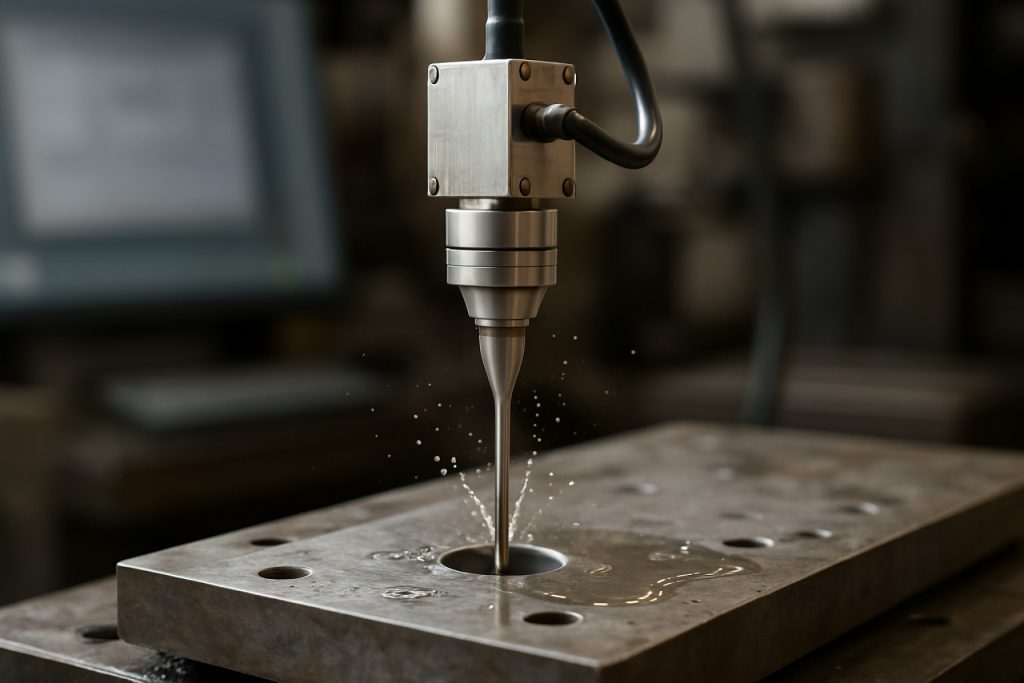
Table of Contents
- Executive Summary: Ultrasonic Drilling in 2025
- Technology Overview: How Guided Ultrasonics Work
- Key Players and Industry Consortiums
- Recent Innovations and Patent Trends
- Current Market Size and 2025–2030 Forecasts
- End-User Applications: Energy, Manufacturing, and Beyond
- Competitive Landscape and Strategic Partnerships
- Regulatory Standards and Industry Guidelines
- Challenges, Risks, and Limitations
- Future Outlook: Next-Gen Ultrasonic Drilling Technologies
- Sources & References
Executive Summary: Ultrasonic Drilling in 2025
Guided ultrasonic drilling technologies are poised to significantly influence advanced manufacturing and materials processing in 2025 and the near future. Ultrasonic drilling, which employs high-frequency vibrations to aid material removal, is increasingly being adapted with guidance systems—ranging from precise tool-path control to real-time feedback integration. These enhancements directly address the requirements for higher accuracy, reduced tool wear, and the ability to process challenging materials such as advanced ceramics, composites, and semiconductor substrates.
Throughout 2024 and into 2025, leading equipment manufacturers have integrated ultrasonic guidance systems using sensors, machine vision, and adaptive control algorithms. For instance, Sonimat and Ultrasonic Systems have advanced their platforms by incorporating guided motion control and real-time monitoring to ensure optimal energy delivery and consistent drilling depth. These solutions are particularly valued in aerospace, electronics, and medical device applications, where tolerances are tight and conventional mechanical drilling can result in microcracks or delamination.
Recent demonstrations by companies like Sonimat have shown that guided ultrasonic drilling can reduce machining time by up to 30% compared to traditional ultrasonic or mechanical methods, while simultaneously improving hole quality and dimensional repeatability. In semiconductor manufacturing, the deployment of guided ultrasonic systems has enabled more complex through-wafer vias and microfeatures, meeting the demand for miniaturization and precision (Ultrasonic Systems).
