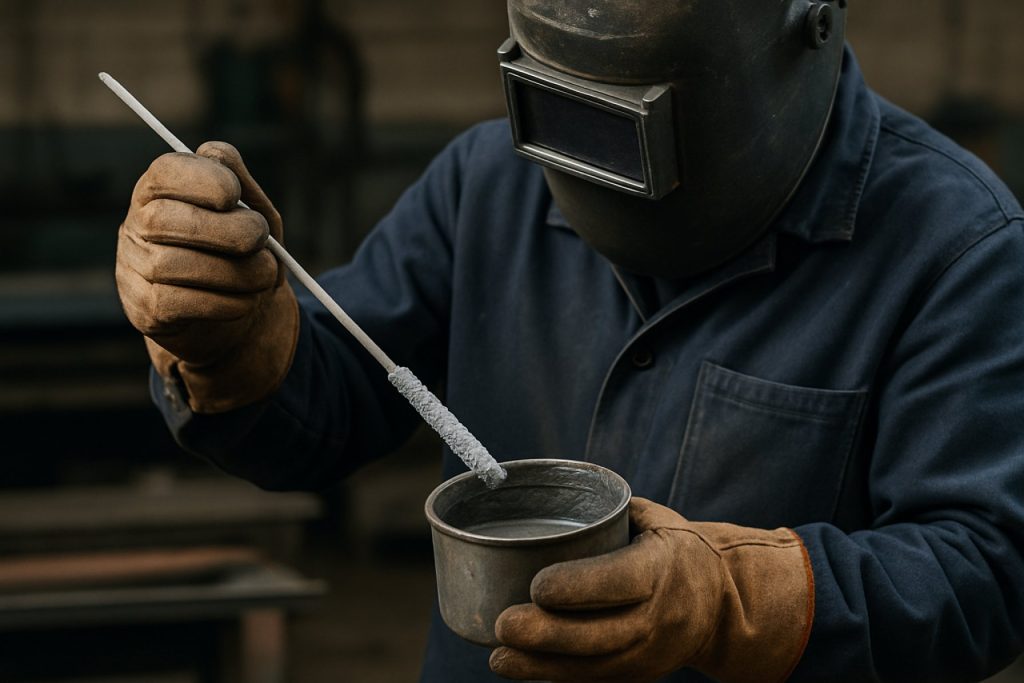
Table of Contents
- Executive Summary: Key Trends and Market Outlook (2025–2030)
- Global Market Forecast: Growth Drivers & Regional Hotspots
- Emerging Technologies in Electrode Coating Formulation
- Raw Materials: Sourcing, Sustainability, and Supply Chain Dynamics
- Regulatory Compliance and Industry Standards (AWS, ISO)
- Top Manufacturers and Strategic Partnerships (ESAB, Lincoln Electric, Bohler Welding)
- R&D Pipeline: Innovations in Performance and Cost Efficiency
- Applications Across Sectors: Construction, Energy, Automotive, and More
- Challenges: Environmental Impact, Costs, and Quality Assurance
- Future Outlook: Competitive Advantage and Long-Term Opportunities
- Sources & References
Executive Summary: Key Trends and Market Outlook (2025–2030)
The welding electrode coating formulation market is poised for significant evolution from 2025 through 2030, driven by advancements in materials science, sustainability imperatives, and increasing industry demand for high-performance welding solutions. Electrode coatings, which play a vital role in shielding the weld zone, stabilizing the arc, and improving weld quality, are witnessing innovation as manufacturers seek to balance performance, cost-efficiency, and environmental concerns.
A key trend in 2025 is the growing adoption of low-hydrogen and environmentally friendly coatings. Major electrode manufacturers are investing in new formulations that minimize hazardous emissions during welding operations and reduce the risk of weld defects such as porosity and cracking. The development and deployment of rutile, basic, and cellulose-based coatings are being refined with advanced additives and binders, providing enhanced mechanical properties and weld bead appearance. For example, leading producers such as Lincoln Electric and ESAB have highlighted their focus on sustainable electrode solutions, responding to stricter workplace safety and environmental regulations across North America, Europe, and Asia.
