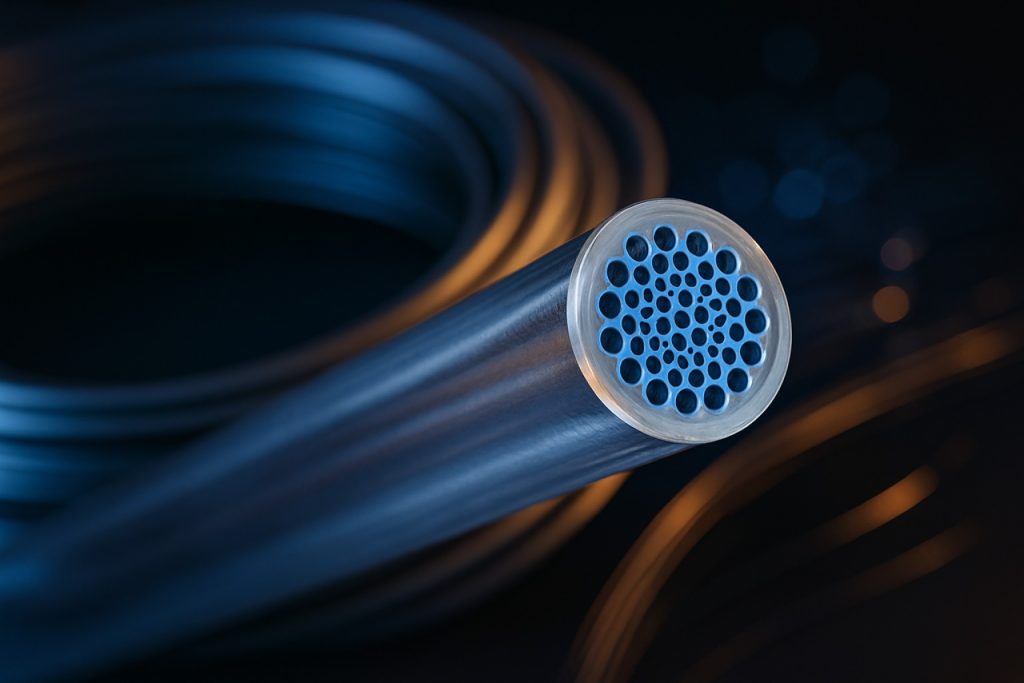
Table of Contents
- Executive Summary: 2025 Market Drivers and Key Insights
- Technology Overview: Zero-Dispersion Photonic Crystal Fiber Fundamentals
- Manufacturing Process Innovations and Leading Techniques
- Key Players & Company Strategies (e.g., nktphotonics.com, corning.com, fibercore.com)
- Current Market Size and 2025–2030 Growth Projections
- Emerging Applications: Telecom, Sensing, Medical, and More
- Competitive Landscape and Global Supply Chain Analysis
- R&D Frontiers: Material Science and Fabrication Advances
- Regulatory Landscape and Industry Standards (e.g., ieee.org, photonics.org)
- Future Outlook: Investment Opportunities and Disruption Scenarios
- Sources & References
Executive Summary: 2025 Market Drivers and Key Insights
The global market for zero-dispersion photonic crystal fiber (PCF) manufacturing is poised for significant momentum in 2025, driven by rapid advancements in optical communications, precision sensing, and high-power laser delivery. As demand for ultra-low dispersion and tailored light-guiding properties intensifies, manufacturers are expanding their capabilities to deliver highly customized PCF solutions. Zero-dispersion PCFs, engineered to minimize chromatic dispersion at specific wavelengths, are increasingly enabling breakthroughs in coherent optical communications, supercontinuum generation, and advanced biomedical instrumentation.
Key market drivers in 2025 include the growing deployment of next-generation data centers, 5G/6G infrastructure, and quantum technology platforms, all of which require fiber solutions with superior dispersion management. Companies such as NKT Photonics and Fujikura are at the forefront, leveraging proprietary stack-and-draw and extrusion fabrication techniques to achieve precise dispersion profiles and low-loss characteristics. These firms are scaling up production to meet the surging needs of telecom operators, research institutions, and medical device manufacturers.
2025 also sees increased collaboration between fiber suppliers and end-users to co-develop application-specific PCF designs, especially for supercontinuum sources and high-power fiber lasers. The integration of advanced process control, real-time monitoring, and improved preform fabrication is enabling higher consistency and yield in commercial manufacturing lines. Notably, innovation in raw material purity and structured preform design, led by manufacturers like Corning, is contributing to reduced attenuation and enhanced performance in zero-dispersion PCFs.