A key 2025 development is the move towards closed-loop guided control, where drilling parameters are automatically adjusted in response to real-time sensor data on vibration amplitude, tool wear, and workpiece integrity. This adaptive approach is being championed by European and Asian manufacturers, who are deploying smart ultrasonic lines in both pilot and production settings. Additionally, collaboration with automation integrators is accelerating the adoption of guided ultrasonic drilling in high-throughput environments.
Looking ahead, the outlook for guided ultrasonic drilling technologies is robust. Ongoing advances in digital sensors, machine learning for process optimization, and integration with Industry 4.0 platforms are expected to further boost reliability and cost-effectiveness. The market is likely to see broader adoption in sectors that require precise, damage-free drilling in advanced materials, with companies like Sonimat and Ultrasonic Systems positioned as key technology enablers through 2025 and beyond.
Technology Overview: How Guided Ultrasonics Work
Guided ultrasonic drilling technologies represent a significant evolution in the field of advanced manufacturing and precision engineering. Unlike conventional mechanical drilling, guided ultrasonic drilling utilizes high-frequency ultrasonic vibrations—typically in the range of 20–40 kHz—superimposed on a drill bit or tool. This vibrational energy, when precisely guided and controlled, reduces the required drilling force, enhances penetration rates, and minimizes heat generation, making it particularly advantageous for hard and brittle materials such as ceramics, composites, and advanced alloys.
The core technology involves an ultrasonic transducer, often piezoelectric, that converts electrical energy into mechanical vibrations. These are transmitted via a booster and horn assembly to the drilling tool, which is brought into contact with the workpiece. The addition of a guided mechanism—often realized through integrated sensors and real-time feedback loops—enables precise tool path control, optimal vibration amplitude, and dynamic response to variations in material hardness or geometry. This guided approach ensures superior accuracy and repeatability, essential for applications in aerospace, medical device manufacturing, and microelectronics.
Recent advancements, as observed in 2024–2025, have focused on improving the integration of ultrasonic systems with CNC machine tools and robotic platforms, allowing for multi-axis guided motion and coordinated process control. For example, SONOTRONIC Nagel GmbH and TELSONIC AG have developed modular ultrasonic drilling heads that can be retrofitted onto existing production equipment, offering manufacturers flexibility and scalability. These systems typically feature closed-loop control, real-time process diagnostics, and user-friendly interfaces, enabling operators to adjust parameters based on in-process feedback.
A defining trend in 2025 is the application of guided ultrasonic drilling in the aerospace sector, where companies such as Safran are exploring its use for drilling fiber-reinforced composites and high-temperature alloys. The technology’s ability to produce cleaner holes with less delamination and tool wear is driving its broader adoption. Similarly, medical technology firms are adapting guided ultrasonic drilling for minimally invasive bone surgery, leveraging precision and reduced thermal damage.
Looking ahead, the next few years are expected to see further miniaturization of ultrasonic components, improved sensor integration, and smarter process automation. The convergence of guided ultrasonic drilling with Industry 4.0 principles—including IoT-enabled monitoring and predictive maintenance—will likely accelerate deployment across advanced manufacturing sectors, underpinning higher productivity and quality standards.
Key Players and Industry Consortiums
The landscape of guided ultrasonic drilling technologies in 2025 is shaped by a mix of established industry leaders, innovative startups, and collaborative consortiums, all focusing on advancing precision, efficiency, and automation in drilling processes. This technology, which harnesses high-frequency ultrasonic vibrations to aid material penetration, is particularly significant in aerospace, energy, and advanced manufacturing sectors.
Among the notable players, SonX remains at the forefront, leveraging its proprietary ultrasonic drilling systems for composite and hard-material applications. The company continues to expand its product lines to meet the increasing demand for precision drilling in aerospace components, driven by the need for lighter and stronger materials. Another prominent firm, DeWalt, has made strides in integrating guided ultrasonic modules with their industrial drilling platforms, focusing on automated and semi-automated solutions for large-scale manufacturing environments.
In the high-tech sector, Bosch has invested heavily in R&D for guided ultrasonic drilling, emphasizing multi-axis robotic integration. Their systems aim to reduce tool wear and improve bore quality in difficult-to-machine alloys, which are increasingly used in electric vehicle and renewable energy infrastructure projects. Similarly, Sandvik is pushing the envelope with sensor-embedded ultrasonic drill bits that offer real-time feedback, facilitating adaptive drilling processes and predictive maintenance.