The integration of digitally enabled quality control and process automation is expected to shape electrode coating production. Companies are deploying real-time monitoring systems and data analytics to ensure uniform coating thickness, improved adhesion, and consistent chemical composition. This digital shift not only enhances product reliability but also reduces material waste and operational costs. Global players such as voestalpine and Kobe Steel are incorporating Industry 4.0 technologies to upgrade their electrode manufacturing lines and meet the rising demand for premium quality welding consumables.
Another noteworthy outlook for the coming years is the diversification of electrode coatings tailored for specialized applications, including high-strength steels, dissimilar metal welding, and offshore structures. There is growing interest in alloyed coatings that provide superior corrosion resistance and mechanical strength, especially for the oil & gas, shipbuilding, and infrastructure sectors. As industries continue to push the boundaries of material performance, electrode producers are expected to intensify their research into novel flux ingredients and nanomaterial enhancements.
Overall, the welding electrode coating formulation industry between 2025 and 2030 is characterized by innovation, regulatory adaptation, and the pursuit of sustainable, high-performance products. With ongoing investment from established manufacturers and a clear trend towards digitalization and customization, the sector is well positioned for robust growth and technological advancement in the near future.
Global Market Forecast: Growth Drivers & Regional Hotspots
The global market for welding electrode coating formulation is poised for steady growth through 2025 and into the following years, driven by rising industrialization, infrastructure expansion, and evolving manufacturing standards. The increasing demand for quality welded joints in construction, shipbuilding, automotive, and energy sectors is propelling advancements in electrode coatings, mainly to improve arc stability, deposition rates, and weld integrity.
Asia-Pacific continues to dominate as the largest and fastest-growing regional hotspot, led by countries such as China, India, and Southeast Asian economies. The region’s booming construction and manufacturing activities are fueling the need for sophisticated electrode technologies and reliable coating materials. Major industry players such as Lincoln Electric, ESAB, and voestalpine Böhler Welding have ramped up their presence and investments in the region to cater to surging demand and localize supply chains.
In North America and Europe, the market is shaped by a focus on automation, high-performance materials, and compliance with stringent environmental standards, especially regarding emissions from flux ingredients and hazardous substances in electrode coatings. Innovations in low-hydrogen and rutile-coated electrodes are gaining traction, as end-users seek formulations that minimize defects and enhance weld quality in critical infrastructure and energy applications. According to technical updates from ESAB and Lincoln Electric, R&D is increasingly focused on environmentally friendly binders and advanced alloying additives that optimize arc performance while reducing ecological impact.
Latin America, led by Brazil and Mexico, is expected to see moderate growth, buoyed by oil & gas and heavy engineering sectors. Meanwhile, in the Middle East and Africa, infrastructure projects and a gradual shift toward local manufacturing are expected to generate fresh demand for coated welding electrodes, especially those tailored for harsh operating environments and diverse base metals.
Growth drivers across all regions include the ongoing shift toward renewable energy infrastructure (wind, solar, hydropower), which requires advanced welding consumables for fabrication and maintenance. Additionally, the adoption of Industry 4.0 practices and the digitalization of welding operations are indirectly influencing electrode formulation requirements, with an emphasis on consistency, traceability, and adaptability to automated welding systems (voestalpine Böhler Welding).
Looking forward, with infrastructure and industrial investments projected to rise globally, the market for welding electrode coating formulations is set to witness incremental innovation, regional diversification, and sustained growth through 2025 and beyond.
Emerging Technologies in Electrode Coating Formulation
The field of welding electrode coating formulation is undergoing significant change in 2025, driven by advances in materials science, automation, and sustainability imperatives. Traditionally, electrode coatings have been based on rutile, basic (lime), or cellulose formulations, each offering unique weld characteristics and applications. However, the demand for improved performance, lower emissions, and cost-effectiveness is propelling the adoption of new technologies and approaches in this sector.
One major development is the integration of nanomaterials and advanced additives into coating formulations. The addition of nano-sized oxides and rare earth elements has been shown to enhance arc stability, increase deposition rates, and improve slag detachability, which is especially relevant for high-specification sectors such as offshore or pipeline welding. Leading manufacturers such as Lincoln Electric and ESAB are investing in research on such additives to optimize electrode performance and weld quality while reducing spatter and fumes.
