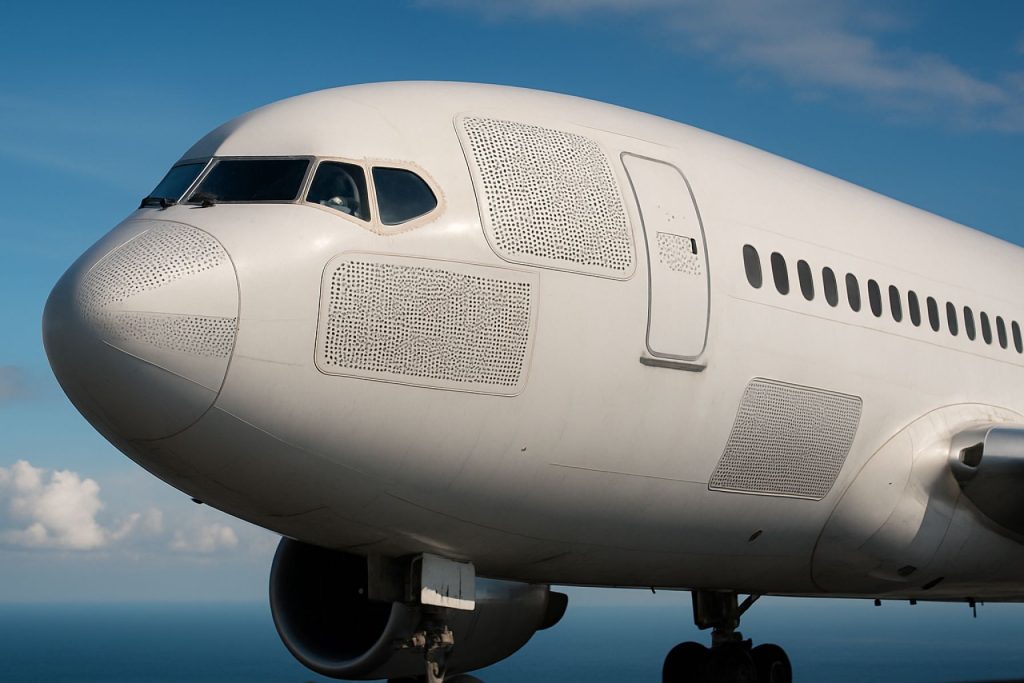
Aeroacoustic Noise Reduction Materials in 2025: Innovations Reshaping Aircraft Silence and Efficiency. Explore How Advanced Materials Are Transforming the Future of Aviation Noise Control.
- Executive Summary: Key Trends and Market Outlook (2025–2029)
- Market Size, Growth Forecasts, and Regional Analysis
- Core Technologies: Materials Science and Acoustic Engineering Advances
- Emerging Innovations: Nanomaterials, Metamaterials, and Smart Surfaces
- Regulatory Landscape and Industry Standards (e.g., FAA, EASA, ICAO)
- Competitive Landscape: Leading Manufacturers and New Entrants
- Application Segments: Commercial Aviation, Urban Air Mobility, and Defense
- Sustainability and Environmental Impact of Noise Reduction Materials
- Challenges, Barriers, and Opportunities for Adoption
- Future Outlook: R&D Pipelines, Investment Trends, and Next-Gen Solutions
- Sources & References
Executive Summary: Key Trends and Market Outlook (2025–2029)
The global focus on reducing aeroacoustic noise—unwanted sound generated by airflow over surfaces—continues to intensify as regulatory bodies and industry stakeholders prioritize quieter, more sustainable transportation and infrastructure. Between 2025 and 2029, the market for aeroacoustic noise reduction materials is poised for robust growth, driven by advancements in material science, stricter noise regulations, and the expanding adoption of electric and hybrid propulsion systems in aerospace and automotive sectors.
Aeroacoustic noise reduction materials encompass a range of engineered solutions, including advanced composites, porous metals, acoustic foams, and metamaterials. These materials are increasingly integrated into aircraft fuselages, engine nacelles, automotive body panels, and wind turbine blades to mitigate noise at the source and along transmission paths. The aviation sector, in particular, is a major driver, as manufacturers respond to evolving noise standards set by organizations such as the International Civil Aviation Organization (ICAO) and the Federal Aviation Administration (FAA). Leading aerospace companies, including Boeing and Airbus, are investing in next-generation noise-reducing materials for both commercial and urban air mobility platforms.
