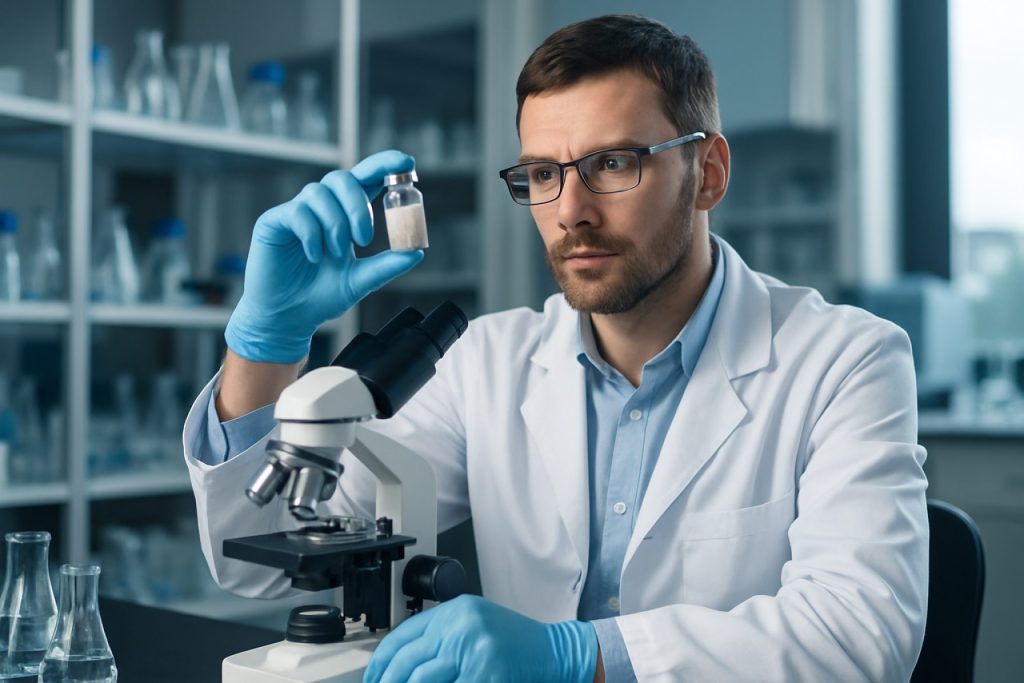
Zeolite Functionalization Engineering in 2025: Transforming Catalysis, Sustainability, and Industrial Performance. Explore How Next-Gen Zeolites Are Redefining Material Science and Market Opportunities.
- Executive Summary: Key Trends and Market Drivers in Zeolite Functionalization
- Global Market Forecasts (2025–2029): Growth, Demand, and Regional Hotspots
- Technological Innovations: New Methods and Functionalization Techniques
- Emerging Applications: Catalysis, Environmental Remediation, and Beyond
- Competitive Landscape: Leading Companies and Strategic Partnerships
- Sustainability and Green Chemistry: Zeolites in Circular Economy Initiatives
- Regulatory Environment and Industry Standards (2025 Update)
- Challenges and Barriers: Scalability, Cost, and Technical Hurdles
- Case Studies: Industrial Deployments and Performance Metrics
- Future Outlook: Disruptive Opportunities and R&D Roadmap to 2030
- Sources & References
Executive Summary: Key Trends and Market Drivers in Zeolite Functionalization
Zeolite functionalization engineering is rapidly evolving as a cornerstone technology in catalysis, environmental remediation, and advanced materials, with 2025 marking a pivotal year for both innovation and commercialization. The sector is witnessing a surge in demand for tailored zeolite materials, driven by the need for higher selectivity, stability, and efficiency in industrial processes. Key trends include the integration of hierarchical porosity, post-synthetic modification, and the incorporation of heteroatoms to enhance catalytic and adsorptive properties.
Major chemical and materials companies are intensifying their focus on zeolite functionalization. BASF, a global leader in chemical manufacturing, continues to expand its portfolio of functionalized zeolites for applications in petrochemical refining and emission control. Their recent investments in R&D facilities underscore a commitment to developing next-generation zeolite catalysts with improved hydrothermal stability and tailored acidity. Similarly, Zeochem, a prominent supplier of molecular sieves and zeolites, is advancing the customization of zeolite frameworks for gas separation and purification, leveraging proprietary post-synthetic modification techniques.
