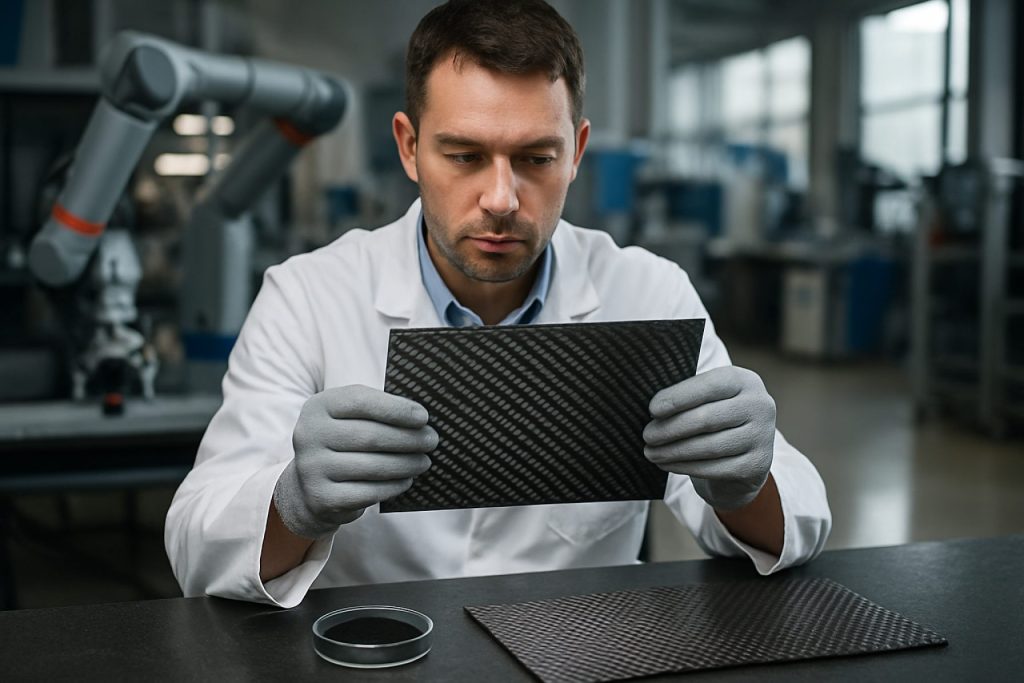
Unlocking the Future of High-Strength Graphene Composites Manufacturing in 2025: How Advanced Processes and Market Forces Are Shaping the Next Era of Ultra-Resilient Materials. Discover the Innovations and Strategic Shifts Driving Industry Growth.
- Executive Summary: 2025 Snapshot and Strategic Insights
- Market Size, Growth Forecasts, and Key Drivers (2025–2030)
- Breakthroughs in Graphene Composite Manufacturing Technologies
- Major Players and Industry Ecosystem Overview
- Raw Material Sourcing and Supply Chain Developments
- Application Trends: Aerospace, Automotive, Construction, and Beyond
- Regulatory Landscape and Industry Standards
- Sustainability, Environmental Impact, and Circular Economy Initiatives
- Investment, M&A, and Partnership Activity
- Future Outlook: Disruptive Innovations and Long-Term Opportunities
- Sources & References
Executive Summary: 2025 Snapshot and Strategic Insights
The high-strength graphene composites manufacturing sector is poised for significant advancements in 2025, driven by both technological innovation and expanding commercial adoption. Graphene’s exceptional mechanical properties—such as tensile strength, flexibility, and conductivity—are increasingly being harnessed to enhance the performance of polymers, metals, and ceramics across industries including aerospace, automotive, energy, and construction.
In 2025, leading manufacturers are scaling up production capacities and refining processes to meet growing demand for high-strength graphene composites. Companies like Directa Plus and First Graphene are at the forefront, leveraging proprietary technologies to produce graphene nanoplatelets and masterbatches that can be integrated into a variety of matrices. Directa Plus has reported successful collaborations with automotive and textile partners, while First Graphene is expanding its PureGRAPH® product line for industrial applications.
Aerospace and defense sectors remain key drivers, with companies such as Lockheed Martin and Airbus exploring graphene-reinforced composites for lightweight, high-strength components. These efforts are supported by ongoing research and pilot projects aimed at improving scalability and cost-effectiveness. In parallel, the construction industry is beginning to adopt graphene-enhanced concrete and coatings, with suppliers like Versarien providing advanced materials for infrastructure projects.
