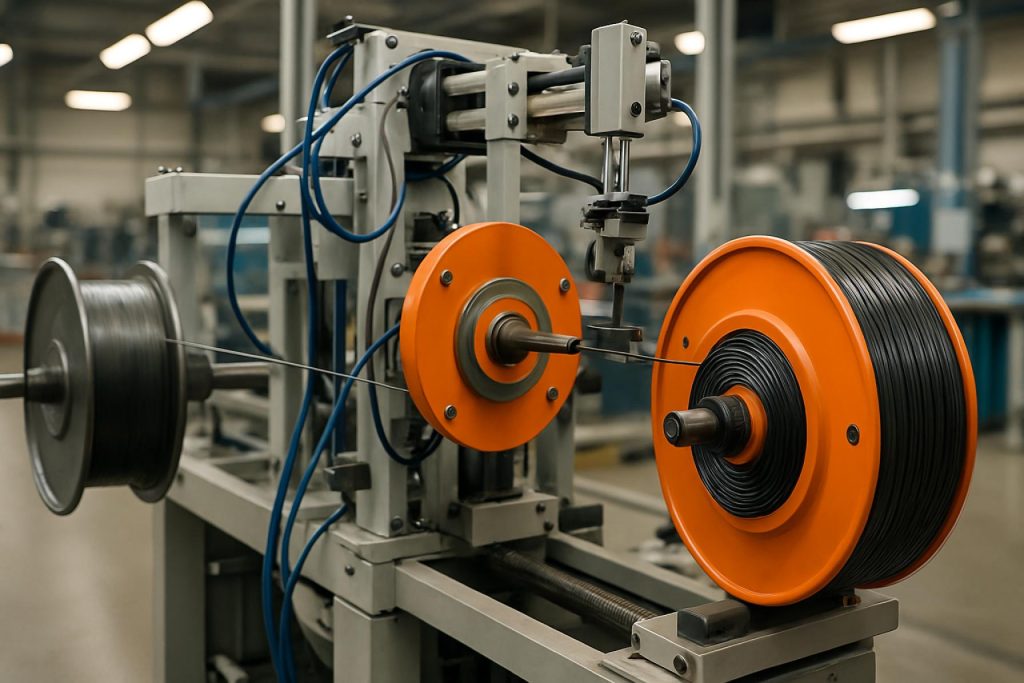
Table of Contents
- Executive Summary: Key Insights & Future Drivers
- Global Market Forecast: 2025–2028 Growth Trends
- Core Technologies Transforming Automation
- Leading Players & Company Innovations (e.g., ssm.ch, neewiremachine.com)
- AI & Smart Sensors: The New Heart of Wire Rewinding Systems
- Regional Analysis: Demand Hotspots & Manufacturing Hubs
- Sustainability & Energy Efficiency Advances
- Integration with Industry 4.0 and IoT
- Challenges, Risks, and Regulatory Landscape
- Strategic Outlook: Opportunities & Investment Priorities for 2025–2028
- Sources & References
Executive Summary: Key Insights & Future Drivers
The automation of wire rewinding machines is gaining momentum in 2025, driven by the increasing need for efficiency, precision, and safety across wire and cable manufacturing sectors. With the global demand for electrical wiring, data cables, and specialty wires on the rise—especially in automotive, renewable energy, and communications—manufacturers are investing heavily in automated solutions to enhance productivity and reduce manual intervention.
Key players such as Schlatter Group, Ziegler Metallbearbeitung, and SAMP S.p.A. are showcasing advanced wire rewinding systems equipped with programmable logic controllers (PLCs), integrated sensors, and Industry 4.0 connectivity. These features facilitate real-time monitoring, automated tension control, and predictive maintenance—drastically minimizing downtime and ensuring consistent coil quality. Recent installations in 2024 and early 2025 highlight a marked shift towards machines capable of remote diagnostics and automatic diameter adjustment, optimizing changeover times and throughput.
Safety regulations and labor shortages are also accelerating automation adoption. By integrating automated handling and quality inspection modules, companies reduce risks associated with manual rewinding and address workforce constraints, especially in regions experiencing demographic shifts. For instance, Mikrosam reports increased inquiries for fully automated rewinding lines tailored to composite wire and specialty cable sectors, aligning with broader trends toward smart manufacturing.