Industry consortiums are playing a pivotal role in standardizing and accelerating the adoption of guided ultrasonic drilling. The ASM International and the SAE International are actively coordinating working groups and technical committees focused on setting best practices, safety protocols, and interoperability standards. These collaborative efforts are further supported by government-funded research, particularly in Europe and North America, where public-private partnerships aim to enhance manufacturing competitiveness and sustainability.
Looking forward, the sector is expected to see deeper integration of AI-driven guidance systems, expanded use of advanced materials, and broader adoption in aerospace, medical device manufacturing, and energy. As key players and industry bodies continue to collaborate and innovate, guided ultrasonic drilling is poised to become a mainstream solution for high-precision, low-damage drilling by the late 2020s.
Recent Innovations and Patent Trends
Guided ultrasonic drilling technologies have witnessed significant advancements in recent years, driven by the demand for increased precision, efficiency, and automation in industrial machining and healthcare applications. As of 2025, the integration of real-time guidance systems with ultrasonic drilling tools is reshaping both manufacturing and medical sectors, resulting in higher accuracy and reduced procedural risks.
One major innovation involves the combination of computer vision and sensor fusion technologies with ultrasonic drilling platforms. Leading manufacturers are embedding advanced feedback mechanisms that enable the drill to detect and adapt to material heterogeneity in real time. For instance, companies specializing in medical device manufacturing are utilizing guided ultrasonic systems for minimally invasive bone surgery, leveraging ultrasonic energy to reduce heat generation and collateral tissue damage while maintaining precise control over drilling trajectories. This is particularly evident in orthopedic and neurosurgical procedures, where patient safety and accuracy are paramount (Stryker).
In industrial contexts, guided ultrasonic drilling is being adopted for composite and advanced material processing, notably in the aerospace and automotive sectors. Manufacturers have reported improved hole quality and extended tool life due to the non-contact, vibration-based cutting mechanism of ultrasonic drills. Integration with robotic arms and digital controllers allows for fully automated guided drilling, reducing manual intervention and increasing throughput (Sandvik). The ongoing miniaturization of ultrasonic transducers and the development of more robust guidance algorithms are expected to further expand applications over the next few years.
Patent activity in this domain reflects escalating innovation. Recent filings highlight breakthroughs such as AI-powered path correction, in-situ defect detection, and dynamic ultrasonic parameter adjustment based on real-time material feedback. Key industry players are accelerating their intellectual property strategies to secure competitive advantages, with a notable increase in filings related to hybrid systems that combine ultrasonic actuation with laser or mechanical guidance for multi-material environments (GE).
Looking ahead, the outlook for guided ultrasonic drilling technologies remains strong. Continuous improvements in sensor integration, AI-driven guidance, and adaptive control are expected to yield systems capable of self-optimizing performance across diverse operational settings. As regulatory approvals for medical and aerospace applications advance, wider adoption is anticipated. The next few years will likely see guided ultrasonic drilling evolve from specialized use cases to a broader industrial and clinical standard.
Current Market Size and 2025–2030 Forecasts
Guided ultrasonic drilling technologies, leveraging high-frequency mechanical vibrations to enhance penetration rates and precision, are gaining traction in industrial and energy sectors. As of 2025, the market is still emerging but demonstrates rapid growth potential, propelled by increasing demand for advanced drilling solutions in sectors such as oil & gas, geothermal, aerospace, and medical device manufacturing. The capability of ultrasonic techniques to drill harder materials with reduced tool wear and greater accuracy positions them as a disruptive alternative to conventional rotary drilling methods.
Major players such as Baker Hughes and Schlumberger are actively investing in research and pilot deployments of guided ultrasonic drilling systems, particularly geared towards downhole applications where steering accuracy and minimal formation damage are critical. These companies have reported successful field trials for ultrasonic-assisted drilling bits, which have demonstrated up to 30% improvement in rate of penetration (ROP) and significant extension of bit life in hard rock formations compared to standard rotary systems.