From a regional perspective, Asia-Pacific remains a hotbed of investment and production expansion, particularly in Japan and China, as domestic companies strengthen their R&D and vertical integration. European firms continue to focus on high-value custom fibers for research and industrial markets, while North America is witnessing increased activity tied to quantum networking and sensor development.
Looking ahead to the next few years, market outlook remains robust. Investments in scalable, automated manufacturing infrastructure are expected to lower production costs and shorten lead times. As new fields such as precision spectroscopy, mid-infrared photonics, and quantum key distribution mature, demand for zero-dispersion PCFs is projected to grow. Industry partnerships and standardization efforts, guided by organizations like IEEE, will further streamline adoption and accelerate innovation across sectors. The convergence of advanced materials, process automation, and end-user collaboration positions the zero-dispersion PCF manufacturing market for sustained growth and technological leadership through 2025 and beyond.
Technology Overview: Zero-Dispersion Photonic Crystal Fiber Fundamentals
Zero-dispersion photonic crystal fibers (PCFs) represent a transformative evolution within the specialty optical fiber domain, offering unique dispersion management capabilities vital for advanced telecommunication, sensing, and nonlinear optics applications. Manufacturing these fibers is a complex process, requiring precision engineering and advanced materials science innovations. As of 2025, the industry has witnessed significant progress in both fabrication techniques and production scalability, driven by the growing demand for fibers with customizable dispersion properties.
The core of zero-dispersion PCF manufacturing lies in the precise arrangement of air holes running along the fiber length, which define the photonic bandgap and, thus, the fiber’s dispersion profile. The most common production method is the stack-and-draw technique, where a preform—composed of stacked capillary tubes and rods made from high-purity silica—is drawn into fiber under carefully controlled thermal conditions. Advances in this process, particularly in controlling the uniformity and geometry of air hole structures, have enabled manufacturers to achieve zero-dispersion wavelengths (ZDWs) at desired points across the visible and near-infrared spectra.
Leading manufacturers such as NKT Photonics and LEONI FiberTech have invested heavily in refining draw-tower processes to minimize structural imperfections that could compromise fiber performance. These companies utilize rigorous online quality monitoring and computerized feedback loops to ensure consistent air hole diameter and pitch, both critical parameters for achieving zero-dispersion at target wavelengths. NKT Photonics in particular has pioneered the development of endlessly single-mode PCFs, which maintain low loss and controlled dispersion even when scaled to kilometer lengths, facilitating their integration into commercial systems.
Material purity remains another key focus area. High-grade synthetic silica is commonly used to minimize attenuation and optimize optical properties. Some manufacturers are exploring novel dopants and modified glass compositions to further tweak dispersion characteristics and enhance mechanical durability. Cleanroom environments and advanced preform preparation techniques are now standard across leading industrial facilities, ensuring reproducible results at higher volumes.
Looking ahead, the next few years are expected to bring further automation to PCF production, with greater integration of artificial intelligence and machine learning for defect detection and process optimization. Industry stakeholders anticipate a shift toward broader adoption of zero-dispersion PCFs in quantum optics and biomedical imaging, prompting additional investments in scalable, cost-effective manufacturing lines. As global market needs for high-bandwidth, ultra-low-dispersion transmission grow, the sector is poised for continued expansion, with established players such as NKT Photonics and LEONI FiberTech setting benchmarks in both quality and innovation.
Manufacturing Process Innovations and Leading Techniques
The manufacturing of zero-dispersion photonic crystal fibers (PCFs) in 2025 is driven by advances in precision fabrication and material control, responding to the stringent demands of telecommunications, quantum technologies, and advanced sensing. Zero-dispersion PCFs, engineered to achieve vanishing chromatic dispersion at targeted wavelengths, require highly controlled microstructured claddings and core geometries. This has pushed the boundaries of both preform fabrication and fiber drawing processes in recent years.
Key manufacturers have refined the stack-and-draw technique, which remains the primary approach for assembling the intricate arrays of air holes that define a PCF’s dispersion profile. The process involves stacking silica capillaries and rods into a preform, which is then fused and drawn into fiber. Innovations now include automated stacking robots for higher reproducibility, real-time shape monitoring during draw, and advanced pressure control to maintain air-hole integrity, minimizing geometric deviations that could compromise zero-dispersion properties.