The manufacturing landscape in 2025 is characterized by a shift toward more sustainable and energy-efficient production methods. Companies are investing in green chemistry approaches and closed-loop recycling systems to minimize environmental impact. For example, Versarien emphasizes eco-friendly processes in its graphene production, aligning with broader industry trends toward sustainability.
Strategically, the sector is witnessing increased collaboration between material producers, end-users, and research institutions to accelerate commercialization. Standardization efforts, led by organizations such as the Graphene Flagship, are helping to establish quality benchmarks and facilitate market entry for new products.
Looking ahead, the outlook for high-strength graphene composites manufacturing is robust. Market participants anticipate continued growth in demand, particularly as cost barriers decrease and performance benefits become more widely recognized. The next few years are expected to see further integration of graphene composites into mainstream manufacturing, with ongoing innovation in both materials and processing technologies driving the sector forward.
Market Size, Growth Forecasts, and Key Drivers (2025–2030)
The high-strength graphene composites manufacturing sector is poised for significant expansion between 2025 and 2030, driven by escalating demand across aerospace, automotive, energy, and advanced electronics industries. As of 2025, the market is characterized by a growing number of commercial-scale projects and increased investment from both established materials companies and innovative startups. The unique mechanical, thermal, and electrical properties of graphene—when integrated into polymer, metal, or ceramic matrices—are enabling the development of next-generation lightweight, high-performance components.
Key industry players such as Directa Plus, a leading European graphene producer, and Haydale Graphene Industries, which specializes in functionalized graphene materials, are scaling up production capacities and forming strategic partnerships with end-users in transportation and energy storage. First Graphene is also expanding its manufacturing footprint, focusing on bulk graphene nanoplatelets for composite reinforcement. These companies are investing in process optimization to ensure consistent quality and cost-effective large-scale output, a critical factor for widespread adoption.
The market’s growth trajectory is underpinned by several drivers. First, the push for lightweighting in automotive and aerospace sectors is accelerating the adoption of graphene composites, as these materials offer superior strength-to-weight ratios compared to traditional carbon fiber or metal alloys. For example, G6 Materials is collaborating with manufacturers to integrate graphene-enhanced resins into structural parts, targeting both performance and sustainability goals. Second, the renewable energy sector is leveraging graphene composites for wind turbine blades and battery casings, where enhanced durability and conductivity are critical.
From a regional perspective, Asia-Pacific is expected to lead market growth, with China and South Korea investing heavily in graphene research and industrialization. Companies like The Sixth Element (Changzhou) Materials Technology are supplying graphene powders and masterbatches to local and international composite manufacturers. Meanwhile, European and North American firms are focusing on high-value applications and regulatory compliance, with increasing attention to environmental, health, and safety standards.
Looking ahead to 2030, the market outlook remains robust, with anticipated compound annual growth rates in the double digits. Key challenges include scaling up defect-free graphene production, ensuring uniform dispersion within composite matrices, and reducing costs to compete with incumbent materials. However, ongoing advances in manufacturing technologies and the formation of cross-industry consortia are expected to address these hurdles, paving the way for broader commercialization and new application domains.
Breakthroughs in Graphene Composite Manufacturing Technologies
The manufacturing of high-strength graphene composites is experiencing significant breakthroughs as the industry moves into 2025, driven by advances in scalable production, improved dispersion techniques, and integration with traditional materials. The focus is on leveraging graphene’s exceptional mechanical properties—such as its tensile strength, flexibility, and lightweight nature—to enhance the performance of polymers, metals, and ceramics in demanding applications.
A key development is the refinement of scalable graphene production methods, particularly chemical vapor deposition (CVD) and liquid-phase exfoliation, which are now being adopted at commercial scale. Companies like Directa Plus and First Graphene have expanded their manufacturing capacities, enabling the supply of high-quality graphene nanoplatelets and powders suitable for composite fabrication. These materials are being integrated into thermoset and thermoplastic matrices, resulting in composites with significantly improved strength-to-weight ratios and durability.