Another significant driver is the push for sustainability and material efficiency. Automated machines now commonly incorporate energy-saving drives and closed-loop control systems, reducing energy consumption and wire waste. Rosendahl Nextrom GmbH highlights its latest rewinding technologies, which offer precise layering and tension management, enabling customers to achieve higher yields from raw material inputs and minimize scrap.
Looking forward, the outlook for wire rewinding machine automation is robust. The convergence of digitalization, artificial intelligence, and advanced robotics is expected to unlock further gains in flexibility and customization. Integration with factory-wide MES (Manufacturing Execution Systems) platforms is anticipated to become standard, enabling end-to-end traceability and data-driven process optimization. As industries continue to prioritize efficiency, quality, and sustainability, automated wire rewinding is poised to remain a pivotal focus through the latter half of the decade.
Global Market Forecast: 2025–2028 Growth Trends
The global market for wire rewinding machine automation is poised for significant evolution during 2025–2028, driven by escalating industrial automation, increasing demand for precision winding in electronics, and continued modernization of wire and cable manufacturing. As manufacturers seek to improve efficiency and product quality, automated rewinding solutions are being integrated across sectors such as automotive, energy, telecommunications, and consumer electronics.
Leading manufacturers are actively investing in advanced automation technologies. For example, SCHNELL S.p.A., a prominent supplier of wire processing machinery, has expanded its automated rewinding solutions, emphasizing software-driven control, real-time monitoring, and remote diagnostics to reduce downtime and enhance productivity. Similarly, KOCH Industrieanlagen GmbH continues to develop fully automated rewinding systems with integrated quality inspection and digital connectivity, supporting Industry 4.0 initiatives.
In 2025, demand for high-precision winding—especially for fine wire used in electric vehicle (EV) motors, renewable energy systems, and miniaturized electronics—will fuel adoption of automated rewinding equipment. Companies like Ziegler Metallbearbeitung GmbH are responding with machines capable of handling ultra-thin wires, equipped with advanced tension control and adaptive speed regulation to minimize breakage and material waste.
- Electrification and Energy Transition: The global shift toward electrification and the expansion of renewable power infrastructure are increasing the need for high-quality wire coils, requiring consistent and efficient rewinding processes. Sampsistemi S.r.l. is targeting this segment with automated spoolers and rewinders tailored for solar, wind, and EV cable production.
- Smart Manufacturing Integration: Integration of IoT-enabled sensors and analytics into rewinding machines is a growing trend, providing predictive maintenance, traceability, and process optimization. Automatismes Sébastien offers rewinding solutions with real-time data acquisition and remote adjustment features.
- Regional Expansion: Asia-Pacific remains the fastest-growing market, with significant investments in wire and cable manufacturing automation, particularly in China, India, and Southeast Asia, as evidenced by the expansion strategies of companies such as Supermac Industries (India) Limited.
Looking ahead to 2028, the wire rewinding machine automation sector is expected to see continued growth, underpinned by advances in robotics, machine vision, and artificial intelligence for adaptive process control. The ongoing push for energy efficiency, product miniaturization, and zero-defect manufacturing will further accelerate the deployment of sophisticated automated rewinding solutions worldwide.
Core Technologies Transforming Automation
Wire rewinding machine automation is undergoing rapid transformation, driven by advancements in core technologies such as robotics, machine vision, Industrial Internet of Things (IIoT), and advanced motion control. As manufacturers strive to enhance production efficiency and product quality, these technologies are being increasingly integrated into new wire rewinding solutions in 2025 and are expected to dominate the landscape in the near future.
A significant shift is the adoption of robot-assisted processes for wire handling and spooling, which reduce manual intervention and enhance precision. Companies like Schleuniger AG have incorporated collaborative robotic arms into their rewinding lines, enabling high-speed, hands-free operation while minimizing the risk of wire damage or tangling. This integration not only increases throughput but also improves workplace safety and consistency.
Machine vision systems are another transformative element. Using advanced cameras and image processing, these systems can detect wire defects, ensure accurate layering during rewinding, and automatically correct misalignments in real time. SAMP S.p.A. has implemented vision-based quality control in its automated rewinding machines, allowing for continuous, non-contact inspection that minimizes waste and guarantees product integrity.
