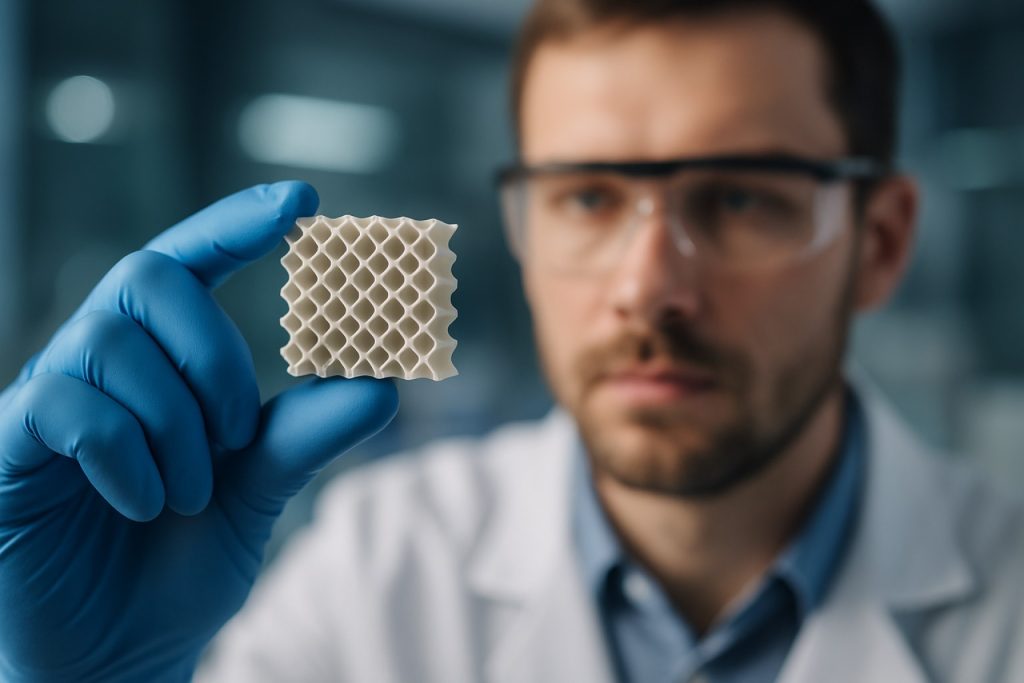
Auxetic Metamaterials Fabrication in 2025: Unleashing Next-Gen Materials for Advanced Engineering. Explore How Novel Fabrication Techniques Are Shaping the Future of Smart Structures and High-Performance Applications.
- Executive Summary: Auxetic Metamaterials Market Outlook 2025–2030
- Key Drivers and Challenges in Auxetic Metamaterials Fabrication
- Innovative Fabrication Techniques: 3D Printing, Laser Sintering, and Beyond
- Major Industry Players and Strategic Collaborations
- Current and Emerging Applications: Aerospace, Medical, Defense, and Consumer Products
- Market Size, Segmentation, and 2025–2030 Growth Forecasts (CAGR: 18–22%)
- Intellectual Property, Standards, and Regulatory Landscape
- Sustainability and Scalability in Auxetic Manufacturing
- Regional Analysis: North America, Europe, Asia-Pacific, and Rest of World
- Future Outlook: Disruptive Trends and Investment Opportunities
- Sources & References
Executive Summary: Auxetic Metamaterials Market Outlook 2025–2030
Auxetic metamaterials—engineered structures exhibiting a negative Poisson’s ratio—are gaining momentum in advanced manufacturing sectors due to their unique mechanical properties, such as enhanced energy absorption, indentation resistance, and tunable deformation. As of 2025, the fabrication landscape for auxetic metamaterials is characterized by rapid technological evolution, with a strong emphasis on scalable production, material diversity, and integration into commercial applications.
Additive manufacturing (AM) remains the dominant fabrication approach, enabling the precise realization of complex auxetic geometries at both micro- and macro-scales. Leading industrial 3D printing companies, such as Stratasys and 3D Systems, have expanded their polymer and metal printing portfolios to support the production of auxetic lattices for prototyping and functional end-use parts. These companies are collaborating with research institutions and OEMs to optimize print parameters for auxetic structures, focusing on repeatability and mechanical performance.
