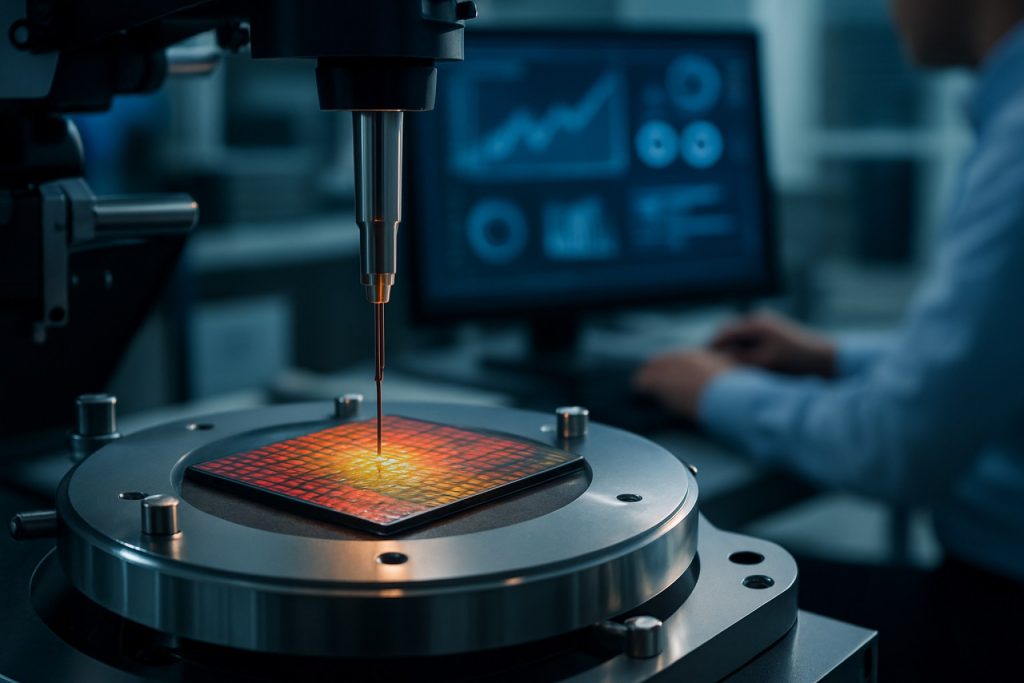
Revolutionizing MEMS Reliability: How Vibration-Based Testing Will Transform Microelectromechanical Systems in 2025 and Beyond. Explore the Next Wave of Precision, Performance, and Market Expansion.
- Executive Summary: Key Trends and Market Drivers in 2025
- Overview of Vibration-Based Testing for MEMS: Principles and Applications
- Current Market Landscape: Leading Players and Regional Hotspots
- Technological Innovations: Advanced Sensors, AI, and Automation in MEMS Testing
- Regulatory Standards and Industry Guidelines (e.g., IEEE, ASME)
- Market Forecast 2025–2030: Growth Projections and Revenue Opportunities
- Emerging Use Cases: Automotive, Medical Devices, Consumer Electronics, and More
- Challenges and Barriers: Technical, Economic, and Supply Chain Considerations
- Competitive Analysis: Strategies of Key Manufacturers and Solution Providers
- Future Outlook: Next-Gen MEMS Testing and Long-Term Industry Impact
- Sources & References
Executive Summary: Key Trends and Market Drivers in 2025
Vibration-based testing is emerging as a critical quality assurance and reliability assessment method for microelectromechanical systems (MEMS) in 2025, driven by the increasing integration of MEMS devices in automotive, consumer electronics, industrial, and medical applications. As MEMS components become more complex and miniaturized, ensuring their mechanical robustness and operational stability under real-world vibration conditions is paramount. This has led to a surge in demand for advanced vibration testing solutions tailored to the unique requirements of MEMS devices.