The push for sustainability is a significant market driver, with regulatory pressures and corporate ESG goals accelerating the adoption of zeolite-based solutions for environmental applications. Honeywell is actively engineering functionalized zeolites for use in air purification and industrial emissions abatement, targeting stricter global standards for NOx and VOC reduction. In parallel, Clariant is developing zeolite catalysts with enhanced selectivity for green chemistry processes, including bio-based feedstock conversion and plastic recycling.
On the technology front, advances in computational modeling and high-throughput experimentation are enabling faster screening and optimization of zeolite functionalization strategies. The adoption of machine learning tools is expected to further accelerate the discovery of novel zeolite structures with bespoke properties, supporting the rapid prototyping of materials for emerging applications such as CO2 capture and hydrogen storage.
Looking ahead, the outlook for zeolite functionalization engineering is robust. Industry analysts anticipate continued growth in demand across sectors such as clean energy, specialty chemicals, and environmental management. Strategic collaborations between manufacturers, end-users, and research institutions are likely to yield new commercial products and scalable processes over the next few years, solidifying zeolite functionalization as a key enabler of sustainable industrial transformation.
Global Market Forecasts (2025–2029): Growth, Demand, and Regional Hotspots
The global market for zeolite functionalization engineering is poised for robust growth between 2025 and 2029, driven by escalating demand for advanced materials in catalysis, environmental remediation, and specialty separations. Zeolite functionalization—modifying the surface or framework of zeolites to impart tailored properties—has become a focal point for industries seeking higher efficiency and selectivity in chemical processes. The market is expected to benefit from both established and emerging applications, with significant investments in research and commercialization.
In 2025, the Asia-Pacific region is projected to remain the largest and fastest-growing market for functionalized zeolites, underpinned by rapid industrialization, environmental regulations, and the expansion of petrochemical and refining sectors. China, in particular, continues to invest heavily in zeolite-based technologies for air and water purification, as well as for advanced catalytic processes. Major regional players such as ChemChina and Sinopec are actively scaling up production capacities and collaborating with research institutes to develop next-generation zeolite materials.
Europe is also witnessing increased demand, especially in the context of the European Green Deal and stricter emission standards. Companies like BASF and Evonik Industries are at the forefront, leveraging their expertise in specialty chemicals to engineer zeolites with enhanced adsorption and catalytic properties. These efforts are aimed at supporting sustainable manufacturing, waste valorization, and the circular economy.
In North America, the United States remains a key innovation hub, with firms such as Honeywell and UOP (a Honeywell company) focusing on functionalized zeolites for refining, gas separation, and emission control. The region’s growth is further supported by government initiatives promoting clean energy and advanced materials research.
Looking ahead to 2029, the global market is expected to see compound annual growth rates in the high single digits, with total market value potentially surpassing several billion USD. Hotspots for demand will include not only traditional sectors like petrochemicals and environmental technologies but also emerging fields such as green hydrogen production, CO2 capture, and pharmaceutical synthesis. The competitive landscape will likely intensify as new entrants and established players invest in proprietary functionalization techniques and scale up pilot projects to commercial production.
Overall, the outlook for zeolite functionalization engineering is marked by technological innovation, regional diversification, and a strong alignment with global sustainability goals, positioning the sector for sustained expansion through 2029.
Technological Innovations: New Methods and Functionalization Techniques
Zeolite functionalization engineering is experiencing rapid technological advancements in 2025, driven by the need for tailored materials in catalysis, adsorption, and environmental applications. The focus has shifted from traditional post-synthetic modification to more precise, scalable, and sustainable methods that enable the fine-tuning of zeolite properties at the molecular level.
One of the most significant innovations is the adoption of one-pot synthesis techniques, which allow for the direct incorporation of functional groups or heteroatoms during zeolite crystallization. This approach enhances the uniformity and stability of the functional sites, reducing the need for energy-intensive post-synthetic treatments. Companies such as BASF and Zeochem are actively developing proprietary synthesis routes that integrate transition metals, organic moieties, or hierarchical porosity, targeting applications in selective catalysis and gas separation.
Another emerging trend is the use of template-free and green synthesis methods. These processes minimize the use of organic structure-directing agents (OSDAs), lowering both cost and environmental impact. Tosoh Corporation, a major zeolite manufacturer, has reported progress in template-free synthesis for industrial-scale production, aiming to meet stricter sustainability standards and regulatory requirements.
