the coming years.
Technological Innovations in FeRAM Materials and Processes
Ferroelectric Random-Access Memory (FeRAM) circuit fabrication is undergoing significant transformation in 2025, driven by advances in materials science, process integration, and device scaling. The core of FeRAM technology lies in its use of ferroelectric materials—traditionally lead zirconate titanate (PZT)—as the storage medium, enabling non-volatile data retention with low power consumption and fast write/read speeds. However, the industry is witnessing a shift toward new materials and process innovations to address scaling challenges and compatibility with advanced CMOS nodes.
One of the most notable trends is the adoption of hafnium oxide (HfO2)-based ferroelectric thin films. Unlike PZT, HfO2 is fully compatible with standard CMOS processes, allowing for easier integration into existing semiconductor manufacturing lines. Companies such as Infineon Technologies AG and Ferroelectric Memory GmbH (FMC) are at the forefront of developing and commercializing HfO2-based FeRAM and related ferroelectric field-effect transistor (FeFET) memory solutions. These materials enable further miniaturization, improved endurance, and scalability to sub-28nm nodes, which is critical for next-generation embedded memory applications.
Process innovations are also shaping FeRAM circuit fabrication. Atomic layer deposition (ALD) and advanced sputtering techniques are being refined to produce ultra-thin, uniform ferroelectric films with precise control over stoichiometry and crystallinity. This is essential for achieving reliable switching characteristics and high yield in mass production. TDK Corporation, a longstanding supplier of FeRAM products, continues to enhance its proprietary deposition and annealing processes to improve device reliability and performance, particularly for automotive and industrial applications.
Integration of FeRAM with advanced logic processes is another area of focus. Foundries such as Taiwan Semiconductor Manufacturing Company (TSMC) and Samsung Electronics are exploring the co-integration of FeRAM with logic and analog circuits, targeting applications in microcontrollers, IoT devices, and edge AI. The ability to fabricate FeRAM at lower thermal budgets and with back-end-of-line (BEOL) compatibility is expected to accelerate adoption in these sectors.
Looking ahead, the outlook for FeRAM circuit fabrication is promising. The convergence of new ferroelectric materials, advanced deposition techniques, and integration strategies is expected to yield FeRAM devices with higher density, lower power, and greater endurance. As industry leaders continue to invest in R&D and scale up production, FeRAM is poised to play a pivotal role in the memory landscape over the next several years.
Competitive Landscape: Leading Manufacturers and New Entrants
The competitive landscape for Ferroelectric Random-Access Memory (FeRAM) circuit fabrication in 2025 is characterized by a mix of established semiconductor manufacturers and a growing cohort of new entrants leveraging advances in materials science and process integration. The sector is driven by the demand for non-volatile memory solutions with low power consumption, high endurance, and fast write/read speeds, particularly for applications in industrial automation, automotive electronics, and emerging IoT devices.
Among the established leaders, Fujitsu remains a dominant force, having pioneered commercial FeRAM production since the late 1990s. The company continues to invest in scaling FeRAM technology, focusing on embedded solutions for microcontrollers and smart cards. Texas Instruments is another key player, offering a portfolio of FeRAM products targeting industrial and automotive sectors, with a focus on reliability and extended temperature operation. Both companies have demonstrated the ability to integrate FeRAM into standard CMOS processes, a critical factor for cost-effective mass production.
In recent years, Infineon Technologies has expanded its presence in the FeRAM market, leveraging its expertise in automotive and security applications. The company’s efforts are directed at integrating FeRAM into secure microcontrollers and sensor modules, addressing the growing need for instant-on memory and data integrity in safety-critical systems. Meanwhile, Micron Technology and Samsung Electronics have signaled interest in next-generation non-volatile memories, including FeRAM, as part of their broader R&D strategies, though their commercial FeRAM offerings remain limited compared to their focus on other memory types.
The competitive landscape is also witnessing the entry of new players, particularly startups and research spin-offs aiming to commercialize advances in hafnium oxide-based ferroelectric materials. These materials promise improved scalability and compatibility with advanced CMOS nodes, potentially overcoming the scaling limitations of traditional lead zirconate titanate (PZT) FeRAM. Companies such as Ferroelectric Memory GmbH (FMC) are actively developing IP and process modules for integration into foundry services, targeting both standalone and embedded FeRAM applications.
