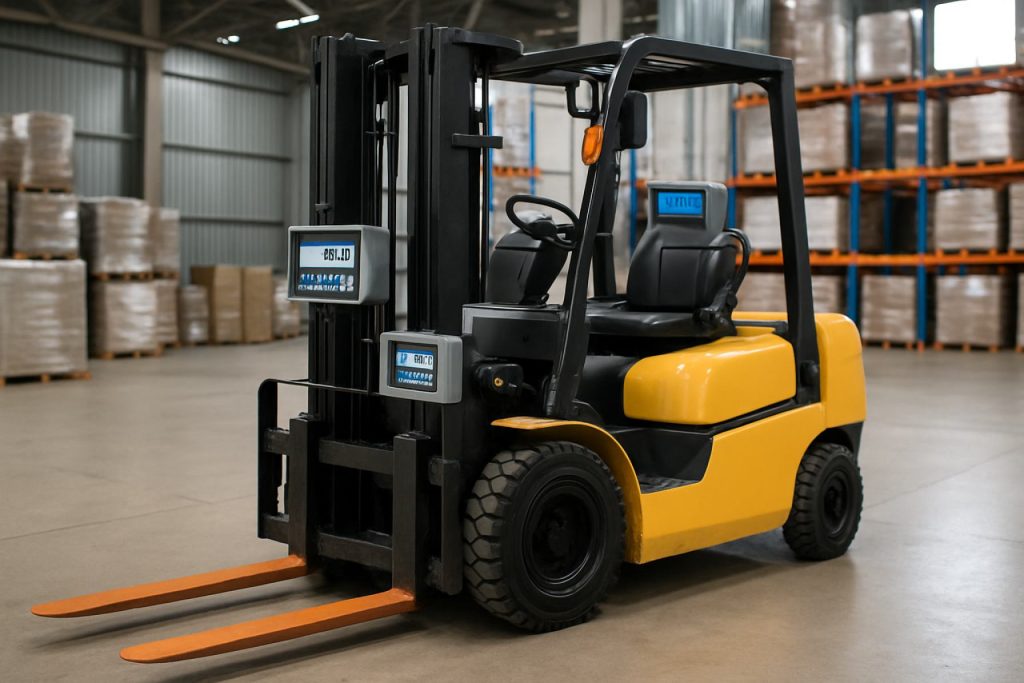
Forklift Weight Calibration Systems in 2025: The Hidden Innovations and Market Shifts Set to Transform Industrial Safety and Efficiency. Discover What’s Next for This Critical Technology Sector.
- Executive Summary: Key Findings for 2025–2030
- Market Size & Forecast: Global and Regional Outlook
- Regulatory Developments Impacting Forklift Calibration
- Breakthrough Technologies: Smart Sensors & IoT Integration
- Competitive Landscape: Leading Players and Strategies
- End-User Segments: Logistics, Manufacturing, and Beyond
- Case Studies: Real-World Deployments and Measured ROI
- Sustainability & Safety: Evolving Industry Standards
- Challenges & Barriers: Adoption and Compliance Hurdles
- Future Outlook: Disruptive Innovations and Market Opportunities
- Sources & References
Executive Summary: Key Findings for 2025–2030
The market for forklift weight calibration systems is experiencing significant technological advancement and growing adoption, driven by the increasing need for precise load measurement, compliance with safety regulations, and operational efficiency in logistics and manufacturing sectors. In 2025, digital transformation is accelerating integration of advanced weighing solutions, such as onboard scales and automated calibration, across fleets of electric and internal combustion forklifts.
Major equipment manufacturers, including Toyota Industries Corporation and Hyster-Yale Materials Handling, are embedding real-time weight monitoring and calibration technologies into new forklift models to enhance both safety and data capture. These systems help prevent overloading, streamline warehouse management, and facilitate compliance with evolving occupational safety standards. Crown Equipment Corporation and Mitsubishi Logisnext are also notable for offering integrated weight calibration options, often combined with telematics and fleet management platforms.
Key findings for 2025–2030 indicate:
- Rising Automation: Automated calibration and self-diagnostic capabilities are rapidly becoming standard, reducing manual intervention and minimizing human error. This trend is particularly evident in solutions developed by companies such as RAVAS (a specialist in mobile weighing systems) and Intercomp Company, both of which are expanding their product portfolios with wireless and IoT-enabled calibration features.