Surface functionalization via advanced grafting and anchoring techniques is also gaining momentum. The development of robust silanation and metalation protocols enables the introduction of acid, base, or redox-active sites with high dispersion and accessibility. Honeywell and Evonik Industries are investing in surface engineering technologies to produce zeolites with enhanced selectivity for volatile organic compound (VOC) removal and CO2 capture.
In parallel, hierarchical zeolite engineering—the creation of multi-level pore structures—remains a key area of innovation. By combining micro-, meso-, and macroporosity, manufacturers are overcoming diffusion limitations and improving catalyst lifetimes. Clariant has introduced commercial zeolite products with engineered porosity, targeting the petrochemical and fine chemical sectors.
Looking ahead, the integration of machine learning and high-throughput experimentation is expected to accelerate the discovery of novel functionalized zeolites. Industry leaders are collaborating with academic institutions to develop predictive models for property optimization, aiming to shorten development cycles and address emerging challenges in energy, environment, and health.
Overall, the next few years will likely see the commercialization of more sophisticated, application-specific zeolite materials, underpinned by advances in functionalization engineering and a strong emphasis on sustainability and process efficiency.
Emerging Applications: Catalysis, Environmental Remediation, and Beyond
Zeolite functionalization engineering is rapidly advancing, enabling a new generation of materials with tailored properties for emerging applications in catalysis, environmental remediation, and beyond. As of 2025, the focus has shifted from traditional zeolite synthesis to precise post-synthetic modifications, such as ion-exchange, surface grafting, and incorporation of heteroatoms, to enhance selectivity, activity, and stability in demanding environments.
In catalysis, functionalized zeolites are increasingly deployed for sustainable chemical transformations. Companies like BASF and Zeochem are at the forefront, developing zeolite-based catalysts with engineered acid sites and metal centers for applications in petrochemical refining, biomass conversion, and emission control. For instance, the integration of transition metals (e.g., Cu, Fe) into zeolite frameworks has led to highly efficient catalysts for selective catalytic reduction (SCR) of NOx, a critical process for meeting stringent emission standards in automotive and industrial sectors. The trend toward single-atom and bimetallic site engineering is expected to accelerate, with pilot-scale demonstrations anticipated by 2026.
Environmental remediation is another area witnessing significant breakthroughs. Functionalized zeolites are being tailored for the selective adsorption and degradation of emerging contaminants, such as per- and polyfluoroalkyl substances (PFAS), heavy metals, and pharmaceutical residues. Honeywell and Clariant are actively commercializing zeolite adsorbents with modified pore structures and surface chemistries to address water and air purification challenges. Recent data indicate that these materials can achieve removal efficiencies exceeding 95% for specific contaminants, with ongoing field trials in municipal and industrial settings. The next few years are expected to see the integration of multifunctional zeolites into modular treatment systems, enhancing scalability and cost-effectiveness.
Beyond catalysis and remediation, zeolite functionalization is opening new frontiers in energy storage, gas separation, and sensor technologies. Companies such as Tosoh Corporation and Arkema are exploring hybrid zeolite composites for advanced battery electrodes and selective CO2 capture. The ability to fine-tune hydrophilicity, redox properties, and framework flexibility is driving innovation in these sectors. Looking ahead, the convergence of machine learning-guided design and scalable manufacturing is poised to accelerate the commercialization of next-generation functionalized zeolites, with significant impact expected across clean energy, environmental, and chemical industries by 2027.
Competitive Landscape: Leading Companies and Strategic Partnerships
The competitive landscape of zeolite functionalization engineering in 2025 is characterized by a dynamic interplay between established chemical giants, specialized material innovators, and a growing number of strategic partnerships aimed at accelerating the commercialization of advanced zeolite-based solutions. As demand surges for tailored zeolites in applications such as catalysis, gas separation, environmental remediation, and sustainable chemical processes, companies are intensifying their focus on proprietary functionalization techniques and collaborative R&D.
Among the global leaders, BASF continues to leverage its extensive expertise in zeolite synthesis and modification, with a strong emphasis on catalytic applications for refining, petrochemicals, and emissions control. BASF’s ongoing investments in process intensification and surface functionalization are aimed at enhancing selectivity and stability, particularly for next-generation hydrocarbon processing and environmental catalysts.
Honeywell, through its UOP division, remains a key player in zeolite engineering, focusing on molecular sieves and custom zeolite formulations for gas processing, air purification, and industrial separations. Honeywell’s recent collaborations with energy and environmental technology firms underscore its commitment to developing zeolites with tailored pore structures and surface chemistries for carbon capture and hydrogen purification.