Automation and digitalization are also shaping electrode coating production. Precision dosing systems and automated mixing technologies are being implemented to ensure consistent coating thickness and composition. Companies like voestalpine are incorporating digital process controls to enhance coating uniformity and reduce material waste, which not only improves final product quality but also aligns with the increasing emphasis on sustainability across the welding industry.
Environmental regulations continue to influence the formulation of welding electrode coatings. There is a clear trend toward lowering hazardous emissions, particularly of hexavalent chromium and other potentially toxic elements. Manufacturers are responding by reformulating coatings to exclude or minimize such substances, in line with evolving standards set by organizations like American Welding Society. This is prompting the adoption of alternative binders and fluxing agents that maintain weld performance while addressing health and safety concerns.
Looking ahead over the next few years, the outlook for welding electrode coating formulation includes further research into eco-friendly materials, such as bio-based binders and recycled minerals, and the development of “smart” coatings that can adapt to welding conditions. As the industry continues to converge on stricter quality and environmental benchmarks, the integration of advanced materials and manufacturing technologies is expected to accelerate, reinforcing the role of innovation in meeting the evolving needs of welding professionals worldwide.
Raw Materials: Sourcing, Sustainability, and Supply Chain Dynamics
The formulation of welding electrode coatings relies heavily on the continuous availability and quality of specific raw materials, such as rutile, ilmenite, calcite, feldspar, manganese ore, and various binders. In 2025, the global supply dynamics of these minerals are being shaped by shifting geopolitical alignments, sustainability requirements, and increasing demand from infrastructure and manufacturing projects. Leading electrode manufacturers are prioritizing secure, traceable supply chains, often diversifying their sourcing strategies to mitigate risks associated with regional disruptions and price volatility.
One of the primary materials, rutile (a titanium dioxide mineral), is experiencing heightened scrutiny due to environmental regulations in major producing countries. This has led manufacturers such as Lincoln Electric and ESAB to explore alternative sourcing locations and increase recycled content in their electrode coatings. Manganese ore, essential for certain low-hydrogen and high-strength electrode types, faces similar challenges, prompting companies to implement more robust supplier screening and invest in logistics resilience.
Sustainability is a growing priority, with electrode producers adopting responsible sourcing protocols aligned with global standards such as ISO 14001. For instance, voestalpine has publicized its commitment to reducing the carbon footprint of its welding consumables by integrating recycled and low-impact raw materials. The use of bio-based binders and fluxes is also under research, as manufacturers seek to lower emissions and address end-user demands for greener products.
Supply chain transparency is becoming more sophisticated, with digital tools enabling real-time tracking of raw materials from mine to manufacturing facility. This digitalization is helping companies like Böhler Welding to quickly adapt to market changes and maintain consistent quality in electrode coating blends. The trend towards localizing supply chains—particularly for critical minerals—continues, with several manufacturers investing in regional processing capabilities to reduce transportation emissions and increase resilience against international trade uncertainties.
Looking ahead, the outlook for raw material sourcing in welding electrode coating formulation remains closely tied to advancements in recycling technologies, regulatory developments, and the evolving demands of global manufacturing. Companies actively involved in electrode production are expected to deepen collaborations with mining and minerals processing firms to secure sustainable, high-purity inputs and to further reduce the environmental impact across their supply chains.
Regulatory Compliance and Industry Standards (AWS, ISO)
The formulation of welding electrode coatings in 2025 is intricately governed by a matrix of regulatory compliance requirements and industry standards, notably those established by the American Welding Society (AWS) and the International Organization for Standardization (ISO). These standards ensure that electrode coatings meet stringent criteria for safety, performance, and environmental impact. Companies and manufacturers must stay abreast of evolving regulations to maintain market access and uphold product reliability.
In the United States, the American Welding Society maintains a comprehensive suite of standards such as AWS A5.1 (for carbon steel electrodes) and AWS A5.4 (for stainless steel electrodes), which specify permissible chemical compositions, coating types, mechanical properties, and testing methods. These requirements are regularly updated to reflect advancements in welding metallurgy, changes in occupational safety norms, and the introduction of new coating technologies, such as low-hydrogen and environmentally friendly formulations. The AWS standards are widely recognized across North America and often serve as a reference point for manufacturers exporting to other regions.