Recent years have seen the commercialization of novel materials such as micro-perforated panels, nanostructured coatings, and lightweight honeycomb composites. For example, Saint-Gobain and 3M are actively developing and supplying advanced acoustic insulation solutions tailored for aerospace and automotive applications. In the wind energy sector, companies like Siemens Gamesa are deploying serrated trailing edge technologies and sound-absorbing materials to reduce turbine blade noise, supporting both regulatory compliance and community acceptance.
Looking ahead to 2029, the market outlook is shaped by several key trends:
- Continued R&D investment in multifunctional materials that combine noise reduction with weight savings and thermal management.
- Integration of digital design and simulation tools to optimize material performance and placement, accelerating time-to-market for new solutions.
- Growing demand from emerging sectors such as electric vertical takeoff and landing (eVTOL) aircraft, where cabin and external noise are critical design considerations.
- Expansion of partnerships between material suppliers, OEMs, and research institutions to accelerate innovation and standardization.
Overall, the period from 2025 to 2029 is expected to witness accelerated adoption of aeroacoustic noise reduction materials, underpinned by regulatory pressures, technological breakthroughs, and the pursuit of quieter, more efficient mobility and energy systems.
Market Size, Growth Forecasts, and Regional Analysis
The global market for aeroacoustic noise reduction materials is experiencing robust growth, driven by increasingly stringent noise regulations, rising air traffic, and the demand for quieter, more efficient aircraft. As of 2025, the market is estimated to be valued in the low single-digit billions (USD), with projections indicating a compound annual growth rate (CAGR) in the range of 6–8% through the late 2020s. This growth is underpinned by ongoing investments in advanced materials and the integration of noise-reducing technologies in both commercial and military aviation sectors.
North America remains the largest regional market, supported by the presence of major aircraft manufacturers and suppliers, as well as regulatory frameworks such as the FAA’s noise standards. The United States, in particular, is home to leading aerospace companies and material innovators, including Boeing and Honeywell, both of which are actively developing and implementing aeroacoustic solutions in new aircraft models. The region also benefits from a strong network of material suppliers and research institutions focused on acoustic performance.
Europe follows closely, with significant contributions from countries such as France, Germany, and the United Kingdom. The European Union’s “Flightpath 2050” vision and the Clean Sky initiatives have accelerated the adoption of advanced noise reduction materials, particularly in collaboration with major OEMs like Airbus and suppliers such as Safran. These companies are investing in lightweight composites, acoustic liners, and metamaterials to meet both regulatory and passenger comfort requirements.
The Asia-Pacific region is emerging as a high-growth market, propelled by rapid expansion in commercial aviation and increasing local manufacturing capabilities. Countries such as China and Japan are investing in indigenous aircraft programs and partnering with global suppliers to incorporate state-of-the-art noise reduction materials. Companies like COMAC are integrating these materials into new aircraft platforms, reflecting the region’s commitment to meeting international noise standards and enhancing competitiveness.
Looking ahead, the market outlook for aeroacoustic noise reduction materials remains positive. Key growth drivers include the electrification of aircraft, which introduces new noise profiles and material requirements, and the proliferation of urban air mobility (UAM) vehicles, where community noise concerns are paramount. As regulatory bodies worldwide continue to tighten noise limits and as airlines prioritize passenger experience, demand for innovative, high-performance noise reduction materials is expected to accelerate through the remainder of the decade.
Core Technologies: Materials Science and Acoustic Engineering Advances
Aeroacoustic noise reduction materials are at the forefront of efforts to mitigate unwanted sound generated by turbulent airflow over surfaces in aerospace, automotive, and wind energy applications. As of 2025, the sector is witnessing rapid advancements in both the composition and application of these materials, driven by stricter regulatory requirements and growing demand for quieter, more efficient vehicles and infrastructure.
One of the most significant trends is the integration of advanced composite materials with tailored microstructures. These composites, often based on carbon fiber or glass fiber matrices, are being engineered with embedded porous layers or micro-perforations to disrupt and dissipate sound waves. For example, leading aerospace manufacturers such as Boeing and Airbus have been actively developing and implementing acoustic liners in engine nacelles and fuselage panels. These liners utilize honeycomb structures and resonant cavities to absorb a broad spectrum of frequencies, significantly reducing noise emissions during takeoff and landing.