Key trends shaping the market in 2025 include the adoption of highly sensitive, automated vibration test platforms capable of simulating a wide range of environmental conditions. Leading MEMS manufacturers and test equipment suppliers are investing in systems that offer precise control over frequency, amplitude, and multi-axis excitation, enabling comprehensive fatigue and resonance analysis. For instance, Bosch, a global leader in MEMS sensor production, continues to emphasize rigorous vibration qualification protocols to meet the stringent reliability standards of automotive and industrial clients. Similarly, STMicroelectronics and Analog Devices are advancing their in-house and partner-based vibration testing capabilities to support the growing deployment of MEMS in safety-critical and high-performance applications.
The proliferation of MEMS in electric vehicles (EVs), autonomous systems, and wearable health devices is a major market driver, as these applications demand exceptional durability and consistent performance under dynamic mechanical stress. Automotive OEMs and Tier 1 suppliers are increasingly specifying advanced vibration test requirements for MEMS-based inertial sensors, pressure sensors, and microphones, pushing the supply chain to adopt more sophisticated test methodologies. Industry bodies such as the Semiconductor Industry Association and MEMS & Sensors Industry Group are also promoting best practices and standardization efforts to harmonize vibration testing protocols across the sector.
Looking ahead, the outlook for vibration-based MEMS testing is robust, with continued innovation expected in test automation, data analytics, and digital twin modeling. Companies are exploring machine learning algorithms to interpret vibration test data, enabling predictive maintenance and faster failure analysis. The expansion of 5G, IoT, and edge computing will further accelerate MEMS adoption, reinforcing the need for reliable vibration testing infrastructure. As a result, the sector is poised for sustained growth, with leading players and technology providers investing in next-generation solutions to address evolving market and regulatory demands.
Overview of Vibration-Based Testing for MEMS: Principles and Applications
Vibration-based testing has become a cornerstone in the quality assurance and reliability assessment of microelectromechanical systems (MEMS), which are increasingly integral to automotive, consumer electronics, medical, and industrial applications. As MEMS devices continue to shrink in size while expanding in functionality, ensuring their robustness against mechanical stresses is critical. Vibration-based testing involves subjecting MEMS components to controlled vibrational stimuli to evaluate their mechanical integrity, performance stability, and failure thresholds.
The principles of vibration-based testing for MEMS are rooted in simulating real-world operational environments. MEMS devices, such as accelerometers, gyroscopes, and pressure sensors, are often exposed to vibrations during transportation, assembly, and end-use. Testing protocols typically include sinusoidal, random, and shock vibration profiles, with parameters tailored to the device’s intended application. The goal is to identify potential failure modes, such as stiction, fatigue, or fracture, and to validate device packaging and mounting strategies.
In 2025, the adoption of vibration-based testing is being driven by the proliferation of MEMS in safety-critical sectors. For example, the automotive industry relies on MEMS accelerometers and gyroscopes for airbag deployment and stability control systems, necessitating rigorous vibration qualification. Leading MEMS manufacturers such as STMicroelectronics, Bosch, and Analog Devices have established in-house vibration testing protocols that comply with international standards like JEDEC and AEC-Q100. These companies operate advanced test laboratories equipped with electrodynamic shakers, laser Doppler vibrometers, and high-speed data acquisition systems to monitor device response in real time.
Recent advancements include the integration of machine learning algorithms to analyze vibration test data, enabling predictive maintenance and early detection of latent defects. Additionally, the miniaturization of test fixtures and the development of wafer-level vibration testing are streamlining high-throughput screening, which is essential for the mass production of MEMS devices. Suppliers of test equipment, such as Brüel & Kjær and MTS Systems, are collaborating with MEMS foundries to develop customized solutions that address the unique challenges of MEMS scale and sensitivity.
Looking ahead, the outlook for vibration-based MEMS testing is shaped by the growing demand for reliability in emerging applications, including autonomous vehicles, wearable health monitors, and industrial IoT sensors. As MEMS devices become more complex and are deployed in harsher environments, the industry is expected to see further innovation in test methodologies, automation, and data analytics, ensuring that MEMS technology continues to meet stringent performance and safety requirements.