Companies such as NKT Photonics and LEONI are recognized for producing specialty PCFs and have recently reported improvements in fabrication consistency and scalable production. NKT Photonics, for example, has highlighted its use of proprietary draw towers and online measurement systems that enable dynamic adjustment of draw parameters, ensuring the air-hole lattice remains within sub-micron tolerances—critical for achieving the desired zero-dispersion point. LEONI, on the other hand, has focused on material purity and surface finish in their preform assembly, reducing scattering losses and improving long-term fiber reliability.
Another significant innovation is the adoption of novel materials and dopants. While pure silica remains the baseline, companies are exploring fluorine doping and tailored glass compositions to extend zero-dispersion wavelengths into new spectral regions, particularly for mid-infrared and visible light applications. This trend is anticipated to accelerate through 2025, with research collaborations between manufacturers and glass suppliers seeking to expand the application range of zero-dispersion PCFs.
Looking ahead, automation and in-line metrology are expected to further reduce defects and enhance batch-to-batch consistency, a prerequisite for wider deployment in quantum communication and next-generation data centers. Industry leaders, including Furukawa Electric and Corning, are investing in these process improvements, signaling a maturing technology ready for broader commercial adoption in the next few years.
Key Players & Company Strategies (e.g., nktphotonics.com, corning.com, fibercore.com)
The global landscape of zero-dispersion photonic crystal fiber (PCF) manufacturing in 2025 is shaped by a select group of specialized companies, each leveraging advanced technologies and strategic partnerships to address the rising demand for ultra-low dispersion and customizable fiber solutions. Key players include NKT Photonics, Corning Incorporated, and Fibercore, all of which are notable for their robust R&D capabilities, proprietary fabrication methods, and long-standing expertise in specialty fiber production.
NKT Photonics continues to be a technological leader, offering a comprehensive portfolio of PCFs with tailored zero-dispersion wavelengths for applications in supercontinuum generation, quantum optics, and high-resolution spectroscopy. Their strategy centers on vertical integration of fiber design, preform fabrication, and in-house drawing processes, which enables precise control over geometric parameters and dispersion profiles. In 2025, NKT is expanding its production capacity and enhancing quality assurance to support growing orders from research institutions and OEMs in Europe, North America, and Asia.
Corning Incorporated, renowned for its large-scale optical fiber production and innovation in glass science, has invested heavily in PCF technology, particularly zero-dispersion variants suitable for telecommunications and sensing. Corning’s approach combines investment in advanced material engineering with strategic collaborations, focusing on scalable manufacturing and reliability. Their recent initiatives target integration with next-generation photonic devices and the development of fibers with improved polarization and loss characteristics, signaling a push into new verticals such as data centers and biomedical diagnostics.
Fibercore specializes in specialty optical fibers, including zero-dispersion PCFs, with a strong emphasis on customization for niche applications such as distributed sensing and high-precision metrology. In the current market environment, Fibercore’s strategy is to build flexible manufacturing systems capable of small-batch, rapid-turnaround orders, responding to the increasing demand for application-specific dispersion profiles and novel core structures. The company is also investing in collaborative R&D with universities and industry partners to accelerate innovation and expand its patent portfolio.
Looking ahead, these key players are expected to intensify their focus on automation, digitalization of manufacturing processes, and sustainable material sourcing. The outlook for 2025 and beyond includes heightened competition, especially as emerging photonics firms in Asia ramp up capabilities, and a growing emphasis on eco-friendly production and lifecycle management. As new applications in quantum technology, telecommunications, and environmental sensing materialize, leading manufacturers are likely to form strategic alliances and bolster their R&D to maintain a competitive edge in the evolving zero-dispersion PCF market.
Current Market Size and 2025–2030 Growth Projections
The market for zero-dispersion photonic crystal fiber (PCF) manufacturing is positioned for notable growth as global demand for high-performance optical fibers strengthens, particularly in telecommunications, sensing, and advanced laser systems. As of 2025, the PCF segment, while remaining a specialized niche within the broader optical fiber market, demonstrates increasing commercial traction. Key manufacturers and industrial players—including NKT Photonics and Thorlabs—report expanding portfolios of zero-dispersion PCF products, indicative of escalating end-user adoption across R&D and industrial sectors.