The IIoT is playing a pivotal role by enabling real-time monitoring and data analytics. Modern wire rewinding machines, such as those offered by Ziegler Metallbearbeitung GmbH, are now equipped with sensors that track parameters like tension, speed, and spool fill status. Data collected from these sensors is transmitted to centralized platforms, where predictive maintenance algorithms can forecast potential failures and schedule timely interventions, reducing unplanned downtime.
Advanced motion control technology—utilizing servo motors and precision drives—ensures smooth and accurate wire winding, even at high speeds or with delicate materials. KOCH Industrieanlagen GmbH demonstrates this with their programmable tension control systems, which automatically adjust for different wire types and diameters, supporting both flexibility and high-quality output.
Looking ahead, experts anticipate a convergence of these technologies with artificial intelligence (AI) for self-optimizing rewinding lines that adapt to changing production needs and wire characteristics with minimal human input. The ongoing R&D investments by leading firms suggest that wire rewinding machine automation will continue to evolve rapidly, delivering higher efficiency, lower operational costs, and more sustainable manufacturing practices through 2025 and beyond.
Leading Players & Company Innovations (e.g., ssm.ch, neewiremachine.com)
The wire rewinding machine automation sector is witnessing significant advancements as leading manufacturers prioritize efficiency, connectivity, and precision. In 2025, several key players are driving innovation by integrating Industry 4.0 technologies, enhancing user interfaces, and expanding their global reach.
SSM Schärer Schweiter Mettler AG (SSM Schärer Schweiter Mettler AG), a Swiss-based leader in precision winding solutions, is advancing automation with its digitalized rewinding platforms. Their latest machines feature smart sensors, remote monitoring, and automated tension control, enabling higher productivity and reducing manual intervention. SSM’s efforts to integrate IoT connectivity allow operators to access machine diagnostics and performance data in real time, supporting predictive maintenance and minimizing downtime.
Another key innovator, Dongguan NEE Wire Machine Co., Ltd. (NEE Wire Machine Co., Ltd.), has introduced rewinding systems with fully automated layer winding, digital length counting, and touch screen controls. The company’s 2025 portfolio emphasizes high-speed, low-noise operation, and compatibility with a broad range of wire diameters and materials. Their machines are increasingly adopted by cable manufacturers seeking to streamline production and maintain consistent coil quality.
In Japan, Shinko Machinery Co., Ltd. (Shinko Machinery Co., Ltd.) is focusing on customized automation for specialty wire applications. Its recent innovations include adaptive tension mechanisms and AI-based defect detection systems, allowing for real-time quality assurance and further reducing labor requirements. Shinko’s modular designs enable quick changeovers and are tailored for industries such as automotive wiring and fine electronics.
Leading Chinese supplier Dongguan Wiremac Machinery Co., Ltd. (Dongguan Wiremac Machinery Co., Ltd.) is expanding its export footprint with rewinding machines that support both automation and digital integration. Their 2025 offerings include compact, energy-efficient models optimized for small-batch runs and prototyping, targeting SMEs and specialized manufacturers.
Looking ahead, the sector’s outlook is shaped by demand for greater operational transparency, energy savings, and seamless integration with upstream and downstream equipment. Players are investing in cloud-based analytics, interoperability standards, and adaptive control algorithms. With the ongoing digital transformation, wire rewinding machine automation is poised for continued innovation and broader adoption across diverse manufacturing segments in the next few years.
AI & Smart Sensors: The New Heart of Wire Rewinding Systems
The integration of artificial intelligence (AI) and smart sensors is rapidly transforming wire rewinding machine automation, with 2025 marking a pivotal year for industry advancements. Modern rewinding systems now incorporate advanced vision systems, real-time data analytics, and adaptive control algorithms to boost efficiency, minimize downtime, and ensure product quality.
Leading manufacturers are embedding AI-driven modules for predictive maintenance and process optimization. For instance, Siemens offers solutions that analyze sensor data from motor drives and tension controllers to detect anomalies and schedule maintenance before a failure occurs, reducing unplanned stoppages and extending equipment lifespan. Similarly, ABB is outfitting automated rewinding lines with smart sensors that monitor wire diameter, spool speed, and environmental conditions, enabling precise adjustments in real time to maintain consistent output.