Looking ahead, the next few years are expected to see intensified competition as established manufacturers push for higher density and lower cost FeRAM solutions, while new entrants seek to disrupt the market with novel materials and process innovations. Strategic partnerships between memory IP providers, foundries, and system integrators are likely to accelerate commercialization, especially as demand for energy-efficient, instant-on memory grows in edge computing and automotive electronics.
Supply Chain Dynamics and Strategic Partnerships
The supply chain dynamics and strategic partnerships in the fabrication of Ferroelectric Random-Access Memory (FeRAM) circuits are undergoing significant transformation as the industry adapts to evolving technological demands and market pressures in 2025. FeRAM, known for its low power consumption, high endurance, and non-volatility, is increasingly sought after for applications in automotive electronics, industrial automation, and IoT devices. The fabrication of FeRAM circuits requires specialized ferroelectric materials—most notably lead zirconate titanate (PZT) and, more recently, hafnium oxide (HfO2)-based compounds—alongside advanced semiconductor manufacturing capabilities.
The global FeRAM supply chain is characterized by a limited number of major integrated device manufacturers (IDMs) and foundries with the expertise and infrastructure to produce these memory devices at scale. Fujitsu remains a pivotal player, leveraging its proprietary FeRAM technology and established manufacturing lines. In recent years, Infineon Technologies has also expanded its FeRAM portfolio, particularly targeting automotive and industrial sectors, and has invested in strengthening its supply chain resilience through vertical integration and long-term supplier agreements.
Strategic partnerships are increasingly central to FeRAM circuit fabrication. For instance, ROHM Semiconductor collaborates with foundries and material suppliers to ensure a stable supply of high-quality ferroelectric films and to optimize process integration for next-generation FeRAM products. Additionally, Taiwan Semiconductor Manufacturing Company (TSMC) has been reported to explore collaborations with memory IP holders and fabless design houses to enable FeRAM integration into advanced CMOS nodes, reflecting a broader industry trend toward heterogeneous integration and system-on-chip (SoC) solutions.
Material supply remains a critical concern, especially as demand for HfO2-based FeRAM grows due to its compatibility with standard CMOS processes. Leading chemical suppliers are forming closer alliances with device manufacturers to ensure purity, consistency, and scalability of ferroelectric materials. This is exemplified by partnerships between semiconductor manufacturers and specialty chemical companies, which are essential for maintaining quality and yield in high-volume production.
Looking ahead, the FeRAM supply chain is expected to become more robust and diversified through increased investment in R&D, the entry of new material suppliers, and the formation of cross-industry consortia. These developments are likely to accelerate the adoption of FeRAM in emerging applications, while strategic partnerships will remain vital for navigating supply chain risks and technological challenges in the coming years.
Application Trends: IoT, Automotive, Industrial, and Consumer Electronics
Ferroelectric Random-Access Memory (FeRAM) circuit fabrication is experiencing a notable surge in application-driven innovation as of 2025, with significant momentum in the Internet of Things (IoT), automotive, industrial, and consumer electronics sectors. FeRAM’s unique combination of non-volatility, low power consumption, high endurance, and fast write/read speeds positions it as a compelling alternative to traditional non-volatile memories such as EEPROM and Flash, especially where energy efficiency and reliability are paramount.
In the IoT domain, the proliferation of edge devices and sensor nodes is driving demand for memory solutions that can operate reliably under intermittent power and harsh environmental conditions. FeRAM’s ability to perform rapid data logging with minimal energy overhead is particularly advantageous for battery-powered and energy-harvesting IoT devices. Leading manufacturers such as ROHM Semiconductor and Fujitsu have expanded their FeRAM portfolios, offering ultra-low-power memory ICs tailored for wireless sensor networks, smart meters, and asset tracking applications.
Automotive electronics represent another high-growth area for FeRAM circuit fabrication. The increasing complexity of advanced driver-assistance systems (ADAS), infotainment, and vehicle electrification requires memory that can withstand wide temperature ranges and frequent data writes. FeRAM’s high endurance and data retention capabilities make it suitable for event data recorders, electronic control units (ECUs), and real-time data logging in vehicles. Infineon Technologies and Texas Instruments are actively integrating FeRAM into automotive-grade components, with a focus on functional safety and reliability.