Current Market Landscape: Leading Players and Regional Hotspots
The market for vibration-based testing in microelectromechanical systems (MEMS) is experiencing robust growth in 2025, driven by the increasing integration of MEMS devices in automotive, consumer electronics, industrial automation, and medical applications. Vibration-based testing is critical for ensuring the reliability and performance of MEMS devices, which are often subjected to dynamic mechanical stresses during operation. The current landscape is shaped by a mix of established global players, innovative regional firms, and a concentration of activity in key geographic hotspots.
Among the leading companies, Robert Bosch GmbH stands out as a dominant force, leveraging its extensive MEMS manufacturing capabilities and in-house testing infrastructure. Bosch’s MEMS sensors are widely used in automotive safety systems and consumer electronics, and the company continues to invest in advanced vibration testing protocols to meet stringent quality standards. Another major player, STMicroelectronics, operates large MEMS production facilities in Europe and Asia, with a strong focus on vibration and shock testing for inertial sensors and microphones. Analog Devices, Inc. is also prominent, particularly in the industrial and aerospace sectors, where its MEMS accelerometers and gyroscopes undergo rigorous vibration qualification to ensure reliability in harsh environments.
In the United States, Texas Instruments and Honeywell International Inc. are key contributors, with Honeywell’s MEMS-based inertial measurement units (IMUs) and pressure sensors being subjected to comprehensive vibration testing for aerospace and defense applications. TDK Corporation, through its subsidiary InvenSense, is a significant player in Asia, supplying MEMS motion sensors for smartphones and wearables, and investing in advanced vibration test systems to ensure product durability.
Regionally, Asia-Pacific remains the largest and fastest-growing market, with China, Japan, South Korea, and Taiwan hosting major MEMS foundries and test service providers. The presence of leading semiconductor manufacturers and a robust electronics supply chain has made the region a hotspot for both MEMS production and associated vibration testing services. Europe, led by Germany and France, is notable for its automotive and industrial MEMS applications, while North America maintains a strong position in aerospace, defense, and medical MEMS testing.
Looking ahead, the market is expected to see further advancements in automated vibration test equipment, data analytics, and simulation tools, as companies strive to reduce test cycle times and improve fault detection. Strategic collaborations between MEMS manufacturers and specialized test equipment suppliers are likely to intensify, particularly in regions with high demand for next-generation sensors and actuators.
Technological Innovations: Advanced Sensors, AI, and Automation in MEMS Testing
Vibration-based testing has become a cornerstone in the quality assurance and reliability assessment of microelectromechanical systems (MEMS), especially as these devices proliferate in automotive, medical, consumer electronics, and industrial applications. In 2025, the sector is witnessing a convergence of advanced sensor technologies, artificial intelligence (AI), and automation, fundamentally reshaping how MEMS vibration testing is conducted.
Leading MEMS manufacturers and test equipment suppliers are integrating high-precision piezoelectric and capacitive sensors into their vibration test platforms. These sensors offer enhanced sensitivity and bandwidth, enabling the detection of minute mechanical anomalies and failure precursors in MEMS devices. For instance, Robert Bosch GmbH, a global leader in MEMS production, continues to refine its in-house vibration testing protocols, leveraging proprietary sensor arrays to ensure the robustness of automotive and consumer MEMS components.
Automation is another key trend, with robotic handlers and automated test cells now standard in high-throughput MEMS production lines. Companies such as Teradyne and Advantest are deploying automated MEMS test systems capable of executing complex vibration profiles, real-time data acquisition, and adaptive test sequencing. These systems reduce human error, increase throughput, and enable 24/7 operation, which is critical as MEMS volumes continue to rise.