One of the persistent challenges—achieving uniform dispersion of graphene within host matrices—has seen notable progress. Advanced functionalization techniques, such as surface modification and the use of compatibilizers, are being implemented to enhance interfacial bonding and prevent agglomeration. Haydale Graphene Industries has pioneered plasma functionalization processes, which tailor the surface chemistry of graphene to optimize its compatibility with various polymers and resins. This has led to the production of composites with up to 30% higher tensile strength compared to conventional carbon fiber-reinforced plastics.
In the metals sector, companies like G6 Materials are developing graphene-aluminum and graphene-copper composites, targeting aerospace and electronics applications where both strength and conductivity are critical. These metal matrix composites are being produced using powder metallurgy and additive manufacturing techniques, allowing for precise control over graphene content and distribution.
Automotive and aerospace manufacturers are beginning to incorporate graphene composites into structural and semi-structural components. For example, Directa Plus has partnered with leading automotive OEMs to develop graphene-enhanced tires and body panels, reporting improved wear resistance and reduced weight. Similarly, Haydale Graphene Industries is collaborating with aerospace suppliers to qualify graphene-reinforced prepregs for next-generation aircraft.
Looking ahead, the outlook for high-strength graphene composites manufacturing is robust. Industry analysts anticipate further cost reductions as production scales, with new hybrid composites—combining graphene with other nanomaterials—expected to enter the market. The next few years will likely see broader adoption across transportation, energy, and construction sectors, as manufacturers continue to demonstrate the reliability and performance benefits of graphene-enhanced materials.
Major Players and Industry Ecosystem Overview
The high-strength graphene composites manufacturing sector is rapidly evolving, with a growing ecosystem of material producers, technology developers, and end-use integrators. As of 2025, the industry is characterized by a mix of established advanced materials companies and innovative startups, each contributing to the scaling and commercialization of graphene-enhanced composites for applications in aerospace, automotive, energy, and consumer goods.
Among the most prominent players, Directa Plus stands out as a leading European manufacturer specializing in graphene nanoplatelets and their integration into composite materials. The company has developed proprietary production processes and collaborates with partners in sectors such as automotive and textiles to deliver high-performance, lightweight solutions. Similarly, Haydale Graphene Industries is recognized for its functionalized graphene materials and advanced dispersion technologies, enabling the scalable production of graphene-reinforced polymers and resins. Haydale’s focus on tailored surface chemistry has facilitated partnerships with aerospace and energy storage companies seeking to leverage the mechanical and electrical enhancements offered by graphene composites.
In North America, XG Sciences is a key supplier of graphene nanoplatelets and masterbatches, supporting a range of composite manufacturers in the automotive and sporting goods industries. The company’s materials are engineered for compatibility with thermoplastics and thermosets, addressing the need for both strength and processability. Another notable player, First Graphene, based in Australia, has expanded its global reach through the supply of high-purity graphene powders and the development of composite formulations targeting construction, mining, and industrial applications.
The industry ecosystem also includes major chemical and materials corporations such as Arkema, which has invested in graphene-enhanced resins and coatings, and Cabot Corporation, which is exploring graphene’s potential in energy storage and conductive composites. These companies bring established manufacturing infrastructure and global distribution networks, accelerating the adoption of graphene composites in mainstream markets.
Looking ahead, the sector is expected to see increased collaboration between graphene producers, composite fabricators, and end-users, with a focus on standardization, quality assurance, and cost reduction. Industry alliances and consortia are likely to play a pivotal role in setting performance benchmarks and facilitating technology transfer. As production capacities expand and processing technologies mature, the high-strength graphene composites market is poised for significant growth, with new entrants and established players alike driving innovation and commercialization through 2025 and beyond.
Raw Material Sourcing and Supply Chain Developments
The sourcing of high-quality graphene and the evolution of its supply chain are pivotal to the advancement of high-strength graphene composites manufacturing. As of 2025, the industry is witnessing a transition from laboratory-scale production to more robust, industrial-scale supply chains, driven by increasing demand from sectors such as aerospace, automotive, and advanced construction materials.
A key development is the scaling up of graphene production methods, particularly chemical vapor deposition (CVD) and liquid-phase exfoliation, which are now being optimized for both quality and cost-effectiveness. Companies like Directa Plus and First Graphene have expanded their manufacturing capacities, focusing on producing graphene nanoplatelets and powders with consistent properties suitable for composite reinforcement. Directa Plus, for example, operates one of Europe’s largest graphene production facilities, supplying materials for polymer and concrete composites.