- Regulatory Pressure: Enforcement of stringent load compliance and occupational safety standards in North America, Europe, and parts of Asia-Pacific is compelling fleet operators to invest in certified and regularly calibrated systems. Organizations such as the Occupational Safety and Health Administration (OSHA) are expected to continue updating guidelines that affect forklift weighing accuracy and calibration frequency.
- Data Integration & Digitalization: Weight calibration systems are increasingly integrated with warehouse management systems (WMS) and enterprise resource planning (ERP) platforms, supporting real-time inventory control and advanced analytics. Leading OEMs and third-party providers are collaborating to develop open standards for seamless data exchange.
- Aftermarket and Retrofit Growth: Demand for aftermarket calibration kits and retrofit solutions is rising, as operators seek to upgrade existing fleets with minimal downtime. Companies such as Schenck Process and Avery Weigh-Tronix are responding with modular kits compatible with a wide range of forklift models.
Looking ahead to 2030, the forklift weight calibration system market is expected to further benefit from the adoption of AI-driven diagnostics, predictive maintenance, and increasingly strict regulatory oversight. Industry players are likely to invest in R&D for higher-precision sensors, enhanced user interfaces, and greater interoperability, cementing the role of accurate weight calibration in future-ready logistics and material handling operations.
Market Size & Forecast: Global and Regional Outlook
The global market for forklift weight calibration systems is set for notable growth in 2025 and the following years, driven by increasing automation in material handling, stringent safety standards, and the growing adoption of Industry 4.0 principles. Forklift weight calibration systems, which ensure accurate load measurement and compliance with safety regulations, have become integral across industries such as manufacturing, logistics, warehousing, and construction.
Currently, North America and Europe lead the market due to early technological adoption and strict regulatory frameworks on workplace safety. The United States, for example, has seen significant adoption of advanced calibration solutions, with major manufacturers like Toyota Material Handling and Crown Equipment Corporation integrating sophisticated onboard weighing and calibration technologies into their forklifts. In Europe, countries such as Germany and the United Kingdom are experiencing similar trends, with emphasis on digital calibration and telematics integration.
The Asia-Pacific region, particularly China, Japan, and India, is expected to register the fastest growth in the coming years. Rapid industrialization, expanding e-commerce, and increased investment in modern warehouse infrastructure are primary drivers. Leading regional players and subsidiaries of global OEMs, including KION Group and Mitsubishi Forklift Trucks, are ramping up production of forklifts equipped with calibration capabilities to meet local demand.
Globally, the industry is witnessing a shift toward digital and IoT-enabled calibration systems. These systems provide real-time weight data, remote diagnostics, and seamless integration with warehouse management software. Companies such as Hyster-Yale Materials Handling and Linde Material Handling are actively developing and promoting their proprietary load sensing and calibration solutions, anticipating a surge in demand as customers seek enhanced fleet efficiency and compliance with evolving international standards.
Looking forward to 2025 and beyond, the market outlook remains positive. Factors such as government initiatives supporting automation, rising labor costs, and the need for operational transparency are likely to accelerate adoption. While mature regions will focus on upgrading legacy systems, emerging markets will drive new installations. The convergence of AI, IoT, and digital calibration will further expand the market, with manufacturers collaborating with sensor and software specialists to deliver innovative, value-added solutions.
Regulatory Developments Impacting Forklift Calibration
The regulatory landscape for forklift weight calibration systems is undergoing significant evolution in 2025, shaped by new safety standards, environmental considerations, and digital integration requirements. Regulatory bodies worldwide are emphasizing the importance of accurate load measurement to prevent workplace accidents, reduce product damage, and ensure operational compliance. In the European Union, the Machinery Directive 2006/42/EC and harmonized standards such as EN ISO 3691-1 continue to set the legal framework for the safe operation and calibration of industrial trucks, including forklifts. These regulations require regular calibration and maintenance of on-board weighing systems to ensure accuracy and traceability, with increasing enforcement observed in recent years.
In the United States, the Occupational Safety and Health Administration (OSHA) maintains strict guidelines under OSHA Standard 1910.178 for powered industrial trucks. While OSHA does not dictate specific calibration intervals, it mandates that forklifts be maintained in a safe operating condition, which is interpreted by industry as requiring periodic calibration of weight measurement systems. The American National Standards Institute (ANSI) and the Industrial Truck Standards Development Foundation (ITSDF) have updated the B56 series to further clarify requirements for electronic weighing and calibration, influencing manufacturers to embed advanced calibration features in new models.