Artificial intelligence and machine learning are being harnessed to analyze the vast datasets generated during vibration testing. AI-driven analytics can identify subtle patterns and predict device failures with greater accuracy than traditional statistical methods. STMicroelectronics, a major MEMS supplier, is actively exploring AI-enhanced test algorithms to improve yield and reliability, particularly for safety-critical applications such as automotive inertial sensors.
Looking ahead, the next few years are expected to bring further integration of edge computing and digital twin technologies into MEMS vibration testing. Digital twins—virtual replicas of physical MEMS devices—will allow for real-time simulation and predictive maintenance, reducing the need for destructive testing. Additionally, the adoption of Industry 4.0 standards is fostering greater interoperability between test equipment, manufacturing execution systems, and enterprise data platforms, as seen in initiatives by Infineon Technologies and other major players.
In summary, the landscape of vibration-based MEMS testing in 2025 is defined by the synergy of advanced sensors, AI, and automation. These innovations are driving higher reliability, faster time-to-market, and lower costs, positioning MEMS for even broader adoption across emerging sectors in the coming years.
Regulatory Standards and Industry Guidelines (e.g., IEEE, ASME)
Vibration-based testing is a critical process in the qualification and reliability assessment of Microelectromechanical Systems (MEMS), especially as these devices are increasingly deployed in safety-critical and high-performance applications such as automotive, aerospace, and medical devices. As of 2025, regulatory standards and industry guidelines governing vibration testing for MEMS are evolving to address the unique challenges posed by the miniaturized and highly integrated nature of these systems.
The IEEE has played a central role in establishing baseline standards for MEMS testing, including vibration protocols. The IEEE 2700-2017 standard, which defines a common sensor performance parameter terminology, remains a reference point, but ongoing working groups are expected to update and expand these guidelines to reflect advances in MEMS technology and the increasing complexity of multi-axis sensors. The IEEE Standards Association continues to facilitate collaboration between industry stakeholders to ensure that vibration testing methodologies remain relevant and robust.
Similarly, the ASME (American Society of Mechanical Engineers) has contributed to the development of mechanical testing standards, including those relevant to MEMS. ASME’s MEMS Division is actively engaged in discussions around the harmonization of vibration test procedures, particularly as MEMS devices are integrated into mission-critical systems. The focus is on ensuring that test conditions accurately simulate real-world operational environments, including high-frequency and multi-axis vibration profiles.
In the automotive sector, the International Electrotechnical Commission (IEC) and the International Organization for Standardization (ISO) have published standards such as IEC 60068-2-6 and ISO 16750-3, which are widely referenced for environmental and mechanical testing of electronic components, including MEMS. These standards are being reviewed and updated to address the specific failure modes and sensitivities of MEMS devices, with input from leading MEMS manufacturers and automotive suppliers.
Major MEMS manufacturers, such as STMicroelectronics, Bosch, and Analog Devices, are actively participating in standardization efforts and often publish their own internal qualification protocols that meet or exceed industry requirements. These companies are also collaborating with standards bodies to ensure that new guidelines reflect the latest technological advancements and field data.
Looking ahead, the next few years are expected to see increased convergence between international standards and industry best practices, driven by the proliferation of MEMS in safety- and mission-critical applications. There is a growing emphasis on digital traceability, data-driven qualification, and the integration of machine learning for anomaly detection during vibration testing. Regulatory bodies and industry consortia are likely to formalize these trends into updated standards, ensuring that MEMS devices continue to meet stringent reliability and safety requirements in increasingly demanding environments.
Market Forecast 2025–2030: Growth Projections and Revenue Opportunities
The market for vibration-based testing in Microelectromechanical Systems (MEMS) is poised for robust growth between 2025 and 2030, driven by escalating demand for high-reliability MEMS devices in automotive, consumer electronics, industrial automation, and medical sectors. As MEMS components become increasingly integral to safety-critical applications—such as automotive airbag sensors, inertial measurement units (IMUs), and medical implants—manufacturers are intensifying their focus on advanced testing methodologies to ensure device durability and performance under real-world vibration conditions.