Smart sensors have evolved beyond simple data collection, now featuring edge computing capabilities. This allows critical calculations, such as tension optimization or defect detection, to be performed directly on the shop floor, minimizing latency. Companies like Rockwell Automation supply embedded sensor and controller platforms that enable wire rewinding machines to self-adjust based on coil characteristics and production targets. These technologies are central to achieving the high-throughput and low-defect rates demanded by wire and cable manufacturing in 2025.
AI-powered quality assurance is another burgeoning trend. Using machine vision, manufacturers can automatically inspect for wire surface defects, improper layering, or tension inconsistencies, reducing waste and manual inspection requirements. SICK AG provides smart optical sensors that integrate seamlessly with rewinding systems, delivering real-time visual analytics to operators and maintenance teams.
Looking ahead, the next few years are expected to bring even deeper integration of AI and smart sensor networks, supported by advances in industrial IoT connectivity and machine learning algorithms. Industry stakeholders anticipate further reductions in human intervention, greater adaptability to custom wire types, and seamless data integration with broader manufacturing execution systems. These trends position AI and smart sensors not just as enhancements, but as the new heart of fully automated, future-ready wire rewinding operations.
Regional Analysis: Demand Hotspots & Manufacturing Hubs
In 2025, the landscape for wire rewinding machine automation is characterized by distinct regional demand hotspots and emerging manufacturing hubs that are shaping global supply chains. Asia-Pacific continues to dominate as both a major manufacturing base and a rapidly expanding market for automated rewinding solutions. China, in particular, stands out due to its robust wire and cable industry, propelled by ongoing investments in electric mobility, infrastructure, and renewable energy. Leading Chinese manufacturers such as Dongguan Haoshuo Technology Co., Ltd. and Suzhou De-Pu Wire Winding Equipment Co., Ltd. are scaling up automation capabilities, introducing smart rewinding machines with features like servo-driven controls and real-time monitoring to meet stringent quality and efficiency demands.
India is another prominent hotspot, with heightened activity in the automotive and power sectors fueling demand for advanced winding and rewinding automation. Domestic firms are investing in tailored automation solutions to increase productivity and reduce labor dependency, while international players are also strengthening their presence. For instance, Elind Technologies Pvt. Ltd. has broadened its product portfolio to include automated rewinding systems for copper and aluminum wire, supporting the country’s expanding electrical manufacturing sector.
Europe remains a core region for high-precision automation, supported by its strong industrial automation culture and strict regulatory standards. Germany and Italy, in particular, are home to several technology leaders—such as Ziegler Automatisierungstechnik GmbH—who are pioneering integration of digital controls, advanced safety features, and remote diagnostics in rewinding machinery. The demand here is driven by the continued modernization of cable production lines, especially for the automotive and renewable energy sectors.
In North America, the United States and Mexico are seeing increased investments in automated wire rewinding equipment as part of broader reshoring and supply chain resilience strategies. Companies such as Wardwell Braiding Co. are responding by developing modular, easily upgradable rewinding solutions to serve both domestic cable manufacturers and international customers seeking North American manufacturing alternatives.
Looking ahead, Southeast Asia—with its growing electronics and appliance manufacturing industries—is poised to become a new manufacturing hub for automated wire rewinding machines. Countries like Vietnam and Thailand are attracting investments from global suppliers aiming to diversify their production bases and take advantage of lower labor costs while adopting automation to ensure competitiveness and quality.
In summary, as automation adoption accelerates, regional leaders are emerging based on a combination of local industrial strengths, investment in innovation, and integration into global supply chains. The coming years will likely see a further shift toward smart and connected rewinding solutions, particularly in Asia-Pacific and Europe, as manufacturers pursue efficiency, flexibility, and quality improvements.
Sustainability & Energy Efficiency Advances
The automation of wire rewinding machines is witnessing significant advancements in sustainability and energy efficiency as the sector adapts to stricter environmental standards and rising operational costs. In 2025, manufacturers are increasingly integrating smart control systems and energy-saving components to reduce the carbon footprint and overall energy consumption of their equipment.