In the automotive sector, companies like Tesla and BMW are incorporating lightweight, sound-absorbing foams and multi-layered laminates into vehicle body panels and undercarriages. These materials not only dampen aeroacoustic noise but also contribute to overall vehicle weight reduction, supporting energy efficiency goals. The use of recycled and bio-based polymers is also gaining traction, aligning with sustainability targets and circular economy principles.
Wind turbine manufacturers, including Siemens Gamesa and GE, are deploying serrated trailing edge attachments and specialized coatings on turbine blades to minimize noise generated by blade-tip vortices. These solutions are often developed in collaboration with academic and research institutions, leveraging computational fluid dynamics (CFD) and acoustic modeling to optimize material properties and geometries.
Looking ahead, the next few years are expected to bring further convergence of materials science and digital engineering. The adoption of additive manufacturing (3D printing) is enabling the production of complex, functionally graded acoustic materials that were previously unachievable with traditional methods. Additionally, the integration of smart materials—capable of dynamically adjusting their acoustic properties in response to changing environmental conditions—is an emerging area of research, with potential for real-time noise control in both aerospace and ground transportation.
Overall, the outlook for aeroacoustic noise reduction materials is robust, with ongoing investment from major OEMs and suppliers, and a clear trajectory toward multifunctional, sustainable, and digitally optimized solutions.
Emerging Innovations: Nanomaterials, Metamaterials, and Smart Surfaces
The pursuit of quieter, more efficient aircraft and wind energy systems is driving rapid innovation in aeroacoustic noise reduction materials, with a particular focus on nanomaterials, metamaterials, and smart surfaces. As of 2025, these advanced materials are transitioning from laboratory research to early-stage commercial applications, promising significant improvements in noise mitigation for aerospace, automotive, and renewable energy sectors.
Nanomaterials, such as carbon nanotubes and graphene-based composites, are being engineered to enhance sound absorption and damping properties while maintaining lightweight characteristics essential for aerospace applications. These materials can be integrated into aircraft fuselage panels, engine nacelles, and rotor blades to disrupt sound wave propagation at the microscopic level. For example, Airbus has been actively exploring nanostructured coatings and composite materials to reduce cabin and external noise, with ongoing collaborations with leading nanotechnology institutes. Similarly, Boeing is investing in advanced material research, targeting both noise and vibration reduction in next-generation aircraft.
Metamaterials—engineered structures with properties not found in nature—are at the forefront of aeroacoustic innovation. These materials can be designed to manipulate sound waves, creating “acoustic cloaks” or redirecting noise away from sensitive areas. In 2024 and 2025, several prototypes of acoustic metamaterial liners for jet engines and wind turbine blades have demonstrated up to 30% reduction in broadband noise in controlled tests. Companies such as Safran and GE Aerospace are leading efforts to integrate metamaterial-based solutions into commercial engine nacelles and auxiliary power units, with field trials expected to expand in the next few years.
Smart surfaces represent another promising avenue, utilizing embedded sensors and actuators to adaptively respond to changing noise conditions. These surfaces can alter their acoustic impedance or vibrational characteristics in real time, optimizing noise reduction across different flight phases or wind conditions. Rolls-Royce is developing adaptive acoustic panels for engine inlets, while Siemens is exploring smart coatings for wind turbine blades that dynamically adjust to minimize aerodynamic noise.
Looking ahead, the integration of these emerging materials is expected to accelerate, driven by stricter regulatory noise limits and growing demand for sustainable, low-noise transportation. Collaborative initiatives between manufacturers, material suppliers, and research institutions are likely to yield commercially viable solutions by the late 2020s, with the potential to reshape noise management strategies across multiple industries.
Regulatory Landscape and Industry Standards (e.g., FAA, EASA, ICAO)
The regulatory landscape for aeroacoustic noise reduction materials is rapidly evolving as global aviation authorities intensify efforts to mitigate aircraft noise pollution. In 2025, the focus remains on harmonizing standards and accelerating the adoption of advanced materials that can help airlines and manufacturers comply with increasingly stringent noise limits.
The Federal Aviation Administration (FAA) in the United States continues to enforce its Stage 5 noise standards, which apply to new subsonic jet airplanes certified after January 1, 2018. These standards require a cumulative 7-decibel reduction in noise compared to previous Stage 4 limits, pushing manufacturers to integrate innovative noise-reducing materials in nacelles, engine liners, and airframe structures. The FAA is also collaborating with industry stakeholders to evaluate the effectiveness of new composite and metamaterial-based solutions in real-world operations.