Industry leaders such as Robert Bosch GmbH, a pioneer in MEMS sensor manufacturing, and STMicroelectronics, a major supplier of MEMS accelerometers and gyroscopes, are investing in state-of-the-art vibration testing infrastructure. These companies are integrating automated, high-throughput vibration test systems into their production lines to meet stringent quality standards and regulatory requirements. The adoption of such systems is expected to accelerate, particularly as MEMS devices proliferate in electric vehicles (EVs), advanced driver-assistance systems (ADAS), and next-generation smartphones.
According to recent industry announcements, Analog Devices, Inc. is expanding its MEMS testing capabilities to address the growing complexity of multi-axis sensors and the need for comprehensive vibration characterization. Similarly, Texas Instruments is enhancing its MEMS quality assurance protocols, emphasizing vibration and shock testing to support the reliability demands of industrial and automotive clients.
From a revenue perspective, the vibration-based MEMS testing market is projected to experience a compound annual growth rate (CAGR) in the high single digits through 2030, with total market value expected to surpass several hundred million USD by the end of the forecast period. This growth is underpinned by the increasing volume of MEMS devices produced globally and the rising adoption of automated test equipment (ATE) from specialized suppliers such as Teradyne and Rohde & Schwarz, both of which are expanding their offerings to include MEMS-specific vibration and environmental test solutions.
Looking ahead, the market outlook remains positive as MEMS technology continues to evolve, with miniaturization and integration trends necessitating even more rigorous vibration testing. The emergence of new application areas—such as wearable health monitors, smart infrastructure, and autonomous robotics—will further expand revenue opportunities for test equipment manufacturers and MEMS foundries alike. Strategic partnerships between MEMS designers, test equipment providers, and end-users are expected to drive innovation in vibration-based testing methodologies, ensuring that MEMS devices meet the reliability standards of tomorrow’s connected world.
Emerging Use Cases: Automotive, Medical Devices, Consumer Electronics, and More
Vibration-based testing is rapidly gaining traction as a critical quality assurance and reliability assessment method for microelectromechanical systems (MEMS) across diverse industries. As MEMS devices become increasingly integral to automotive safety, medical diagnostics, and consumer electronics, the demand for robust, high-throughput vibration testing solutions is accelerating in 2025 and is expected to intensify over the next several years.
In the automotive sector, MEMS accelerometers, gyroscopes, and pressure sensors are foundational to advanced driver-assistance systems (ADAS), airbag deployment, and vehicle stability controls. Leading automotive suppliers such as Bosch and Continental have integrated vibration-based testing into their MEMS production lines to ensure sensor reliability under harsh operational conditions, including extreme temperature fluctuations and mechanical shocks. The shift toward electric and autonomous vehicles is further amplifying the need for rigorous vibration qualification, as these vehicles rely on a greater number of MEMS-based sensors for navigation and safety.
In medical devices, MEMS are increasingly used in implantable sensors, drug delivery systems, and diagnostic equipment. Companies like STMicroelectronics and Analog Devices are advancing MEMS solutions for medical applications, where vibration-based testing is essential to validate device performance and longevity, especially for devices exposed to patient movement or external vibrations. Regulatory scrutiny is also driving the adoption of standardized vibration testing protocols to ensure patient safety and device efficacy.
Consumer electronics represent another major growth area. MEMS microphones, inertial measurement units (IMUs), and environmental sensors are ubiquitous in smartphones, wearables, and smart home devices. Companies such as Infineon Technologies and TDK Corporation are investing in advanced vibration testing platforms to support high-volume MEMS production, focusing on miniaturization and multi-axis vibration testing to simulate real-world usage scenarios. The proliferation of augmented reality (AR) and virtual reality (VR) devices is expected to further boost demand for MEMS vibration testing, as these applications require precise motion sensing and robust reliability.