Current market estimates place the global value of zero-dispersion PCF manufacturing in the low hundreds of millions of USD, representing a small but rapidly expanding share of the specialty fiber sector. This growth is underpinned by heightened requirements for fibers with tailored dispersion profiles in fields such as ultrafast laser delivery, nonlinear optics, and broadband supercontinuum generation. The trend is further reinforced by the active involvement of organizations such as NKT Photonics, which has reported ongoing investments in new PCF fabrication technologies, and LEONI Fiber Optics, which has expanded its product range to include advanced microstructured fibers for industrial and scientific markets.
Looking ahead from 2025 through 2030, market forecasts anticipate a compound annual growth rate (CAGR) in the range of 7–10% for the zero-dispersion PCF sector, outpacing general optical fiber market averages. This acceleration is driven by continued innovation in fiber design and manufacturing processes, which enable better control over modal properties and dispersion characteristics. Emerging applications in quantum technologies, high-precision medical imaging, and environmental sensing are expected to further propel demand for zero-dispersion PCFs, encouraging manufacturers to scale up production capacity and invest in new fabrication infrastructure.
Regionally, Europe and Asia-Pacific are projected to remain at the forefront of both production and adoption, with leading suppliers such as NKT Photonics (Denmark) and Sumitomo Electric Industries (Japan) continuing to invest in next-generation manufacturing capability. North America, led by players like Thorlabs, is anticipated to see steady growth, supported by research-driven demand and increased integration of PCFs in advanced photonics platforms.
In summary, the zero-dispersion photonic crystal fiber manufacturing market is set to experience robust expansion through 2030, propelled by technological advancements, broadening application areas, and sustained investment from global industry leaders.
Emerging Applications: Telecom, Sensing, Medical, and More
Zero-dispersion photonic crystal fibers (ZDF-PCFs) are rapidly establishing their role in advanced technological sectors, driven by their unique ability to tailor dispersion characteristics and enhance nonlinear effects. As of 2025, momentum in manufacturing ZDF-PCFs is being shaped by increasing demands from telecom, sensing, and medical industries, as well as ongoing advances in fabrication techniques.
In telecommunications, ZDF-PCFs are being leveraged for high-capacity data transmission, low-latency networking, and robust signal integrity. The capacity to custom-engineer zero-dispersion wavelengths has allowed suppliers such as NKT Photonics and Thorlabs to provide specialty fibers that address chromatic dispersion limitations in both classical and quantum communication systems. Recent industry announcements emphasize the integration of ZDF-PCFs in coherent optical transmission platforms, enabling higher bit rates and longer repeaterless spans.
Sensing applications represent another fast-growing domain. ZDF-PCFs’ high nonlinearity and spectral broadening properties are being utilized in distributed temperature, strain, and gas sensing. Manufacturers like LEONI FiberTech are expanding their offerings of specialty PCFs for industrial monitoring, environmental hazard detection, and infrastructure health assessment. The next few years are expected to see further diversification, including compact sensor designs and integration with photonic chips for real-time analytics.
In the medical field, ZDF-PCFs are driving forward progress in biomedical imaging and laser surgery. Their tailored dispersion profiles support the generation of supercontinuum light sources, which underpin advanced imaging modalities such as optical coherence tomography (OCT). Companies such as NKT Photonics are actively developing ZDF-PCFs for biophotonics, facilitating high-resolution, deep-tissue imaging, and spectroscopic diagnostics. Continued progress in biocompatible fiber coatings and miniaturized devices is anticipated throughout 2025 and beyond.
Looking forward, the ZDF-PCF manufacturing landscape is expected to benefit from greater automation, improved preform fabrication, and tighter process controls. Industry players, including NKT Photonics, LEONI FiberTech, and Thorlabs, are investing in scalable production lines to meet rising quality and volume requirements. As applications extend into quantum technologies, ultrafast optics, and environmental monitoring, the coming years are set to witness further collaboration between manufacturers, system integrators, and end users, propelling ZDF-PCFs into new realms of performance and functionality.
Competitive Landscape and Global Supply Chain Analysis
The competitive landscape of zero-dispersion photonic crystal fiber (PCF) manufacturing in 2025 is characterized by a small cohort of highly specialized companies with advanced capabilities in fiber design and material processing. This niche market is driven by the demand for ultra-broadband optical communications, high-precision sensing, and ultrafast laser applications, all of which benefit from the unique dispersion properties of PCFs. Key players include NKT Photonics (Denmark), Fujikura (Japan), and Yangtze Optical Fibre and Cable Joint Stock Limited Company (YOFC) (China), each leveraging proprietary methods and vertically integrated production lines to ensure high purity, structural precision, and consistency.