Globally, ISO standards—particularly ISO 2560 (covered electrodes for manual metal arc welding of non-alloy and fine grain steels) and ISO 3580 (covered electrodes for manual metal arc welding of creep-resisting steels)—provide a harmonized framework for electrode coating formulations. These standards are increasingly adopted in Europe, Asia, and emerging markets, requiring manufacturers to synchronize their product development and quality control systems accordingly. ISO standards also emphasize traceability, consistent batch quality, and labeling requirements, which are becoming more critical as supply chains globalize.
In 2025, regulatory trends are also being shaped by heightened attention to environmental, health, and safety (EHS) considerations. For instance, the reduction of hazardous substances—such as hexavalent chromium or certain fluorides—in electrode coatings is a growing mandate, aligning with global initiatives like REACH in Europe. Manufacturers such as Lincoln Electric and ESAB continue to innovate in developing coatings that comply with these environmental directives while maintaining weld quality and operational efficiency.
Looking ahead, industry stakeholders anticipate further tightening of standards, particularly concerning the traceability of raw materials, emissions during welding, and recyclability of spent electrodes. This is likely to drive increased collaboration between standards bodies, manufacturers, and end users to develop coatings that are not only compliant but also optimized for emerging applications such as additive manufacturing and advanced high-strength steels.
Top Manufacturers and Strategic Partnerships (ESAB, Lincoln Electric, Bohler Welding)
In 2025, the global welding electrode market is being significantly shaped by the innovation and collaboration strategies of leading manufacturers, particularly in the area of electrode coating formulations. Companies such as ESAB, Lincoln Electric, and Bohler Welding (a brand of voestalpine Böhler Welding) are at the forefront of developing advanced coatings that enhance weld quality, improve productivity, and address evolving regulatory and environmental requirements.
The latest trends in electrode coating formulation focus on increasing deposition efficiency, reducing spatter, and achieving specific mechanical properties while minimizing hazardous emissions. For instance, ESAB continues to invest in proprietary flux compositions, with a growing emphasis on low-hydrogen and rutile-based coatings intended to meet stricter standards for weld integrity and operator safety. Their R&D efforts are increasingly directed at sustainability, including the reduction of hexavalent chromium and other potentially hazardous elements in coating materials.
Lincoln Electric has also intensified its efforts in electrode coating innovation, focusing on formulating coatings that enable high-performance welding in demanding sectors such as offshore, energy, and infrastructure. The company’s recent advances include the development of electrodes with enhanced arc stability and optimized slag release, which improve workflow efficiency and reduce post-weld cleaning time. Lincoln Electric’s ongoing collaborations with steel producers and end-users enable rapid prototyping and field validation of new coating technologies, reinforcing its position as a technology leader in the sector.
Meanwhile, Bohler Welding emphasizes tailored solutions in electrode coatings, targeting both common and highly specialized applications. Through strategic partnerships with major fabrication companies and industry consortia, Bohler has introduced electrodes with advanced alloying elements in the coating, supporting critical applications such as nuclear and cryogenic welding. Their focus on digitalization and process automation extends to electrode manufacturing, allowing for precise control over coating thickness and composition.
Looking ahead, the next few years will likely see further strategic partnerships across the supply chain, as material suppliers, research institutions, and fabricators work with manufacturers to co-develop coatings that meet emerging standards for strength, corrosion resistance, and environmental safety. With major players such as ESAB, Lincoln Electric, and Bohler Welding investing heavily in both formulation science and collaborative innovation, the electrode coating segment is poised for continued advancement in performance and sustainability.
R&D Pipeline: Innovations in Performance and Cost Efficiency
In 2025, the research and development (R&D) pipeline for welding electrode coating formulations is characterized by a dynamic blend of incremental improvements and disruptive innovations. The industry’s primary goals remain the enhancement of weld quality, reduction of production costs, and alignment with increasingly stringent environmental and safety standards. Market-leading manufacturers and industry consortia are focusing on both the refinement of traditional coatings and the exploration of novel materials for future-ready electrodes.