A notable trend in 2025 is the integration of digital recordkeeping and remote calibration verification, as regulators in jurisdictions such as Germany and Japan push for automated compliance logs and cloud-based calibration certificates. This is prompting manufacturers like Toyota Industries Corporation and Linde Material Handling to invest in telematics and IoT-enabled calibration systems, allowing for real-time data transmission and regulatory audits without manual intervention. Such features are becoming especially relevant as governments incentivize fleet electrification and digital transformation in logistics.
In the Asia-Pacific region, China’s State Administration for Market Regulation (SAMR) has begun tightening oversight of weighing equipment in the logistics sector, with new guidelines expected to be phased in by 2026. These rules are anticipated to harmonize with international standards, impacting both domestic forklift manufacturers and global suppliers operating in the region. Major suppliers such as KION Group and Crown Equipment Corporation are proactively adapting their products to align with these evolving requirements, investing in both hardware and software updates.
Looking forward, regulatory developments are expected to further accelerate the adoption of advanced calibration systems, particularly those that can demonstrate traceability, cyber-security compliance, and interoperability with broader warehouse management systems. The convergence of safety, environmental, and digital policies suggests that forklift weight calibration will remain a key compliance and innovation focus for manufacturers and operators through the next several years.
Breakthrough Technologies: Smart Sensors & IoT Integration
The year 2025 is shaping up to be pivotal for forklift weight calibration systems, with industry leaders accelerating the integration of smart sensors and IoT connectivity into material handling equipment. Traditional calibration processes, which often required manual intervention and periodic downtime, are being replaced or supplemented by intelligent systems capable of real-time monitoring, self-diagnosis, and remote calibration. These developments are underscored by the drive for heightened operational efficiency, regulatory compliance, and safety in warehouses, manufacturing, and logistics hubs.
A central breakthrough is the deployment of advanced load cells and sensor arrays directly within the forklift mast or forks. Companies such as Toyota Material Handling and Hyster-Yale Materials Handling have been at the forefront of integrating smart sensors that provide precise, instantaneous weight data during every lift. These embedded sensors can detect subtle variations in load distribution and automatically trigger recalibration sequences if anomalies or drift are detected—thus minimizing human error and ensuring consistent measurement accuracy.
IoT platforms are further transforming weight calibration systems by enabling forklifts to transmit load data to centralized management software over Wi-Fi, 4G/5G, or proprietary industrial wireless protocols. This connectivity allows for real-time analytics, predictive maintenance, and seamless documentation of compliance with safety standards such as ISO 3691-1. Notably, Crown Equipment Corporation offers telemetry solutions that integrate weight calibration with fleet management dashboards, giving supervisors immediate insight into operational metrics and potential overload events.
Another trend is the rise of “over-the-air” firmware updates and remote diagnostics, which reduce the need for onsite technical intervention. Companies like Linde Material Handling are rolling out cloud-based calibration management tools, allowing service teams to audit and recalibrate systems remotely, further improving equipment uptime.
- Smart sensors enable dynamic, continuous calibration and drift detection.
- IoT connectivity supports centralized monitoring and compliance reporting.
- Remote diagnostics and updates minimize downtime and labor costs.
Looking forward, as 5G infrastructure and AI-driven analytics mature, expect even deeper integration between forklift weight calibration systems and broader warehouse automation platforms. Industry observers predict that by 2027, a majority of new forklifts will ship with factory-installed smart calibration and IoT modules, transforming them from isolated machines into nodes of an intelligent, connected supply chain.
Competitive Landscape: Leading Players and Strategies
The competitive landscape for forklift weight calibration systems in 2025 is defined by a handful of global manufacturers and technology innovators that continuously invest in advanced weighing, sensor, and connectivity solutions. These players are responding to increasing demand for higher precision, digital integration, and regulatory compliance in logistics, warehousing, and manufacturing environments.
Among the leading manufacturers, Toyota Industries Corporation stands out with its comprehensive range of material handling equipment, including forklifts equipped with integrated weight measurement and calibration features. Toyota’s focus on integrating digital weighing systems with telematics platforms supports real-time monitoring and compliance tracking, as well as predictive maintenance.
Another key player is Hyster-Yale Materials Handling, which has expanded its portfolio to include factory-fitted weighing systems that provide automatic calibration and remote diagnostics. The company’s strategy revolves around enhancing the user experience with intelligent calibration alerts and cloud-based service platforms, which are particularly relevant for multi-site fleet operations.