Several leading machine builders have introduced innovations such as regenerative drive systems, which recover and reuse braking energy, and high-efficiency servo motors that minimize energy losses during operation. For example, Schlatter Industries AG emphasizes the use of energy-efficient drives and automation technologies in their wire winding and rewinding solutions, helping clients achieve both productivity improvements and lower energy bills. These systems can automatically adjust motor speed and torque to match the wire type and production requirements, eliminating unnecessary power consumption during idle or low-load periods.
Another trend is the adoption of integrated digital monitoring platforms. Companies such as Automatic Takeups Inc. are equipping rewinding machines with IoT-enabled sensors and real-time analytics, allowing operators to track energy usage, identify inefficiencies, and implement predictive maintenance strategies. This not only extends machine lifespan but also prevents energy waste caused by overheating or suboptimal operation.
Materials and process innovation are also supporting sustainability goals. For instance, KOCH Industrieanlagen GmbH is developing systems that minimize scrap generation during changeovers and spool transitions, addressing both material efficiency and energy use. Automated tension and alignment controls ensure consistent winding, reducing the need for rework and further conserving resources.
Looking ahead, regulatory measures in regions such as the European Union are expected to accelerate the adoption of eco-friendly automation features. The incorporation of advanced software for process optimization, coupled with continued improvements in electric motor and drive technology, is likely to become standard across new models by 2026–2028. As wire manufacturers and processors face mounting pressure to demonstrate environmental responsibility, energy-efficient automated rewinding machines will play a central role in meeting sustainability targets and reducing operational costs without compromising productivity.
Integration with Industry 4.0 and IoT
In 2025, the integration of Industry 4.0 concepts and Internet of Things (IoT) technologies into wire rewinding machine automation is accelerating, driving significant advancements in operational efficiency, quality control, and data-driven maintenance. Manufacturers are increasingly deploying smart sensors, edge computing modules, and cloud connectivity within their rewinding systems to enable real-time monitoring, remote diagnostics, and predictive maintenance. This digital transformation aligns with the broader trend of connected manufacturing, where machines communicate seamlessly with enterprise resource planning (ERP) and manufacturing execution systems (MES).
Leading companies in the sector have launched new models of wire rewinding machines equipped with IoT-ready control panels and advanced human-machine interfaces (HMIs). For example, Schlatter Group has incorporated intelligent automation and digital connectivity features into its wire processing machinery, enabling remote support and performance analytics. Similarly, Ziegler Metallbearbeitung GmbH offers wire winding and rewinding solutions with integrated data collection capabilities, supporting real-time process optimization and traceability.
A key development is the adoption of open industrial communication protocols such as OPC-UA and MQTT, which facilitate interoperability between rewinding machines and factory-wide automation networks. Companies like Siemens AG provide automation controllers and IoT gateways that are increasingly being embedded in wire processing lines, allowing centralized monitoring and control over multiple machines. This connectivity not only streamlines production but also enables predictive analytics—reducing unplanned downtime by triggering maintenance only when data-driven indicators suggest imminent failure.
Another trend is the emergence of digital twins and virtual commissioning. By creating a digital replica of the rewinding machine, manufacturers can simulate workflows, optimize settings, and train operators in a risk-free environment before actual deployment. Bosch Rexroth supports such applications with its automation platforms, helping customers achieve faster time-to-market and enhanced production flexibility.
Looking ahead, the outlook for wire rewinding machine automation within the context of Industry 4.0 and IoT remains robust. As end-users in the automotive, electronics, and construction sectors continue to demand higher quality and traceability, manufacturers are expected to further invest in smart rewinding solutions that support advanced analytics, remote troubleshooting, and seamless integration with smart factories.
Challenges, Risks, and Regulatory Landscape
The automation of wire rewinding machines is advancing rapidly, yet several challenges and risks persist as the industry heads through 2025 and into the near future. One significant challenge involves the integration of advanced automation technologies—such as programmable logic controllers (PLCs), robotics, and Industrial Internet of Things (IIoT) solutions—into legacy manufacturing environments. Many wire and cable producers must retrofit or upgrade existing machinery to accommodate these systems, which can lead to compatibility issues and increased capital expenditure. For example, Schlatter Group highlights the complexity of integrating new automation modules into established production lines, emphasizing the need for robust engineering and technical support.