Supply chain integration is another significant trend. Leading graphene producers are forming strategic partnerships with composite manufacturers to ensure reliable sourcing and tailored material specifications. First Graphene has established collaborations with resin and polymer companies to co-develop graphene-enhanced masterbatches, streamlining the incorporation of graphene into existing composite manufacturing lines. Similarly, Graphenea supplies both raw graphene materials and value-added intermediates, supporting a range of industrial customers in Europe and North America.
Geographical diversification of supply is also underway. While China remains a major producer, European and Australian companies are increasing their market share, reducing dependency on single-region supply and enhancing resilience against geopolitical risks. Graphenea (Spain) and First Graphene (Australia) are notable for their efforts to establish local supply chains and support regional manufacturing ecosystems.
Looking ahead, the next few years are expected to bring further improvements in raw material standardization and traceability, as industry bodies and consortia work to define quality benchmarks for graphene used in high-strength composites. This will facilitate broader adoption in safety-critical applications, such as aerospace and infrastructure. Additionally, sustainability is gaining prominence, with companies exploring greener production methods and recycling strategies for graphene-containing composites.
In summary, 2025 marks a period of rapid maturation for the graphene raw material supply chain, characterized by increased production capacity, strategic partnerships, regional diversification, and a growing emphasis on quality and sustainability—laying a strong foundation for the widespread adoption of high-strength graphene composites.
Application Trends: Aerospace, Automotive, Construction, and Beyond
The application of high-strength graphene composites is accelerating across multiple industries, with aerospace, automotive, and construction sectors at the forefront of adoption in 2025. The unique combination of exceptional mechanical strength, low weight, and multifunctional properties is driving manufacturers to integrate graphene-enhanced materials into next-generation products.
In aerospace, the demand for lighter and stronger materials is pushing the integration of graphene composites into structural components, interior panels, and even coatings. Companies such as Airbus have publicly explored graphene-based materials for aircraft structures, aiming to reduce weight and improve fuel efficiency. Similarly, Boeing has engaged in research partnerships to evaluate graphene’s potential in both primary and secondary aircraft structures. The focus in 2025 is on scaling up manufacturing processes, with several pilot projects transitioning to limited production runs for non-critical components.
The automotive industry is leveraging graphene composites to achieve lighter vehicles with enhanced crashworthiness and improved energy efficiency. Ford Motor Company has incorporated graphene into under-hood components, citing improvements in mechanical performance and noise reduction. Meanwhile, Toray Industries, a global leader in advanced materials, is actively developing graphene-reinforced thermoplastics and thermosets for automotive body panels and battery enclosures. The trend in 2025 is toward integrating graphene composites in electric vehicles, where weight reduction directly translates to increased range and performance.
In construction, graphene composites are being adopted for their superior strength-to-weight ratio and durability. Versarien is collaborating with concrete manufacturers to produce graphene-enhanced concrete, which offers higher compressive strength and reduced material usage. This innovation is particularly relevant for sustainable construction, as it enables the creation of lighter structures with lower carbon footprints. Additionally, Directa Plus is supplying graphene materials for coatings and membranes that improve the longevity and resilience of building materials.
Beyond these sectors, high-strength graphene composites are finding applications in sports equipment, marine vessels, and energy storage systems. The outlook for 2025 and the following years is marked by continued process optimization, cost reduction, and the gradual expansion of graphene composite use from niche, high-performance applications to broader commercial markets. As manufacturing scalability improves and regulatory standards evolve, the penetration of graphene composites is expected to accelerate, reshaping material choices across industries.
Regulatory Landscape and Industry Standards
The regulatory landscape for high-strength graphene composites manufacturing is rapidly evolving as the material transitions from laboratory research to commercial-scale applications. In 2025, regulatory bodies and industry organizations are intensifying efforts to establish clear guidelines and standards to ensure product safety, environmental responsibility, and consistent material performance. This is particularly crucial as graphene composites are increasingly adopted in sectors such as aerospace, automotive, and construction, where reliability and compliance are paramount.