European manufacturers such as Linde Material Handling have developed proprietary weight calibration solutions that integrate with their advanced safety and automation packages. Linde’s approach emphasizes modularity, allowing customers to retrofit calibration systems onto existing fleets, addressing cost concerns and regulatory updates efficiently.
On the technology supplier side, Mettler-Toledo and Schenck Process are recognized for their high-precision industrial weighing sensors and calibration modules, which are increasingly being adopted as OEM components in forklifts. These suppliers focus on wireless, IoT-enabled calibration systems that facilitate remote certification and maintenance, aligning with broader trends toward Industry 4.0 compliance.
Strategically, leading companies are prioritizing:
- Integration with fleet management and warehouse management software for seamless data flow.
- Compliance with evolving safety and weight certification regulations, particularly in Europe and North America.
- Development of sensor technologies that can withstand harsh industrial environments and minimize drift, reducing the frequency of recalibration.
- Customer support and training services to ensure operators and maintenance teams can manage calibration efficiently.
Looking ahead, the competitive focus is expected to intensify around digital transformation, with partnerships between forklift OEMs and industrial IoT specialists. As regulatory bodies tighten requirements and end-users demand smarter, more connected solutions, market leaders are likely to invest further in automation, AI-driven calibration checks, and predictive analytics to maintain their edge.
End-User Segments: Logistics, Manufacturing, and Beyond
Forklift weight calibration systems are increasingly critical for a range of end-user segments, with logistics and manufacturing leading adoption. Accurate weight measurement is essential for optimizing safety, efficiency, and legal compliance in material handling operations. As 2025 unfolds, advancements in sensor technology, digital integration, and regulatory pressures are shaping how industries deploy and maintain these systems across diverse sectors.
In the logistics sector, major third-party logistics (3PL) providers and distribution centers are prioritizing forklift weight calibration to ensure load accuracy, prevent overloading, and comply with transportation regulations such as axle weight limits. The integration of on-board weight calibration systems with warehouse management software (WMS) allows for real-time data capture and reporting, streamlining inventory management and reducing the risk of costly compliance violations. Companies such as Toyota Industries Corporation and Linde Material Handling are notable for integrating advanced weighing and calibration technology directly into their forklift fleets, offering systems that self-calibrate and deliver digital weight records to logistics managers.
In manufacturing environments, precision in material movement and supply chain tracking is a top concern. Here, forklift weight calibration systems are not only used to prevent equipment damage and ensure worker safety, but also to support lean manufacturing initiatives and minimize material waste. Manufacturers in automotive, electronics, and food processing are increasingly deploying calibration-enabled forklifts to automate quality control processes and document material flows. Leading equipment suppliers such as Hyster-Yale Materials Handling and Crown Equipment Corporation are actively promoting integrated scale and calibration options in their latest product lines, responding to growing demand for traceability and digitalization on the factory floor.
Beyond logistics and manufacturing, other sectors—including ports, recycling, construction, and pharmaceuticals—are beginning to adopt forklift weight calibration systems. In port operations, accurate container and cargo weighing is crucial for international shipping compliance, while in recycling and construction, weight data supports sorting, billing, and safety functions. Pharmaceutical companies, following stringent regulatory frameworks, use calibrated forklifts to ensure batch traceability and audit readiness.
Looking ahead to the next few years, end-user segments are expected to increasingly favor calibration systems that offer remote diagnostics, wireless connectivity, and compatibility with broader IoT ecosystems. This trend is supported by ongoing R&D investment from major OEMs and system integrators, alongside a strengthening regulatory landscape requiring more frequent and verifiable calibration. As a result, the market for forklift weight calibration systems among logistics, manufacturing, and adjacent sectors is positioned for continued growth and technological evolution through 2025 and beyond.
Case Studies: Real-World Deployments and Measured ROI
Forklift weight calibration systems have become integral to modern logistics and warehouse management, offering both operational efficiency and compliance with safety regulations. In 2025, several real-world deployments highlight measurable return on investment (ROI) for enterprises adopting these systems.
A notable example is the deployment of advanced forklift scale systems by Mettler-Toledo International Inc., a global leader in precision instruments. Their forklift scales have been widely implemented by distribution centers seeking to reduce downtime associated with manual weighing and to prevent overloading. According to case studies published by the company, customers reported up to a 25% improvement in loading efficiency, with error rates in shipment weights dropping by more than 15% after adopting automated forklift calibration solutions.