In Asia, Tosoh Corporation and ChemChina are expanding their portfolios of functionalized zeolites, targeting both traditional markets and emerging sectors such as battery materials and green hydrogen production. Tosoh’s advancements in ion-exchange zeolites and ChemChina’s integration of zeolite engineering into broader specialty chemical platforms highlight the region’s growing influence in the global value chain.
Specialty materials companies such as Zeochem and Clariant are also at the forefront, offering a range of engineered zeolites for niche applications, including pharmaceutical purification, air drying, and advanced adsorption processes. Clariant’s strategic partnerships with academic institutions and industrial end-users are accelerating the translation of laboratory-scale functionalization breakthroughs into scalable commercial products.
Strategic alliances are increasingly shaping the sector. Joint ventures between chemical producers and technology startups are fostering rapid prototyping and pilot-scale validation of novel zeolite functionalities. For example, collaborations between major oil & gas companies and zeolite specialists are targeting the development of catalysts for renewable fuels and plastic upcycling, with several demonstration projects expected to reach maturity by 2026.
Looking ahead, the competitive landscape is expected to further intensify as companies race to secure intellectual property around advanced functionalization methods and to establish supply chain resilience for critical raw materials. The next few years will likely see increased cross-sector partnerships, particularly in response to regulatory pressures for cleaner processes and the global push toward decarbonization.
Sustainability and Green Chemistry: Zeolites in Circular Economy Initiatives
Zeolite functionalization engineering is rapidly advancing as a cornerstone of sustainable chemistry and circular economy initiatives in 2025. The ability to tailor zeolite surfaces and frameworks with specific functional groups or metal centers is enabling new applications in green catalysis, waste valorization, and resource recovery. This progress is driven by both academic breakthroughs and industrial-scale implementations, with a focus on reducing environmental impact and enhancing process efficiency.
A key trend in 2025 is the integration of green synthesis methods for zeolite functionalization. Companies are increasingly adopting solvent-free, low-temperature, and template-free routes to modify zeolites, minimizing hazardous byproducts and energy consumption. For example, leading zeolite manufacturers such as Zeochem and Honeywell are investing in scalable post-synthetic modification techniques, including ion exchange, grafting, and encapsulation, to introduce catalytic or adsorptive functionalities tailored for circular economy processes.
Functionalized zeolites are now central to advanced catalytic systems for biomass conversion, CO2 capture, and plastic upcycling. In 2025, several pilot projects are underway where zeolites modified with transition metals or organic moieties are used to convert waste streams into valuable chemicals or fuels. For instance, BASF is developing zeolite-based catalysts for the depolymerization of polyolefins, supporting closed-loop recycling of plastics. Similarly, W. R. Grace & Co. is commercializing zeolite adsorbents functionalized for selective CO2 capture from industrial flue gases, contributing to decarbonization efforts.
Data from industry consortia and early deployments indicate that functionalized zeolites can improve process selectivity and reduce energy requirements by up to 30% compared to conventional materials. This is particularly significant in the context of circular economy targets, where maximizing resource efficiency and minimizing waste are paramount. The European Union’s Green Deal and similar regulatory frameworks in Asia and North America are accelerating the adoption of such technologies, with incentives for companies that demonstrate measurable sustainability gains.
Looking ahead, the outlook for zeolite functionalization engineering is robust. Ongoing collaborations between material suppliers, chemical producers, and end-users are expected to yield new generations of multifunctional zeolites with tunable properties. The next few years will likely see the commercialization of zeolites engineered for specific circular economy applications, such as nutrient recovery from wastewater and catalytic upcycling of mixed plastic waste. As the sector matures, companies like Arkema and Evonik Industries are poised to play pivotal roles in scaling up sustainable zeolite technologies, reinforcing their importance in the global transition to greener industrial processes.
Regulatory Environment and Industry Standards (2025 Update)
The regulatory environment for zeolite functionalization engineering is evolving rapidly in 2025, reflecting the growing industrial adoption of advanced zeolite materials in sectors such as petrochemicals, environmental remediation, and pharmaceuticals. Regulatory bodies are increasingly focused on ensuring the safety, sustainability, and performance of functionalized zeolites, particularly as their applications expand into sensitive areas like water purification and emissions control.