Looking ahead, the next few years will likely see the emergence of new use cases in industrial automation, aerospace, and environmental monitoring, where MEMS devices must withstand increasingly complex vibration profiles. Industry leaders are collaborating with equipment manufacturers to develop automated, high-throughput vibration test systems capable of supporting the evolving requirements of MEMS innovation. As MEMS technology continues to advance, vibration-based testing will remain a cornerstone of quality assurance, enabling the deployment of reliable, high-performance devices across critical applications.
Challenges and Barriers: Technical, Economic, and Supply Chain Considerations
Vibration-based testing is a critical process in the quality assurance and reliability assessment of microelectromechanical systems (MEMS), but the sector faces a range of technical, economic, and supply chain challenges as it moves through 2025 and into the coming years. These barriers are shaped by the increasing complexity of MEMS devices, the demand for higher throughput, and the evolving global supply landscape.
Technical Challenges remain at the forefront. MEMS devices are becoming more miniaturized and integrated, with complex multi-axis sensing and actuation functions. This miniaturization complicates the application of vibration stimuli and the accurate measurement of device responses. High-frequency and multi-axis vibration testing, essential for automotive and aerospace MEMS, requires advanced shakers and fixturing systems that can introduce and measure vibrations without introducing artifacts or damaging delicate structures. Leading MEMS manufacturers such as STMicroelectronics and Bosch are investing in custom test platforms and digital twins to simulate and validate vibration profiles, but the lack of standardized test protocols for emerging MEMS types remains a bottleneck.
Economic Barriers are also significant. The capital expenditure for state-of-the-art vibration test equipment, including high-precision shakers, laser Doppler vibrometers, and automated handling systems, is substantial. For example, companies like Texas Instruments and Analog Devices must balance the cost of in-house testing infrastructure with the option of outsourcing to specialized test houses. The need for high-throughput, parallel testing to meet the volume demands of consumer electronics and automotive sectors further drives up costs. Smaller MEMS foundries and fabless design houses may struggle to justify these investments, potentially limiting innovation and market entry.
Supply Chain Considerations have become more pronounced in the wake of global disruptions. The MEMS testing ecosystem relies on a network of equipment suppliers, such as Kistler and Brüel & Kjær, for vibration test systems and sensors. Lead times for critical components, including piezoelectric actuators and high-precision motion stages, have lengthened due to semiconductor supply constraints and geopolitical factors. Additionally, the push for regionalization and onshoring of MEMS manufacturing in the US, Europe, and Asia is leading to fragmented supply chains, with varying access to advanced test technologies.
Looking ahead, the sector is expected to address these challenges through increased collaboration on test standards, investment in modular and scalable test platforms, and the integration of AI-driven data analytics for faster failure detection. However, the pace of MEMS innovation may continue to outstrip the evolution of vibration-based testing capabilities, making this a persistent area of focus for industry leaders and suppliers.
Competitive Analysis: Strategies of Key Manufacturers and Solution Providers
The competitive landscape for vibration-based testing in the MEMS sector is characterized by a blend of established instrumentation manufacturers, MEMS device producers, and specialized solution providers. As MEMS applications proliferate in automotive, consumer electronics, medical, and industrial domains, the demand for advanced, high-throughput, and highly sensitive vibration testing solutions is intensifying. In 2025 and the coming years, several strategic trends and initiatives are shaping the approaches of key players.
Leading instrumentation companies such as Keysight Technologies and National Instruments are leveraging their expertise in precision measurement and modular test systems to offer scalable vibration testing platforms. These companies are focusing on integrating real-time data analytics, automation, and machine learning capabilities to enable faster fault detection and predictive maintenance for MEMS devices. Their solutions are increasingly compatible with Industry 4.0 environments, supporting remote monitoring and cloud-based data management.