In parallel, advancements in digital light processing (DLP) and selective laser sintering (SLS) are enabling the fabrication of auxetic metamaterials with finer feature resolution and improved scalability. EOS, a key player in industrial SLS, is actively supporting the development of auxetic components for aerospace and medical device applications, leveraging their expertise in powder-bed fusion technologies. The push towards multi-material printing is also notable, with companies like Materialise providing software and hardware solutions for integrating auxetic designs into multi-functional assemblies.
Beyond AM, roll-to-roll processing and advanced textile manufacturing are being explored for large-area auxetic sheets and fabrics, particularly for sportswear, protective gear, and flexible electronics. Freudenberg Group, a global leader in technical textiles, is investing in the development of auxetic nonwovens and composites, aiming to commercialize these materials for impact mitigation and filtration applications.
Looking ahead to 2030, the auxetic metamaterials fabrication market is expected to benefit from continued investment in automation, in-line quality control, and sustainable material sourcing. Industry stakeholders are prioritizing the development of recyclable and bio-based auxetic materials, aligning with broader environmental goals. The convergence of digital design, advanced manufacturing, and material science is set to accelerate the adoption of auxetic metamaterials across automotive, aerospace, healthcare, and consumer sectors, with leading manufacturers and technology providers playing a pivotal role in scaling up production and driving market growth.
Key Drivers and Challenges in Auxetic Metamaterials Fabrication
The fabrication of auxetic metamaterials—materials exhibiting a negative Poisson’s ratio—has advanced rapidly in recent years, driven by demand from sectors such as aerospace, medical devices, and advanced manufacturing. As of 2025, several key drivers and challenges are shaping the landscape of auxetic metamaterials fabrication.
Key Drivers
- Advanced Additive Manufacturing: The proliferation of high-resolution 3D printing technologies, such as selective laser sintering (SLS) and digital light processing (DLP), has enabled the precise fabrication of complex auxetic geometries at both micro- and macro-scales. Companies like Stratasys and 3D Systems are actively developing printers and materials compatible with auxetic designs, facilitating rapid prototyping and small-batch production.
- Material Innovation: The development of new polymers, composites, and metal alloys with tunable mechanical properties is expanding the application range of auxetic metamaterials. For instance, Evonik Industries is investing in specialty polymers that can be processed into auxetic structures, while BASF is exploring advanced polyurethane systems for flexible auxetic foams.
- Industry Demand: Sectors such as aerospace and defense are seeking lightweight, impact-resistant materials, while the medical field is exploring auxetic scaffolds for tissue engineering and prosthetics. This cross-sectoral demand is incentivizing both startups and established manufacturers to invest in scalable fabrication methods.
Key Challenges
- Scalability and Cost: While laboratory-scale fabrication of auxetic structures is well-established, scaling up to industrial production remains challenging. The complexity of auxetic geometries often leads to higher production costs and slower throughput compared to conventional materials.
- Material Limitations: Not all materials are suitable for auxetic structuring. Achieving the desired mechanical properties without compromising durability or manufacturability is a persistent challenge. Companies like Arkema are researching new resins and composites to address these limitations.
- Quality Control and Standardization: Ensuring consistent mechanical performance across batches is critical, especially for safety-critical applications. Industry bodies such as ASTM International are beginning to develop standards for testing and certifying auxetic metamaterials, but comprehensive guidelines are still in development.
Outlook (2025 and Beyond)
Looking ahead, the auxetic metamaterials sector is expected to benefit from ongoing advances in digital manufacturing, materials science, and standardization. As companies like Stratasys, 3D Systems, and Evonik Industries continue to innovate, the transition from prototyping to mass production is likely to accelerate, unlocking new commercial applications and driving broader adoption across industries.
Innovative Fabrication Techniques: 3D Printing, Laser Sintering, and Beyond
The fabrication of auxetic metamaterials—materials exhibiting a negative Poisson’s ratio—has advanced rapidly in recent years, with 2025 marking a period of significant innovation in manufacturing techniques. The drive for scalable, precise, and cost-effective production has led to the adoption and refinement of several advanced methods, most notably 3D printing (additive manufacturing), laser sintering, and emerging hybrid processes.
3D printing remains at the forefront of auxetic metamaterial fabrication. The technology’s layer-by-layer approach enables the creation of complex, re-entrant, and chiral geometries that are otherwise difficult or impossible to achieve with traditional subtractive methods. Leading industrial 3D printer manufacturers such as Stratasys and 3D Systems have expanded their portfolios to include high-resolution polymer and metal printers capable of producing auxetic structures for prototyping and functional applications. In 2025, the focus has shifted toward multi-material printing, allowing for the integration of auxetic regions within conventional materials, thus enabling tunable mechanical properties in a single build process.