In the European Union, the Registration, Evaluation, Authorisation and Restriction of Chemicals (REACH) framework continues to set the benchmark for chemical safety, requiring detailed documentation and risk assessments for new and modified zeolite products. The European Chemicals Agency (ECHA) has recently updated its guidance to address the unique properties of nano- and micro-structured zeolites, emphasizing the need for comprehensive characterization and lifecycle analysis. This is particularly relevant for companies such as Zeochem, a major supplier of specialty zeolites, which has expanded its portfolio to include functionalized variants for environmental and pharmaceutical uses.
In the United States, the Environmental Protection Agency (EPA) is intensifying oversight of engineered nanomaterials, including functionalized zeolites, under the Toxic Substances Control Act (TSCA). The EPA’s 2024-2025 action plan includes new reporting requirements for manufacturers and importers of advanced zeolite materials, focusing on potential environmental and health impacts. Companies like Honeywell, which produces zeolite-based adsorbents and catalysts, are actively engaging with regulators to ensure compliance and to help shape industry standards.
Industry standards are also being updated to reflect advances in zeolite functionalization. The International Zeolite Association (IZA) and ASTM International are collaborating on new protocols for the characterization, performance testing, and quality assurance of functionalized zeolites. These standards are expected to be finalized by 2026 and will provide a framework for consistent product quality and regulatory compliance across global markets.
Looking ahead, the regulatory landscape is expected to become more harmonized, with increased cooperation between major jurisdictions such as the EU, US, and Asia-Pacific. This will likely facilitate international trade and accelerate the adoption of innovative zeolite technologies. However, manufacturers will need to invest in robust documentation, traceability, and testing capabilities to meet evolving requirements. As the market for functionalized zeolites grows, proactive engagement with regulatory bodies and standards organizations will be critical for maintaining market access and ensuring the safe, sustainable deployment of these advanced materials.
Challenges and Barriers: Scalability, Cost, and Technical Hurdles
Zeolite functionalization engineering, which involves tailoring the surface and pore properties of zeolites for advanced applications, faces several significant challenges as the field moves into 2025 and beyond. Despite the promise of functionalized zeolites in catalysis, adsorption, and environmental remediation, the transition from laboratory-scale innovation to industrial-scale deployment is hindered by issues of scalability, cost, and technical complexity.
One of the primary barriers is the scalability of functionalization processes. Laboratory methods, such as post-synthetic modification and template-assisted synthesis, often rely on precise control of reaction conditions and the use of expensive reagents. Scaling these processes to the multi-ton quantities required for industrial applications can lead to inconsistencies in product quality and performance. For example, companies like Zeochem and Honeywell, both major producers of zeolites, have highlighted the need for robust, reproducible, and cost-effective functionalization protocols to meet the demands of sectors such as petrochemicals, gas separation, and environmental technologies.
Cost remains a significant hurdle. The introduction of functional groups or metal centers into zeolite frameworks often requires rare or expensive precursors, as well as energy-intensive processes. This can make functionalized zeolites considerably more expensive than their unmodified counterparts, limiting their adoption in cost-sensitive industries. Furthermore, the need for specialized equipment and stringent process controls adds to capital and operational expenditures. BASF, a global leader in chemical manufacturing and zeolite-based catalysts, continues to invest in process optimization to reduce costs, but acknowledges that economic viability is a key challenge for widespread commercialization.
Technical hurdles also persist, particularly in achieving uniform and stable functionalization at scale. Maintaining the structural integrity of zeolites during modification, preventing leaching of active sites, and ensuring long-term stability under operational conditions are ongoing concerns. The development of new functionalization chemistries that are both selective and robust is a major research focus. Industry players such as Clariant and Arkema are actively engaged in collaborative R&D efforts to address these issues, often partnering with academic institutions to accelerate innovation.
Looking ahead, the outlook for overcoming these challenges is cautiously optimistic. Advances in process intensification, automation, and green chemistry are expected to improve scalability and reduce costs. However, the pace of industrial adoption will depend on continued investment in R&D, cross-sector collaboration, and the development of standardized protocols for quality assurance. As the market for advanced zeolite materials grows, the ability to engineer functionalized zeolites at scale will be a critical determinant of commercial success.
Case Studies: Industrial Deployments and Performance Metrics
In 2025, zeolite functionalization engineering continues to gain momentum as a critical enabler for advanced industrial applications, particularly in catalysis, gas separation, and environmental remediation. Industrial deployments are increasingly focused on tailoring zeolite frameworks and surface properties to achieve higher selectivity, stability, and throughput in real-world processes.