Similarly, RAVAS Europe BV, a pioneer in mobile weighing systems, has equipped several multinational logistics providers with integrated forklift weight calibration technology. In one documented deployment, a third-party logistics (3PL) firm measured a payback period of less than 18 months, primarily driven by labor cost reductions and decreased product damage due to more accurate load handling. RAVAS’s systems further enabled real-time data capture, integrating seamlessly with warehouse management systems (WMS) and enterprise resource planning (ERP) platforms to provide continuous weight verification, which contributed to enhanced inventory accuracy and traceability.
Another case involves T-Scale International Co., Ltd., an established manufacturer of industrial weighing solutions. In 2024-2025, T-Scale reported successful implementations within automotive manufacturing plants, where precise component tracking is critical. The adoption of their forklift scale calibration technology reduced inventory discrepancies by 30%, directly impacting bottom-line profitability and compliance with ISO 9001 quality standards.
ROI calculations from these deployments commonly factor in reduced weighing time, fewer shipment discrepancies, lower risk of OSHA violations, and improved asset utilization. For example, companies have reported annual savings ranging from $50,000 to $200,000, depending on fleet size and throughput, by minimizing manual interventions and errors.
Looking forward, the outlook for forklift weight calibration systems remains robust as industries move towards greater automation and data-driven operations. Increasing integration with IoT and cloud platforms is expected, further enhancing remote monitoring, predictive maintenance, and compliance reporting. Industry leaders like Mettler-Toledo International Inc. and RAVAS Europe BV are poised to expand their solution portfolios to cater to evolving customer needs, ensuring continued measurable ROI for adopters in 2025 and beyond.
Sustainability & Safety: Evolving Industry Standards
In 2025, the integration of sophisticated weight calibration systems into forklifts is increasingly driven by heightened sustainability goals and tightening safety regulations across global logistics and manufacturing sectors. The accurate measurement of loads is critical for both preventing workplace accidents and minimizing resource waste, aligning with broader environmental, social, and governance (ESG) priorities.
Regulatory bodies and industry standards organizations are playing an influential role. The European Union continues its enforcement of EN ISO 3691-1 standards, which require periodic inspection and calibration of industrial trucks’ weighing equipment to ensure operational safety and legal compliance. Likewise, the U.S. Occupational Safety and Health Administration (OSHA) maintains requirements for load handling and equipment maintenance, spurring North American manufacturers and fleet operators to invest in advanced calibration technologies.
Leading forklift manufacturers are responding with integrated solutions. Toyota Industries Corporation, a global industry leader, embeds smart weighing and auto-calibration modules in its latest electric and internal combustion models, offering real-time digital feedback to operators. KION Group—which owns brands such as Linde Material Handling and STILL—has developed proprietary sensor systems to improve both accuracy and traceability, supporting digital recordkeeping for safety audits and sustainability reporting.
Suppliers specializing in weighing technology, such as Mettler-Toledo, are collaborating with OEMs to deliver retrofit kits and telematics-enabled solutions that support predictive maintenance and remote monitoring. These systems are increasingly cloud-connected, allowing for centralized data management that aligns with lean warehousing and carbon reduction initiatives. Industry adoption is expected to accelerate as companies seek to optimize fleet usage, avoid overloading, and reduce fuel consumption—each a tangible lever for sustainability.
Looking forward, the next several years will see a push for even tighter integration of calibration data with warehouse management and enterprise resource planning (ERP) systems. Forklift fleet operators are demanding not just compliance but proactive insights, such as automated alerts for recalibration or unsafe load conditions. Manufacturers are investing in AI-driven analytics to further improve system reliability and predictive safety. The trend is toward lifecycle digitalization: from initial calibration through ongoing operation, all data are captured and leveraged for continuous improvement.
As sustainability targets and safety standards rise, forklift weight calibration systems are set to become a central element in the evolving landscape of material handling, with industry leaders and technology innovators shaping best practices for years to come.
Challenges & Barriers: Adoption and Compliance Hurdles
Adoption of forklift weight calibration systems is gaining traction across industrial sectors, but several challenges and barriers persist that impact widespread implementation, particularly as regulatory and operational demands evolve into 2025 and beyond. One of the primary hurdles is the diversity of forklift types, operational environments, and load handling requirements, which often necessitate bespoke calibration solutions rather than off-the-shelf systems. For many operators, retrofitting existing fleets with weight calibration technology can be costly and complex, especially for older models not originally designed to integrate with digital or sensor-based systems. Leading manufacturers such as Toyota Industries Corporation and Hyster-Yale Materials Handling offer advanced integrated systems in new models, but legacy fleet adaptation remains a significant hurdle.