In industrial automation, FeRAM is being adopted for programmable logic controllers (PLCs), motor drives, and industrial IoT gateways, where robust non-volatile memory is essential for system configuration, parameter storage, and event logging. The technology’s resilience to radiation and electromagnetic interference further enhances its appeal in factory and process automation environments. Murata Manufacturing continues to develop FeRAM modules optimized for industrial use, emphasizing long-term data integrity and operational stability.
Consumer electronics, including wearables, smart cards, and portable medical devices, are also benefiting from FeRAM’s low power profile and fast access times. The ongoing miniaturization of FeRAM circuit fabrication processes—such as the adoption of 28nm and below nodes—enables integration into compact, multifunctional devices. Companies like Panasonic are leveraging FeRAM for secure memory in contactless payment systems and health monitoring devices.
Looking ahead, the next few years are expected to see further scaling of FeRAM fabrication, with increased collaboration between memory suppliers and system integrators to address emerging requirements in AI-enabled edge devices, autonomous vehicles, and secure embedded systems. The continued evolution of ferroelectric materials and process integration techniques will likely expand FeRAM’s footprint across diverse application domains.
Regulatory Standards and Industry Initiatives (e.g., IEEE, JEDEC)
The regulatory landscape and industry initiatives surrounding Ferroelectric Random-Access Memory (FeRAM) circuit fabrication are evolving rapidly as the technology matures and adoption expands in sectors such as automotive, industrial, and IoT. In 2025, the focus is on harmonizing standards for device reliability, interoperability, and environmental compliance, with key organizations such as the IEEE and JEDEC playing central roles.
The IEEE continues to be instrumental in setting foundational standards for non-volatile memory technologies, including FeRAM. The IEEE Standards Association is actively engaged in updating and refining protocols that address the unique characteristics of ferroelectric materials, such as polarization fatigue, retention, and endurance. These standards are critical for ensuring that FeRAM devices meet the rigorous demands of mission-critical applications, particularly in automotive and industrial automation, where data integrity and long-term reliability are paramount.
Meanwhile, JEDEC Solid State Technology Association is advancing its work on standardizing performance metrics, testing methodologies, and packaging requirements for FeRAM. JEDEC’s committees are collaborating with leading FeRAM manufacturers to define specifications that facilitate multi-vendor compatibility and streamline qualification processes. This includes efforts to align FeRAM standards with those of other non-volatile memory types, such as MRAM and ReRAM, to support hybrid memory architectures and simplify integration into existing semiconductor supply chains.
Environmental and safety regulations are also shaping FeRAM fabrication. Compliance with global directives such as RoHS and REACH is now a baseline requirement, prompting manufacturers to optimize their processes for reduced hazardous substance use and improved recyclability. Industry initiatives, often coordinated through consortia and working groups, are focusing on lifecycle assessments and the development of eco-friendly ferroelectric materials. These efforts are supported by major FeRAM suppliers, including Fujitsu and Texas Instruments, both of which are actively involved in industry forums and standards development.
Looking ahead, the next few years are expected to see increased convergence between international standards bodies, with joint task forces addressing emerging challenges such as scaling FeRAM to advanced process nodes and ensuring cybersecurity in memory-enabled devices. The ongoing collaboration between regulatory organizations and industry leaders is anticipated to accelerate the adoption of FeRAM in safety-critical and high-reliability markets, while also fostering innovation in fabrication techniques and material science.
Challenges: Scalability, Cost, and Integration with CMOS
Ferroelectric Random-Access Memory (FeRAM) has garnered significant attention as a non-volatile memory technology, offering fast write speeds, low power consumption, and high endurance. However, as the semiconductor industry advances into 2025 and beyond, FeRAM circuit fabrication faces persistent challenges in scalability, cost, and integration with mainstream CMOS processes.