A notable case is the deployment of functionalized zeolites in petrochemical refining. Sinopec Group, one of the world’s largest integrated energy and chemical companies, has reported ongoing optimization of zeolite-based catalysts for fluid catalytic cracking (FCC) units. By introducing hierarchical porosity and metal-exchange functionalization, Sinopec has achieved improved conversion rates and product selectivity, with reported increases in gasoline yield and reductions in coke formation. These enhancements are supported by in-house pilot plant data and are being scaled to commercial units in 2025.
In the realm of environmental applications, BASF has advanced the use of functionalized zeolites for selective catalytic reduction (SCR) of nitrogen oxides (NOx) in automotive and stationary emissions control. BASF’s Cu- and Fe-exchanged zeolite catalysts have demonstrated high NOx conversion efficiencies (>95%) and extended operational lifetimes under harsh conditions, as validated in field trials with major automotive OEMs. The company is also exploring the integration of zeolite membranes for industrial gas separations, targeting CO2 capture and hydrogen purification.
Another significant deployment is by Honeywell, which has commercialized zeolite-based adsorbents and catalysts for air separation and natural gas upgrading. Honeywell’s UOP division has engineered zeolites with tailored Si/Al ratios and surface modifications to enhance selectivity for oxygen and nitrogen, as well as for the removal of trace contaminants. Performance metrics from recent installations indicate improved energy efficiency and reduced operational costs compared to legacy materials.
Looking ahead, the outlook for zeolite functionalization engineering is robust. Industry leaders are investing in digital process optimization and high-throughput screening to accelerate the discovery of novel zeolite structures and functional groups. Collaborations between manufacturers and end-users are expected to yield further improvements in catalyst lifetimes, regeneration cycles, and process integration. As regulatory pressures on emissions and energy efficiency intensify, the adoption of advanced functionalized zeolites is projected to expand across sectors, with measurable impacts on sustainability and operational performance.
Future Outlook: Disruptive Opportunities and R&D Roadmap to 2030
Zeolite functionalization engineering is poised for significant advancements through 2025 and into the next decade, driven by the convergence of materials science, catalysis, and sustainability imperatives. The sector is witnessing a surge in R&D investments aimed at tailoring zeolite properties—such as acidity, pore size, and surface chemistry—to unlock disruptive applications in energy, environment, and chemical manufacturing.
A key trend is the development of hierarchical and multi-functional zeolites, which combine micro- and mesoporosity to enhance molecular transport and catalytic efficiency. Major industrial players like BASF and W. R. Grace & Co. are actively engineering zeolites with customized frameworks and surface modifications to address challenges in refining, petrochemicals, and emission control. For instance, BASF’s recent innovations in zeolite-based catalysts are targeting improved selectivity and durability for automotive and industrial emissions abatement, aligning with tightening global regulations.
Another disruptive opportunity lies in the integration of zeolites with emerging technologies such as CO2 capture, hydrogen production, and renewable feedstock conversion. Companies like Honeywell are advancing zeolite sorbents and membranes for gas separation and purification, with pilot projects underway to scale up these solutions for industrial decarbonization. The functionalization of zeolites with metal nanoparticles or organic moieties is also being explored to create hybrid catalysts for biomass valorization and green chemistry, with several collaborative initiatives between industry and academia expected to yield commercial prototypes by 2027.
Digitalization and high-throughput experimentation are accelerating the discovery of novel zeolite structures and functionalization pathways. The adoption of machine learning and computational modeling by leading manufacturers is enabling the rapid screening of zeolite compositions for targeted applications, reducing development cycles and costs. Zeochem, a global supplier of specialty zeolites, is investing in digital R&D platforms to optimize product performance for pharmaceutical, environmental, and energy storage markets.
Looking ahead to 2030, the R&D roadmap for zeolite functionalization engineering will likely focus on:
- Scalable synthesis of defect-engineered and heteroatom-doped zeolites for next-generation catalysis.
- Integration of zeolites into advanced composite materials for batteries, sensors, and water purification.
- Development of circular economy solutions, including zeolite regeneration and recycling technologies.
With sustained investment and cross-sector collaboration, zeolite functionalization is set to play a pivotal role in enabling cleaner processes, resource efficiency, and new value chains across the chemical and energy industries.