A key development is the ongoing work by the International Organization for Standardization (ISO) and the International Electrotechnical Commission (IEC), which are collaborating on a series of standards specific to graphene materials, including terminology, characterization methods, and safety protocols. The ISO/TS 80004-13:2017 standard, which defines terminology for graphene and related two-dimensional materials, is being updated to reflect advances in composite manufacturing and to harmonize definitions across global markets. These efforts are expected to culminate in new or revised standards by 2026, providing a more robust framework for manufacturers and end-users.
In the European Union, the Registration, Evaluation, Authorisation and Restriction of Chemicals (REACH) regulation continues to play a central role in the approval and monitoring of graphene-based materials. Companies such as Directa Plus and Versarien are actively engaged in ensuring their graphene products comply with REACH requirements, including detailed risk assessments and documentation of potential environmental and health impacts. These companies are also participating in industry consortia to share best practices and contribute to the development of sector-specific guidelines.
In North America, the American Society for Testing and Materials (ASTM International) is expanding its suite of standards for graphene materials, with new test methods for mechanical, electrical, and thermal properties of graphene composites under review. These standards are critical for manufacturers such as XG Sciences and Advanced Graphene Products, who are scaling up production and seeking to assure customers of consistent quality and regulatory compliance.
Looking ahead, the next few years will likely see increased regulatory scrutiny as graphene composites enter more consumer-facing and safety-critical applications. Industry groups such as the Graphene Flagship and the National Graphene Association are expected to play a pivotal role in facilitating dialogue between manufacturers, regulators, and end-users, ensuring that evolving standards keep pace with technological innovation and market needs.
Sustainability, Environmental Impact, and Circular Economy Initiatives
The manufacturing of high-strength graphene composites is increasingly shaped by sustainability imperatives, environmental regulations, and the adoption of circular economy principles. As the sector matures in 2025, leading producers and technology developers are integrating eco-friendly practices across the value chain, from raw material sourcing to end-of-life management.
A key sustainability driver is the shift toward greener graphene production methods. Traditional chemical vapor deposition (CVD) and chemical exfoliation processes often involve hazardous chemicals and significant energy consumption. In response, companies such as Directa Plus have scaled up water-based, chemical-free graphene production, reducing both emissions and waste. Similarly, Versarien emphasizes environmentally benign processes, including the use of sustainable graphite sources and energy-efficient exfoliation techniques.
In composite manufacturing, the integration of graphene into biopolymers and recycled matrices is gaining traction. For example, Graphenea collaborates with partners to develop graphene-enhanced composites using recycled plastics and bio-based resins, aiming to lower the carbon footprint of advanced materials. These efforts are supported by industry-wide initiatives to standardize life cycle assessments (LCA) and promote transparency in environmental performance.
Waste minimization and resource efficiency are also central to the sector’s circular economy strategies. Companies are investing in closed-loop manufacturing systems, where offcuts and defective parts are reprocessed into new composite materials. Haydale Graphene Industries has piloted recycling protocols for graphene-enhanced thermoplastics, enabling the recovery and reuse of both polymer and graphene components without significant loss of performance.
End-of-life management is a growing focus, with research and pilot projects exploring the recyclability and safe disposal of graphene composites. Industry consortia, often in partnership with automotive and aerospace OEMs, are developing guidelines for dismantling, sorting, and reprocessing composite parts. The European Union’s regulatory push for extended producer responsibility and eco-design is accelerating these efforts, with several manufacturers aligning their product development with anticipated compliance requirements.
Looking ahead, the sector is expected to further embrace digital tools for environmental monitoring and traceability, such as blockchain-based material passports. The convergence of sustainability, regulatory compliance, and customer demand for greener products is set to drive innovation in both process and product design. As a result, high-strength graphene composites are poised to play a pivotal role in the transition to a more circular and low-impact advanced materials industry over the next several years.
Investment, M&A, and Partnership Activity
The high-strength graphene composites manufacturing sector is experiencing a notable surge in investment, mergers and acquisitions (M&A), and strategic partnerships as the industry matures and demand for advanced materials accelerates. In 2025, this activity is being driven by the need for scalable production, integration into end-use applications, and the pursuit of cost-effective, high-performance solutions for sectors such as aerospace, automotive, and energy storage.