Selective Laser Sintering (SLS) and Direct Metal Laser Sintering (DMLS) have also gained traction for fabricating auxetic metamaterials, particularly in metals and high-performance polymers. Companies like EOS and SLM Solutions are recognized for their industrial-grade SLS and DMLS systems, which offer the precision and repeatability required for the intricate lattice structures characteristic of auxetic designs. These methods are increasingly used in aerospace, automotive, and biomedical sectors, where the unique deformation behavior of auxetic materials can enhance energy absorption, impact resistance, and conformability.
Beyond these established techniques, 2025 is witnessing the emergence of hybrid fabrication approaches. These combine additive manufacturing with subtractive processes (such as CNC milling) or post-processing treatments (like thermal or chemical etching) to further refine the microstructure and surface properties of auxetic metamaterials. Additionally, companies specializing in advanced materials, such as Arkema, are developing new printable polymers and composites tailored for auxetic architectures, expanding the range of functional properties achievable.
Looking ahead, the outlook for auxetic metamaterial fabrication is promising. The convergence of digital design, advanced manufacturing, and material science is expected to yield scalable production methods suitable for mass customization. Industry leaders are investing in automation and quality control systems to ensure consistency and reliability, paving the way for broader adoption in sectors ranging from protective equipment to flexible electronics and medical devices.
Major Industry Players and Strategic Collaborations
The landscape of auxetic metamaterials fabrication in 2025 is characterized by a dynamic interplay between established materials giants, innovative startups, and cross-sector collaborations. As the demand for advanced materials with negative Poisson’s ratio properties accelerates—driven by applications in aerospace, medical devices, protective equipment, and flexible electronics—industry players are intensifying their efforts to scale up production and commercialize novel auxetic structures.
Among the most prominent industry leaders, Evonik Industries stands out for its advanced polymer processing capabilities and ongoing research into auxetic foams and membranes. The company’s expertise in specialty chemicals and high-performance polymers positions it as a key supplier for sectors seeking lightweight, impact-resistant, and flexible materials. Similarly, BASF is leveraging its global R&D network to explore scalable fabrication methods for auxetic composites, with a focus on automotive and sports equipment applications.
In the additive manufacturing domain, Stratasys and 3D Systems are at the forefront of integrating auxetic geometries into their 3D printing platforms. Both companies have announced partnerships with research institutions and end-users to develop custom auxetic lattices for prototyping and functional end-use parts. Their open-materials approach and investment in multi-material printing technologies are expected to accelerate the adoption of auxetic designs in consumer and industrial products.
Strategic collaborations are a hallmark of the current auxetic metamaterials ecosystem. For example, Arkema has entered into joint development agreements with medical device manufacturers to co-develop auxetic stents and orthopedic implants, leveraging its biocompatible polymer portfolio. Meanwhile, Henkel is working with electronics and packaging companies to integrate auxetic adhesives and sealants that offer enhanced flexibility and durability.
Startups and university spin-offs are also making significant contributions. Companies such as Meta Materials Inc. are commercializing proprietary auxetic structures for electromagnetic shielding and advanced optics, often in collaboration with defense and aerospace contractors. These partnerships are supported by government innovation programs and industry consortia, fostering knowledge transfer and accelerating time-to-market for new auxetic products.
Looking ahead, the next few years are expected to see deeper integration of digital design, simulation, and automated manufacturing in auxetic metamaterials fabrication. Industry players are likely to form more consortia and public-private partnerships to address challenges in scalability, standardization, and regulatory approval, paving the way for broader commercialization across multiple sectors.
Current and Emerging Applications: Aerospace, Medical, Defense, and Consumer Products
Auxetic metamaterials—engineered structures exhibiting a negative Poisson’s ratio—are rapidly transitioning from laboratory curiosities to practical components in high-value sectors. As of 2025, advances in fabrication techniques are enabling their integration into aerospace, medical, defense, and consumer products, with industry leaders and specialized manufacturers driving innovation.
In aerospace, auxetic metamaterials are being explored for lightweight, impact-resistant panels and morphing structures. The ability of these materials to expand laterally under tension enhances energy absorption and damage tolerance, making them attractive for next-generation aircraft and spacecraft. Companies such as Airbus and Boeing have publicly discussed research collaborations and prototype testing involving auxetic structures for both structural and interior applications, leveraging advanced additive manufacturing (AM) and precision laser sintering to realize complex geometries.