One significant trend in the R&D pipeline involves the optimization of flux compositions. Traditional coatings—such as rutile, basic, and cellulose-based formulations—are being systematically modified to improve arc stability, reduce spatter, and enhance slag detachability. For example, manufacturers like Lincoln Electric and ESAB are actively engaged in developing advanced flux recipes that incorporate microalloying elements and engineered mineral blends. These adjustments not only boost mechanical properties such as tensile strength and impact resistance but also offer improved weld bead appearance and reduced post-weld clean-up time.
Another focal point is the integration of sustainable and environmentally friendly materials into electrode coatings. With regulatory frameworks tightening around hazardous substances, R&D teams are assessing alternatives to traditional compounds like potassium silicate binders and fluorides. For instance, Böhler Welding is reportedly experimenting with bio-based binders and low-dust formulations that minimize airborne particulates during welding, addressing both worker safety and environmental impact.
Cost efficiency remains a critical driver, prompting the search for locally sourced minerals and recycled raw materials to reduce dependence on imported or volatile commodities. Several leading suppliers are investing in process innovations that enable the use of lower-cost additives without compromising electrode performance. This approach is particularly relevant in regions where supply chain disruptions or geopolitical factors impact access to traditional raw materials.
Looking ahead, the outlook for welding electrode coating formulation R&D in the coming years points towards further digitalization and the adoption of data-driven design. Manufacturers are leveraging advanced simulation tools and AI-assisted formulation platforms to rapidly prototype and test new compositions, shortening development cycles and facilitating customization for specific applications. Strategic collaborations between manufacturers, research institutions, and industry bodies, such as those promoted by American Welding Society, are expected to accelerate innovation and standardization across the sector. Collectively, these advancements signal a robust and forward-looking R&D landscape dedicated to marrying performance with cost and sustainability imperatives.
Applications Across Sectors: Construction, Energy, Automotive, and More
Welding electrode coating formulation plays a crucial role in determining the performance and suitability of electrodes across various industrial sectors. In 2025 and the coming years, advancements in coating technologies are expected to significantly influence applications in construction, energy, automotive, and other industries. The formulation of electrode coatings is tailored to meet the specific requirements of each sector, such as mechanical strength, corrosion resistance, and weld quality.
In the construction sector, the demand for high-strength, low-alloy steels and advanced fabrication techniques has pushed manufacturers to develop electrode coatings that enhance weld metal toughness and minimize hydrogen-induced cracking. Innovations in basic and rutile coating formulations are enabling more reliable performance in critical infrastructure, such as bridges and high-rise buildings. Leading electrode producers like Lincoln Electric and ESAB are actively introducing electrodes with improved moisture resistance and arc stability to address construction industry needs, particularly in regions with variable climate conditions.
In the energy sector, including oil and gas, renewable energy, and power generation, the focus is on electrodes that can withstand harsh environments and critical service conditions. Coatings incorporating alloying elements for improved corrosion and heat resistance are being formulated to meet stringent industry standards. For instance, Böhler Welding is developing specialized electrode coatings for power plant maintenance and offshore platforms, addressing the sector’s evolving material and regulatory requirements.
The automotive industry is experiencing rapid adoption of advanced high-strength steels and lightweight materials, necessitating electrode coatings that deliver precise weld bead profiles and minimal spatter. Coating formulations are increasingly being optimized for robotic and automated welding systems, supporting high-throughput manufacturing environments. Companies like Kobe Steel (KOBELCO) are focusing on low-fume, environmentally friendly coatings to align with automotive sustainability initiatives and worker safety regulations.
Beyond these sectors, applications in shipbuilding, railways, and heavy machinery manufacturing also benefit from tailored electrode coating formulations. The continual evolution in electrode chemistry enables manufacturers to address diverse welding challenges, from joining dissimilar metals to achieving superior mechanical properties in thick sections. With ongoing R&D investments and increasing demand for quality and sustainability, the next few years are expected to see further sector-specific innovations in welding electrode coatings, supporting productivity and compliance across industries.
Challenges: Environmental Impact, Costs, and Quality Assurance
The formulation of welding electrode coatings in 2025 faces a complex set of challenges, primarily centered around reducing environmental impact, controlling costs, and ensuring consistent quality assurance. As global environmental regulations tighten, especially regarding hazardous substances in manufacturing processes, the welding industry is under increasing pressure to reformulate coatings to minimize emissions of harmful gases, heavy metals, and particulates. For example, the restriction of certain elements such as chromium and fluoride—commonly found in some electrode coatings due to their beneficial welding properties—necessitates the search for alternative materials or advanced capture technologies that do not compromise weld quality.