Key players in the graphene composites space are attracting significant capital to expand manufacturing capacity and accelerate commercialization. Directa Plus, a leading European graphene producer, has continued to secure funding to scale up its proprietary production processes and deepen its partnerships with global manufacturers in textiles, rubber, and composites. Similarly, First Graphene, based in Australia, has announced new investment rounds in 2025 to support the expansion of its high-shear exfoliation technology, which is central to producing bulk quantities of graphene for composite applications.
Strategic partnerships are also shaping the landscape. Haydale Graphene Industries has entered into multiple joint development agreements with major chemical and materials companies to co-develop graphene-enhanced resins and thermoplastics, targeting automotive and aerospace markets. These collaborations are designed to accelerate the qualification and adoption of graphene composites in high-value sectors, leveraging Haydale’s patented functionalization technology.
M&A activity is intensifying as established chemical and advanced materials companies seek to acquire or invest in graphene specialists to secure access to intellectual property and production know-how. For example, Vorbeck Materials in the United States has been the subject of acquisition interest from multinational chemical conglomerates aiming to integrate graphene composites into their product portfolios. Meanwhile, Graphenea, a prominent European graphene manufacturer, has expanded its strategic alliances with both upstream suppliers and downstream composite fabricators, positioning itself as a key node in the global supply chain.
Looking ahead, the outlook for investment and partnership activity in high-strength graphene composites manufacturing remains robust. The sector is expected to see further consolidation as companies seek to achieve economies of scale and secure market share. Additionally, cross-sector partnerships—particularly with automotive OEMs and aerospace primes—are anticipated to intensify, as end-users push for the integration of graphene composites into next-generation lightweight structures and energy systems. The ongoing influx of capital and collaborative ventures is set to accelerate the transition of graphene composites from pilot-scale to mainstream industrial adoption over the next several years.
Future Outlook: Disruptive Innovations and Long-Term Opportunities
The future of high-strength graphene composites manufacturing is poised for significant transformation as the industry moves into 2025 and beyond. The convergence of scalable production methods, advanced material integration, and expanding end-use applications is expected to drive disruptive innovations and open long-term opportunities across multiple sectors.
One of the most promising developments is the maturation of large-scale graphene production technologies. Companies such as Directa Plus and First Graphene are investing in proprietary processes to deliver high-purity graphene nanoplatelets and powders at industrial volumes. These advancements are critical for enabling the consistent supply of graphene required for composite manufacturing, particularly in automotive, aerospace, and energy storage applications.
In 2025, the integration of graphene into polymer, metal, and ceramic matrices is expected to become more sophisticated, with a focus on optimizing dispersion and interfacial bonding. Haydale Graphene Industries is actively developing functionalized graphene additives that enhance mechanical strength, electrical conductivity, and thermal stability in composite materials. Their work is paving the way for next-generation lightweight components with superior performance characteristics.
Automotive and aerospace manufacturers are increasingly collaborating with graphene suppliers to co-develop structural parts and coatings. For example, G6 Materials is working on graphene-enhanced resins and adhesives, targeting applications that demand high strength-to-weight ratios and improved durability. These partnerships are expected to accelerate the commercialization of graphene composites in critical load-bearing and protective components.
Looking ahead, the industry anticipates breakthroughs in automated manufacturing techniques, such as additive manufacturing (3D printing) of graphene-reinforced composites. This approach promises to unlock complex geometries and tailored material properties, further expanding the design space for engineers. Companies like Graphenea are exploring the integration of graphene into printable inks and filaments, which could revolutionize rapid prototyping and on-demand production.
Sustainability and circularity are also emerging as key drivers. The recyclability of graphene composites and the use of bio-based matrices are under active investigation, with the goal of reducing environmental impact and supporting green manufacturing initiatives. Industry bodies and consortia are expected to play a pivotal role in establishing standards and best practices for safe, responsible deployment of graphene materials.
Overall, the outlook for high-strength graphene composites manufacturing is highly optimistic. As production costs decrease and technical barriers are overcome, the adoption of these advanced materials is set to accelerate, unlocking new markets and enabling disruptive innovations across transportation, infrastructure, energy, and beyond.
Sources & References
- Directa Plus
- First Graphene
- Lockheed Martin
- Airbus
- Versarien
- Haydale Graphene Industries
- G6 Materials
- Arkema
- Cabot Corporation
- Boeing
- Toray Industries
- ISO
- ASTM International
- Advanced Graphene Products