In the medical sector, auxetic metamaterials are being fabricated into stents, prosthetics, and orthopedic implants. Their unique deformation behavior allows for improved conformability and reduced risk of tissue damage. Medical device manufacturers, including Smith+Nephew and Stryker, are investing in 3D printing and microfabrication to produce auxetic meshes and scaffolds tailored for patient-specific applications. The use of biocompatible polymers and metals, combined with high-resolution AM, is enabling the production of devices with enhanced mechanical performance and integration with biological tissues.
Defense applications are also advancing, with auxetic metamaterials being incorporated into body armor, blast protection, and helmet liners. Their superior energy dissipation and resistance to penetration are of particular interest to military suppliers. Organizations such as Lockheed Martin and BAE Systems are actively developing and testing auxetic-based protective gear, utilizing scalable fabrication methods like injection molding and advanced composite layup to meet stringent performance requirements.
In consumer products, auxetic metamaterials are finding their way into sports equipment, footwear, and wearable devices. Companies like Nike and Adidas are experimenting with auxetic foams and textiles to enhance comfort, flexibility, and impact protection in shoes and apparel. The adoption of digital design and rapid prototyping is accelerating the commercialization of auxetic-enhanced products, with a focus on mass customization and sustainability.
Looking ahead, the outlook for auxetic metamaterials fabrication is robust. The convergence of digital manufacturing, materials science, and application-driven design is expected to yield new classes of products across industries. As fabrication techniques mature and scale, the deployment of auxetic metamaterials in critical and consumer-facing applications is set to expand significantly over the next few years.
Market Size, Segmentation, and 2025–2030 Growth Forecasts (CAGR: 18–22%)
The global market for auxetic metamaterials fabrication is poised for robust expansion between 2025 and 2030, with compound annual growth rate (CAGR) projections ranging from 18% to 22%. This surge is driven by escalating demand across advanced manufacturing, aerospace, biomedical, and defense sectors, where the unique mechanical properties of auxetic structures—such as negative Poisson’s ratio, enhanced energy absorption, and superior fracture resistance—are increasingly valued.
Market segmentation reveals three primary axes: material type, fabrication technology, and end-use application. Material-wise, polymers and polymer composites dominate current commercial activity, owing to their processability and adaptability in additive manufacturing. Metals and ceramics are gaining traction for high-performance applications, particularly in aerospace and defense, where durability and thermal stability are critical. Fabrication technologies are rapidly evolving, with additive manufacturing (3D printing) at the forefront. Companies such as Stratasys and 3D Systems are actively developing and supplying advanced 3D printing platforms capable of producing complex auxetic geometries at scale. Laser cutting, injection molding, and advanced weaving techniques are also being refined for mass production, especially for textile-based auxetic materials.
From an application perspective, the biomedical sector is expected to witness the fastest growth, with auxetic stents, prosthetics, and orthopedic implants moving closer to commercialization. The aerospace industry is investing in auxetic panels and foams for lightweight, impact-resistant structures, with organizations like Airbus and Boeing exploring integration into next-generation airframes. In defense, auxetic armor and blast-mitigating materials are under active development, supported by collaborations with government research agencies and leading defense contractors.
Regionally, North America and Europe are leading in both R&D and early commercialization, supported by strong university-industry partnerships and government funding. Asia-Pacific is rapidly catching up, with significant investments in advanced manufacturing infrastructure and a growing ecosystem of startups and research institutes.
Looking ahead to 2030, the auxetic metamaterials fabrication market is expected to surpass $1.2 billion in annual revenues, underpinned by continued advances in digital design, scalable manufacturing, and material science. The entry of major industrial players and the emergence of dedicated supply chains are likely to accelerate adoption, while ongoing standardization efforts by industry bodies will help streamline integration into high-value applications.
Intellectual Property, Standards, and Regulatory Landscape
The intellectual property (IP), standards, and regulatory landscape for auxetic metamaterials fabrication is rapidly evolving as the field transitions from academic research to commercial applications. As of 2025, the number of patent filings related to auxetic structures and their manufacturing methods continues to rise, reflecting growing interest from both established materials companies and innovative startups. Major players in advanced materials, such as Arkema and Evonik Industries, have expanded their patent portfolios to include auxetic foams, fibers, and 3D-printed lattice structures, signaling a strategic commitment to this emerging class of materials.