Cost management is another significant hurdle. Prices for key raw materials, such as rutile, iron powder, and various mineral binders, have experienced volatility due to supply chain disruptions and increased demand across sectors. This volatility directly impacts the cost structure of coated electrodes. Manufacturers are exploring recycling and reprocessing scrap material to buffer these fluctuations, but integrating recycled content must be balanced against strict quality standards required by end users in critical industries such as automotive, shipbuilding, and infrastructure.
Quality assurance remains paramount, as even minor inconsistencies in coating thickness, composition, or moisture content can result in weld defects, reduced mechanical performance, and increased rework costs. To address this, companies are investing in automation, real-time process monitoring, and advanced material characterization techniques. The adoption of machine vision and inline sensors is gradually improving lot-to-lot consistency, allowing for tighter control over coating application and drying processes. For example, leading manufacturers like ESAB and Lincoln Electric are integrating digital quality management systems to ensure that welding electrodes meet global standards such as AWS and EN ISO.
Looking ahead, the industry outlook for the next few years suggests an acceleration in research and development focused on sustainable coating materials, such as bio-based binders and low-toxicity fluxes. Industry collaboration and partnerships with academic institutions are expected to play a key role in developing new chemistries that are both environmentally friendly and cost-effective, without sacrificing weld quality. At the same time, regulatory agencies and industry bodies—including American Welding Society—are expected to update standards to reflect advances in formulation science, pushing manufacturers to continually adapt. These converging drivers underscore the need for a balanced approach in electrode coating formulation, one that aligns environmental stewardship with operational efficiency and high-quality performance.
Future Outlook: Competitive Advantage and Long-Term Opportunities
The future outlook for welding electrode coating formulation in 2025 and the ensuing years is characterized by increasing technological sophistication, regulatory demands, and evolving end-user requirements, all of which are shaping the sector’s competitive dynamics and long-term opportunities. As key industries such as construction, automotive, shipbuilding, and energy infrastructure continue to demand higher productivity and improved weld quality, electrode manufacturers are focusing on advanced coating chemistries that deliver enhanced performance and compliance with tightening environmental standards.
One of the most significant trends is the accelerated development of low-hydrogen and environmentally friendly coatings. These formulations help mitigate hydrogen-induced cracking and reduce emissions of hazardous fumes, aligning with stricter occupational safety and environmental regulations anticipated in major markets. Leading electrode producers are investing in research to engineer coatings with improved arc stability, reduced spatter, and superior slag detachability, providing tangible productivity benefits to fabricators. For example, Lincoln Electric Holdings and ESAB have publicly discussed their commitment to electrode innovation, including flux compositions tailored for high-strength and specialty applications.
Digitalization and automation in welding processes are also influencing electrode coating development. The integration of Industry 4.0 solutions—such as real-time quality monitoring and automated storage/handling systems—requires electrodes with consistent coating integrity and predictable melting characteristics. This is driving manufacturers to refine their powder blending, extrusion, and curing methods to achieve tighter quality tolerances, as noted by companies like voestalpine Böhler Welding.
Long-term opportunities will likely emerge from the growing adoption of high-performance alloys and dissimilar material joining, especially as industries transition toward lighter-weight and more corrosion-resistant structures. Electrode coatings optimized for such materials—e.g., stainless steels, nickel-based alloys, and advanced high-strength steels—are expected to see higher demand. Companies with robust R&D capabilities and vertically integrated supply chains are poised to gain a competitive edge, as they can more quickly adapt formulations to meet specific customer and regulatory requirements.
Geographically, Asia-Pacific remains a major driver for volume growth, with investments in infrastructure and manufacturing. However, North America and Europe are setting the tone for regulatory compliance and sustainable manufacturing, prompting global suppliers to innovate accordingly. The competitive landscape will increasingly reward those able to deliver high-performance, compliant, and cost-effective electrode coatings, underscoring the importance of ongoing formulation advancements for sustained leadership in the welding consumables sector.