In Europe, the European Union Aviation Safety Agency (EASA) aligns closely with ICAO Annex 16 Volume I, which sets international noise certification standards. EASA’s Environmental Protection requirements are expected to tighten further in the coming years, with ongoing consultations about incorporating lifecycle assessments of noise reduction materials and their recyclability. This regulatory push is prompting European OEMs and suppliers to accelerate R&D in lightweight, high-performance acoustic liners and advanced sound-absorbing composites.
At the global level, the International Civil Aviation Organization (ICAO) continues to update its noise certification framework, with the Committee on Aviation Environmental Protection (CAEP) reviewing new evidence on the effectiveness of next-generation materials. ICAO’s Balanced Approach encourages member states to adopt both operational and technological solutions, including the use of novel materials, to achieve community noise reduction targets.
Industry standards are also being shaped by organizations such as the SAE International, which develops technical specifications for the testing and qualification of aeroacoustic materials. These standards are critical for ensuring that new products meet both regulatory and operational requirements.
Looking ahead, regulatory agencies are expected to further incentivize the adoption of advanced noise reduction materials through certification credits, funding for demonstration projects, and public-private partnerships. The convergence of regulatory pressure and industry innovation is likely to accelerate the commercialization of metamaterials, nanostructured composites, and bio-based acoustic solutions, setting new benchmarks for aircraft noise performance by the late 2020s.
Competitive Landscape: Leading Manufacturers and New Entrants
The competitive landscape for aeroacoustic noise reduction materials in 2025 is characterized by a blend of established aerospace suppliers, advanced materials specialists, and a growing cohort of innovative entrants. The sector is driven by increasingly stringent noise regulations, particularly in aviation and urban air mobility, as well as the demand for lighter, more efficient, and sustainable solutions.
Among the leading manufacturers, Eaton continues to play a significant role, leveraging its expertise in engineered materials and aerospace systems. The company’s portfolio includes advanced acoustic insulation and damping materials tailored for both commercial and military aircraft. Eaton has recently expanded its R&D efforts to develop lighter-weight composites that maintain high noise attenuation, responding to the dual pressures of fuel efficiency and regulatory compliance.
Another major player, Saint-Gobain, is recognized for its high-performance acoustic foams and composite laminates. The company’s aerospace division supplies noise reduction materials for engine nacelles, fuselage panels, and cabin interiors. In 2024–2025, Saint-Gobain has focused on integrating recycled content and bio-based polymers into its product lines, aligning with sustainability goals set by major OEMs.
In the United States, Honeywell remains a key supplier of aeroacoustic solutions, offering proprietary sound-absorbing panels and vibration-damping systems. The company’s recent collaborations with electric vertical takeoff and landing (eVTOL) manufacturers highlight its commitment to next-generation urban air mobility, where noise reduction is a critical enabler for public acceptance and regulatory approval.
Emerging entrants are also shaping the competitive landscape. Startups such as Zotefoams are gaining traction with advanced closed-cell foams that offer superior acoustic performance at reduced weight. These materials are being evaluated for both traditional aircraft and new eVTOL platforms. Additionally, 3M is leveraging its expertise in adhesives and specialty materials to introduce novel damping films and lightweight acoustic barriers, targeting both retrofit and OEM markets.
Looking ahead, the next few years are expected to see intensified competition as manufacturers race to meet evolving noise standards and sustainability targets. Partnerships between material innovators and aerospace OEMs are likely to accelerate, with a focus on multifunctional materials that combine noise reduction, fire resistance, and environmental performance. The entry of new players, particularly those with expertise in nanomaterials and bio-based composites, is anticipated to further diversify the market and drive technological advancements.
Application Segments: Commercial Aviation, Urban Air Mobility, and Defense
Aeroacoustic noise reduction materials are increasingly critical across commercial aviation, urban air mobility (UAM), and defense sectors as regulatory and societal pressures mount for quieter, more sustainable flight. In 2025 and the coming years, the application of advanced materials and engineered structures is accelerating, driven by both technological innovation and evolving operational requirements.