The current global market size for guided ultrasonic drilling technologies is estimated to be in the low hundreds of millions USD, predominantly concentrated in North America and select European and Middle Eastern regions where high-value drilling operations justify the adoption of advanced solutions. Market adoption is expected to accelerate between 2025 and 2030, with CAGR projections ranging from 18% to 25%, driven by the expanding applicability of the technology in geothermal well construction, carbon capture and storage (CCS) wells, and precise borehole creation for aerospace structural components.
In the next five years, further commercialization is anticipated as companies such as Halliburton continue to develop integrated guidance, real-time feedback, and automation for ultrasonic drilling assemblies. The convergence of ultrasonic energy with digital downhole sensors and AI-driven steering algorithms is expected to unlock new levels of drilling efficiency and real-time formation evaluation. Several pilot projects slated for late 2025 and 2026 aim to validate these integrated systems in complex environments, which could catalyze broader industry adoption by 2030.
Looking ahead, the outlook for guided ultrasonic drilling technologies remains strongly positive, contingent upon continued field validation and cost reductions. As deployment scales, both capital and operational expenditures are expected to decrease, further widening the addressable market. Regulatory focus on efficient, low-environmental-impact drilling is also expected to bolster adoption, positioning ultrasonic guidance as a transformative technology in the global drilling landscape.
End-User Applications: Energy, Manufacturing, and Beyond
Guided ultrasonic drilling technologies are experiencing significant advancements and adoption across diverse end-user sectors, particularly within energy and advanced manufacturing. These systems leverage high-frequency mechanical vibrations to enhance drilling efficiency, precision, and material adaptability. As of 2025, the energy industry—especially oil & gas and geothermal—continues to drive much of the commercial deployment and field testing of guided ultrasonic drilling solutions.
In the oil & gas sector, leading companies are integrating ultrasonic drilling modules with traditional rotary drilling assemblies to improve rate of penetration (ROP), reduce bit wear, and enable access to harder or unconventional formations. Schlumberger has publicly demonstrated pilot projects employing guided ultrasonic tools to augment well construction, reporting improved borehole quality and lower non-productive time. Similarly, Baker Hughes has explored hybrid systems that synchronize ultrasonic actuation with real-time downhole guidance, enhancing accuracy during extended reach drilling and sidetracking operations.
The geothermal sector is another focal point for guided ultrasonic drilling, as the technology offers a pathway to economically access high-temperature, hard-rock reservoirs. Companies like Halliburton have collaborated with public research institutes to pilot ultrasonic drilling heads, noting promising results in terms of reduced tool failure and accelerated drilling through crystalline rock. With rising demand for renewable energy and the global push for decarbonization, the geothermal application space is projected to see continued investment and field validation of these advanced tools through 2025 and beyond.
In advanced manufacturing, guided ultrasonic drilling is increasingly adopted for precision machining of aerospace components, medical devices, and semiconductors. Manufacturers such as SONXTECH and Ultrasonic Systems offer turnkey solutions for automated guided ultrasonic machining, enabling the processing of brittle or composite materials with minimal microcracking and superior dimensional control. With the growth in demand for lightweight, high-performance materials in automotive and aerospace industries, these technologies are expected to gain further traction.
Looking ahead, ongoing R&D and cross-sector collaboration are anticipated to yield further gains in tool robustness, control software, and data-driven process optimization. As digitalization and automation continue to permeate both energy and manufacturing sectors, guided ultrasonic drilling is positioned to become a key enabling technology for next-generation subsurface access and precision fabrication.
Competitive Landscape and Strategic Partnerships
The competitive landscape for guided ultrasonic drilling technologies is rapidly evolving in 2025, as established drilling equipment manufacturers and innovative technology firms race to commercialize advanced guided ultrasonic systems. These technologies, which leverage high-frequency ultrasonic vibrations to enhance rock penetration and directional control, are being integrated into both conventional and automated drilling platforms across energy, mining, and construction sectors.
Key industry players such as Baker Hughes and Halliburton are actively developing and patenting guided ultrasonic drilling modules, aiming to improve drilling efficiency and reduce non-productive time (NPT) in challenging subsurface environments. In 2024 and early 2025, Schneider Electric announced strategic investments in real-time monitoring and control systems specifically designed to integrate with ultrasonic drilling heads, giving operators enhanced feedback for precision drilling and wellbore steering.