Scalability remains a central concern for FeRAM. The core of FeRAM technology is the ferroelectric capacitor, typically based on lead zirconate titanate (PZT) or, more recently, hafnium oxide (HfO2)-based materials. While HfO2 offers better compatibility with advanced CMOS nodes, achieving uniform ferroelectric properties at sub-28nm geometries is still a technical hurdle. The scaling of ferroelectric layers can lead to reduced polarization, increased variability, and reliability issues, which directly impact device performance and yield. Companies such as Texas Instruments and Fujitsu, both long-standing FeRAM producers, continue to invest in process improvements, but the industry has yet to demonstrate high-volume FeRAM production at the most advanced nodes.
Cost is another significant barrier. FeRAM fabrication requires additional process steps compared to standard CMOS, particularly for integrating ferroelectric materials and ensuring their stability during high-temperature processing. The use of PZT, for example, introduces contamination risks and necessitates dedicated equipment, increasing capital and operational expenditures. Even with the shift toward HfO2-based ferroelectrics, which are more CMOS-friendly, the need for precise deposition and annealing steps adds to manufacturing complexity. As a result, FeRAM remains more expensive per bit than established non-volatile memories like flash, limiting its adoption to niche applications where its unique attributes are essential.
Integration with CMOS is a critical challenge for FeRAM’s future. The industry’s move to advanced logic nodes and 3D integration schemes demands that memory technologies be fully compatible with front-end-of-line (FEOL) and back-end-of-line (BEOL) processes. While HfO2-based FeRAM shows promise due to its compatibility with standard CMOS process flows, issues such as interface engineering, thermal budget constraints, and process-induced defects must be addressed. Leading foundries and memory suppliers, including Infineon Technologies and TSMC, are actively researching integration schemes, but commercial-scale solutions are still in development.
Looking ahead, the outlook for FeRAM circuit fabrication will depend on continued material innovation, process optimization, and collaboration between memory suppliers and foundries. If these challenges can be overcome, FeRAM could see broader adoption in embedded applications, IoT, and automotive electronics, where its speed and endurance offer clear advantages.
Future Outlook: Roadmap for FeRAM Circuit Fabrication to 2030
The future outlook for Ferroelectric Random-Access Memory (FeRAM) circuit fabrication through 2030 is shaped by ongoing advances in materials science, process integration, and scaling strategies. As of 2025, FeRAM is positioned as a promising non-volatile memory technology, offering low power consumption, high endurance, and fast write/read speeds. The industry is witnessing a renewed focus on FeRAM, driven by the need for energy-efficient memory solutions in IoT, automotive, and edge computing applications.
Key players such as Texas Instruments and Fujitsu have maintained leadership in FeRAM development and manufacturing. Texas Instruments continues to supply discrete FeRAM products, targeting industrial and automotive sectors where data integrity and low power are critical. Fujitsu has been a pioneer in integrating FeRAM into microcontrollers and smart cards, and is expected to expand its portfolio with higher-density and more robust FeRAM solutions in the coming years.
From a fabrication perspective, the transition to advanced nodes and the integration of new ferroelectric materials are central to the roadmap. The adoption of hafnium oxide (HfO2)-based ferroelectrics is a significant trend, as these materials are compatible with standard CMOS processes and enable further scaling. Leading foundries and equipment suppliers, such as TSMC and Applied Materials, are actively exploring process modules and deposition techniques to support HfO2-based FeRAM integration, aiming for sub-28nm nodes by the late 2020s.
The next few years will likely see increased collaboration between memory manufacturers and semiconductor foundries to address challenges in ferroelectric layer uniformity, endurance, and retention. Industry consortia and standardization bodies, including JEDEC, are expected to play a role in defining reliability and performance benchmarks for FeRAM, facilitating broader adoption in mission-critical applications.
Looking toward 2030, the FeRAM fabrication roadmap anticipates the commercialization of embedded FeRAM in advanced logic and microcontroller platforms, leveraging the maturity of HfO2 processes. The convergence of FeRAM with other emerging memory technologies, such as MRAM and ReRAM, may also drive hybrid memory architectures, further expanding the application space. As the semiconductor industry intensifies its focus on sustainability and energy efficiency, FeRAM’s low-power profile positions it as a key enabler for next-generation electronics.
Sources & References
- Fujitsu
- Texas Instruments
- Infineon Technologies
- ROHM Semiconductor
- Micron Technology
- Ferroelectric Memory GmbH
- Murata Manufacturing
- IEEE
- JEDEC Solid State Technology Association