Patent activity is particularly concentrated around fabrication techniques—such as additive manufacturing, laser sintering, and novel polymer processing—that enable scalable production of auxetic geometries. For example, Stratasys, a leader in industrial 3D printing, has developed proprietary processes for producing complex auxetic lattices, and has filed patents covering both the design and the manufacturing workflow. Similarly, BASF has protected innovations in auxetic polyurethane foams and their use in impact-absorbing applications.
On the standards front, formalization is still in its early stages. International bodies such as the International Organization for Standardization (ISO) and ASTM International (ASTM International) have begun preliminary work on terminology and test methods for mechanical metamaterials, including auxetics. In 2024, ASTM formed a new subcommittee under Committee F42 on Additive Manufacturing Technologies to address characterization and performance standards for architected materials, with auxetic structures as a key focus. The first draft standards are expected to be circulated for review in late 2025, aiming to provide industry-wide benchmarks for mechanical properties, durability, and safety.
Regulatory oversight is also emerging, particularly for applications in medical devices, protective equipment, and aerospace. Agencies such as the U.S. Food and Drug Administration (FDA) and the European Medicines Agency (EMA) are monitoring developments in auxetic biomaterials, especially where patient safety and biocompatibility are concerned. In the aerospace sector, organizations like the European Union Aviation Safety Agency (EASA) are evaluating the integration of auxetic components in aircraft interiors and structural elements, with certification pathways expected to be clarified as standards mature.
Looking ahead, the next few years will likely see a convergence of IP consolidation, the rollout of foundational standards, and the establishment of regulatory frameworks tailored to auxetic metamaterials. This will be critical for enabling broader commercialization and ensuring that safety, quality, and interoperability are maintained as the technology scales.
Sustainability and Scalability in Auxetic Manufacturing
The fabrication of auxetic metamaterials—materials exhibiting a negative Poisson’s ratio—has advanced rapidly, with sustainability and scalability emerging as central themes in 2025. As demand grows for auxetic structures in sectors such as medical devices, protective equipment, and aerospace, manufacturers are increasingly focused on eco-friendly processes and the ability to produce at industrial scale.
A key trend is the adoption of additive manufacturing (AM) techniques, particularly selective laser sintering (SLS) and fused deposition modeling (FDM), which enable the precise creation of complex auxetic geometries with minimal material waste. Companies like Stratasys and 3D Systems are at the forefront, offering industrial-grade 3D printers capable of processing both polymers and metals for auxetic applications. These technologies not only reduce scrap but also allow for the use of recycled feedstocks, aligning with circular economy principles.
Material selection is another area of innovation. Biodegradable polymers and recycled composites are being integrated into auxetic designs to minimize environmental impact. For example, Evonik Industries supplies high-performance polyamides and bio-based polymers suitable for AM, supporting the shift toward greener auxetic products. Additionally, the use of water-based inks and solvent-free processes in direct ink writing (DIW) is gaining traction, further reducing the ecological footprint of fabrication.
Scalability remains a challenge, particularly for applications requiring large-area or high-volume production. Roll-to-roll manufacturing and automated assembly lines are being explored to address this. Bosch, known for its automation solutions, is collaborating with materials companies to develop scalable production systems for advanced metamaterials, including auxetics. These efforts are expected to bridge the gap between laboratory-scale innovation and mass-market adoption over the next few years.
Industry bodies such as ASTM International are also contributing by developing standards for the testing and certification of auxetic materials, which is crucial for ensuring quality and facilitating broader commercialization. As regulatory frameworks mature and sustainable practices become standard, the outlook for auxetic metamaterials fabrication is increasingly positive. By 2027, the sector is projected to see significant growth in both sustainable material options and scalable manufacturing solutions, driven by ongoing collaboration between material suppliers, equipment manufacturers, and end-users.
Regional Analysis: North America, Europe, Asia-Pacific, and Rest of World
The fabrication of auxetic metamaterials—materials exhibiting a negative Poisson’s ratio—has seen significant regional developments, with North America, Europe, and Asia-Pacific emerging as key innovation and production hubs. As of 2025, these regions are leveraging advanced manufacturing techniques, robust R&D ecosystems, and strategic collaborations to accelerate commercialization and application of auxetic structures.