Manufacturing zero-dispersion PCFs requires advanced stack-and-draw techniques, combined with rigorous quality control to achieve the necessary air-hole lattice structures and core geometries. Recent investments in automation and process monitoring have enabled manufacturers to improve yields and reduce defect rates. For example, NKT Photonics has reported ongoing enhancements in their fiber drawing towers to support higher throughput and improved reproducibility, addressing growing demands from research and industrial sectors.
The global supply chain for zero-dispersion PCF manufacturing remains relatively concentrated, with most production taking place in Europe and Asia. Material sourcing, particularly for high-purity silica preforms, has been robust due to established suppliers and long-term contracts. However, the need for specialized equipment and skilled labor continues to pose challenges for new entrants, reinforcing the dominant positions of established suppliers such as Fujikura and YOFC.
Geopolitical tensions and export control regulations have prompted some manufacturers to consider localized supply chains and enhanced inventory strategies. In 2025, several companies are increasing their focus on regional manufacturing hubs and strategic partnerships to mitigate supply risks, particularly for customers in telecommunications and defense. As an example, YOFC has expanded its production capacity in China and initiated collaborative projects with domestic research institutes to accelerate technology transfer and product development.
Looking forward, the competitive landscape is expected to remain relatively stable through the next few years, with incremental improvements in process automation and material science driving modest capacity growth. Strong intellectual property portfolios and close customer relationships are likely to preserve market positions for established leaders. However, demand for new applications—such as quantum communications and advanced biomedical imaging—could spur further investment and possible entry of new players with disruptive technologies.
R&D Frontiers: Material Science and Fabrication Advances
Research and development in zero-dispersion photonic crystal fiber (PCF) manufacturing have accelerated into 2025, as both academic and industrial players focus on advancing materials science and fabrication technologies. The drive stems from expanding applications in supercontinuum generation, precision metrology, and advanced optical communications, all of which benefit from PCFs engineered for zero or near-zero chromatic dispersion at specific wavelengths.
One of the key frontiers is the refinement of silica and alternative glass materials with ultra-high purity and tailored refractive indices. Major manufacturers such as NKT Photonics have continued to innovate in stack-and-draw fabrication, optimizing air-hole geometry and lattice pitch to precisely control dispersion characteristics. In 2025, efforts have intensified on achieving tighter tolerances at the preform stage, utilizing advanced automated stacking and real-time dimensional feedback during the fiber drawing process. These advances have enabled repeatable production of PCFs with zero-dispersion wavelengths (ZDWs) tuned to customer requirements, particularly in the visible and near-infrared regions.
Material science breakthroughs are also emerging from collaborations between fiber producers and specialty glass suppliers. Heraeus and Corning Incorporated are exploring doped silica and novel soft glass compositions, which allow for dispersion engineering beyond what is possible with pure silica. This enables the fabrication of PCFs with ZDWs shifted further into the mid-infrared, opening new possibilities for sensing and medical diagnostics.
A significant R&D focus has been on minimizing structural imperfections such as air-hole collapse and surface roughness, both of which can compromise dispersion profiles. Advanced inspection systems and closed-loop control during drawing, as implemented by companies like LEONI Fiber Optics, are helping to ensure the fidelity of microstructured designs at scale. These systems employ machine learning algorithms for defect prediction and process optimization, leading to higher yields and lower manufacturing costs.
Outlook for the next few years points to increased integration of additive manufacturing and laser-assisted structuring techniques, which promise even greater flexibility in PCF design. Industry leaders anticipate that by 2027, hybrid approaches combining conventional stack-and-draw with 3D microprinting could enable rapid prototyping of custom PCFs with complex, application-specific dispersion profiles. As demand grows for broadband and tunable light sources in quantum technologies and biophotonics, the pace of innovation in zero-dispersion PCF manufacturing is expected to remain robust, with ongoing contributions from both established manufacturers and emerging players.