Emerging technology firms such as Sonimat and Ultrasonic Systems have formed alliances with major oilfield service providers to jointly trial guided ultrasonic prototypes in both onshore and offshore projects. These partnerships are focused on validating the operational reliability, bit life extension, and potential for lower carbon footprints due to reduced energy input requirements. Notably, Sandvik has initiated collaborations with academic institutions and battery minerals exploration companies to adapt guided ultrasonic drilling for hard-rock lithium and rare earth element extraction, reflecting the technology’s versatility beyond traditional hydrocarbon targets.
Strategic partnerships are also extending to digitalization and automation. Siemens and Honeywell are integrating their industrial automation platforms with ultrasonic drilling controls, allowing remote operation and real-time performance analytics. These collaborations aim to increase safety, minimize manual intervention, and enable autonomous drilling workflows, which are priorities in both high-risk environments and remote locations.
Looking ahead to the next few years, competitive dynamics are expected to intensify as pilot projects transition to large-scale commercial deployments. Companies are prioritizing intellectual property protection and cross-sector alliances to accelerate market adoption. As regulatory agencies and industry consortia, such as American Petroleum Institute, develop safety and interoperability standards for guided ultrasonic drilling, the landscape will likely favor those with robust R&D pipelines and established field-testing partnerships. The sector’s trajectory indicates that by 2027, guided ultrasonic drilling technologies will be an integral part of advanced drilling solutions, with cross-industry applications and a strong foundation of strategic collaborations.
Regulatory Standards and Industry Guidelines
Guided ultrasonic drilling technologies are increasingly gaining prominence in industrial sectors such as aerospace, energy, and advanced manufacturing. As adoption accelerates, the development and enforcement of regulatory standards and industry guidelines have become pivotal to ensure safety, interoperability, and performance consistency. In 2025, oversight and standardization efforts are being shaped by a combination of international standards organizations, governmental agencies, and industry consortia.
The International Organization for Standardization (ISO) plays a significant role in setting the benchmark for ultrasonic testing and drilling apparatus. Standards such as ISO 16810 (non-destructive testing—ultrasonic testing—terminology) and ISO 13585 (non-destructive testing of welds—ultrasonic testing—technique testing) are being referenced and, in some cases, updated to account for the nuances of guided ultrasonic applications in drilling. In addition, the International Electrotechnical Commission (IEC) is actively engaged in harmonizing electrical safety and electromagnetic compatibility standards for ultrasonic equipment, which is critical given the integration of sensors and real-time guidance systems within these platforms.
In the United States, the American Society for Nondestructive Testing (ASNT) continues to provide recommended practices and certification frameworks for operators and equipment in the ultrasonic domain. Their standards, including ASNT SNT-TC-1A for personnel qualification and certification, are being adapted by manufacturers of guided ultrasonic drilling systems to ensure that field personnel can safely and effectively deploy these technologies. Similarly, in Europe, the European Committee for Standardization (CEN) is working to align its EN series standards with emerging ultrasonic drilling capabilities to facilitate cross-border acceptance and market access.
Industry groups such as the American Petroleum Institute (API) and the Aerospace Industries Association (AIA) are collaborating with technology developers and end-users to devise application-specific guidelines, particularly for downhole drilling and composite material fabrication, respectively. These guidelines address not only technical performance but also environmental considerations and data interoperability requirements.
Looking ahead, the next few years are expected to see the introduction of specialized standards tailored to guided ultrasonic drilling, reflecting advances in automation, artificial intelligence integration, and remote operation. Stakeholders anticipate that regulatory alignment will streamline the commercialization process and enhance user confidence, while also supporting safe scaling of this innovative drilling technology across diverse industrial environments.
Challenges, Risks, and Limitations
Guided ultrasonic drilling technologies, which harness high-frequency vibrations to enhance the penetration and precision of drilling processes, have gained traction in sectors such as aerospace, energy, and advanced manufacturing. Despite notable advances and pilot deployments in 2025, several challenges, risks, and inherent limitations still constrain their wider adoption and full industrialization.
A principal technical challenge remains process control and repeatability. Ultrasonic drilling systems, especially those designed for guided or steerable applications, require precise synchronization between ultrasonic vibrations and the mechanical feed. Variations in material composition, thickness, and heterogeneities can lead to inconsistent cutting rates, tool wear, and surface finish. Manufacturers like Sonimat and Weber Ultrasonics emphasize the need for advanced sensor integration and closed-loop feedback systems to maintain process stability, but such systems increase complexity and cost.