MEMS device manufacturers, including STMicroelectronics and Bosch, are investing in in-house and collaborative development of custom vibration test protocols tailored to their specific sensor and actuator designs. These companies are prioritizing the miniaturization of test fixtures and the adoption of wafer-level testing to reduce costs and accelerate time-to-market. Strategic partnerships with test equipment suppliers are common, enabling co-development of application-specific solutions that address the unique mechanical and environmental stresses encountered by MEMS in end-use scenarios.
Specialized solution providers such as Polytec and Brüel & Kjær (now part of HBK) are differentiating themselves through advanced laser Doppler vibrometry and non-contact measurement technologies. These firms are expanding their product portfolios to support high-frequency, high-resolution testing required for next-generation MEMS, including those used in LiDAR, inertial navigation, and biomedical implants. Their strategies include enhancing software suites for automated data interpretation and compliance with evolving international standards.
Across the sector, there is a notable emphasis on sustainability and energy efficiency in test operations, as well as on the development of open interfaces for interoperability with broader manufacturing execution systems. The competitive outlook for 2025 and beyond suggests that companies able to deliver flexible, high-throughput, and data-driven vibration testing solutions—while supporting rapid MEMS innovation cycles—will maintain a strong market position. Ongoing investments in R&D, ecosystem partnerships, and digital transformation are expected to further intensify competition among leading manufacturers and solution providers.
Future Outlook: Next-Gen MEMS Testing and Long-Term Industry Impact
The future of vibration-based testing for Microelectromechanical Systems (MEMS) is poised for significant transformation as the industry moves into 2025 and beyond. As MEMS devices become increasingly integral to automotive safety, consumer electronics, medical devices, and industrial automation, the demand for robust, high-throughput, and highly sensitive testing methodologies is intensifying. Vibration-based testing, which evaluates the mechanical and dynamic reliability of MEMS components under simulated operational stresses, is at the forefront of this evolution.
Leading MEMS manufacturers and test equipment suppliers are investing in next-generation vibration test platforms that offer higher frequency ranges, improved automation, and real-time data analytics. For example, Bosch, a global leader in MEMS sensor production, is actively developing advanced test protocols to ensure the reliability of their automotive and consumer MEMS sensors, particularly as these devices are increasingly deployed in safety-critical applications such as autonomous vehicles and medical monitoring. Similarly, STMicroelectronics is expanding its MEMS testing capabilities to address the growing complexity and miniaturization of sensors, with a focus on multi-axis vibration testing and machine learning-driven fault detection.
On the equipment side, companies like Teradyne and National Instruments are introducing modular, scalable vibration test systems that integrate seamlessly with automated production lines. These systems are designed to handle the increasing test volumes associated with high-volume MEMS manufacturing, while also providing the flexibility to adapt to new device architectures and test standards. The integration of artificial intelligence and edge computing into test platforms is expected to further enhance defect detection rates and reduce false positives, a critical factor as MEMS devices become more complex and their failure modes more subtle.
Industry bodies such as the SEMI are also playing a pivotal role by developing standardized vibration test protocols and reliability benchmarks, facilitating interoperability and quality assurance across the global MEMS supply chain. As regulatory requirements tighten—especially in automotive and medical sectors—compliance with these standards will become a key differentiator for MEMS manufacturers.
Looking ahead, the convergence of advanced vibration-based testing, automation, and data analytics is expected to drive down test costs, improve device yields, and accelerate time-to-market for next-generation MEMS products. The long-term industry impact will likely include greater reliability and safety in end-use applications, expanded adoption of MEMS in emerging fields such as IoT and wearable health, and a more resilient, innovation-driven MEMS ecosystem.
Sources & References
- Bosch
- STMicroelectronics
- Analog Devices
- Semiconductor Industry Association
- Brüel & Kjær
- MTS Systems
- Texas Instruments
- Honeywell International Inc.
- Advantest
- Infineon Technologies
- IEEE
- ASME
- International Organization for Standardization (ISO)
- Rohde & Schwarz
- National Instruments
- Polytec