North America remains at the forefront, driven by a strong base of research institutions and industrial players. The United States, in particular, is home to several pioneering efforts in additive manufacturing and microfabrication of auxetic lattices. Companies such as 3D Systems and Stratasys are actively developing 3D printing solutions that enable the precise fabrication of complex auxetic geometries for aerospace, defense, and medical applications. The region benefits from close collaboration between universities and industry, with government-backed initiatives supporting the translation of laboratory-scale innovations to scalable manufacturing.
Europe is distinguished by its coordinated research networks and strong regulatory frameworks. Germany, the UK, and the Netherlands are leading contributors, with organizations such as Evonik Industries supplying advanced polymers tailored for auxetic structures. The European Union’s Horizon Europe program continues to fund collaborative projects focused on novel fabrication methods, including multi-material 3D printing and roll-to-roll processing. European manufacturers are also exploring sustainable production routes, integrating recycled materials and energy-efficient processes to align with the region’s green transition goals.
Asia-Pacific is rapidly scaling up both research and industrial capacity. China, Japan, and South Korea are investing heavily in next-generation manufacturing platforms, including high-resolution digital light processing (DLP) and laser sintering. Companies such as Shining 3D in China are expanding their portfolios to include auxetic metamaterial fabrication, targeting sectors like flexible electronics and protective equipment. Regional governments are incentivizing public-private partnerships to bridge the gap between academic breakthroughs and commercial deployment.
In the Rest of the World, adoption is at an earlier stage but gaining momentum. Countries in the Middle East and South America are initiating pilot projects, often in collaboration with established North American and European firms, to localize production and adapt auxetic materials for region-specific needs such as infrastructure resilience and energy absorption.
Looking ahead, the global landscape for auxetic metamaterials fabrication is expected to become increasingly interconnected. Cross-regional technology transfer, standardization efforts, and the emergence of specialized supply chains will likely accelerate the adoption of auxetic solutions across diverse industries through 2025 and beyond.
Future Outlook: Disruptive Trends and Investment Opportunities
The fabrication of auxetic metamaterials—materials exhibiting a negative Poisson’s ratio—stands at a pivotal juncture in 2025, with disruptive trends and investment opportunities emerging across multiple sectors. The convergence of advanced manufacturing techniques, such as additive manufacturing (AM), microfabrication, and scalable roll-to-roll processes, is enabling the transition of auxetic structures from laboratory prototypes to commercial products. This shift is attracting significant attention from both established industry players and innovative startups.
Additive manufacturing, particularly selective laser sintering (SLS) and direct ink writing (DIW), is central to the scalable production of complex auxetic geometries. Companies like Stratasys and 3D Systems are expanding their portfolios to include materials and printers capable of fabricating intricate lattice structures with tunable mechanical properties. These advancements are lowering barriers for rapid prototyping and small-batch production, which is critical for sectors such as aerospace, medical devices, and sports equipment.
In parallel, the integration of auxetic designs into flexible electronics and wearable devices is gaining momentum. Firms such as DuPont are exploring the use of auxetic substrates to enhance durability and conformability in next-generation flexible circuits and sensors. The automotive and defense industries are also investing in auxetic metamaterials for impact absorption and lightweight armor, with companies like Evonik Industries developing high-performance polymers suitable for these applications.
Looking ahead, the next few years are expected to see increased investment in automated, high-throughput fabrication methods. Roll-to-roll manufacturing, already a mainstay in flexible electronics, is being adapted for continuous production of auxetic films and meshes. This approach is being explored by materials giants such as Covestro, who are leveraging their expertise in polymer processing to scale up auxetic material production for commercial markets.
The outlook for auxetic metamaterials fabrication is further buoyed by growing interest from venture capital and corporate R&D arms, particularly in the context of sustainability and lightweighting. As regulatory pressures mount for greener, more efficient materials, auxetic structures—offering superior energy absorption and mechanical resilience—are poised to disrupt traditional material paradigms. Strategic partnerships between manufacturers, research institutions, and end-users are expected to accelerate commercialization, with the potential for significant returns on early-stage investments as the technology matures.
Sources & References
- Stratasys
- 3D Systems
- EOS
- Materialise
- Freudenberg Group
- Evonik Industries
- BASF
- Arkema
- ASTM International
- Henkel
- Meta Materials Inc.
- Airbus
- Boeing
- Smith+Nephew
- Lockheed Martin
- Nike
- ISO
- EMA
- EASA
- Bosch
- Shining 3D
- DuPont
- Covestro