Another critical limitation is tool durability. Ultrasonic transducers and drill bits are subject to accelerated wear due to combined mechanical and vibrational stresses, especially when operating in hard or abrasive materials such as ceramics, composites, or geological formations. This can lead to higher maintenance cycles and unexpected downtime. Some suppliers are actively developing advanced tool materials and coatings, yet as of 2025, the operational lifespan of ultrasonic drill bits still trails that of conventional superabrasive tools in many demanding scenarios.
Economic risks also remain significant. Initial capital investment in guided ultrasonic drilling systems is substantially higher than for traditional mechanical drilling equipment. Integration with existing manufacturing or drilling workflows requires substantial process reengineering, operator retraining, and in some cases, facility upgrades. As noted by Sonotronic, potential users cite concerns over return on investment and long-term support for these relatively novel systems.
Operationally, the technology faces limitations in scalability and applicability. While ultrasonic-assisted drilling excels in applications demanding high precision or minimal thermal/mechanical stress—such as micro-drilling in brittle materials—it is less effective for large-diameter or deep-hole applications. The energy required to maintain high-frequency vibrations over extended drill lengths increases disproportionately, leading to efficiency losses and system overheating.
Looking to the next few years, further progress hinges on robust material developments, digital process optimization, and demonstrable lifecycle cost savings. Industry bodies and leading manufacturers are collaborating on standardization and interoperability initiatives to address these bottlenecks. Nonetheless, until these technical and economic barriers are more fully overcome, guided ultrasonic drilling will likely remain a specialized—rather than ubiquitous—solution in industrial drilling and manufacturing landscapes.
Future Outlook: Next-Gen Ultrasonic Drilling Technologies
Guided ultrasonic drilling technologies are poised to become a transformative force in precision manufacturing and advanced materials processing by 2025 and in the years immediately following. These systems leverage high-frequency ultrasonic vibrations—often in the range of 20-40 kHz—combined with advanced guidance mechanisms, such as robotic arms and computer vision, to achieve unprecedented accuracy in drilling complex geometries, delicate substrates, and composite materials. The integration of real-time guidance is especially critical for sectors like aerospace, automotive, and medical device manufacturing, where tolerances are tight and material integrity is paramount.
Recent demonstrations and pilot deployments have shown marked improvements in hole quality, reduced delamination in composites, and significant decreases in tool wear compared to conventional mechanical or abrasive drilling. Companies such as SONOTRONIC Nagel GmbH and Dukane are actively developing ultrasonic drilling systems with integrated guidance modules, targeting automated production lines and robotic workcells. These systems can dynamically adjust drilling trajectories based on feedback from force sensors and optical monitoring, enabling adaptive machining in response to material inconsistencies or part misalignment.
The outlook for 2025–2027 is shaped by several converging trends. First, the growing adoption of composite and multi-material assemblies in aerospace and automotive applications is accelerating demand for drilling solutions that can handle brittle or layered substrates without causing microcracks or delamination. Second, the push for Industry 4.0-compliant manufacturing is driving investments in digitalized, data-driven process control—an area where guided ultrasonic systems, with their sensor-rich feedback loops, offer a compelling advantage. Third, advances in industrial robotics are lowering barriers to the deployment of guided ultrasonic heads on multi-axis platforms, allowing for more flexible and scalable machining cells.
- Aerospace: Aircraft OEMs and tier suppliers are increasingly specifying ultrasonic drilling for composite airframes. Airbus has highlighted the importance of novel drilling technologies to maintain structural integrity in next-generation jets.
- Medical devices: The demand for precision-drilled micro-features in implants and surgical tools is expected to support adoption of guided ultrasonic systems, with companies like Dukane collaborating with medical device OEMs.
- Energy and electronics: Ultrasonic drilling is being eyed for silicon, sapphire, and ceramics in battery and semiconductor manufacturing, with guidance systems enabling process repeatability.
Looking ahead, continued R&D and early commercial deployments are forecast to improve not only process accuracy and speed, but also to reduce operating costs and environmental impact by minimizing tool consumption and scrap. As digital manufacturing ecosystems mature, guided ultrasonic drilling is expected to play a central role in high-value, precision-driven industrial sectors.