Another key risk is cyber security. As wire rewinding machines become more connected through IIoT, they are increasingly vulnerable to cyber threats, including unauthorized access and data breaches. Manufacturers such as Siemens AG are actively developing and promoting industrial security solutions tailored for automated manufacturing environments, but the rapidly evolving threat landscape demands continuous vigilance and investment.
Workforce adaptation also presents a challenge. The shift toward automation requires operators and maintenance personnel to acquire new digital and technical skills. Rosendahl Nextrom emphasizes ongoing training and upskilling as essential for successful automation projects, noting that insufficient workforce preparation can hinder both productivity gains and machine uptime.
Regulatory compliance is another important consideration. Automated wire rewinding machines must meet stringent safety, environmental, and operational standards, which can vary by region. In the European Union, for instance, machinery must comply with the EU Machinery Directive (2006/42/EC) and relevant CE marking requirements. Sicme Italia Impianti provides guidance on how automation solutions can be designed to meet these regulatory demands, including risk assessments and conformity documentation.
Looking forward, evolving standards related to machine safety, data privacy, and energy efficiency are expected to shape the regulatory environment. Ongoing collaboration between manufacturers, automation suppliers, and regulatory bodies will be critical to ensuring that wire rewinding machine automation is both safe and compliant as the industry continues to innovate through 2025 and beyond.
Strategic Outlook: Opportunities & Investment Priorities for 2025–2028
The strategic outlook for wire rewinding machine automation from 2025 to 2028 is marked by accelerating investment in digitalization, process integration, and sustainability-driven upgrades. As global manufacturing sectors—particularly electrical, automotive, and cable industries—pursue higher productivity and quality, demand for automated rewinding solutions is expected to intensify. Key opportunities and priorities are emerging across multiple dimensions:
- Integration of Industry 4.0 Capabilities: Market leaders are investing in smart automation, with a focus on data-driven monitoring, predictive maintenance, and remote diagnostics. For example, Schlatter Group and Automata Packaging Systems have enhanced their wire rewinding lines by embedding IoT sensors and cloud connectivity, enabling real-time performance tracking and more agile production scheduling.
- Electrification and E-Mobility: The rapid global expansion of electric vehicles (EVs) and renewable energy infrastructure is driving demand for specialized wire forms and high-volume production. Firms like SAMP S.p.A. are developing advanced rewinding machines capable of handling multiple wire diameters and materials, supporting the sector’s diversification and scalability needs.
- Focus on Energy Efficiency and Waste Reduction: With sustainability becoming a board-level priority, investments are being directed towards automation solutions that minimize material scrap, reduce energy consumption, and support closed-loop manufacturing. Makinate Srl highlights the growing market for energy-efficient and retrofit-ready rewinding equipment, aligning with global decarbonization goals.
- Customization and Flexibility: As batch sizes decrease and product complexity increases, manufacturers are prioritizing rewinding machines with modular designs and quick-change capabilities. QUEINS Machines GmbH and others are responding with configurable platforms that allow rapid adaptation to evolving wire specifications and customer requirements.
Looking ahead, investment priorities will likely center around digital control retrofits, cross-line automation (integrating rewinding with upstream and downstream processes), and enhanced operator interfaces. Strategic partnerships between machine makers, automation specialists, and end-users will further accelerate innovation. Given regulatory and market pressures for traceability and sustainability, companies that proactively implement advanced automation in their wire rewinding operations are poised to capture significant competitive advantages through 2028 and beyond.
Sources & References
- Schlatter Group
- SAMP S.p.A.
- Mikrosam
- Rosendahl Nextrom GmbH
- Supermac Industries (India) Limited
- Schleuniger AG
- Ziegler Metallbearbeitung GmbH
- SSM Schärer Schweiter Mettler AG
- Dongguan Wiremac Machinery Co., Ltd.
- Siemens
- Rockwell Automation
- SICK AG
- Elind Technologies Pvt. Ltd.
- Ziegler Automatisierungstechnik GmbH
- Wardwell Braiding Co.
- Bosch Rexroth
- Makinate Srl