In commercial aviation, the focus remains on reducing engine and airframe noise to comply with stringent airport noise regulations and improve passenger comfort. Leading aircraft manufacturers such as Boeing and Airbus are integrating next-generation acoustic liners, porous materials, and composite structures into nacelles and fuselage sections. For example, the use of advanced honeycomb sandwich panels and micro-perforated liners in engine nacelles has demonstrated significant reductions in fan and jet noise. Suppliers like Safran and GE Aerospace are actively developing and supplying these materials, with ongoing research into meta-materials and adaptive structures that can further attenuate noise across a broader frequency range.
The urban air mobility segment, encompassing electric vertical takeoff and landing (eVTOL) vehicles, presents unique challenges and opportunities for aeroacoustic noise reduction. UAM vehicles operate at lower altitudes and closer to populated areas, making noise a critical barrier to public acceptance and regulatory approval. Companies such as Joby Aviation and Lilium are investing in proprietary blade designs, shrouded rotors, and advanced composite materials to minimize both tonal and broadband noise. The integration of lightweight, sound-absorbing composites and the optimization of propeller and rotor geometries are expected to yield further improvements as these vehicles approach commercial deployment in the next few years.
In the defense sector, noise reduction materials are increasingly valued not only for stealth and survivability but also for operational safety and crew comfort. Major defense contractors such as Lockheed Martin and Northrop Grumman are incorporating advanced acoustic damping materials into both fixed-wing and rotary platforms. These include viscoelastic layers, composite skins, and specialized coatings designed to suppress noise signatures and reduce detectability by acoustic sensors. The next few years are likely to see further adoption of adaptive and tunable materials, enabling real-time noise management in dynamic operational environments.
Overall, the outlook for aeroacoustic noise reduction materials is robust, with cross-sector collaboration and rapid material innovation expected to deliver quieter, more efficient aircraft across commercial, urban, and defense applications by the late 2020s.
Sustainability and Environmental Impact of Noise Reduction Materials
Aeroacoustic noise reduction materials are increasingly scrutinized for their sustainability and environmental impact, especially as the aviation and wind energy sectors intensify efforts to meet stricter regulatory and societal expectations in 2025 and beyond. Traditionally, noise reduction in aerospace and wind turbine applications has relied on synthetic foams, composites, and fibrous materials, many of which are derived from petrochemicals and present end-of-life disposal challenges. However, the current landscape is shifting toward eco-friendly alternatives and circular economy principles.
In 2025, leading aerospace manufacturers are prioritizing the integration of recyclable and bio-based materials into their noise attenuation solutions. For instance, Airbus has publicly committed to increasing the use of sustainable materials across its aircraft, including cabin and engine nacelle components where aeroacoustic performance is critical. The company is exploring natural fiber composites and recycled thermoplastics, which offer both noise dampening and reduced environmental footprint. Similarly, Boeing is advancing research into lightweight, recyclable acoustic liners and insulation materials, aiming to minimize both operational noise and lifecycle emissions.
In the wind energy sector, manufacturers such as Siemens Gamesa Renewable Energy are deploying noise-reducing blade add-ons and coatings that are designed for recyclability. Siemens Gamesa’s “RecyclableBlade” technology, for example, incorporates resin systems that allow for full blade recycling at end-of-life, addressing a major environmental concern associated with composite waste. These innovations are coupled with bio-based resins and natural fiber reinforcements, which further reduce the carbon footprint of noise mitigation solutions.
Material suppliers are also responding to sustainability demands. Huntsman Corporation and BASF are developing new grades of polyurethane and melamine foams with recycled content and lower embodied energy, specifically targeting aerospace and wind turbine acoustic applications. These materials are engineered to maintain high sound absorption while enabling easier recycling or safe incineration at end-of-life.
Looking ahead, the next few years are expected to see increased adoption of life cycle assessment (LCA) tools to quantify the environmental benefits of new aeroacoustic materials. Regulatory bodies in Europe and North America are likely to introduce stricter requirements for material transparency and recyclability, further accelerating the shift toward sustainable solutions. The convergence of noise reduction performance and environmental stewardship is set to define the competitive landscape for aeroacoustic materials through the remainder of the decade.
Challenges, Barriers, and Opportunities for Adoption
The adoption of aeroacoustic noise reduction materials in aerospace and transportation sectors is accelerating, yet several challenges and barriers persist as of 2025. One of the primary technical challenges is balancing noise attenuation with other critical material properties such as weight, durability, and thermal resistance. For instance, advanced composite materials and metamaterials designed for noise reduction must not compromise the structural integrity or add significant weight to aircraft, which would negatively impact fuel efficiency and emissions targets. Companies like Airbus and Boeing are actively researching and integrating lightweight acoustic liners and innovative surface treatments, but the need for further optimization remains.