Regulatory Landscape and Industry Standards (e.g., ieee.org, photonics.org)
The regulatory landscape and industry standards for zero-dispersion photonic crystal fiber (PCF) manufacturing are rapidly evolving to accommodate advances in fiber design, fabrication techniques, and application requirements. As of 2025, the sector is witnessing ongoing efforts to harmonize technical specifications and quality benchmarks, driven primarily by the increasing deployment of PCFs in telecommunications, sensing, and nonlinear optics.
Key standardization bodies are actively shaping the framework within which zero-dispersion PCFs are produced and qualified. The Institute of Electrical and Electronics Engineers (IEEE) continues to play a pivotal role through its Photonics Society, which coordinates working groups dedicated to optical fibers and integrated photonics. IEEE standards, such as those addressing characterization methods for dispersion and attenuation, form the backbone for interoperability across global supply chains.
The Optica (formerly OSA) also contributes by publishing consensus-driven recommendations and best practices, with a focus on measurement accuracy and reporting protocols for specialty fibers, including zero-dispersion PCFs. Such guidance is critical as manufacturers strive to ensure product consistency and reliability for demanding applications in quantum communications and high-power laser delivery.
On the international front, the International Electrotechnical Commission (IEC) is working on updates to its IEC 60793 series—covering optical fiber definitions, test procedures, and product specifications—to better reflect the unique geometries and performance characteristics of PCFs. Collaboration between IEC, IEEE, and national standards bodies is expected to intensify in the next few years, aiming to close gaps related to microstructured cladding designs, zero-dispersion wavelength tolerances, and novel materials.
Industry stakeholders—including leading fiber manufacturers and equipment suppliers—are increasingly engaging with these organizations to shape the regulatory framework. Companies are also initiating internal qualification programs based on recommendations from standards bodies, anticipating that future procurement contracts will require documented compliance with updated guidelines.
Looking ahead, the regulatory outlook for zero-dispersion PCF manufacturing is set to become more rigorous, with anticipated advances in automated process monitoring, traceability, and environmental safety standards. The convergence of global standards will likely facilitate broader market acceptance and accelerate commercialization, especially in sectors where fiber performance and reliability are mission-critical. As the sector matures, continuous input from manufacturers, end-users, and standards organizations will remain essential to ensure that regulatory frameworks keep pace with technological innovation.
Future Outlook: Investment Opportunities and Disruption Scenarios
The future of zero-dispersion photonic crystal fiber (PCF) manufacturing is poised for significant technological advancement and commercial expansion through 2025 and the following few years. As demand intensifies in sectors such as high-speed telecommunications, quantum optics, and advanced sensing, zero-dispersion PCFs offer unique advantages in managing signal integrity and minimizing nonlinear effects. The global push for faster, more reliable data transmission and precision instrumentation is driving both investment and disruptive innovation within this specialized segment of fiber optics.
In 2025, leading industrial fiber manufacturers and research-driven firms are expected to increase capital allocation toward R&D and pilot production lines for zero-dispersion PCFs. Key players such as NKT Photonics and Fujikura have already demonstrated cutting-edge fabrication processes with sub-micron tolerances and scalable draw-tower systems, setting industry benchmarks for both performance and manufacturability. Investments are focused on refining stack-and-draw techniques, improving fiber uniformity, and reducing production costs—a necessary step to support broader commercial adoption beyond niche markets.
Meanwhile, government-backed programs in Europe and Asia are fostering collaborative innovation ecosystems, linking academic research with industrial prototyping facilities. For example, several consortia involving NKT Photonics and other European manufacturers are targeting the integration of zero-dispersion PCFs into next-generation data centers and medical imaging platforms. This public-private model is accelerating technology transfer and attracting venture capital, with expectations that first-to-market suppliers will secure advantageous positions in emerging application verticals.
The outlook is also shaped by potential disruption scenarios. The development of new glass materials, alternative hole-structure designs, and hybrid fiber architectures could rapidly shift competitive dynamics. If breakthroughs in mass-production techniques—such as automated preform stacking or real-time defect monitoring—materialize by 2026, barriers to large-scale adoption will diminish. Additionally, the convergence of PCF manufacturing with integrated photonics and silicon photonics foundries, as explored by firms like Fujikura, could introduce new modularity and cost efficiencies, fundamentally altering supply chain structures.
In summary, investment opportunities in zero-dispersion PCF manufacturing are closely tied to both incremental process improvements and the possibility of disruptive technology leaps. Strategic partnerships, intellectual property positioning, and early-mover advantages in application-driven markets will be decisive factors as the industry navigates the pivotal years ahead.