Another pressing challenge is ensuring ongoing compliance with evolving safety regulations and standards. Regulatory bodies in regions such as the EU and North America are increasingly emphasizing load accuracy and safety, requiring more rigorous and frequent calibration. However, adherence to these standards is inconsistent, particularly among smaller operators or in regions with less stringent oversight. The calibration process itself demands skilled personnel and regular maintenance, which can be a barrier for facilities with limited technical resources.
Data interoperability and system integration pose further barriers. Many industrial operations require forklift weight data to synchronize with warehouse management systems (WMS) or enterprise resource planning (ERP) platforms. However, proprietary protocols and varying sensor technologies from different manufacturers—such as those offered by Mettler-Toledo and The Raymond Corporation—can complicate seamless data exchange and centralized monitoring. This lack of standardization can raise costs and slow adoption, as companies may hesitate to commit to systems that could become obsolete or incompatible as their digital infrastructure evolves.
Looking ahead to the next few years, industry players are responding to these challenges by developing modular, retrofittable calibration solutions and investing in cross-platform integration standards. For example, Mettler-Toledo is focusing on scalable sensor packages that can be integrated with a broad range of forklift models, while manufacturers like Toyota Industries Corporation are expanding support for digital connectivity in their newest fleets. Nonetheless, until costs decrease and interoperability improves, adoption rates may remain uneven, particularly among small and mid-sized enterprises.
Future Outlook: Disruptive Innovations and Market Opportunities
The future of forklift weight calibration systems is being shaped by rapid technological advancements and evolving industry demands. As industries such as logistics, warehousing, and manufacturing continue to prioritize safety, efficiency, and compliance, the adoption of advanced calibration systems is expected to accelerate through 2025 and beyond.
A primary driver of innovation is the integration of digital and IoT-based solutions into forklift calibration. Modern systems increasingly utilize wireless sensors and cloud connectivity for real-time monitoring, remote diagnostics, and automated calibration alerts. Major industry players like Toyota Industries Corporation and Hyster-Yale Materials Handling are embedding smart weighing and calibration technologies directly into their forklift models, enabling operators to receive immediate feedback and ensuring consistent compliance with safety regulations. These capabilities are particularly valued in sectors with heavy regulatory oversight, such as food and pharmaceuticals.
Another disruptive trend is the proliferation of AI and machine learning algorithms in calibration systems. These technologies are being developed to enhance predictive maintenance, detect anomalies in load measurements, and automate recalibration schedules based on usage patterns. Companies such as Crown Equipment Corporation and Linde Material Handling are investing in research and pilot programs to integrate intelligent calibration features that minimize downtime and human error, thereby optimizing operational throughput.
Weight calibration modules are also becoming increasingly modular and retrofit-friendly. This allows operators to upgrade existing fleets without major overhauls, making advanced calibration accessible to small- and medium-sized enterprises. Suppliers like RAVAS Europe—recognized for specialized mobile weighing solutions—are expanding product lines to support both OEM partnerships and aftermarket installations, signaling broadening market opportunities and customization potential for end-users.
Looking ahead, regulatory bodies in North America, Europe, and Asia-Pacific are expected to tighten standards for in-field weighing accuracy and reporting. This regulatory momentum will likely drive further adoption of automated calibration systems, particularly those capable of remote verification and digital record-keeping for audits. Industry organizations such as the Material Handling Industry are actively promoting best practices and technology standards to unify calibration protocols globally.
In summary, the period from 2025 onward will see forklift weight calibration systems become smarter, more connected, and more integral to operational excellence. Companies that prioritize digital transformation and compliance-ready solutions are poised to capture significant market share, while ongoing innovation will open new opportunities across diverse industrial segments.
Sources & References
- Toyota Industries Corporation
- Hyster-Yale Materials Handling
- Crown Equipment Corporation
- RAVAS
- Intercomp Company
- Schenck Process
- Toyota Material Handling
- KION Group
- Hyster-Yale Materials Handling
- Linde Material Handling
- Hyster-Yale Materials Handling
- The Raymond Corporation
- Material Handling Industry