Cost is another significant barrier. High-performance noise reduction materials, such as those incorporating nanostructures or advanced polymers, often come with elevated production and integration costs. This can limit their widespread adoption, especially among smaller manufacturers or in cost-sensitive market segments. The supply chain for specialized materials, including advanced foams and micro-perforated panels, is still maturing, with key suppliers like 3M and Huntsman Corporation working to scale up production and reduce costs through process innovation.
Regulatory pressures and evolving standards present both challenges and opportunities. Stricter noise regulations from bodies such as the International Civil Aviation Organization (ICAO) are driving demand for more effective noise reduction solutions. However, the certification process for new materials is lengthy and complex, requiring extensive testing and validation. This can delay market entry and increase development costs. Industry groups and manufacturers are collaborating to streamline certification pathways and share best practices, aiming to accelerate the adoption of next-generation materials.
On the opportunity side, the push for sustainable aviation and urban air mobility is creating new markets for aeroacoustic materials. Electric vertical takeoff and landing (eVTOL) vehicles, for example, face stringent community noise requirements, spurring innovation in lightweight, high-performance acoustic treatments. Companies such as Safran and GKN Aerospace are investing in R&D to develop solutions tailored for these emerging platforms.
Looking ahead, advances in material science—particularly in the fields of metamaterials and bio-inspired structures—are expected to yield more effective and versatile noise reduction options. Collaborative efforts between manufacturers, suppliers, and regulatory bodies will be crucial to overcoming current barriers. As production scales and costs decrease, broader adoption across commercial aviation, urban mobility, and even automotive sectors is anticipated in the next few years.
Future Outlook: R&D Pipelines, Investment Trends, and Next-Gen Solutions
The future of aeroacoustic noise reduction materials is being shaped by a convergence of advanced research, increased investment, and the urgent need for quieter, more sustainable aviation and transportation systems. As of 2025, the sector is witnessing a surge in R&D activity, with leading aerospace manufacturers, material science innovators, and government agencies prioritizing the development of next-generation solutions.
Major aerospace companies are at the forefront of this movement. Boeing and Airbus have both announced ongoing research collaborations with universities and material suppliers to develop lightweight, high-performance acoustic liners and metamaterials for engine nacelles and airframes. These efforts are driven by increasingly stringent noise regulations, such as those set by the International Civil Aviation Organization (ICAO), and by growing public demand for quieter urban air mobility (UAM) vehicles.
Material innovation is a key focus. Companies like Honeywell and Safran are investing in nanostructured composites, porous ceramics, and advanced polymer foams that offer superior sound absorption while minimizing weight penalties. For example, Safran’s R&D pipeline includes next-generation acoustic panels designed for both commercial aircraft and emerging electric vertical takeoff and landing (eVTOL) platforms. These materials are being engineered to target specific frequency ranges associated with engine and airflow noise, leveraging computational modeling and additive manufacturing for rapid prototyping and customization.
Investment trends indicate a robust outlook. According to public statements and annual reports, both GE Aerospace and Rolls-Royce are allocating significant resources to noise reduction technologies, with a focus on integrating novel materials into next-gen propulsion systems. Additionally, suppliers such as 3M are expanding their product lines to include advanced acoustic insulation solutions tailored for aerospace and high-speed rail applications.
Looking ahead to the next few years, the sector is expected to see the commercialization of bio-based and recyclable noise reduction materials, aligning with broader sustainability goals. Collaborative initiatives between industry and government—such as those led by NASA—are accelerating the transition from laboratory-scale breakthroughs to real-world deployment. The integration of smart materials capable of adaptive noise control, as well as the use of digital twins for predictive acoustic performance, are anticipated to become mainstream by the late 2020s. Overall, the outlook for aeroacoustic noise reduction materials is one of rapid innovation, cross-sector collaboration, and expanding market adoption.
Sources & References
- Boeing
- Airbus
- Siemens Gamesa
- Honeywell
- GE
- Rolls-Royce
- Siemens
- European Union Aviation Safety Agency
- International Civil Aviation Organization
- Eaton
- Zotefoams
- Joby Aviation
- Lockheed Martin
- Northrop Grumman
- BASF
- GKN Aerospace
- NASA